
Учебное пособие 800664
.pdf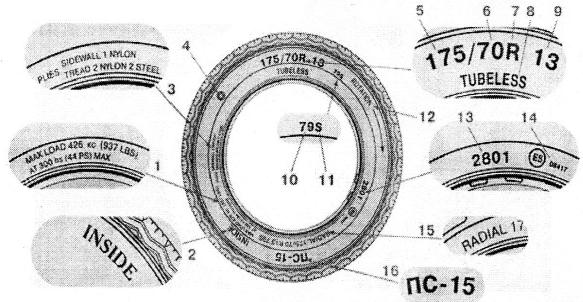
Рис. 4.6. Пример нанесения информации на шине: 1 – максимальная нагрузка и давление (стандарт США); 2 – обозначение внутренней стороны шины при асимметричном рисунке протектора; OUTSIDE – наружная сторона; 3 – количество слоев и тип корда каркаса и брекера; 4 – товарный знак заводаизготовителя; 5 – ширина профиля (мм); 6 – низкопрофильная серия шины (отношение высоты профиля к ширине ≈70%); 7, 15 – обозначение радиальной шины; при отсутствии R – шина диагональная; 8 – обозначение бескамерной шины; 9 – посадочный диаметр (дюйм); 10 – индекс грузоподъемности (табл. 4.3); 11 – индекс скорости (табл. 4.4); 12 – обозначение направления вращения шины; 13 – дата изготовления шины (порядковый номер недели и год
после |
2000 года); |
14 – знак официального утверждения шины |
(номер |
сертификата |
и условный номер страны, выдавшей сертификат); |
16 – наименование модели
Процесс взаимодействия пневматического колеса с опорной поверхностью отличается значительной площадью пятна контакта из-за небольшой радиальной жесткости (рис. 4.7) по сравнению со стальным колесом.
Пятно контакта пневматического колеса с опорной поверхностью составляет значительную площадь. При качении такого колеса по опорной поверхности возникают две зоны: зона сцепления I и зона скольжения II.
В зоне сцепления отсутствует скольжение шины относительно опорной поверхности, а в зоне II элементы шины имеют скорость больше поступательной скорости V оси колеса.
Соотношение этих зон зависит от многих факторов. Для конкретных шин и опорной поверхности это соотношение определяется величиной силы тяги Тφ, создаваемой ведущим колесом при подводимом к нему крутящем моменте, который реализуется на колесе в окружную силу Рк .
110
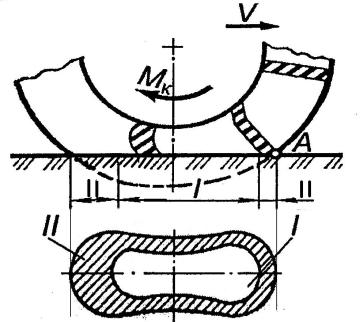
ё
Рис. 4.7. Зона сцепления (I) и зона скольжения (II) в области контакта шины с опорной поверхностью
По мере роста силы тяги зона сцепления I уменьшается, а зона скольжения II растет. Как только в пятне контакта зона скольжения достигнет 100 % , возникает полное буксование колеса. Поступательная скорость становиться ровна нулю, перемещение прекращается.
Величина силы тяги, реализуемой на оси колесного движителя, может быть определена для конкретной опорной поверхности с учетом предполагаемого коэффициента сцепления движителя с опорной поверхностью. В табл. 4.5 приведены усредненные показатели коэффициентов сопротивления перекатыванию f и коэффициентов сцепления μ для пневмоколесных и гусеничных движителей.
