
Методическое пособие 236
.pdfОборудование и материалы Заготовки под сварку, пост РДС или полуавтоматической
сварки в защитном газе, фрезерный или отрезной станок, система пробоподговки образцов, включающая низкоскоростной отрезной станок Полилаб 930М, шлифовально-полировальный станок Шлиф-1, установку элетрохимического полирования Шлиф – 2 ТМ, шкаф вытяжной 15.04, абразивные материалы, полировальные пасты, химические реактивы, химическая посуда, металлографические микроскопы МИМ-8М, ЛВ-34 и РВ-21-1 с камерой визуализации DM130.
Задание
1.Изучите последовательность и методику операций изготовления макро- и микрошлифов.
2.В соответствии с заданием преподавателя изготовьте образцы для исследований.
3.Подберите с помощью методических указаний и справочной литературы необходимые материалы для подготовки и травления металлографических шлифов.
4.Изготовьте в соответствии с заданием металлографические шлифы сварных соединений и исследуйте их на микроскопе.
5.Определите наблюдаемые зоны макро- и микроструктуры, возможные дефекты соединения.
Содержание отчета
1.Краткие сведения о методике приготовления металлографических шлифов из данных сплавов.
2.Технология подготовки образцов и составы травителей.
3.Рисунки, наблюдаемых в микроскоп макро- и микроструктур с их описанием.
Макро- и микроанализ.
В металлографических исследованиях различают методы макроанализа при помощи макрошлифов и микроанализа с использованием микрошлифов.
19
Строение металла, изучаемое при помощи макроанализа, называют макроструктурой. Это, как правило, более грубые детали структуры – конгломераты отдельных зерен, химическая и структурная неоднородность, дефекты в виде больших пор, трещин, подрезы, непровары, нарушения геометрии сварного шва в сварных соединениях и т.д. Макрошлиф изучают невооруженным глазом или при небольших (до 30 крат) увеличениях. Визуальный осмотр сварных швов дает информацию о наплывах, подрезах,
газовых |
порах непроварах и трещинах. |
|
|
Дендритное строение сварного шва, |
а также |
трещины, |
|
непровары |
более четко выявляются |
после |
травления |
исследуемых поверхностей сварного шва различными травителями. Например, для травления сварных соединений сталей используют 10–25 % - ный водный раствор азотной кислоты. Глубокое травление или травление в реактиве на общую химическую неоднородность позволяют выявить зону термического влияния.
Изучение изломов и методы выявления неоднородности используют при исследовании и структурной и химической неоднородности металлов и сплавов, которая возникает при термической и химико-термической обработке.
Так неоднородность, возникающую после цементации, можно выявить глубоким травлением исследуемой поверхности макрошлифа в 50 %-ном водном растворе соляной кислоты при температуре 80 С в течение 3 мин.
Изменение формы и размеров зерна в результате рекристаллизации может быть установлено также глубоким травлением. Например, глубокое травление в 50 % -ном водном растворе NaOH в течение 5-10 мин. и последующее травление в реактиве, состоящем из 2 частей HCl, 3 частей HNO3 и 1 части воды, в течение нескольких секунд выявляют форму и размер макрозерна, возникающего в алюминиевом образце после рекристаллизации.
20
Структуру металла, изучаемую при микроанализе, называют микроструктурой.
Микроанализ дает возможность определять тонкую структуру металлов и сплавов после деформации, термической обработки и других технологических операций, а также форму и размер структурных составляющих.
Методика изготовления микрошлифа схожа с методикой, используемой в макроанализе, однако имеет свои особенности и более сложна.
Приготовление микрошлифов.
Успех проведения металлографического анализа в большой мере предопределяется качеством приготовления шлифа и выбором условий травления. Поэтому продолжаются работы по созданию оборудования и методик металлографического анализа применительно к определенным группам материалов, а качественное приготовление микрошлифа по-прежнему считается искусством.
Наиболее трудоемкой частью работы является приготовлением микрошлифа. Эта работа требует от исполнителя известных навыков.
