
Учебное пособие 800664
.pdfi |
kii |
|
xii |
, |
(4.3) |
|
|||||
|
|
|
r |
|
|
|
|
|
д |
|
где ii – передаточное отношение от вращающейся детали до колеса; rд - динамический радиус ведущего колеса.
Тогда без учета потерь на трение в трансмиссии общая кинетическая энергия колесного тягача
|
m 2 |
2 |
1 |
Jiii2 |
m 2 |
|
1 |
Jiii2 |
|
|
||||
T |
x |
|
|
x |
|
|
x |
1 |
|
|
. |
(4.4) |
||
2 |
2 |
r2 |
2 |
mr2 |
||||||||||
|
|
|
|
|
|
д |
|
|
|
|
д |
|
|
|
Для гусеничного тягача необходимо учитывать кинетическую энергию
гусениц |
m 2 |
/ 2 |
(где m – |
масса |
гусениц), |
а вместо r |
д |
подставлять радиус |
||||||
|
г x |
|
г |
|
|
|
|
|
|
|
|
|
|
|
ведущего колеса гусеничного движителя rвк |
|
|
|
|
||||||||||
|
|
|
|
|
m x2 |
|
|
mг |
1 |
2 |
|
|
|
|
|
|
|
Tг |
|
|
1 |
|
|
|
Jiii |
. |
|
(4.5) |
|
|
|
|
2 |
m |
mr2 |
|
||||||||
|
|
|
|
|
|
|
|
|
|
вк |
|
|
|
|
Таким образом, кинетическая энергия тягача выражается через кинетическую энергию поступательных масс, если выражение в скобках заменить коэффициентом учета вращающихся масс машины δ
|
колесн |
1 |
1 |
|
|
Jiii2 , |
|||
|
mr |
2 |
|||||||
|
|
|
mг |
|
д |
|
|
||
|
|
|
|
|
|
|
1 |
2 |
|
|
гусен 1 |
|
|
|
|
Jiii . |
|||
m |
|
mr2 |
|||||||
|
|
|
|
|
|
|
|
вк |
|
(4.6)
(4.7)
Точное определение δ затруднительно, поэтому для тяговых расчетов машин с механической и гидромеханической трансмиссией пользуются эмпирической зависимостью
1 c |
c i2 |
, |
(4.8) |
1 |
2 тр |
|
|
где c1 и c2 – эмпирические коэффициенты; iтр – общее передаточное число трансмиссии.
Для гусеничных машин
с1 0,25 0,4; |
c2 0,0025 0,0060. |
(4.9) |
Для колесных машин
100
c1 0,03 0,005; |
c2 0,0020 . |
Коэффициент c1 учитывает влияние масс движителя, а c2 – вращающихся масс двигателя. Массы коробки передач и других промежуточных агрегатов трансмиссии незначительно влияют на коэффициент δ.
При определении коэффициента δ для прицепов и полуприцепов можно пользоваться формулой
1 c, |
(4.10) |
где с = 0,02 – 0,05 в зависимости от количества осей прицепа. Используя выражения (4.4) и (3.5), можно получить дифференциал
кинетической энергии
dT m d . |
(4.11) |
Сумма элементарных работ внешних и внутренних сил
dWi dWe dWh dWf dW dWp dWв , |
(4.12) |
где dWe – элементарная работа двигателя; dWf – элементарная работа сил сопротивления качению; dWh – элементарная работа силы тяжести при движении на продольном уклоне; dWη – элементарная работа сил внутреннего трения в трансмиссии и движителе; dWp – элементарная полезная работа на рабочем органе или на крюке; dWв – элементарная работа сил сопротивления воздуха.
Если предположить, что в переходном режиме двигатель передает мощность, равную мощности в установившемся режиме, то элементарная работа (в эрг) за время dt
dWe 1000Ndt. |
(4.13) |
Элементарная работа силы сопротивления качению на элементарном перемещении dx при движении на подъем
dWf Gfdxcos . |
(4.14) |
Элементарная работа силы тяжести при движении на уклоне может в зависимости от направления движения быть положительной или отрицательной
dWh Gsin dx. |
(4.15) |
101
Элементарная работа сил внутреннего трения может быть выражена через коэффициент полезного действия трансмиссии
dW 1000N 1 dt . |
(4.16) |
Элементарная работа сил сопротивления Pр на крюке или рабочем органе
dWp Ppdx . |
(4.17) |
Элементарная работа сил Pв сопротивления воздуха
dW |
Pdx. |
(4.18) |
в |
в |
|
Обычно силу сопротивления воздуха рассчитывают по эмпирической формуле
P k F 2 |
, |
(4.19) |
|
в |
|
|
|
где kω – коэффициент обтекаемости; F – площадь лобового сопротивления, принимаемая равной произведению колеи тягача на его высоту. Сопротивление воздуха следует учитывать при ν > 50 км/ч.
