
Методическое пособие 511
.pdfПонятие «автоматизированный», в отличие от понятия «автоматический», подчёркивает необходимость участия человека в отдельных операциях, как в целях сохранения контроля над процессом, так и в связи со сложностью или нецелесообразностью автоматизации отдельных операций.
Составными частями АСУ ТП могут быть отдельные системы автоматического управления (САУ) и автоматизированные устройства, связанные в единый комплекс. Такие как системы диспетчерского управления и сбора данных (SCADA), распределенные системы управления (DCS), и другие более мелкие системы управления (например, системы на программируемых логических контроллерах (PLC)). Как правило, АСУ ТП имеет единую систему операторского управления технологическим процессом в виде одного или нескольких пультов управления, средства обработки и архивирования информации о ходе процесса, типовые элементы автоматики: датчики, устройства управления, исполнительные устройства. Для информационной связи всех подсистем используются промышленные сети.
Основа автоматизации технологических процессов
— это перераспределение материальных, энергетических и информационных потоков в соответствии с принятым критерием управления (оптимальности).
1.Частичная автоматизация — автоматизация от-
дельных аппаратов, машин, технологических операций. Производится когда управление процессами вследствие их сложности или скоротечности практически недоступно человеку. Частично автоматизируется как правило действующие оборудование. Локальная автоматизация широко применяется на предприятиях пищевой промышленности.
2.Комплексная автоматизация — предусматривает автоматизацию технологического участка, цеха или предприятия функционирующих как единый, автоматизированный комплекс. Например, электростанции.
40
3. Полная автоматизация — высшая ступень автома-
тизации, при которой все функции контроля и управления производством (на уровне предприятия) передаются техническим средствам. На современном уровне развития полная автоматизация практически не применяется, так как функции контроля остаются за человеком. Близкими к полной автоматизации можно назвать предприятия атомной энергетики.
4.2. Инструментальное обеспечение автоматизированного производства
Производительность автоматической линии или автоматического станка зависит от применяемого режущего инструмента.
Учитывая специфику работы в условиях автоматизированного производства и стремясь сократить потери времени, конструкторы разработали большое количество разнообразных конструкций, в которых нашли отражение следующие идеи:
а) применение взаимозаменяемого инструмента, настраиваемого на размер, что исключает потери времени на первоначальную наладку;
б) использование сил резания для частичного или полного крепления инструмента, что. упрощает конструкции механизма крепления инструмента, обеспечивая более высокую точность установки и, главное, сокращение времени на установку, закрепление, открепление и снятие режущей части или самого инструмента;
в) встройка узлов автоматической подналадки и регулирования инструмента для компенсации систематических погрешностей размеров заготовки, что обеспечивает повышение размерной стойкости инструмента и сокращает указанные выше потери времени;
41

г) использование принципа обновления режущих участков одной и той же кромки (прерывное или непрерывное), обновления резцов (зубьев) самих режущих инструментов.
Наряду с указанными проблемами большое значение имеет формирование и отвод стружки в условиях работы автоматического станка. В этом направлении также найдены решения, обеспечивающие нормальный стружкоотвод. Ниже приводится описание отдельных конструкций инструментов для автоматизированных производств с указанием их особенностей.
Рис. 13. Схемы быстросменных крепления а) быстросменных пластинок; б) резцовой вставки;
в, г) – осевого режущего инструмента В автоматизированном производстве используется
обычный стандартный инструмент (резцы, сверла, зенкеры,
развертки, цековки, фрезы, метчики и др.). Однако техни-
42
ческие требования к инструментальным материалам и к точности изготовления — повышенные.
Чтобы простои оборудования автоматических линий, связанные с заточкой затупившегося режущего инструмента, были минимальными, линии должны быть оснащены быстросменной инструментальной оснасткой, оснащенных хвостовиками различной формы.
Часто при обработке корпусных деталей в линии требуется совместить в одну операцию сверление отверстия и снятие фаски или сверление ступенчатых отверстий под го-
ловку болта. Для этой цели применяют ступенчатые сверла двух видов: переточенные из стандартных и специальные четырехленточные. Глубокие отверстия сверлят ружейными сверлами. Для обработки ступенчатых отверстий и канавок на торцовых поверхностях используют комбинированные инструменты.
