
- •ORGANIZATIONS AND THEIR GOALS
- •THE MANAGEMENT PROCESS
- •Decision Making
- •Accounting System
- •Cost Accounting System
- •MANAGERIAL ACCOUNTING
- •FINANCIAL ACCOUNTING
- •Managers at all levels
- •Counsel
- •Treasurer
- •Personnel Director
- •Chief of
- •Chief of
- •Surgery
- •Chief of
- •Director of
- •Director of
- •Chief of Medical
- •Chief of
- •Internal
- •Chief of
- •Chief of
- •Production
- •Stage 1
- •Production
- •Stage II
- •Input
- •Process
- •Output
- •A particular
- •Work-in- Process
- •Inventory
- •Cost of
- •until the
- •Cost
- •Cost
- •Cost
- •Costs
- •Simplified decision
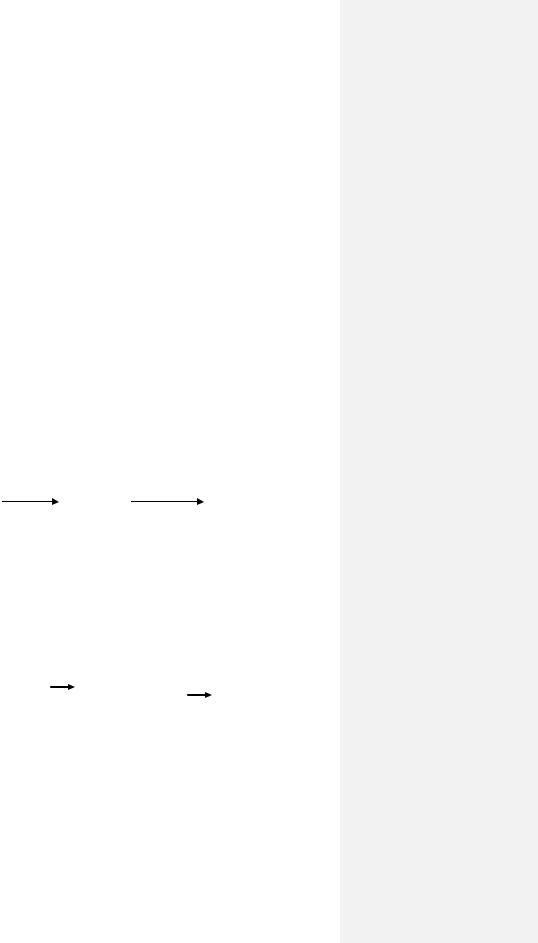
A Systems Perspective
Managerial accounting constitutes one of several systems used by managers in running an organization. A system is an integrated structure designed to accomplish a stated purpose. A system consists of a set of inputs, a process, and a set of outputs, which are defined as follows:
Input: data entered into a system, which are intended to have a measurable effect on the system.
Process: a set of activities performed by the system in order to achieve the stated purpose.
Output: information generated by the system, which is available to the system’s users for a variety of purposes.
Exhibit 1-6 shows the components of a system and illustrates them for Olympia Regional Hospital. As you study this text, you will see that the managerial accounting function incorporates elements of many systems, all of which are intended to help managers run an organization.
Exhibit 1-6. Elements of a System
Elements of system
Definitions of system elements
Illustration of system elements: Olympia Regional Hospital
|
Input |
|
|
Process |
|
|
|
|
Output |
|
|
|
|
|
|
|
|
|
|
|
|
|
|
|
|
Data entered |
Activities |
|
Information |
|
||||||||
into the |
|
|
performed by |
generated by |
|
|||||||
system. |
|
|
the system |
|
the system. |
|
||||||
|
|
|
|
|
|
|
|
|||||
|
Data: patient’s |
|
|
A particular |
|
|
Information: |
|||||
|
name; |
details |
|
|
activity: crea- |
|
|
the patient’s |
||||
|
of treatment; |
|
|
tion of a pati- |
|
|
bill, used for |
|||||
|
cost of hospi- |
|
|
ent |
billing, |
|
|
billing the |
|
|||
|
tal room, me- |
|
|
which includes |
|
|
patient and |
|
||||
|
dicines, |
tests, |
|
|
a total bill and |
|
|
submission of |
||||
|
and professio- |
|
|
itemized expen |
|
|
claims |
to |
||||
|
nal care. |
|
|
|
ses. |
|
|
|
insurers |
|
||
|
|
|
|
|
|
|
|
|
|
|
|
|
|
|
|
|
|
|
|
|
|
|
|
|
|
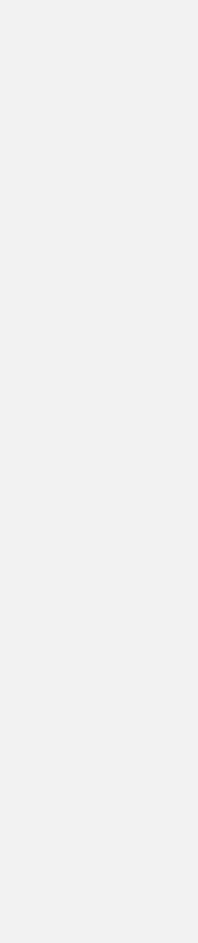
STRATEGIC COST MANAGEMENT AND THE VALUE CHAIN
How are the good and services that we all consume created? Usually many activities are involved in securing basic raw materials and turning them into valuable products of services. The set of linked, value-creating activities, ranging from securing basic raw materials and energy to the ultimate delivery of products and services, is called the value chain. Although there may be only one organization involved in a particular value chain, usually there are many. For example, Olympia Regional Hospital’s value chain would include not only the hospital, but also the suppliers of pharmaceutical products and medical suppliers, the manufacturers of diagnostic equipment, the private-practice physicians whose patients use Olympia, and the ambulance services that transport patients to the hospital.
In order for any organization to most effectively achieve its goals, it is important for its managers to understand the entire value chain in which their organization participates. This understanding can help managers ask, and answer, important questions about their organization’s strategy. Should the company concentrate on only a narrow link in the value chain, such as manufacturing and assembly? Or should it expand in operational scope to include securing the raw materials or distributing the final product to end users? Are there opportunities to form beneficial linkages with suppliers, which come earlier in the value chain? Or with customers?
