
Методическое пособие 364
.pdf
81
Из рис.67 следует, что каждому элементарному проводнику соответствуют индивидуальные места перегибов и что перегибов у проводника должно быть два. Гибка элементарных проводников на ребро производится в пакете, но только пакет должен быть собран под “гребенку ”.
На рис.68 показано, что гребенка 1 выполнена с
1 |
t |
2 |
|
|
Рис.68. Сборка пакета проводов под “гребенку” для формовки перегибов
уступами с шагом “t” и провода полустержня упираются каждый в отдельный уступ. Гибка пакета производится в гибочном штампе. Затем провода вынимают из штампа, выравнивают их торцами и скрепляют в середине скобой.
Плетут каждый полустержень отдельно. Для получения целого плетеного стержня вкладывают между полустержнями изоляционную прокладку. Затем складывают полустержни боковыми сторонами и рихтуют по всей длине плетеной части. Плетеную часть обильно промазывают лаком и весь стержень обматывают тканой тесьмой. Затем производится опрессовка плетеной части в пресс-форме гидравлического пресса, после чего проверяют на отсутствие замыканий между элементарными проводниками. Лобовые части формуют и прессуют под прессом, при этом они также обильно промазываются лаком и бандажируются тесьмой. В заключение тщательно (до блеска) зачищают концы проводников, лудят их и соединяют между собой серебряным
82
припоем. Изолируют стержни слоем непрерывной изоляции с помощью изолировочных головок. Это - трудоемкий процесс. Так, для изолировки всех стержней турбогенератора 100 тыс. кВт приходится намотать до 100 км микаленты. Лента накладывается в несколько этапов. После каждого слоя ленты стержень тщательно компаундируется. При компаундировании стержень обматывают слоем тканой ленты встык, который затем снимают вместе с натеками компаунда.
После укладки в пазы статора головки стержней соединяют пайкой с помощью специальных медных хомутов.
В высоковольтных машинах (выше 6000кВ) поверхность обмотки статоров покрывают полупроводящим лаком 462п с примесью сажи для предотвращения коронирования.
10. Пайка и свапка соединен й в обмотках
Токоведущие части электрических машин соединяют между собой чаще всего пайкой или сваркой. Их достоинство – надежность контактного соединения, стабильность и минимальная величина. переходного сопротивления. Пайка и сварка токоведущих частей имеют определенную специфику.
Пайка – процесс соединения деталей при помощи вспомогательного легкоплавкого материала. Соединяемые поверхности деталей во время пайки не переходят в расплавленное состояние.
Сварка – соединение за счет расплавления материала деталей в местах их соприкосновения. При сварке детали подвергаются местному разогреву до температуры плавления.
Чаще всего токоведущие части в машинах соединяют методом пайки. Материалы, используемые для этой цели, называют припоями. В электротехнической промышленности используются различные припои, отличающиеся по температуре плавления, химическому составу, сортаменту и др. В зависимости от температуры плавления припои
83
разделяют на твердые и мягкие. Мягкие припои имеют температуру плавления до +4000С. Припои с более высокой температурой плавления относят к твердым.
К припою предъявляют серьезные технологические требования. Он должен хорошо смачивать поверхность материала соединяемых деталей. Высокая смачивающая способность обеспечивает проникновение расплавленного припоя в глубокие и узкие щели между поверхностями соединяемых деталей. Этими свойствами в достаточной степени обладает чистое олово. Неудобства с его повсеместном применении в указанных целях связано с тем, что оно имеет высокую цену, а при низких температурах (ниже
–300С) резко меняет свои физические свойства.
Долгое время для пайки применялся единственный тип мягкого припоя – «тритник». Он состоит их 2-х частей олова и одной части свинца. Особенность этого сплава в том, что он переходит из жидкого состояния в твердое, минуя тестообразную размягченную фазу. Его недостаток – сравнительно высокая стоимость и низкая температура плавления.
Внастоящее время на основе олова выпускается широкий спектр мягких припоев, обладающих различными технологическими и экономическими характеристиками. Все они в качестве основного компонента содержат олово.
Такие припои получили наименование “припои оловянистосвинцовые”, сокращенно – ПОС. В зависимости от содержания олова различают марки этих припоев: ПОС-90, ПОС-61, ПОС50, ПОС-40, ПОС-30, ПОС-18. При повышении содержания олова повышается жидкотекучесть припоя, качество пайки повышается, но при этом одновременно растет его стоимость.
