
Учебное пособие 800438
.pdfпри этом изменяется не только химический состав, но и свойства стали.
Специальные элементы, которые преднамеренно добавляют в углеродистую сталь при ее выплавке с целью получения требуемых свойств стали, называются легирующими элементами, а полученная сталь — легированной сталью. Суммарное содержание легирующих элементов в стали, выраженное в весовых процентах, называется степенью легирования.
Такие постоянно присутствующие в стали элементы, как марганец и кремний, считаются легирующими элементами при содержании марганца более 1% и кремния более 0,8%.
Легированием стали (различными элементами в разном количестве) и применением соответствующей термической обработки можно получить, по сравнению с углеродистой сталью, большую вязкость при одинаковой прочности, большую прочность при одинаковой вязкости и даже более высокие и прочность и вязкость.
Но преимущества легированных сталей по сравнению с углеродистыми заключаются не только в более высоких механических свойствах. Легированием можно изменить и физикохимические свойства стали, получить сталь нержавеющую, кислотостойкую, жаропрочную, немагнитную, магнитную, с особыми тепловыми и электрическими свойствами.
1.7.15.Классификация легированных сталей
Воснову классификации легированных сталей заложены четыре признака: равновесная структура (после отжига), структура после охлаждения на воздухе (после нормализации), состав и назначение сталей.
По типу равновесной структуры стали подразделяются на доэвтектоидные, эвтектоидные, заэвтектоидные и ледебуритные.
71
Эвтектоидные стали имеют перлитную структуру, а доэвтектоидные и заэвтектоидные наряду с перлитом содержат соответственно избыточный феррит или вторичные карбиды типа МезС.
В структуре литых ледебуритных (карбидных) сталей присутствует эвтектика (ледебурит), образованная первичными карбидами вкупе с аустенитом; поэтому по структуре они могут быть отнесены к белым чугунам, но их причисляют к сталям с учетом меньшего, чем у чугунов, содержания углерода (< 2%) и возможности подвергать пластической деформации.
Классификация по структуре после нормализации предполагает разделение сталей на три основных класса: перлитный, мартенситный и аустенитный.
Классификация по химическому составу предполагает разделение легированных сталей (в зависимости от вводимых элементов) на хромистые, марганцовистые, хромоникелевые, хромоникельмолибденовые и т.п.
Согласно той же классификации стали подразделяют по общему количеству легирующих элементов в них на низколегированные (до 2,5% легирующих элементов), легированные (от 2,5 до 10%) и высоколегированные (более 10%).
Разновидностью классификации по химическому составу является классификация по качеству. Качество стали — это комплекс свойств, обеспечиваемых металлургическим процессом, таких, как однородность химического состава, строения и свойств стали, ее технологичность. Эти свойства зависят от содержания газов (кислород, азот, водород) и вредных примесей — серы и фосфора.
По качеству легированные стали подразделяют на качественные (до 0,04% S и до 0,035% Р), высококачественные (до 0,025% S и до 0,025% Р) и особовысококачественные (до
0,015% S и до 0,025% Р).
72
По назначению стали подразделяют на конструкционные (например, цементуемые, улучшаемые), инструментальные и стали с особыми свойствами. К последним относят «автоматные», пружинные, шарикоподшипниковые, износостойкие, коррозионностойкие, теплоустойчивые, жаропрочные, электротехнические и другие стали.
1.7.16. Маркировка легированных сталей
Обозначение марки включает в себя цифры и буквы, указывающие на примерный состав стали. В начале марки приводятся двузначные цифры (например, 12ХН3А), указывающие среднее содержание углерода в сотых долях процента. Буквы справа от цифры обозначают легирующие элементы: А - азот, Б - ниобий, В - вольфрам, Г - марганец, Д - медь, Е - селен, К - кобальт, Н - никель, М - молибден, П - фосфор, Р - бор, С - кремний, Т - титан, Ф - ванадий, Х - хром, Ц - цирконий, Ч - редкоземельные элементы, Ю — алюминий. Следующие после буквы цифры указывают примерное содержание (в целых процентах) соответствующего легирующего элемента (при содержании 1…1,5% и менее цифра отсутствует, например 30ХГС).
