
- •ORGANIZATIONS AND THEIR GOALS
- •THE MANAGEMENT PROCESS
- •Decision Making
- •Accounting System
- •Cost Accounting System
- •MANAGERIAL ACCOUNTING
- •FINANCIAL ACCOUNTING
- •Managers at all levels
- •Counsel
- •Treasurer
- •Personnel Director
- •Chief of
- •Chief of
- •Surgery
- •Chief of
- •Director of
- •Director of
- •Chief of Medical
- •Chief of
- •Internal
- •Chief of
- •Chief of
- •Production
- •Stage 1
- •Production
- •Stage II
- •Input
- •Process
- •Output
- •A particular
- •Work-in- Process
- •Inventory
- •Cost of
- •until the
- •Cost
- •Cost
- •Cost
- •Costs
- •Simplified decision
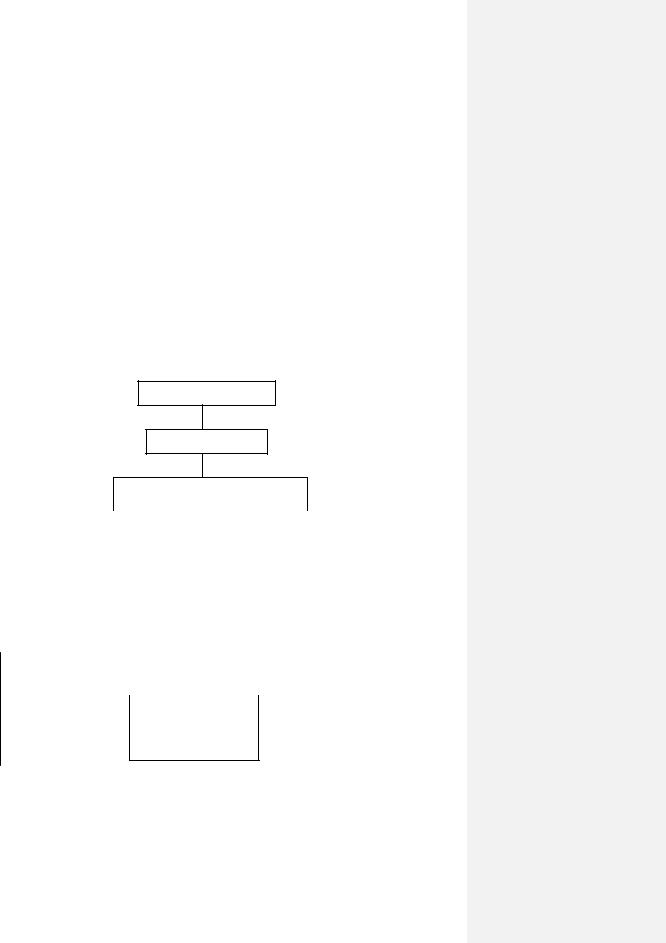
alternative. Often, that information is also intended to influence the manager’s decision.
To illustrate, let us consider Olympia Regional Hospital’s annual budget.
Although the budget is prepared under the direction of the controller, it must be approved by the hospital’s administrator and, ultimately, by the board of trustees. As part of the budget approval process, the administrator and the trustees will make important decisions that determine how the hospital’s resources will be allocated. Throughout the year, the decisions of management will be facilitated by the information contained in the budget. Management decisions also will be influenced by the budget, since at year-end actual expenditures will be compared with the budgeted amounts. Explanations will then be requested for any significant deviations.
