
Дерябин Проектирование фасонных резцов 2013
.pdf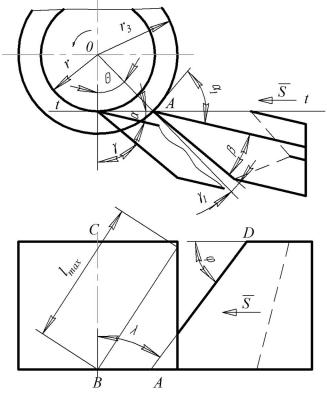
пространстве режущей кромкой, называемая инструментальной поверхностью, представляет собой в общем случае цилиндрическую поверхность, касающуюся поверхности детали по линии ее осевого профиля. Линия осевого профиля детали служит направляющей инструментальной поверхности, а ее образующие совпадают с траекториями точек режущей кромки.
Рис. 15. К выводу уравнений профиля тангенциального резца
При такой схеме формообразования траектория каждой точки режущей кромки на поверхности резания представляет собой плоскую спираль, вследствие чего поверхность резания каждого элементарного участка режущей кромки есть винтообразная поверхность. На поверхности детали траектории точек режущей кромки
21
располагаются в виде винтовых линий с шагом p = S0 tgϕ, где S0 –
подача на оборот детали. Поэтому профиль детали, обработанной тангенциальным резцом, не будет совершенно гладким. При значениях S0 и φ, обычно используемых при обработке, отклонения реального профиля детали от теоретического малы и удовлетворяют требованиям производства.
3.2. Геометрия режущей части
Режущую кромку резца для уменьшения сил резания располагают под углом φ = 45…75° к направлению вектора подачи или под углом λ = 15…45° к оси детали. В отличие от радиальных резцов величины углов γ и α резцов тангенциальных назначать в зависимости от обрабатываемого материала нельзя.
Задняя поверхность тангенциального резца представляет собой цилиндрическую поверхность, образующие которой пересекают траектории точек режущей кромки под углом α, а направляющая есть проекция профиля детали на плоскость, перпендикулярную этим образующим.
Поскольку передняя поверхность резца есть плоскость, пересекающая образующие задней поверхности под одним углом, то для изучения геометрии режущей части можно рассмотреть одно сечение режущего клина плоскостью, перпендикулярной оси детали.
Режущая кромка вступает в работу в точке А (см. рис. 15), лежащей на поверхности заготовки радиусом r3, а заканчивает профилирование в точке В, лежащей на поверхности детали радиусом r. Нормаль ОА к поверхности детали в точке А разделяет пространство под линией t-t на две части. Режущий клин резца должен располагаться справа от этой нормали так, чтобы между образующей задней поверхности и линией t-t в момент профилирования был угол α, а между передней гранью и нормалью ОА был угол γ1. Исходя из условий обработки задний угол α = 2,5…7°, передний угол
γ1 = 0…5°, угол клина βmin = 45°.
При этих значениях θmax =90°−αmin −γ1min −βmin = 42,5°. В общем случае (см. рис. 15) можно найти, что
22
θ = arccos(r / r3 ). |
(3.1) |
Равенство (3.1) ограничивает величину припуска на обработку. Наибольший радиус поверхности заготовки в каждом сечении детали для обеспечения минимальных значений углов α, γ, β не
должен превышать величину
r3 max = r / cos θmax =1,35r. |
(3.2) |
Если на отдельных участках профиля условие (3.2) не выполняется, то необходимо обработку вести за несколько переходов.
Исходя из рис. 15 , можно установить, что
α1 = α +θ, γ = γ1 +θ. |
(3.3) |
Таким образом, при расчете тангенциального фасонного резца задний угол α и передний угол γ в момент профилирования задают
сучетом значения угла θ так, чтобы угол β ≥ 45°.
3.3.Профилирование тангенциальных фасонных резцов
Для определения координат точек профиля тангенциального фасонного резца (нормального сечения его задней поверхности) следует поступать следующим образом. Уравнения поверхности детали (2.11) переписывают из системы координат S1 (x1y1z1) в систему координат S0 (x0y0z0), связанную с инструментальной поверхностью [3]. Далее находят в этой системе координат уравнение режущей кромки как линии пересечения инструментальной поверхности передней гранью резца. Затем, переписав уравнение режущей кромки в систему координат S2 (x2y2z2), связанную с резцом, находят уравнение его задней поверхности, нормальное сечение которой и есть искомый профиль резца.