Существуют различные способы приготовления микрошлифов. Сущность их сводится к обработке поверхности шлифа абразивными частицами различной зернистости, нанесенными на бумажную или матерчатую основы, либо входящими в состав специальных паст. В настоящее время большое распространение получил способ приготовления шлифов на корундовых водоупорных бумагах с различной зернистостью (по ГОСТ 3647-71): КЗ-16, КЗ-12, КЗ-8, КЗ- 6, КЗ-5, КЗ-4, КЗМ-40, КЗМ-28, КЗМ-20, КЗМ-14.
Полирование проводят на сукне или фетре, который периодически смачивают водным раствором окиси хрома или алюминия. При изготовлении микрошлифов необходимо соблюдать следующие основные правила, которые можно считать общими для подавляющего большинства металлов.
21
Шлифование следует осуществлять последовательным переходом от более крупнозернистой бумаги к бумаге с меньшей зернистостью. При переходе от одного номера бумаги к другому необходимо изменять положение образца относительно диска на 90 и шлифовать до тех пор, пока не исчезнут следы обработки от предшествующего номера бумаги. Чтобы избежать попадания частиц более грубого абразива на бумагу следующего номера, образец необходимо каждый раз промывать водой. Не следует делать резкого перехода с грубой шлифовки на мелкую, так как в результате этого часто создается кажущееся представление о хорошей подготовке поверхности. На самом деле происходит лишь сглаживание верхних гребней, образовавшихся после грубой шлифовки, и заполнение впадин между ними абразивом и смятым металлом. Это обнаруживается после травления образца, на котором четко проявляются царапины. Не рекомендуется сильно прижимать образец к шлифовальной бумаге, так как это может привести к перегреву его поверхности и существенному изменению структуры поверхностного слоя. Чтобы образец не перегревался, его периодически охлаждают в воде.
Шлифовка образцов производится либо вручную, когда шлифовальная бумага кладется на ровные плоские плиты (стекло, мрамор), либо на специальных станках с закреплением шлифовальной бумаги на вращающихся дисках или лентах.
При приготовлении шлифов на образцах из пористых материалов (например, серый чугун) или из материалов с легко выкрашивающимися включениями перед окончательной полировкой образец нагревают до 70 – 80 С и погружают в расплавленный парафин. После охлаждения избыток парафина удаляют с поверхности шлифа ватным тампоном и шлиф окончательно полируют на сукне.
При шлифовке мягких материалов рекомендуется смачивать шлифовальную бумагу керосином, а при обработке цветных металлов - покрывать ее тонким слоем парафина.
22
Качество шлифовки проверяют осмотром поверхности образца под лупой.
Если исследуемые образцы имеют небольшие размеры (проволока, тонкие ленты, мелкие детали и т.п.), то для приготовления шлифа их зажимают в струбцины или заливают в легкоплавкие материалы (сплав Вуда, бакелит и т.д.), а также в эпоксидной смоле.
Заключительная операция подготовки поверхности микрошлифа – полирование - не должна занимать более 3-4 мин. Соблюдение этого правила особенно важно при работе с материалами, содержащими в структуре большие количества твердых и хрупких фаз (карбидов, интерметаллидов и т.п.). При сильном прижиме образца в процессе шлифования эти частицы разрушаются и выкрашиваются. Абразивный материал забивается в образовавшиеся лунки, и на шлифе при просмотре под микроскопом на месте включений наблюдаются «запятые» или «точки». Это создает искаженное представление о структуре металла, количестве и размерах неметаллических включений. В случае такого некачественного приготовления шлифа его целесообразно переделать шлифованием на бумагах последних номеров.
Приготовление шлифов на шлифовальных бумагах имеет ряд недостатков, которые особенно ощутимы при работе с образцами из сильно наклепывающихся или наволакивающихся материалов.
