
Наукоемкие химические технологии учебное пособие
..pdfлюбого перемещения катализаторного слоя, который должен оставаться плоским во время всей операции (поэтому и заполнение конвертора должно быть особенно тщательным). Температура технологического газа на выходе из конвертора должна превышать температуру конденсации образовавшихся паров серы не менее, чем на 10–15 °С.
Температурный режим в каталитических конверторах поддерживают так, чтобы температура реакционного газа на выходе из них составляла: в первом – 300–320 °С (для более полного гидролиза CS2 и COS в H2S), во втором – 230–220 °С и в третьем – 220–210 °С (для более полного окисления сероводорода).
Снижение температуры в каталитическом конверторе сдвигает равновесие реакции сероводорода в сторону образования серы, но при этом снижается скорость самой реакции окисления, что особенно ощутимо при наличии третьего реактора.
Для эффективной работы установок Клауса необходимы:
•наличие восстановительной среды во всех точках потока и в слоях катализатора в период работы, пуска и остановки производства с целью снижения скорости сульфатирования катализатора;
•контроль за перепадом температур в каталитических реакторах, влияющим на продолжительность работы и активность катализатора;
•использование в процессе, по возможности, несульфатирующихся катализаторов;
•оптимизация процесса посредством точной регулировки подачи воздуха в печь и использования автоматических анализаторов соотношения продуктов реакции в отходящих газах;
•оптимизация профиля температур по всем стадиям процесса, что способствует повышению степени извлечения серы на 1–2 % (понижение температуры способствует более глубокому протеканию основных реакций и более полному
41
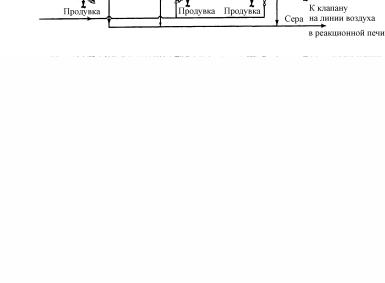
выделению серы при сепарации и конденсации). Снижение температуры на выходе из конденсатора серы может оказаться эффективным и экономически оправданным, несмотря на соответствующее снижение давления получаемого пара;
•дополнительная установка третьей каталитической ступени и конденсатора-сепаратора на линии отходящих газов, которая позволяет повысить степень извлечения серы примерно на 2 %;
•контактный подогрев газа перед каждым каталитическим конвертором, что также позволяет повысить степень извлечения серы на 2 %;
•усовершенствование системы контроля и управления процессом.
Рис. 10. Технологическая схема каталитической стадии производства серы методом Клауса: 1 – каталитические реакторы; 2 – подогреватели газа; 3 – конденсаторы серы
Затраты на мероприятия, связанные с изменениями схемы и улучшением технологии, осуществление которых воз-
42
можно без прекращения работы основного оборудования, могут оказаться намного ниже, чем на создание новых установок.
Степень извлечения серы на обычных установках Клауса не превышает 96–97 %. Более полное извлечение серы ограничивается тем, что реакция Клауса обратима, из-за чего полное превращение H2S и SO2 невозможно.
Кроме того, вода, образующаяся по реакции Клауса
ине удаленная полностью из продуктов реакции (что практически невозможно), затрудняет дальнейшее превращение
иограничивает степень извлечения серы. К тому же, соблю-
дение стехиометрического соотношения H2S:SO2, равного 2:1, на практике трудновыполнимо.
Сцелью улавливания серы и уменьшения ее выбросов в атмосферу разработано несколько модификаций процесса Клауса.
Более подробная технологическая схема каталитической стадии представлена на рис. 10.
II.НОВЫЕ ТЕХНИЧЕСКИЕ РЕШЕНИЯ
ВПРОИЗВОДСТВЕ АММИАКА
1.Энергосберегающие технологии
всуществующих производствах аммиака
Производства аммиака являются интенсивными потребителями энергии. Часть ее составляет электричество и топливный газ, но основная часть – это природный газ. Современные производства аммиака требуют порядка 30 ГДж энергии для производства одной тонны аммиака. Это соответствует примерно 830 нм3 высококалорийного природного газа на тонну аммиака.