These questions involve fundamental, strategic issues about how an organization can best meet its goals. Although many factors affect such decisions, one important factor concerns the cost incurred in creating value in each link in the value chain. In order for a company to achieve a sustainable competitive advantage, it must either (1) perform one or more activities in the value chain at the same quality level as its competitors, but at a lower cost, or (2) perform its value chain activities at a higher quality level than its competitors, but at no greater cost. Understanding the value chain, and the factors that cause costs to be incurred in each activity in the value chain, is a crucial step in the development of a firm’s strategy. These cost-causing factors are called cost drivers, and we will have much more to say about them throughout the text. The overall recognition of the importance of cost relationships among the activities in the value chain, and the process of managing those cost relationships to the firm’s advantage, is called strategic cost management. Issues in strategic cost management will arise in a variety of contexts as we pursue our study of managerial accounting.
Theory of Constraints Along with a value-chain analysis, managers should carefully examine the chain of linked activities with a view toward identifying the constraints that prevent their organization from reaching a higher level of achievement. Sometimes called the theory of constraints, this approach seeks to
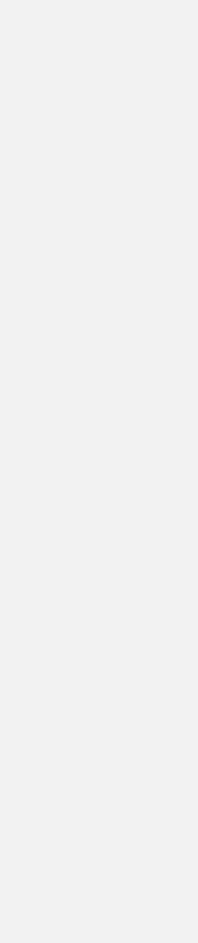
find the most cost-effective ways to alleviate an organization’s most limiting constraints. When binding constraints are relaxed, the organization can reach a higher level of goal attainment.
MANAGERIAL ACCOUNTING AS A CAREER
Managerial accountants serve a crucial function in virtually any enterprise. As the providers of information, they are often in touch with the heartbeat of the organization. In most businesses, managerial accountants interact frequently with sales personnel, finance specialists, production people, and managers at all levels. To perform their duties effectively, managerial accountants must be knowledgeable not only in accounting but in the other major business disciplines as well. Moreover, strong oral and written communication skills are becoming increasingly important for success as a managerial accountant.
Professional Organizations
To keep up with new developments in their field, managerial accountants often belong to one or more professional organizations. The largest of these is the Institute of Management Accountants (IMA). The IMA publishes a monthly journal entitled Management Accounting, and it also has published many research studies on managerial accounting topics. Other professional organizations in which managerial accountants hold membership include the Financial Executives Institute, the American Institute of Certified Public Accountants, the Institute of Internal Auditors, and the American Accounting Association.
The primary professional association for managerial accountants in Canada is the Society of Management Accountants of Canada (La Societe des Comptables en Management du Canada). Great Britain’s main professional organization is the Institute of Chartered Management Accountants, and Australia’s organization is the Institute of Chartered Accountants in Australia. In all, over 75 countries have professional organizations for their practicing accountants.
Professional Certification
In keeping with the importance of their role and the specialized knowledge they must have, managerial accountants can earn a professional certification. In the United States, the IMA administers the Certified Management Accountant (CMA) program. The requirements for becoming Certified Management Accountant include meeting specified educational requirements and passing the CMA examination. In Canada, a managerial accountant may be certified as a Registered Industrial Accountant (RIA) by the Society of Management
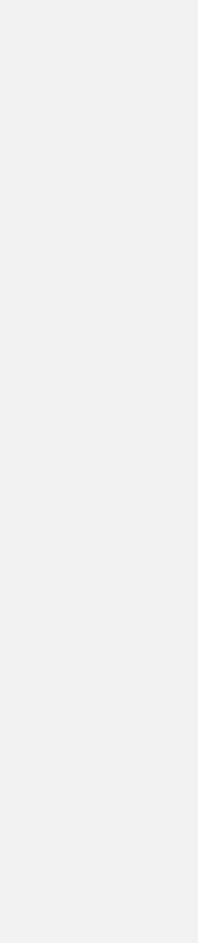
Accountants of Canada. Great Britain and many other countries also have professional certification programs for their managerial accountants.
Professional Ethics
As professionals, managerial accountants have an obligation to themselves, their colleagues, and their organizations to adhere to high standards of ethical conduct. In recognition of this obligation, the IMA (formerly called the National Association of Accountants) developed the following ethical standards for managerial accountants.
Competence managerial accountants have a responsibility to:
Maintain an appropriate level of professional competence by ongoing development of their knowledge and skills.
Perform their professional duties in accordance with relevant laws, regulations, and technical standards.
Prepare complete and clear reports and recommendations after appropriate analyses of relevant and reliable information.
Confidentiality Managerial accountants have a responsibility to:
Refrain from disclosing confidential confidential information acquired in the course of their work except when authorizes, unless legally obligated to do so.
Inform subordinates as appropriate regarding the confidentialily of information acquired in the course of their work and monitor or their activities to assure the maintenance of that confidentiality.
Refrain from using or appearing to use confidential information acquired in the course of their work for unethical or illegal advantage either personally or through third parties.
Integrity Managerial accountants have a responsibility to:
Avoid actual or apparent conflicts of interest and advise all appropriate parties of any potential conflict.
Refrain from engaging in any activity that would prejudice their ability to carry out their duties ethically.
Refuse any gift, favor, or hospitality that would influence or appear to influence their actions.
Refrain from either actively or passively subverting one attainment of the organization’s legitimate and ethical objectives.