Значительные преимущества в этом отношении представляет методика изготовления микрошлифов с помощью алмазных эластичных дисков. Такие диски внедрены в практику многих металлографических лабораторий. В этом случае шлиф последовательно обрабатывают на трех дисках, имеющих различную зернистость: АСО10, АСМ40, АСМ3. В комплекте с дисками дается алмазная паста, с помощью которой можно проводить предварительное полирование перед окончательной доводкой на сукне с водной суспензией окиси хрома.
23
При шлифовании диск слегка увлажняют водой. Рекомендуемая скорость вращения 700 - 800 об/мин. Режущая способность алмазных зерен со временем снижается, так как диск забивается и сошлифовывается металлом. В этом случае его следует чистить обычной шкуркой (№ 25, 16), тщательно промыть водой и бензином. При правильном использовании работоспособность диска сохраняется в течение года. Обработку образца проводят при незначительном прижатии образца к диску.
Главными преимуществами обработки шлифов таким способом являются оздоровление условий труда вследствие отсутствия абразивной пыли, возможность равномерного съема металла, без преимущественного удаления одной из фаз, отсутствие наклепанного слоя на поверхности шлифа и сокращение времени приготовления шлифа.
Электрохимическое полирование и травление.
Метод электрохимического полирования, при котором образец в качестве анода помещают в электролитическую ванну, находит все более широкое применение. Состав электролита (растворы кислот), материал катода (свинец, медь, цинк, алюминий и т.д.) и плотность тока на аноде (образце) зависят от полируемого материала. На сегодняшний день данные по электрохимическому полированию и травлению большинства используемых в технике металлов и сплавов достаточно широко представлены в справочной литературе.
При пропускании тока через электрохимическую систему все неровности, оставшиеся после шлифовки образца, в процессе анодного растворения сглаживаются, и образец приобретает ровную зеркальную поверхность. При электрополировании возможно удаление слоя со структурой, искаженной в результате наклепа при механической обработке поверхности.
Электрохимическое полирование имеет свои особенности, связанные со значительным выделением тепла в
24
ходе процесса и разогревом электролита. Также необходимо учитывать возможное воздействие электролита на материал электролитической ванны.
Смешивание кислот может сопровождаться сильным разогревом электролита, поэтому необходимо соблюдать меры предосторожности. Пользоваться электролитом можно после его охлаждения до комнатной температуры. Электролизные ванны изготавливают из кислотоупорных материалов. Неподогреваемые ванны делают из стекла, фарфора, фторопластов; подогреваемые – из нержавеющей стали. Если в состав электролита входит плавиковая кислота, то для электролиза используют ванночки из материалов, не подверженных действию плавиковой кислоты (винипласт, эбонит). Катоды вырезают из листового металла: меди, свинца, нержавеющей стали и др. Длительность электрополирования зависит от целей исследования и определяется скоростью съема металла (7-10 мкм/мин). В процессе электрополирования происходит разогрев электролита, что снижает его полирующую способность и усиливает травление. Необходимо либо периодически охлаждать электролит, либо помещать сосуд с электролитом в более емкий сосуд с проточной водой. Погружение шлифа в электролит и его удаление проводят под напряжением. Для равномерного протекания процесса полирования электролит перемешивают механической или электрической мешалкой. По окончании полирования шлиф необходимо промыть в проточной воде и высушить (лучше горячим воздухом и мягкой неворсистой тканью). У отработанного электролита полирующая способность заметно снижается, что легко устанавливается при визуальном наблюдении за качеством получаемой поверхности.
Электролитическое полирование сварных соединений. При разработке оптимальных параметров электрополирования сварных соединений важной характеристикой является длительность процесса электролиза. Для получения
25
сопоставимых результатов на ряде исследуемых образцов необходимо строго соблюдать место вырезки образца для исследований. В противном случае размеры тех же самых дефектов на поперечном шлифе зоны соединения даже в пределах одного образца могут оказаться несравнимыми.