Вособо ответственных случаях, если между спаиваемыми деталями имеются очень узкие щели, пайку осуществляют чистым оловом, если это допустимо по климатическим условиям. Для лужения, а также в случае широких щелей между деталями применяют малооловянистые
84
припои, как более дешевые. Пайку мягкими припоями применяют в случаях, если места паек не нагреваются до температуры выше 100–120оС. Наиболее механически прочными являются припои ПОС–61 и ПОС–50. Припой ПОС–
90обладает высокой коррозионной стойкостью.
Сразработкой новых нагревостойких типов изоляции рабочие температуры обмоток в машинах возросли. В таких машинах пайку оловянистыми припоями выполнять нельзя. В
таких случаях применяют твердые (твердоплавкие) припои. Температура плавления твердых припоев от 600 до 850оС.
Наиболее широкое применение нашли твердые припои: 1- на основе серебра ( ПСР–71 – 71% серебра; 28% меди; 1% фосфора); 2- медно-фосфористые (МФ–1, МФ–2, МФ–3, ПМФ–7 –
содержание фосфора 7–8,5%, остальное медь). Медно-фосфористые припои имеют наименьшую
стоимость, не требуют применения флюсов при пайке. Они обеспечивают высокую механическую прочность и электропроводность соединения. С этой точки зрения ими следует заменять оловянистые припои. Недостатком МФ является низкая пластичность соединения. При работе в условиях сильных ударов, изгибов, вибраций такие соединения могут разрушаться. В ответственных случаях их заменяют более дорогими припоями типа ПСР. Припои типа ПСР применяют также для пайки соединений в микромашинах.
Важным моментом при выполнении паек является тщательная очистка мест пайки от посторонних веществ, загрязнений. Особенно чувствительны к этому припои ПОС. Для достижения качественной очистки применяют вспомогательный материал – флюс. Его применение диктуется необходимостью снятия окислов с поверхностей спаев, что позволяет получить хорошую смачиваемость припоем поверхностей спаев и обеспечивает хорошую сцепляемость припоя с материалом спаиваемых деталей. Флюс наносят на поверхность спаев после предварительной зачистки их

85
металлической щеткой, напильником или стеклянной шкуркой. Эти поверхности должны быть также обезжирены. Флюсы не могут заменить механической зачистки.
Тип применяемого флюса зависит от марки паяемых материалов. Для пайки меди мягкими припоями применяют в качестве флюсов канифоль (порошок), КЭЦ (раствор канифоли
|
|
|
|
|
|
в спирте |
в |
соотношении |
|||
|
|
|
|
|
|||||||
|
|
|
|
|
1:1), |
раствор канифоли в |
|||||
|
|
|
|
|
|
||||||
|
|
|
|
Слои |
|||||||
|
|
|
|||||||||
|
|
|
|
нихрома |
бензине. |
После окончания |
|||||
|
|
|
|||||||||
|
|
|
|||||||||
|
|
|
|
|
пайки |
|
|
канифоль |
|||
|
|
|
|
|
|||||||
Рис.69 Паяльник с |
покрывает |
место пайки |
|||||||||
тонким |
слоем, |
защищая |
|||||||||
контактным нагревом |
|||||||||||
его от коррозии. |
|
||||||||||
|
|
|
|
|
|
|
|||||
|
|
|
|
|
При |
пайке |
медных |
сплавов |
(латуни) в качестве флюса применяют
|
|
|
|
|
|
|
|
|
|
|
борную |
кислоту. |
При |
пайке |
медно- |
||
|
|
|
|
|
|
|
|
|
|
||||||||
|
|
|
|
|
|
|
|
|
|
фосфористыми припоями |
флюс |
не |
|||||
|
|
|
|
|
|
|
|
|
|
|
|||||||
|
|
|
|
|
|
|
|
|
|
|
требуется. |
|
|
|
|
|
|
|
|
|
|
|
|
|
|
|
|
|
|
|
|
|
|
||
|
|
|
|
|
|
|
|
|
|
|
Расплавление припоев, |
разогрев |
|||||
|
|
|
|
|
|
|
|
|
|
|
|||||||
|
|
|
|
|
|
|
|
|
|
|
спаев |
осуществляется |
с |
помощью |
|||
|
|
|
|
|
|
|
|
|
|
|
паяльников. Различают следующие типы |
||||||
Рис70. Дуговой |
паяльников, |
применяемых |
в |
||||||||||||||
электромашиностроении: |
|
|
|
с |
|||||||||||||
паяльник |
|
|
|
||||||||||||||
нагревательными |
|
|
спиралями |
||||||||||||||
|
|
|
|
|
|
|
|
|
|
|
|
|
мощностью до 100 Вт , t – до 500оС.; с контактным нагревом (рис.69); ультразвуковые для пайки алюминия; дуговые (рис.70).