Таким образом, уравнение кинетической энергии тягача примет вид
mvdv 1000N |
тр |
dt Gf cos dx Gsin dx P dx Pdx . |
(4.20) |
|
|
p |
в |
|
Разделив обе части на dx, после преобразования получим
m |
d2x |
|
1000Nд тр |
G f cos sin P |
P . |
(4.21) |
|
dt2 |
v |
||||||
|
|
p |
в |
|
Выражение (4.21) является дифференциальным уравнением движения тягача. Оно показывает, на что расходуется мощность двигателя. Его можно решать относительно ускорения тягача d2x/dt2, если известны все силы
сопротивления, или относительно силы Pр при известном ускорении (например,
при d2x/dt2 = 0).
Последний прием широко используется при тяговых расчетах транспортных машин [3, 5].
4.2. Рабочие органы (движители) транспортных машин
Большинство строительно-технологических машин оснащено устройствами для перемещения по опорной поверхности по произвольной траектории. Таковым устройством (рабочим органом) может быть колесо
102
(колесный движитель), гусеница (гусеничный движитель), роторно-винтовой движитель, движители дискретного взаимодействия с опорной поверхностью (шагающая система).
Перемещение машин по опорным поверхностям с малой несущей способностью достигается использованием воздушной подушки. Из названных видов движителей в строительно-технологических машинах в основном применяются колесные и гусеничные движители. Реже применят шагающие движители. Эти движители (кроме шагающих) могут работать как в транспортном, так и тяговом режиме в зависимости от задач, которые решаются технологической машиной. Другие названные виды движителей могу быть эффективны только в определенных условиях.
4.2.1. Колесные движители строительных машин
Взаимодействие колесного движителя технологической машины с опорной поверхностью реализуется в нескольких практических ситуациях:
-качение жесткого колеса по твердой поверхности (кранового колеса по рельсу);
-качение деформируемого колеса по деформируемой поверхности (пневматического колеса скрепера по свежесрезанному грунту);
-качение деформируемого колеса по твердой поверхности (пневматического колеса автомобиля по асфальтобетону).
В кинематических и статических расчетах технологических машин используют такие параметры колесного движителя: наружный диаметр Dк, свободный радиус ненагруженного колеса r0= Dк /2 и радиальная нагрузка Fр. Под действием радиальной нагрузки любое колесо деформируется в зоне контакта на величину δ. Величина деформации зависит также от свойств и параметров колеса и свойств опорной поверхности. Свободный радиус деформированного колеса уменьшается на величину δ и характеризуется статическим радиусом колеса Rcт= R0 – δ. Качение по опорной поверхности нагруженного радиальной нагрузкой колеса характеризуется кинематическим радиусом rк, отличным от статического радиуса.
rк = Vк /ωк , |
(4.22) |
где Vк – поступательная скорость оси колеса; ωк – угловая скорость вращения колеса.
При качении колеса по опорной поверхности на него действует ряд факторов (радиальная нагрузка, крутящий момент, центробежная сила, давление воздуха в пневматической шине, сила сопротивления качению), которые изменяют статический радиус. Катящееся колесо в реальных условиях взаимодействия с опорной поверхностью характеризуется динамическим радиусом rд. Динамический радиус такого колеса подвержен влиянию скорости
103
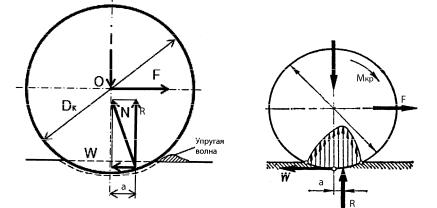
колеса Vк и подводимого к нему крутящего момента Мкр. При увеличении скорости движения машины динамический радиус увеличивается, а при увеличении крутящего момента – уменьшается.
