
Методическое пособие 679
.pdf3. РЕЗУЛЬТАТЫ ИССЛЕДОВАНИЙ СВОЙСТВ БЕТОНА ПОВЫШЕННОЙ ТЕРМОСТОЙКОСТИ ДЛЯ ОГНЕСТОЙКИХ ЖЕЛЕЗОБЕТОННЫХ ИЗДЕЛИЙ
3.1.Определение рационального состава бетона
3.1.1.Оценка свойств компонентов бетона с термодинамических позиций
Получение бетона повышенной термостойкости, снижающего теплопроводность в процессе огневого воздействия, с необходимыми показателями свойств: требуемой усадкой как при твердении, так и при огневом воздействии; высокой адгезией к несущему конструкционному слою; высокой стойкостью к огневому воздействию, потребовало целенаправленного выбора сырьевых материалов, методика которого представлена в главе 2.
Методической основой исследований являлся метод Ван-Осс-Гуда (VOG) – метод тестовых жидкостей [101, 102]. Были использованы тестовые жидкости: неполярная – дийодметан - и две полярные – вода и формамид - с известными величинами свободной поверхностной энергии.
Использовались следующие компоненты бетона: шунгит, цемент, граншлак, асбест. Свойства исходных компонентов представлены в табл. 3.1.
|
|
|
|
|
Таблица 3.1 |
Характеристики исходных компонентов бетона |
|
||||
|
|
|
|
|
|
|
Дисперсность |
Плотность, кг/м3 |
|||
Вид и характеристика |
|
|
|
|
|
удельная площадь |
|
модуль |
|
|
|
компонента бетона |
|
|
|
||
поверхности |
|
крупности |
истинная |
насыпная |
|
|
|
||||
|
Sуд, м2/кг |
|
Мкр |
|
|
Цемент ПЦ 500 Д0, |
280 |
|
- |
3100 |
1100 |
ОАО «Осколцемент» |
|
||||
|
|
|
|
|
|
|
|
|
|
|
|
Граншлак |
|
|
|
|
|
Липецкого |
- |
|
2,98 |
2300 |
500 |
металлургического |
|
|
|
|
|
комбината |
|
|
|
|
|
Шунгит |
|
|
|
|
|
Зажогинского |
- |
|
1,43 |
2200 |
400 |
месторождения (п. Толвуя, |
|
|
|
|
|
республика Карелия) |
|
|
|
|
|
Асбест хризотиловый |
|
|
|
|
|
А-6К-30 |
20000 |
|
- |
2500 |
200 |
(г. Асбест, |
|
|
|
|
|
Екатеринбург.обл.). |
|
|
|
|
|
|
|
51 |
|
|
Результаты экспериментальных исследований методом тестовых жидкостей выбранных компонентов бетона повышенной термостойкости показали следующее.
Шунгит: все тестовые жидкости как гидрофильные (вода и формамид), так и гидрофобная (дийодметан) впитываются мгновенно, вероятно, в силу большого капиллярного эффекта и высокой адсорбционной способности шунгита. Однако, визуальные наблюдения за характером взаимодействия - время впитывания и высыхания контактной поверхности тестовых жидкостей с поверхностью образца из шунгита - позволяют их распределить в соответствии с отмеченными характеристиками в следующий ряд (по увеличению времени): вода, формамид, дийодметан.
I «Цемент +дийодметан» образует каплю, которая быстро расплывается, но на поверхности остается зеркало жидкости. Капля воды в некоторых случаях сохраняет шарообразную форму при большей площади контакта, чем во втором образце, содержащем цемент и граншлак. То есть, можно предполагать, что образец из цемента без шлака более гидрофилен.
II «Цемент + шунгит + дийодметан» впитывается при быстром растекании капли. Вода образует каплю с θ > 900, то есть с малой площадью контакта сцепления. Капля не растекается и крепко держится на поверхности, не отрываясь от образца при его вращении на 1800. Можно предположить, что поверхность преимущественно имеет гидрофобный характер, а высокое сцепление с гидрофильной водой обусловлено в основном Ван-дер-Вальсовыми силами при достаточно развитой поверхности образца.
III «Шлак» - закономерности аналогичны шунгиту.