Пайка коллекторов паяльниками малопроизводительна и обладает низким качеством спаев. Поэтому пайку коллекторов производят обычно в специальных ваннах (см. рис.71). Время воздействия высокой температуры на коллектор должно быть минимальным. Применяют для пайки предварительно залуженных поверхностей. Места спаев нагревают пламенем паяльной лампы, после чего к месту спая подносят палочку припоя.
86
Для выполнения спаев в крупных электрических машинах применяется пайка с нагревом паяльной лампой. С помощью паяльника с нагревательными спиралями паяют
порше
t 320–340oC
при
Рис. 71 Паяльная ванна
соединения обмоток машин малой мощности, осуществляют пайку бандажей. Для выполнения пайки твердыми припоями разогрев спая может осуществляться дуговым паяльником.
В случаях, если возникает необходимость местного разогрев массивного проводника, чтобы не повредить
изоляцию вблизи мест |
|
|
|
||
пайки, |
применяют |
|
|
|
|
более |
эффективные |
|
|
|
|
способы |
|
нагрева. |
|
|
|
|
|
|
|
||
Соединяемые |
детали |
|
|
|
|
соединяют |
между |
|
|
|
|
собой угольными или |
|
|
|
||
графитными |
|
Рис. 72 Паяльные клещи |
|
||
электродами. |
Для этой |
|
|
|
цели могут быть использованы специальные паяльные клещи (Рис.). С их помощью можно припаять провода 5–25 мм2. В места соединения вкладывают пластинки твердого припоя и разогревают их для получения не окисляемых контактных поверхностей применяют лужение. Лужению подвергают также детали, которые в последствии будут подвержены пайке. Существует два способа лужения: электролитическое и горячее.
87
Электролитическое лужение применяют для мелких деталей (кабельные наконечники, крепеж и т.п.). Для этого их нанизывают на проволоку и опускают в гальваническую ванну. Припой осаждается на деталях при пропускании тока через электролит.
Горячее лужение осуществляется путем окунания детали в ванну с расплавленным припоем. Предварительно эти поверхности зачищаются и покрываются флюсом.
Для полуды алюминиевых проводов применяют горячее ультразвуковое или абразивное лужение.
Способ сварки для соединения проводников все шире применяется в электромашиностроении. Концы катушек, подлежащие сварке, скручивают между собой. От сварочного трансформатора один конец подводят к скрученным концам катушек, другой – к угольному электроду. Концы проводов оплавляют электрической дугой. При передержке дуги может наступить пережог материала. Механическая прочность соединения резко падает. Электродуговую сварку применяют для наплавки короткозамыкающих колец в КЗ роторах с медными стержнями. Из-за опасности пережога проводников часто сварку заменяют пайкой твердыми припоями.
В последнее время появились методы холодной сварки. Для этой цели свариваемые детали подвергают сжатию специальными клещами или под гидравлическим прессом. Преимущества этого метода перед пайкой: высокая надежность крепления; не нужны припои, флюсы; снижается трудоемкость работ; исключается опасность повреждения изоляции или пережога проводников.
11. Бандажи и пазовые клинья
При вращении ротора на пазовые и лобовые части обмоток действуют центробежные усилия. Величину этих усилий можно определить:
|
|
|
|
88 |
|
P |
mv |
2 |
m 2 R |
(v= R), |
(12) |
R |
|
||||
|
|
|
|
|
где: m – масса рассматриваемой части; v – линейная скорость;- угловая скорость; R – расстояние центра тяжести рассматриваемого участка от оси вращения.
Отсюда можно найти отношение центробежного усилия к массе:
P |
|
v2 |
2 R . |
(13) |
|
m |
R |
||||
|
|
|
Если диаметр ротора 500 см (R=25 см; n=1000 об/мин,
т.е. = n/30=1000 /30=105 1/c), то
P |
|
P |
|
2 R |
|
1052 0.25 |
281, |
(14) |
|
Q |
mg |
g |
9.81 |
|
|||||
|
|
|
|
|
|
где g – ускорение свободного падения,
т.е., если учесть, что центр тяжести обмотки расположен на расстоянии от вала, меньшем радиуса ротора, то центробежная сила в приведенном примере не менее чем в 250 раз больше веса обмотки.
Поскольку центробежная сила растет пропорционально квадрату скорости, то в принятом примере при больших скоростях получим еѐ значения в зависимости от частоты вращения ротора (см. табл. 2).
