
4201
.pdf
Приложение 3
1. Методические основы расчета нормы времени на работы, выполненные на токарном станке
Обработку деталей с применением токарных станков принято называть токарными работами. Расчет нормы времени на эти виды работ производится по методике расчета норм и нормативов для станочных работ с использованием типовых общемашиностроительных нормативных таблиц. Выбор и обоснование параметров режимов резания производится исходя из конкретных производственных условий и технологической карты производственного задания:
H ВР |
t ПЗ |
tОП |
tОБС |
tОТЛ , |
(3.1) |
||
где t ПЗ , |
tОБС , |
tОТЛ |
определяется по нормативным таблицам, |
непосред- |
|||
ственно учитывая содержание производственного задания |
|
||||||
tОП |
tОСН |
tвспом. , |
|
(3.2) |
|||
t |
t |
маш |
|
l |
l1 l2 |
i, |
|
|
|
|
|
||||
осн |
|
|
|
n S |
|
|
|
|
|
|
|
|
|
|
где l - геометрические размеры обрабатываемой поверхности (мм); l1 - величина врезания и перебега резца (мм);
l2 - величина взятия пробной стружки (мм);
n - скорость вращения обрабатываемой детали (об/мин);
S - подача режущего инструмента в мм на один оборот детали; i - число проходов (шт).
Так как токарная обработка предполагает снятие в результате обработки заготовки излишнего припуска до получения детали определенных параметров, то необходимо учитывать, что слой материала, который может быть срезан за один проход, может быть меньше, чем весь припуск на резание. Тогда глубина резания за один проход обозначают – «t », а весь припуск на резание обозначается буквой « h ».
Для того чтобы определить количество проходов, необходимых для снятия всего припуска, пользуются формулой
i |
h |
шт, |
(3.3) |
|
t |
||||
|
|
|
причем i всегда целое число. Если в расчете i получается числом дробным, необходимо округлить результат до ближайшего большего целого числа.

Продолжение приложения 3
Например: если i 2,3, принимаем i 3 , но глубина резания для двух про-
ходов будет равна t , а для третьего - 13 t .
При обработке цилиндрических поверхностей (обтачивание, растачивание, рассверливание, внешнее и внутреннее шлифование) глубина реза-
ния равна 1 разности диаметров заготовки до обработки ( D ) и детали по-
2
сле обработки за данный проход ( d ):
t |
D d |
мм, |
(3.4) |
|
2 |
||||
|
|
|
Подача – величина перемещения режущего инструмента относительно обрабатываемой детали, пройденная за определенный отрезок времени. Подача обозначается буквой « S ».
При работе на обрабатывающих станках различают три вида подачи:
минутная, за один оборот, на один зуб режущего инструмента. |
|
||||
Между минутной подачей ( SМ ) и подачей на один оборот SОБ |
имеет- |
||||
ся следующая зависимость: |
|
||||
S |
|
|
S М |
мм/об, |
(3.5) |
ОБ |
|
n |
|||
|
|
|
|
||
|
|
|
|
|
|
SМ |
SОБ |
n , мм/об, |
(3.6) |
где n - число оборотов обрабатываемой детали или режущего инструмента в 1 мин.
Между подачей на один зуб SZ и подачами SM и SОБ имеется следу-
ющая зависимость: |
|
||||||
S |
|
|
S M |
мм/зуб, |
(3.7) |
||
Z |
|
|
|
||||
|
|
|
n Z |
|
|||
|
|
|
|
|
|||
S |
|
|
SОБ |
мм/зуб, |
(3.8) |
||
Z |
|
||||||
|
|
Z |
|
||||
|
|
|
|
|
|||
где Z - число зубьев режущего инструмента. |
|||||||
Скорость резания V |
- это перемещение режущей кромки инструмен- |
та относительно обрабатываемой поверхности детали в направлении главного движения в единицу времени. При обработке на станках с вращательным главным движением (токарные, фрезерные, сверлильные и др.) скорость резания измеряется по окружности вращения, поэтому называется окружной и определяется по формуле
V |
D n |
м/мин, |
(3.9) |
|
1000 |
||||
|
|
|
где D - начальный диаметр обрабатываемой поверхности детали или диаметр режущего инструмента, мм;

Продолжение приложения 3
n - число оборотов обрабатываемой детали или режущего инструмента в 1 мин;
- отношение длины окружности к диаметру, равное 3,14.