Расположение системы координат показано на рис. 16. Уравнения поверхности детали (1.11) в системе S0 (x0 y0 z0) име-
ют вид
x0y0z0
= Ri cost + r, |
|
= Ri sin t, |
(3.4) |
= lli . |
|
23
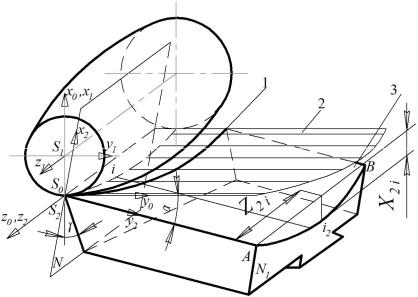
Рис. 16. Схема профилирования тангенциального резца
Уравнения передней поверхности в системе S0: |
|
|||
xn |
= r − Ri , |
|
||
y |
n |
= l |
tgλ+(R −r) tgγ, |
(3.5) |
|
i |
i |
|
|
|
|
= li . |
|
|
zn |
|
Переписав уравнение (3.5) в систему S2 (x2 y2 z2), получим урав-
нения задней поверхности резца: |
|
|
||||
x2 |
= [li tgλ +(Ri |
−r) tgγ]sin α −(Ri |
−r)cos α, |
|
||
y |
|
= [l |
tgλ +(R |
−r) tgγ]cos α +(R |
−r)sin α, |
(3.6) |
|
2 i |
i |
i |
|
|
|
|
|
= li . |
|
|
|
|
z2 |
|
|
|
|
||
Рассекая поверхность (3.6) плоскостью у2 |
= const, |
например |
у2 = 0, получаем уравнения для расчета координат профиля тангенциального резца:
x2 = li tgλsin α −[(Ri −r)cos(α + γ)/ cos γ], (3.7)
z2 = li .
24
где Ri – радиус i-й точки профиля детали; r – минимальный радиус профиля детали; li – расстояние от базового торца детали i-й точки профиля.
Профиль тангенциального резца по координатам x2 и z2 строят в плоскости N. На рис. 16 в плоскости N1, параллельной N, показаны координаты точки i2 профиля резца, обрабатывающей точку i1 профиля детали. Образующая точки А задней поверхности резца проходит через начало координат S2, поэтому точка А – базовая точка профиля. Из этой точки проводят линию АВ , параллельную базе крепления (линия АВ параллельна оси z2). Размеры z2 откладывают на линии АВ от базового торца, а размеры x2 – от линии АВ к опорному торцу, так как координаты х2 точек профиля резца, вычисленные по формуле (3.7), согласно принятым системам координат, отрицательные.
4. РАСЧЕТ КООРДИНАТ ТОЧЕК ПРОФИЛЯ ФАСОННЫХ РЕЗЦОВ
4.1. Алгоритм расчета
Алгоритм расчета фасонных резцов состоит из трех этапов. На этапе I определяются значения координат узловых и промежуточных точек профиля детали, на этапе II определяются значения координат точек профиля резца, и на этапе III определяются размеры профиля резца от измерительной базы. Расчеты на этапах I и II выполняются одинаково для всех типов резцов.
Этап I. Определение координат точек профиля детали (см. рис. 9). Сначала выбирается база для линейных размеров. Такой базой является та торцовая поверхность детали, от которой заданы линейные размеры. Если линейные размеры проставлены цепью (рис. 17, а), то необходимо их пересчитать так, чтобы они были заданы от одной базы БТ (рис. 17, б). Неуказанные допуски размеров назначаются по 14 квалитету.
Далее определяются узловые точки, которыми являются точки начала и конца каждой поверхности детали. Узловые точки нумеруются, начиная от базового торца.