Теперь, имея ориентировочное представление о силах, действующих на обмотку, можно сделать совершенно естественный вывод: обмотка ротора нуждается в
Таблица 2
n (об/мин) |
1000 |
2000 |
3000 |
|
P/Q |
250 |
1000 |
4500 |
|
Центробежная сила (кг) |
250 |
1000 |
4500 |
|
на 1 кг веса обмотки |
||||
|
|
|

89
дополнительном механическом креплении. С целью механического крепления пазовой части обмоток применяют: закрытые пазы, клинья, бандажи. Бандажи и клинья должны обеспечивать высокую степень прессовки частей обмоток с целью исключения возможности их взаимного перемещения и нарушения балансировки ротора, а также разрушения изоляции.
Клинья применяют в случаях полузакрытых и полуоткрытых пазов. Клинья – более распространенные детали для крепления обмотки в пазах. Недостатки фиксации обмотки с помощью клиньев: клинья занимают большую часть паза по сравнению с бандажом; забивание клиньев трудоемкая операция (в малых машинах при крупносерийном производстве заклинивание производится на автоматах); возможность усушки клиньев и ослабления обмотки в пазу (для деревянных клиньев).
Если же в конструкции предусмотрен открытый паз, фиксация пазовой части осуществляется иногда бандажами. Недостатки фиксации с помощью бандажей: обмотка фиксируется не по всей длине пазовой части, что приводит к возрастанию удельных усилий под бандажами; усложнение технологии из-за необходимости выполнения канавок под бандажи, нужны листы разного диаметра; необходимость пайки начала и конца бандажной проволоки усложняет технологию, наличие пайки снижает надежность механической фиксации; как правило, бандажи выполняют стальной проволокой, что повышает коэффициент пазового рассеяния; процесс пайки бандажей способствует более быстрому старению изоляции из-за перегревов.
При конструировании машин бандажи применяют только в случаях, если это дает увеличение коэффициента заполнения паза медью.
Лобовые части роторов, за исключением роторов турбогенераторов и короткозамкнутых обмоток типа
|
|
90 |
|
«беличьей |
клетки», |
укрепляют |
проволочными |
бандажами (в микромашинах лобовые части бандажируют нитками).
Если на обмотку якоря, например, на лобовые части, намотать слой проволоки с некоторым натяжением, то обмотка будет сжата по направлению к оси ротора с некоторым усилием (Рис73.). Усилие Q выбирается из таких соображений, чтобы возникающие при
|
проволока |
работе |
|
машины |
||||
Т |
центробежные |
силы |
Р |
|||||
|
|
|
|
|
были |
|
меньше |
|
|
|
|
|
|
|
|||
|
|
|
|
|
|
(P<Q).Поэтому |
||
|
|
|
Р |
|
|
|||
|
|
|
|
проволоку |
необходимо |
|||
|
паз |
|
|
|
||||
|
|
|
|
держать |
натянутой |
с |
||
|
|
|
|
|
||||
|
|
|
|
|
усилием “Т”. |
|
|
|
|
|
|
|
|
|
|
||
Рис.73 . Усилия, действующие |
Сила |
|
Q |
|||||
на бандажную проволоку |
обеспечивается |
выбором |
||||||
|
|
|
|
|||||
|
|
|
|
|
диаметра |
и |
силы |
натяжения проволоки при намотке бандажа. При этом нельзя забывать о том, что натяжение бандажной проволоки при ее намотке создает изгибающее усилие на вал, что может привести к его деформации.
Начало и конец бандажа зажимается жестяными полосками и припаивается. Равномерно по окружности витки бандажа фиксируют полосками жести с припайкой (Рис.74).
Пайка бандажей – очень трудоемкий процесс.
Разработка |
новых |
пайк |
||
менее |
трудоемких |
|||
|
||||
способов |
фиксации |
пайк |
||
бандажей |
|
дает |
||
|
|
|||
значительный |
|
|
||
экономических |
|
|
||
эффект. |
|
|
|
|
Для |
|
|
Рис.74. Крепление витков и |
|
изготовления |
|
концов проволочного бандажа |

91
бандажей применяют стальную луженую проволоку диаметром 0,4–2,5 мм. Под бандажами укладываются полоски из изоляционного материала в соответствии с классом изоляции машины. В крупных машинах (D>800 мм) намотка проволочного бандажа ведется в несколько слоев, причем намотка каждого последующего слоя ведется с натяжением, на 10% меньше, чем для предыдущего слоя.
В процессе пропитки вследствие размягчения изоляции бандажи теряют свое натяжение, на лобовых частях может наблюдаться сползание бандажа. В этом случае полезно бывает наложить поверх уже выполненного дополнительно технологический бандаж. Намотка проволоки технологического бандажа ведется вразбежку по всей длине ротора. После пропитки и сушки технологические бандажи снимают (они могут быть использованы повторно с другими роторами), ротор бандажируется стационарными бандажами.
