
теор / Теплообменное оборудование предприятий
.pdf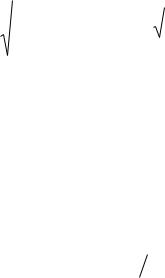
Это условие равновесия можно выразить в виде критериальной зависимости
|
|
|
|
|
|
|
|
|
|||
|
4 g г |
|
|
|
|
|
|
||||
Fe d 3 |
|
3 Reвит2 |
|
, |
(7.9) |
||||||
|
|||||||||||
|
|
3 2 |
|
г |
|
|
|
|
|
||
|
|
г |
|
|
|
|
|
|
где Fe – критерий Федорова; Reвит – критерий Рейнольдса при скорости, равной скорости витания частицы; d – диаметр капли, м;
и г – плотность капли и газа, кг/м3; г – кинематическая вязкость газа, м2/с. Определив при данном диаметре частицы критерий Fe по графику на рис. 7.7, находят соответствующее значение Reвит , по которому определяют скорость витания частицы
Wвит Reвит г d . |
(7.10) |
7.3. Расчет скруббера с насадкой
При противоточном движении газа и жидкости в насадочных скрубберах по мере возрастания скорости наблюдаются четыре характерных режима движения потоков: пленочный, промежуточный, турбулизации и эмульгирования.
В режиме эмульгирования интенсивность тепло- и массообмена достигает максимального значения, одновременно происходит накапливание жидкости и, когда вся насадка затапливается жидкостью, происходит захлебывание и начинается выброс жидкости из колонны. При проектировании скрубберов принимают рабочую скорость Wг
несколько меньше скорости эмульгирования Wэ
|
|
Wг (0,80 0,85) Wэ , |
м/с . |
|
|
(7.11) |
||||||||
|
Скорость газов, соответствующая оптимальному режиму работы |
|||||||||||||
скруббера, определяется по формуле |
|
|
|
|
|
|
|
|
|
|||||
|
|
Re' 0,045 Ar 0,57 |
|
L |
|
|
, |
|
|
(7.12) |
||||
|
|
|
G |
|
|
|
||||||||
|
|
|
|
|
|
|
|
|
|
|
|
|
||
|
|
4 V W |
|
|
d3 |
|
|
( |
|
)g |
|
|||
где |
Re' |
св опт |
|
г |
; Ar |
э |
|
|
|
г |
|
г |
|
. (7.13) |
|
|
|
|
|
|
|
|
|
||||||
|
|
г S |
|
|
|
|
|
|
2 |
|
|
|
||
|
|
|
|
|
|
|
|
|
|
|
|
|||
|
|
|
|
|
|
|
|
|
|
|
г |
|
|
|
|
|
|
|
|
131 |
|
|
|
|
|
|
|
|
|

|
|
В этих формулах: Wопт – оптимальная скорость газа, м/с; и |
||||||
|
г |
– плотность жидкости и газа, кг/м3; |
|
г |
– вязкость газа, Па с ; |
|||
|
|
|
|
|
|
|
||
L – расход газа, кг/с; |
G – расход воды, кг/с. |
|
||||||
|
|
Величина dэ |
называется |
эквивалентным |
(гидравлическим) |
|||
диаметром насадки и рассчитывается |
|
|
|
|
||||
|
|
|
dэ 4 Vсв S |
, м , |
(7.14) |
|||
где |
Vсв – свободный объем насадки, м3/м3 ; S – поверхность насадки |
|||||||
в единице объема, м2/м3. |
|
|
|
|
|
|||
|
|
Оптимальная скорость газа рассчитывается из числа Re' |
||||||
|
|
|
Wопт Re' г dэ г . |
(7.15) |
||||
|
|
Активный объем скруббера определяется по формуле |
||||||
|
|
|
B Q k t S |
, м3 , |
(7.16) |
|||
где |
Q – количество теплоты, передаваемое в скруббере, Вт; k – ко- |
|||||||
эффициент теплопередачи насадки, Вт/(м2 °С); t |
– средняя разность |
|||||||
температур теплоносителей, °С; |
– |
коэффициент смачиваемости |
(отношение поверхности смоченной насадки к полной ее поверхности).