Выбор режима резания (глубины, подачи, скорости) производится с учетом частоты вращения шпинделя станка, сил резания, крутящего момента и мощности, потребной на резание. Эти понятия являются дополнительными характеристиками режима резания.
Число оборотов детали измеряется в об/мин.
От выбранной скорости резания зависит частота вращения шпинделя станка. Зная скорость резания, можно определить число оборотов детали, инструмента или шпинделя станка в минуту. Из вышеприведенной формулы (п.3.9.) получаем:
n |
1000 V |
об/мин, |
(3.10) |
|
d |
||||
|
|
|
В практике технического нормирования принято параметры режимов резания выбирать исходя из показателей обрабатываемости материала, режущих свойств инструментального материала, геометрических параметров и стойкости инструмента, требований к чистоте и точности обработки.
Показателями обрабатываемости материалов являются:
-скорость резания при обработке определенным режущим инструментом и при постоянных значениях стойкости инструмента, подачи и глубины резания;
-силы резания при определенном режиме резания;
-чистота обработанной поверхности при определенном режиме резания.
Обрабатываемость стали зависит от ее химического состава (содержания углерода, кремния и легирующих элементов: хрома, никеля, молибдена и др.) и от ее химических свойств. При увеличении содержания углерода свыше 0,6%, а также при наличии кремния и легирующих элементов ухудшается обрабатываемость стали быстрорежущими инструментами. С повышением прочности ( в ) и твердости (НВ) обрабатываемого материа-
ла коэффициент обрабатываемости по скорости резания и по силе резания уменьшается.
Применяемые в настоящее время в промышленности инструментальные материалы могут быть разделены на 3 основные группы:
1)инструментальные стали;
2)металлокерамические сплавы;
3)минералокерамические материалы.
К числу инструментальных сталей относятся быстрорежущие стали (Р18, Р19), инструментальные легированные стали (В1, В2, 9КС, ХВ2 и др.) и инструментальные углеродистые стали (У10А, У12А и др.).

Продолжение приложения 3
К числу металлокерамических сплавов относятся сплавы карбида вольфрама с кобальтом (ВК2, ВК3, ВК8, ВК12 и др.) и сплавы карбида титана и карбида вольфрама с кобальтом (Т5К10, Т15К6, Т30К4, Т60К6 и
т.д.).
Режущим материалом в металлокерамических сплавах являются зерна карбидов вольфрама и титана, обладающие высокой твердостью, износоустойчивостью и термостойкостью. Кобальт в этих сплавах выполняет роль цементирующего вещества.
Основой металлокерамических материалов типа ЦМ-332 является окись алюминия.
Минералокерамические режущие инструменты имеют теплостойкость и износоустойчивость в 1,5 - 2 раза выше, чем у твердых сплавов.
Режущие свойства инструментальных материалов определяются стойкостью инструмента, изготовленного из данного материала, при определенном режиме резания. Высоким режущим свойствам инструментального материала обычно сопутствует его высокая твердость, износостойкость и термостойкость, т.е. способность сохранять свои механические свойства при высокой температуре.
Кроме того, существенными признаками, характеризующими режущие свойства инструментального материала, является его механическая прочность, т.е. сопротивление изгибу и ударная вязкость, а также удельная теплопроводность.
Геометрические параметры режущего инструмента неразрывно связаны с выбором режима резания. Изменяя отдельные геометрические параметры инструмента, можно существенно изменить скорость резания, силы резания, чистоту обработанной поверхности и характер стружкообразования.
Уменьшение главного угла в плане () при прочих равных условиях
приводит к увеличению скорости и улучшению теплопровода от вершины резца. Однако уменьшение главного угла в плане не всегда целесообразно, т.к. оно ведет к увеличению длины врезания, что является невыгодным при коротких проходах.
Вспомогательный угол в плане (
ту обработанной поверхности. Если 1 40 , чистота обработанной по-
верхности будет лучше.
Требования к шероховатости (чистоте) и точности обрабатывае-
мого материала. В соответствии с ГОСТом 2789-73 чистота (шероховатость) обработанной поверхности определяется 14 классами шероховатости (чистоты); основными параметрами классов шероховатости являются

Продолжение приложения 3
числовые значения среднего арифметического отклонения профиля « Ra » и высота неровностей профиля по десяти точкам « Rz ».
