
Дерябин Проектирование сложнопрофилныкх зуборезныкх инструментов 2015
.pdf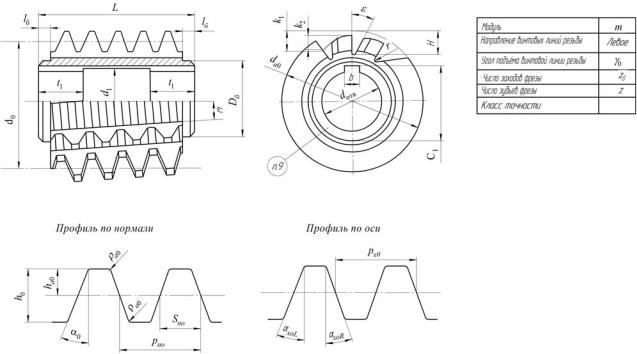
21
Рис. 4.2. Фреза червячная

Алгоритм расчёта включает в себя три этапа:
I.Расчёт параметров исходного производящего червяка фрезы. II. Расчёт параметров профиля зуба фрезы.
III. Расчёт параметров режущей части.
I. Расчёт параметров исходного производящего червяка фрезы
1. Нормальный угол профиля |
|
αn0 = α. |
(4.1) |
Для фрез, обрабатывающих зубчатые колёса с mn < 2 мм под
шевингование или шлифование, |
|
αn0 = α – (0,5…1)°. |
(4.2) |
2.Число витков (заходов) производящего червяка:
–чистовые фрезы – z0 = 1;
–черновые фрезы – z0 = 2–7;
–фрезы под шевингование – z0 = 1–3.
3.Делительный угол подъёма витков производящего червяка для одновитковых фрез назначается ориентировочно по табл. 4.1.
|
|
|
|
|
Таблица 4.1 |
||
|
|
|
Модуль mn, мм |
|
|
||
Класс |
|
|
|
|
|||
точно- |
до 2 |
до 4 |
до 5,5 |
до 8 |
до 14 |
до 20 |
|
сти |
|
Делительный угол подъёма γ0, град |
|
||||
колеса |
|
|
|||||
0,9…1, |
|
|
|
|
|
||
6, 7 |
1,5…2 |
2,1…2,5 |
2,5…2,9 |
2,9…3,0 |
– |
||
3 |
1,5…2, |
||||||
8–10 |
2,7…3,3 |
3,3…3,9 |
4,0…5,7 |
3,7…5,7 |
|||
1…1,5 |
6 |
||||||
|
|
|
|
|
Для многовитковых фрез угол γ0 следует увеличивать при z0 = 2 в 1,8…2 раза, а при z0 > 2 в (z0 – 1) раз по сравнению с углом γ0 одновитковых фрез, принятым по вышеуказанной таблице.
4. Высота делительной головки витка производящего червяка (зуба фрезы)
h |
= m (h* +c* ). |
(4.4) |
a0 |
n a |
|
5. Высота витка производящего червяка (зуба фрезы) |
|
|
h0 |
= h1 +0,3mn . |
(4.5) |
22
6. Делительный диаметр производящего червяка (фрезы) расчётный
d0' = |
mn z0 |
. |
(4.6) |
|
|||
|
sin γ0 |
|
7. Диаметр поверхности вершин производящего червяка (фрезы)
da0 = d0′ +2ha0 . (4.7)
Диаметр поверхности вершин округляют до величины, кратной
0,5 мм.
8. Действительный делительный диаметр производящего червяка (фрезы)
d0 = da0 −2ha0 . |
(4.8) |
9. Делительный угол подъёма витков исходного производящего червяка уточнённый
|
|
|
|
|
||
|
γ0 =arcsin |
mn z0 |
. |
(4.9) |
||
|
|
|
||||
|
|
d0 |
|
|
||
10. |
Нормальный шаг исходного производящего червяка (фрезы) |
|||||
|
pn0 = pn1 = πmn . |
|
(4.10) |
|||
11. |
Осевой шаг производящего червяка (фрезы) |
|
||||
|
px0 = |
pn0 |
. |
|
(4.11) |
|
|
|
|
||||
|
|
cos γ0 |
|
|
||
12. |
Ход витков производящего червяка (фрезы) |
|
||||
|
pz0 = px0 z0 . |
|
(4.12) |
II.Расчёт параметров профиля зуба фрезы
13.Нормальная делительная толщина зуба
– для чистовых, черновых и фрез под шевингование при mn ≥ 2
мм
Sn0 = 0,5 pn0 ± S. |
(4.13) |
Величина S определяется по формулам (3.3)–(3.7) в зависимо- |
|
сти от назначения фрезы; |
|
– для фрез под шевингование при mn < 2 мм |
|
Sn0 =0,5 pn0 −2ha0 (tgα−tgαn0 ). |
(4.14) |
14. Осевая делительная толщина зуба
23

Sx0 = |
Sn0 |
. |
(4.15) |
|
|||
|
cos γ0 |
|
Далее с п. 15 по п. 21 и с п. 24 по п. 27 приводятся расчеты для фрез с модификацией зуба.