Высококачественные стали обозначаются буквой А, а особовысококачественные — буквой Ш, помещенными в конце марки (30ХГСА, 30ХГСШ). Если буква А расположена в середине марки (14Г2АФ), то это свидетельствует о том, что сталь легирована азотом.
При обозначении автоматных сталей с повышенной обрабатываемостью резанием буква А ставится в начале марки (А20, А40Г). Если автоматная сталь легирована свинцом, то обозначение марки начинается с сочетания букв АС (АС35Г2, где цифра 35 обозначает среднее содержание углерода в сотых долях процента). Маркировка шарикоподшипниковой стали начинается с буквы Ш (ШХ 15, где 15 — среднее содержание
73
хрома в десятых долях процента). В начале обозначения марки быстрорежущих сталей стоит буква Р, за которой следует цифра, отражающая концентрацию вольфрама (Р18, Р6М5). Опытные стали, выплавленные на заводе «Электросталь», первоначально обозначают буквами ЭИ (электросталь исследовательская) или ЭП (электросталь пробная) с порядковым номером разработки (освоения), например ЭИ962 (11Х11Н2В2МФ), ЭП33 (10Х11Н23ТЗМР). Такое упрощенное обозначение сталей, особенно высоколегированных, в дальнейшем широко используется и в заводских условиях.
При маркировке сплавов на железоникелевой основе указывается количественное содержание никеля (в процентах) с перечислением лишь буквенных обозначений остальных легирующих элементов, например ХН38ВТ, ХН45МВТЮБР.
1.7.17. Хромомарганцевокремнистая сталь (хромансиль)
Хромомарганцевокремнистая сталь (хромансиль) является основной самолетной сталью [6,7].
Сталь ЗОХГСА в среднем содержит 0,3 % углерода и по 1,0 % хрома, марганца и кремния. Она обладает высокими механическими свойствами, хорошей свариваемостью, хорошей (до 25 мм) прокаливаемостью, удовлетворительной обрабатываемостью режущими инструментами и высокой пластичностью в отожженном состоянии, что позволяет проводить гибку, выколотку и штамповку. Для изготовления деталей самолетов хромансиль поступает в виде листов, профилей, труб, прутков, поковок и проволоки.
Сталь ЗОХГСА употребляется для ответственных сварных и механически обрабатываемых деталей: стыковых соединений, полок, поясов, деталей шасси, болтов и т. п.
Высокопрочная самолетная сталь ЗОХГСНА содержит 1,6 % никеля, что придает ей повышенную прочность, пла-
74
стичность и вязкость. Но при обработке этой стали на высокую прочность она приобретает повышенную чувствительность к концентрации напряжений при статической и особенно при многократной статической нагрузке.
Сталь ЗОХГСНА хорошо сваривается дуговой сваркой, удовлетворительно - атомноводородной, плохо - газовой, обладает высокой прокаливаемостью (до 50 - 60 мм), но проявляет склонность к образованию флокенов. Сталь ЗОХГСНА применяется для изготовления наиболее ответственных деталей шасси, крыла и центроплана самолета, стыковых соединений, полок лонжерона и болтов.
Для уменьшения коробления и поводки, устранения закалочных трещин охлаждение стали хромансиль при закалке необходимо проводить в масле или в горячей воде (60 – 70 °С), а при обработке сложных конструкций рекомендуется изотермическая или ступенчатая обработка.
Также разработаны новые высокопрочные стали, которые обладают высокими механическими свойствами, хорошей свариваемостью и идут на изготовление деталей самолета не только простой, но и сложной конфигурации. По химическому составу эти стали от стали хромансиль отличаются тем, что они легированы не только никелем, как сталь ЗОХГСНА, но и другими элементами, такими как вольфрам, молибден, алюминий и титан.
