
4201
.pdf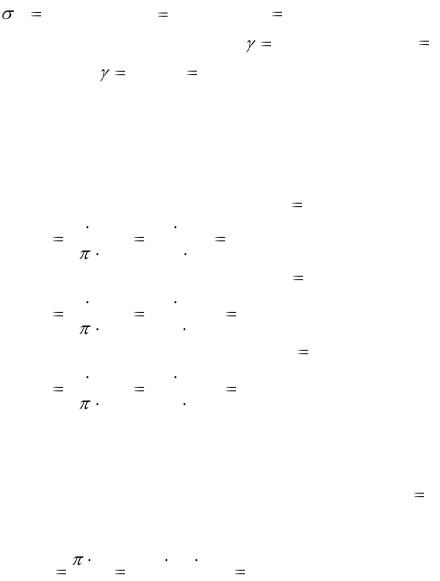
Продолжение приложения 3
ния, допускаемой прочностью механизма подач. При обработке стали проверку подачи производят после выбора режима резания по табл. 11
Выбор скорости резания
Исходя из принятой стойкости режущего инструмента и установленных значений глубин резания и подачи, а также учитывая механические свойства обрабатываемого материала, определяется нормативная скорость резания по таблицам. В них для каждого вида обрабатываемых материалов и применяемых режущих инструментов приводятся значения скорости резания.
|
По табл. 3 определяется скорость резания. Для обработки стали |
|||||||||
B |
72 кг/мм2 |
|
с t до 8 мм, S |
0,78 мм/об скорость резания для обра- |
||||||
|
|
|
|
|
|
|
|
|
|
|
ботки резцом с углом в плане |
450 |
составляет V 58 м/мин и для рабо- |
||||||||
ты с резцом |
900 , V |
51 м/мин. |
|
|||||||
|
|
Определение числа оборотов шпинделя в минуту |
||||||||
|
С учетом найденной скорости производится расчет числа оборотов |
|||||||||
шпинделя: |
|
|
|
|
|
|
|
|
||
|
а) для первого перехода, при D |
90 мм |
||||||||
|
n |
V 1000 |
58 100 |
|
205 об/мин; |
|||||
|
|
|
|
|
|
|
||||
|
D |
|
3,14 |
90 |
|
|||||
|
|
|
|
|
|
|
||||
|
б) для второго перехода, при D |
61,5 мм |
||||||||
|
n |
V 1000 |
51 1000 |
200 |
об/мин; |
|||||
|
|
|
|
|
|
|
||||
|
D |
|
3,14 |
81,5 |
||||||
|
|
|
|
|
|
|||||
|
в) для третьего перехода, при D |
71,5 мм |
||||||||
|
n |
V 1000 |
51 1000 |
227 |
об/мин. |
|||||
|
|
|
|
|
|
|
||||
|
D |
|
3,14 |
71,5 |
||||||
|
|
|
|
|
|
Расчетное число оборотов корректируется по паспортным данным станка nn и берется ближайшее меньшее n (табл. 1).
Подбирается ближайшее значение для каждого перехода. В данном примере для всех трех переходов число оборотов n 200 об/мин.
Отсюда после корректировки находим фактическую скорость резания: а) для первого перехода;
V |
D |
3,14 90 200 |
57 |
м/мин; |
||
|
|
|
||||
1000 |
1000 |
|||||
|
|
|
б) для второго перехода

Продолжение приложения 3
V |
|
|
D |
3,14 81,5 200 |
51м/мин; |
||||||
|
|
|
|
|
|
|
|
|
|||
1000 |
1000 |
|
|
||||||||
|
|
|
|
||||||||
в) для третьего перехода D 71,5 мм |
|||||||||||
V |
|
|
D |
3,14 71,5 200 |
45 |
м/мин. |
|||||
|
|
|
|
|
|
|
|||||
1000 |
1000 |
||||||||||
|
|
|
|
По табл. 11 определяется сила подачи при резании. При обработке с глубиной резания t = 5 мм, подачей S = 0,678 мм для резца = 45
сила подачи РX составляет 265 кг (для работы со скоростью резания V = 65 м/мин), т.е. меньше, чем допускаемая механизмом станка (РX = 360 кг).
