
Дерябин Проектирование сложнопрофилныкх зуборезныкх инструментов 2015
.pdfМинистерство образования и науки Российской Федерации
НАЦИОНАЛЬНЫЙ ИССЛЕДОВАТЕЛЬСКИЙ ЯДЕРНЫЙ УНИВЕРСИТЕТ «МИФИ»
Трехгорный технологический институт
И.П. Дерябин, И.Н. Миронова
ПРОЕКТИРОВАНИЕ
СЛОЖНОПРОФИЛЬНЫХ ЗУБОРЕЗНЫХ ИНСТРУМЕНТОВ
Рекомендовано к изданию УМО "Ядерные физика и технологии"
Москва 2015
УДК 621.9.02.001.2(076.5) + 621.914.6(076.5) ББК 34.63-5 Д369
Дерябин И.П., Миронова И.Н. Проектирование сложнопрофильных зуборезных инструментов: Учебное пособие. – М.: НИЯУ МИФИ, 2015. – 60 с.
Учебное пособие составлено в соответствии с Государственным образовательным стандартом по дисциплине «Режущий инструмент» и «Процессы и операции формообразования». Изложена методика проектирования сложнопрофильных режущих инструментов, предназначенных для обработки зубчатых колес, к которым относятся червячные зуборезные инструменты. Приведены конструктивные элементы, обширная база данных, алгоритмы расчёта фрез и необходимые приложения, облегчающие расчёты и выполнение курсового проекта. Даны варианты заданий для выполнения курсового проекта.
Учебное пособие предназначено для бакалавров по направлению 15.03.05 «Конструкторско-технологическое обеспечение машиностроительных производств» и специалистов по направлению 15.05.01 «Проектирование технологических машин и комплексов» при выполнении курсовых и дипломным проектов, в том числе с использованием САПР металлорежущих инструментов, а также для инженеров конструкторскотехнологических служб машиностроительных и приборостроительных предприятий.
Пособие подготовлено в рамках Программы создания и развития НИЯУ МИФИ.
Рецензент д-р техн. наук, проф. Б.А. Лопатин
ISBN 978-5-7262-2169-4 © Национальный исследовательский ядерный университет «МИФИ», 2015
Предисловие
Повышение экономической эффективности промышленности за счет интенсификации производственных и технологических процессов неразрывно связано с увеличением производительности технологического оборудования. Одним из основных методов увеличения производительности является применение сложнопрофильных режущих инструментов.
Из механических передач, применяемых в современных машинах и механизмах, наибольшее распространение получили передачи зубчатые благодаря высокой нагрузочной способности, компактности, кинематической точности и ряду других достоинств.
Претерпев длительный путь развития, теория передач зацеплением
внастоящее время имеет эффективный аналитический аппарат, позволяющий совершенствовать старые и создавать новые системы зубчатых зацеплений. Поскольку качественные характеристики зубчатого зацепления при его эксплуатации в значительной мере зависят от правильности изготовления его звеньев, к зуборезным инструментам, оборудованию и технологическим процессам предъявляются жесткие требования.
Боковые поверхности зубьев зубчатых колес, составляющие высшую кинематическую пару в процессе передачи движения и воспринимающие нагрузку, образуются в станочном зацеплении. В целях повышения точности и производительности обработку зубчатых колес проводят по методу центроидного огибания или методу обкатки.
При таком методе обработки боковые поверхности зубьев зубчатых колес являются огибающими производящей поверхности инструмента
вотносительном движении в станочном зацеплении. Производящей поверхностью инструмента называют поверхность, которую описывают в пространстве его режущие кромки. Отсюда следует, что в зависимости от формы профиля боковой поверхности зуба колеса и схемы станочного зацепления необходимо отыскать такую производящую поверхность, а также и форму режущих кромок, которые обеспечат требуемую форму профиля зуба колеса. Решение этой задачи состав-
3
ляет первый этап расчета зуборезного инструмента. Для решения этой задачи используется аналитический аппарат теории огибающих. Второй этап расчета зуборезных инструментов заключается в том, чтобы правильно назначить параметры конструктивных элементов инструмента: диаметр, число зубьев и т.д.
Проектирование зуборезных инструментов связано с выполнением большого объема расчетов. В связи с этим в последнее время большое внимание уделяется разработке систем автоматизированного проектирования таких инструментов. В учебном пособии описан алгоритм расчета для таких систем, а также приведены методы расчета и проектирования инструментов для обработки зубчатых колес с эвольвентным профилем зубьев внешнего зацепления и шлицевых валов с эвольвентным и прямолинейным профилем зубьев. Наибольшую производительность и точность обработки такого типа изделий обеспечивают червячные зуборезные инструменты.