Exhibit 1-3. Organization Chart for Olympia Regional Hospital
Board of Trustees
Administrator
Deputy of Administrator
|
|
|
|
|
|
|
|
|
|
|
|
|
|
|
|
|
|
|
|
|
|
|
|
|
|
|
|
|
|
|
|
|
|
|
|
|
|
|
|
|
|
|
|
|
|
|
|
|
|
|
|
|
Counsel |
|
|
Personnel Director |
|
|
|
Controller |
|
Treasurer |
|||||||||||||||
|
|
|
|
|
|
|
|
|
|
|
|
|
|
|
|
|
|
|
|
|
|
|
|||
|
|
|
|
|
|
|
|
|
|
|
|
|
|
|
|
|
|
||||||||
|
|
|
|
|
|
|
|
|
|
|
|
|
|
|
|
|
|
|
|
|
|||||
Chief of |
|
|
Chief of |
|
|
Chief of |
|
|
Director of |
|
|
Director of |
|
||||||||||||
Physician |
|
|
Surgery |
|
|
Nurses |
|
|
Admissions and |
|
|
Purchasing, |
|
||||||||||||
|
|
|
|
|
|
|
|
|
|
|
|
|
|
|
Patient Records |
|
|
Housekeeping |
|
||||||
|
|
|
|
|
|
|
|
|
|
|
|
|
|
||||||||||||
|
|
|
|
|
|
|
|
|
|
|
|
|
|
|
|
|
|
|
|
|
|
and Facilities |
|
||
|
|
|
|
|
|
|
|
|
|
|
|
|
|
|
|
|
|
|
|
|
|
||||
|
|
|
|
|
|
|
|
|
|
|
|
|
|
|
|
|
|
|
|
|
|
|
|
|
|
|
|
|
|
|
|
|
|
|
|
|
|
|
|
|
|
|
|
|
|
|
|
|
|
|
|
Chief of Medical
Support
Services
|
|
|
|
|
|
|
|
|
|
|
|
|
|
|
|
|
|
|
|
|
|
|
|
|
|
|
|
|
|
|
|
|
|
|
|
Chief of |
|
Chief of |
|
Chief of |
|
Supervisor |
|
Supervisor |
|
Supervisor |
|||||||
Internal |
|
Orthope |
|
Pediatrics |
|
of Radio- |
|
of Dieteti- |
|
of Diagno |
|||||||
Medicine |
|
dics |
|
|
|
|
logy |
|
cs |
|
stic Labo- |
||||||
|
|
|
|
|
|
||||||||||||
|
|
|
|
|
|
|
ratory |
||||||||||
|
|
|
|
|
|
|
|
|
|
|
|
|
|
|
|
||
|
|
|
|
|
|
|
|
|
|
|
|
|
|
|
|||
|
|
|
|
|
|
|
|
|
|
|
|
|
|
|
|
|
|
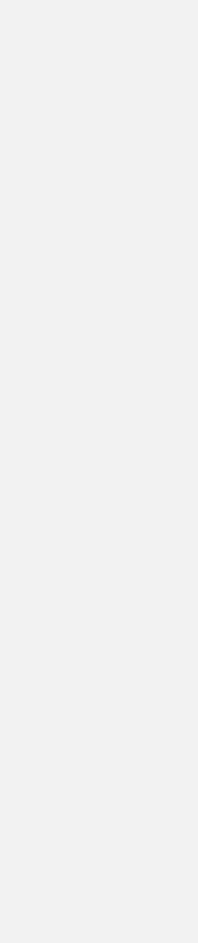
Exhibit 1-4. Controller versus Treasurer at Olympia Regional Hospital
|
|
Controller |
|
Treasurer |
|
1) |
Supervises |
the |
accounting |
1) Manages relationships with donors, |
|
department |
|
|
|
creditors, investors, and government |
|
|
|
|
|
|
agencies that provide financial support |
2) |
Prepares all reports for external |
2) Maintains custody of cash and other |
|||
parties (financial accounting) |
assets |
||||
3) Prepares all reports and information |
3) Manages investments |
||||
for |
internal |
users |
(managerial |
|
|
accounting) |
|
|
|
|
|
4) |
Assists line |
managers throughout |
4) Responsible for credit policy and |
||
the hospital |
in interpreting and using |
collection of accounts |
|||
managerial accounting information |
|
||||
5) |
Prepares |
reports |
required for |
5) manages the hospital’s insurance |
|
taxation and |
governmental reporting; |
coverage |
|||
advises management on tax-related |
|
||||
issues |
|
|
|
|
|
|
Behavioral Issues |
|
|
The reactions of both individuals and groups to managerial accounting information will significantly affect the course of events in an organization.
How will Olympia Regional Hospital’s chief of surgery react to a budget? How will data regarding the cost of providing radiological services affect the way the supervisor of radiology prices those services? How much detail should be included in the quarterly accounting reports to the administrator? If too much detail is provided, will the administrator be overloaded with information and distracted from the main points?
All of these questions involve the behavioral tendencies of people and their cognitive limitations in using information. The better a managerial accountant’s understanding of human behavior is, the more effective he or she will be as a provider of information.
Costs and Benefits
Information is a commodity, much like wheat or corn. Like other goods, information can be produced, purchased and consumed. It can be of high or low quality, timely or late, appropriate for its intended use or utterly irrelevant. As is true of all goods and services, information entails both costs and benefits. The costs of providing managerial accounting information to the managers in
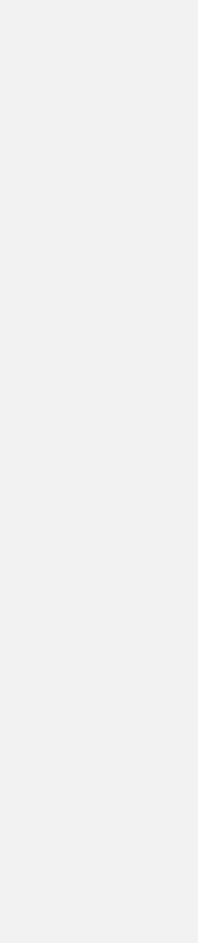
Olympia Regional Hospital include the cost of compensation for the controller and Accounting Department personnel, the cost of purchasing and operating computers, and the cost of the time spent by the information users to read, understand and utilize the information. The benefits include improved decisions, more effective planning, greater efficiency of operations at lower costs, and better direction and control of operations.