15. Модификация головки зуба фрезы (расчёт проводить для фрез под шевингование и шлифование при mn > 2 мм).
15.1. Торцовый угол профиля производящего контура
|
tgα |
n0 |
|
|
||
αt 0 |
=arctg |
|
. |
(4.16) |
||
cosβ |
||||||
|
|
|
|
15.2. Радиус кривизны активного профиля обрабатываемого колеса в нижней точке
ρp1 = aw sin αtw −0,5 da22 −db22 . |
(4.17) |
15.3. Высота модификации головки (высота «усика»)
|
|
|
|
|
0,5 S |
|
|
|
hq0 |
= ha0 |
− x1mn − |
0,5d1 sin αt 0 |
−ρp1 − |
sin αt 0 |
. (4.18) |
||
cosβ |
||||||||
|
|
|
|
|
|
|
15.4. Расстояние от точки начала модификации до поверхности вершин вдоль линии теоретического исходного контура (проставляется на чертеже)
Сq0 |
= |
hq0 |
. |
(4.19) |
|
||||
|
|
cosαn0 |
|
|
15.5. Нормальная глубина модификации головки зуба |
|
|||
αq |
0 =0,5 S. |
(4.20) |
16. Модификация ножки зуба фрезы (расчёт проводить для фрез под шевингование при mn > 6 мм и для чистовых и черновых фрез
при наличии модификации вершины зуба колеса). |
|
16.1. Высота модификации головки зуба колеса: |
|
– для фрез под шевингование |
|
hg1 = 0,5…0,8 мм; |
(4.21) |
–для фрез чистовых величина hg1 в миллиметрах указывается на чертеже колеса или задаётся коэффициентом h*g исходного контура;
–для фрез черновых
hg1 = hg чист +0,5 S tgα. |
(4.22) |
16.2. Торцовая глубина модификации головки зуба колеса:
24

– для фрез под шевингование |
|
|
|
|
|
|||
|
αt1 = |
0,5 S |
|
; |
|
(4.23) |
||
|
cosβ |
|
|
|||||
|
|
|
|
|
|
|||
– для фрез чистовых величина αt1 |
в миллиметрах указывается |
|||||||
на чертеже колеса или задаётся коэффициентом |
* исходного кон- |
|||||||
тура; |
|
|
|
|
|
|
|
|
– для черновых фрез |
|
|
|
|
S |
|
|
|
αt1 |
= αt1чист + |
|
|
. |
(4.24) |
|||
2cosβ |
||||||||
|
|
|
|
|
17. Угол линии модификации торцового производящего контура (первое приближение)
αtМ 0 = arctg tgα0 + at1 . (4.25)
cosβ hg
18.Диаметр основной окружности линии модификации вершин зубьев колеса
dbM1 = d1cosαtM0.
19. Диаметр окружности модификации вершины зуба dg1 = da1 – 2hg1.
20.Угол профиля на окружности модификации вершин
=d
αg1 arccos dbg11 ;
(4.26)
(4.27)
(4.28)
αgM 1 = arccos dbM 1 . (4.29)
dg1
21.Толщина зуба колеса по окружности модификации вершин
Stg1 |
= dg1 |
|
0,5π+2x1tgα |
+invαt −invαg1 |
. |
(4.30) |
|
||||||
|
|
|
z1 |
|
|
Значения инвалют приведены в приложении 2. 22. Угол профиля на окружности вершин
|
|
|
|
|
αta1 |
= arccos |
db1 |
. |
(4.31) |
|
||||
|
da1 |
|
|
23. Толщина зуба колеса на окружности вершин
os
25

24. Угол профиля линии модификации на окружности вершин
|
|
dbM 1 |
|
(4.33) |
αtaM 1 |
|
|
||
= arccos |
da1 |
|
|
|
|
|
|
|
25. Толщина зуба на поверхности вершин колеса, нарезанного с модификацией профиля
|
|
|
|
|
|
|
|
|
|
|
S |
taM1 |
= d |
a1 |
|
Stg1 |
+invα |
tM 0 |
−invα |
|
(4.34) |
|
||||||||||
|
|
|
|
|
taM 1 |
|
||||
|
|
|
|
dg1 |
|
|
|
|
|
26. Торцовая глубина модификации головки зуба расчётная
′at1 = 0,5(Sta1 −StaM 1 ). |
(4.35) |
Если 'at1 < at1 ( 'at1 > at1 ) , то увеличить (уменьшить) угол αtM0 (см. п. 17) и повторить расчёт, начиная с п. 18. Подбор величины угла αtM0 следует прекратить, если
'at1 − at1 ≤ 0,03 .