В связи с введением в 60-х годах крупных производств аммиака, основанных на центробежных компрессорах, производственные мощности возросли с 600 до 1800 т аммиака
43
в сутки. В то же время общее потребление энергии новых установок снизилось с 40 до 30 ГДж на тонну аммиака. Однако у многих производств аммиака потребление энергии в настоящее время далеко превышает цифру 30.
За последние двадцать лет был разработан ряд технологий по улучшению энергоэффективности на производствах аммиака. Две из них оказали наибольшее влияние.
Прежде всего, было разработано вращающееся оборудование с гораздо большей эффективностью компрессии и расширения по сравнению с тем, что было 10 лет назад. Это привело к значительной экономии энергии приводного оборудования, особенно для двух вращающихся потребителей энергии: компрессора синтез-газа и компрессора подпиточного синтез-газа.
Вторая разработка имела место в секции удаления СО2. В стандартных проектах требовалось общее потребление энергии 120 МДж на кмоль удаленного СО2. Эта цифра может быть гораздо ниже 80 МДж/кмоль путем таких средств, как применение лучшего абсорбента и/или установка так называемого ребойлера обратного потока. Однако недавно разработаны технологии с минимальным потреблением энергии: 40 МДж/кмоль с раствором MDEA и даже 10 МДж/кмоль с более дорогим Selexol.
Основным моментом каждой реконструкции является скорее экономия природного топливного газа, чем экономия природного технологического газа. Топливный газ применяется в радиантных горелках первичного риформинга, в газовой турбине, если она используется, а также дополнительно – в горелках пароперегревателя или в горелках вспомогательного котла.
Радиантные горелки в первичном риформинге являются наибольшими потребителями топливного газа на производстве аммиака. Естественно, что многие проекты по реконструкции, связанные с повышением эффективно-
44
сти, фокусируются на снижение потребления газа этими горелками.
Температура подогрева обычной парогазовой смеси на стандартном производстве аммиака составляет порядка 500 °С. Расход топливного газа в радиантных горелках может быть снижен путем подачи парогазовой смеси при более высокой температуре в радиантные трубы. Эта повышенная температура обычно достигается путем большего нагрева в секции конвекции. Небольшое повышение, скажем, до 520 °С, вполне достижимо в проектных пределах имеющегося оборудования.
Также могут иметь место более высокие температуры порядка 600 °С, что соответствует снижению расхода природного газа в радиантных горелках до 15 %. Однако для этих более высоких температур требуется дорогостоящая модернизация системы на входе в катализаторные трубы.
Другим методом снижения расхода топливного газа в радиантных горелках является добавление в систему предварительного риформинга. Преимущество предварительного риформинга заключается в том, что не требуется модернизации системы на входе катализаторной трубы. Система работает следующим образом. Парогазовая смесь подогревается до максимально допустимой температуры в системе на входе катализаторных труб, скажем, до 500–520 °С. Далее она проходит через адиабатический прериформинг (наполненный катализатором сосуд), в котором высшие углеводороды ПГС преобразуются в метан, СО и водород. Часть метана также преобразуется в СО и водород. Эти реакции приводят к падению температуры на 60–70 °С. Прореагировавшая газовая смесь, выходящая из риформинга при температуре около 440 °С, снова подогревается в секции конвекции примерно до 500–520 °С и поступает на вход катализаторных труб. Подача предварительно реформированной смеси снижает расход природного газа порядка на 8 %.
45
Третьим способом снижения нагрузки радиантных горелок является использование парогазовой смеси с более низким соотношением пар:углеводород. Такой подход снижает поток массы, проходящий через катализаторные трубы, означающий, что потребуется меньше тепла для нагревания газовой смеси до требуемых 800 °С на выходе катализаторных труб. При такой технологии достигается снижение расхода газа в радиантных горелках на 2–3 %.
