
Методическое пособие 693
.pdf
Для подшипников с короткими цилиндрическими роликами приведенная нагрузка равна:
Q = Fr·Kб·КТ·Кк.
Приведенная осевая нагрузка для упорно-радиальных шарико- и роликоподшипников:
Q = (X· Fr + Y·Fa)Kб·КТ.
При расчете радиально-упорных шарико- и роликоподшипников необходимо читывать, что в них радиальном нагружении и отсутствии осевого зазора и натяга возникает дополнительная осевая сила. Тогда, осевая нагрузка Fa действующая на радиально-упорный подшипник определяется с учетом осевой составляющей S радиальной нагрузки Fr, действующей на опоры.
Рис. 27.2. Схема нагружения радиально-упорного подшипника
Для радиальных и радиально-упорных шарикоподшипников
S= е Fr.
Для конических роликоподшипников
S= 0,83 е Fr.
где е – вспомогательный коэффициент.
Величина коэффициента е выбирается по таблицам ка-
талога подшипников в зависимости от соотношения A ,
C0
99

где А – осевая нагрузка (А = Fa);
С0 – статическая грузоподъемность подшипника
Отношение |
A |
выбирается согласно типу предвари- |
|
|
|||
C0 |
|||
|
|
тельно принятого подшипника по таблице каталога подшипников.
Зная S1 = е Fr1 |
и S2 = е Fr2, можно определить расчетные |
|||
осевые нагрузки Fa1 |
и Fa2 |
с учетом значений S1 |
и S2. |
|
Величины Fa1 |
и Fa2 |
определяют по формулам в зависи- |
||
мости от схемы нагружения принятых подшипников. |
||||
Например, для радиально-упорных подшипников. |
||||
|
|
|
|
Таблица 27.1 |
Условия нагружения |
|
Осевые нагрузки |
||
1. S1 > S2; Fa > 0 |
|
|
Fa1 = S1; |
|
2. S1 < S2; Fa ≥ S1 – S2 |
|
Fa2 = S1+ Fa |
(Fa = А) |
|
3. S1 < S2; Fa ≤ S1 – S2 |
|
Fa1 = S2 – Fa |
|
|
|
|
|
Fa2 = S2 |
|
27.9. Подбор подшипников качения
По вычисленной приведенной нагрузке (Q) и расчетному
ресурсу L |
60n |
L |
миллионов оборотов на основе исходной |
||
|
|
||||
|
106 |
|
h |
|
|
|
|
|
|
||
зависимости |
|
C |
|
L определяемую требуемую динамиче- |
|
|
|
|
|
||
|
|
|
|
Q
скую грузоподъемность:
C QL1 / ,
Lh – ресурс подшипника, в час.
Зная «С» по каталогу выбирают подшипник.
Часто подшипники подбирают по конструктивным соображениям, тогда расчетом проверяют их ресурс
100

106 C
Lh 60n Q ,
где Lh – ресурс подшипника в часах n – частота вращения, об/мин.
В общем машиностроении ресурс подшипника принима-
ют Lh = 2500…10000 час.
Подшипники, работающие при переменных режимах подбирают по эквивалентной нагрузке. Под эквивалентной нагрузкой понимают нагрузку, которая вызывает такой же эффект усталости, что и весь комплекс действительных нагрузок.
|
Q3L |
Q3L |
... Q3L |
|
Qэкв |
1 1 |
2 2 |
n n |
, |
3 |
|
|
|
|
|
|
L |
|
|
где Q1 – постоянная нагрузка, действующая в течение L1 миллионов оборотов;
Q2 – постоянная нагрузка, действующая в течение L2 миллионов оборотов;
L – общее число миллионов оборотов, в течение которого действуют нагрузки Q1, Q2, …, Qn.
Суммирование производят по числу режимов работы. Если нагрузка на подшипник изменяется по линейному
закону от Qmin до Qmax , то
Qэкв Qmin 32Qmax .
27.10. Статическая грузоподъемность подшипников
Подшипники качения грузоподъемных транспортных и других машин периодически подвержены нагрузкам без вращения. В этом случае основной характеристикой подшипника является его статическая грузоподъемность, т.е. нагрузка на невращающийся подшипник. Статическая грузоподъемность выбирается из условия, при котором общая остаточная дефор-
101
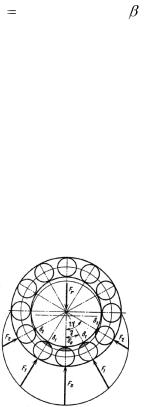
мация тела качения и кольца не должна превышать величину, заметно влияющую на работу подшипника.
Например, статическая грузоподъемность радиальных и радиально-упорных подшипников равна:
C0 K0 i
Z
dm2
Cos ,
где К0 – коэффициент, равный для радиальных и радиальноупорных подшипников К0 = 1,25;
i, Z – число рядов и число тел качения в ряду; dm – диаметр шарика, мм;
β – номинальный угол контакта.