27. Расстояние от начальной точки модификации до средней линии исходного производящего контура
hM 0 |
= |
d1 |
× |
|
|
|
|
2(tgαtM 0 |
−tgαt 0 ) |
|
|
(4.36) |
|||
|
|
|
|
|
|||
|
|
|
|
|
2 |
' |
|
× invαtaM +invαt 0 −invαa1 |
−invαtM 0 −inv |
|
at1 |
. |
|||
|
|
||||||
|
|
|
|
|
da1 |
|
|
|
|
|
|
|
|
III.Расчёт параметров режущей части
28.Число зубьев фрезы
z = |
2,6bπ |
, |
(4.37) |
|
ϕ |
||||
|
|
|
где ϕ=arccos da0 −2h1 . da0
Коэффициент b = 1 для чистовых фрез, b = 0,75 для черновых фрез со шлифованным профилем, b = (1,2…1,3) для черновых фрез
снешлифованным.
29.Задний угол на вершине зуба
26

δа = 9…12°. |
(4.38) |
|
30. Величина первого затылования |
|
|
k |
= πda0 tgδa . |
(4.39) |
1 |
z |
|
|
|
округляется до значения, кратного 0,5 при k < 5, до целого числа при k ≥ 5 мм. Величина второго затылования (только для инструментов со шлифованным профилем)
k2 = 1,5k1. (4.40) 31. Действительный задний угол при вершине зуба
|
k1z |
|
|
|
δa =arctg |
. |
(4.41) |
||
πda0 |
||||
|
|
|
Угол δа должен быть не менее 9° при α0 = 20° и не менее 12° при
α= 15°.
32.Диаметр расчётный начальной поверхности винтовых стружечных канавок (при осевых канавках фрезы не определяются)
dрас = da0 −2ha0 −2σk1,
где σ = 0,1 для чистовых, σ = 0,25 для черновых фрез. 33. Угол наклона стружечных канавок (для фрез
навками не определяется)
|
m z |
0 |
|
ω= arctg |
n |
. |
|
|
|
||
|
|
|
|
dрас cos γ0 |
|
34.Шаг винтовых стружечных канавок
Т= tgр2zω0 .
(4.42)
с осевыми ка-
(4.43)
(4.44)
Направление стружечных канавок обратно направлению витков исходного производящего червяка.
35. Осевой угол профиля. Для фрез с осевыми стружечными канавками
|
|
tgα0 |
|
|
|
αх0 |
=arctg |
. |
(4.45) |
||
|
|||||
|
cosγ0 |
|
|
Для фрез с винтовыми канавками
|
|
|
k z |
0 |
|
(4.46) |
αx0 L( R) |
= arcctg ctgα0cosγ0 |
|
1 |
. |
||
T |
|
|||||
|
|
|
|
|
|
27
Вформуле (4.46) верхний знак относится к левой (L), а нижний
–к правой (R) сторонам профиля фрезы с правым направлением витков исходного производящего червяка. При изменении направления витков фрезы знаки в (4.46) изменяют на противоположные.
36. Радиус закругления профиля вершины зуба фрезы
ρa0 |
= |
|
C |
; |
|
|
(1−sin α0 ) |
|
|||
|
|
|
|
|
|
для фрез под шевингование |
|
|
|||
ρa0 |
= |
(0,1...0,15)mn |
. |
||
|
|
|
(1−sin α0 ) |
В формуле (4.47) С = с*m – радиальный зазор в передаче. 37. Радиус закругления профиля ножки зуба фрезы
ρf0 = 0,3mn.
(4.47)
(4.48)
(4.49)
38. Высота зуба фрезы
H = h0 + 0,5(k1 + k2) + r, (4.50)
где r – радиус закругления впадины зуба определяется по табл. 4.2.
|
|
|
|
Таблица 4.2 |
|
|
|
|
|
mn |
2–2,25 |
2,5–9 |
10 |
Свыше 10 |
r, мм |
1,5 |
2,0 |
2,5 |
3,0 |
Для выполнения второго затылка k2 строится окружность по условным вершинам зубьев, для этого рассчитывается высота зуба
H2 = h0 + k2 + r.
39. Диаметр посадочного отверстия фрезы |
|
dотв = da0 – 2(H + t), |
(4.51) |
где t – толщина тела фрезы; t = 2,5mn – для фрез с торцовым шпоночным пазом; t = 3mn – для фрез с продольным шпоночным пазом.
