
Методическое пособие 365
.pdf
эллипса, а затем корректируют эти измерения с учетом сферической внешней поверхности образца с радиусом R = 37.5+h, где h – толщина испытуемого образца. Расчет выполняют по формулам
|
|
2 R arcsin |
|
l1 |
|
|
|
|
e |
ln[ |
2 R |
]; |
|||||
|
|
|
|
|||||
1 |
|
|
l0 |
|
|
|
|
|
|
|
|
|
|
|
|
|
|
|
|
|
2 R arcsin |
|
l2 |
|
|
|
|
|
|
|
2 R |
(15) |
|||
|
|
|
|
|
||||
e |
ln[ |
|
|
|
|
]; |
||
|
|
|
|
|
||||
2 |
|
|
l0 |
|
|
|
|
|
|
|
|
|
|
|
|
|
e2 . e1
где l1, l2 – длины диагоналей выделенных ячеек разрушенного образца.
Затем выполняют аналогичные измерения 5-7 ячеек в перпендикулярном к трещине направлении, пересекающем центр выделенных ячеек с обеих сторон трещины, и вычисляют в них деформации. По результатам строят графики зависимости наибольшей деформации в ячейке от ее положения вдоль перпендикуляра к трещине (рис.18,а). Так же, как и в случае плоской деформации (рис.12), предельная
деформация устойчивости |
e* |
) |
определяется в ячейке, где |
|
1( |
|
стабилизируется падение деформации (см.рис.18,б).
31

|
Направление |
|
измерения |
Напрвление |
Рис.18,а |
измерения |
|
|
s |
e1
e1j Рис.18,б
Расчет предельной деформации устойчивости при двухосном растяжении e(*1) выполняют путем экстраполяции
32

правой |
ветви |
|
диаграммы предельных |
|
деформаций |
|||||||||
(рис.19) по результатам выполненных испытаний и |
||||||||||||||
наибольшей из двух определенных ранее предельных плоских |
||||||||||||||
деформаций устойчивости |
{e* |
|
,e* |
}max |
(см.рис.19) |
|
||||||||
|
|
|
|
|
|
|
(0)0 |
(0)90 |
|
|
|
|
|
|
|
|
|
|
|
|
|
|
|
|
Рис.19 |
|
|
||
|
|
|
|
e1 |
|
|
|
|
|
|
|
|
|
|
|
|
|
|
|
|
|
|
|
|
e* |
|
|
|
|
|
|
|
|
|
|
|
|
|
|
(1) |
|
|
|
|
|
e* |
|
e* |
|
|
|
|
|
|
|
|
|
||
|
|
(0)90 |
|
|
(0) |
|
|
|
|
|
|
|
|
|
|
|
|
|
0 |
|
|
|
|
|
1 |
|
|
|
|
На графике предельная деформация, соответствующая |
||||||||||||||
двухосному |
растяжению, |
|
определяется |
при |
=1. |
Расчет |
||||||||
деформации выполняется методом наименьших квадратов по |
||||||||||||||
формуле |
|
|
|
|
|
|
|
|
|
|
|
|
|
|
|
m |
|
|
|
|
m |
|
|
|
|
|
|
||
|
|
e j |
j |
e* |
|
( |
|
j |
( |
j |
)2 ) |
|
|
|
|
|
1 |
|
(0) max |
|
|
|
|
|
|
||||
e(1)* |
j |
1 |
|
|
|
|
j |
1 |
|
|
|
; |
|
|
|
|
|
|
m |
|
|
|
|
|
|
(16) |
|||
|
|
|
|
|
|
|
( |
j )2 |
|
|
|
|
|
|
|
|
|
|
|
j |
1 |
|
|
|
|
|
|
|
|
где m – число экспериментально полученных деформаций; |
||||||||||||||
e* |
max{e* |
,e* |
|
}. |
|
|
|
|
|
|
|
|
|
|
(0) max |
|
(0)0 |
(0)90 |
|
|
|
|
|
|
|
|
|
|
|
Результаты измерений заносят в протокол (табл.5) |
|
33
Таблица 5. |
|
|
|
|
|
|
|
|
|
|
|
|
|
|
|||
Равномерное двухосное растяжение |
|
|
|
|
|
|
|
|
|||||||||
Ф.И.О. |
|
|
|
|
|
|
|
|
|
Дата |
|
|
|
|
|
||
Материал |
|
|
|
Состояние |
|
|
Толщина, мм |
|
|
|
|
||||||
|
|
|
|
|
|
|
|
|
|
|
|
|
|
||||
Напр.прокатки |
Длина ячейки вдоль |
|
Длина - поперек, мм |
|
|||||||||||||
|
|
|
|
|
|
|
|
|
|
|
|
|
|
|
|
|
|
№ |
|
|
|
|
Слева от трещины |
|
|
|
|
Справа от трещины |
|
||||||
|
|
|
Вдоль оси |
|
Поперек оси |
|
Вдоль оси |
Поперек оси |
|||||||||
ячейки |
|
|
|
|
|
||||||||||||
|
До |
|
После |
|
До |
|
После |
До |
|
|
После |
До |
|
После |
|||
|
|
|
|
|
|
|
|
||||||||||
1 |
|
|
|
|
|
|
|
|
|
|
|
|
|
|
|
|
|
2 |
|
|
|
|
|
|
|
|
|
|
|
|
|
|
|
|
|
3 |
|
|
|
|
|
|
|
|
|
|
|
|
|
|
|
|
|
4 |
|
|
|
|
|
|
|
|
|
|
|
|
|
|
|
|
|
5 |
|
|
|
|
|
|
|
|
|
|
|
|
|
|
|
|
|
34