Следовательно, выбранная подача по станку не лимитирует режим резания. Необходимо отметить, что такая проверка проводится только при черновом точении для сечения стружки, близкой к допустимой для данного станка, которая учитывается в паспорте.
Проверка выбранного режима по мощности
Согласно паспорту, станок в пределах выбранного режима имеет постоянную мощность на разных числах оборотов. Проверку режима производим по мощности.
По табл. 4 определяется мощность, потребная на резание. При обработке стали t 4,25мм, S 0,78 мм/об и V 57 м/мин мощ-
ность на резание (по наиболее загруженному переходу) составляет 5,8 кВт. Согласно паспортным данным, мощность на шпинделе по приводу станка при работе с числом оборотов шпинделя n 200 и минуту составляет 8,0 кВт, т.е. больше мощности, потребной на резание. Следовательно,
установленный режим резания по мощности осуществим.
3. Расчет составных частей нормы времени
Определение основного (технологического времени)
Основное технологическое время определяется по формуле
t0 |
l l1 |
l2 |
мин, |
|
n |
S |
|||
|
|
где l -длина обрабатываемой поверхности;
l1 - величина врезания и перебега резца, в мм;
l2 - дополнительная длина на взятие пробной стружки, в мм;
n - число оборотов в минуту;
S - подача на один оборот шпинделя, в мм/об.
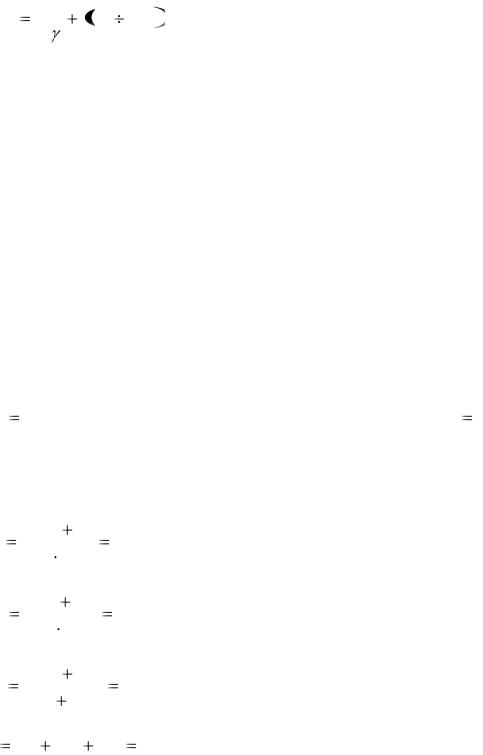
Продолжение приложения 3
Длиной врезания называется путь, который проходит режущий инструмент от момента начала резания до момента, когда достигнута полная глубина резания.
lвраз. |
t |
0,5 2,0 |
мм, |
|
|
||||
tg |
||||
|
|
|
где - главный угол в плане резца в градусах;
t - глубина резания.
Чем больше глубина резания, тем больше величина врезания.
Может быть такая обработка, когда нет выхода (перебега) резца из зоны резания (при обработке валов упорно-проходными резцами). Величина перебега при обработке на проход (т.е. с выходом из зоны резания) составляет 1 - 5 мм в зависимости от размеров обработки.
Длина проходов при взятии пробных стружек определяется так. Вначале протачивается небольшой кусок и проверяется, обеспечивается ли нужный размер. Если нет, то протачивается еще кусок, пока не достигнут заданного размера. На настроенных станках работа ведется без пробных стружек, поэтому в формулу основного времени величину 2 не включают.
Она имеет место при точной обработке или при грубой обработке в условиях единичного производства. В зависимости от точности l2 берется в
пределах 5 - 10 мм.
Согласно табл. 5 величина врезания и перебега для резца с углом в плане 450 принимается равной 8 мм и для резца с углом
900 рав-
ной 4 мм.