Коэффициент смачиваемости рассчитывается |
|
||||
3 |
|
|
|
|
|
S f H |
w |
|
, |
(7.17) |
|
|
|
|
|
|
где S – поверхность насадки в единице объема, м2/м3 ; Hw – плотность орошения, м3/(м2 ч) .
Плотность орошения определяется по формуле
|
|
H |
w |
4 G D2 |
, |
|
|
|
(7.18) |
||||||
|
|
|
|
|
|
|
|
|
|
|
|
|
|
||
где D – диаметр скруббера, м, который рассчитывается |
|
|
|
|
|||||||||||
|
|
D |
|
|
|
|
. |
|
|
|
|
|
|||
|
|
|
4 L Wг г |
|
|
|
(7.19) |
||||||||
Значения функции плотности орошения |
Таблица 7.1. |
||||||||||||||
Hw , м3/(м2 ч) . |
1 |
2 |
|
|
4 |
|
6 |
8 |
10 |
20 |
|
40 |
60 |
|
|
f Hw |
24 |
15 |
|
|
9,8 |
|
7,5 |
6,6 |
6,0 |
4,8 |
|
4,2 |
3,8 |
|
|
|
|
|
|
|
|
|
132 |
|
|
|
|
|
|
|
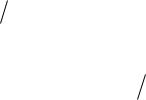
Коэффициент теплопередачи насадки можно определить по формуле Н.М, Жаворонкова
|
Ki 0,01 Re0,7 Re0,7 |
Pr0,33 |
, |
(7.20) |
|
|
г |
ж |
г |
|
|
где Ki k dэ |
г – критерий Кирпичева. |
|
|
|
|
Определив активный объем насадки В рассчитывают ее высоту |
|||||
|
H 4 B D2 |
, м |
|
|
(7.21) |
7.4. Расчет деаэратора
Целью расчета является определение необходимой поверхности контактирования пара со струйками воды, что обеспечивается установкой определенного числа тарелок в деаэраторной колонке.
Поверхность контактирования рассчитывается на основе совместного решения уравнения теплового баланса (1.6) и уравнения теплопередачи (1.4). Коэффициент теплопередачи k принимается в
пределах 8000–10000 Вт/(м2 °С), температурный напор рассчитывается как среднелогарифмический по формуле (1.9) в соответствии со схемой (в) на рис. (1.5).
После преобразования выражение для расчета поверхности контактирования принимает вид
|
|
G2 Cp |
|
t |
н |
t' |
|
2 |
|
|
|
|
F |
|
|
lg |
|
2 |
, м |
|
, |
(7.22) |
|
|
k |
tн t"2 |
|
||||||||
|
|
|
|
|
|
|
|||||
где |
G2 – расход воды, кг/с; Cp – теплоемкость воды, Дж/(кг°С); |
||||||||||
tн |
– температура насыщения, °С; |
t'2 |
и t"2 |
– температура воды на |
входе и выходе, °С.
Затем по формуле С.Ф. Копьёва определяется поверхность одной струйки
|
|
|
0,75 |
|
2 |
|
|
|
L |
|
|
|
|||
f 4,2 do h |
|
|
1 |
|
|
, м , |
(7.23) |
|
|
||||||
|
|
1 |
|||||
|
|
|
|
|
|
|
|
|
h |
|
|
|
|
||
|
|
|
|
|
|
где do 4 6 мм – диаметр отверстий;
h 40 50 мм – высота борта тарелки;
L 400 500 мм – высота отсека деаэраторной колонки (рис. 7.8).
133

Количество струек, обеспечивающих поверхность контактирования, составит
m F f . |
(7.24) |
Элементарный расход |
воды, |
проходящий через одно отверстие, составит
G
Рис. 7.8. К расчёту деаэратора
Скорость истечения определяется по формуле
W |
|
|
|
2 g h , м/с , |
(7.26) |
||
где 0,65 0,7 – коэффициент расхода; g – ускорение свободно- |
го падения, м/с2 ; h – высота борта, мм.
Число отверстий в одной тарелке (число струек в одном отсеке) составит n G2 G , число тарелок Z m
n .