25
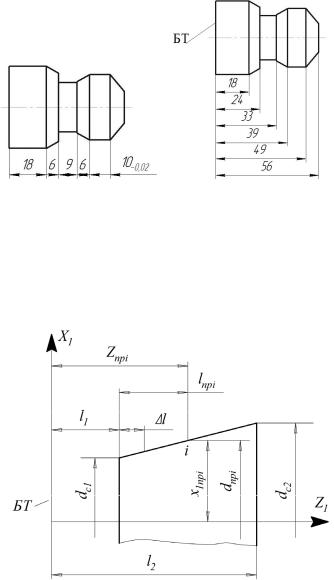
а |
б |
Рис. 17. Простановка линейных размеров:
а– на чертеже детали; б – от базы БТ для расчета координат
1.Координаты узловых (начала и конца поверхности) точек (рис. 18) определяется по формуле:
xi = 0,5dci = 0,5(di +esi −0,5Tdi ) . |
(4.1) |
Рис. 18. Определение координат узловых и промежуточных точек
26
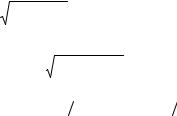
Координата Zi равна расстоянию от базового торца li узловой
точки.
2. Координаты промежуточных точек каждой элементарной поверхности определяются следующим образом.
Цилиндрическая поверхность: координаты начала xi и конца xi+1 поверхности определяются по формуле (4.1), координаты Zi = li,
Zi+1 = li+1.
Коническая поверхность. Для неточных конических поверхно-
стей (фаски и т.п.) расчет ведут по крайним точкам: |
|
x1 = 0,5dc1 , x2 = 0,5dc2 , Z1 = l1 , Z2 = l2 , |
(4.2) |
где dc1, dc2 – средние диаметры узловых точек, сопряженных с конической поверхностью поверхностей; l1 ,l2 – расстояния от базо-
вого торца (БТ) до узловых точек конической поверхности.
Для точных конических поверхностей расчет ведут по 10 точкам
поверхности, разделяя ее на участки (рис. 18): |
|
l = (l2 −l1 ) / 9 . |
(4.3) |
Координаты крайних узловых точек определяют по формулам (4.3), а промежуточных – по формулам
Xпрi = 0,5dc1 +lпрi [(dc1 −dc2 ) / 2(li −li−1)], |
|
Zпрi = l1 +lпрi , |
(4.4) |
где lпрi = ln, n = 0;1;2...9.
Поверхность, описанная дугой окружности (торовая поверх-
ность). Если поверхность неточная, то расчет выполняется для крайних узловых точек по (4.2), а радиус поверхности сохраняется. Для точных поверхностей расчет выполняется по 10 точкам. Длина хорды (рис. 19):
c = |
(l |
−l )2 |
+ |
(dc1 −dc2 )2 |
. |
(4.5) |
|
||||||
|
i−1 |
i |
4 |
|
|
|
|
|
|
|
|
||
Расстояние от центра 0 дуги до хорды |
|
|||||
|
h = r2 |
−0,25c2 . |
(4.6) |
|||
|
|
c |
|
|
|
|
Координаты средней точки М хорды: |
|
|||||
Xм = (dc1 +dc2 ) |
4, Zм = (li−1 +li ) 2 . |
(4.7) |
Угол между хордой и положительным направлением оси
27
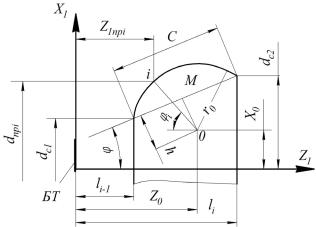
ϕ = arctg |
dc2 −dc1 |
. |
|
|
|
|
(4.8) |
||||
|
|
|
|||||||||
|
|
|
2(li−1 −li ) |
|
|||||||
Координаты центра дуги: |
|
|
|
|
|
|
|
|
|
||
X0 = Xм + K1h |
|
cos ϕ |
|
, Z0 = Zм + K2h |
|
sin ϕ |
|
, |
(4.9) |
||
|
|
|
|
где K = ±1 – число, характеризующее вид поверхности и расположение центра 0 относительно ее границ.
Рис.19. Определение координат промежуточных точек торовой поверхности
Правило знаков следующее: |
|
|
|
– если поверхность выпуклая и ϕ<90° K1 |
= −1; |
K2 = +1 ; |
|
– если поверхность выпуклая и ϕ >90° K1 |
= K2 |
= −1; |
|
– если поверхность вогнутая и ϕ<90° K1 |
= +1; |
K2 = −1; |
|
– если поверхность вогнутая и ϕ >90° K1 |
= K2 = +1. |
Координаты промежуточных точек (радиус rс со знаком + для выпуклых, со знаком – для вогнутых поверхностей):
Xпрi = X0 +rc |
|
sin ϕi |
|
; Zпрi =li−1 +lпрi , |
(4.10) |
||||||
|
|
||||||||||
где ϕi = arccos |
Z0 |
−(li−1 |
+lпрi |
|
) |
; lпрi = ln; |
l = (li −li−1 ) / 9; |
|
|||
|
|
rc |
|
|
|
|
|||||
|
|
|
|
|
|||||||
|
|
|
|
|
|
|
|
|
|
|
|
n = 0,1, 2,...,9. |
|
|
|
|
|
|
|
|
|
|
|
|
|
|
|
|
|
|
28 |
|
|

Координаты точек поверхности, заданной произвольной кривой, определяются так же, как для узловых точек, так как на чертежах размеры таких поверхностей задаются координатным методом.