Обработка детали производится с установкой резца по лимбу без пробных стружек, поэтому дополнительная длина на взятие пробной стружки не учитывается. Тогда для поверхности I:
t0 |
|
|
|
515 |
|
8 |
|
|
|
3,35мин; |
|
|
|
|
|
|
|
|
|
|
|||
|
|
|
|
|
|
|
|
|
|||
1 |
200 |
0,78 |
|
|
|
|
|||||
|
|
|
|
|
|||||||
для поверхности 2: |
|
|
|
|
|||||||
t02 |
|
|
|
90 |
|
4 |
|
|
|
0,6 мин; |
|
|
|
|
|
|
|
|
|
|
|||
200 |
0,76 |
|
|
||||||||
|
|
|
|
|
|||||||
для поверхности 3: |
|
|
|
|
|||||||
t0 |
|
|
|
70 |
|
4 |
|
|
|
|
0,48мин. |
|
|
|
|
|
|
|
|
|
|
||
|
|
|
|
|
|
|
|
|
|
||
3 |
200 |
|
0,78 |
|
|
|
|||||
|
|
|
|
|
|||||||
Основное технологическое время на операцию равно: |
|||||||||||
t0 |
t0 |
t0 |
2 |
|
t |
0 |
3 |
4,43 мин. |
|||
|
1 |
|
|
|
|
|

Продолжение приложения 3
Определение вспомогательного времени
Элементы вспомогательного времени повторяются с каждой обрабатываемой деталью либо в определенной последовательности через некоторое количество деталей:
При работе на токарных станках вспомогательное время, как правило, ручное или машинно-ручное включает в себя следующие элементы:
t B |
t B |
t B |
t B |
t B , |
|
1 |
2 |
3 |
4 |
где
где
t B1 - время на установку и снятие детали (время на установку, закреп-
ление, выверку, раскрепление и снятие детали; в этот комплекс входит время на пуск и остановку станка);
t B2 - время, связанное с переходом (время на подвод инструмента,
установку на размер по лимбу или по пробной стружке, включение и выключение подачи, отвод инструмента в исходное положение);
t B3 - время на контрольные измерения (время на окончательные и
пробные измерения);
t B4 - время на межоперационные действия.
t B |
t B' |
t B'' |
, |
4 |
4 |
4 |
|
t B' 4 - время смены инструмента (время на смену инструмента или на
изменение положения инструментальной (резцовой) головки, если многоинструментальная операция);
t B'' 4 - время изменения режима (время на смену режимов, оно не по-
вторяется с каждым режимом).
Все эти затраты времени указаны в нормативах вспомогательного времени.
По табл. 7 время на установку и снятие детали массой 30 кг с креплением в центрах с надеванием хомутика при установке подъемником составляет 1,8 мин.
Вспомогательное время, связанное с переходом для станков II группы при диаметре обработки до 100 мм, составляет 0,13 мин (табл. 6).
На три перехода время составит 0,39 мин.
Время на приемы, не вошедшие в комплекс (поворот резцовой головки), равно 0,05 мин (табл. 6).
Вспомогательное время на операцию составит: tB 1,8 0,39 0,05 2,24мин.
Зная основное и вспомогательное время, находим оперативное время: tОП t0 tB 4,43 2,24 6,67мин.

Продолжение приложения 3
Время на обслуживание рабочего места определяется в зависимости от типа производства в % от основного или оперативного времени. По табл. 8 время на обслуживание рабочего места равно 2,5% от оперативного времени.
Время перерывов на отдых и личные надобности устанавливается по нормативам в зависимости от условий производства и работы оборудования.
Время на отдых и личные надобности рассчитывается в процентах от оперативного времени, в том числе время на личные надобности для всех видов работ предусматривается в среднем 2 % от времени смены. По табл. 8 для нашего примера время на отдых и личные надобности равно 4 % от оперативного времени.
Штучное время определяется по формуле
t ШТ tОП I |
|
К |
6,67 I |
6,5 |
7,1мин, |
||
|
|
|
|
||||
100 |
100 |
||||||
|
|
|
где К – время на обслуживание рабочего места, отдых и личные надобности в % от оперативного времени.
Подготовительно-заключительное время затрачивается станочником только в начале и в конце работы над данной партией деталей, и его продолжительность не зависит от числа штук в партии. Оно зависит от сложности деталей от зажимного приспособления, от количества инструментов, от размеров станка.
Подготовительно-заключительное время входит в состав нормы времени, если станочник сам выполняет накладку станка, пробную обработку деталей, получает и сдает инструмент. Такой порядок характерен для мелкосерийного, реже для серийного и главным образом для единичного производства. Подготовительно-заключительное время устанавливается в абсолютном значении по нормативам на партию деталей или на смену, реже
– в процентах от оперативного времени.
