
Измельчение - определение и виды измельчения, применимость видов измельчения
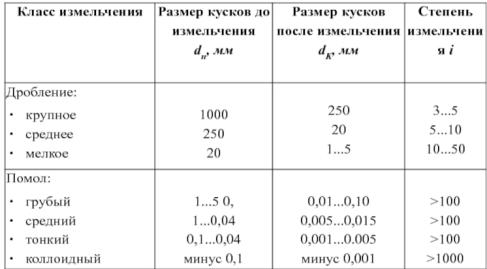
1) Измельчение - определение и виды измельчения, применимость
видов измельчения Измельчение — процесс уменьшения размеров кусков (частиц) твердых
материалов путем механического воздействия.
По размеру измельчённого продукта измельчение разделяют на два типа:
1. Дробление:
Цель дробления — получение кускового продукта необходимой крупности, а
также подготовка к помолу.
2. Помол:
Цель помола — увеличение дисперсности твёрдого материала, придание ему
определённого гранулометрического состава и формы частиц, дезагрегирование.
Крупное дробление мягких хрупких материалов выполняют раскалыванием, среднее и мелкое - ударом. Помол осуществляют ударом и истиранием.
Крупное измельчение связано с дроблением крупногабаритных отходов производства изделий методом термоформования, коллоидное - с получением порош кообразных полимеров, а также с подготовкой пигментов и кра сителей. Крупное дробление кусковых материалов, поступающих в виде кусков и глыб различной величины ( мрамор, кварц, плавиковый шпат, полевой шпат, гранит, доломит, ферросплавы и др.), осуществляется под молотами и в щековых дробилках. Ферросплавы, ввиду их высокой прочности и вязкости, обычно дробят под механическими молотами. Минералы, руды и хрупкие ферросплавы с успехом проходят дробление в щековых дробилках.
Мелкое и тонкое дробление применяют только для руд, идущих на обогащение.
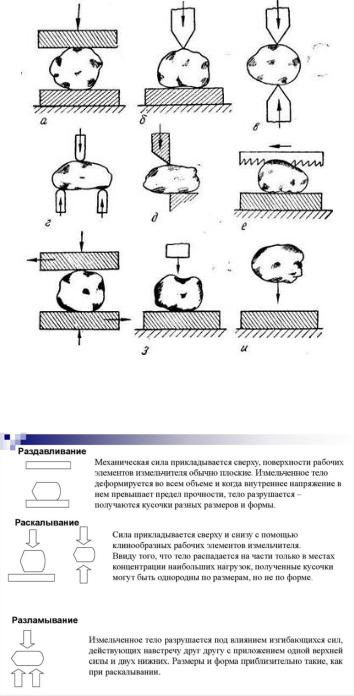
Грубый помол - для переработки цельного неочищенного зерна: пшеничного; ржаного; рисового; овсяного; кукурузного; ячменного; гречневого.
Измельчение может осуществляться ручным и машинным способами. Ручное измельчение типично для аптечного производства, где оно производится пести ками в ступках и другими простыми инструментами (резаки, терки и пр.). Машинное измельчение, единственно рациональное в лабораторных и заводских условиях, выполняется на разнообразных по своему устройству машинах-измельчителях.
Способы измельчения
а— раздавливание; б, в — раскалывание; г — разламывание; д — резание; е
—распиливание; ас — истирание; а — жесткий удар; и — свободный удар.

Раздавливание - применяют для получения кусковых материалов; получения минерального порошка из известнякового щебня в шаровых или молотковых мельницах
Управляемое термическое раскалывание применяется при резке стеклянных трубок в производстве электровакуумных приборов, керамических подложек интегральных схем, для резки листового и фасонного стекла.
Разрезание и распиливание применяют в тех случаях, когда нужно получить
куски материала определенного размера и заданной формы. Растирание применяют для тонкого измельчения мягких и вязких материалов.
При этом его всегда комбинируют с раздавливанием или ударом.
Пластичные и эластичные материалы лучше измельчаются срезом и
истиранием.
Машины для измельчения (дробления и помола) делят на дробилки и мельницы. Классификация машин для измельчения по конструктивным
особенностям приведена на схеме
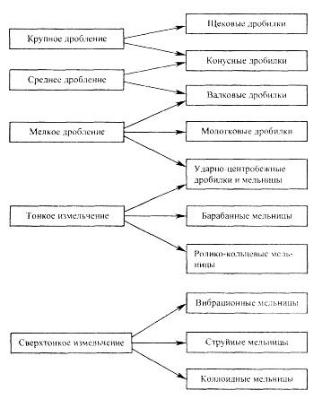
2) Степень измельчения - понятие и принцип расчета
Степень измельчения
Степенью измельчения (i) называют отношение среднего диаметра (dн) наиболее крупных кусков до измельчения к среднему диаметру (dк) наиболее крупных кусков,
полученных после измельчения:
i = dн/dк
Общую степень измельчения вычисляют путем суммирования всех результатов измельчения, которые были выполнены в несколько приемов. За один прием обработки степень измельчения крупных кусков составляет 2 – 6, средних – 5 – 10,
мелких – 10 – 50 и наиболее мелких – 50 и выше.