Классическая температура подогрева технологического воздуха составляет примерно 500 °С.
Более высокая температура через нагрев в секции конвекции первичного риформинга имеет эффект двух видов.
Прежде всего, добавленное тепло может быть использовано для снижения расхода газа в радиантных горелках, так как реформированная газовая смесь из первичного риформинга может подаваться на вторичный риформинг при более низкой температуре. Таким образом, расход может быть снижен примерно на 5 %.
Во-вторых, дополнительное тепло может быть использовано для увеличения температуры на выходе вторичного риформинга. Это снизит проскок метана из вторичного риформинга и уменьшит продувочный поток в системе синтеза аммиака.
Существуют и другие способы энергосбережения в производствах аммиака. Они связаны с повышением конечной температуры вторичного риформинга, с увеличением чистоты синтез-газа, в частности за счет более полной конверсии СО и более тонкой очистки газа от СО2, с более эффективным использованием тепла синтеза аммиака, с применением новых более активных катализаторов.
Так, фирмой Sud-Chemie разработан и выпускается новый катализатор AmoMax-10 на основе нестехиометрического оксида железа – вьюстита (Fe1–x O). Этот катализатор проявляет на 70 % более высокую активность по сравнению
46
с обычными железными катализаторами синтеза аммиака на основе магнетита. Кроме того, AmoMax-10 имеет более низкую температуру восстановления и более высокую прочность, что обеспечивает более длительный срок его эксплуатации (до 15 лет).
Основные мероприятии по усовершенствованию производства аммиака приведены ниже:
|
Мероприятия |
|
Получаемый результат |
||
по усовершенствованию |
|||||
|
|||||
Секция риформинга |
|
|
|||
1. |
Предварительный |
на- |
Снижение энергетических |
||
грев воздуха на горелки. |
|
затрат. |
|||
2. |
Предварительный |
на- |
Снижение энергетических |
||
грев |
технологического |
воз- |
затрат. |
||
духа до более высокой тем- |
|
||||
пературы. |
|
|
|
||
3. |
Предварительный |
на- |
Снижение энергетических |
||
грев |
парогазовой |
смеси |
до |
затрат. |
|
более высокой температуры. |
|
||||
4. |
Снижение соотношения |
Снижение энергетических |
|||
пар/газ. |
|
|
затрат, увеличение произво- |
||
|
|
|
|
дительности. |
|
5. |
Замена труб печи пер- |
Снижение энергетических |
|||
вичного риформинга. |
|
затрат, увеличение произво- |
|||
|
|
|
|
дительности. |
|
6. |
Проведение вторичного |
Снижение энергетических |
|||
риформинга с избытком воз- |
затрат на первичном рифор- |
||||
духа или с воздухом, обога- |
минге, увеличение произво- |
||||
щенным кислородом. |
|
дительности. |
|||
7. |
Установка |
предвари- |
Снижение энергетических |
||
тельного риформинга. |
|
затрат, увеличение произво- |
|||
|
|
|
|
дительности. |
|
8. |
Установка |
более |
эф- |
Снижение энергетических |
|
фективных горелок. |
|
затрат. |
47
Мероприятия |
|
Получаемый результат |
|||||
по усовершенствованию |
|||||||
|
|
|
|
||||
Секция конверсии оксида |
|
|
|
|
|||
углерода |
|
|
|
|
|
|
|
1. Использование |
более |
1. Снижение |
энергетиче- |
||||
активного медьпромотиро- |
ских затрат за счет использо- |
||||||
ванного катализатора |
высо- |
вания более низкого соотно- |
|||||
котемпературной |
конверсии |
шения пар:газ. |
|
|
|||
СО. |
|
|
2. Более |
низкое содержа- |
