
Автоматизация сварочных процессов
..pdfМинистерство образования и науки Российской Федерации Федеральное государственное бюджетное образовательное
учреждение высшего профессионального образования «Пермский национальный исследовательский политехнический университет»
В.Я. Беленький, В.В. Мелюков, Д.Н. Трушников
АВТОМАТИЗАЦИЯ СВАРОЧНЫХ ПРОЦЕССОВ
Утверждено Редакционно-издательским советомуниверситета в качестве учебного пособия
Издательство Пермского национального исследовательского
политехнического университета
2013
1
УДК 621.791-52 (075.8)
Б43
Рецензенты:
канд. техн. наук О.А. Косолапов (Пермский военный институт внутренних войск МВД России);
д-р техн. наук, профессор Е.А. Кривоносова (Пермский национальный исследовательский политехнический университет)
Беленький, В.Я.
Б43 Автоматизация сварочных процессов : учеб. пособие / В.Я. Беленький, В.В. Мелюков, Д.Н. Трушников. – Пермь : Изд-во Перм. нац. исслед. политехн. ун-та, 2013. – 103 с.
ISBN 978-5-398-01097-8
Рассматриваются вопросы управления оборудованием в сварочном производстве применительно к задачам автоматизации сварочных процессов. Изложены основы моделирования тепловых процессов при использовании сварочных источников теплоты различной конфигурации и оптимального управления сварочными процессами. Представлены методы управления процессами дуговой, контактной и электронно-лучевой сварки.
Предназначено для студентов специальности 150202 «Оборудование и технология сварочного производства» по дисциплине «Автоматизация сварочных процессов»
Учебное пособие подготовлено и издано при финансовой поддержке Министерства образования Пермского края
ISBN 978-5-398-01097-8 |
© ПНИПУ, 2013 |
2
ОГЛАВЛЕНИЕ |
|
Введение................................................................................. |
4 |
1. Общие вопросы управления техническими системами ........... |
5 |
1.1. Применение систем управления |
|
в сварочном производстве .................................................. |
5 |
1.2. Общая схема системы управления |
|
сварочным оборудованием ............................................... |
10 |
1.3. Элементы систем управления ........................................... |
11 |
1.4. Понятие оптимизации в задачах управления................... |
11 |
2. Автоматизация управления сварочным оборудованием........ |
19 |
2.1. Автоматизация управления дуговой сваркой.................. |
19 |
2.2. Автоматизация управления контактной сваркой............. |
51 |
2.3. Автоматизация управления |
|
электронно-лучевой сваркой............................................. |
65 |
3. Моделирование процессов сварки и термообработки............ |
76 |
3.1. Применение моделирования систем |
|
управления в системах управления.................................. |
76 |
3.2.Математическое моделирование тепловых процессов при использовании источников
нагрева различной конфигурации .................................... |
76 |
3.3. Обратная задача теплопроводности |
|
и методы ее решения.......................................................... |
81 |
Библиографический список.......................................................... |
99 |
3
ВВЕДЕНИЕ
Основной задачей современного производства является повышение конкурентоспособности производимой продукции. Важнейшими составляющими конкурентоспособности являются качество продукции и её себестоимость.
Наиболее актуальной проблемой организации современного производства является нехватка квалифицированного персонала. Но при успешном решении данной проблемы содержание штата квалифицированных специалистов-сварщиков является экономически затратным. При ручном управлении процессом даже высокая квалификация персонала не позволяет снижать долю бракованных изделий ниже определенного порогового уровня. Поэтому для повышения качества выпускаемой продукции и снижения издержек производства технологический процесс сварки в первую очередь нуждается в автоматизации.
К технологическим методам повышения качества продукции относят изменение технологии производства, подбор обрабатывающего оборудования и строгое обоснование режимов обработки.
Подбор или изменение технологии производства требует знания современных технологий обработки материалов, а также должен учитывать влияние применяемых технологий на физические и эксплуатационные характеристики материалов изделий. При выборе технологического оборудования необходимо знание основных его характеристик, обеспечивающих заданные параметры технологического процесса. Используемые режимы обработки должны обеспечить заданное качество конечной продукции, что требует выявления численных зависимостей показателей качества от режимов обработки, параметров материала и изделия, а также свойств используемого оборудования.
На современном этапе развития сварочных технологий широко применяется предварительное и on-line математическое моделирование физических процессов и процессов управления.
4
1. ОБЩИЕ ВОПРОСЫ УПРАВЛЕНИЯ ТЕХНИЧЕСКИМИ СИСТЕМАМИ
Автоматическим регулированием называется изменение какой-либо физической величины по требуемому закону без непосредственного участия человека.