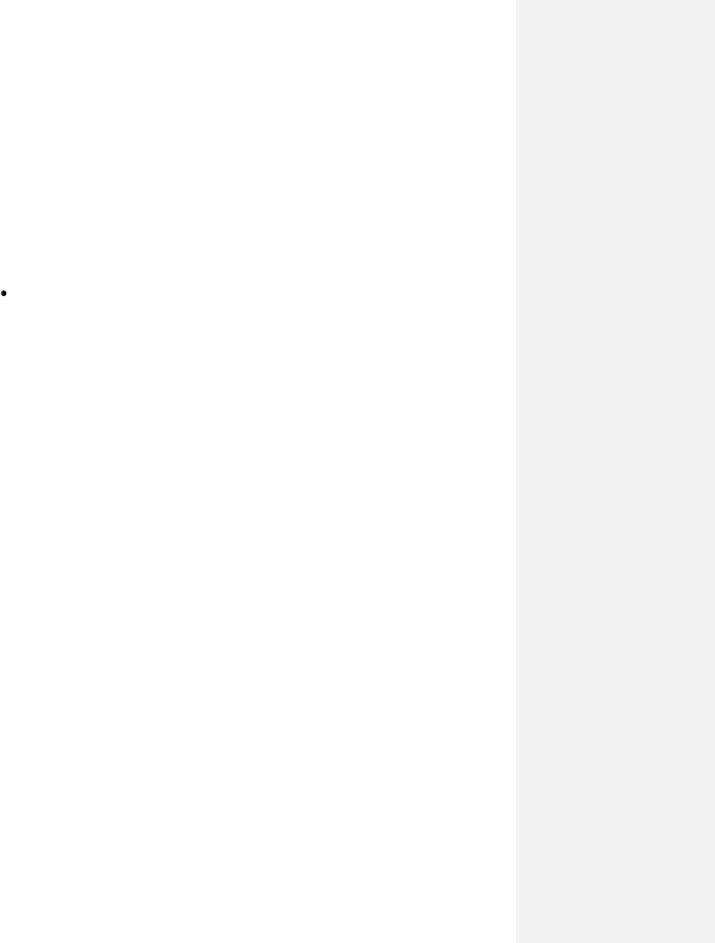
Recognize and communicate professional limitation or other constraints that would preclude responsible judgment or successful performance of an activity.
Communicate unfavorable as well as favorable information and professional judgments or opinions.
Refrain from engaging in or supporting any activity that would discredit the profession.
Objectivity managerial accountants have a responsibility to:
Communicate information fairly and objectively.
Disclose fully all relevant information that could reasonably be expected to influence an intended user’s understanding of the reports, comments, and recommendations presented.
In resolving an ethical problem, the managerial accountant should discuss the situation with his or her immediate supervisor, assuming that individual is not involved in the problem. If the supervisor is involved in the ethical problem, the accountant should discuss the matter with the next higher level of management.
SUMMARY
All organizations have goals, and their managers need information as they strive to attain those goals. Information is needed for the management functions of decision making, planning, directing operations, and controlling.
Managerial accounting is an important part of any organization’s management information system. The four objectives of managerial accounting activity are: (1) providing information for decision making and planning, (2) assisting managers in directing and controlling operations, (3) motivating managers towards the organization’s goals, and (4) measuring the performance of managers and subunits within the organization.
Managerial accounting differs from financial accounting in several ways. The users of managerial accounting information are managers inside the organization. Managerial accounting information is not mandatory, is unregulated, and draws on data from the basic accounting system as well as other data sources. The users of financial accounting information are interested parties outside the organization, such as investors and creditors. Financial accounting information is required for publicly held companies, is regulated by the Financial Accounting Standards Board, and is based almost entirely on historical transaction data.
Managerial accounting is a profession with a certification process and a code of ethical standards. Managerial accountants are highly trained professionals, who can contribute significantly to the success of any enterprise.
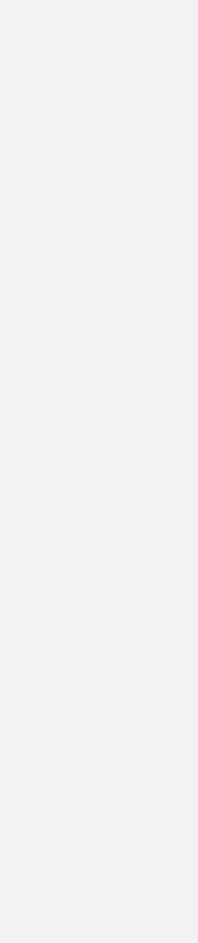
KEY-TERMS |
|
|
Activity accounting |
Cost driver |
Line positions |
Activity-based costing |
Cost management |
Managerial accounting |
(ABC) |
system |
Non-value-added costs |
Attention-directing |
Database manage- |
Planning |
function |
ment system |
Staff positions |
Certified Management |
Decision making |
Strategic cost mana- |
Accountant (CMA) |
Decision support |
gement |
Controller or (compt- |
system |
System |
roller) |
Directing operations |
Treasurer |
Controlling |
Financial accoun- |
Value chain |
Cost accounting system |
ting |
|
|
Internal auditor |
|
|
Just-in-Time (JIT) |
|
|
production system |
|
REVIEW QUESTIONS |
|
|
1 – List and define the four basic management activities.
2 – List and describe four important differences between managerial and financial accounting .
3 – Distinguish between cost accounting and managerial accounting.
4 – Distinguish between line and staff positions.
5 – Distinguish between the following two accounting positions: controller and treasurer.
6 – What is meant by the following statement? “Managerial accounting often serves an attention-directing role”.
7 – What is the chief difference between manufacturing and service industry firms?
8– Define the following terms: just-in-time, cost management system, non- value-added costs, system and decision support system.
9– Define and explain the significance of the term CMA.
10– Briefly explain what is meant by each of the following ethical standards for managerial accountants: competence, confidentiality, integrity, and objectivity.
11– Can a managerial accountant play an important role in a nonprofit organization? Explain your answer.
12– What do you think it means to be professional? In your view, are managerial accountants professionals?
13– Define the term strategic cost management.
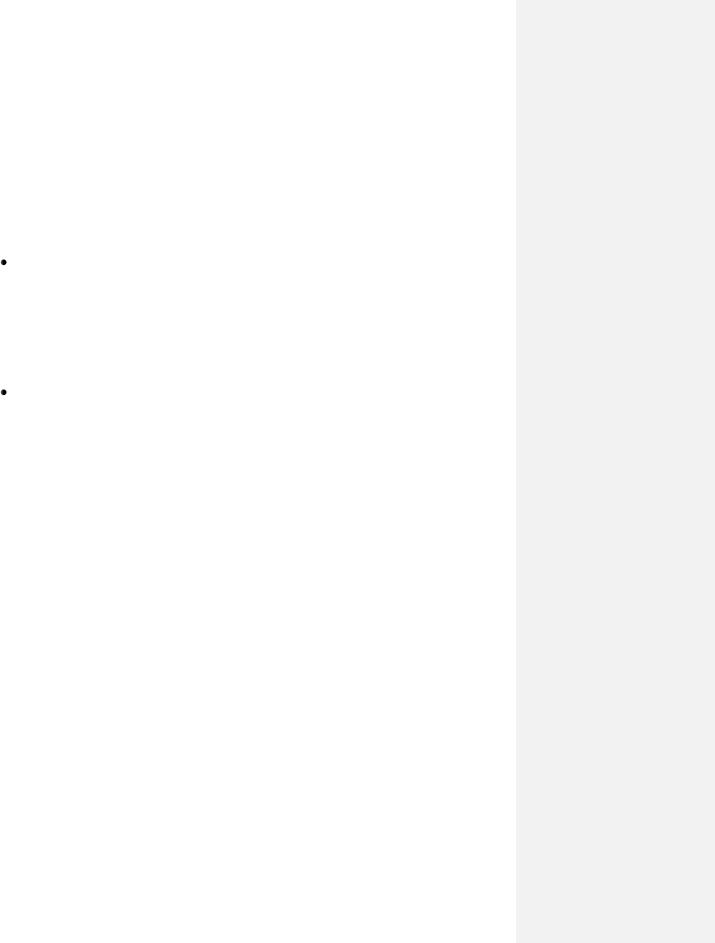
UNIT 2
BASIC COST TERMS AND CONCEPTS
After completing this unit, you should be able to:
Explain what is meant by “different costs for different purposes”.