Стационарные бандажи наматывают с одного куска проволоки, спайки и скрутки не допускаются. Изоляция обмотки относительно бандажей проверяется мегомметром.
Наложение бандажей на ротор электрической машины производится на бандажировочных станках. Они относятся к
так называемому «нестандартному оборудованию», т.е.
Динамометр
Рис.75. Создание натяжения проволоки и его измерение
обычно изготавливаются самими заводами для собственных нужд. Станки должны быть снабжены устройством для 92
92
натяжения проволоки и динамометром для контроля натяжения.
Натяжение проволоки создается числом роликов, огибающих проволоку и силой сжатия прокладок. Мелкие якоря устанавливаются в центрах. Крупные якоря или скользящими подшипниками. Вращение якорю сообщается ременной передачей, для чего ремень накладывают на коллектор или на бочку ротора.
Бандажи из стеклолаколенты начали внедрять вначале для стяжки стержней силовых трансформаторов, а затем – и для бандажирования роторов. Материал представляет собой стеклоленту из ориентированного волокна, пропитанную лаком. Лента наматывается по спирали (виток на виток), специального крепления конца не требуется. Способ этот очень перспективен для роторов электрических машин.
Для изготовления клиньев используют твердые породы дерева (дуб, бук, береза), текстолит, прессшпан и другие изоляционные материалы. В случае применения дерева необходимо следить за качественной просушкой. Для изготовления клиньев пригодны куски древесины без какихлибо пороков (сучков, сколов и т.п.).
В случае большой длины якоря вдоль паза располагается несколько клиньев. Поэтому при серийном и
|
|
деревянные |
|
|
|
|
текстолитовые |
|||||||||||||
|
|
|
|
|
|
|
|
|
|
|
|
|
|
|
|
|
|
|
|
|
|
|
|
|
|
|
|
|
|
|
|
|
|
|
|
|
|
|
|
|
|
|
|
|
|
|
|
|
|
|
|
|
|
|
|
|
|
|
|
|
|
|
|
|
|
|
|
|
|
|
|
|
|
|
|
|
|
|
|
|
|
|
|
|
|
|
|
|
|
|
|
|
|
|
|
|
|
|
|
|
|
|
|
|
|
|
|
|
|
|
|
|
|
|
|
|
|
|
|
|
|
|
|
|
|
|
|
|
|
|
|
|
|
|
|
|
|
|
|
|
|
|
|
|
|
|
|
|
|
|
|
|
|
|
|
|
|
|
|
|
|
|
|
|
|
|
|
|
|
|
|
|
|
|
|
|
|
|
|
|
|
|
|
|
|
|
|
|
|
|
|
|
|
|
|
|
|
|
|
|
|
|
|
|
|
|
|
|
|
|
|
|
|
|
|
|
|
|
|
|
|
|
|
|
|
|
|
|
|
|
|
|
|
|
|
|
|
|
|
|
|
|
|
|
|
|
|
|
|
|
|
|
|
|
|
|
|
|
|
|
|
|
|
|
|
|
|
|
|
|
|
|
|
|
|
|
|
|
|
|
|
|
|
|
|
|
|
|
|
|
|
|
|
|
|
|
|
|
|
|
|
|
|
|
|
|
|
|
|
|
|
|
|
|
|
|
|
|
|
|
|
|
|
|
|
|
|
|
|
|
|
|
|
|
|
|
|
|
|
|
|
|
|
|
|
|
|
|
|
|
|
|
|
|
|
|
|
|
|
|
|
|
|
|
|
|
|
|
|
|
|
|
|
|
|
|
|
|
|
|
|
|
|
|
|
|
|
|
|
|
|
|
|
|
|
|
|
|
|
|
|
|
|
|
|
|
|
|
|
|
|
|
|
|
|
|
|
|
|
Рис.76. Изготовление пазовых клиньев
массовом производстве возникает необходимость в большом количестве клиньев. Изготовление их идет на автоматах.

93
Поперечное сечение клина выбирается минимальным из условия величины коэффициента заполнения паза. Но слишком большой клин – трудно или невозможно забить. Клин входит в паз туго, ведь он должен создать прессующее усилие в пазу.
При забивании клиньев (молотком) их концы расплющиваются, раскалываются, поэтому такие клинья нужно удалять.
Удаление связано с излишними расходами материала и затратами времени.