Установлено, что для классов 6 - 12 основным является параметр Ra , а для классов 1 - 5 и 13 - 14 - Rz .
На шероховатость (чистоту) обработанной поверхности влияют: величина подачи, свойства обрабатываемого материала, значение главного и вспомогательного углов в плане, величина износа инструмента, принятая в качестве критерия затупления, а также скорость резания.
Точность обработанной поверхности в машиностроении определяется классом точности, т.е. характеристикой точности изготовления изделия (детали, узла, машины или прибора), которая определяется значениями допусков, указанных в стандартах.
Существует несколько классов точности, они обозначаются порядковыми номерами. Номер класса точности возрастает с увеличением допусков. В общесоюзной системе допусков (ОСТ) для цилиндрических соединений с размерами от 1до 500 мм имеются следующие классы точности: 1, 2, 2а, 3, 3а, 4, 5, которые используются, как правило, для сопрягаемых раз-
меров, и 7, 8, 9, 10 – для неответственных, так называемых свободных размеров.
Стойкость и износ режущего инструмента. Износ инструментов в процессе резания непрерывно возрастает. При достижении определенной величины износа инструмент снимается со станка и направляется в переточку. Допустимая величина износа режущего инструмента называется критерием затупления « », измеряется в миллиметрах.
Период от начала работы инструмента до достижения износа, равного критерию затупления, называется стойкостью или периодом стойкости (Т) и исчисляется в минутах машинного времени. Нормальная стойкость находится в пределах от 60 до 90 минут.
Износ и стойкость инструмента связаны между собой и со всеми элементами режима резания определенными функциональными зависимостями. С увеличением периода стойкости увеличивается износ инструмента и уменьшается скорость резания.
Между периодами стойкости и скоростью резания существует следующая зависимость:
T m |
CV |
мин, |
(3.11) |
||
V M |
|||||
|
|
|
|||
V M |
|
CV |
м/мин, |
(3.12) |
|
T m |
|||||
|
|
|
где T - стойкость инструмента в минутах;
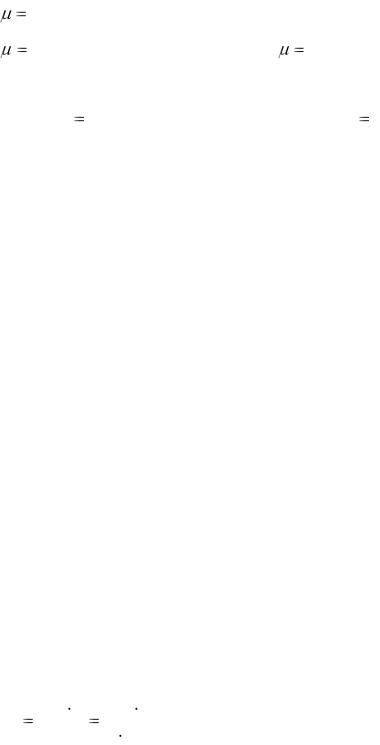
Продолжение приложения 3
CV - коэффициент, величина которого зависит от вида обработки,
свойств режущих инструментов и обрабатываемого материала; V - скорость резания, в м/мин;
1 |
- показатель относительной |
скорости (для твердых сплавов |
|
m |
|||
|
|
||
5, для быстрорежущих сталей |
8 ); |
m - показатель относительной стойкости (величина, обратная показателю относительной скорости); при обработке сталей твердыми сплавами m 0,2 , для быстрорежущей стали m 0,125 .
Выбранные параметры режима резания необходимо проверять на соответствие по принятым ограничениям. Основными ограничениями при токарной обработке детали являются допустимые силы резания и мощности станка.
Силы резания. В процессе резания металл оказывает сопротивление резанию в виде сил, возникающих на режущем инструменте.
Общая сила, воспринимаемая инструментом (р), разлагается на три взаимоперпендикулярные составляющие. Так, при работе на токарных станках резцом общее усилие резания раскладывается на:
а) тангенциальную составляющую (или вертикальное усилие резания PZ ), направленную по касательной к обрабатываемой поверхности;
б) радиальную составляющую PY , которая действует по радиусу об-
рабатываемой детали; в) осевую составляющую, которая направлена в сторону подачи. Осе-
вое усилие резания PX называют силовой подачей.