Describe the behavior of variable and fixed costs, both in total and on a per-unit basis.
Understand the concept of a cost driver and the importance of identifying an organization’s cost drivers.
Distinguish between direct and indirect costs and controllable and uncontrollable costs.
Distinguish between product costs, period costs, and expenses.
Give examples of merchandise costs, marketing costs, administrative costs, research and development costs, and three types of manufacturing costs.
Describe the role of costs on the income statement and balance sheet of a merchandising company, a manufacturing company, and a service industry firm.
Prepare a schedule of cost of goods manufactured, a schedule of cost of goods sold, and an income statement for a manufacturer.
Define and give examples of an opportunity cost, an out-of-pocket cost, a sunk cost, a differential cost, a marginal cost, and an average cost.
Explain the behavioral tendencies many people show when they encounter opportunity costs and sunk costs.
The process of management involves planning, control, and decision making. Managers can perform each of these functions more effectively with information provided by managerial accountants. Much of this information focuses on the costs incurred in the organization. Foe example, in planning the routes and flight schedules of American Airlines, managers must consider aircraft fuel costs, salaries of flight crews, and airports landing fees. Controlling the costs of manufacturing personal computers requires that Hewlett-Packard’s accountants carefully measure and keep track of production costs. In making decisions about tuition and admission requirements, a university’s board of trustees must have information about the costs of providing educational services.
Each of these examples focuses on costs of one types or another. An important first step in studying managerial accounting is to gain an understanding of the various types of costs incurred by organizations. In this
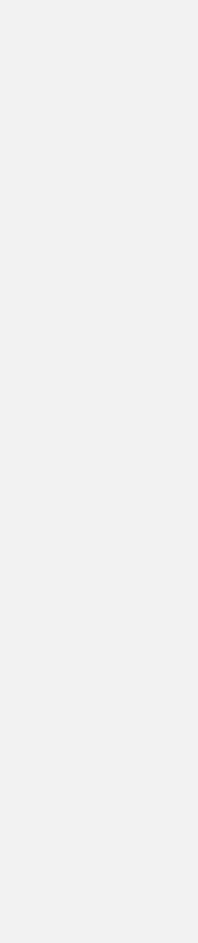
chapter, we will study the cost terms, concepts, and classifications routinely used by managerial accountants.
COST CLASSIFICATIONS: DIFFERENT COSTS FOR DIFFERENT PURPOSES
The world cost can have different meanings depending on the context in which it is used. Cost data that are classified and recorded in a particular way for one purpose may be inappropriate for another use. For example, the costs incurred in producing gasoline last year are important in measuring Exxon’s income for the year. However, those costs may not be useful in planning the company’s refinery operations for the next year if the cost of oil has changed significantly or if the methods of producing gasoline have improved. The important point is that different cost concepts and classifications are used for different purposes. Understanding these concepts and classifications enables the managerial accountant to provide appropriate cost data to the managers who need it.
Fixed and Variable Costs
One the most important cost classifications involves the way a cost changes in relation to changes in the activity of the organization. Activity refers to a measure of the organization’s output of products or services. The number of automobiles manufactured by General Motors, the number of days of patient care provided by Massachusetts General Hospital, and the number of insurance claims settled by Allstate are all measures of activity. The activities that cause costs to be incurred are called cost drivers.
Variable Costs A variable cost changes in total in direct proportion to a change in the level of activity (or cost driver). If activity increases by 20 percent, total variable cost increases by 20 percent also. For example, the cost of sheet metal used by Chrysler will increase by approximately 5 percent if automobile production increases by 5 percent. The cost of napkins and other paper products used at a Pizza Hut will increase by roughly 10 percent if the restaurant’s patronage increases by 10 percent.
Fixed Costs A fixed cost remains unchanged in total as the level of activity (or cost driver) varies. If activity increases or decreases by 20 percent, total fixed cost remains the same. Examples of fixed costs include depreciation of plant and equipment at a Texas Instruments factory, the cost of property taxes at a Ramada Inn, and the salary of a subway driver employed by the New York Transit Authority.
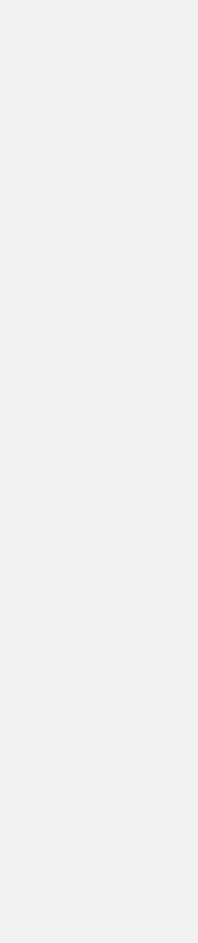
To summarize, as the activity level increases, total fixed cost remains constant but unit fixed cost declines. It is vital in managerial accounting to thoroughly understand the behavior of both total fixed costs and unit fixed costs.