Размеры тарелок определяются следующим образом. Площадь
тарелки составляет |
. |
|
Ф 0,785 D2 D2 |
(7.27) |
|
вн |
|
|
Исходя из расположения отверстий по вершинам равностороннего треугольника, эта же площадь определяется
|
Ф t 2 sin n тр . |
(7.28) |
||||||||||
Приравнивая выражения 7.27 и 7.28, получим |
|
|||||||||||
|
|
|
|
|
|
|
|
|
|
|
|
|
D |
|
|
t2 |
sin n |
d2 |
, м . |
(7.29) |
|||||
|
|
|
тр |
0,785 |
||||||||
|
|
|
|
|
|
|
|
|||||
|
|
|
|
|
|
|
|
|
|
|
|
|
Величина Dвн определяется из уравнения расхода |
||||||||||||
|
|
|
|
|
|
|
|
|
|
|
|
|
Dвн |
|
|
|
|
|
4 Dп |
|
|
, м , |
(7.30) |
||
|
|
|
|
|
||||||||
|
|
|
|
Wп п |
|
п – плотность |
||||||
где D – расход пара, кг/с; |
Wп – скорость пара, м/с; |
пара, кг/м3.
134

Скорость пара принимается из условий предотвращения уноса воды и составляет 15–20 м/с.
Активная высота колонки составляет H L Z 1 .
Если в деаэратор поступает несколько смешивающихся потоков воды, то в качестве расчетной принимается средняя температура
tвср |
t1 G1 t2 G2 tn Gn |
. |
(7.31) |
|
|||
|
G1 G2 Gn |
|
В этом случае поверхность контактирования рассчитывается
|
Gi Cp |
|
t |
н |
tср |
|
|
F |
|
lg |
|
в |
. |
(7.32) |
|
|
|
|
|
||||
|
k |
|
tн t"2 |
|
Более точным является метод расчета ЦКТИ, в соответствии с которым определяется подогрев воды на каждой тарелке
|
t |
н |
t |
к-1 |
|
L 0,5 |
|
0,3 |
|
|
|
lg |
|
|
|
|
|
W |
|
, |
(7.33) |
||
|
|
|
|
|
|
||||||
tн tк |
0,0586 |
|
|
|
|||||||
|
do |
|
|
|
|
где tк-1 – температура воды на предыдущей тарелке (температура воды, поступающей в данный отсек); tк – конечная температура во-
ды на тарелке (температура воды, выходящей из данного отсека). Обозначив правую часть выражения (7.33) буквой А, его можно
записать следующим образом:
|
tн tк-1 tн tк 10А . |
(7.34) |
Откуда |
tк tн tн tк-1 10А . |
(7.35) |
Рассчитанное число тарелок должно обеспечивать требуемую величину недогрева.
Этот метод позволяет определить число отверстий в тарелке с учетом конденсата, полученного в данном отсеке.
Более подробные сведения о конструкциях и методах расчёта деаэраторов приведены в технических материалах [28].
135
Выводы
В разделе 7 представлены смесительные теплообменники, которые нашли широкое применение для очистки продуктов сгорания (скрубберы) и подготовки питательной воды (деаэраторы), а также для увлажнения или осушки, подогрева или охлаждения воздуха в системах кондиционирования. Приведены особенности расчёта скруббера без насадки и с насадкой.
Вопросы для самоконтроля
1.Опишите сферу применения смесительных теплообменников.
2.Чем отличается полый скруббер от насадочного?
3.Какие типы насадок используются в смесительных аппаратах?
4.Для чего предназначен деаэратор?
5.Перечислите типы деаэраторов?
136
ГЛАВА 8. РАСЧЁТ НА ПРОЧНОСТЬ ЭЛЕМЕНТОВ ТЕПЛООБМЕННОГО ОБОРУДОВАНИЯ
8.1. Материалы и области их применения
Расчёт элементов и узлов на прочность является неотъемлемой частью инженерного расчета любого теплообменного или энергетического оборудования, обеспечивающего условия его надёжной и безопасной работы, и регламентируется утверждёнными нормами [29,30].
Элементы и узлы оборудования должны выдерживать напряжения, возникающие от внутреннего или внешнего давления, от собственной массы конструкции, включая массу находящейся в аппарате рабочей среды, от термических деформаций.