Здесь определенную пользу приносит направляющая коробочка – обойма из листовой стали, выполняющая роль кондуктора. Применение обоймы позволяет уменьшить брак от
|
клин |
разрушения |
клиньев и |
|
защитить лобовые части |
||
|
|
||
|
|
от ударов молотка. |
|
Рис. 77 Направляющая |
|
Технологический |
|
|
процесс |
заклинивания |
|
коробочка - обойма |
|
||
|
пазов и |
изготовления |
|
|
|
клиньев нельзя считать совершенным. В последнее время пазы микромашин иногда заклиниваются хлопчатобумажным шнуром, пропитанным лаком или компаундом. Обрезка шнура производится после заклинивания паза.
Заклинивание может выполняться на полуавтомате с производительностью до 70 пазов в минуту.
12. Пропитка и сушка обмоток
Ранее мы говорили, что практически все обмотки подвергаются пропитке лаком или компаундированию. После пропитки обмотка приобретает новые свойства: повышается нагревостойкость; улучшается теплоотвод от проводников; повышается влагостойкость изоляции; повышается электрическая прочность изоляции; повышается механическая прочность изоляции, т.е. обмотка устойчива к воздействию
94
вибраций и других перегрузок; повышается химическая стойкость.
После пропитки наружные поверхности обмоток обычно покрывают эмалями ( 50–70 мкм) для защиты от воздействия грязи, масел, механических контактов с деталями машины и т.п.
Современное электромашиностроение располагает большим арсеналом пропиточных лаков и компаундов, покровных лаков и эмалей, клеящих лаков. Разработаны и применяются в промышленности специальные пропиточные установки, обеспечивающие автоматически заданный режим пропитки и сушки. Тип установки определяется способом пропитки и масштабами производства.
Различают следующие способы пропитки: погружение в лак; на стендах с нижней подачей лака; струйным поливом, капельная; вакуумные способы (вакуумно-нагнетательные); ультразвуковые пропитки; компаундирование и др.
Непропитанные изоляционные материалы (особенно волокнистые виды изоляции) хорошо впитывают влагу из окружающего воздуха. Эта влага, которая попадает в изоляцию во время ее хранения, а также во время изготовления и хранения обмоток, затрудняет проникновение пропиточных лаков в обмотку. Будучи законсервированной в обмотке, она будет ухудшать параметры изоляции, может привести даже к еѐ электрическому пробою. Поэтому перед пропиткой обмотки и изоляционные материалы подвергаются сушке.
Время предварительной сушки зависит от температуры сушки. Однако верхний предел допустимой температуры сушки ограничивается классом изоляции. В этом случае сокращение времени сушки может быть достигнуто применением вакуумной сушки. Якорь, статор или обмотку нагревают до определенной температуры при нормальном атмосферном давлении, после чего давление в камере понижают на заданное время (время сушки). Если подогрев осуществить в вакууме, то время сушки можно сократить еще
95
больше (но это имеет значение лишь при массовом производстве). После просушки изделия сразу же направляются на пропитку. Время между сушкой и пропиткой строго регламентировано.
Операцию предварительной сушки можно опустить в случае применения при пропитке водоэмульсионных лаков. Вода, содержащаяся в таком лаке в виде эмульсии, смешиваясь с влагой, имеющейся в изоляции, способствует хорошей пропитке.
Пропитка окунанием является наиболее простым и распространенным способом. Для лучшего проникновения лака в изоляцию изделие предварительно подогревают до температуры порядка 70оС. Если изделие идет на пропитку непосредственно после сушки, то дополнительный его подогрев не требуется. Обмотка должна находится в погруженном состоянии до прекращения выделения пузырьков воздуха.
Если пропитка многократная (что зависит от типа машины и конструкции обмотки), то первая пропитка наиболее длительная (до 1 часа). Изделие располагается в баке с лаком таким образом, чтобы пазы (ось магнитопровода) находились в вертикальном положении. Якорь погружают коллектором вверх. Все это способствует лучшему заполнению пор изоляции и обмотки пропиточным материалом.
Концы валов, коллектор и другие детали обычно стараются защищать от воздействия лака. Если это невозможно, то после пропитки эти места сразу протирают ветошью, смоченной в растворителе.
В пропиточном отделении должен быть установлен строгий контроль над составом (чистотой) лака, его вязкостью. Котлы и ванны периодически очищают от остатков лака, а погружаемые изделия тщательно очищают от грязи продувают сжатым воздухом.
Недостатки этого метода: необходимость погружать изделие в лак полностью; повышенный расход лака и
96
увеличение трудоемкости работ из-за попадания лака на металлические детали и сопрягаемые поверхности изделия; лаковая пленка на поверхности магнитопровода затрудняет выполнение лакокрасочного покрытия (некоторые сочетания лаков и эмалей дают плохую адгезию); выделения из пропиточных ванн и сушильных шкафов дают большую загазованность помещений; большое время пропитки.