Силы резания необходимы при выборе режима резания. Так, например, радиальное усилие PY принимается в расчет при определении проги-
ба детали и возникающих вследствие прогиба неточностей формы обработанной поверхности.
Осевое усилие резания PX следует учитывать при проверке выбранно-
го режима резания по прочности механизма подачи.
Вертикальная (тангенциальная) составляющая PZ нужна при расчете
двойного крутящего момента и мощности резания.
Крутящий момент. Вертикальное усилие резания PZ создает на обрабатываемой детали крутящий момент, который определяется по формуле
M |
pZ r |
|
PZ Д |
кгм, |
(3.13) |
1000 |
2 1000 |
где M - крутящий момент резания, кгм; PZ - вертикальное усилие резания, кг;

Продолжение приложения 3
Д - диаметр обрабатываемой детали, мм.
Возникающий в процессе резания крутящий момент не должен превышать крутящего момента на шпинделе станка или
M CT M ,
где M CT - крутящий момент на шпинделе станка, кгм.
В практике нормирования обычно поверка выбранного режима резания по прочности механизма главного движения производится не по одинарному крутящему моменту, а по двойному крутящему моменту, который определяется из формуле (3.14).
2M |
PZ Д |
кгм, |
(3.14) |
1000 |
Мощность, потребная на резание, зависит от усилия резания ( PZ ) и
скорости резания (V ). Она определяется по нормативным таблицам или по следующей формуле:
N P |
PZ |
V |
|
PZ |
V |
, |
(3.15) |
|
60 |
102 |
6120 |
||||||
|
|
|
где PZ - вертикальное (тангенциальное) усилие резания, кг;
V - скорость резания, м/мин;
60 –числовой множитель перевода секунд в минуты; 102 – работа 102 кгм/сек = 1 кВт.
В паспорте станка указывается эффективная мощность на шпинделе N Э (мощность на инструменте) или мощность электродвигателя Nд .
Эффективная мощность на шпинделе станка N Э определяется по формуле
' |
(3.16) |
N Э N д СТ , |
где Nд - мощность электродвигателя станка;
СТ - коэффициент полезного действия станка (КПД).
Мощность электродвигателя станка определяется следующим образом:
N д |
N P |
, |
(3.17) |
|
CT |
||||
|
|
|
||
Мощность, потребная на резание |
N P , не должна превышать эффек- |
|||
тивной мощности станка: |
|
|||
N P |
NЭ , |
(3.18) |
Режимы резания определяются обрабатываемостью материалов, режущими свойствами и областью применения инструментальных материалов, геометрическими параметрами режущей части инструмента, требова-

Продолжение приложения 3
ниями к шероховатости (чистоте) и точности обработки поверхности, стойкостью и износом режущего инструмента.
2. Порядок выбора режима резания
Назначению режима резания предшествует разработка технологического процесса, в котором должны содержаться следующие данные:
а) исполнительные размеры, допуски и шероховатости (чистота обработанной поверхности);
б) припуск на обработку; в) конструкции, геометрические параметры и материал режущей ча-
сти инструмента; г) механические свойства обрабатываемого материала (предел проч-
ности B кг/мм2 или твердость по Бринелю НВ);
д) размеры заготовки и способ ее крепления в приспособлении; е) тип и модель станка.
Выбор режима резания рассмотрим на конкретном примере для токарных работ.
Назначение режима резания и определение основного машинного времени осуществляется отдельно для черновой и чистовой токарной обработки в следующей последовательности;
1.Выбирается максимально возможная глубина резания.
2.Устанавливается максимально допустимая величина подачи.
3.Определяется норматив скорости резания и соответствующее ему число оборотов шпинделя в минуту.
4.Определяются силы резания P и мощность, потребная для резания.
5.Найденные параметры режима резания проверяются по возможности их осуществления и корректируются в соответствии с паспортными данными.
6.Рассчитывается время: основное, оперативное, штучное штучнокалькуляционное.