Материалы данного учебного пособия необходимы для формирования у студентов следующих компетенций:
–способности собирать и анализировать исходные информационные данные для проектирования технологических процессов изготовления машиностроительной продукции, средств технологического оснащения, автоматизации и управления (ПК-5);
–способности принимать участие в разработке средств технологического оснащения машиностроительных производств (ПК-9);
–способности разрабатывать проектную и рабочую техническую документацию машиностроительных производств, оформлять законченные проектно-конструкторских работы (ПК-14);
–способности участвовать в организации выбора технологий, средств технологического оснащения, вычислительной техники для реализации процессов проектирования, изготовления, технологического диагностирования и программных испытаний изделий машиностроительных производств (ПК-39).
4
1. ОСНОВНЫЕ ПАРАМЕТРЫ ЗУБОРЕЗНЫХ ЧЕРВЯЧНЫХ ФРЕЗ
Червячные фрезы применяют для обработки прямозубых, косозубых и шевронных цилиндрических колёс, а также для нарезания зубьев червячных колёс с различными видами зацепления. Червячная фреза как инструмент получается из червяка путём прорезания канавок, образующих переднюю поверхность зубьев и пространство для размещения стружки, и затылования зубьев для создания задних углов по всему контуру.
По конструктивному исполнению червячные фрезы бывают цельные, насадные и сборные. По виду обработки они подразделяются на черновые (многозаходные), чистовые и прецизионные. По виду исходного червяка, положенного в основу червячной фрезы, они бывают эвольвентные, архимедовы, конволютные для нарезания колёс с эвольвентным зацеплением.
Для нарезания зубчатых колёс с циклоидальным зацеплением и с зацеплением Новикова применяют фрезы, в основу которых положены соответствующие червяки.
Червячные фрезы работают на специальных зубофрезерных станках моделей 5К301, 5К320, 5К32 и др., а также на тяжёлых станках моделей 5342, 5345, 5364. В процессе нарезания фреза и заготовка вращаются относительно своих осей. За один оборот фрезы заготовка повернётся на 1/z1 при однозаходной фрезе и на z0/z1, если фреза многозаходная (здесь z1 – число зубьев нарезаемого колеса, z0 – число заходов фрезы). Кроме того, на станке выполняются движение врезания инструмента в радиальном направлении к заготовке и движение суппорта для подачи. Подачу инструмента осуществляют вдоль оси заготовки при обработке цилиндрических колёс; в радиальном направлении – при обработке червячных колёс или цилиндрических колёс с узким ободом и в тангенциальном направлении к заготовке – при нарезании червячных колёс [4–6].
Метод зубофрезерования червячными фрезами является высокопроизводительным и универсальным и получил широкое распространение во всех видах производств для обработки цилиндрических и червячных колёс. Обработка ведется непрерывно по методу обката. Одна червячная фреза может обрабатывать колёса с любым числом зубьев данного модуля. Недостатком метода зубофрезеро-
5

вания при осевой и радиальной подачах является ограниченность числа резцов, огибающих профиль зубьев обрабатываемого колеса; вследствие этого шероховатость обработанной поверхности зубьев в ряде случаев высокая.
Число резов, профилирующих каждую боковую сторону зуба изделия,
zпроф = nпрофz, |
(1.1) |
где nпроф = l/P0 – число витков фрезы, участвующих в профилировании (зацеплении); l – активная длина линии профилирования (зацепления); Р0 – шаг между зубьями фрезы в направлении линии профилирования, т.е. основной шаг; z – число зубьев фрезы.
Длина |
|
|
|
l = r2 |
−r2 |
, |
(1.2) |
a |
0 |
|
|
где ra и r0 –радиусы соответственно наружной и основной окружностей нарезаемого колеса. Чем больше число зубьев фрезы z и число зубьев колеса z1 и чем меньше угол профиля зубьев фрезы, тем больше огибающих резов.
При проектировании зуборезных червячных фрез должны быть заданы некоторые параметры зубчатого колеса: модуль m, угол давления на делительном диаметре, т.е. угол зацепления α, высота зуба h1 и высота головки зуба ha. Передний угол γ принимают для вершины режущих кромок и задний угол δa по наружному диаметру. Для стандартных фрез γ = 0, δa = 10…12°.
В зависимости от вида и точности обработки колеса выбирают также число заходов фрезы и класса её точности. Для чистовой обработки применяют однозаходные фрезы, для черновой, предварительной – многозаходные (рис. 1.1).