Таблица 4.5 Коэффициенты сопротивления перекатыванию w и сцепления μ
Тип пути |
Пневмоколесный ход |
Гусеничный ход |
||
|
f |
μ |
f |
μ |
Шоссе асфальтобетонное |
0,015-0,02 |
0,45-0,55 |
0,03-0,035 |
0,35-0.45 |
Шоссе цементобетонное |
0,015-0,02 |
0,6-0.75 |
0,03-0,035 |
0,3-0,4 |
Дорога булыжная |
0,025-0,035 |
0,4-0,5 |
0,05-0,07 |
0,4-0,5 |
Дорога грунтовая сухая |
0,03-0.05 |
0,5-0,7 |
0.05-0,07 |
0,45-0.55 |
Дорога грунтовая мокрая |
0,05-0,15 |
0,35-0,5 |
0,1-0,15 |
0,4-0,5 |
Дорога сухая песчаная |
0,1-0,3 |
0,65-0,75 |
0,1-0,15 |
0,2-0,25 |
Дорога снежная, плотная |
0,03-0,04 |
0,15-0,35 |
0,06-0,07 |
0,25-0,35 |
111
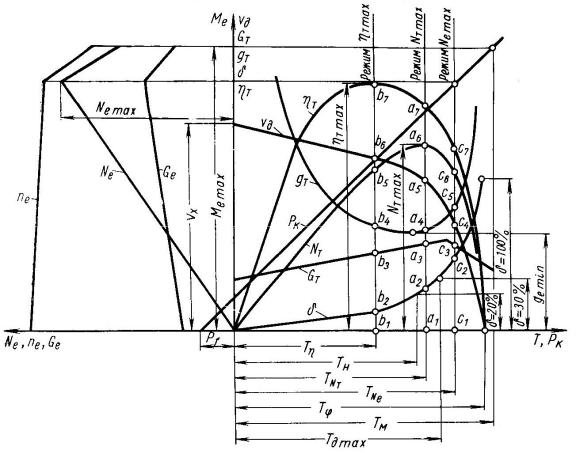
Вопросами тяговой механики землеройно-транспортных машин успешно занимался д.т.н. проф. Н.А. Ульянов. Разработанная им теория позволяет использовать теоретические и опытные тяговые характеристик колесных землеройно-транспортных машин (ЗТМ) для оценки эффективности работы таких машин и выбирать оптимальный режим их работы.
На рис. 4.8 показан вариант такой тяговая характеристика
Рис. 4.8. Тяговая характеристика как средство оценки тяговоэкономических показателей ЗТМ
На ней хорошо просматриваются возможность в зависимости от грунтовых условий, параметров колесного движителя, характеристики силовой установки анализировать тяговый режим землеройно-транспортной машины. Это позволяет определить условия, отвечающие максимальному значению тягового КПД ηт мах (точка b7), или максимальной тяговой мощности NT (точка а6), или минимальному значению удельного расхода топлива gт(точка ge min), прогнозировать часовой расход топлива Gт для того или иного тягового режима работы ЗТМ.
Такая характеристика позволяет определить максимальную силу тяги, реализуемую сцеплением пневматического колеса с грунтом Тφ, возникающую при полном проскальзывании колесного движителя, или выбрать оптимальный
тяговый режим буксовании колесного движителя |
для |
получения |
максимального тягового КПД при буксовании движителя δ ≈ 10 %. |
|
112
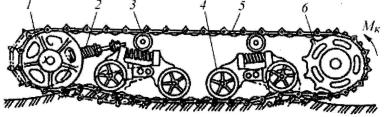
Целесообразно основные оценочные показатели тяговых и топливноэкономических качеств ЗТМ определять:
-на режиме максимальной тяговой мощности (точки а1 – а8);
-на режиме максимального тягового КПД (точки b1 – b6);
-на режиме максимальной мощности двигателя (точки с1 – с7).
4.2.2.Гусеничные движители
При производстве работ на начальных этапах строительства на грунтах с низкой несущей способностью предпочтительно использовать строительные машины смонтированные на раме с гусеничным движителем.
Гусеничный движитель (рис. 4.9) обеспечивает передвижение машины с помощью двух замкнутых в кольцо сборных лент (гусениц) 5. Каждая лента охватывает систему, состоящую из ведущей звездочки 6, натяжного колеса 1 и ряда поддерживающих 3 и опорных 4 катков, укрепленных на балке ходовой рамы. Гусеничные ленты состоят из отдельных шарнирно соединенных стальных элементов (траков) специальной конфигурации.
Рис. 4.9. Общий вид гусеничного движителя
Из траков можно собирать замкнутое кольцо необходимой длины. Ширина гусеничной ленты определена длиной траков.
Гусеничный движитель обладает рядом положительных свойств:
-обеспечивает низкие удельные давления машины на грунт;
-обеспечивает высокую проходимость по мягким, топким грунтам;
-обладает высокой маневренностью;
-обеспечивает лучшую устойчивость машин от опрокидывания;
-обладают хорошим сцеплением с грунтовой поверхностью;
-позволяет реализовать высокую силу тяги на крюке;
-преодолевать подъемы до 35º;
-меньшее сопротивление передвижению, чем колеса по грунту;
-меньшие потери мощности на самопередвижение.