2.5.ЛАБОРАТОРНАЯ РАБОТА № 5
Определение модуля Юнга и коэффициента Пуассона
Цель работы. Определение упругих механических характеристик материала, необходимых для оценки пружинения и утяжки формообразуемой детали.
Теоретическая справка. Модуль Юнга и коэффициент Пуассона являются упругими характеристиками. При моделировании операций пластического формообразования эти характеристики используются для оценки пружинения и утяжки заготовки из-за ее деформирования в направлениях, перпендикулярных направлению формообразования. Пружинением называется отклонение контура детали от контура шаблона или теоретического (расчетного) контура детали. Пружинение оценивается смещением контрольной поверхности детали относительно теоретического контура в направлении нормали к контуру в любой точке. Утяжкой детали называется уменьшение характерных размеров контура поперечного сечения в направлении, перпендикулярном направлению усилий формообразования.
Испытания. Модуль Юнга определяется на первом этапе растяжения образца в упругой зоне, соответствующей прямо пропорциональному участку диаграммы растяжения (Рис.20).
Рассмотрим процедуру определения модуля Юнга с помощью механического рычажного тензометра Гугенбергера
(Рис.21)
35

РР02
0.7Р02
Рi
Рi-1
0.1Рmax
l
li-1 li
Рис.20
Описанный в литературе прибор устанавливают на образце, вдоль его оси, в области расчетной длины. Образец предварительно растягивают до приблизительно 0.1Рmax. Затем производят ступенчатое нагружение образца усилиями Рi до нагрузки 07Р02. Величина интервала нагружения должна быть такой, чтобы в указанном диапазоне упругого деформирования (0.1Pmax-0.7P02) их число n было 5-7. На каждой ступени нагружения фиксируют изменение li базовой длины l0. По полученным результатам вычисляют модуль Юнга
n
|
l0 |
|
|
|
(Pi Pi 1 ) |
|
|
E |
|
|
i 2 |
|
; |
(17) |
|
F0 (n |
1) |
|
|
n |
|||
|
|
|
|
|
|||
|
|
|
li |
|
|
||
|
|
|
|
|
|
|
|
|
|
|
|
|
i 2 |
|
|
36