При проектировании аппаратов производят выбор конструкционных материалов, а затем расчётом определяют размеры частей, узлов, деталей, которые обеспечивают их прочность в процессе эксплуатации и при пробных испытаниях.
Существует два основных метода расчёта на прочность [31]: по предельным напряжениям и по предельным нагрузкам.
В первом методе пределом несущей способности конструкции принимают достижение любым сечением какой–либо её детали предела текучести, т.е. начала пластической деформации. В расчёте по предельным нагрузкам за опасное принимают напряжение, вызывающее общую пластическую деформацию всего нагруженного узла. Величина максимально допускаемой силы при расчёте по предельным нагрузкам всегда больше, чем при расчёте по предельным напряжениям.
Метод расчёта по предельным нагрузкам применим для пластических материалов, малоуглеродистых сталей, меди и её сплавов, алюминия и т.п., из которых изготавливают большинство теплообменных аппаратов. Этот метод позволяет точнее учитывать несущую способность конструкции, но неприменим для расчёта деталей из хрупких материалов (закалённые стали, серые чугуны и др.), разрушение которых наступает без заметной пластической деформации. Такие детали рассчитывают по методу предельных напряжений.
При определении допускаемых напряжений в сосудах, работающих под давлением, пользуются коэффициентом запаса прочности, правильный выбор которого не только обеспечивает безопасную работу оборудования, но и способствует уменьшению расхода конструкционных материалов.
137
Вэнергетике при изготовлении конструкций нашли применение стали различных марок. Стали классифицируются по химическому составу, назначению, способу выплавки.
По химическому составу стали делят на углеродистые и легированные. Углеродистой сталью называется сплав железа с углеродом с содержанием углерода до 2 %. По содержанию углерода стали подразделяют на малоуглеродистые (до 0,25 % С), средне– углеродистые (0,25 – 0,6 % С) и высокоуглеродистые (до 2 % С). Кроме железа и углерода эти стали содержат марганец (до 0,8 %), кремний (до 0,4 %), а также вредные примеси: серу (до 0,05 %) и фосфор (до 0,05 %).
Взависимости от содержания легирующих элементов стали делят на три группы: низколегированные – суммарное содержание легирующих добавок менее 2,5 %, среднелегированные – от 2,5 до 10 %
ивысоколегированные – более 10 %. Кроме указанных выше, легирующими элементами являются хром, никель, титан, алюминий, вольфрам, молибден, ванадий и др.
По назначению стали делятся на три основные группы: конструкционные (углеродистые и низколегированные); инструментальные
истали с особыми свойствами – жаропрочные, коррозионно-стойкие
иокалиностойкие.
По способу выплавки различают стали кислородно-конвертер- ные, мартеновские и электростали.
Работоспособность материала в конструкции характеризуется комплексом свойств, таких как прочность, надёжность и долговечность. Прочность металла – способность сопротивляться деформации при приложении нагрузки. Надежность – способность материала кратковременно работать вне расчётной ситуации. Долговечность – время, при которой материал способен эксплуатироваться в соответствии с заданными техническими условиями.
Для оценки механических свойств металла используют два параметра: прочность и пластичность. Основным критерием прочности является временное сопротивление разрыву в , представляющего
собой отношение максимальной силы, которую способен выдержать образец, к его начальной площади поперечного сечения. Основным критерием пластичности является относительное удлинение при растяжении.
Углеродистая сталь обыкновенного качества разделяется на три группы в зависимости от назначения: А – по механическим свойст-
138
вам; Б – по химическому составу; В – по механическим свойствам и по химическому составу.
Углеродистые стали различают по качеству – обыкновенного качества и качественные, по степени раскисления – кипящие, полуспокойные и спокойные.
Марки углеродистых сталей имеют буквенно-цифровое обозначение: буквы Ст обозначают "сталь", цифры от 0 до 6 – условный номер марки в зависимости от химического состава и механических свойств. Буква А в обозначении группы стали не ставится.
Для обозначения степени раскисления к обозначению марки стали после номера добавляют индексы: кп – кипящая, пс – полуспокойная, сп – спокойная. Для обозначения категорий сталей в конце к обозначению марки добавляют цифровой номер соответствующей категории. Первую категорию в обозначении марки стали не указывают.