Норма подготовительно-заключительного времени для расчетных условий по табл. 8 составляет 7 мин.
Зная подготовительно-заключительное время, определяют норму времени. Норма времени может быть установлена на партию деталей ( t )
или при подетальной калькуляции – на одну штуку tшт к - (штучно-
калькуляционное время).
Результаты выбора режима резания и расчета основного времени используются в дальнейшем для практической деятельности.
Выбор режимов резания и расчет нормы времени для операции «Подрезка торцов» проводится аналогично. Для выбора режима резания используются соответствующие нормативные таблицы.

Продолжение приложения 3
4. Индивидуальные задания для расчета нормы времени на выполнение токарных работ
Станок – токарно-винторезный 1К62. Деталь – втулка.
Материал детали – сталь СТ5.
Режущий инструмент – резец проходной. Материал режущей кромки резца – Т15К6. Количество деталей в партии – 100 штук. Производство серийное.
Группа станков – 2.
Количество режущего инструмента – 1.
Установка резца на размер производится по лимбу.
Обработка производится без изменения оборотов, подачи и без поворота резцедержателя. Время вспомогательное, связанное с переходом, не вошедшее в комплексы работ – не считать.
Типовой технологический процесс обработки втулки
А. Установить заготовку в 3-кулачковом самоцентрирующем патроне. 1. Обточить DЗ до D .
Б. Переустановить втулку. 2. Обточить D до d на l . В. Снять втулку.
Паспортные данные станка 1К62 (выписка неполная)
Число оборотов шпинделя в минуту: 80, 100, 125, 160, 200, 250, 315,
400, 500, 530, 690, 800, 1000, 1100.
Продольные подачи S мм в минуту: 0,47; 0,52; 0,57; 0,61; 0,78; 0,87;
0,95; 1,04; 1,14; 1,21; 1,40; 1,56; 1,74.
Наибольшая сила, допустимая механизмом продольной подачи
X 360 кг.
Мощность электродвигателя 10 кВт.

Варианты задания для расчета норм на токарные работы
Заготовка |
Деталь |
3 |
D |
D |
d |
d |
|||
|
X |
|
|
|
|
|
l |
|
|
|
Z |
d3
Варианты |
Размеры заготовки |
|
Размер детали |
|
Вес заго- |
||
|
ДЗ |
LЗ |
D |
d |
L |
l |
товки, кг |
1 |
30 |
50 |
28 |
22 |
45 |
15 |
2,16 |
2 |
32 |
55 |
30 |
24 |
50 |
20 |
2,65 |
3 |
34 |
60 |
32 |
26 |
88 |
25 |
3,06 |
4 |
36 |
65 |
34 |
28 |
60 |
30 |
3,57 |
5 |
38 |
70 |
36 |
30 |
65 |
35 |
4,11 |
6 |
40 |
75 |
38 |
32 |
70 |
40 |
4,40 |
7 |
42 |
80 |
40 |
34 |
75 |
40 |
5,33 |
8 |
44 |
85 |
42 |
36 |
80 |
40 |
5,99 |
9 |
46 |
90 |
44 |
38 |
85 |
40 |
6,70 |
10 |
48 |
95 |
46 |
40 |
90 |
40 |
7,45 |
11 |
50 |
100 |
48 |
42 |
95 |
40 |
9,04 |
12 |
30 |
40 |