IV «Асбест» - наблюдается характер взаимодействия с тестовыми жидкостями аналогичный или очень схожий с тем, что отмечен у шунгита и шлака. То есть, по интенсивности взаимодействия тестовые жидкости можно расположить в следующий ряд:
Вода > Формамид > Дийодметан Таким образом, поверхность асбеста носит ярко выраженный гидро-
фильный характер без особых преимуществ для кислотной или основной составляющей полярной компоненты со свободной поверхностной энергией.
Результаты исследований, проведенные методом тестовых жидкостей выбранных компонентов бетона повышенной термостойкости, показали правомерность предположения об эффективном совмещении материалов – шунгита, цемента, граншлака, асбеста, что обеспечивает стабильность бетона и его требуемые свойства для огнестойких железобетонных изделий.
Выполненные исследования показали совместимость выбранных компонентов бетона, предназначенного для создания огнестойких конструкций на основе вариатропных изделий. Выбранные компоненты обеспечат такому бетону низкий показатель усадочности, высокую стойкость к огневому воздействию, высокую адгезию к несущему слою конструкции, возможность изменять теплотехнические показатели в зависимости от температуры огневого воздействия, обладая при этом стойкостью к растрескиванию и отслоению.
52

3.1.2. Влияние дисперсности шунгита на физико-механические характеристики и термостойкость бетона
При введении шунгита в бетон необходимо снизить напряжение, возникающее в бетоне повышенной термостойкости при огневом воздействии за счет вспучивания шунгита. Эта задача может быть решена путем оптимизации размера зерен шунгита.
Механизм вспучивания шунгита можно условно разделить на две ступени [124]. На первой ступени при нагреве частиц шунгита до 400 – 500 0С происходит выделение газопаровых систем в результате окислительно-восстановитель- ных реакций. Интенсивное вспучивание шунгитовых частиц, наблюдаемое на второй ступени в диапазоне температур от 500 0С до 1200 0С, обусловлено протеканием химических реакций. Это предположение подтверждается результатами многочисленных исследований [94, 96 – 98, 124], которые показывают, что при высокотемпературных воздействиях многокомпонентная система шунгита претерпевает существенные изменения, связанные с преобразованием его структуры.
На рис. 3.1 приведена зависимость насыпной плотности шунгита от размера его частиц при температуре обжига 1200 0С.
5-10 |
10-20 |
20-40 |
|
|
|
Рис. 3.1. Зависимость насыпной плотности шунгита от размера его фракции после обжига при температуре 1200 0С [124]
Показано, что с уменьшением размера частиц шунгита после обжига понижается коэффициент вспучивания материала и, следовательно, повышается его насыпная плотность.
Приведенные данные дали основание предположить целесообразность применения частиц шунгита мелких фракций в проектируемых бетонах повышенной термостойкости.
Наши исследования показали, что для повышения термостойкости бетона размер частиц шунгита не должен превышать 5 мм. Так как использование крупных частиц шунгита размером более 5 мм при их вспучивании вызы-
53

вает появление значительных напряжений и, соответственно, микротрещин в бетоне, что нашло подтверждение в результатах наших испытаний, приведенных на рис. 3.2 (для бетона, состав которого приведен в табл. 3.2).
Установлено, что при использовании в составе бетона частиц шунгита с размером 5 мм и более при температурных воздействиях наблюдается снижение прочности бетона. При использовании частиц шунгита с размером от 5 мм до 0,63 мм наблюдается рост прочности бетона по сравнению с бетоном, содержащим более крупные его фракции.
0,315-0,63 0,63- 1,25 1,25-2,5 2,5-5,0 5,0-10,0 10,0-20,0
Рис. 3.2. Прочность бетона с добавкой шунгита разной дисперсности после одного цикла испытания на термостойкость при температуре 1000 0С
Выявленные свойства шунгита и, соответственно, шунгизитобетона были отмечены и в других работах [94, 96 – 98, 124].
3.1.3. Обоснование рационального состава бетона повышенной термостойкости с позиций теории протекания
Учитывая особенности, связанные с увеличением объема частиц шунгита при высокотемпературном нагреве, необходимо рассмотреть требуемую их рациональную концентрацию в цементном камне.