Основными конструктивными параметрами червячной фрезы являются наружный диаметр da0, длина L, диаметр отверстия под оправку dотв, число зубьев z, угол наклона ω0 и направление канавок, размеры профиля зубьев. Наружный диаметр фрезы da0 принимается по нормалям и стандартам с учётом паспортных данных зубофрезерного станка, или же задаются углом подъёма витков исходного червяка γ0 и определяют делительный d0, а затем наружный диаметр фрезы. При определении диаметра надо учитывать следующие противоречивые обстоятельства: с одной стороны, чем больше диаметр фрезы, тем выше точность и производительность
6

обработки; с другой стороны, с увеличением диаметра фрезы она становится дороже, увеличиваются крутящий момент и длина врезания в заготовку. Для чистовых фрез рекомендуется принимать диаметр больше, чем для черновых, а для прецизионных ещё больше, чем для чистовых. ГОСТ 9324-80 установил диаметр фрез общего назначения для m = 1–25 мм от 71 до 305 мм.
Рис. 1.1. Конструктивные параметры червячной фрезы
При определении диаметра расчётным способом сначала задают угол подъёма витков γ0. Для чистовых фрез γ0 = 3…5°, для прецизионных его принимают равным до 3°.
При равенстве ω0 = γ0
sin γ |
|
= |
πm |
= |
m |
, |
(1.3) |
0 |
πd0 |
|
|||||
|
|
|
d0 |
|
отсюда делительный диаметр
d0 = |
m |
. |
(1.4) |
|
|||
|
sin γ0 |
|
Наружный и внутренний диаметры
dа0= d0 + 2 ha0; df0= d0 – 2 hf0, (1.5)
где ha0, hf0 – высота головки и ножки зубьев фрезы, обычно равны
1,25…1,3m.
7
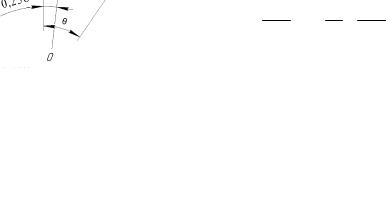
По мере переточки зубьев по передней поверхности диаметры фрезы уменьшаются вследствие наличия заднего угла. При этом будет увеличиваться угол подъёма винтовой линии γ0 и уменьшаться угол наклона канавки ω0 на делительном диаметре фрезы. Всё это изменяет теоретический необходимый профиль зубьев. Действительный же профиль не меняется и остаётся постоянным при затыловании резцом, когда образующими затылованных поверхностей являются режущие кромки зубьев фрезы. При шлифовании затылованных поверхностей действительный профиль зубьев по мере переточки будет изменяться. В результате возникает погрешность профиля. Чтобы уменьшилась эта погрешность, у червячных фрез (рис. 1.2) расчётное сечение 0–0 не должно совпадать с начальным сечением 1–0 для новой фрезы. Это несовпадение со-
ставляет (0,15…0,25)Рz или (0,15…0,25)θ, где Рz и θ – соответст-
венно окружной и угловой шаг между зубьями (канавками) фрезы:
Pz = πdza0 , θ = 2zπ = 360z ° , (1.6)
где z – число зубьев фрезы.
В конечном сечении 2–0, соответствующим окончательно сточенной фрезе (примерно на 2/3 толщины зуба) d2, da2 и df2 по сравнению с расчетными уменьшаются на 0,5k. Величина затылования для однозаходных фрез
Рис. 1.2. Сечение зуба фрезы |
|
|
|
|
k1 = |
πda0 |
|
tgδa , |
(1.7) |
||
|
|
|
|
z |
|||||||
|
|
|
|
|
|
|
|
|
|
||
для многозаходных фрез, у которых большой угол γ0, |
|
|
|||||||||
k |
= |
πda0 |
tgδ |
a |
cosγ |
0 |
. |
|
|
|
(1.8) |
|
|
|
|
||||||||
1 |
|
z |
|
|
|
|
|
|
|
||
|
|
|
|
|
|
|
|
|
|
|
Диаметр отверстия под оправку можно рассчитать из условия прочности и жёсткости, затем расчётное значение скорректировать по нормальному ряду диаметров оправок по ГОСТ 9472-90. Ориентировочно диаметр посадочного отверстия dотв = (0,20…0,45)da0. Для повышения жёсткости диаметр отверстия надо принимать по возможности большим. После этого необходимо проверить, чтобы
8
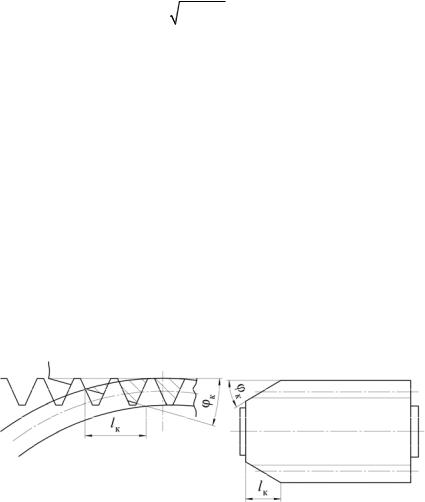
расстояние между дном стружечной канавки и шпоночным пазом, т.е. толщина стенки фрезы t ≥ (0,25…0,3) d.