28 |
22 |
35 |
10 |
1,72 |
13 |
32 |
45 |
30 |
24 |
40 |
15 |
1,88 |
14 |
34 |
50 |
32 |
26 |
45 |
20 |
2,55 |
15 |
36 |
55 |
34 |
28 |
50 |
25 |
3,02 |
16 |
38 |
60 |
36 |
30 |
55 |
30 |
3,53 |
17 |
40 |
65 |
38 |
32 |
60 |
35 |
4,08 |
18 |
42 |
70 |
40 |
34 |
65 |
40 |
4,53 |
19 |
44 |
75 |
42 |
36 |
70 |
40 |
5,29 |
20 |
46 |
80 |
44 |
38 |
75 |
40 |
5,96 |
21 |
48 |
85 |
46 |
40 |
80 |
40 |
6,66 |
22 |
50 |
90 |
48 |
42 |
85 |
40 |
8,13 |
23 |
30 |
60 |
28 |
22 |
55 |
20 |
2,69 |
24 |
32 |
65 |
30 |
24 |
60 |
25 |
3,06 |
25 |
34 |
70 |
32 |
26 |
65 |
25 |
3,57 |
26 |
36 |
70 |
34 |
28 |
65 |
25 |
3,84 |
27 |
38 |
70 |
36 |
30 |
65 |
25 |
4,11 |
28 |
40 |
75 |
38 |
32 |
70 |
30 |
4,70 |
29 |
42 |
75 |
40 |
34 |
70 |
30 |
4,99 |
30 |
44 |
80 |
42 |
36 |
75 |
30 |
5,64 |
Таблица 1
ВЫПИСКА ИЗ ПАСПОРТА ТОКАРНО-ВИНТОРЕЗНОГО СТАНКА
|
|
Наиболь- |
|
|
Наибольшая эффективная допустимая |
|
|
|
|||
|
|
ший допу- |
|
|
мощность на шпинделе, кВт (NЗ) |
|
|
|
|||
|
Число обо- |
стимый |
|
Мощность |
|
|
|
|
|
|
|
|
ротов |
двойной |
|
|
|
|
|
|
|
|
|
|
|
электро- |
|
с учетом |
|
|
|
|
|||
№ ступени |
шпинделя |
крутящий |
|
|
по наиболее |
Подачи, мм/об (S) |
|||||
|
двигателя, |
|
полуторо- |
||||||||
|
в минуту |
момент на |
|
по приводу |
слабому |
|
|
|
|||
|
(n) |
шпинделе, |
|
кВт (NЗ) |
|
кратной пе- |
звену |
|
|
|
|
|
|
|
|
регрузки |
|
|
|
||||
|
|
кгм (МСТ) |
|
|
|
|
|
|
|
||
|
|
|
|
|
|
|
|
|
|
|
|
|
|
|
|
|
|
|
|
|
|
||
1 |
12,5 |
260 |
|
|
8 |
|
|
1,67 |
Продольные |
||
2 |
16 |
260 |
|
|
8 |
|
|
2,14 |
|
|
|
3 |
20 |
260 |
|
|
8 |
|
|
2,67 |
0,30; |
0,34; |
0,39; |
4 |
25 |
260 |
|
|
8 |
|
|
3,34 |
0,43; |
0,47; |
0,52; |
5 |
31,5 |
260 |
|
|
8 |
|
|
4,2 |
0,57; |
0,61; |
0,7; |
6 |
40 |
260 |
|
|
8 |
|
|
5,35 |
0,78; |
0,87; |
0,95; |
7 |
50 |
260 |
|
|
8 |
|
|
6,7 |
1,04; |
1,14; |
1,2; |
8 |
63 |
248 |
|
|
8 |
12,0 |
8 |
1,4; |
1,56; |
1,74; |
|
9 |
80 |
195 |
|
|
8 |
|
|
8 |
1,9; |
2,08; |
2,28; |
10 |
100 |
156 |
|
|
8 |
|
|
8 |
2,42; |
2,8; |
3,12; |
11 |
125 |
124 |
|
|
8 |
|
|
8 |
3,48; |
3,8; |
4,16; |
12 |
160 |
98 |
|
10,0 |
8 |
|
|
8 |
|
|
|
13 |
200 |
78 |
|
|
8 |
|
|
8 |
|
|
|
14 |
260 |
62 |
|
|
8 |
|
|
8 |
|
|
|
15 |
315 |
52 |
|
|
8,5 |
12,75 |
8,5 |
Поперечные |
|||
16 |
400 |
40,4 |
|
|
8,3 |
12,45 |
8,3 |
|
|
|
|
17 |
500 |
30,8 |
|
|
7,9 |
11,86 |
7,9 |
0,30; |
0,34; |
0,39; |
|
18 |
630 |
23,8 |
|
|
7,7 |
11,56 |
7,7 |
0,43; |
0,47; |
0,52; |
|
19 |
630 |
25,0 |
|
|
8,1 |
12,15 |
8,1 |
0,57; |
0,6; |
0,7; |
|
20 |
800 |