|||
|
|
|
ние СО на выходе. |
|
|||
2. Применение |
селектив- |
Снижение количества СО, |
|||||
ных катализаторов на низко- |
которое подвергается |
мета- |
|||||
температурной |
конверсии |
нированию. |
|
|
|
||
СО. |
|
|
|
|
|
|
|
Секция выделения СО2 |
|
Снижение |
энергетических |
||||
1. Использование более |
|||||||
энергетически выгодных аб- |
затрат за счет использования |
||||||
сорбентов. |
|
|
более низкого |
соотношения |
|||
|
|
|
пар:газ. |
|
|
|
|
2. Использование более |
Уменьшение количества цир- |
||||||
эффективной насадки. |
|
кулирующего |
абсорбента |
||||
|
|
|
и тепла извне. |
|
|
||
3. Замена в абсорбере та- |
Способствует |
увеличению |
|||||
релок на насадку. |
|
|
мощности, |
снижает |
потери |
||
|
|
|
давления в абсорбере. |
|
|||
4. Замена в регенераторе |
Уменьшает давление в реге- |
||||||
тарелок на насадку. |
|
нераторе и расход тепла из- |
|||||
|
|
|
вне. |
|
|
|
|
Секция синтеза |
|
|
|
|
|
|
|
1. Применение более эф- |
1. Снижение затрат на ка- |
||||||
фективных катализаторов. |
тализатор, повышение степе- |
||||||
|
|
|
ни конверсии при более низ- |
||||
|
|
|
ком давлении, |
уменьшение |
|||
|
|
|
затрат на циркуляцию. |
|
|||
2. Дополнительная |
осуш- |
2. Увеличение производи- |
|||||
ка синтез-газа. |
|
|
тельности колонны синтеза. |
48
Мероприятия |
Получаемый результат |
||
по усовершенствованию |
|||
|
|||
3. Замена аксиального хо- |
3. Уменьшение падения |
||
да газа на радиальный. |
давления в колонне, увели- |
||
|
|
чение производительности |
|
|
|
колонны синтеза. |
|
4. Установка |
дополни- |
4. Увеличение производи- |
|
тельного конвертора. |
тельности колонны синтеза. |
||
5. Выделение |
водорода |
5. Снижение энергетиче- |
|
и азота из продувочного газа. |
ских затрат, снижение со- |
||
|
|
держания инертов, увеличе- |
|
|
|
ние мощности. |
2. Технология аммиака фирмы Kellog
Технология фирмы Kellog включает два новых улуч-
шенных процесса: The Kellog Advanced Ammonia Process (KААР) и The Kellog Reforming Exchanger System (KRES).
Технология KААР основана на использовании нового катализатора на основе металлического рутения, нанесенного на карбидную основу. Катализатор проявляет высокую активность при относительно низких температурах (380–420 °С) и низких давлениях (130–140 атм.).
Технология KRES использует вместо трубчатой печи парового риформинга новый аппарат – теплообменый ре-
формер (reforming exchanger).
Основные стадии: компрессия воздуха и природного газа, очистка от серы, автотермический паровоздушный риформинг, паровой риформинг в аппарате KRES, паровая конверсия СО, очистка от СО2, очистка газа метанированием, осушка синтез-газа на цеолитах, выделение метана, части азота, аргона на криогенной установке, сжатие синтез-газа, синтез аммиака в колонне синтеза KААР, выделение аммиака в холодильном теплообменнике (refrigeration exchanger).
49

50
1 |
2 |
3 |
4 |
5 |
|
||||
|
|
|
|
6 |
9 |
7 |
|
10
8 12
11
Рис. 11. Технология синтеза аммиака фирмы Kellog Brown & Root: 1 – воздушный компрессор; 2 – подогреватель; 3 – автотермический реформер; 4 – аппарат KRES; 5 – аппараты паровой конверсии СО; 6 – колонна очистки конденсата; 7 – система выделения аммиака; 8 – колонна синтеза KAAP; 9 – компрессор синтез-газа; 10 – система криогенной очистки газа; 11 – регенератор; 12 – абсорбер
50