
ЛабТММ_3
.pdf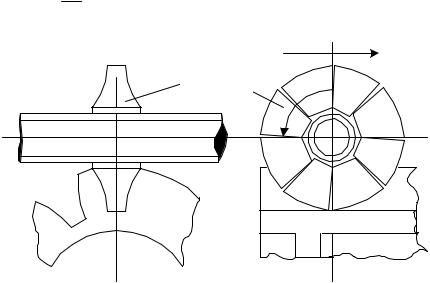
Лабораторна робота №8.
Моделювання процесу виготовлення зубчастих коліс способом обкочування.
Мета роботи: ознайомлення з технологією нарізання зубів способом обкочування; дослідження впливу зміщення інструмента на форму зубів.
Обладнання: лабораторний прилад, заготовка з картону, олівець, циркуль.
Теоретичні відомості.
Зубчасті колеса можна виготовляти різними способами: різанням, литвом, пластичною деформацією (штамповка або накатка). Існує два принципово різні способи нарізання зубів: копіювання та обкатка.
Метод копіювання полягає в тому, що за кресленнями ретельно побудованих профілів зубів виготовляється дискова фреза. Різальна кромка фрези має форму западини між зубами. Обертаючись, фреза переміщується в напрямку бічної твірної зубів. За кожний хід фрези вздовж осі колеса нарізається одна западина. Після проходження всієї западини фреза повертається у вихідне положення; колесо, що нарізається, повертається
на величину кута τ = 2zπ , де z - число зубів колеса та процес повторюється. На рис.18
показаний процес нарізання колеса дисковою фрезою.
Фреза |
Рис.18 |
В даній лабораторній роботі розглядатиметься другий спосіб. При цьому способі в основу геометрії інструмента покладено так зване твірне колесо або рейку, бічні поверхні зубів яких мають різальні кромки. Різальному інструменту та заготовці надається той відносний рух, який би мали два зубчастих колеса, що знаходяться у правильному зачепленні. Як інструмент використовують довбяк, черв’ячну фрезу та зубчасту рейку.
Довбяк (колесо-інструмент) виконує поступальний рух паралельно осі колеса, що нарізається. Одночасно колесу та довбяку надається обертовий рух з тим самим відношенням кутових швидкостей, якби довбяк та колесо знаходилися у зачепленні. Практично процес довблення відбувається не безперервно, а має ряд послідовних операцій, які складаються з руху довбяка вверх та вниз, повороту колеса, що нарізається, тощо. При цьому профіль зуба виглядає як обвідна всіх положень різальної кромки довбяка.
При виготовленні зубчастого колеса за допомогою інструментальної рейки рух інструмента відбувається у вертикальному напрямку зворотно-поступально, паралельно
28
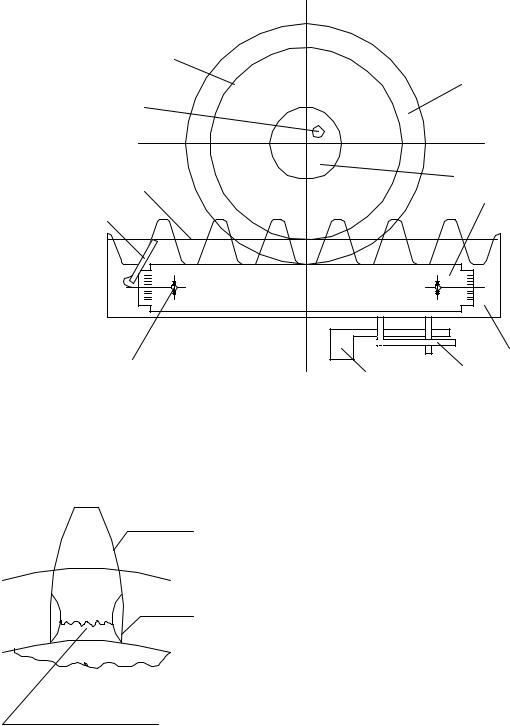
осі колеса, що нарізається. Заготовка має подвійний рух в горизонтальній площині: обертається навколо своєї осі та одночасно переміщується вздовж рейки. Процес виконується на спеціальних зуборізних верстатах.
Замість рейки може бути використана черв’ячна фреза.