Сталь 25ХГСА применяется для изготовления ответственных сварных и штампованных деталей. Особенно рекомендуется она, когда необходимы хорошая свариваемость и значительная пластическая деформация деталей в процессе изготовления. Благодаря пониженному содержанию углерода (0,22 - 0,29 %) эта сталь сваривается и штампуется лучше, чем сталь ЗОХГСА.
Сталь 30Х2ГСН2ВМ (ВЛ1) служит для изготовления деталей сложной конфигурации (лонжероны крыла, стабилизатора, шпангоуты фюзеляжа). Сваривается ручной дуговой
75
сваркой, после которой, не допуская охлаждения сварных швов ниже 200°, детали переносят в печь с температурой 650° и далее охлаждают на воздухе.
Сталь ЭИ643 рекомендуется для деталей шасси и болтов, работающих на срез, растянутых и сжатых поясов лонжеронов конструкций одноразового действия, сжатых поясов лонжеронов конструкций многоразового действия и других ответственных деталей, не имеющих значительных концентраторов напряжений. Сталь сваривается ручной дуговой и автоматической сваркой под флюсом. Конструкции можно подвергать термической обработке после сварки или изготавливать из термически обработанных элементов.
1.7.18. Чугуны
Чугуны — более дешевый материал, чем стали. Содержание углерода в них больше 2,14%. Они обладают хорошими литейными свойствами и пониженной температурой плавления. За счет этого из чугунов можно делать отливки значительно более сложной формы, чем из сталей [3,4,5].
В зависимости от того, в какой форме присутствует углерод в сплавах, различают белые, серые, высокопрочные и ковкие чугуны. Высокопрочные чугуны являются разновидностью серых, но из-за повышенных механических свойств их выделяют в особую группу.
Белый чугун. Такое название он получил по виду излома, который имеет матово-белый цвет. Весь углерод в этом чугуне находится в связанном состоянии в виде цементита. В этих чугунах фазовые превращения протекают согласно диаграмме состояния (Fe—Fe3C). Эти чугуны имеют большую твердость (НВ 450...550) из-за присутствия в них большого количества цементита; и как следствие этого, они очень хрупкие и для изготовления деталей машин не используются. От-
76
ливки из белого чугуна служат для получения деталей из ковкого чугуна с помощью графитизирующего отжига.
Отбеленные чугуны-отливки имеют поверхностные слои (12…30 мм) со структурой белого чугуна, а сердцевина — серого чугуна. Высокая твердость поверхности такой отливки позволяет ей хорошо работать против истирания. Эти свойства отбеленного чугуна применяются для изготовления валков листовых прокатных станов, колес, шаров для мельниц, тормозных колодок и многих других деталей, работающих в условиях износа.
Серый чугун. Такое название чугун получил по виду излома, который имеет серый цвет. В структуре серого чугуна имеется графит. Поскольку структура чугуна состоит из металлической основы и графита (в форме пластин), то и свойства его будут зависеть от этих двух составляющих.
По структуре металлической основы серые чугуны разделяют на три вида.
1.Серый перлитный со структурой перлит + графит. Количество связанного углерода составляет 0,8%.
2.Серый ферритно-перлитный со структурой феррит + перлит +графит. Количество связанного углерода < 0,8%.
3.Серый ферритный со структурой феррит + графит. Весь углерод в виде графита.
Марка серого чугуна состоит из букв Сч (серый чугун) и
цифры, показывающей значение временного сопротивления при растяжении (кгс/мм2), например, Сч15, Сч40.
Графит способствует измельчению стружки при обработке резанием и оказывает смазывающее действие, что повышает износостойкость чугуна. Номенклатура отливок из серого чугуна и их масса разнообразны: от деталей в несколько граммов до 100 т и более.
Для деталей, работающих при повышенных температурах, применяют легированные серые чугуны, которые дополнительно содержат хром, никель, молибден и алюминий.
77
Высокопрочный чугун. Высокопрочными называют чугуны, в которых графит имеет шаровидную форму. Их получают путем модифицирования магнием. Этот процесс сопровождается сильным возгоранием, поэтому чистый магний заменяют лигатурами (например, сплавом магния и никеля).