Identifying Cost Drivers
An important first step in understanding the cost behavior in any organization is identifying the cost drivers upon which various types of costs depend. A cost driver is any event or activity that causes costs to be incurred. In most organizations different types of costs respond to widely differing cost drivers. For example, in a manufacturing firm the cost of assembly labor would be driven by the quantity of products manufactured as well as the number of parts in each product. In contrast, the cost of machine setup labor would be driven by the number of production runs. The cost of material-handling labor would be driven by material-related factors such as the quantity and cost of raw material used, the number of parts in various products, and the number of rawmaterial shipments received. Thus, it may be an oversimplification to lump all manufacturing labor costs together and say that they are driven by the quantity of products manufactured. In state-of-the-art cost management systems, accountants are careful to separate various types of costs into different cost pools and identify the most appropriate cost driver for each cost pool.
In identifying a cost driver, the managerial accountant should consider the extent to which a cost or pool of costs varies in accordance with the cost driver. The higher the correlation between the cost and the cost driver, the more accurate will be the resulting understanding of cost behavior. Another important consideration is the cost of measuring the cost driver. Thus, there is a costbenefit trade-off in the identification of cost drivers. As the number of cost drivers used in explaining an organization’s cost behavior increases, the accuracy of the resulting information will increase. However, the cost of the information will increase also. The concept of a cost driver will be an important aspect of many of the topics discussed in subsequent chapters. The following example illustrate the use of cost drivers in the service sector.
ILLUSTRATION FROM MANAGEMENT ACCOUNTING PRACTICE
COST DRIVERS IN THE AIRLINE INDUSTRY
A recent study of the U.S. airline industry revealed that two distinct types of cost drivers have significant effects on an airline’s costs. Volume-based cost drivers include (1) aircraft capacity, including both passenger and cargo capacity, and (2) number of passengers. Operations-based cost drivers include the following characteristics of an airline’s operations: (1) product-line diversity, as measured by route density – “by increasing the number of flights over its
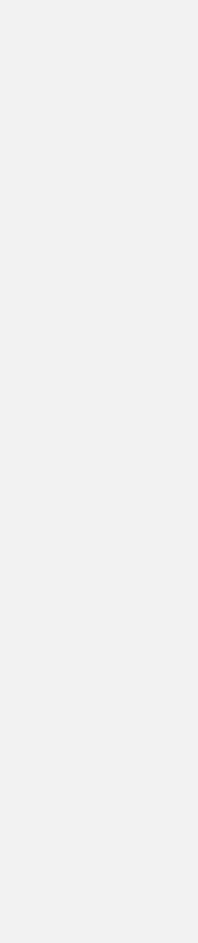
network, a carrier is offering a more diversified set of services”; (2) degree of hub concentration, which refers to the extent to which an airline structures its
“route systems so that many flights arrive and depart hubs within a few hours of each other, with passengers and cargo exchanging planes in between” and (3) hub domination, which is the extent to which an airline is able to monopolize, and thus control, the facilities and services at its hub airports.
Direct and Indirect Costs
An important objective of managerial accounting is to assist managers in controlling costs. Sometimes cost control is facilitated by tracing costs to the department or work center in which the cost was incurred. Such tracing of costs to departments is known as responsibility accounting. A cost that can be traced to a particular department is called a direct cost of the department. For example, the salary of an auto mechanic is a direct cost of the automotive service department in a Sears department store. The cost of paint used in the painting department of a Toyota plant is a direct cost of the painting department.
A cost that is not directly traceable to a particular department is called an indirect cost of the department. The costs of national advertising for Walt Disney World are indirect costs of each of the departments or subunits of the recreational complex, such as the Magic Kingdom and Epcot Center. The salary of a General Electric Company plant manager is an indirect cost of each of the plant’s production departments. The plant manager’s duties are important to the smooth functioning of each of the plant’s departments, but there is no way to trace a portion of the plant manager’s salary cost to each department.
Whether a cost is a direct cost or an indirect cost of a department often depends on which department is under consideration. A cost can be a direct cost of one department or subunits in the organization but an indirect cost of other departments. While the salary of the General Electric Company plant manager is an indirect cost of the plant’s departments, the manager’s salary is a direct cost of the plant.
An important objective of a cost management system is to trace as many costs as possible directly to the activities that cause them to be incurred. Sometimes called activity accounting, this process is vital to management’s objective of eliminating non-value-added costs. There are costs of activities that can be eliminated without deterioration of product quality, performance, or perceived value.
Controllable and Uncontrollable Costs
Another cost classification that can be helpful in cost control involves the controllability of a cost item by a particular manager. If a manager can control or heavily influence the level of a cost, then that cost is classified as a controllable
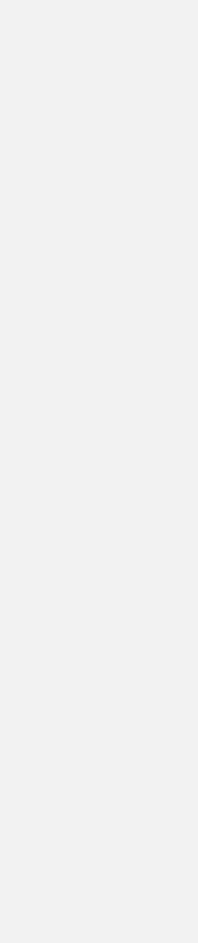
cost of that manager. Costs that a manager cannot influence significantly are classified as uncontrollable costs of that manager. Many costs are not completely under the control of any individual. In classifying costs as controllable or uncontrollable, managerial accountants generally focus on a manager’s ability to influence costs. The question is not, Who controls the cost? But, Who is in the best position to influence the level of a cost item? Exhibit 2-1 lists several cost items along with their typical classification as controllable or uncontrollable.
Some costs may be controllable in the long run but not on the short run. For example, the long-term costs associated with computing equipment leased by a hospital are controllable when the 10-year lease is negotiated. In the short run, however, after the lease is signed, the rental costs are uncontrollable until the lease period ends.
Manufacturing Costs
To assist managers in planning and cost control, managerial accountants classify costs by the functional area of the organization to which the costs relate. Some examples of functional areas are manufacturing, service production, merchandise, marketing, administration, and research and development.