За допомогою лабораторного приладу (рис.19) змоделюємо процес виготовлення зубчастого колеса. На цьому приладі диск 1 імітує заготовку, рейка 2 – вихідний твірний контур різального інструмента. В процесі руху рейка 2 огинає диск 1 як вихідний твірний контур заготовку. При переміщенні ∆z рейки диск повертається на кут ∆ϕ = ∆zr . При
послідовному обведенні зубів рейки олівцем можна отримати на диску профілі зубів, які
|
11 |
1 |
|
10 |
|
||
|
|
||
8 |
|
9 |
|
7 |
|
2 |
|
|
|
||
|
|
0 |
|
6 |
|
3 |
|
5 |
4 |
||
|
|||
|
Рис.19 |
|
моделюють в масштабі 1:1 зуби колеса, що виготовляється на верстаті.
Рейку 2 можна зміщувати відносно диску 1 в радіальному напрямку. Положення рейки фіксується за допомогою лінійної шкали. Профілі зубів, отримані при різних
зміщеннях тх, дають можливість оцінити вплив зміщення на форму зуба.
Евольвента
Підріз
Ослаблення основи зуба
Рис.20
При нарізанні коліс, в яких zi < zmin виникає
явище підрізання ніжки зуба (рис. 20). Таке явище є небажаним, бо суттєво зменшує міцність зуба на згин. Підрізування зубів уникають шляхом зміщення інструмента від центра заготовки. Найменше значення коефіцієнта зміщення інстументальної рейки, при якому буде відсутнє підрізування зуба, для zi < zmin
визначається за формулою |
x |
min |
= h |
zmin − zi |
, де z |
min |
- |
|
|||||||
|
|
a |
zmin |
|
|
||
|
|
|
|
|
|
|
мінімальна кількість зубів, яку можна нарізати на колесі з нульовим зміщенням інструментальної рейки. Для стандартного інструмента з параметрами
ha =1, α = 200 величина zmin =17 .
29

Значне збільшення величини х приводить до загострення головки зуба. Зміщення х,
при якому товщина зуба по колу вершин sa = 0,2 т, називається |
максимально |
допустимим ( хдоп ). Зміщення інструмента, яке зодовольняє умові |
xmin < x ≤ xдоп , |
називається необхідним зміщенням. |
|
Послідовність виконання роботи.
1.Вибрати паперове коло-заготовку у відповідності з діаметром, що вказаний на диску 1 приладу. Розділити паперове коло на квадранти та провести ділильне коло, діаметр якого вказаний на рейці 2. Встановити паперове коло на диск 1 та закріпити кришкою 9.
2.Послабити гвинти 6 та встановити рейку 2 в нульове положення тх=0. При цьому риска на рейці повинна співпасти з нульовою позначкою на шкалі, а ділильна пряма рейки дотикнутися до ділильного кола.
3.Повернути важіль 4 в бік клавіші 5 та перевести рейку вправо до упору. Важіль
4повернути у вихідне положення. Повернути рукоятку 7 так, щоб послабити натяг тросу 8 та повернути диск 1 у положення, зручне для викреслювання профілей в одному з квадрантів. Рукоятку 7 повернути у вихідний стан. Натискати клавішу 5 та обводити олівцем профілі зубів рейки. Отримати 2-3 профілі зубів колеса.
4.За кількістю зубів z = dm (d - діаметр ділильного кола, т – модуль), визначити
мінімальне значення коефіцієнта зміщення інструментальної рейки xmin = 1717− z .
Отримане значення заокруглити до більшого (у відповідності до таблиці 6). Визначити величину зміщення рейки l = mx .
5.Встановити рейку з додатним зміщенням тх та викреслити профілі зубів. Для зручності розміщення зубів на папері диск повертають відносно його центру. Для цього послаблюють поворотом рукоятки 7 натяг тросу 8. Після встановлення диска в потрібному положенні трос знову затягують.
6.Виконати п.5 для від’ємного зміщення рейки, яке прийняти рівним (–l).
7.Визначити основні розміри коліс зі зміщеннями та без нього за формулами, наведеними у таблиці 7. Заповнити вільні комірки таблиці.
8.Нанести на паперову заготовку коло западин та вершин. Виміряти ділильну товщину зуба та порівняти отримане значення з розрахунковим.