18,5 |
|
|
7,6 |
11,4 |
7,2 |
1,04; |
1,14; |
1,21; |
|
21 |
1000 |
14 |
|
|
7,2 |
10,8 |
7,2 |
1,04; |
1,14; |
1,21; |
|
22 |
1250 |
10,9 |
|
|
7,0 |
10,5 |
7,0 |
1,4; |
1,56; |
1,74; |
|
23 |
1600 |
8,4 |
|
|
6,9 |
10,35 |
6,9 |
1,9; |
2,08; |
|
|
24 |
2000 |
6 |
|
|
6,2 |
10,05 |
6,2 |
|
|
|
|
Наибольшее усилие, допускаемое механизмом подач, кг: |
|
|
продольное РХ = 360 кг |
|
|||||||
|
|
|
|
|
|
|
|
|
РZ = 1200 кг |
|
|
|
|
|
|
|
|
|
|
поперечное РХ =550 кг |
|
||
Наибольший диаметр изделия, устанавливаемого под станиной, мм |
|
400 |
|
|
|||||||
Наибольший диаметр обрабатываемого прутка, мм |
|
|
|
36 |
|
|
|||||
Наибольшая длина обтачивания, мм |
|
|
|
|
|
1330 |
|
|
|||
Число резцов в резцедержателе |
|
|
|
|
|
4 |
|
|
|||
Наибольший размеры державки резца, мм |
|
|
|
ширина «В» 25 |
|
|
|||||
|
|
|
|
|
|
|
|
высота «Н» 25 |
|
|

Таблица 2
ПОДАЧИ ДЛЯ ЧЕРНОВОГО НАРУЖНОГО ТОЧЕНИЯ Резцы с пластинками из твердого сплава и быстрорежущей стали
Обрабаты- |
Размер дер- |
Диаметр де- |
|
|
|
Глубина резания, мм (t). до: |
|
||||
ваемый ма- |
жавки резца, |
тали, мм. до |
|
3 |
|
5 |
|
8 |
|
12 |
Свыше 12 |
териал |
мм |
|
|
|
|
|
Подача, мм/ об (S) |
|
|
||
|
|
20 |
0,3 |
– 0,4 |
|
- |
|
- |
|
- |
- |
|
|
40 |
0,4 |
– 0,5 |
0,3 – 0,4 |
|
- |
|
- |
- |
|
|
16 х 25 |
60 |
0,5 |
– 0,7 |
0,4 |
– 0,6 |
|
0,3 – 0,5 |
|
- |
- |
|
|
100 |
0,6 – 0,9 |
0,5 |
– 0,7 |
|
0,5 – 0,6 |
|
0,4 – 0,5 |
- |
|
Стали кон- |
|
400 |
0,8 – 1,2 |
0,7 – 1,0 |
|
0,6 – 0,8 |
|
0,5 – 0,6 |
- |
||
|
20 |
0,3 |
– 0,4 |
|
- |
|
- |
|
- |
- |
|
струкцион- |
|
|
|
|
|||||||
|
40 |
0,4 – 0,5 |
0,3 |
– 0,4 |
|
- |
|
- |
- |
||
ные углеро- |
20 х 32 |
|
|
||||||||
60 |
0,6 – 0,7 |
0,5 – 0,7 |
|
0,4 – 0,6 |
|
- |
- |
||||
дистые ле- |
25 х 25 |
|
|
||||||||
100 |
0,8 – 1,0 |
0,7 – 0,9 |
|
0,5 – 0,7 |
|
0,4 – 0,7 |
- |
||||
гированные |
|
|
|
||||||||
|
600 |
1,2 – 1,4 |
1,0 – 1,2 |
|
0,8 – 1,0 |
|
0,6 – 0,9 |
0,4 – 0,6 |
|||
и жаропроч- |
|
|
|
||||||||
|
60 |
0,6 – 0,9 |
0,5 – 0,8 |
|
0,4 – 0,7 |
|
- |
- |
|||
ные |
|
|
|
||||||||
25 х 40 |
100 |
0,8 – 1,2 |
0,7 – 1,1 |
|
0,6 – 0,9 |
|
0,5 – 0,8 |
- |
|||
|
|
|
|||||||||
|
|
1000 |
1,2 – 1,5 |
1,1 – 1,5 |
|
0,9 – 1,2 |
|
0,8 – 1,0 |
0,7 – 0,8 |
||
|
32 х 40 |
500 |
1,1 – 1,4 |
1,1 – 1,4 |
|
1,0 – 1,2 |
|
0,8 – 1,2 |
0,7 – 1,1 |
||
|
40 х 63 |
2500 |
1,3 – 2,0 |
1,3 – 1,8 |
|
1,2 – 1,6 |
|
1,1 – 1,5 |
1,0 – 1,5 |
||
|
|
и более |
|
|
|
|
|
|
|
|
|
Примечание: 1. При обработке жаропрочных сталей и сплавов подачи свыше 1,0 мм/об не применять.