Образец
P |
P |
li |
l0 |
Рис.21
Коэффициент Пуассона вычисляют в области упругого деформирования (см. рис.20). Для этого на каждом этапе упругого ступенчатого нагружения наряду с продольной деформацией на базовой длине экстензометра li (Рис.22). определяют поперечную деформацию образца. Для
этого крепится и поперечный экстензометр.
i |
|
|
l |
|
|
|
|
Продольн |
0 |
|
ый |
|
|
|
l |
|
|
B |
|
B |
|
litrans |
Поперечн |
|
l0 |
|
|
ый |
|
|
|
Рис.22
37
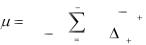
В процессе испытания после очередного i-ого этапа нагружения измеряют либо приращение поперечной базовой длины или (при отсутствии поперечного экстензометра) - ширину образца Bi микрометром (см. рис.22).
Учитывая результаты, описанные в предыдущем параграфе, вычисляют коэффициент Пуассона по формуле
1 |
|
n 1 l trans |
l trans |
|
|||
|
|
|
|
i |
i 1 |
. |
(18) |
|
|
|
|
|
|
||
|
(n |
1) i 1 |
li 1 |
|
|||
Если измерения поперечной деформации проводили по |
|||||||
изменению ширины |
образца, |
ltrans в (18) заменяется |
|||||
|
|
|
|
|
|
|
i |
соответственно на Bi.
Результаты испытаний заносят в протокол, показанный ниже
38

Таблица 6. |
|
|
|
|
|
|
|
|
|
|
|
|
|
|
|
|
|
|
|
|
|
|
||||
Протокол испытаний по определению модуля Юнга и коэффициента Пуассона |
|
|
||||||||||||||||||||||||
Ф.И.О. испытателя |
|
|
|
|
|
|
|
|
|
|
Дата |
|
|
|
|
|
|
|
|
|
||||||
Материал |
|
|
|
|
|
Состояние |
|
|
Полуфабрикат |
|
|
|
|
|
||||||||||||
|
|
|
|
|
|
|
|
|
|
|
|
|
|
|
|
|
|
|
|
|
|
|
|
|
||
№ образца |
|
|
Напр. прокатке |
|
|
Место разрыва |
|
|
|
|
|
|||||||||||||||
|
|
|
|
|
|
|
|
|
|
|
|
|
|
|
|
|
|
|
|
|
|
|
|
|
|
|
Ширина,мм |
|
|
|
|
|
|
Толщина,мм |
|
|
|
|
|
Площадь F0,мм2 |
|
|
|
||||||||||
Испыт.машина |
|
|
|
База тензометра l0 = 20.0 мм; Цена деления |
c = 0.001 мм |
|
|
|||||||||||||||||||
|
|
|
|
|
|
|
|
|
|
|
|
|
|
|
|
|
|
|
||||||||
Усилия и удлинения в упругой зоне |
|
|
|
|
|
|
|
|
|
|
|
|
|
|||||||||||||
№ |
1 |
|
|
|
2 |
|
3 |
|
4 |
|
5 |
6 |
|
7 |
|
|
8 |
|
9 |
10 |
|
|||||
Продольный тензометр |
|
|
|
|
|
|
|
|
|
|
|
|
|
|
|
|
|
P, Н
li,мм
li
Поперечный тензометр
li,мм
li 0
39
Параллельно с традиционным методом определения упругих характеристик материала выполняется эксперимент по их определению с помощью электронных датчиков перемещений и усилия.
Для этого на образце устанавливают цифровые датчики перемещений типа МТ10 в продольном и поперечном направлениях к оси образца. В процессе нагружения в упругой области записывается текстовый файл показаний датчиков.
Обработку результатов испытаний целесообразно проводить в Excelсреде по формулам (17), (18).
Полученные двумя способами значения сравнивают по точности, вычисляя относительные погрешости определения этих характеристик 2-м способом как наименее трудоемкого.
40