Таблиця 6.
z |
|
9 |
|
10 |
|
11 |
|
12 |
|
|
13 |
14 |
|
15 |
|
16 |
|||
x |
|
0.48 |
|
0.42 |
|
0.36 |
|
0.30 |
|
0.24 |
0.18 |
|
0.12 |
|
0.06 |
||||
|
|
|
|
|
|
|
|
|
|
|
|
|
|
|
|
|
Таблиця 7. |
||
Назва |
|
Позначення та формула |
|
x<0 |
|
x=0 |
|
|
x>0 |
|
|||||||||
параметрів |
|
|
|
|
|
|
|
Розр |
Вимір. |
|
Розр |
Вимір. |
Розр |
Вимір. |
|||||
Коефіцієнт |
|
|
|
x |
|
|
|
|
|
|
|
|
|
|
|
|
|||
зміщення |
|
|
|
|
|
|
|
|
|
|
|
|
|
|
|
|
|
|
|
Зміщення |
|
|
|
l=mx |
|
|
|
|
|
|
|
|
|
|
|
|
|||
інструмента |
|
|
|
|
|
|
|
|
|
|
|
|
|
|
|
|
|
||
Діаметр кіл: |
|
|
|
|
|
|
|
|
|
|
|
|
|
|
|
|
|
||
- ділильного |
|
|
d=mz |
|
|
|
|
|
|
|
|
|
|
|
|
||||
-основного |
|
db |
= d cosαw |
|
|
|
|
|
|
|
|
|
|
|
|
||||
-западин |
|
d f = m(z −2ha −2c +2x) |
|
|
|
|
|
|
|
|
|
|
|
||||||
-вершин |
|
|
|
|
|
|
|
|
|
|
|
|
|
|
|
||||
|
|
da = m(z + 2ha + 2x) |
|
|
|
|
|
|
|
|
|
|
|
|
30
Крок по |
|
|
|
|
|
|
|
ділильному |
p = πm |
|
|
|
|
|
|
колу |
|
|
|
|
|
|
|
Товщина зуба |
π |
|
|
|
|
|
|
по ділильно- |
s = m( 2 + 2x tgα) |
|
|
|
|
|
|
му колу |
|
|
|
|
|
|
|
Ширина запа- |
|
|
|
|
|
|
|
дин по діли- |
e=p-s |
|
|
|
|
|
|
льному колу |
|
|
|
|
|
|
|
Контрольні запитання.
1.Які методи виготовлення зубчастих коліс ви знаєте?
2.Що називають вихідним твірним (виробничим) контуром інструментальної рейки?
3.Які параметри визначають геометрію вихідного твірного контуру інструментальної рейки?
4.Як розміщена ділильна пряма рейки відносно ділильного кола колеса при х=0, х>0,
х<0?
5.Як визначити коефіцієнт зміщення, при якому виникає підрізування зуба?
6.Які параметри зубчастого колеса залежать від зміщення ? Які не залежать?
7.Як визначається мінімальне, допустиме та необхідне зміщення інструментальної рейки?
8.При якому зміщенні інструментальної рейки можна нарізати зубчасті колеса з числом зубів, меншим, ніж мінімально допустиме?
Лабораторна робота №9.
Кінематичний аналіз і синтез плоских кулачкових механізмів.
Мета роботи: навчитися будувати діаграми переміщень веденої ланки кулачкового механізму; ознайомитися з методом графічного диференціювання; виконати кінематичний синтез кулачкового механізму.
Обладнання: кулачковий механізм, стояк, індикатор переміщень годинникового типу.
Теоретичні відомості.
Кулачковими називаються механізми, до складу яких входить вища кінематична пара, одним з елементів якої є поверхня змінної кривизни. Кулачкові механізми складаються з двох основних ланок. Ланку, якій належить елемент вищої кінематичної пари, виконаний у вигляді поверхні змінної кривизни, називають кулачком. Якщо вихідна ланка, яка утворює з кулачком вищу кінематичну пару, здійснює поступальний рух, то її називають штовхачем, якщо коливальний – коромислом.
Постійний контакт штовхача та кулачка забезпечується силовим або геометричним замиканням. При силовому замиканні контакт ланок зазвичай досягається за допомогою пружини.