27.11. Распределение нагрузки между телами качения
Если рассматривать распределение нагрузки R, действующей на радиальный шарикоподшипник, то окажется, что эта нагрузка распределяется между телами качения неравномерно. Нагруженная зона составляет не более 180º.
Рис. 27.3. Распределение нагрузки между телами качения
Для упрощения предположим, что тела качения занимают симметричное положение относительно нагрузки, тогда
R = P0 + 2P1Cosγ + 2P2Cos2γ,
где γ , 2γ, …nγ – углы между направлением силы R и радиальной плоскостью соответствующего шарика.
102
Осевая сила при точном изготовлении и отсутствии взаимного перекоса колец распределяется между телами качения практически равномерно.
В шарикоподшипниках начальный контакт между шариком и кольцами происходит в точке. После приложения нагрузки зона контакта принимает эллиптическую форму. При этом необходимо, чтобы контактное напряжение в центре этой площадки не превышало допустимого значения (ζH max ≤ [ζ]H), [ζ]H = 5000 МПа.
27.12. Потери на трение складываются из следующих составляющих
а) трение между телами качения и кольцами Этот вид трения состоит из трения качения и дополни-
тельного трения скольжения. Качение в наиболее чистом виде характерно для цилиндрических роликоподшипников.
В этом случае все точки линии контакта по длине ролика имеют одинаковую окружную скорость. В шарикоподшипниках и сферических роликоподшипниках контактов в поперечном сечении происходит по дуге. Окружные скорости точек линии контакта различны, что приводит к проскальзыванию и потерям на трение скольжения.
б) трение скольжения тел качения (роликов) в конических роликоподшипниках. В этом случае трение скольжения имеет место между торцевой поверхностью ролика и буртом внутреннего кольца.
в) трение, связанное с погрешностями формы тел качения и колец, переносом роликов и т.д.
г) трение тел качения о сепаратор и сепаратора о кольца д) сопротивление масла е) трение в уплотнениях (встроенные уплотнения).
При малых нагрузках основное значение имеют сопротивления, связанные со смазкой и трением в сепараторе, а при более высоких – трение на площадке контакта между телами качения и кольцами.
103
Момент трения в подшипниках обычно представляется простейшими зависимостями.
M = 0,5·fR·R·d или M = 0,5·fA·A·d,
где R и A – радиальная и осевая нагрузки;
fR и fA – приведенные коэффициенты трения; d – диаметр вала.
Более точно момент трения в подшипнике определяется по формуле:
M = 0,5(T + f0R)d,
где T = cd – сила сопротивления, не зависящая от нагрузки. Значения коэффициентов fR , fA, f0, и с при окружных скоростях на шейке вала до 10 м/с и умеренной смазке находят из таблицы.
27.13. Смазка подшипников качения
Смазка подшипников необходима для уменьшения трения, для усиления теплоотвода, для предотвращения коррозии и уменьшении шума. В качестве смазки подшипников применяют пластичные смазки и минеральные масла.
Пластичные смазки целесообразно применять для подшипников, труднодоступных для повседневного обслуживания, работающих в загрязненной среде. Применение пластичных смазок целесообразно для подшипников, работающих с
окружной скоростью на валу V≤ 7 м/с при температуре tсро ≤
70…100 ºС. С этой целью широко применяют различные вазелины, солидолы и более тугоплавкие смазки. Эти смазки экономичны, способны длительное время (до года) работать без замены, лишь с периодическим (через 3 мес.) пополнением. В корпусе подшипника для пластичной смазки предусматривают некоторое свободное пространство (стенки крышек располагают не вплотную к подшипнику). Это пространство первоначально заполняют на 2/3 от свободного объема при n ≤ 1500
об/мин и на 1/3…1/2 при n > 1500 об/мин.
104
Однако сейчас все больше применение находят герметизированные подшипники с одноразовой смазкой. Пластичные смазки герметизируют уплотнения подшипников:
ЦИАТИМ-201 – до 90 ºС, Литол-24 – до 100 ºС, ЦИАТИМ-221 – до 150 ºС.
Жидкие смазки применяют, когда требуются минимальные потери на трение и при высоких температурах. В качестве жидкой смазки применяют минеральные масла.
К недостатками жидких смазок следует отнести их меньшую экономичность, больший расход и применение более сложных уплотнений. Вязкость жидкой смазки выбирают:
–тем выше, тем больше t° среды, для предупреждения ее чрезмерного разжижения;
–тем выше, чем больше нагрузки, т.к. прочность пленки расчет с увеличением вязкости;
–тем ниже, чем выше частота вращения (воизбежание повышения потерь на трение).
Индустриальные жидкие масла И-Л-А7 – маловязкие; И-Л-А27 – маловязкие; И-Г-А-32 – средневязкие.