Для обозначения полуспокойной стали с повышенным содержанием марганца к обозначению марки стали после номера ставят букву Г.
Сталь углеродистая качественная в соответствии со стандартом выпускается 24 марок. В обозначении марки стали цифры показывают среднее содержание углерода в сотых долях процента. Сталь углеродистая и низколегированная для котлостроения и сосудов, работающих под давлением, маркируется так же, как и углеродистая обыкновенного качества, но в конце после цифрового обозначения содержания углерода ставится буква К.
Наименование легированных марок сталей и сплавов состоит из обозначения элементов и следующих за ним цифр. Цифры, стоящие после букв, указывают среднее содержание легирующего элемента в процентах, кроме элементов, присутствующих в стали в малых количествах. Цифры перед буквенным обозначением указывают среднее или максимальное содержание углерода в стали в сотых долях процента.
Химические элементы в марках стали обозначены следующими буквами: марганец – Г, кремний – С, хром – X, никель – Н, молибден – М, вольфрам – В, ванадий – Ф, титан – Т, алюминий – Ю, медь – Д, ниобий – Б, кобальт – К, бор – Р, фосфор – П, цирконий – Ц, селен – Е.
Области применения сталей и их назначение приводится в соответствии с [32] в табличной форме (табл. 8.1–8.4).
139
Таблица 8.1 Назначение углеродистых сталей обыкновенного качества
Марка |
Вид |
|
|
Назначение |
|
|
Предель- |
|||
стали |
поставки |
|
|
|
|
|
|
ная рабо- |
||
|
|
|
|
|
|
|
|
|
|
чая темпе- |
|
|
|
|
|
|
|
|
|
|
ратура, °С |
1 |
|
2 |
|
|
3 |
|
|
|
|
4 |
Ст 0 |
Листовой, |
Нерассчитываемые |
|
второ- |
– |
|||||
|
фасонный |
степенные элементы |
свар- |
|
||||||
|
и сортовой |
ных конструкций: настилы, |
|
|||||||
|
прокат |
|
обшивка и др. |
|
|
|
|
|
||
Ст 2 сп, |
Листовой, |
Малонагружаемые элементы |
300 |
|||||||
Ст 2 пс |
сортовой и |
конструкций, |
работающие |
|
||||||
|
фасонный |
при постоянных нагрузках и |
|
|||||||
|
прокат, |
|
положительных |
|
тем- |
|
||||
|
трубы |
|
пературах: до 150 °С (эле- |
|
||||||
|
|
|
|
менты котлов) и до |
|
|
|
|
||
|
|
|
|
300 °С (сосуды, трубопро- |
|
|||||
|
|
|
|
воды); газопроводы |
|
|
|
|
||
Ст 2 кп |
То же |
|
То же , но до 200 °С (сосу- |
200 |
||||||
|
|
|
|
ды, трубопроводы) |
|
|
|
|
||
|
|
|
|
|
|
|||||
Ст 3 сп |
Листовой, |
Несущие |
элементы |
конст- |
425 |
|||||
|
сортовой и |
рукций, |
работающие |
при |
|
|||||
|
фасонный |
температурах |
выше |
нуля |
|
|||||
|
прокат, |
|
(сталь групп А, Б, В); также |
|
||||||
|
трубы, |
по- |
работающие |
при |
|
пе- |
|
|||
|
ковки |
для |
ременных |
нагрузках |
(сталь |
|
||||
|
армирова- |
группы В категории 5) в ин- |
|
|||||||
|
ния |
желе- |
тервале температур от -40 до |
|
||||||
|
зобетон- |
+425 °С. Сосуды под давле- |
|
|||||||
|
ных |
кон- |
нием; трубопроводы пара, |
|
||||||
|
струкций |
воды, горючего газа при |
|
|||||||
|
|
|
|
температуре |
до |
200 |
°С |
|
||
|
|
|
|
(трубные элементы котлов), |
|
|||||
|
|
|
|
485 °С (сосуды) и |
300 |
°С |
|
|||
|
|
|
|
(трубопроводы); |
каркасы; |
|
||||
|
|
|
|
газопроводы |
|
|
|
|
|
140