Кулачкові механізми, так само як важільні та зубчасті, можуть бути плоскими або просторовими. Штовхачі в кулачкових механізмах можуть мати різні форми елементів вищої кінематичної пари: загострену, плоску, циліндричну або сферічну. Якщо вісь штовхача зміщена відносно осі обертання кулачка на величину е , то кулачковий механізм називається зміщеним , а відстань е - зміщенням або ексцентриситетом. У випадку, коли е=0, механізм називається центральним.
31
Профілем кулачка називається лінія перетину циліндричної поверхні кулачка з площиною, перпендикулярною до його осі.
Основними параметрами кулачкових механізмів є:
• r0 – мінімальний радіус кулачка, який з’єднує центр обертання кулачка з найближчою точкою на його профілі;
• rmax - максимальний радіус кулачка, який з’єднує центр обертання кулачка з найбільш віддаленою точкою на його профілі;
•h – хід штовхача;
•фазові кути – кути повороту кулачка, що визначають відповідні періоди руху
штовхача;
•кути профілю кулачка – центральні кути, які відповідають характерним
ділянкам профілю кулачка; в плоскому кулачку сума всіх профільних кутів дорівнює 3600.
Максимальний хід штовхача для центрального кулачкового механізму визначається різницею найбільшого і найменшого радіусів кулачка.
Задача кінематичного дослідження полягає в тому, щоб при заданих профілі кулачка та розмірах інших ланок механізму встановити закон руху вихідної ланки (штовхача або коромисла), тобто залежності переміщень, швидкостей та прискорень вихідної ланки від часу s(t), v(t), a(t) або кута повороту кулачка s(ϕ1 ), v(ϕ1 ), a(ϕ1 ) .
Найбільш простим та наочним є графічний метод виконання кінематичного аналізу. Він базується на побудові кінематичних діаграм. Повертаючи кулачок на рівні кути, будують діаграму s = s(ϕ1 ) переміщень штовхача. Шляхом її графічного
диференціювання знаходять залежності s′ = s′(ϕ1 ) , а потім s′′ = s′′(ϕ1 ) , які характеризують
зміну аналогів швидкості та прискорення штовхача.
Аналогом швидкості називають першу похідну від переміщення за узагальненою
координатою |
|
s′(ϕ1 ) , причому |
v = |
ds |
= |
ds |
|
dϕ1 |
= s′ ω1 при поступальному русі та |
|||||
dt |
dϕ1 |
dt |
||||||||||||
|
|
|
|
|
|
|
|
|
|
|
||||
ω = |
dϕ |
= |
dϕ |
|
dϕ1 |
=ϕ′ ω1 при обертовому. |
Як випливає з наведених формул, аналоги |
|||||||
dt |
dϕ1 |
dt |
||||||||||||
|
|
|
|
|
|
|
|
|
|
|
швидкостей чисельно дорівнюють значенням швидкостей відповідних точок або ланок при ω1=1, а у загальному випадку є відношенням швидкостей s′ = vω1 , ϕ′ =ω
ω1 . Тому їх
часто називають передаточними функціями.
Аналогом прискорення називають другу похідну від переміщення за узагальненою
координатою: s′′ = |
d 2 s |
|
ϕ′′ = |
d 2ϕ |
|
|
, |
|
. |
||
dϕ12 |
dϕ12 |
Зручність використання аналогів швидкості та прискорення під час досліджень пояснюється тим, що ці величини для заданої кінематичної схеми механізму залежать тільки від узагальненої координати і не залежать від швидкості руху початкової ланки, тобто кінематичне дослідження можна вести чисто геометричними методами.