Чрезмерное |
увеличение |
продолжительности |
электрополирования |
сварных соединений видоизменяет |
первоначальную форму дефектов в исследуемом сечении. Подобная картина формоизменения дефекта является результатом попадания в поле зрения нижерасположенных участков непроваров и свидетельствует об эффекте «переполирования».
Электролитическое травление, как уже отмечалось,
осуществляется с учетом особенностей материала образца. Так для травления титановых сплавов наиболее универсальными для выявления микроструктуры являются реактивы, в состав которых входит плавиковая кислота, а для большинства сплавов на основе железа - азотная кислота. В то же время во многих случаях в электролите одного состава можно полировать различные металлы, применяя индивидуальные режимы полирования.
В каждом конкретном случае при травлении шлифов из сплавов следует несколько изменять процентное содержание той или другой составляющей реактива, учитывая его воздействие при травлении. Составляющие реактивов влияют по-разному. Например, плавиковая кислота оказывает травящее действие; азотная кислота придает поверхности блеск, так как растворяет окисные пленки; глицерин используют в качестве ингибитора, замедляющего травление.
Выбор конкретного травителя, условий травления определяется целью исследований, характеристиками материала, квалификацией исследователя. В общем случае можно руководствоваться рекомендациями по выбору травителей и условиям травления, приводимым в различной справочной литературе.
26
Методика химического травления.
Травление может быть общим (при этом выявляется вся микроструктура) и избирательным (выявляется какая-либо деталь микроструктуры).
Для составления травителей в качестве растворителей применяют водопроводную или дистиллированную воду, различные спирты. Поскольку водопроводная вода содержит минеральные соли, она является слабым электролитом и оказывает влияние на скорость процесса травления. Чем более концентрированный раствор приготовляют для травления, тем меньшее значение имеет состав воды. В качестве растворителя применяют спирты: этиловый, метиловый, амиловый, бутиловый, пропиловый, глицерин, этиленгликоль, а также ацетон. Выбор растворителя зависит от состава травителя и сплава. Если нужна высокая скорость травления и контрастность изображения, применяют в качестве растворителя воду. Для получения большей четкости при выявлении мелких деталей микроструктуры и уменьшения их окисления при травлении и сушке применяют в качестве растворителя спирты.
Все применяемые для составления реактивов вещества должны быть высокой степени чистоты для получения качественной картины микроструктуры.
Обычно травители применяют при комнатной температуре. Если надо ускорить процесс травления, то их подогревают до определенной температуры (в зависимости от состава).
Для составления травителей обычно применяют кислоты (азотная, пикриновая, серная, хромовая, соляная, плавиковая, уксусная, щавелевая, муравьиная), щелочи (едкий калий и едкий натр), соли (окислители и восстановители). Кислоты, как правило, оказывают разъедающее действие на металл. Окислители вводят в травитель для образования окисных пленок различного цвета, по которому узнают фазу. Восстановители обычно добавляют в травитель для уменьшения
27
интенсивности растворения и для выделения на определенных фазах сплава окрашенных осадков, по цвету которых узнают некоторые фазы.
Выявление микроструктуры металла при химическом травлении проводят различными способами: погружением образца в травитель, втиранием травителя в поверхность шлифа и смачиванием поверхности шлифа травителем.
При травлении первым способом шлиф погружают в ванночку с травителем. Если травление кратковременное (несколько секунд), то шлиф берут пинцетом и опускают полированной поверхностью вниз, не касаясь дна ванночки. Если травление занимает более длительное время или одновременно травят несколько шлифов, то их погружают в ванночку с реактивом полированной поверхностью вверх. В процессе травления ванночку слегка покачивают. При этом поверхность шлифа взаимодействует со свежим раствором и с нее удаляются продукты травления. Толщина слоя травителя у поверхности шлифа должна быть около 5 мм.
Второй способ травления применяют, если при действий травителя на поверхности шлифа образуются пленки, препятствующие дальнейшему выявлению структуры. В этом случае поверхность шлифа протирают, слегка нажимая ватным тампоном, обильно смоченным реактивом. Механическое воздействие способствует удалению образовавшихся пленок. Травление проводят в резиновых перчатках.
