
Базы данных материалов для САПР в машиностроении. Елисеев В.В., Хливненко Л.В
.pdfБАЗЫ ДАННЫХ МАТЕРИАЛОВ ДЛЯ САПР В МАШИНОСТРОЕНИИ
Учебное пособие
Воронеж 2018
МИНИСТЕРСТВО НАУКИ И ВЫСШЕГО ОБРАЗОВАНИЯ РОССИЙСКОЙ ФЕДЕРАЦИИ
Федеральное государственное бюджетное образовательное учреждение высшего образования «Воронежский государственный технический университет»
БАЗЫ ДАННЫХ МАТЕРИАЛОВ ДЛЯ САПР В МАШИНОСТРОЕНИИ
Учебное пособие
Утверждено учебно-методическим советом университета в качестве учебного пособия
Воронеж 2018
1
УДК 539.37, 621 (075.8) ББК 34.42я7
Б179
Рецензенты:
кафедра технической механики Воронежского государственного университета инженерных технологий (зам. зав. кафедрой д-р техн. наук, проф. В. Г. Егоров); д-р техн. наук, проф. С. С. Одинг
Авторский коллектив:
В. В. Елисеев, Л. В. Хливненко, А. М. Гольцев, Ю. Б. Рукин, Н. С. Переславцева
Базы данных материалов для САПР в
Б179 машиностроении: учебное пособие / В. В. Елисеев [и др.]; ФГБОУ ВО «Воронежский государственный технический университет». - Воронеж: Изд-во ВГТУ, 2018. - 94 с.
ISBN 978-5-7731-0710-1
Учебное пособие включает краткое теоретическое описание и методику выполнения лабораторных работ по определению механических характеристик материалов, а также технологических параметров процесса пластического формообразования.
Издание соответствует требованиям Федерального государственного образовательного стандарта высшего образования по направлению подготовки бакалавров 22.03.01 «Материаловедение и технологии материалов» (профиль «Физическое материаловедение»), дисциплине «Механика материалов и основы конструирования».
Ил. 47. Табл. 10. Библиогр.: 9 назв.
|
УДК 539.37,621 (075.8) |
|
ББК 34.42я7 |
ISBN 978-5-7731-0710-1 |
© ФГБОУ ВО «Воронежский |
|
государственный технический |
|
университет», 2018 |
2
ВВЕДЕНИЕ
Основные данные, необходимые для моделирования операции пластического формообразования на прессовом оборудовании с ЧПУ, можно разделить на три типа: основные механические характеристики сопротивления пластическому деформированию, предельные характеристики пластичности материала различной природы, параметры поверхности начала пластического течения [9]. Для моделирования операций пластического течения требуются также и характеристики взаимодействия заготовки с инструментом.
К первому типу данных относятся стандартные характеристики прочности и пластичности материалов: пределы прочности и текучести, равномерная деформация и относительное остаточное удлинение. Сюда же следует отнести параметры анизотропии, которые описывают анизотропию свойств большинства листовых материалов.
Ко второму типу данных относят предельные деформационные свойства сплава, превышение которых приводит к появлению различных браковочных признаков на поверхности детали: недопустимый рост зерна, выпучивание складки, линии скольжения, трещины, разрывы и т.д.
Третий раздел механических характеристик предназначен для описания поверхности начала пластического течения материала для различных условий пластического течения [4].
Четвертый тип данных включает условия трения в области контакта заготовки с инструментом, которые описываются обычно коэффициентами трения и технологическими параметрами процесса, влияющими на характер трения между заготовкой и инструментом.
Результаты испытаний используют в различных вычислительных пакетах на базе метода конечных элементов
(ANSYS, ABAQUS, PAM-STAMP, LS-DYNA, RADIUS, PAM CRASH и др.) для прогнозирования разрушения деталей в
3
процессе динамического воздействия на конструкцию, т.е. Crash test. Прогноз предельного поведения материала заготовки строится на диаграммах предельных деформаций и диаграмме разрушения, основанных на модели разрушения срезом и отрывом.
Необходимо также отметить, что большинство механических и технологических характеристик материалов зависят от скорости деформирования, особенно важных в случае динамического нагружения, когда скорость деформирования достигает 103 с-1.
Точность и эффективность моделирования технологических операций зависит не в последнюю очередь от точности определения механических характеристик. Для решения этой задачи необходима автоматизация процессов измерения и совершенных методов обработки результатов испытаний с использованием современных компьютерных систем и электронных датчиков измерений.
Компьютерная модель конструкции помимо базы данных геометрии деталей включает базу данных материалов. Эксплуатация деталей происходит в упругой области материала. Однако их изготовление и поведение в критических ситуациях обычно приходится на пластическую область. Поэтому для изготовления деталей без дефектов и прогнозирования отказов необходимо знать предельные свойства материалов.
В настоящем пособии студентам предлагается познакомиться с основными видами механических и технологических испытаний, которые необходимо проводить в ЦЗЛ авиационного и машиностроительного предприятия для формирования баз данных САПР технологических операций холодной штамповки деталей из листа и профиля.
Все приведенные в пособии иллюстрации – авторские.
4
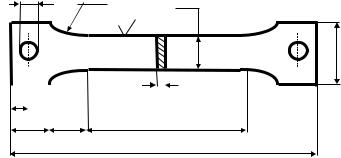
ГЛАВА 1. МЕХАНИЧЕСКИЕ ХАРАКТЕРИСТИКИ МАТЕРИАЛОВ
1.1. Лабораторная работа № 1 Определение параметров кривой течения по испытаниям
на одноосное растяжение
Цель работы: определение характеристик сопротивления пластическому деформированию материала параметров аппроксимации кривой течения в координатах обобщенное истинное напряжение - обобщенная пластическая логарифмическая деформация e уравнением Свифта:
A(e )m, |
(1.1) |
0 |
|
где А, m, 0 - параметры аппроксимации.
1.1.1. Методика испытаний
Вырезаются образцы из полки профильной детали. Размеры образца для испытаний на одноосное растяжение представлены на рис. 1.1.
12 |
R30 |
20 |
0.10 |
2 отв. |
|
|
|
|
2,5 |
|
|
|
|
|
|
|
|
h |
|
|
|
|
|
|
|
|
20 |
|
|
|
|
|
|
|
h* толщина образца |
|||
40 |
40 |
|
|
80 0.10 |
240
40
Рис. 1.1
5
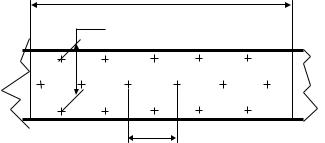
Подготовка образцов к испытанию: размеры поперечного сечения образца в области рабочей длины измеряются с точностью 0.01 мм. Первоначальная площадь поперечного сечения F0 определяется как минимальная по результатам двух-трех измерений ширины B0 и толщины h0 в области расчетной длины образца. На рабочей длине наносят границы на базе l0 =80 мм и прямоугольную сетку с шагом 15 мм. Точность нанесения сетки 0.02 мм (рис. 1.2).
Расчетная длина образца l0=80 мм
b0
a0
Рис. 1.2
Испытания: проводят на стандартном оборудовании, обеспечивающем растяжение образца по схеме одноосного растяжения при постоянной скорости деформирования
0.001-0.005c-1.
Измерение растягивающего усилия и осевого удлинения производят электронными аналоговыми датчиками, сигнал с которых поступает на карту оцифровки в персональный компьютер (рис.1.3). С помощью специального программного обеспечения, написанного в среде LABVIEW-7, производится оцифровка и визуализация диаграммы растяжения в режиме реального времени. Эта функция обеспечивает получение табулированной диаграммы растяжения, которая записывается в текстовый файл для последующей обработки и построения
6