Важным фактором взаимодействия колеса с опорной поверхностью является радиальная статическая жесткость колеса. Статическую жесткость колеса определяют по формуле
ск = Fр / δ, |
(4.23) |
где Fр – изменение вертикальной нагрузки на колесо.
Применяемые колесные движители строительно-технологических машин существенно различаются по статической жесткости. Однако, принципиальный характер взаимодействия стального колеса с рельсом и пневматической шины с грунтовой опорной поверхностью аналогичен. При качении этих колес по опорной поверхности возникает сопротивление качению, которое будет отличаться по величине в силу различной жесткости колес при одинаковой вертикальной нагрузке.
При качении стального колеса по стальному рельсу происходит образование наплыва впереди колеса и явление упругого гистерезиса, как показано на рис. 4.1, а. В результате эпюра сил сжатия по поверхности контакта становится несимметричной относительно вертикальной оси.
а б Рис. 4.1. Схемы взаимодействия колесного движителя с опорной
поверхностью: а – качение стального колеса по рельсу; б – эпюра давлений колеса на опорную поверхность
На рис. 4.1, б показана эпюра сил давления в зоне контакта при качении колеса по опорной поверхности. В правой части от оси колеса пятно контакта сопровождается повышенным давлением из-за суммарной деформации колеса и бегущей волны опорной поверхности. В левой части происходит упругое восстановление формы контактируемых поверхностей. Давление здесь получается меньше. Равнодействующая сил давления будет смещена от оси колеса по ходу его движения на расстояние "а", создавая момент сопротивления вращению Мс = Fр∙а. Качение колеса станет возможным, если к
104
колесу приложить крутящий момент Мкр ≥ Мс или толкающую силу Fт, которая создаст момент для вращения колеса
Мв= Fт∙rк∙ ≥ Мс. |
(4.24) |
В первом случае колесо будет называться ведущим, во втором случае – ведомым.
Если колесо при взаимодействии с опорной поверхностью создает момент сил трения, противодействующий подводимому к колесу крутящему моменту, такое колесо называют тормозным.
Из уравнения моментов сил относительно оси колеса Fp∙ a = Wк∙ rк определяют силу сопротивления качению
Wk = Fp∙а/rк. |
(4.25) |
Отношение a/rк = fк называют коэффициентом сопротивления качению. Коэффициент сопротивления качению стальных колес по рельсам зависит
от диаметра и материала колес, а также от формы контактирующих поверхностей. Численная величина этого коэффициента представлена в табл. 4.2.
Таблица 4.2
Коэффициент сопротивления качению fк, мм, стальных колес по рельсам
Головка |
|
Диаметр ходового колеса, мм |
|
||
рельса |
200 - 320 |
400 - 630 |
710 |
800 - 900 |
1000 |
|
|
|
|
|
|
Плоская |
0,3 |
0,5 |
0,6 |
0,7 |
0,7 |
Скругленная. |
0,4 |
0,6 |
0,8 |
1,0 |
1,2 |
При качении колеса энергия расходуется не только на преодоление сопротивления качению в зоне контакта, но и на преодоление сопротивлений сил трения на оси колеса. Конструкция обода колеса также может создавать дополнительные сопротивления. Величина их определяется конструктивным исполнением элементов ориентации колеса на рельсе. Сопротивление качению стального колеса по горизонтальному рельсу без учета других факторов (ветра, уклона опорной поверхности, сил инерции) определяют по формуле:
W Fp |
|
o do 2 fk |
fp, |
(4.26) |
|
||||
|
|
Dk |
|
где μо – коэффициент трения на оси колеса; dо – диаметр оси колеса;
fp – коэффициент трения реборд.
Другой распространенный вид рабочего органа транспортной машины представляет пневматическое колесо в виде упругой оболочки, заполненной
105

воздухом под давлением. Оболочка устанавливается на стальном ободе, который крепится на оси ходовой рамы машины. Ходовая рама с несколькими пневматическими колесами создает опорный контур строительной или транспортной машины. Наиболее распространен четырехопорный прямоугольный контур. Через обод на колесо может передаваться и крутящий момент. В этом случае колесо называют ведущим.
Пневматическая оболочка колеса имеет конструктивные элементы со специфическими названиями (рис. 4.2). Оболочка состоит из борта 1, бортовой проволоки 2, каркаса 3, брекера 4, боковины 5, протектора 6.