Как частицы исходного, так и частицы переработанного материала имеют неправильную форму, поэтому для определения показателей диаметров,
используется размер отверстий сит, сквозь которые просеивают сыпучие материалы.
Дробление и размол осуществляется машинами самых разных конфигураций и габаритов. Измельчение материалов может осуществляться в одну или несколько
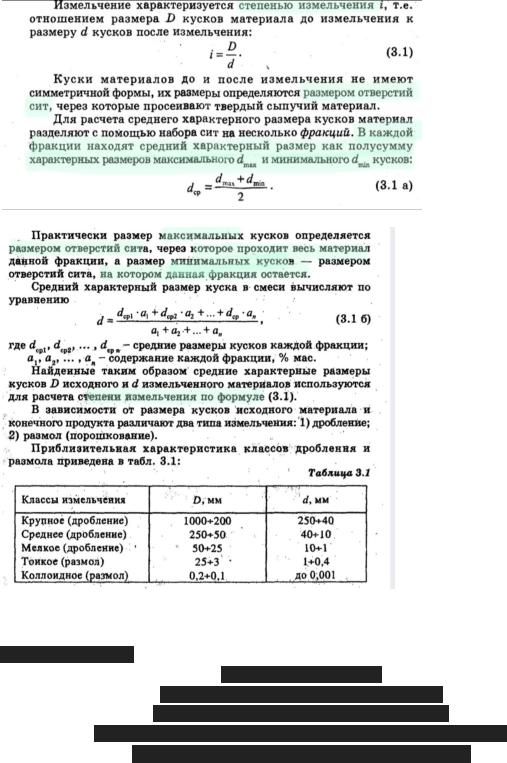
стадий. При необходимости высокой степени измельчения, процесс разбивается на
несколько этапов, т.к. один этап не позволяет получить частицы необходимой
конечной крупности.
Вопрос 3. Основные задачи и числовые характеристики измельчения
Задачи измельчения
1.Простота дозирования
2.Усиление фармакологической активности
3.Увеличение удельной поверхности веществ
4.Повышение скорость химический и диффузионных процессов
5.Увеличение их свободную поверхностную энергию
Степень измельчения вещества- это отношение диаметра материала до измельчения (D) к диаметру частиц измельченного материала (d)
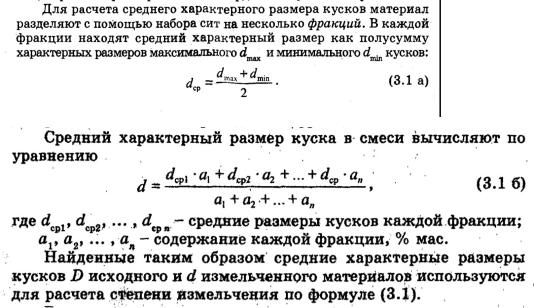
i=D/d
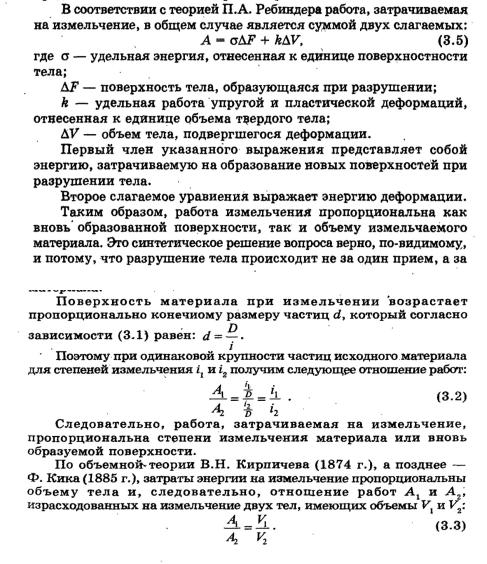
4) Классификация измельчаемых материалов, особенности подходов к их измельчению в зависимости от строения и структуры.
Измельчение — это процесс уменьшения размера частиц материала путем механического воздействия.
В результате измельчения увеличивается поверхность измельчаемых материалов, что позволяет:
●увеличить удельную поверхность вещества;
●увеличить свободную поверхностную энергию;
●значительно увеличить скорость химических и диффузионных процессов;
●усилить фарм. активность вещества;
По современным представлениям, измельчение твердых тел основывается на том, что под действием механических усилии в измельчаемом материале возникают внутренние напряжения и при достижении предела прочности материала последний разрушается. При прекращении внешнего воздействия трещины за счет молекулярных сил могут смыкаться, при этом тело подвергается лишь упругой деформации.