Существуют следующие способы смазки жидкими маслами: а) смазка окунанием в масляную ванну – для подшипни-
ков горизонтальных валов при n ≤ 10000 об/мин.
Уровень масла не выше центра нижнего шарика, а при n > 3000 об/мин еще ниже.
б) смазка разбрызгиванием из общей масляной ванны – для подшипников горизонтальных валов редукторов, коробок передач. Масло захватывается и разбрызгивается одним из зубчатых колес, специальной шестерней или дисками. В корпусе создается туман. Ставят маслоотражательные кольца.
в) капельная смазка осуществляется индивидуальными дозирующими аппаратами с индивидуальной регулировкой расхода. Применяется для мелких подшипников, быстроходных валов (n > 10000 об/мин);
105
г) смазка масляным туманом рекомендуется при n > 45000 об/мин. Она обеспечивает хорошее охлаждение и защиту подшипника. Недостаток – загрязнение воздуха парами масла. Для смазки нужен сжатый воздух фильт-осушитель воздуха, регулятор давления и распылитель масла.
27.14.Посадки подшипников
Всистеме соединения колец подшипников с валом и корпусом кольца принимают за основные детали, предельные отклонения которых назначаются независимо от потребного характера посадок. Различные посадки обеспечивают соответствующих отклонений валов и отверстий корпусов. Посадку внутренних колец подшипников осуществляют по системе отверстия, а наружных – по системе вала. При этом следует иметь в виду, что поле допуска внутреннего кольца подшипника располагается не в тело, а из него, поэтому соединение вал
–внутреннее кольцо получается более плотным, чем в обычном соединении.
27.15.Зазоры в подшипниках
Одним из важных условий нормальной работы подшипников является выдерживание в них оптимальных зазоров.
Увеличенные против оптимальных зазоры понижают точность вращения, увеличивают неравномерность распределения сил между телами качения, усиливают вибрации. Уменьшение зазоров ухудшает способность воспринимать осевую нагрузку, приводит к повышению температуры. В общем случае величина оптимального зазора зависит от условий работы подшипников.
Различают начальный геометрический зазор в подшипнике, обеспечиваемый заводом-изготовителем. Посадочный зазор в подшипнике смонтированном в узле машины. Этот зазор меньше начального на величину
(0,55…0,75)δВ + (0,5…0,6)δК,
106
где δВ и δК – натяги посадки подшипника на вал и в корпус. Уменьшение при этом геометрического зазора связано с
контактными деформациями в местах посадки, с радиальными деформациями колец, вала и корпуса.
Рабочий зазор (зазор в подшипнике, работающем под нагрузкой) равняется посадочному зазору минус температурное изменение зазора плюс контактные деформации тел качения и колец от радиальной нагрузки. Температурные изменения зазора связаны еще и тем, что внутреннее кольцо нагревается на 5…10 ºС больше наружного из-за худших условий теплоотдачи.
28. ПОДШИПНИКИ СКОЛЬЖЕНИЯ
Учебные вопросы
1.Общие сведения
2.Классификация
3.Конструкции подшипников скольжения
4.Подшипниковые материалы
5.Критерии работоспособности и расчета подшипников скольжения
6.Условные расчеты подшипников
7.Тепловой расчет подшипников
8.Проектировочный расчет подшипников жидкостной смазки
28.1. Общие сведения
Подшипники скольжения применяются ограниченно и лишь в тех областях, где они сохранили свои преимущества, а именно: для весьма быстроходных валов, в режиме работы которых долговечность подшипников качения очень мала; для осей и валов, требующих весьма точной установки; для валов очень большого диаметра (при отсутствии стандартных подшипников качения); когда по условиям сборки подшипник должен быть разъемным; при работе подшипника в воде, агрессивной среде для тихоходных валов неответственных механизмов и в особых условиях.
107

Подшипник скольжения должны удовлетворять следующим основным требованиям:
а) конструкции и материалы должны быть такими, чтобы потери на трение и износ их и вала были минимальными;
б) должны быть достаточно жесткими и прочными; в) размеры их трущихся поверхностей должны быть дос-
таточными для восприятия действующего на них давления; г) сборка, установка и обслуживание должны быть про-
стыми.
Для уменьшения трения и нагрева, повышения КПД подшипники смазывают.
В зависимости от толщины масляного слоя в подшипнике, он работает в режиме жидкостного, полужидкостного или полусухого трения.
Рис. 28.1 Изменение коэффициента трения в подшипнике скольжения
При жидкостном трении рабочие поверхности вала и подшипника полностью разделены слоем смазки, толщина которого должна быть больше суммы неровностей обработки поверхностей вала и подшипника.
При полусухом трении между валом и подшипником преобладает сухое трение, а при полужидкостном – преобладает жидкостное.
Наиболее благоприятным режимом является работа подшипника в условиях жидкостного трения. В этом случае обес-
108