Вместе с тем гусеничный движитель обладает некоторыми недостатками. Масса гусеничного движителя может составлять до 30 % массы машины, он сложнее в обслуживании, имеет более низкий КПД по сравнению с пневмоколесным движителем и невысокие транспортные скорости. Машины с гусеничным движителем работают в сложных грунтовых условиях. Шарниры
113
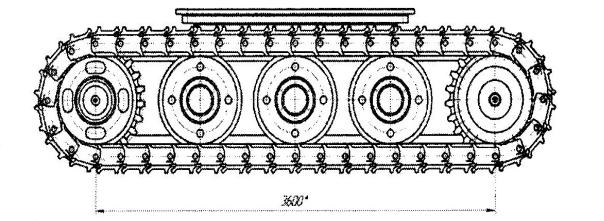
гусеничных лент подвергаются интенсивному абразивному износу и требуют частой замены. Для перемещения машин с гусеничным движителем по
городским дорогам общего пользования |
необходимы специальные |
транспортные средства. |
|
Гусеничные движители характеризуют площадью опорной поверхности |
|
S = B×L, |
(4.27) |
где В – ширина гусеничной ленты, м;
L – длина гусеничной ленты, контактируемая непосредственно с опорной поверхностью в движении, м.
Обычно, под расчетной длиной гусеничной ленты большинства строительных машин понимают длину гусеничного движителя от оси ведущей звездочки до натяжного катка (ленивца) (рис. 4.10).
Рис. 4.10. Общий вид экскаваторного гусеничного движителя
Машина с гусеничным движителем массой т (тонн) характеризуется средним удельным давлением на опорную поверхность
qср = m / 2S, МПа. |
(4.28) |
Большинство строительных машин на гусеничном ходу (экскаваторы, краны, бульдозеры, трубоукладчики) имеют среднее давление на грунт 0,1÷0,2 МПа. Машины высокой проходимости (снегоходы, болотоходы) должны иметь средние удельные давления не более 0, 015 ÷ 0,02 МПа. Предельно допустимые давления (МПа): для песка – 0,3÷0,5; для суглинка – 0,6÷0,8; для плотной глины 0,8÷1,0; для дороги с твердым покрытием – до 1,5.
Давление на опорную поверхность существенно зависит от типа гусеничного движителя. Он может быть малоопорным или многоопорным. При малоопорном движителе (рис. 4.10) давление под катками может существенно превышать среднее удельное давление. При многоопорном движителе местное
114
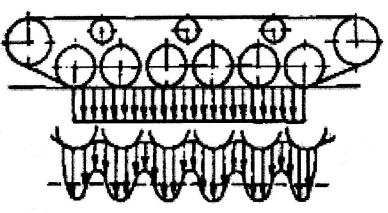
удельное давление с учетом деформации грунта приближается к среднему удельному давлению. На рис. 4.11 показан характер эпюры давлений для многоопорного гусеничного движителя.
Рис. 4.11. Эпюра давлений на грунт многоопорного гусеничного движителя
Важной характеристикой гусеничного движителя являются его тяговосцепные свойства. Их можно оценить тяговым коэффициентом полезного действия ηт, который вычисляют по формуле:
ηт = ηг ηтр (1-δ)(1-Fсп / Fт), |
(4.29) |
где ηг = 1- кд L– КПД движителя (гусеницы); ηтр – кпд трансмиссии; δ – буксование в долях единицы;
Fсп – сила сопротивления движению, Н; Fт – касательная сила тяги, Н.
КПД движителя ηг учитывает потери мощности на трение в механизме ходовой части. Он зависит от длины гусеницы L. Коэффициент кд для составных металлических гусениц можно принимать
кд = 0, 016 ...0,022.
Потери на трение в шарнирах, соединяющих траки, будут меньше при расположении ведущего колеса в кормовой части машины по сравнению с носовым его расположением. В этом случае нижняя ветвь гусеницы нагружается растягивающим усилием, и качение опорных катков происходит по натянутой ленте с меньшими изгибами опорной поверхности.