кривой течения материала в координатах: истинное напряжение – логарифмическая деформация.
Диаграмму растяжения записывают в координатах: растягивающее усилие Р (Н) - удлинение l (мм); максимальное растягивающее усилие Fm (H); утонение или ширина границ рабочей части образца на расстоянии не менее ширины образца от места разрушения.
Системарегистрации,обработки и визуализации экспериментальныхданных
Датчик
крутящего момента. Датчикулов кручения
Датчик
усилия
Датчик |
|
BMC |
|
карта |
|
осевого |
|
|
удлинения |
|
|
|
|
|
|
|
|
Датчик
окружного
удлинения
Датчик
давления
Рис. 1.3
1.1.2. Обработка результатов испытаний В результате обработки диаграммы растяжения
рассчитывают параметры сопротивления пластическому растяжению: условный предел текучести Rp02 и предел прочности Rm, равномерное остаточное удлинение Ag :
Rp0.2 |
|
|
Fp0.2 |
|
|
|
|
|
|
; |
|
||
|
S0 |
(1.2) |
||||
|
|
|
|
|
||
|
|
Fm |
|
|
|
|
R |
. |
|
|
|||
|
|
|||||
m |
|
S0 |
|
|
||
|
|
|
|
7

A ln |
l0 l lg |
; |
(1.3) |
|
|||
g |
l0 |
|
|
|
|
|
Fp0.2 - усилие растяжения, соответствующее условному пределу текучести при остаточной деформации 0,2 % (рис.1.4). Для вычисления этой величины ординату соответствующей точки на кривой течения умножают на масштаб по усилию:
|
|
F |
(1.4) |
|
F |
|
~m |
; |
|
|
|
Fm |
|
S0 - исходная площадь поперечного сечения образца до растяжения; l- масштаб диаграммы по удлинению:
l |
|
lu l0 |
; |
(1.5) |
|
||||
|
|
lr |
|
lu - длина рабочей части образца после разрушения. Расчету подлежат результаты испытаний только тех образцов, разрушение которых произошло в области, отстоящей не менее трети расчетной длины от ее границ.
Рекомендуется также определять относительное остаточное удлинение A на базовой длине 80 мм как стандартную характеристику, по которой дополнительно можно проверить качество проведенного эксперимента.
A |
lu l0 |
100 (%); |
(1.6) |
|
|||
|
l0 |
|
Диаграммы растяжения образцов, ориентированных в одном направлении, аппроксимируют уравнением Свифта (1.1). Аппроксимация производится методом наименьших квадратов с помощью вычислительной программы. Для подготовки входных данных с каждой кривой растяжения (рис.1.4) снимают координаты 1000-5000-ти точек через
8

равные интервалы по времени. Точка диаграммы, соответствующая пределу текучести, является первой в этом диапазоне, а пределу прочности - последней. Кроме того, для каждой кривой вводят: наибольшую нагрузку Fm в ньютонах, абсциссу остаточного удлинения lr, площадь поперечного сечения S0, расчетную длину образца после разрушения lu и абсциссу, соответствующую равномерному удлинению lg.
~
F (в масштабе F)
~
Fm
F~p0.2
|
|
С=0.002 lr(l0/(lu-l0)) |
||
C |
|
lg |
|
l (в масштабе l) |
|
|
|||
|
|
|
|
|
|
|
|
|
|
lr
Рис. 1.4
На выходе программы получают все перечисленные характеристики материала (1.2) - (1.5) и параметры уравнения (1.1), рассчитанные по методу наименьших квадратов. Результаты выдаются в виде средних арифметических характеристик и их среднеквадратических отклонений.
Ниже приводится протокол испытания (табл. 1.1), который заполняется как на стадии измерения исходных размеров образца, так и после записи диаграммы растяжения и измерения образца после разрушения.
9