Exhibit 2-1. Controllable and Uncontrollable Costs
|
Cost Item |
|
Manager |
|
Classification |
||||
Cost of raw material used |
Supervisor |
|
of |
the |
Controllable (Quantity is |
||||
to produce circuit boards |
production |
department |
controllable, but the price |
||||||
in a Hewlett-Packard |
for circuit boards |
|
probably is not) |
||||||
factory |
|
|
|
|
|
|
|
|
|
Cost of food used in a |
Restaurant manager |
|
Controllable (Quantity is |
||||||
McDonald’s restaurant |
|
|
|
|
|
|
controllable, but the price |
||
|
|
|
|
|
|
|
|
|
probably is not) |
Cost |
of |
national |
Manager |
of |
the |
Hertz |
Uncontrollable |
||
advertising for the Hertz |
rental |
agency |
at |
the |
|
||||
car rental company |
Syracuse airport |
|
|
||||||
Cost |
of |
national |
Manager |
of |
a |
Penney’s |
Uncontrollable |
||
accounting |
and data |
store |
in |
|
Gainesville, |
|
|||
processing operations for |
Florida |
|
|
|
|
|
|
||
Penney’s |
|
|
|
|
|
|
|
|
Manufacturing costs are further classified into the following three categories: direct material, direct labor, and manufacturing overhead.
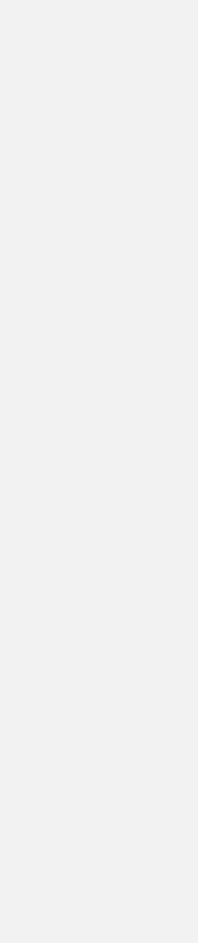
Direct Material Raw material that is consumed in the manufacturing process, is physically incorporated in the finished product, and can be traced to products conveniently is called direct material. Examples include the sheet metal in a general Electric refrigerator and the paper in a Sports Illustrated magazine.
Direct Labor The cost of salaries, wages and fringe benefits for personnel who work directly on the manufactured product is classified as direct-labor cost. Examples include the wages of personnel, such as employer-paid healthinsurance premiums and the employer’s pension contributions, should also be classified as direct-labor costs. Such costs are just as much a part of the employees’ compensation as are their regular wages. Although conceptually correct, this treatment of fringe benefits is not always observed in practice. Many companies classify all fringe-benefit costs as overhead, which is defined next.
Manufacturing Overhead All other costs of manufacturing are classified as manufacturing overhead, which includes three types of costs: indirect material, indirect labor, and other manufacturing costs.
Indirect Material The cost of materials that are required for the production process but do not become an integral part of the finished product are classified as indirect-material costs. An example is the cost of drill bits used in a metalfabrication shop. The drill bits wear out and are discarded, but they do not become part of the product. Materials that do become an integral part of the finished product but are insignificant in cost are also often classified as indirect material. Materials such as glue or paint may be so inexpensive that it is not worth tracing their cost to specific products as direct materials.
Indirect Labor The costs of personnel who do not work directly on the product, but whose services are necessary for the manufacturing process, are classified as indirect labor. Such personnel include production-department supervisors, custodial employees, and security guards.
Other Manufacturing Costs All other manufacturing costs that are neither material non labor costs are classified as manufacturing overhead. These costs include depreciation of plant and equipment, property taxes, insurance, and utilities such as electricity, as well as the costs of operating service departments. Service departments are those that do not work directly on manufacturing products but are necessary for the manufacturing process to occur. Examples include equipment-maintenance departments and computer-aided-design (CAD) department. In some manufacturing firms, departments are referred to as work centers.
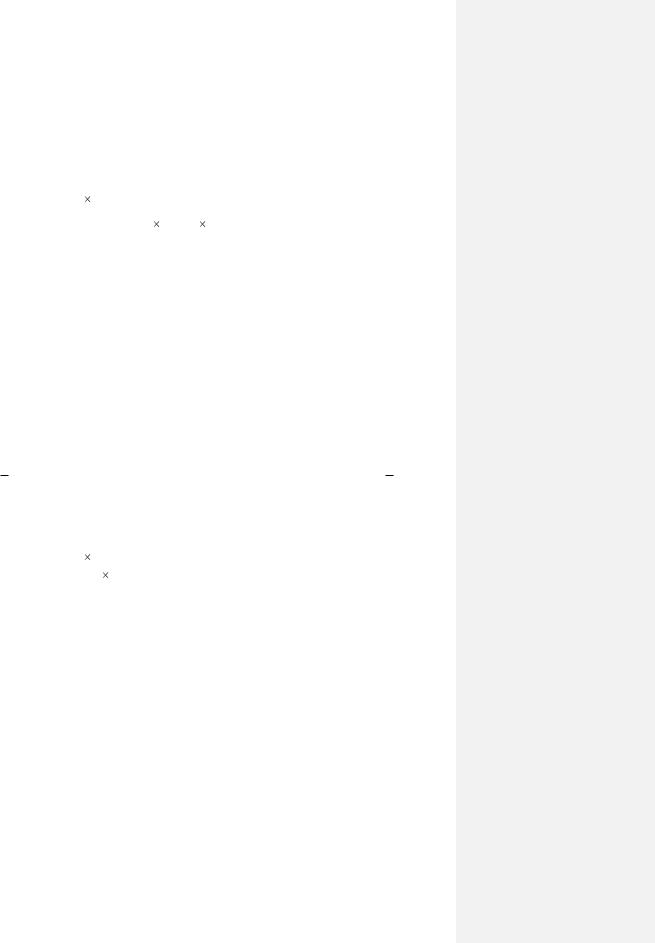
Other manufacturing overhead costs include overtime premiums and the cost of idle time. An overtime premium is the extra compensation paid to an employee who assembles radios earns $16.00 per hour. The technician works 48 hours during a week instead of the scheduled time of 40 hours. The overtime pay scale is time and a half, or 150 percent of the regular wage. The technician’s
compensation for the |
week is classified as follows: |
|
|||
Direct-labor cost ($16 |
48) ........................................................... |
|
|
$768 |
|
Overhead (overtime premium: |
1 |
$16 8) ................................. |
64 |
||
2 |
|||||
|
|
|
|
||
Total compensation paid ................................................................. |
|
|
$832 |
Only the extra compensation of $8 per hour is classified as overtime premium. The regular wage of $16 per hour is treated as direct labor, even for the eight hours worked on overtime.