Шины различают по конструкции каркаса. В радиальной шине нити в слоях каркаса, и брекера параллельны друг другу. В каркасе нити имеют меридиональное направление от борта к борту, а направление нитей в слоях брекера близко к окружному.
В диагональной шине каркас и брекер состоят из слоев с перекрещивающимися нитями корда под углом 45 – 60°.
Рис. 4.2. Конструкция каркаса пневматических шин: а – с диагональным каркасом; б – с радиальным каркасом. 1 – борт; 2 – бортовая проволока; 3 – каркас; 4 – брекер; 5 – боковины; 6 – протектор
Каркас шины – это силовой элемент, воспринимающий радиальную нагрузку на шину. Каркас образуют один или несколько слоев обрезиненного корда, закрепленного на бортовых кольцах.
Брекером называют пояс, охватывающий каркас покрышки по его внешней части непосредственно под протектором.
Протектор – это толстая резиновая рельефная часть покрышки, которая непосредственно соприкасается с дорогой. Рельефный рисунок протектора определяет приспособленность шины для разных дорожных условий. Рельеф протектора относят к одному из типов ( рис. 4.3): дорожный, универсальный, зимний, повышенной проходимости. Рисунок протектора может быть
106
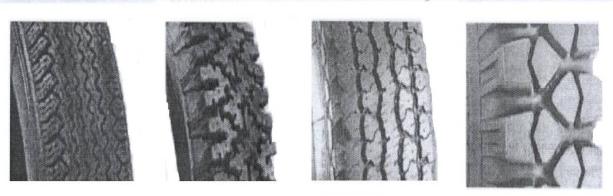
направленным и ненаправленным. Шина с ненаправленным рисунком протектора устанавливается на ходовой раме машины произвольно, с направленным рисунком должна быть установлена по направлению стрелки на ее боковине.
а |
б |
в |
г |
Рис. 4.3. Рисунки протекторов шин: |
а – дорожный; |
б – зимний; |
|
в – универсальный; |
г – повышенной проходимости |
|
Конструкция шины во многом определяет ее жесткость. Наибольшей жесткостью обладают шины с диагональным расположением слоев корда. Шины с радиальным кордом всегда мягче шин с диагональным кордом. Диагональные шины более долговечны, имеют хорошее сцепление с дорогой, пониженное сопротивление качению. Диагональные шины предпочтительны в условиях бездорожья при высоких ударных нагружениях на плохих дорогах.
В зависимости от способа соединения шины с ободом различают колеса камерные и бескамерные. Камерная шина состоит из наружной части (покрышки) и внутренней герметичной оболочки (камеры). Бескамерная шина
– это усовершенствованная покрышка, выполняющая одновременно роль покрышки и камеры.
Шины различаются профилем – наружным контуром в радиальном сечении при установке на соответствующем ободе. Профиль шины замеряют без нагрузки при заданном в ней давлении воздуха (рис. 4.4).
Наружный диаметр D – наибольший диаметр радиального сечения шины. Посадочный диаметр d – диаметр цилиндра, контактирующий с
основанием борта шины.
Ширина профиля В – расстояние между двумя плоскостями при касании ими боковин шины.
Высота профиля Н – полуразность между наружным и посадочным диаметром шины.
107
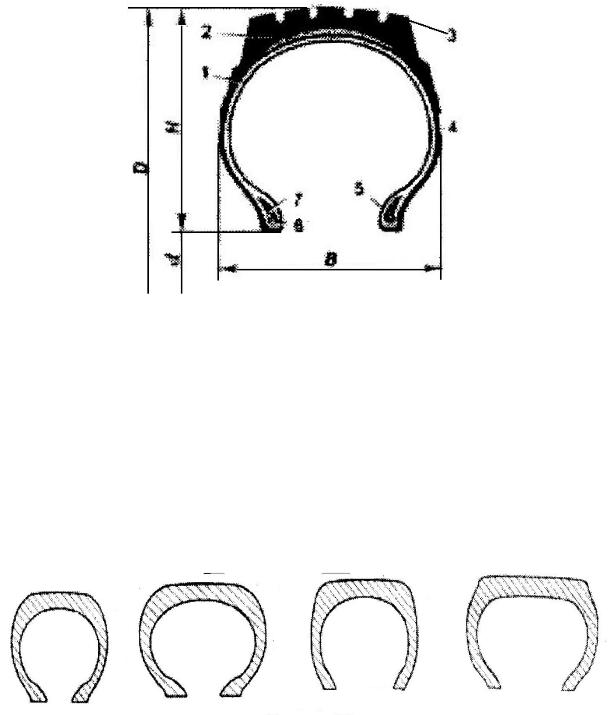
Рис. 4.4. Параметры профиля шины
По конфигурации профиля радиального сечения шины в зависимости от отношения высоты Н к ширине профиля В выделяют шины обычного профиля
– Н/В > 0,8 (рис. 4.5, а), широкопрофильные – 0,6 < Н/В < 0,8 (рис. 4.5, б),
низкопрофильные шины – 0,71 < Н/В < 0,85 (рис. 4.5, в), сверхнизкопрофильные – Н/В < 0,70 (рис. 4.5, г).
