
Дерябин Проектирование сложнопрофилныкх зуборезныкх инструментов 2015
.pdf
диаметру δa = 10…12°. Червячные фрезы могут проектироваться и изготовляться и с положительным передним углом γ = 10…15°. В сечении, нормальном к боковым режущим кромкам, задний и передний углы будут иными, значительно меньшими, чем для вершинной режущей кромки.
На рис. 1.4 показана схема определения боковых задних углов в нормальном сечении. Из рисунка видно, что
KKn =sin αn ; Kn = πdzа0 tgαn ;
K = πdza0 tgδa .
Разделив первое выражение на второе, получим
tgαn = tgδa·sinαn.
Аналогичное выражение можно получить и для переднего угла в нормальном сечении к боковым режущим кромкам
tgγn = tgγ·sinδa.
С учётом того, что задние поверхности винтовые, задний угол в нормальном сечении к боковым режущим кромкам
tgαn = Ra0 tgδa sin α cosγC ,
RС
где Rа0 – радиус вершин зубьев фрезы; RC – радиус фрезы для рассматриваемой точки С; γС – угол подъёма винтовой линии на цилиндре радиусом RC.
Анализ этих уравнений показывает, что на боковых режущих кромках углы резания получаются недостаточными. Так, для фре-
зы, у которой α = 20°, γ = 10°, δa = 10…12°, имеем γn = 2°30`, αn = = 2°30`…3°.
2. ТОЧНОСТЬ ЧЕРВЯЧНЫХ ФРЕЗ
По ГОСТ 9324-80 цельные червячные фрезы изготовляют пяти классов точности: АА, А, В, С, D с модулем m = 1–20 мм. При m = = 8–25 мм их делают сборными классов точности А, В, С и D. Фрезы класса АА применяют для нарезания зубчатых колёс 7-й степе-
11
ни точности; фрезы класса точности А служат для нарезания колёс 8 степени точности; фрезы класса В – для колёс 9-й степени точности, и колёса 10-й степени точности нарезают фрезами классов С и D, которые можно делать с нешлифованным профилем.
Мелкомодульные фрезы с m = 0,15–0,9 мм изготавливаются по ГОСТ 10331-81 диаметром Da0 = 25 и 32 мм четырёх классов точности ААА, АА, А и В. Фрезы класса ААА применяют для нарезания зубьев цилиндрических колёс 5-й и 6-й степени точности. Причём большое значение имеет точность базирования фрезы по отверстию. Отверстие под оправку тщательно шлифуется и выполняется с точностью 5–7-го квалитета.
Точность изготовления фрез проверяется по отдельным элементам конструкции, основными из которых являются: отклонение толщины зуба, профиль передней поверхности зубьев, радиальное и торцовое биение буртиков, погрешность шага винтовых стружечных канавок, радиальное биение по вершинам зубьев, погрешность винтовой линии фрезы, погрешность профиля; погрешность осевого шага, конусность по наружному диаметру, разность соседних окружных шагов и накопленная погрешность окружного шага стружечных канавок погрешность зацепления.
Нормы точности изготовления различных фрез в зависимости от модуля приводятся в указанных ГОСТах.
Число заходов чистовых фрез z0 = 1. Число заходов фрез под шевингование преимущественно принимается равным 1; в массовом производстве зубчатых колес с нечетным числом зубьев иногда принимается z0 = 2, с четным числом зубьев – z0 = 3. Следует иметь в виду, что увеличение числа заходов фрезы приводит к увеличению погрешностей шага зубьев из-за погрешностей деления на заходы при изготовлении инструмента.
Число зубьев z (стружечных канавок) червячной фрезы выбирается в зависимости от класса точности и модуля. Для прецизионных (класса АА) червячных фрез и фрез многозаходных (z0 > 1) в зависимости от модуля m рекомендуется принимать: m = 1–1,75 мм и z = 16; m = 2–5,5 мм и z = 14; m = 6–10 мм и z = 12.
Для чистовых и черновых фрез общего назначения, однозаходных фрез под шевингование, т.е. с модифицированным профилем рекомендуется принимать: m = 1–2,75 мм и z = 12; m = 3–6 мм и z = = 10; m = 6,5–12 мм и z = 9.
12
Геометрические параметры фрезы: передний угол γ = 0°, задний угол δa= 9–12°. Увеличение переднего и заднего угла до определенных пределов увеличивает период стойкости инструмента. Увеличение переднего угла γ до определенного для каждого модуля значения позволяет увеличить точность профиля нарезаемого этим инструментом зубчатого колеса, но увеличивает трудности переточки инструмента. На производстве по пути увеличения переднего угла, как правило, не идут. Из-за трудностей шлифования задних поверхностей зубьев фрез с увеличением заднего угла его не рекомендуется увеличивать больше 12°.