Idle time is time that is not spent productively by an employee due to such events as equipment breakdowns or new setups of production runs. Such idle time is an unavoidable features of most manufacturing processes. The cost of an employee’s idle time is classified as overhead so that it may be spread across all production jobs, rather than being associated with a particular production job. Suppose that during one 40-hour shift, a machine breakdown resulted in idle
time of 1 12 hours and a power failure idled workers for an additional 12 hour. If
an employee ears $14 per hour, the employee’s wages for the week will be classified as follows:
Direct-labor cost ($14 38) .............................................................. |
$532 |
Overhead (idle time: $14 2) .......................................................... |
28 |
Total compensation paid ................................................................... |
$560 |
Both overtime premiums and the cost of idle time should be classified as manufacturing overhead, rather than associated with a particular production job, because the particular job on which idle time or overtime may occur tends to be selected at random. Suppose several production jobs are scheduled during an eight-hour shift, and the last job remains unfinished at the end of the shift. The overtime to finish the last job is necessitated by all of the jobs scheduled during the shift, not just the last one. Similarly, if a power failure occurs during one of several production jobs, the idle time that results is not due to the job that happens to be in process at the time. The power failure is a random event, and the resulting cost should be treated as a cost of all of the department’s production.
To summarize, manufacturing costs include direct material, direct labor, and manufacturing overhead. Direct labor and overhead are often called conversion
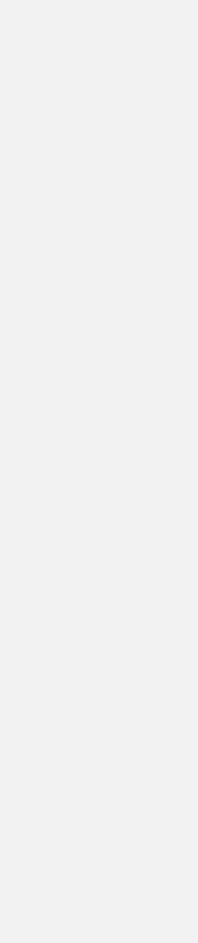
costs, since they are the costs of “converting” raw material into finished products. Direct material and direct labor are often referred to as prime costs.
Changing Cost Structures An organization’s cost structure refers to the relative proportion of its variable and fixed costs. As manufacturing firms move toward computer-integrated manufacturing systems, their cost structures are shifting toward proportionately greater fixed costs. In such highly automated manufacturing environments, variable costs such as direct labor constitute a much lower proportion of total manufacturing cost than in the past. Fixed costs, such as depreciation of computer and robotic equipment, occupy a much larger proportion of production costs.
Production Costs in Service Industry Firms and Nonprofit
Organizations
Service industry firms and many nonprofit organizations are also engaged in production. What distinguishes these organizations from manufacturers is that a service is consumed as it is produced, whereas a manufactured product can be stored in inventory. Such businesses as hotels, banks, airlines, professional sports franchises, and automotive repair shops are in the business of producing services. Similarly, nonprofit organizations such as the American Red Cross or the Greater Miami Opera Association also are engaged in service production. While less commonly observed in service firms, the same cost classifications used in manufacturing companies can be applied. For example, an airline produces air transportation services. Direct material includes such costs as jet fuel, aircraft parts, and food and beverages. Direct labor includes the salaries of the flight crew and the wages of aircraft-maintenance personnel. Overhead costs include depreciation of baggage handling equipment, insurance, and airport landing fees.
The process of recording and classifying costs is important in service industry firms and nonprofit organizations for the same reasons as in manufacturing firms. Cost analysis is used in pricing banking and insurance services, locating travel and car-rental agencies, setting enrollment targets in universities, and determining cost reimbursements in hospitals. As such organizations occupy an ever-growing role in our economy, applying managerial accounting to their activities will take on ever-greater importance.
ILLUSTRATION FROM MANAGEMENT ACCOUNTING PRACTICE
ARNOT OGDEN MEMORIAL HOSPITAL
An article in Business Week reported that hospitals now track costs patient by patient, doctor by doctor, and disease by disease. Hospitals
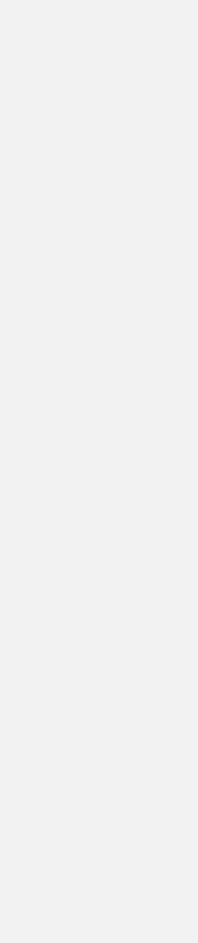
employ computerized databases to help them organize and maintain the data they need to make cost-effective decisions in treating patients. For example, at Arnot Ogden Memorial Hospital in Elmira, New York, when a pharmacist fills a prescription the data also are entered directly into the patient’s computer file. Doctors also can place information on a patient’s treatment directly into the patient’s file. As a result, the hospital’s accounting department can immediately determine the cost of a patient’s treatment. Similarly, the hospital’s accounting personnel can track treatment costs for each type of disease and each doctor who uses the hospital.
Nonmanufacturing Costs
Many other functional cost classifications are used besides manufacturing costs. Four of the most important ones are:
1.Merchandise costs
2.Marketing costs
3.Administrative costs
4.Research and development cost
Merchandise costs are the costs incurred by retailers and wholesale firms to acquire merchandise for resale. Merchandise costs include the purchase cost of the goods plus transportation costs.
Marketing costs include the costs of selling goods or services and the costs of distribution. Selling costs (or order-getting costs) include salaries, commissions and travel costs of sales personnel, and the costs of advertising and promotion. Distribution costs (or order-filling costs) refer to the costs of storing, handling, and shipping finished products.
Administrative costs refer to all costs of running the organization as a whole. The salaries of top-management personnel and the costs of the accounting, legal, and public relations activities are examples of administrative costs.
Research and development costs include all costs of developing new products and services. Such costs are becoming increasingly important as international competition increases and as high-technology firms make up a growing segment of the economy. The costs of running laboratories, building prototypes of new products, and testing new products are all classified as research and development (or R&D) costs.