Для гусеничных машин существует оптимальное соотношение между длиной и шириной гусеницы γ = L/B, при котором она имеет наилучшие тягово-сцепные свойства и максимальный КПД (рис. 4.12). Максимум тягового КПД достигается при γ ≈ 8,1.
115
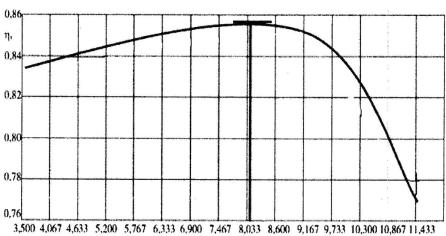
γ
Рис. 4.12. Зависимость КПД гусеничного движителя от соотношения γ = L/B
Cилу сопротивления передвижению машины с гусеничным движителем при прямолинейном движении вычисляют по формуле:
|
Fсп= Wвн + Wи + Wn + Wк + Wв + Wкр, |
(4.30) |
где Wвн |
– сопротивление сил трения в трансмисси, Н; |
|
Wк |
– сопротивление перекатыванию гусеничной ленты, Н; |
|
Wи |
– сопротивление инерции при трогании с места, Н; |
|
Wn – сопротивление при движении на подъем, Н; |
|
|
Wв |
– сопротивление ветра, Н. |
поверхности из |
Для прямолинейного движения по горизонтальной |
данных уравнений исключаются Wn и Wкр.
Сопротивление сил инерции при пуске механизма определяют по
формуле |
|
G V |
|
|
|
W |
|
, |
(4.31) |
||
|
|||||
И |
|
g tp |
|
||
где G – снаряженный вес , Н; |
|
|
|
|
|
V – скорость передвижения экскаватора, м/с; |
|
||||
g – ускорение силы тяжести, м/с2; |
|
||||
tp – время разгона 2÷3 с. |
|
|
|
|
|
Сопротивление подъему |
|
|
|
|
|
Wn = G · sinα, |
(4.32) |
||||
где α – угол подъема. |
|
|
|
|
|
Сопротивление перекатыванию типового экскаваторного |
гусеничного |
||||
движителя можно определять по формуле |
|
||||
а) для многоопорной гусеницы: |
|
116
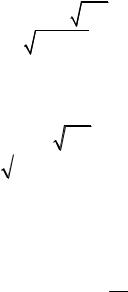
W |
|
|
1,5 n b p2 D |
|
||||
K |
|
|
|
|
H |
; |
(4.33) |
|
|
|
|
|
|||||
|
|
ρ0 |
|
DH h |
|
|||
|
|
|
|
б) для малоопорной гусеницы:
W |
|
2,67 |
n b p2 |
D |
(4.34) |
|||||
K |
|
|
|
|
|
H |
, |
|||
|
|
|
|
|
||||||
ρ0 |
|
DH h |
||||||||
|
|
|
|
|
||||||
|
|
|
|
|
|
где DH – диаметр направляющих колес; n – число гусениц;
b – ширина гусеницы;
h – глубина погружения экскаватора: h p , см;
ρ0
p – фактическое удельное давление на грунт, Па;
0 – коэффициент удельного сопротивления грунта смятию, для определенной почвы коэффициент постоянный.
Так, для крупного песка и влажной средней глины 0 = 0,3·9,81·104 Н/м2; для средней глины и влажной плотной глины 0 = 0,5·9,81·104 Н/м2;
Сопротивление давления ветра определяют по формуле
Wb F ρв , |
(4.35) |
где F – надветренная площадь, м2;
в – допустимое давление ветра по ГОСТ 1451-77 в = 125 Па.
Сопротивление развороту складывается из сопротивления опорной поверхности и сопротивления скалывания грунта при повороте гусеницы:
Wкр |
2(Mтр Мск ) |
, |
(4.36) |
|
|||
|
В |
|
где Мтр – полный момент трения одной гусеницы.