С одной стороны повышение содержания шунгита безусловно приводит к снижению прочностных характеристик цементного камня, а с другой стороны, их наличие предопределяет повышение термостойкости бетона. Присутствие частиц шунгита в недостаточном количестве приводит либо к образованию невзаимосвязанных «кластеров», способствующих получению неоднородной структуры бетона в целом, либо к образованию единого непрерывного «кластера», т.е. взаимно контактирующих в объеме частиц шунгита в цементном камне. Необходимо, чтобы из шунгитовых частиц в цементном камне формировалась непрерывная структура без разрывов, что приводило бы к однородности структуры бетона в целом [125, 126].
54

Для решения этой задачи в нашей работе привлекались фундаментальные положения теории протекания [125, 127]. Важным моментом является оптимизация составляющих в бетоне, а именно в цементном камне связующих материалов цемента и шунгита.
Существует две задачи протекания: по касающимся и по перекрывающимся сферам [128, 129]. Наиболее предпочтительным с точки зрения эффективности как технологической, так и экономической, является создание систем, в которых реализуется модель протекания по касающимся сферам. Безусловно, эта модель имеет вероятностно-детерминированный характер, что подтверждается многочисленными исследованиями, в том числе с использованием ЭВМ
[125].
Вместе с тем возможно с достаточно высокой вероятностью определить необходимое содержание частиц (сфер) шунгита для создания в композите бесконечного «кластера» из касающихся сфер. Модель протекания по касающимся сферам представлена на рис. 3.3.
Рис. 3.3. Плоская решетчатая модель протекания по касающимся сферам [125]: а – бесконечный кластер; б – изолированный кластер; d – диаметр сферы (стрелкой указан «путь» протекания)
Опираясь на представления теории протекания [127], описывающей возникновение бесконечных связных структур «кластеров», состоящих из отдельных элементов, представленная модель на рис. 3.3 тесно связана с проблемой формирования структуры композитов с дисперсными наполнителями.
Условие протекания по касающимся сферам формулируется в следующем виде [125]
vcl= Nc1 πd3/6 = 0,16 + 0,01, |
(3.1) |
где d – диаметр сферы; Nc1 – критическое число сфер в единице объема. Очевидно, что появление пути протекания обусловлено возникновением
бесконечного кластера (рис. 3.3, а), образующегося из касающихся сфер самопроизвольно возникающей совокупности большого числа связанных между со-
55

бой частиц, когда силы взаимодействия между частицами являются преобладающими.
Исходя из представленного условия, что частицы наполнителя (шунгита) вступают в прямой контакт между собой при объемной его доле, равной vс1=0,16, в композите возникает бесконечный кластер из контактирующих частиц [125].
Таким образом, решение задачи на протекание по касающимся сферам сводится к определению величины концентрации шунгита vс1 согласно зависимости (3.1). С учетом плотности зерен шунгита нами в данных исследованиях общая масса шунгита в составе цементного камня составляет примерно 16 % от объема вяжущего [125]. Заниженная концентрация содержания шунгита связана с особенностями его вспучивания и изменением элементного состава при температурных воздействиях в силу его взаимодействия с составляющими цементного камня.
Следует отметить, что достигнутые результаты испытаний свойств бетона повышенной термостойкости подтвердили правильность наших предположений о выборе состава бетона. Оптимизация состава бетона повышенной термостойкости для вариатропных огнестойких железобетонных конструкций проводилась последовательно по показателям средней плотности бетона и прочности при поддержании постоянной величины подвижности бетонной смеси от 8 до 10 см. Содержание компонентов бетона на 1 м3 варьировалось в следующих диапазонах: цемент от 590 до 248 кг; шунгит от 36 до 177 кг; асбест от 10 до 40 кг; гранулированный шлак от 800 до 1420 кг; вода затворения подбиралась в количестве, необходимом для обеспечения заданной подвижности бетонной смеси.