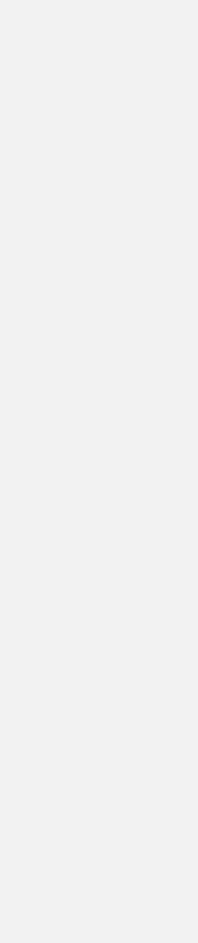
Product Costs, Period Costs, and Expenses
An important issue in both managerial and financial accounting is the timing with which the costs of acquiring assets or services are recognized as expenses. An expense is defined as the cost incurred when an asset is used up or sold for the purpose of generating revenue. The terms product cost and period cost are used to describe the timing with which various expenses are recognized.
A product cost is a cost assigned to goods that were either purchased or manufactured for resale. The product cost is used to value the inventory of manufactured goods or merchandise until the goods are sold. In the period of the sale, the product costs are recognized as an expense called cost of goods sold. The product cost of merchandise inventory acquired by a retailer or wholesaler for resale consists of the purchase cost of the inventory plus any shipping charges. The product cost of manufactured inventory consists of direct material, direct labor, and manufacturing overhead.
Another term for product cost is inventoriable cost, since a product cost is stored as the cost of inventory until the goods are sold. In addition to retailers, wholesalers, and manufacturers, the concept of product cost is relevant to other producers of inventoriable goods. Agricultural firms, lumber companies, and mining firms are examples of nonmanufacturers that produce inventoriable goods. Apples, timber, coal, and other such goods are inventoried at their product cost until the time period during which they are sold.
All costs that are not product costs are called period costs. These costs are identified with the period of time in which they are incurred rather than with units of purchased or produced goods. Period costs are recognized as expenses during the time period in which they are incurred. All research and development, marketing, and administrative costs are treated as period costs. This is true in manufacturing, retail, and service industry firms. Examples of period costs are salaries of sales personnel, advertising expenditures, depreciation of office equipment, salaries of top management, and the costs of running productresearch proframs.
Balance Sheet
Since retailers, wholesalers, and manufacturers sell inventoriable products, their balance sheets are also affected by product costs. Exhibit 2-2 displays the current assets section from recent balance sheet of H.J.Heinz and Wal-Mart. Included in the current-assets section of each of these balance sheets in inventory. Manufacturers, such as H.J. Heinz, have three types of inventory. Raw-materials inventory includes all materials before they are placed into production. Work-in-process inventory refers to manufactured products that are only partially completed at the date when the balance sheet is prepared. Finished-goods inventory refers to manufactured goods that are complete and
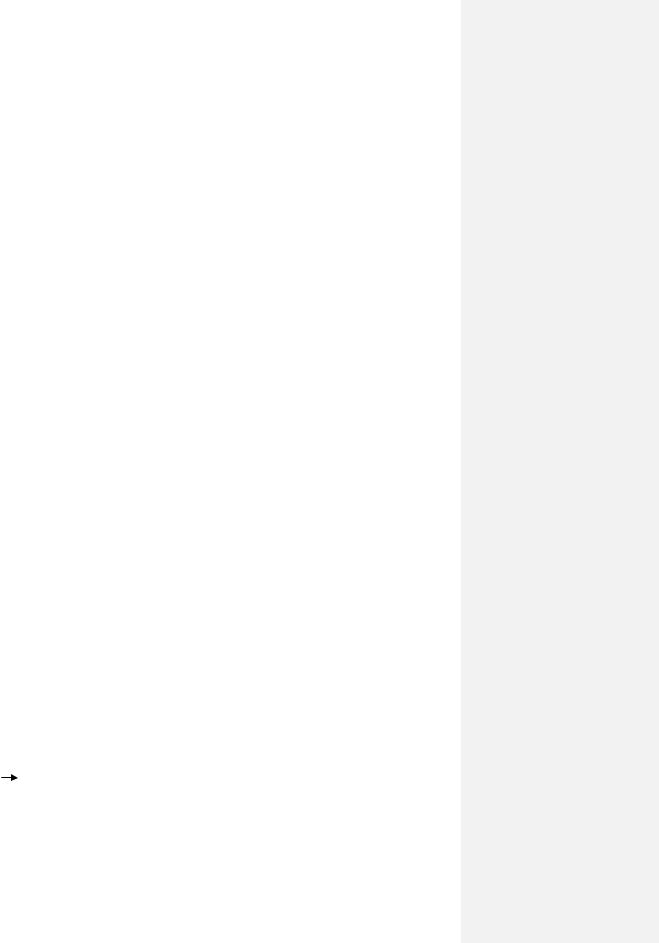
ready for sale. The values of the work-in-process and finished-goods inventories are measured by their product costs.
On the Wal-Mart balance sheet, the cost of acquiring merchandise is listed as the value of the merchandise inventories.
COST FLOWS IN A MANUFACTURING COMPANY
Direct material, direct labor, and manufacturing overhead are the three types of production costs incurred by manufacturers. These costs are product costs because they are stored in inventory until the time period when the manufacturer’s products are sold. Manufacturers have product costing systems to keep track of the flow of these costs from the time production begins until finished products are sold. This flow of manufacturing costs is depicted in Exhibit 2-3. As direct material is consumed in production, its cost is added to work-in-process inventory. Similarly, the costs of direct labor and manufacturing overhead are accumulated in work in process. When products are finished, their costs are transferred from work-in-process inventory to finishedgoods inventory. The costs then are stored in finished goods until the time period when the products are sold. At that time, the product costs are transferred from finished goods to cost of goods sold, which is an expense of the period when the sale is made. Exhibit 2-3 concentrates on the conceptual basis of a product costing system.
Manufacturers generally prepare a schedule of cost of goods manufactured and a schedule of cost of goods sold to summarize the flow of manufacturing costs during an accounting period. These schedules are intended for internal use by management and are generally not made available to the public.
Exhibit 2-2. Partial Balance Sheets for a Manufacturer and a Retailer (all figures in thousands of dollars)
H.J. Heinz Company
Partial Balance Sheet for a Recent Year
|
Current assets: |
|
|
Cash and cash equivalents ................................ |
$ 150,979 |
Value |
Short-term investments ..................................... |
162,985 |
measured |
Accountants receivable (net) ............................ |
678,109 |
by product |
Inventories: |
|
costs |
Finished goods and work in process ................ |
677,599 |
|
Raw material (packaging material |
|
|
and ingredients) .............................................. |
290,260 |