Диаметр dотв округляется до ближайшего меньшего стандартного значения по ГОСТ 9472-90.
Диаметр выточки в отверстии фрезы d1 (см. рис. 4.2) для уменьшения посадочной поверхности с точностью до 1 мм
d1 = 1,05dотв.
Размеры шпоночного паза [1, 2] приведены в табл. 4.3.
28
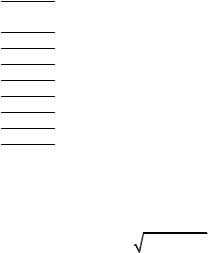
|
|
|
|
|
|
|
Таблица 4.3 |
|
|
|
|
|
|
|
|
Номи- |
|
Размер шпоночного паза |
|
Допускае- |
|||
нальный |
|
|
Высота паза от про- |
Радиус |
мое |
||
диаметр |
Ширина паза b, |
тивоположной сто- |
закруг- |
смещение |
|||
отверстия |
мм |
роны отверстия С1, |
ления в |
паза |
|||
фрезы dотв, |
|
|
мм |
|
пазу R, |
относитель- |
|
мм |
номи- |
допуск |
номинал |
|
допуск |
мм |
но оси |
|
нал |
|
|
|
|
|
отверстия |
16 |
4 |
С11 |
17,7 |
|
Н12 |
0,4+0,2 |
0,07 |
22 |
6 |
С11 |
24 |
|
Н12 |
0,7+0,3 |
0,09 |
27 |
7 |
С11 |
29,8 |
|
Н12 |
0,9+0,3 |
0,09 |
32 |
8 |
С11 |
34,8 |
|
Н12 |
0,9+0,3 |
0,09 |
40 |
10 |
С11 |
43,5 |
|
Н12 |
0,9+0,3 |
0,09 |
50 |
12 |
С11 |
53,5 |
|
Н12 |
1+0,5 |
0,12 |
60 |
14 |
С11 |
64,2 |
|
Н12 |
1,1+0,5 |
0,12 |
40. Диаметр буртиков фрезы (округляется до числа, кратного
0,5)
Dб = da0 – 2H – (1,5…3). (4.52) 41. Длина нарезанной части фрезы
|
|
lф = (h1 / 2tgα0 ) + (da1 −h1 )h1 +(n +1) px0 , |
(4.53) |
|||
где n – |
число осевых перестановок фрезы, n = 8–2. |
|
||||
42. Длина фрезы |
L = lф + 2lб , |
|
|
(4.54) |
||
|
|
|
|
|
||
где lб – длина буртиков определяется по табл. 4.4. |
|
|||||
|
|
|
|
|
|
Таблица 4.4 |
|
|
|
|
|
|
|
mn |
|
1–3,25 |
3,5–7 |
7–14 |
|
Свыше 14 |
lб, мм |
|
3 |
4 |
5 |
|
6 |
Длина шлифованной части посадочного отверстия t (см. рис. 4.2) с каждого торца (подсчитывается с точностью до 1 мм) определяется по формуле
t1 = (0,3…0,2)L.
43. Угол профиля стружечной канавки ε (см. рис. 4.2) принимается согласно табл. 4.5. Бóльшее значение облегчает процесс заты-
29

лования фрез резцом, увеличивает объем пространства для размещения стружки.
|
|
|
Таблица 4.5 |
|
|
|
Свыше 10 |
z |
8 |
9–10 |
|
ε, град |
25 |
22 |
18 |
4.2.Пример расчёта червячных фрез
4.2.1.Для прямозубых зубчатых колес (β = 0)
Исходными данными являются:
–модуль m = 4;
–число зубьев z1 = 28, z2 = 65;
–угол наклона зубьев β = 0;
–коэффициенты смещения х1 = – 0,568, х2 = – 0,723;
–тип исходного контура – 1;
–межосевое расстояние – 180 мм;
–степень точности передачи – 8-B.
Рассчитанные параметры зубчатой передачи приведены в приложении 1.
I.Расчёт параметров исходного производящего червяка фрезы
1.Нормальный угол профиля αn0 = α = 20°.
2.Число витков производящего червяка z0 = 1.
3.Делительный угол подъёма витков производящего червяка
(берется из табл. 4.1) γ0 = 2,6°.
4. Высота делительной головки витка производящего червяка (зуба фрезы)
ha0 = mn (ha* +c* ) = 4(1+0,25) = 5.
5. Высота витка производящего червяка (зуба фрезы) h0 = h1 +0,3mn = 8,165 + 0,3 4 = 9,365.
30