Согласно методике подбора рационального состава композиционного бетона повышенной термостойкости, описанной в главе 2, полученные данные по критерию Стьюдента являлись достоверными, а по критерию Фишера – значимыми. Результаты оптимизации состава бетона повышенной термостойкости по плотности и прочности показали, что достижение бетоном плотности, лежащей в диапазоне 1480 кг/м3 (твердение образцов протекало при нормальных условиях: температуре ± 20 0С, влажности 100 % в течение 28 сут.), прочности при сжатии 12 МПа и прочности при изгибе 2,5 МПа обеспечивается путем применения рационального его состава, приведенного в табл. 3.2.
После проектирования состава бетона с учетом высказанных ранее предположений была выбрана дозировка шунгита в количестве 44 кг/м3.
Таблица 3.2
Состав бетона повышенной термостойкости
|
|
3 |
|
|
Средняя плотность |
|
Расход материалов, кг/м |
|
|
||
|
|
|
бетона в сухом |
||
|
|
|
|
|
|
цемент |
шунгит |
асбест |
|
граншлак |
состоянии, кг/м3 |
390 |
44 |
13 |
|
950 |
1447 |
|
|
|
56 |
|
|
В качестве сравнения в работе использовался эталонный состав бетона, широко применяемый для изготовления бетона повышенной термостойкости, но с отсутствием шунгита в своем составе.
3.2. Исследование изменений структуры бетона повышенной термостойкости после температурных воздействий
3.2.1. Влияние температурных воздействий на изменение элементного состава цементного камня в зоне контакта с зернами шунгита
Выполненные исследования элементного состава цементного камня бетона повышенной термостойкости в зоне контакта с зернами шунгита показали следующее. При повышении температуры от 900 0С до 1100 0С происходит изменение элементного состава цементного камня в зоне контакта с частицами шунгита (табл. 3.3).
Установлено, что при повышении температуры от 900 0С до 1100 0С увеличивается процент содержания углеродосодержащих соединений в контактной зоне более чем в 15 раз, содержание кислорода и оксидов алюминия меняется несущественно, но снижается в 2 раза содержание оксидов кремния, а оксидов кальция – в 3 раза. Это свидетельствует о проявлении активности шунгита с повышением температуры и об изменении не только элементного, но и, вероятно, фазового состава цементного камня в зоне контакта с зернами шунгита.
Таблица 3.3
Элементный состав цементного камня в зоне контакта с зернами шунгита после термических воздействий при температуре 900 ° С и 1100 ° С
|
Содержание, масс. % |
|
||
Химические элементы и оксиды |
|
|
|
|
после термических |
после термических |
|
||
|
|
|||
|
воздействий при 900 |
0С |
воздействий при 1100 |
0С |
С |
2,07 |
|
32,48 |
|
О2 |
47,64 |
|
45,14 |
|
Na2O |
- |
|
1,31 |
|
MgO |
3,92 |
|
1,84 |
|
Al2O3 |
2,09 |
|
1,39 |
|
SiO2 |
13,92 |
|
6,72 |
|
S |
0,48 |
|
0,25 |
|
CI |
- |
|
0,78 |
|
CaO |
29,76 |
|
9,87 |
|
Fe2O3 |
0,11 |
|
0,23 |
|
Итого |
100 |
|
100 |
|
По результатам экспериментов логично сделать следующие предварительные обобщения. На фоне изменения элементного состава в контактной зоне
57

происходит также вспучивание частиц шунгита, которое может быть осуществлено только в случае изменения вязко-пластичных свойств шунгита. Как будет показано далее (см. п. 3.3.1) этот процесс нашел подтверждение в снижении плотности бетона после его термической обработки. Важным является и тот момент, что увеличение объема частиц шунгита происходит за счет их вспучивания. Возникновения значительных напряжений при вспучивании шунгита, которые могли бы способствовать появлению трещин в бетоне, не наблюдается. Одной из причин такого поведения исследуемого материала может быть изменение фазового состава вяжущего в контактной зоне, что еще раз косвенно находит подтверждение в изменении элементного состава цементного камня в зоне контакта с зернами шунгита. Отмеченное явление, вероятно, приводит к изменению свойств цементного камня и, в частности, к повышению его стойкости к трещинообразованию.
3.2.2. Изменение нано- и микроструктуры бетона после температурных воздействий
Осуществлялось изучение структуры бетона, подвергнутого однократному воздействию высоких температур. Результаты, полученные на «срезах бетонов» методом атомно-силовой микроскопии представлены на рис. 3.4.