Физическая величина, подлежащая регулированию, называется регулируемой величиной, а технический агрегат или процесс, который регулируется, – регулируемым объектом.
1.1. Применение систем управления в сварочном производстве
Получение качественных сварных швов требует высокой квалификации специалистов-сварщиков. Для их подготовки необходимо длительное время и высокие затраты. Таким образом, при ручном управлении технологическим процессом (ТП) возникают следующие проблемы:
–необходимость подготовки и содержания штата высококвалифицированных специалистов;
–плохая воспроизводимость изделий при ручном управлении;
–необходимость непрерывного решения оптимизационных задач при управлении технологическим процессом производства готовых изделий: оптимизация качества продукции, скорости обработки, энерго- и ресурсопотребления и т.п.
Альтернативой квалифицированному ручному управлению является автоматизация технологических процессов сварки, то есть создание АСУТП. Работы по автоматизации сварочного производства ведутся уже более полувека [55]. Первоначально разрабатывались системы контроля и регулирования отдельных параметров процесса. В настоящее время используется комплексный подход к автоматизации технологических процессов сварки, ЭЛУ, которые предусматривают решение следующих задач:
5
–автоматизация основных и вспомогательных технологических операций;
–оптимизация режимов обработки;
–повышение надежности системы управления,обеспечение
требуемой воспроизводимости технологических операций;
–прогнозирование нестандартных ситуаций и алгоритмов выхода из них;
–полное документирование ТП.
Кроме того, всовременныхСУреализованыследующие задачи:
–совмещение источника энергии с зоной термообработки;
–выполнение алгоритмов управления параметрами энергетического инструмента – дуги, электронного луча и т.д.;
–выполнение алгоритмов управления скоростью сварки и перемещением изделия;
–регистрация параметров процесса.
Каждую из задач может решать отдельная, локальная СУ, или все задачи могут одновременно решаться комплексной СУ.
В целом классификация систем управления сварочными процессами соответствует общепринятой классификации систем управления любыми технологическими процессами и имеет специфику только в связи с особенностью объекта управления, что отражается в классификации систем по управляемым параметрам. Системы управления сварочным оборудованием можно классифицировать по нескольким признакам.
По времени реакции на внешние события системы управления ЭЛУ можно разделить на системы жесткого или мягкого реального времени и системы, работающие вне реального времени. Под жестким реальным временем применительно к СУ можно понимать такое быстродействие системы, которое обеспечит гарантированное соблюдение технологических параметров в заданных пределах. Как правило, это системы с обратной связью, например система стабилизации тока дуги или луча или система управления сервоприводом перемещения изделия. Алгоритм работы таких систем и регуляторов достаточно прост, не требует большого объёма вычислений и учитывает достаточно
6
высокую инерционность сварочных процессов. Система мягкого реального времени может допустить кратковременный выход технологических параметров за допустимые пределы ввиду инерционности измерительного либо исполнительного оборудования, а также сравнительно большого объёма вычислений. Частным примером такой системы может служить система управления разверткой электронного луча: при смене формы развертки параметры режима могут быть кратковременно нарушены. Системы, работающие вне реального времени, как правило, выполняются разомкнутыми и не гарантируют соблюдения заданных технологических параметров процесса. Это так называемые системы прямого программного управления, для которых управляющее воздействие на весь цикл обработки изделия просчитано заранее и занесено в память. Применение таких систем обусловлено невозможностью расчетов тепловых моделей в реальном времени ввиду значительного объёма вычислений и высоких требований к аппаратуре ЭВМ.
По типу используемых сигналов и принципа действия вычислителя СУ различают аналоговое и цифровое управление. На современном этапе развития вычислительной техники применение цифровых микропроцессоров и компьютеров практически безальтернативно. К цифровым сигналам ЭЛУ относятся лишь сигналы двоичных датчиков и управляющие сигналы современных сервоприводов. Следует заметить, что большинство контролируемых и управляемых сигналов сварочных процессов (температуры, токов, напряжений, давления, сигналы развертки) имеют аналоговую форму, поэтому используются соответствующие преобразователи – цифроаналоговые преобразователи (ЦАП) и аналого-цифровые преобразователи (АЦП).