Этап II. Определение координат точек профиля детали в порядке их расположения относительно базового торца, X2i, Z2i – координаты соответствующих точек профиля резца.
1.Передний γ и задний α углы и угол наклона базы ε назначают по рекомендациям раздела 2.2.
2.Наружный диаметр круглого резца:
– для наружного точения |
|
D = (6...8)tmax ; |
(4.11) |
– для внутреннего точения |
|
D = 0,75D0 , |
(4.12) |
где tmax – максимальная глубина профиля детали; D0 – диаметр от-
верстия до обработки.
Значение рассчитанного диаметра В округляется до ближайшего стандартного значения (см. табл. 2 в п. 5).
3. Определяют радиус базовой точки на профиле детали:
– при наружном точении – это минимальный радиус детали
r= rmin,
–при внутреннем точении – максимальный радиус детали
r = rmax.
Примечание. По формулам, кроме формулы (4.15), расчет про-
водить для всех точек профиля. |
|
|
4. Вспомогательные величины: |
|
|
sin F =(Zi sin ε+r cos ε)sin γ/ A; |
(4.13) |
|
A = x sin2 γcos2 ε+cos2 |
γ; |
(4.14) |
i |
|
|
tgϕ = tgγcosε; |
|
(4.15) |
t = F −ϕ. |
|
(4.16) |
5. Координаты поверхности детали в системе S0 :
xi1 = xi cost,yi1 = xi sin t,
zi1 = zi .
x0i = (xi1 −r)cos γcosε− yi1 sin γ−Zi1 cos γsin ε;
29
y0i =(xi1 −r )sin γcosε+ yi1 cos γ −Zi1 sin γsin ε; |
(4.17) |
|
z0i =(xi1 −r )sin ε+ zi cos ε. |
||
|
||
6. Координаты точек профиля: |
|
|
а) призматический резец |
|
|
x2i = x0i cos(α+ γ)+ y0i sin(α+ γ); z2i = z0i ; |
(4.18) |
б) круглый резец: сначала вычисляем величину hр (см. рис. 7) установки резца на станке по формуле (2.2) и округляем её до десятых долей миллиметров, далее вычисляем фактическое значение заднего угла α:
|
α = arcsin(hp / 2D); |
|
(4.19) |
|
tgτ = |
0,5Dsin (α+ γ) − y0i |
; |
|
|
0,5D cos(α+ γ) − x0i |
|
|||
1 |
|
|
|
|
|
|
|
|
|
x2i = x0i cos τi + y0i sin τi −0,5D cos(α+ γ −τi ); |
(4.20) |
|||
|
|
z2i = z0i . |
|
|
Тангенциальные фасонные резцы. |
|
|
||
1. Вспомогательный угол |
|
|
||
|
|
θ = arccos(dmin / d ), |
|
(4.21) |
где dmin – минимальный диаметр профиля детали; d3 – диаметр
заготовки.
Если θ > 42°, то обработку детали необходимо выполнять за несколько проходов. Приняв припуск на чистовую обработку 2...3 мм на диаметр, определяют угол θ по формуле (4.21) при значении d3 = dmin +(2...3) мм.
1.Задний угол в момент профилирования α = 2,5...7°.
2.Передний угол в момент профилирования (см. п. 3.2)
γ = θ+(0...5°) . |
(4.22) |
3. Радиус базовой точки профиля детали |
|
r = rmin . |
(4.23) |
4. Координаты точек профиля резца (расчет выполнять для каж-
дой точки профиля детали): |
(xi −r)cos(α+ γ) |
|
|
|
|
x2i = z0i tgλsin α− |
|
; z2i = z0i . |
(4.24) |
||
cos γ |
|||||
|
|
|
|||
|
30 |
|
|
|