3. ИСХОДНЫЙ И ИСХОДНЫЙ ПРОИЗВОДЯЩИЙ КОНТУРЫ
Основные параметры зубьев зубчатых колес определяются размерами исходного контура зубчатой рейки. Подобно этому размеры зубьев зуборезного инструмента характеризуются параметрами исходного контура инструментальной рейки, положенной в основу конструкции данного инструмента. Аналогично исходному контуру при зубонарезании вводится понятие: теоретический исходный производящий реечный контур (исходный производящий) – это контур зубьев рейки, заполняющий впадины исходного контура так, чтобы между линией впадин исходного производящего контура и линией вершин исходного контура оставался зазор с*m. Этот зазор исключает из процесса резания поверхности впадин инструмента.
Форма зуба инструментальной рейки соответствует форме впадины между зубьями нарезаемого колеса, и зуборезный инструмент работает в паре с нарезаемым колесом без бокового и радиального зазоров. Поэтому различие между указанными рейками сводится к следующему: толщина зуба зубчатой рейки (ГОСТ 13755-81) S1 = πm/2. В действительности зубчатые колеса изготовляются с обязательным боковым зазором, т. е. с уменьшенной толщиной зуба S1 < πm/2. Это утонение зуба нарезаемого колеса достигается путем смещения инструмента к центру колеса на величину, регламентируемую допусками на зубчатые колеса.
13
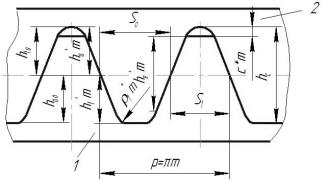
Размеры зубьев колёс эвольвентного зацепления определяются параметрами исходного контура (рис. 3.1). Параметры исходного контура стандартизированы (табл. 3.1) [2].
Рис. 3.1. Исходный (1) и исходный производящий (2) контуры
|
|
|
Таблица 3.1 |
Параметры исходного контура (ГОСТ 13755-81) (mn ≥ 1 мм) |
|||
|
|
|
|
Наименование параметра |
Обозначение |
Численное значение |
|
Угол главного профиля |
|
α |
20 |
Коэффициент высоты го- |
|
h* |
1 |
ловки |
|
a |
|
Коэффициент радиального |
|
с* |
0,25 |
зазора |
|
|
|
Коэффициент высоты ножки |
h* |
= h* +c* |
1,25 |
|
f |
a |
|
Коэффициент радиуса кри- |
|
ρ* |
0,38 |
визны переходящей кривой |
|
f |
|
Коэффициент граничной |
|
h* |
2 |
высоты |
|
l |
|
Коэффициент глубины за- |
|
h* |
2 |
хода зубьев в паре исходных |
|
||
контуров |
|
ω |
|
|
|
|
В обоснованных случаях параметры исходного контура могут быть измены. Например, для передач, нарезаемых долбяками, допускается увеличение с* до 0,35.
14

Для улучшения работы высокоскоростных и тяжелонагруженных зубчатых передач с внешними зубьями исходный контур модифицируют. Параметры модификации (рис. 3.2): коэффициент
высоты модификации |
h* |
и коэффициент глубины модификации * |
|
g |
|
назначаются конструктором.
Для передач с mn = 1 мм значения параметров модификации hg* ≤ 0,45 , * ≤0,02 .
а б
Рис. 3.2. Параметры модификации исходного контура (а) и график выбора величины * (б)
Параметры исходного контура эвольвентных шлицевых соединений с углом профиля α = 30° регламентированы ГОСТ 6033-80 (табл. 3.2).
Геометрические параметры зубчатых колёс эвольвентных передач определяются по методике, приведённой в работе [3], а размеры валов и втулок эвольвентных шлицевых соединений по ГОСТ
6033-80.
Согласно ГОСТ 16530-83 геометрическим параметрам зубчатых колёс и инструмента присваиваются следующие индексы:
а – относящийся к поверхности вершин и к головке зуба; b – относящийся к основной окружности;
f – относящийся к поверхности впадин и к ножке зуба;
n – нормальный или относящийся к нормальному сечению;
t – окружной торцовый или относящийся к торцовому сечению; w – относящийся к начальной поверхности;
х – осевой или относящийся к осевому сечению;
15
у – относящийся к любой сосной поверхности или окружности; р – относящийся к нижней точке активного профиля;
g – относящийся к начальной точке модификации у вершины зуба;
q – относящийся к начальной точке модификации у основания зуба.
Цифровые индексы относятся соответственно:
1 – к шестерне и колесу, для нарезания которого рассчитывается инструмент;
2 – к колесу передачи и к колесу, образующему передачу с колесом, для которого рассчитывается инструмент;
0 – к инструменту;
01 – к станочному зацеплению.