Пропитка в водоэмульсионных лаках не допускает предварительного нагрева изделия, поскольку водно-лаковая эмульсия распадается при соприкосновении с нагретой поверхностью.
При пропитке с нижней подачей лака изделия устанавливаются на специальном стенде, лак подается внутрь статора или в бачок с роторами из резервуара через лакопроводы. Данный метод пропитки позволяет сократить расход лака, снижается загазованность помещения. Недостаток
– снижение производительности по сравнению с предыдущим методом за счет дополнительных работ (замазывание щелей и отверстий в статоре). Способ применяется в условиях мелкосерийного производства.
Пропитка струйным поливом применяется для пропитки лаком КП статоров асинхронных двигателей единой серии 1–5 габаритов. Статор устанавливается вертикально на горловину, сверху на лобовые части поливается лак. Лак КП в этом случае дает хорошее заполнение. Сушка производится путем индукционного нагрева статора. Время полимеризации лака небольшое.
Вакуумная пропитка применяется для пропитки мелких статоров и роторов, а также полюсных катушек. Для пропитки применяют лак К47 (кремнийорганический). Последовательность пропитки: сушка; охлаждение до 70оС; сушка под вакуумом в автоклаве; пропитка (для улучшения заполнения лаком его подают в автоклав под давление 8 Атм.); стекание остатков лака.
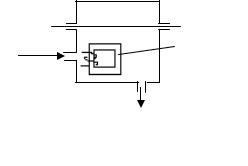
|
|
|
|
97 |
|
|
|
|
|
После пропитки изделие подвергают сушке (до 10–12 |
|||||||||
часов). Предварительный нагрев изделия перед пропиткой до |
|||||||||
160оС позволяет значительно сократить время сушки (до 2х |
|||||||||
часов), но не всякая изоляция допускает перегрев изделия. |
|||||||||
Качественная |
сушка |
во |
многом |
предопределяет свойства |
|||||
|
|
лак |
|
|
изоляции. |
Следует |
|||
|
|
|
|
помнить, что лак, как |
|||||
|
|
|
|
|
|||||
Н2О |
|
|
излучатель |
правило, |
содержит |
два |
|||
|
|
|
|
компонента: |
|||||
|
вода |
|
|
|
|
||||
|
|
|
|
|
|
||||
|
|
|
|
|
пленкообразующее |
||||
|
|
Н2О |
|
вещество |
(смола, |
||||
|
|
|
|
|
|
|
|||
Рис. 78 |
Схема ультразвуковой |
компаунд или др.) и |
|||||||
растворитель. В начале |
|||||||||
|
пропитки |
|
|
||||||
|
|
|
сушки |
температура |
не |
||||
|
|
|
|
|
|||||
|
|
|
|
|
должна |
|
превосходит |
||
точку кипения растворителя. Такая температура держится до |
|||||||||
момента его полного удаления, что можно оценить |
|||||||||
отсутствием конденсата в выходящем из печи воздухе. Далее |
|||||||||
температуру можно повысить до уровня, допустимого для |
|||||||||
заложенной в изделие изоляции. Это ускорит полимеризацию |
|||||||||
пленкообразующего вещества. Периодически рекомендуется, |
|||||||||
не допуская снижения температуры изделия, измерять |
|||||||||
сопротивление изоляции. Полимеризацию можно считать |
|||||||||
законченной, если повышение сопротивления изоляции |
|||||||||
приостановится. В технологическую инструкцию вносится |
|||||||||
время испарения растворителя и время полимеризации |
|||||||||
пленкообразовантеля. |
|
|
|
|
|
|
|||
Ультразвуковая пропитка применяется для пропитки |
|||||||||
обмоток микромашин. Дает уменьшение времени пропитки и |
|||||||||
повышает заполнение. Время пропитки снижается до 2–2,5 |
|||||||||
часов. Лак проникает между пластинами магнитопровода и |
|||||||||
коллектора. |
|
|
|
|
|
|
|
||
Хоть это и хорошо, но процесс сушки значительно |
|||||||||
усложняется. Поэтому здесь часто применяют токовую сушку |
98
обмоток. Лучше – переменным током. Особое внимание следует обратить на качество сушки после первой пропитки.
Компаундирование обмоток – это пропитка их в битумных компаундах, а для микромашин – в эпоксидных смолах с предварительной пропиткой лаком.