|
|
|
|
|
|
|
Продолжение приложения 3 |
|||||
|
|
|
|
|
|
I |
2 |
3 |
||||
|
|
|
|
|
|
|
71,5 |
|
|
|
|
|
|
|
|
|
|
|
|
|
|
61,5 |
|
|
|
|
|
|
|
|
|
|
|
|
||||
|
|
|
|
|
|
|
|
|
|
|
|
|
|
|
81,5 |
|
|
|
|
|
|
|
|
|
|
|
|
|
|
|
|
|
|
|
|
|
|
|
|
|
|
|
|
|
|
|
|
|
|
|
|
|
|
|
|
|
|
|
|
|
|
|
|
|
|
|
|
|
|
|
|
|
|
|
|
|
|
|
|
|
|
|
|
|
|
|
|
|
|
|
|
|
|
|
|
|
|
80 |
70 |
|
|||
|
|
|
|
|
|
|
|
|||||
|
|
|
515 |
|
|
|||||||
|
|
|
|
|
|
|
|
|
||||
|
|
|
|
|
|
|
|
|
|
|
|
|
|
|
725 |
|
|
|
|
|
|
|
|
|
|
|
|
|
|
|
|
|
|
|
|
|
||
|
|
|
|
|
|
|
|
|
|
|
|
|
Рис. 3.1. Чертеж вала
Характеристика технологического процесса
Наименование операции – обточка |
Изделие. |
|
|
по диаметру и шеек черновая. |
Наименование детали – вал. |
||
Разряд работы – 4. |
№ детали. |
|
|
Станок: токарно-винторезный. |
№ чертежа. |
||
Модель – 1К62, N = 10 кВт. |
Количество деталей на одно изде- |
||
Инвентарный № 157. |
лие. |
|
|
Число станков, обслуживаемых ра- |
Род и размер заготовки – горячая |
||
бочим – 1. |
штамповка. |
||
Число одновременно устанавливае- |
90 725 мм с припуском по шей- |
||
мых деталей –1. |
кам вала 5 мм на сторону, сталь |
||
|
40Х, |
B |
72 кг/мм2. |
|
|
|
|
|
Вал черновой – 30 кг. |
||
|
Размер партии – 200 шт. |
Исходные данные к примеру
Деталь – вал.
Операция – обточка по диаметру и шейке с одной стороны, черновая.
Обрабатываемый материал – сталь хромистая 40Х, B 72 кг/мм2.
Характер заготовки – горячая штамповка 90 725 мм. Вес заготовки – 30 кг.
Станок – токарно-винторезный 1К62.
Инструмент – резец проходной, 450 , Т5К10, 1 шт.; резец проходной,
900 ; Т5К10, 1 шт.
Приспособление – центра, хомутик.

Продолжение приложения 3
Выбор глубины резания
Исходя из припуска на обработку устанавливается максимально возможная глубина резания «t», т.к. она оказывает меньшее влияние на стойкость резца и скорость резания, чем подача.
Надо стремиться, чтобы припуск на черновую обработку снять сразу. Сумма припуска на черновую обработку hчерн. и чистовую обработку
hчист. представляет собой припуск на сторону при токарной обработке
цилиндрических поверхностей.
По величине общего припуска на обработку 5,0 мм (на сторону) с учетом необходимости оставления припуска на чистовую обработку 0,75 мм устанавливается глубина резания t 4,25 мм, для обработки по наружному
диаметру 81,5 мм; для обработки шейки 71,5 мм - t 5 мм и шейки
61,5 мм - t 5 мм.
Определение подачи
При черновой обработке выбор подачи производится всегда в два этапа: а) определяется величина подачи по нормативам; б) производится уточнение подачи после проверки ее по целому ряду
ограничений (таких как прочность державки резца, прочность пластинки твердого сплава; усилие, допускаемое механизмом подач станка; крутящий момент или эффективная мощность резания, допускаемые механизмом главного движения станка; жесткость системы станок – приспособление – деталь – инструмент (СПИД); заданная точность и шероховатость обработанной детали).
В зависимости от глубины резания, свойств обрабатываемого и режущего материала, геометрических параметров резца по нормативной таблице определяется подача на 1 оборот детали.
По табл. 2 определяется подача, величина которой для обработки стали резцом с размером державки 25 х 25 мм при точении детали диаметром до 100 мм с глубиной резания = 5 мм рекомендуется в пределах 0,7 – 0,9 мм/об.
Принимается среднее значение подачи S 0,8 мм/об. Выбранная подача сопоставляется с паспортными данными по табл. 1. Ближайшее значение подачи по паспорту станка S 0,78 мм/об, которое и принимается для работы. Принятая для работы подача проверяется по осевой силе реза-