Если травитель очень быстро выявляет микроструктуру, то несколько его капель пипеткой наносят на поверхность шлифа, после чего образец промывают.
Продолжительность травления зависит от химического состава материала и вида термической обработки, концентрации травителя и его химической активности, от увеличения, при котором будет проводиться изучение микроструктуры (чем больше увеличение, тем меньше длительность травления). Время травления подбирают
28
основываясь на справочных данных и корректируя их экспериментально.
Качество травления проверяют под микроскопом при том же увеличении, при котором будет производиться дальнейшее изучение шлифа. Если поверхность шлифа, видимая под микроскопом, очень светлая, нет четкости контуров структуры, то шлиф недотравлен, и производят повторное травление. Если же поверхность шлифа, видимая под микроскопом, темная, с широкими темными границами структурных составляющих, то шлиф перетравлен. В этом случае его переполировывают, чтобы снять поверхностный слой, и повторно травят. Если при полировании в течение 1—2 мин. следы травления не удаляются, то поверхностный слой металла надо снять шлифованием, а длительность повторного травления уменьшить.
После окончания травления, чтобы избежать окисления шлифа, его очищают от остатков травителя и продуктов травления. Для этого шлиф сначала промывают проточной водой, а затем протирают спиртом и высушивают. Очень чистая поверхность шлифа получается при последовательном промывании следующими растворами: 50 % ацетона, 50 % метилового спирта и 0,5 % лимонной кислоты, 50 % ацетона и 50 % метилового спирта; чистым бензолом.
После промывания шлиф тщательно высушивают либо струей теплового воздуха, либо прикладыванием фильтровальной бумаги.
Для микроскопического исследования структуры металлов используются металлографические микроскопы, которые рассматривают предметы в отраженном свете и предназначены для исследования строения непрозрачных предметов (металлов, пластмасс, металлокерамики и т.д.) при увеличениях до 2000 крат. При визуальном наблюдении рекомендуется применять желто-зеленые фильтры, наиболее чувствительные для человеческого глаза. Исследование
29
структуры под микроскопом может проводиться в светлом и темном поле, иногда в поляризованном свете.
При исследовании в светлом поле весь пучок лучей света поступает на поверхность микрошлифа, отражается от нее, проходит через оптическую систему микроскопа и попадает в глаз исследователя.
Для исследования в темном поле включаются специальная линза для темного поля, диафрагма, пропускающая пучок в виде светового кольца, и устанавливается эпиобъектив, имеющий параболическое зеркало, назначение которого – сконцентрировать кольцевой пучок лучей и направить его под углом на поверхность микрошлифа. Это дает возможность более четко выявить отдельные, в основном выступающие над поверхностью микрошлифа структурные составляющие, которые обладают лучшей отражательной способностью, остальные участки поверхности будут рассеивать лучи и выглядят темными. Обычно исследование в темном поле применяется как дополнительное к исследованию в светлом поле.
Для исследования в поляризованном свете в систему микроскопа включают поляризатор и анализатор, которые обеспечивают волновые колебания света в одной определенной плоскости. Поляризованные лучи отражаются от различных структурных составляющих по-разному и, следовательно, выявляют их (особенно неметаллические включения).
Микроанализ позволяет проводить не только качественное исследование структуры металла. Он используется и для количественной оценки структурных составляющих, например для измерения величины зерна, глубины слоя и т.д. При определении конкретных размеров используются объект–микрометры и окуляр–микрометры.
Объект-микрометр – стеклянная или металлическая пластинка, на которую нанесена шкала длиной в 1 мм с ценой деления 0,01 мм.