Чугуны с шаровидным графитом имеют более высокую прочность и при этом некоторую пластичность.
Маркируются высокопрочные чугуны по пределу прочности (σв) и относительному удлинению (δ), например Вч45-5, где ~ 45 кгс/мм2 — предел прочности, а ~ 5% — относительное удлинение.
Ковкий чугун. Ковкими называют чугуны, в которых графит имеет хлопьевидную форму. Их получают в результате специального графитизирующего отжига доэвтектического белого чугуна. Графит в таких чугунах называют углеродом отжига. По сравнению с серым, ковкий чугун обладает более высокой прочностью, что связано с меньшим влиянием хлопьевидной формы графита на механические свойства металлической основы.
Полное отсутствие литейных напряжений, которые снимаются за счет длительного отжига, и разобщенность графитовых включений обусловливают высокие механические свойства ковких чугунов.
Маркировка ковких чугунов: буквы Кч и цифры (как у высокопрочных чугунов), например, Кч30-6, Кч80-1,5.
2. МАТЕРИАЛЫ С ОСОБЫМИ СВОЙСТВАМИ
2.1. Конструкционные композиционные материалы на металлической матрице
Композиционные материалы (КМ) - это объемноармированные различными наполнителями металлы, сплавы,
78
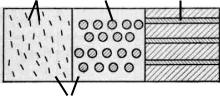
полимеры [6]. Прочность, жесткость и другие эксплуатационные характеристики таких материалов значительно выше. Уже сейчас известны многочисленные примеры успешного применения КМ. Алюминий, армированный стальной проволокой, применяется для изготовления оболочек ракет и топливных баков. Массу топливных баков при этом удается снизить на 14 % при сохранении эксплуатационных характеристик. Некоторые элементы фюзеляжа военных самолетов изготавливаются из алюминиевых сплавов, армированных волокнами бора и проволокой из стали. Использование КМ в двигателе аппаратов вертикального взлета снижает массу двигателя на 33 %, а массу маршевых двигателей на 45 %.
По форме наполнителя можно выделить три типа КМ: КМ, армированные частицами, КМ, армированные волокнами, слоистые КМ. Схемы образования структур таких материалов показаны на рис. 26. Для уменьшения анизотропии волокнистых КМ, слои волокон могут располагаться под разными углами друг к другу.
Частицы Волокна Слои
Матрица
Рис. 26. Схема структур композиционных материалов (КМ) [6,7]
79
2.1.1. Композиционные материалы, армированные частицами
Микроструктура материалов, упрочненных частицами, состоит из матрицы и равномерно в ней распределенных упрочняющих частиц [6]. Если размер упрочняющих частиц l ≤ 10-5 см, то материал называют дисперсно-упрочненным, если l ≥ 10-4 см, то это – материалы, упрочненные частицами. Объемная доля упрочняющей фазы в КМ первого типа может быть различной и колеблется от нескольких (в дисперсноупрочненных КМ) до десятков процентов в КМ, упрочненных частицами.
Получают КМ, армированные дисперсными частицами, методами порошковой металлургии. Основными технологическими этапами этих методов являются: получение порошковых смесей, прессование порошков, спекание с последующей деформацией и термическая обработка.
Вдисперсно-упрочненных материалах матрица воспринимает основную часть внешней нагрузки, а дисперсные частицы создают эффективное сопротивление перемещению дислокаций в объеме зерна. Чем больше это сопротивление, тем выше степень упрочнения материала.
Такие материалы обладают высокой температурной стабильностью структуры, что позволяет им сохранять прочно-
стные характеристики в широком температурном интервале, вплоть до (0,7 ..0,8) tплм, где tплм - температура плавления матрицы.
Вматериалах, упрочненных частицами, нагрузка распределяется между матрицей и частицами.
Примерами отечественных дисперсно-упрочненных КМ являются ВДУ-1, ВДУ-2 и ВДУ-3. Матрицей КМ ВДУ-1 и ВДУ-2 является никель, дисперсными упрочнителями частицы оксидов тория и гафния с содержанием частиц до 5 % .
80