Длина режущей части фрезы
l = 2 |
r2 |
−r2 |
+(3...9)P |
, |
(1.9) |
ф |
a0 |
f 0 |
x0 |
|
|
где ra0, rf0 – радиус наружной и внутренней окружности колеса; Рх0
– осевой шаг между зубьями фрезы.
Ширина буртиков принимается lб = 3…5 мм. Они служат для контроля биения фрезы при изготовлении и установке её на оправку шпинделя зубофрезерного станка. Таким образом, общая длина фрезы L = lф + 2lб. Диаметр буртиков D = (1,5…1,7)dотв. Их делают на 1…2 мм ниже дна стружечной канавки.
Из уравнения (1.9) видно, что чем больше модуль и диаметр нарезаемого колеса, тем больше длина фрезы. Например, для колеса m = 5 мм, диаметром 500 мм длина фрезы должна быть около 300 мм. Длину фрезы можно уменьшить, если её сделать с заборным конусом (рис. 1.3). В этом случае не только изменяются размеры фрезы, (фреза становится короче), но и происходит перераспределение нагрузки на режущие зубья. При зубофрезеровании наибольшую площадь срезают зубья, входящие в работу. Делая заборный конус, мы более равномерно распределяем работу резания на другие зубья вдоль оси фрезы. Вследствие этого происходит более равномерное изнашивание инструмента. Длина заборного конуса lк делается 1,5…2 шага, а его угол φк = 18…30°.
Рис. 1.3. Фреза с заборным конусом
Число зубьев z должно быть по возможности наибольшим. С увеличением z увеличивается число резцов, уменьшается шероховатость поверхности, уменьшается толщина срезаемого слоя. Число
9
зубьев насадных цельных фрез ограничивается условиями затылования, а сборных – условиями крепления зубьев. Для червячных фрез обычной точности z = 12–9, для прецизионных z = 16–12, для сборных затылованных z = 10–8.
Канавки, образующие переднюю поверхность зубьев и пространство для размещения стружки, могут быть винтовыми, перпендикулярными виткам зубьев фрезы на делительном диаметре в расчётном сечении, и прямыми, проходящими через ось, если передний угол γ = 0, или параллельными оси, если γ0 ≠ 0.
Стандартные фрезы изготовляют с канаками первого типа. Шаг винтовой канавки Р = πd0·ctgω0. Передние углы для левой и правой режущих кромок у таких фрез получаются одинаковыми.
Фрезы с прямыми канавками проще в заточке и изготовленные на основе архимедова червяка имеют меньшее теоретическое изменение профиля при переточках. Однако передние углы γ для левой и правой режущей кромок у них разные: с одной стороны в осевом направлении γ = + γ0, с другой стороны γ = –γ0. Поэтому фрезы с прямыми канавками делают с небольшими углами подъёма витков
γ0 = 3…5°.
Глубина канавки для фрез с одним затылованием
Н = h0 + k1+ r. (1.10)
При двойном затыловании
H = h |
+ |
k 1 +k2 |
+r , |
(1.11) |
|
||||
0 |
2 |
|
|
|
|
|
|
||
где h0 – высота зуба фрезы, обычно h0 = 2,5m; k и k1 |
– величины |
затылования шлифованной и нешлифованной части зуба, k2 =
=(1,25…1,6)k1; r – радиус закругления дна канавки, обычно r =
=1…3 мм.
Для фрез, имеющих модуль более 5 мм, как правило, делается двойное затылование, так как из-за опасности срезания кругом режущей кромки следующего зуба при одинарном затыловании значительная часть зуба получается незатылованной. Поэтому сначала до термообработки фрезы делают резцом второй затылок на величину k1, а затем первый затылок на величину k – шлифовальным кругом после термообработки. Считается нормальным, если длина шлифованного затылка равна 0,5Р, т.е. доходит до сечения фрезы 2–0 (см. рис. 1.2). Угол канавки ε = 20…30°. Стандартные червячные фрезы имеют передний угол γ = 0 и задний угол по наружному
10