На радиальную жесткость шин большое влияние оказывает давление сжатого воздуха в шине. Жесткость шин и податливость упругих элементов подвески должна быть согласована.
а |
б |
|
в |
г |
Рис. 4.5. Конфигурация |
профилей |
шин: |
а – обычный профиль; |
|
б – широкопрофильная |
шина; в |
– |
низкопрофильная шина; |
|
г – сверхнизкопрофильная шина |
|
|
|
|
Автомобильные |
заводы |
рекомендуют |
соблюдать предписанные |
типоразмеры шин, давление воздуха в них и параметры подвески для конкретных марок автомобилей.
108
Шины российского производства в соответствии с ГОСТ 4754 должны иметь:
-товарный знак производителя;
-наименование страны-производителя;
-обозначение шины;
-торговая марка (модель шины);
-индекс несущей способности (грузоподъемности) (табл. 4.3);
-индекс категории скорости (табл. 4.4);
-“Tubeless” – для бескамерных шин;
-“Reinforced” – для усиленных шин;
-“M+S” – для зимних шин;
-“All seasons” – для всесезонных шин;
-“ PSI” – индекс давления от 20 до 85 для шин с индексом «С»;
-“E” – знак официального утверждения с номером утверждения и страны, выдавшей сертификат;
-«ГОСТ 4754»;
-знак направления вращения для шин с направленным рисунком протектора;
-“TWI” – место расположения индикатора износа;
-дату изготовления из трех цифр (две цифры обозначают неделю, третья – год;
-штамп технического контроля.
Таблица 4.3
Индексы и величина нагрузки шин
Индекс |
60 |
66 |
72 |
76 |
80 |
84 |
87 |
90 |
93 |
96 |
98 |
100 |
Нагрузка, |
250 |
300 |
355 |
400 |
450 |
500 |
545 |
600 |
650 |
710 |
750 |
800 |
кг |
|
|
|
|
|
|
|
|
|
|
|
|
Индекс |
101 |
102 |
103 |
104 |
105 |
106 |
108 |
110 |
111 |
113 |
114 |
116 |
Нагрузка, |
825 |
850 |
875 |
900 |
925 |
950 |
1000 |
1060 |
1090 |
1150 |
1180 |
1250 |
кг |
|
|
|
|
|
|
|
|
|
|
|
|
Индекс |
118 |
119 |
120 |
121 |
122 |
123 |
124 |
125 |
126 |
127 |
128 |
129 |
Нагрузка, |
1320 |
1360 |
1400 |
1450 |
1500 |
1550 |
1600 |
1650 |
1700 |
1750 |
1800 |
1850 |
кг |
|
|
|
|
|
|
|
|
|
|
|
|
|
|
|
|
Обозначение индексов скорости |
|
|
Таблица 4.4 |
||||||||
|
|
|
|
|
|
|
|
||||||||
Индекс |
|
J |
|
K |
L |
M |
N |
P |
Q |
R |
S |
T |
U |
H |
|
скорости |
|
|
|
|
|
|
|
|
|
|
|
|
|
|
|
Скорость |
|
100 |
110 |
120 |
130 |
140 |
150 |
160 |
170 |
180 |
190 |
200 |
210 |
|
|
макс, |
|
|
|
|
|
|
|
|
|
|
|
|
|
|
|
км/час |
|
|
|
|
|
|
|
|
|
|
|
|
|
|
|
На рис. |
4.6 |
показан пример обозначений на шине необходимой о ней |
информации.
109