Таблица 3.2
Параметры исходного контура эвольвентных соединений с углом профиля 30° (ГОСТ 6033-80)
|
|
Величина параметра |
|
||
|
Центрирование |
|
Центрирование по боковым |
||
Параметр |
по наружному |
|
поверхностям при форме |
||
|
диаметру |
|
дна впадины |
||
|
соединения |
|
плоской |
|
закруглённой |
Вал |
|
|
|
|
|
h* |
0,55 |
|
0,45 |
|
0,45 |
a |
|
|
|
|
|
h*f |
0,55…0,65 |
|
0,55…0,65 |
|
0,83 |
|
|
|
|
|
|
Втулка |
|
|
|
|
|
Ha* |
0,45 |
|
0,45 |
|
0,45 |
H*f |
0,55 |
|
0,55…0,65 |
|
0,77 |
K* |
0,15 |
|
0,15 |
|
0,15 |
Соединение |
|
|
|
|
|
ρ*f |
0,15 |
|
0,15 |
|
0,15 |
c* |
0,1 |
|
0,1 |
|
0,1 |
min |
|
|
|
|
|
Для построения производящей поверхности режущего инструмента используется исходный производящий контур (см. рис. 3.1).
16

Высотные размеры зуба исходного производящего реечного контура определяются по формулам:
h |
= h* m ; |
h |
f 0 |
= (h* +c* )m ; |
h = h |
+h |
f 0 |
. |
(3.1) |
|
a0 |
f n |
|
a |
n |
0 a0 |
|
|
|
Толщина зуба инструмента по делительной прямой отличается от теоретического значения толщины зуба исходного производящего реечного контура:
S0 = 0,5πmn ± S . |
(3.2) |
В формуле (3.2) верхний знак (+) относится к инструментам, обрабатывающим колесо окончательно (чистовые инструменты), нижний (–) – к инструментам, обрабатывающим колесо под последующую чистовую обработку (черновые инструменты).
Величина S определяется в зависимости от назначения инструмента. Для чистовых инструментов, обрабатывающих зубчатые колёса,
S = 2EHs tgα, |
(3.3) |
где EHs – наименьшее дополнительное смещение исходного производящего контура, необходимое для обеспечения минимального гарантированного бокового зазора между неработающими сторонами зубьев в передаче. Величина EHs назначается по ГОСТ 164381 (табл. 3.3).
Для черновых инструментов, обрабатывающих зубчатые колёса, величина S равна припуску на толщину зуба под последующую обработку.
Для нарезания черновым инструментом под чистовое зубофрезерование или зубодолбление
S =1,2 |
3 m tgα. |
(3.4) |
|
n |
|
Для нарезания колёс под шевингование или шлифование зубьев
S =0,5 |
3 m tgα . |
(3.5) |
|
n |
|
Величина S для чистовых инструментов, обрабатывающих детали с эвольвентными шлицами, определяется по формулам:
для втулки
S = EIе, |
(3.6) |
для вала |
|
S = esе. |
(3.7) |
17
Значения отклонений EIе и esе принимать по ГОСТ 6033-80 и в формулу (3.2) подставлять с учётом знака отклонения.
Для черновых инструментов, обрабатывающих детали с эвольвентными шлицами, величину S определять по формулам (3.4), (3.5).
Таблица 3.3
Сопря- |
Степень |
Смещение EHs (мкм) при делительном диаметре |
|||||||||
точности |
|
|
|
колеса, мм |
|
|
|
||||
жение |
по нормам |
до |
до |
до |
до |
до |
до |
до |
до |
до |
|
|
плавности |
80 |
125 |
180 |
250 |
315 |
400 |
500 |
630 |
800 |
|
Н |
3–6 |
12 |
14 |
16 |
18 |
20 |
22 |
25 |
28 |
32 |
|
7 |
13 |
15 |
18 |
20 |
22 |
25 |
28 |
32 |
36 |
||
|
|||||||||||
Е |
3–6 |
30 |
35 |
40 |
46 |
52 |
57 |
63 |
70 |
80 |
|
7 |
34 |
40 |
45 |
50 |
56 |
63 |
70 |
80 |
90 |
||
|
|||||||||||
|
3–6 |
48 |
55 |
63 |
70 |
80 |
90 |
100 |
110 |
125 |
|
D |
7 |
52 |
60 |
70 |
80 |
90 |
100 |
110 |
120 |
140 |
|
|
8 |
55 |
65 |
75 |
85 |
100 |
110 |
120 |
130 |
150 |
|
|
3–6 |
75 |
85 |
100 |
115 |
130 |
140 |
155 |
175 |
200 |
|
С |
7 |
80 |
95 |
110 |
125 |
140 |
150 |
170 |
190 |
220 |
|
8 |
90 |
105 |
120 |
140 |
160 |
170 |
190 |
210 |
240 |
||
|
|||||||||||
|
9 |
100 |
110 |
130 |
150 |
170 |
180 |
200 |
220 |
260 |
|
|
3–6 |
120 |
140 |
160 |
185 |
210 |
230 |
250 |
280 |
320 |
|
В |
7 |
130 |
150 |
170 |
200 |
230 |
250 |
270 |
300 |
350 |
|
8 |
140 |
170 |
190 |
220 |
250 |
280 |
300 |
340 |
380 |
||
|
9 |
160 |