30
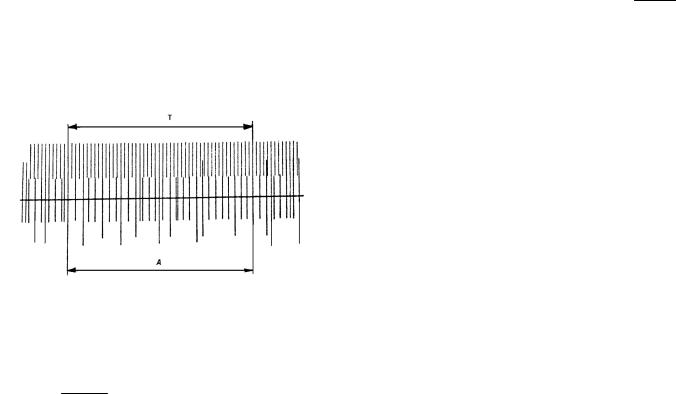
Окуляр–микрометр отличается от окуляра лишь наличием стеклянной пластинки со шкалой, имеющей 100 делений.
Для определения цены деления окуляра–микрометра объект-микрометр устанавливается вместо шлифа на предметный столик и шкалы обоих микрометров совмещаются (рис. 3.1).
Рис. 3.1. Совмещение шкалы объект – микрометра со шкалой окуляр - микрометра
После совмещения некоторых участков шкал проводится вычисление цены деления окуляра по формуле
Цок Цоб Т ,
А
где Цоб – цена деления объект-микрометра, равная 0,01
мкм;
Т – число делений объект-микрометра, совпавших с числом делений окуляр-микрометра А.
Зная цену деления окуляр-микрометра, можно аналогичным образом измерить интересующий нас микрообъект, помещая его вместо объект–микрометра на предметный столик.
Например, средняя величина зерна d3 исследуемого металла или сплава может быть вычислена следующим образом:
31
d3 Цок N , |
|
n |
|
где Цок – цена деления окуляр–микрометра; |
|
N – число делений |
окуляра, в границах которых |
подсчитывалось количество зерен;
n – среднее число зерен, уместившихся на отрезке длиной ЦокN при горизонтальном и вертикальном положениях шкалы окуляр–микрометра.
Следует помнить, что оптический микроскоп не является аппаратом, который может обнаружить кристаллик любого размера. Величина 0,6 мкм, характеризующая разрешающую способность оптического микроскопа, теоретическая. Практически, из-за несовершенства оптической системы микроскопа, она близка к 1 мкм. Таким образом, детали структуры с размерами менее 1 мкм не будет разрешаться микроскопом.
Лабораторная работа № 4
МЕТОДИКА ИССЛЕДОВАНИЯ ТЕПЛОВЫХ ПРОЦЕССОВ
Цель работы
1.Изучить методику измерения и контроля высоких температур.
2.Приобрести навыки изготовления и калибровки термопар, их использования.
3.Провести согласно методике экспериментальную часть (термический анализ).
4.Обработать экспериментальные данные и проанализировать полученные результаты.
Оборудование и материалы Хромелевая и алюмеливая проволоки (возможно
использование других материалов), образцы из легкоплавких
32
сплавов и материалов, электропечь, потенциометр КСП-4, милливольтметр, термометры, керамические и металлические тигли.
Задание
1.Изучите методику изготовления и проверки термопар.
2.В соответствии с заданием преподавателя выберите тип термопары и изготовьте её.
3.С помощью методических указаний и справочной литературы выполните калибровку изготовленной термопары..
4.Используя изготовленную термопару проведите термический анализ процесса кристаллизации заданного сплава.
Содержание отчета
1.Краткие сведения о методах измерения температур
ииспользуемых термоприемниках.
2.Методика изготовления термопары, результаты её проверки и калибровки. При необходимости калибровочные кривые.
3.Полученные графики (кривые охлаждения) и обработка результатов измерений.
Измерения высоких температур.
Многие технологические процессы в различных отраслях промышленности ведутся при температурах, превышающих 1000 С. Качество выпускаемой продукции во многом зависит от правильного теплового режима технологического процесса, протекающего в большинстве случаев в узких пределах температур. Знание температур часто позволяет правильно осмыслить результаты исследований, правильно их интерпретировать, а наличие средств измерения температур во многих случаях стимулирует развитие новых направлений в науке и технике.