По количеству управляемых параметров СУ сварочным оборудованием существующие можно разделить на однопараметрические и многопараметрические. Многопараметрические системы могут быть с независимыми параметрами, связанными только общим вычислителем, например СУ подачи газа и СУ
7
током электрической дуги, и многоконтурными системами с взаимозависимыми параметрами, например система управления током дуги и температурой, температурой и размерами пятна нагрева и т.д. Принципы построения таких систем изложены в [71, 17–20]. Только многопараметрические, многоконтурные системы и системы с распределёнными параметрами позволяют удовлетворить современные требования к качеству управления сварочными процессами. В то же время контуры управления вспомогательными подсистемами, такими как подсистема подачи защитного газа или система охлаждения, могут быть выделены в отдельные независимые системы управления, что позволит унифицировать эти подсистемы для оборудования различных марок и назначения, использовать стандартные решения и в конечном счете уменьшить капитальные и эксплуатационные расходы на автоматизацию.
По выполняемым функциям управления СУ можно разделить на системы слежения за стыком; системы управления мощностью источника энергии; системы позиционирования детали; системы управления разверткой; системы управления вакуумным оборудованием и т.д.
По наличию или отсутствию обратной связи системы управления можно разделить на разомкнутые, замкнутые одноконтурные и замкнутые многоконтурные системы управления.
Достоинства и недостатки систем управления приведённых типов известны и приводятся в специальной литературе [17–20, 34, 71, 72, 73, 75]. В настоящее время большинство систем проектируется замкнутыми как обеспечивающие лучшую точность и быстродействие. Многоконтурные системы применяются в многопараметрических регуляторах [73], при одновременном управлении взаимозависимыми параметрами, например температурой и мощностью луча [64].
По уровню автоматизации можно выделить полностью автоматические системы управления, автоматизированные системы управления и системы поддержки принятия решений (экс-
8
пертные системы). Автоматические системы управления исключают человека из контура управления, следовательно, обслуживающий персонал ЭЛУ не может повлиять на технологический процесс. Комплексную автоматическую систему управления создавать нецелесообразно ввиду множества субъективных факторов, изменяющихся со временем, например изменение формы, сплава, технологии обработки изделий. В то же время некоторыми параметрами ЭЛУ следует управлять в автоматическом режиме, например током электронного луча. Ввиду инерционности установки в процессе сварки или термообработки требуется стабилизировать ток электронного луча, что реализовано, например, в [74]. Большинство существующих систем управления в области сварки – автоматизированные, т.е. позволяют оператору в любой момент вмешаться в ход технологического процесса с целью коррекции каких-либо параметров, например температурного режима. В ходе термообработки часто используется визуальное определение температуры, чаще по цвету свечения нагретой заготовки (цветовая температура [76]), реже по яркости свечения (яркостная температура [76]). Если данная система не оборудована дистанционным измерителем температуры – пирометром или тепловизором, – управление током луча происходит вручную по результатам визуального наблюдения за обрабатываемой областью, и наличие опытного оператора-сварщика необходимо [38]. Экспертные системы целесообразно применять в мелкосерийном производстве. Для этого целесообразно создать банк данных режимов термической обработки различных сплавов и геометрических форм деталей [77]. Такая система управления часто работает в режиме советчика и рекомендует использовать человеку тот или иной стандартный режим. Окончательное решение о выбранных параметрах обработки принимает человек, соглашаясь или отвергая рекомендованное системой решение. В общем случае система-советчик напрямую не связана с ЭЛУ и может входить в АСУП [78].
9
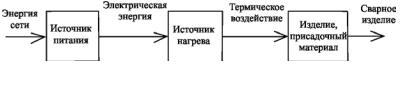
1.2. Общая схема системы управления сварочным оборудованием
При автоматическом регулировании сварочных процессов конечной целью является создание системы автоматического регулирования параметрами режима сварки.
Современный уровень развития сварочной техники и технологии предполагает большое разнообразие источников нагрева, их энергетических характеристик и способов теплового воздействия на изделие. При рассмотрении процессов сварки как объектов автоматического управления целесообразно исходить из общей для всех способов сварки последовательности преобразования энергии.
Электрическая энергия, поступающая из промышленной сети, преобразуется в источнике питания в форму, наиболее полно соответствующую каждому конкретному источнику нагрева, который затем преобразует электрическую энергию в термическое воздействие на изделие и присадочный материал.
Таким образом, формирование сварного соединения можно рассматривать как результат функционирования системы «источник питания – источник нагрева – изделие» (рис. 1.1).
Рис. 1.1. Обобщенная схема сварочного процесса
Отдельные компоненты этой системы объединены обратными связями в сложную многосвязную систему. Действие этих связей проявляется в том, что изменения процесса формирования сварного соединения оказывают обратное воздействие на источники нагрева и питания.
Выбор электронного луча как инструмента термической обработки обусловлен высокой концентрацией энергии в пучке
10