2. При обработке прерывистых поверхностей и на работах с ударами следует табличные
значения подачи умножать на коэффициент K |
S |
0,75 0,85 . |
|
|
3. При обработке сталей закаленных к табличным данным применять коэффициент: для сталей с НRC 44 – 56 КЗ = 8,0, для сталей с НRC 57 – 62 КЗ = 0,5.
где НRC – твердость обрабатываемого материала по Роквеллу.
Таблица 3
СКОРОСТЬ РЕЗАНИЯ Сталь конструкционная углеродистая, хромистая, хромоникелевая и стальные отливки
|
|
Предел прочности при растяжении, кг/мм2 |
|
|
|
|
|
|
|
|
|
|
|
|
|
|
|
|
|
|
||||||
44-49 |
50-55 |
56-62 |
63-70 |
71-79 |
80-89 |
90-100 |
Свыше |
|
|
|
|
|
|
|
|
|
|
|
|
|
|
|
|
|
||
100 |
|
|
|
|
|
|
|
|
|
|
|
|
|
|
|
|
|
|||||||||
|
|
|
|
|
|
|
|
|
|
|
|
|
|
|
|
|
|
|
|
|
|
|
|
|
|
|
|
|
|
Твердость по Бринелю НВ |
|
|
|
|
|
|
|
|
|
Подача, мм до: |
|
|
|
|
|
|
|
||||||
120-140 |
141-158 |
159-177 |
178-200 |
201-226 |
227-255 |
256-286 |
Свыше |
|
|
|
|
|
|
|
|
|
|
|
|
|
|
|
|
|
||
286 |
|
|
|
|
|
|
|
|
|
|
|
|
|
|
|
|
|
|||||||||
|
|
|
|
|
|
|
|
|
|
|
|
|
|
|
|
|
|
|
|
|
|
|
|
|
|
|
|
|
|
Глубина резания, мм до: |
|
|
|
|
|
|
|
|
|
|
|
|
|
|
|
|
|
|
|
||||
2 |
|
1 |
- |
- |
|
- |
- |
- |
- |
0,25 |
0,38 |
0,54 |
0,75 |
0,97 |
1,27 |
1,65 |
2,15 |
2,8 |
- |
- |
- |
- |
|
- |
||
4 |
|
2 |
1 |
- |
|
- |
- |
- |
- |
0,14 |
0,25 |
0,38 |
0,54 |
0,75 |
0,97 |
1,27 |
1,65 |
2,15 |
2,8 |
- |
- |
- |
|
- |
||
8 |
|
4 |
2 |
1 |
- |
- |
- |
- |
- |
0,14 |
0,25 |
0,38 |
0,54 |
0,75 |
0,97 |
1,27 |
1,65 |
2,15 |
2,8 |
- |
- |
|
- |
|||
20 |
|
8 |
4 |
2 |
1 |
- |
- |
- |
- |
- |
0,14 |
0,25 |
0,38 |
0,54 |
0,75 |
0,97 |
1,27 |
1,65 |
2,15 |
2,8 |
- |
|
- |
|||
- |
|
20 |
8 |
4 |
2 |
1 |
- |
- |
- |
- |
- |
0,14 |
0,25 |
0,38 |
0,54 |
0,75 |
0,97 |
1,27 |
1,65 |
2,15 |
2,8 |
|
- |
|||
- |
|
- |
20 |
8 |
4 |
2 |
1 |
- |
- |
- |
- |
- |
0,14 |
0,25 |
0,38 |
0,54 |
0,75 |
0,97 |
1,27 |
1,65 |
2,15 |
|
2,8 |
|||
- |
|
- |
- |
20 |
8 |
4 |
2 |
1 |
- |
- |
- |
- |
- |
0,14 |
0,25 |
0,38 |
0,54 |
0,75 |
0,97 |
1,27 |
1,65 |
|
2,15 |
|||
- |
|
- |
- |
- |
|
20 |