Чрезвычайно большое разнообразие условий производства, различие требований к точности и диапазону
33
измерений не позволяют создать универсальные методы и средства измерений.
Температуру как физическую величину измерить непосредственно невозможно. Для этой цели в термоприемниках используют какое-либо термометрическое свойство тела, связанное с его температурой функциональной зависимостью.
К таким термометрическим свойствам тел относятся:
а) механические (тепловое расширение газа, жидкости, твердого тела, изменение упругих свойств газа и др.);
б) тепловые (энтальпия, фазовые переходы и др.); в) электрические (электрическое сопротивление,
термоэлектрический эффект и др.); г) излучательные (тепловое излучение, отношение
монохроматических яркостей и др.).
Для измерения высоких температур используют в основном два метода: бесконтактный и контактный.
Ктермоприемникам, в которых используют бесконтактный метод, относятся всевозможные пирометры: радиационные, оптические (яркостные), фотоэлектрические (яркостные отношения), спектрометры и т.д.
Ктермоприемникам, в которых используют контактный метод, относятся термометры сопротивления, термоэлектрические (первичным измерительным преобразователем является термопара), газовые, жидкостные и т.д.
Применение тех или иных термоприемников зависит от конкретных требований контроля процесса, особенностей объектов измерения, диапазона измеряемых температур и т.д.
Бесконтактные методы применяют главным образом при измерении температуры движущихся объектов, например слитков, слябов или полос при прокатке, струи жидкого металла при разливке, а также для измерения температуры в закрытых объектах (в вакуумных печах) и в других случаях,
34

когда измерение контактными методами затруднено, особенно при температурах выше 2000 С.
Контактные методы применяются, когда может быть осуществлен непосредственный контакт между термоприемником и объектом измерения, например при измерении температуры жидкой стали в конверторах, мартеновских, электродуговых, индукционных печах, ковшах; в закрытых малодоступных объектах, в которых тепловые процессы осуществляются в воздушных, нейтральных средах, водороде или вакууме; в некоторых движущихся и вращающихся объектах; при сравнительно быстротекущих реакциях – взрывах, газах, движущихся с большими скоростями, и т.п.
Оба метода измерения имеют свои преимущества и недостатки.
Бесконтактный метод незаменим при длительных измерениях температур выше 2000-2500 С. При этом во многих случаях различные коэффициенты излучения измеряемых тел требуют введения поправок на нечерноту излучения, а если она неизвестна или изменяется в процессе измерения, то возникают дополнительные погрешности, исключить которые часто не представляется возможным.
При контактном методе измерения на показания первичных измерительных преобразователей (термоприемников), работа которых основана на электрических свойствах, в большей степени влияют качество теплового контакта между телом и чувствительным элементом приемника, а также точность монтажа, последнего на объекте, что предопределяет снижение или исключение отвода тепла по термоприемнику, а следовательно, уменьшение систематических погрешностей, вызванных этим явлением.
Термопары и термоэлектрические термометры позволяют осуществлять измерения в очень широком диапазоне температур от 270 до 3000 С; достигать высокой точности измерения; передавать результаты измерений (т.э.д.с.) на
35
значительные расстояния и осуществлять автоматическую регистрацию показаний; производить недорогие по стоимости измерения вследствие невысокой цены самих термометров.
Термоэлектродвижущая сила (т.э.д.с.), возникающая в месте спая двух проводников, зависит от природы этих проводников, температуры спая и не зависит от распределения температуры вдоль проводников при условии их полной однородности по длине в смысле химического состава и характера механической обработки.
Результирующая т.э.д.с. в замкнутой цепи, состоящей из различных проводников, является суммой всех т.э.д.с., возникающих в местах спаев, находящихся при различных температурах.