Для нарезания резьбы на автоматических линиях, применяют метчики, резьбонарезные и резьбонакатные головки; для фрезерных операций— различные фрезы (торцовые, цилиндрические, концевые, дисковые и т. д.). Наибольшее применение на автоматических линиях обработки корпусных деталей получили торцовые фрезы сборных конструкций с ножами, оснащенными твердым сплавом.
4.3. Станочное оборудование автоматизированных производств
Промышленная техника, используемая в различных отраслях производства, постоянно развивается. Станочное оборудование становится более совершенным. Современные машины автоматизированного производства имеют сложное устройство, обладают высокой точностью при выполнении операций, имеют высокий уровень производительности.
43
Они позволяют заменить ручной труд (один станочник может контролировать работу нескольких станков одновременно). Повышение степени автоматизации оборудования требуется для обеспечения надежности его эксплуатации. Оно имеет более высокую стоимость, но может быстро окупиться (при условии работы в две или три смены).
Длительная эксплуатация оборудования без своевременного и правильного технического обслуживания может привести к поломке станка или возникновению различных неполадок. При интенсивном использовании машин (в несколько смен) необходимо обслуживать автоматизированное производство не менее чем один раз в три смены. Например, наладка, настройка и подготовка к работе осуществляются рабочими, эксплуатирующими станок в первую смену. Машинисты выполняют следующие процедуры:
1.комплектуют и осуществляют первоначальный контроль обрабатываемых деталей;
2.налаживают, проверяют состояние и комплектование режущих инструментов и крепежной оснастки;
3.проверяют и вносят изменения в управляющие про-
граммы;
4.контролируют общее состояние станка. Машинистами (дежурными рабочими) второй и третьей
смены осуществляются наблюдение за работой оборудования в автоматическом режиме, контроль качества обработанных заготовок, устранение мелких неисправностей.
Станочная система – это совокупность станков и вспомогательного оборудования, используемая для обработки заготовок широкой номенклатуры на основе одного или нескольких технологических процессов.
Автоматическая станочная система – это совокуп-
ность станков и вспомогательного оборудования, взаимодействующих между собой, которые объединены автоматическими подсистемами (транспортно-накопительной и системой
44
управления). Особенность автоматических станочных систем заключается в минимальном участии человека. Оно ограничивается наблюдением, иногда выполнением некоторых технологических операций.
Станочные системы подразделяются на несколько видов в зависимости от типа производства:
1.специальные (или непереналаживаемые);
2.специализированные (или переналаживаемые);
3.универсальные (или гибкие).
К первой группе относятся непереналаживаемые автоматические линии, которые позволяют подвергать обработке одновременно две заготовки. Универсальная группа включает гибкие автоматизированные линии, используемые для обработки заготовок широкой номенклатуры с различными технологическими маршрутами. К специализированным линиям относят универсальные станки, обрабатывающие до 15 деталей одновременно. Среди них выделяют:
1.автоматический станочный модуль (рис. 14) – ме-
таллорежущие оборудование, снабженное устройством управления и системой автоматической смены обрабатываемых заготовок и выполняющее множество автоматических циклов;
2.адаптивный станочный модуль – станок, осущест-
вляющий контроль и наладку процесса обработки, коррекцию качества обработанных деталей;
3.гибкий производственный модуль имеет свойства первых двух модулей, дополнительно оснащен механизмами смены инструмента, деталей, устройствами удаления отходов;
45
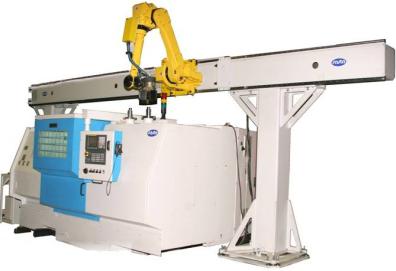
Рис. 14. Автоматический станочный модуль
4. гибкую автоматизированную линию и гибкий автоматизированный участок – единицы оборудования, объе-
диненные автоматизированными системами управления и транспортно-накопительными системами для обрабатываемых деталей.