Компаундирование битумом применяется для пропитки обмоток крупных машин и в других случаях, когда машина работает в условиях повышенной влажности.
Хорошему проникновению лака способствует предварительной вакуумирование катушек с последующей подачей компаунда под давлением. Битумные компаунды перед компаундирование подогревают до 150оС. в последнее время разработаны специальные автоклавы, в которых компаунд может подогреваться до 175–185оС.
Катушки в автоклав складывают с прокладками, обеспечивающими зазор между катушками 10–15 мм. Вакуумная сушка в автоклаве производится при давлении не выше 160 мм.рт.ст. После компаундирования в автоклав подается разогретый компаунд, вакуум доводится до 20 мм.рт.ст., а через 15–20 мин давление повышается до 6–7 атм.
Процесс «вакуум–давление» повторяется до 4–х раз, затем давление до 6 атм выдерживается 5 часов. После окончания компаундирования автоклав продувают сжатым воздухом и при атмосферном давлении дают возможность стечь с катушек остаткам компаунда.
После изъятия катушек из автоклава с них немедленно снимают технологический слой киперной ленты. Контроль качества пропитки – выборочный, путем вскрытия одной из катушек. Практикуется также прием взвешивания изделия до и после пропитки.
Компаундирование обмоток микромашин эпоксидными компаундами осуществляется в специальных формах в следующей последовательности: смола смешивается с отвердителем; изделие помещают в специальную заливочную форму, куда под давлением подают компаунд. Производится

99
выдержка на воздухе (до 4х часов в зависимости от марки смолы), а затем - запеканке в печи (до 4х часов при температуре 100–160оС, в зависимости от класса изоляции).
После пропитки производится сушка пропитанной обмотки. Она предназначена для удаления растворителя и запекания (полимеризации) лаковой пленки. Сушка обмоток производится в специальных сушильных шкафах. Время сушки после каждой пропитки зависит от размеров изделия, типа изоляции, марки лака, способа и температуры сушки. Увеличение температуры сушки сокращает ее время, но одновременно ускоряет старение изоляции. Поэтому температура сушки не должна превышать допустимую для данного класса изоляции.
Одновременно в печь загружают изделия, имеющие соизмеримые размеры, общую марку пропиточного лака, один класс изоляции. Изделия в печи размещают из условия хорошего доступа воздуха к каждому изделию.
Отсчет времени сушки ведется с момента достижения изделиями заданной температуры сушки (контролируется по сопротивлению обмотки или термопарами).
Кремнийорганические лаки требуют ступенчатой температуры сушки: 110–130оС – удаление растворителя, 180– 190оС – запекание лака. Качество сушки проверяют по величине сопротивления изоляции при температуре сушки. Иногда можно встретить, что сопротивление изоляции контролируют в холодном изделии, периодически извлекая его из печи. Это – неверно, такая технология может привести к браку.
Способы сушки: конвекционный – циркуляция воздуха между калорифером и изделиями; терморадиационный – нагрев инфракрасным излучением специальных излучателей до +300–450оС (лампы, трубы с теплоносителем, ТЭНы и другие); индукционный – токами высокой частоты разогревают корпус статора; токовый – нагрев постоянным током, протекающим по обмоткам. Но лучше здесь применить
100
переменный ток. Он обеспечивает одновременный нагрев и проводников и сердечника.
14. Контроль и испытание обмоток
Качество обмотки определяет долговечность и надежность работы электрической машины. В процессе изготовления обмоток состояние их изоляции, отсутствие обрывов, правильность соединений проверяется неоднократно на следующих этапах их изготовления: в процессе и по окончании изготовления катушки; в процессе и после укладки обмоток в пазы; по окончании сборки машины. Последний этап входит в программу испытаний электрической машины.
Рассмотрим контроль и испытание обмоток на первых двух этапах.
На первом этапе изготовления проверяют: геометрические размеры; правильность маркировки выводов; электрическую прочность изоляции; электрическое сопротивление изоляции; активное сопротивление обмотки, количество витков (если их много, то выборочно).
На втором этапе, после насадки коллектора, проверяют отсутствие замыканий между пластинами и электрическую прочность изоляции пластин относительно корпуса (рекомендуется непосредственно перед укладкой в пазы). До распайки петушков следует проверить электрическую прочность и сопротивление корпусной изоляции обмотки, произвести контроль витковой изоляции, измерить сопротивление обмотки. После пайки коллектора следует также проверить правильность соединения, отсутствие обрывов, прочность изоляции и отсутствие витковых замыканий в обмотке готового якоря (статора).
Величина испытательного напряжения:
2UH+500
2UH+1000 1 мин.
1.3UH