Мтр μ р b |
l2 |
, |
(4.37) |
|
|||
4 |
|
|
где l – длина гусеницы, м; b – ширина гусеницы, м;
р – фактическое давление на грунт, Па; μ – коэффициент удельного трения гусеницы о грунт (0,25÷1,0); В – расстояние между осями гусениц, м;
117
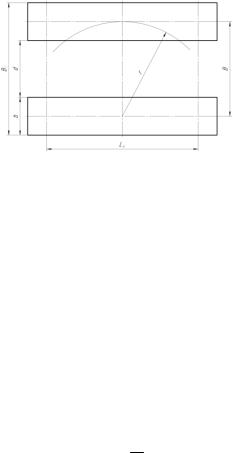
Мск – момент сопротивления скалыванию грунта:
Мск = 0,29 · K∙h·l12 , |
(4.38) |
где К – коэффициент сцепления грунта, К = 0,25÷2,5 кгс/см2; h – глубина погружения гусеницы;
l1 – длина опорной части гусеницы.
Заводом-изготовителем (расчеты экскаватора ЭО-5221) предлагается следующий вариант расчета сопротивления развороту, схема которого приведена на рис. 4.13.
Рис. 4.13. Схема разворота |
|
||||||
|
|
Мкр |
Мс |
, |
(4.39) |
||
|
|
||||||
|
|
|
r |
|
|
|
|
где Мс – момент сопротивления развороту; |
|
|
|
||||
r – радиус разворота. |
|
|
|
||||
Мс |
μ G Lcp |
|
, |
|
(4.40) |
||
|
|
||||||
4 |
|
|
|
|
|
||
где μ – коэффициент сопротивления повороту; |
|
||||||
Lср – продольная база. |
, |
|
(4.41) |
||||
μ a (1 a)r2 |
|
||||||
|
|
μmax |
|
|
|
B
где max 0,8,
а – постоянный коэффициент, принимаемый равным 0,85; r2 – радиус поворота по забегающей гусенице:
r2 = d + b.
Из схемы видно, что r = r2, и, таким образом, находим Wкр. Внутренние и внешние сопротивления гусеничного ходового
оборудования движению в процентах от веса экскаватора приведены в табл. 4.6.
118
Внутреннее сопротивление ходового механизма при движении задним ходом определяется из следующего выражения:
Wвн = W1 + W2 + W3 + W4 + W5 + W6 + W7, |
|
(4.42) |
||||
где W1 – сопротивление в подшипниках опорных катков; |
|
|
||||
W1 |
(G gзв ) fпр dоп |
, |
|
|
(4.43) |
|
|
|
|
|
|||
|
Dоп |
|
|
|
|
|
где fпр – приведенный коэффициент в подшипниках колес |
|
|
||||
( fпр ≈ 0,015÷0,2); |
|
|
|
|
|
|
|
|
|
|
|
Таблица 4.6 |
|
Сопротивление гусеничного хода движению, % веса машины |
|
|||||
Сопротивление |
Малоопорная |
Многоопорная |
||||
|
|
|
гусеница |
гусеница |
||
Подшипников опорных катков W1 |
1,6 |
– 1,8 |
1,6 |
– 1,8 |
||
ведущих колес W2 |
1,1 |
– 1,2 |
1,1 |
– 1,2 |
||
направляющих W3 |
|
0 – 1,6 |
0 – 1,6 |
|||
Катанию опорных катков W4 |
0,4 |
– 0,5 |
0,8 |
– 0,9 |
||
Изгибанию гусеничной цепи на ведущих |
|
|
|
|
|
|
колесах W5 |
1,3 |
– 1,5 |
1,3 |
– 1,5 |
||
То же, на направляющих колесах W6 |
0,4 ÷ 2,5 |
0,4 |
– 2,5 |
|||
Всего Wвн |
4,8 ÷ 9,1 |
5,2 |
÷ 9,5 |
|||
Сопротивление инерции при pазгоне Wn |
1 |
– 2 |
1 |
– 2 |
||
Сопротивление катанию на горизонтальном |
|
|
|
|
|
|
пути при трогании с места WK |
|
8 – 17,5 |
6,5 – 15 |
|||
Полное сопротивление на горизонтальном |
|
|
|
|
|
|
пути без разворота WГ |
13,8 |
– 27,8 |
12,7 |
– 25,7 |
W2 – сопротивление в подшипниках ведущих колес:
W2 |
|
1,5 Sтяг fпр dв.к. |
; |
(4.44) |
|
||||
|
|
Dв.к. |
|
W3 – сопротивление в подшипниках направляющих колес:
W3 |
|
2 Sтяг fпр dн.к. |
; |
(4.45) |
|
||||
|
|
Dн.к. |
|
W4 – сопротивление катанию опорных катков:
119