Вопросы для самоподготовки
1.Чем характеризуется автоматизация технологического процесса?
2.Чем определяется производительность автоматической линии?
3.Что такое станочная система?
4.Что представляет собой автоматическая станочная
система?
5.Какие виды станочных систем существуют?
46
Раздел 2. СРЕДСТВА АВТОМАТИЗАЦИИ ПРОИЗВОДСТВЕННЫХ ПРОЦЕССОВ
Лекция № 5 ОСНОВЫ АВТОМАТИЗАЦИИ ТЕХНОЛОГИЧЕСКИХ
ПРОЦЕССОВ
Теоретические вопросы:
5.1.Требования к металлорежущему оборудованию и производственным процессам, подлежащим автоматизации
5.2.Типовые и групповые технологические процессы
5.3.Промышленные роботы
5.1.Требования к металлорежущему оборудованию и производственным процессам, подлежащим автоматизации
Одной из особенностей современного машиностроительного производства является постоянный рост объёмов и сложности проектных работ в сфере технологической подготовки производства, что обусловлено следующими причинами:
—увеличивается номенклатура и сложность выпускаемых машин и приборов, которые характеризуются использованием новых конструкционных материалов, более высокими требованиями к качеству;
—повышаются требования к качеству технологических решений, обеспечивающих конкурентоспособность изделий за счет снижения себестоимости продукции и повышения ее качества;
—расширяются возможности оборудования с ЧПУ, требующего дополнительной разработки управляющих про-
47
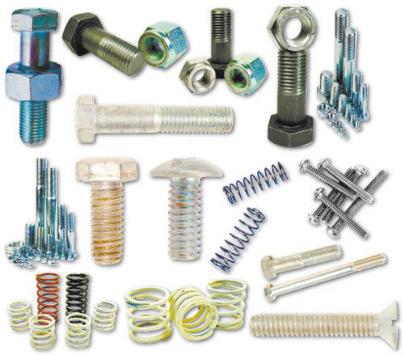
грамм и детального проектирования операционной технологии;
— значительно сокращаются сроки подготовки производства для выпуска новых изделий.
Рис. 15. Крепежные и подвижные элементы деталей машин и механизмов
В этих условиях наиболее важным направлением совершенствования технологической подготовки производства (далее ТПП) является ее автоматизация на базе использования ЭВМ.
Применение ЭВМ в технологическом проектировании накладывает свой отпечаток на постановку технологических задач, а также требует решения ряда дополнительных задач.
48
Тип производства предъявляет основные требования к ТПП и технологическому оборудованию. В массовом производстве главное требование к оборудованию — высокая производительность, а в серийном и единичном — гибкость (универсальность и мобильность), вызванная необходимостью частой сменяемости выпускаемых изделий.
До недавнего времени понятия автоматизации и гибкости считались альтернативными. Однако в последние годы граница между указанными требованиями к технологическому оборудованию в массовом и серийном производствах заметно «размывается».
Это обусловлено, с одной стороны, спросом рынка, требующего частой сменяемости объекта производства, с другой стороны, развитием средств управления технологическим оборудованием на базе использования достижений микроэлектроники и средств числового программного управления.
Поэтому в настоящее время независимо от типа производства (массовое, серийное, единичное) к технологическому оборудованию в качестве главных предъявляются требования высокой производительности и гибкости.
Таким образом, главная задача автоматизации —
производительность и гибкость.
Обязательным и первостепенным условием выполнения указанных требований является автоматизация рабочего цикла оборудования, т.е. автоматизация задания и выполнения управляющей программы каждой единицей технологического оборудования.
Под управляющей программой металлорежущим станком понимается последовательность команд, обеспечивающих функционирование рабочих органов станка по выполнению операции обработки заготовки детали. УП содержит технологическую и геометрическую информацию.
Технологическая информация — это данные о техно-
логии обработки, содержащие сведения о смене заготовок и
49