а) после 700 0С |
б) после 900 0С |
в) после 1100 0С
Рис. 3.4. Наноструктура поверхности бетона повышенной термостойкости и ее изменение при температурных воздействиях
58
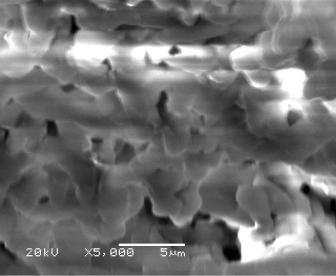
Сравнение результатов, позволило отметить следующее. Сформировавшаяся наноструктура поверхности цементного камня эталонных образцов бетона, подвергнутых однократному воздействию высоких температур равной 700 0С, характеризуется относительной их сглаженностью (рис. 3.4, а), что является причиной снижения сцепления между слоями бетона и, соответственно, приводит к уменьшению его прочности.
Наноструктура поверхности цементного камня в зоне его контакта с зернами шунгита в бетоне повышенной термостойкости отличается большей шероховатостью и, соответственно, более развитой удельной поверхностью (рис. 3.4, б), что, вероятно, и обеспечивает получение материала с более высокими показателями термостойкости. При температурных воздействиях от 900 0С до 1100 0С в бетоне повышенной термостойкости наблюдаются незначительные изменения структуры (рис. 3.4, в), что косвенно подтверждается результатами механических испытаний прочностных показателей бетона.
Исследования микроструктуры показали, что при температуре 700 0С в бетоне эталонного состава наблюдается формирование агрегированной структуры с частичным трещинообразованием (рис. 3.5).
Рис. 3.5. Электронно-микроскопические снимки поверхности бетона после температурного воздействия 700 0С (× 5000 раз)
Агрегация структуры при температурном воздействии 700 0С присутствует и в бетоне повышенной термостойкости. Наличие трещин не наблюдается. С увеличением температуры до 900 0С (рис. 3.6, а) в бетоне повышенной термостойкости степень агрегирования возрастает, что, вероятно, связано с началом вспучивания шунгита.
Визуально микротрещины не наблюдаются. Однако, снижение прочности бетона (см. п. 3.3.1) дает основание предполагать о накоплении дефектов в структуре. При температурах выше 1100 0С происходит интенсивное вспучивание шунгита, структура цементного камня (рис. 3.6, б) из гранулированной пе-
59

реходит в частично оплавленную с четко выраженными локальными плотными зонами. Формирование неоднородной структуры приводит к снижению прочности бетона (см. п.3.3.1).
а) структура бетона после 900 0С |
б) структура бетона после 1100 0С |
Рис. 3.6. Электронно-микроскопические снимки поверхности бетона повышенной термостойкости после температурного воздействия от 900 0С до 1100 0С (× 5000 раз)
3.2.3. Изменение макроструктуры бетона после температурных воздействий
Нано- и микроскопические исследования согласуются с оптическими исследованиями макроструктуры (рис. 3.7). Установлено, что существенные изменения в структуре бетона происходят при температуре более 900 0С. Эти изменения связаны с появлением образований в виде агрегатов в структуре бетона (рис. 3.7, г). На образцах отсутствуют микроповреждения в виде трещин и каверн. При температурном воздействии 1100 0С на поверхности цементного камня четко просматриваются зерна вспученного шунгита (рис. 3.7,е). В то же время наличия трещин и локальных разрушений не наблюдается (рис. 3.7,д).
Таким образом, исследования структуры бетона повышенной термостойкости на различных масштабных уровнях позволили сделать следующее обобщение. При температурных воздействиях до 900 ºC существенных различий между структурой бетона эталонного состава и предлагаемого бетона повышенной термостойкости нет. При воздействии более высоких температур (вплоть до 1100 ºC) наблюдаются значительные различия в структурах этих бетонов. На наноуровне структура цементного камня бетона повышенной термостойкости уже при температурном воздействии 700 ºC по сравнению со структурой бетона эталонного состава имеет значительные различия, которые только усиливаются при температурном воздействии 900 ºC и 1100 ºC.
60