180 |
200 |
240 |
280 |
300 |
320 |
360 |
420 |
|
|
10 |
180 |
200 |
220 |
260 |
300 |
320 |
360 |
400 |
450 |
|
|
3–6 |
190 |
220 |
250 |
290 |
320 |
360 |
400 |
440 |
500 |
|
А |
7 |
200 |
240 |
280 |
320 |
360 |
400 |
440 |
480 |
530 |
|
8 |
220 |
260 |
300 |
340 |
380 |
420 |
480 |
530 |
600 |
||
|
9 |
250 |
280 |
320 |
360 |
420 |
480 |
530 |
600 |
670 |
|
|
10 |
260 |
300 |
340 |
400 |
450 |
530 |
600 |
670 |
750 |
18
4. ПРОЕКТИРОВАНИЕ ЧЕРВЯЧНЫХ ФРЕЗ ДЛЯ ОБРАБОТКИ ЦИЛИНДРИЧЕСКИХ ЗУБЧАТЫХ КОЛЁС
Червячные фрезы для обработки цилиндрических зубчатых колёс и шлицевых валов с эвольвентным профилем зубьев представляют собой инструмент, в который преобразуется исходный производящий червяк, образующий с обрабатываемой деталью сопряжённое станочное зацепление. Станочное зацепление – зацепление инструмента с нарезаемым колесом.
Режущие кромки фрезы являются линиями пересечения поверхности витков исходного производящего червяка передней поверхностью стружечных канавок.
В станочном зацеплении режущие кромки фрезы воспроизводят производящую поверхность, параметры которой в нормальном сечении должны соответствовать заданному исходному производящему контуру. Производящей поверхностью инструмента называется воображаемая поверхность, содержащая режущие кромки или образуемая при их движении, огибающей которой в относительном движении является требуемая боковая поверхность зуба.
Теоретически точную эвольвентную поверхность зуба колеса можно получить, если производящая поверхность червячной фрезы эвольвентная. Однако технологические трудности производства и контроля таких фрез привели к тому, что червячные фрезы конструируют на базе более технологичных архимедовых и конволютных производящих червяков.
Конструктивно червячные фрезы для эвольвентных цилиндрических колёс выполняются насадными, сборными или цельными. Шпоночный паз выполняется, как правило, в посадочном отверстии, но для увеличения диаметра посадочного отверстия, что способствует повышению жёсткости системы СПИД (станок – приспособление – инструмент – деталь), желательно шпоночный паз выполнять на одном из торцов.
Конструкции фрез и требования приведены в ГОСТ 9324-80, 10331-81, 15127-83, 16771-81, 18692-73.
Профиль зубьев червячных фрез под шевингование модифицируют. Профиль зубьев фрезы отличается от профиля исходного производящего контура (рис. 4.1) наличием «усиков» на вершине
19

зуба (для mn = 2–6 мм) или наличием «усиков» и фланка у основания зуба (для mn > 6 мм).
Червячные фрезы цельные изготовляются из быстрорежущих сталей марок Р18, Р12, Р9К5, Р9К10, Р9Ф2К5, Р6М5. Гребёнки сборных червячных фрез выполняют из быстрорежущих сталей и твёрдых сплавов. Корпуса сборных фрез выполняют из сталей 45, 40Х, углеродистых или легированных инструментальных сталей.
Рис. 4.1. Модификации профиля фрезы под шевингование
Зубья червячных фрез выполняются затылованными по архимедовой спирали или по дуге окружности. Затылование по дуге окружности применяется для фрез с относительно небольшой высотой профиля зуба, например, для червячных шлицевых фрез.
Передний угол γ = 0° для чистовых фрез и фрез под шевингование. Для черновых инструментов γ = 9…11°, но при этом требуется корректировка профиля зубьев фрез.
Технические условия на изготовление, контроль и приёмку фрез назначают по ГОСТ 9324-80. Пример выполнения рабочего чертежа приведён на рис. 4.2.
4.1. Алгоритм расчёта червячных фрез
Исходными данными являются параметры исходного контура и геометрические размеры зубчатой передачи [3]. Если по каким-то причинам геометрические размеры зубчатой передачи не указаны на чертеже, то они определяются по зависимостям, приведённым в работе [3] (см. прил. 1).
20