8 |
4 |
2 |
- |
- |
- |
- |
- |
- |
0,14 |
0,25 |
0,38 |
0,54 |
0,75 |
0,97 |
1,27 |
|
1,65 |
||
- |
|
- |
- |
- |
|
- |
20 |
8 |
4 |
- |
- |
- |
- |
- |
- |
- |
0,14 |
0,25 |
0,38 |
0,54 |
0,75 |
0,97 |
|
1,27 |
||
|
|
Характер обработки |
|
Главный угол в плане, |
|
|
|
|
|
|
|
Скорость резания, м/мин |
|
|
|
|
|
|
||||||||
|
|
|
|
град |
|
|
|
|
|
|
|
|
|
|
|
|
|
|
||||||||
|
|
|
|
|
|
|
|
|
|
|
|
|
|
|
|
|
|
|
|
|
|
|
|
|
|
|
Наружное продольное и |
поперечное |
|
45 – 60 |
|
188 |
|
167 |
148 |
132 |
117 |
104 |
93 |
82 |
73 |
65 |
58 |
51 |
46 |
|
41 |
||||||
точение |
при |
отношении |
диаметров |
|
|
|
|
|||||||||||||||||||
|
|
|
|
|
|
|
|
|
|
|
|
|
|
|
|
|
|
|
|
|||||||
начальной и конечной обработки |
|
90 |
|
167 |
|
148 |
132 |
117 |
104 |
93 |
82 |
73 |
65 |
58 |
51 |
46 |
41 |
|
36 |
|||||||
D1 : D2 = 0,8 + 1,0 |
|
|
|
|
|
|
|
|||||||||||||||||||
|
|
|
|
|
|
|
|
|
|
|
|
|
|
|
|
|
|
|
|
|
|
|
||||
Поперечное точение |
при отношении |
|
45 – 60 |
|
230 |
|
200 |
179 |
159 |
141 |
125 |
111 |
99 |
88 |
78 |
70 |
62 |
55 |
|
49 |
||||||
диаметров начальной и конечной об- |
|
|
|
|
||||||||||||||||||||||
|
|
|
|
|
|
|
|
|
|
|
|
|
|
|
|
|
|
|
|
|||||||
работки |
|
|
|
|
|
|
90 |
|
199 |
|
177 |
157 |
140 |
124 |
110 |
98 |
87 |
78 |
69 |
61 |
54 |
48 |
|
43 |
||
D1 : D2 = 0,5 +0,7 |
|
|
|
|
|
|
|
|||||||||||||||||||
|
|
|
|
|
|
|
|
|
|
|
|
|
|
|
|
|
|
|
|
|
|
|
||||
Растачивание (до D = 500 мм) |
|
|
45 – 60 |
|
167 |
|
148 |
132 |
117 |
104 |
93 |
82 |
73 |
65 |
58 |
46 |
46 |
41 |
|
36 |
||||||
|
|
90 |
|
148 |
|
132 |
117 |
104 |
93 |
82 |
73 |
65 |
58 |
51 |
51 |
41 |
36 |
|
32 |
|||||||
|
|
|
|
|
|
|
|
|
|
|
||||||||||||||||
Прибавочный коэффициент на скорость резания в зависимости |
|
Поверхность |
|
|
Без корки |
|
|
С коркой |
|
|
|
|
|
|||||||||||||
|
|
от состояния поверхности заготовки |
|
|
|
|
|
|
|
|
|
|
|
литейной |
|
литейной |
|
|||||||||
|
|
|
|
|
|
|
|
|
|
|
|
|
|
|
|
|
|
|
|
|
|
|
загрязненной |
|||
|
|
|
|
|
|
|
|
|
|
Коэффициент (К) |
|
|
|
0,1 |
|
|
0,8 – 0,85 |
|
0,5 – 0,6 |
|