Thus, there are both costs and benefits associated with managerial accounting information. The desirability of any particular managerial accounting technique or information must be determined in light of its costs and benefits. We will reinforce this cost-benefit trade-off throughout the text by pointing out areas where management accounting it. Information could be improved, but only at too great a cost.
Evolution and Adaptation in Managerial Accounting
Compared to financial accounting, managerial accounting is a young discipline. As a result, managerial accounting concepts and tools are still evolving as new ways are found to provide information that assists management. Moreover, the business environment is changing rapidly. For managerial accounting to be as useful a tool in the future as it has been in the recent past, managerial accounting information must be adapted to reflect those changes. Several changes in the business environment that are especially pertinent to managerial accounting are discussed briefly here. The effect of these changes on various topics in managerial accounting will be explored in subsequent chapters.
Service versus Manufacturing Firms The service sector occupies a growing role in the United States economy. As more and more companies provide financial, medical, communication, transportation, consulting, and hospitality services, managerial accounting techniques must be adapted to meet the needs of managers in those industries. The key difference between service and manufacturing firms is that most services are consumed as they are produced. Services cannot be inventoried like manufactured goods. Service organizations also tend to be more labor intensive than manufacturing firms. Many of the techniques developed for measuring costs and performance in manufacturing companies have been adapted successfully to service industry firms. Throughout the text, you will notice that roughly two-thirds of the illustrations of managerial accounting techniques involve service industry firms and nonprofit organizations.
Emergence of New Industries Scientific discoveries are opening up whole new industries that were not even contemplated a short time ago. Such discoveries as genetic engineering, superconductivity, and artificial hearts have spawned business activities in which managers face new challenges. Managerial
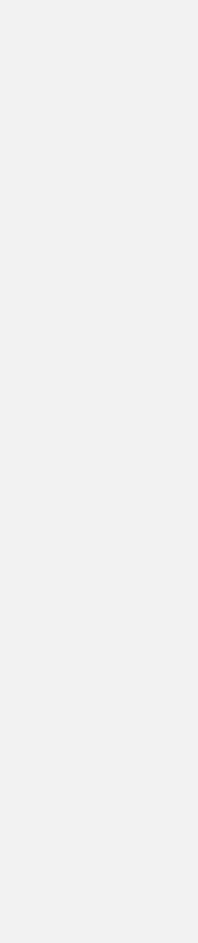
accountants face new challenges as they seek to provide relevant information in these new high-tech industries.
Globalism “It’s a small world!” Although this cliche has been around a long time, it concisely sums up today’s business environment. Nowadays the marketplace is truly a global one. A firm is just as likely to be in competition with a company from Japan, Germany, or Korea as its crosstown rival. Intense
international competition is forcing companies |
to |
strive for |
excellence in |
product quality and service more than ever before. |
|
|
|
Just-in-Time Inventory Management |
In |
traditional |
manufacturing |
settings, inventories of raw materials and parts, partially completed components, and finished goods were kept as a buffer against the possibility of running out of a needed item. In recent years, however, managers have come to realize that large buffer inventories are costly. They consume valuable resources and generate hidden costs. Consequently, many companies have completely changed their approach to production and inventory management. These manufacturers have adapted a new strategy for controlling the flow of manufacturing in a multistage production process. In a just-in-time (or JIT) production system, raw materials and parts are purchased or produced just in time to be used at each stage of the production process. This approach to inventory and production management brings considerable cost savings from reduced inventory levels.
The key to the JIT system is the “pull” approach to controlling manufacturing. To visualize this approach, look at Exhibit 1-5, which displays a simple diagram of multistage production process. The flow of manufacturing activity is depicted by the solid arrows running down the page from one stage of production to the next. However, the signal that triggers more production activity in each stage comes from the next stage of production. These signals, depicted by the dashedline arrows, run up the page. We begin with sales at the bottom of the exhibit. When sales activity warrants more production of finished goods, the goods are “pulled” from production stage III by sending a signal that more goods are needed. Similarly, when production employees in stage III need more inputs, they send a signal back to stage II. This triggers production activity in stage II. Working our way back up to the beginning of the process, purchases of raw materials and parts are triggered by a signal that they are needed in stage I. This pull system of production management, which characterizes the JIT approach, results in a smooth flow of production and significantly reduced inventory levels. The result is considerable cost savings for the manufacturer.
Further details of the JIT production system and other changes in the manufacturing environment will be covered in subsequent chapters. The impact of these changes will be a recurrent theme throughout the book.