Т.э.д.с. зависит только от температуры спая двух проводников. Однако общий случай, т.е. изменение электродвижущей силой в зависимости от разности температур двух спаев, может быть также использован в технике измерения температур (дифференциальные термопары).
Присутствие промежуточного проводника f не влияет в данном случае на т.э.д.с. всей цепи. Подобным же путем можно было бы включить не одно, а несколько промежуточных звеньев при условии, что все они будут находиться при одинаковой температуре t1. Это обстоятельство имеет большое практическое значение при некоторых способах калибрования термоэлементов и при изготовлении термопар спаиванием между собой двух проволок промежуточным припоем.
Величина т.э.д.с. зависит, как уже было сказано, от природы спаиваемых металлов. Здесь экспериментатору нужно дать себе отчет в том, какая точность измерений ему требуется и какова чувствительность инструмента, который он будет применять для отсчета.
Чувствительность какой-либо пары металлов dE dt
36

выражается обычно в микровольтах* или в милливольтах на градус.
Чувствительность |
различных |
пар |
dE |
далеко |
|
dt |
|||||
|
|
|
|
неравномерна во всем интервале температур, при которых пара применяется. Особенно опасны в этом отношении такие сплавы, т.э.д.с. которых, вследствие происходящих внутренних процессов, может не только неравномерно нарастать с повышением температуры, но и иметь в некотором интервале отрицательный знак и затем снова приобретать положительное значение. Во всяком случае, если исследователь подбирает термопару сам, он легко это обнаружит предварительным испытанием проволок при помощи гальванометра и горелки.
Основные требования к термоэлектродам.
1. Температура плавления менее тугоплавкого термоэлектрода термопары должна превосходить максимальную измеряемую температуру примерно на 200-300С. При температурах, близких к точкам плавления термоэлектродных материалов, в них может возникать форсированное перерождение структуры и состава вследствие рекристаллизации, миграции составляющих и других физикохимических процессов. Приводящих к быстрому разрушению электродов и возникновению погрешностей при измерениях температуры.
2. Материал термоэлектродов должен обладать достаточно высоким сопротивлением разрыву для обеспечения надежной работы термоэлектродов при возможных частых механических и температурных воздействиях, а также достаточным запасом пластичности для обеспечения возможности их пластической деформации от слитков вплоть до тонких проволок и для погашения растягивающих
* 1 микровольт = 1 10-6 вольт, обозначается мкв. 1 милливольт = 1 10-3 вольт, обозначается мв.
37
напряжений, которые возникают из-за различия коэффициентов температурного расширения керамики и термоэлектродов.
3.Проволочные термоэлектроды должны обеспечивать возможность выполнения надежного рабочего спая (сваркой, скруткой, узлом).
4.Термоэлектроды должны обладать высокой химической и физической однородностью (гомогенностью), что обеспечивает их более длительную и стабильную работу в термопарах (с минимальной погрешностью измерений). Термоэлектрическая однородность проволок определяется, прежде всего, их химической однородностью. Проволоки из чистых металлов и монофазных сплавов (твердых растворов) более гомогенны, чем из многофазных сплавов, поэтому их предпочитают в качестве электродов.
5.Термоэлектроды должны длительно сохранять стабильность физических свойств после многократных повторных предположительных пребываний в средах с предельно допустимыми высокими температурами.
Основные типы термопар.
В очень большом диапазоне температур, от 100 до 1500С, хорошо применять платино-платинородиевую термопару, обладающую, правда, небольшой чувствительностью, но зато чрезвычайно стойкую в температурном отношении. Этой термопарой можно уверенно пользоваться для измерения температур вблизи 1000 С.
Для более низких температур, порядка 600-800 С, выгоднее применять термопары из специальных сплавов никеля и хрома.
Будучи очень стойкими до 900 С, такие термопар обладают т.э.д.с. в 4-6 раз большей, чем платиноплатинородиевые. Это обстоятельство нужно иметь в виду при наличии большого количества термопар и гальванометров в лаборатории. Неопытный лаборант может легко спутать эти
38