Особенности подходов к измельчению в зависимости от строения и структуры.
В зависимости от размера кусков исходного материала и конечного продукта различают 2 типа измельчения:
1)размол (порошкование)
2)дробление
Крупное, среднее и мелкое дробления осуществляют в дробилках сухим способом, а тонкое и коллоидное измельчение – сухим и мокрым способом. При мокром дроблении уменьшается пылеобразование и получаются частицы более однородные по размерам и облегчается выгрузка материала. Дробление материалов осуществляется:
●раздавливанием,
●истиранием,
●ударом,
●раскалыванием,
●распиливанием,
●разрезанием,
●разламыванием.
Для достижения оптимальной степени измельчения процесс осуществляют постадийно на последовательно соединенных дробильно-рамольных машинах. Изрезывающие машины применяют для измельчения растительного материала. Раздавливающие применяют при крупном и среднем измельчениях, истирание – при тонком измельчении.
В зависимости от физико-механических свойств и размеров кусков (крупности) измельчаемого материала выбирают тот или иной вид воздей ствия. Так, дробление твердых и хрупких материалов производят раздавливанием , раскалыванием и ударом, твердых и вязких - раздавливанием и истиранием.
5. Требования к измельчаемым материалам, количественные показатели
требования к проведению процесса измельчения:
●ЛВ при измельчении должны хранить неизмененными свой состав и фармакологические свойства
●Периодически необходимо удалять достаточно измельченные частицы из сферы помола
●Предотвращать пылеобразование
●Влажность материала должна быть соответствующей
●Последовательное использование дробильно-разламывающих машин
=В процессе дробления происходит большой расход энергии, поэтому основным принципом экономии энергии в процессе измельчения материала является «не дробить ничего лишнего». Данный принцип предполагает предварительное отделение частиц материала равных по крупности или являющихся мельче, чем конечный продукт дробления. В результате такой фильтрации удается избежать перегрузки оборудования и получить продукт равномерной крупности.
=Какое-либо вещество, прежде чем отравиться на обработку или на проведение химической реакции, должно быть надлежаще подготовлено. То есть его форма и свойства должны быть изменены до такой степени, чтобы протекание производственного процесса на всех его технологических стадиях происходило наилучшим образом, а химическая реакция прошла успешно и дала максимальный выход продукта.
В химической промышленности очень важным параметром является участвующая во взаимодействии площадь поверхности материалов. Именно от нее во многом зависит конечный результат той или иной производимой химической реакции. Поэтому очень важно придать частицам веществ такой размер, который обеспечит оптимальное протекание данной реакции путем развития достаточной контактирующей поверхности. С этой целью было разработано множество способов, которые отлично зарекомендовали себя на практике.
Одним из таких способов является разделение того или иного используемого материала на более меньшие части для увеличения площади его поверхности.
Твердые материалы для увеличения их поверхности подвергают измельчению, которое осуществляется в специальных машинах - дробилках. В случае жидких материалов добиться этого можно за счет использования таких эффективных приемов, как распыление или орошение.
Увеличение площади поверхности твердых или жидких веществ позволяет:
-существенно повысить скорость химической реакции;
-облегчить обращение с ними;
-добиться наиболее совершенной формы выпускаемого продукта.
Степень измельчения
Степенью измельчения (i) называют отношение среднего диаметра (dн) наиболее крупных кусков до измельчения к среднему диаметру (dк) наиболее крупных кусков, полученных после измельчения:
i = dн/dк
Общую степень измельчения вычисляют путем суммирования всех результатов измельчения, которые были выполнены в несколько приемов. Как частицы исходного, так и частицы переработанного материала имеют неправильную форму, поэтому для определения показателей диаметров, используется размер отверстий сит, сквозь которые просеивают сыпучие материалы.
6.Классификация оборудования для измельчения, краткая характеристика
1.По способу измельчения
-режущие (изрезывание лрс производится с помощью машин носящих название травоили корнерезки. Основная деталь этих машин - ножи, устройством и характером движения которых обуславливается тип и конструкция траво- и корнерезок)
Простейшие по устройству-соломорезки: дисковые(массивные ножи
скриволинейным лезвием) и барабанные(ножи изогнуты по винтовым линиям, для измельчения сухой травы)
Вкорнерезках нож массивный, падая вниз своей массой, усиливает режущий эффект. Нож совершает поступательно-возвратное движение вверх и вниз при помощи кривошипного механизма или коленчатого вала.
В траво и корнерезках движение ленточного транспортера, питающих валиков и ножей происходит согласованно, так что растительная масса выступает вперед на определенную длину в соответствии с заданной степенью измельчения.