Експериментальну побудову діаграми s = s(ϕ1 ) здійснюють за допомогою
лабораторного пристрою (рис.21). Кулачок 2 встановлюють в положення, яке відповідає крайньому нижньому положенню штовхача 3. Повертають ручку 4 так, щоб кулачок повертався на однакову кількість поділок шкали 5. Одночасно за індикатором визначають лінійне переміщення s штовхача. Результати вимірювань заносять у таблицю:
|
|
|
|
|
|
|
|
|
|
|
Таблиця 8. |
||
ϕ , град |
0 |
30 |
60 |
90 |
120 |
150 |
180 |
210 |
240 |
270 |
300 |
330 |
|
s, мм |
|
|
|
|
|
|
|
|
|
|
|
|
|
32
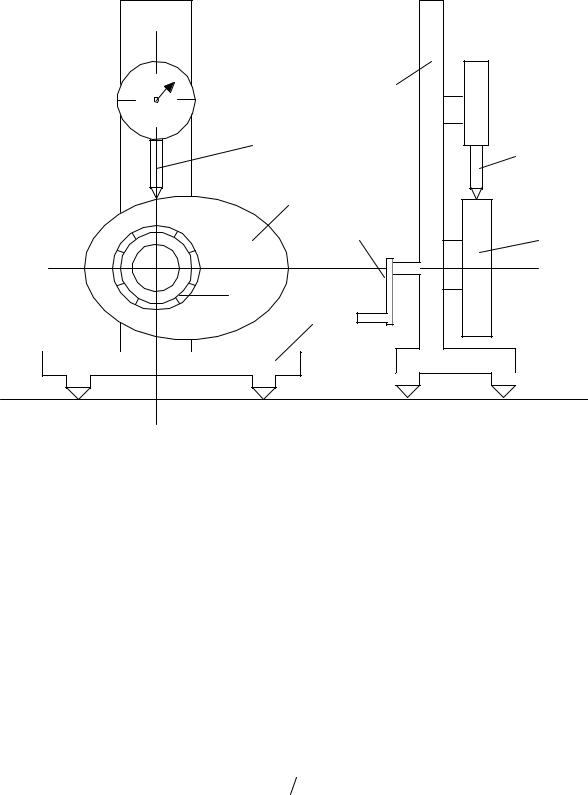
|
1 |
3 |
3 |
|
|
2 |
|
4 |
2 |
5 |
|
1 |
|
Рис.21 |
|
Вимірювання виконуються на протязі одного оберту кулачка. Кінематичним циклом руху механізму називається послідовність переміщень його ланок за період зміни координати початкової ланки. За даними таблиці у масштабі µs будується діаграма
переміщень штовхача. Масштаб по осі абсцис обирається за наступною формулою: µϕ = 2πl , де l – довжина відрізка на діаграмі, який зображує один оберт кулачка
(здебільше вибирають l =120 мм). Для побудови діаграм аналога швидкості s′ = s′(ϕ1 ) та аналога прискорення s′′ = s′′(ϕ1 ) отриману діаграму переміщень двічі графічно
диференціюють, використовуючи метод дотичних або метод хорд /7/. Масштаби побудованих діаграм визначають за формулами:
µs′ = |
µs |
, µs′′ = |
µs′ |
, де Н1, Н2 – полюсні відстані на діаграмах. |
|
|
|||
|
µϕ H1 |
µϕ H 2 |
При відомій кутовій швидкості обертання кулачка ω1 по побудованих діаграмах аналогів швидкості та прискорення можна визначити залежності переміщення, швидкості та прискорення штовхача від часу. При цьому масштаби діаграм s = s(t), v = v(t), a = a(t)
будуть визначатися за формулами: µ |
t |
= µ |
ϕ |
ω , µ |
v |
= µ |
s′ |
ω , µ |
a |
= µ |
s′′ |
ω2 . |
|
|
1 |
|
1 |
|
|
Побудова профілю кулачка за заданими законами руху вхідної (кулачка) та вихідної (штовхача або коромисла) ланок є задачею кінематичного синтезу кулачкових механізмів. Вона розв’язується графічним або аналітичним способом.
Послідовність виконання роботи.
1.Ознайомитися з будовою та принципом дії кулачкового механізму.
2.Повертаючи кулачок, встановити залежність s = s(ϕ1 ) та результати вимірювань занести у таблицю 8.
33
3.Вибрати масштаб та побудувати діаграму s = s(ϕ1 ) .
4.Використовуючи метод хорд, побудувати діаграми аналога швидкості s′ = s′(ϕ1 ) та аналога прискорення s′′ = s′′(ϕ1 ) . Визначити масштаби.
5.Задати ω1=1с-1 та обчислити масштаби µv , µa .
6.Визначити за допомогою побудованих діаграм переміщення, швидкість та прискорення штовхача при повороті кулачка на кут ϕ =_________.
7.По діаграмі переміщень побудувати профіль кулачка графічним способом.
Контрольні запитання.
1.Який механізм називається кулачковим?
2.Сформулювати переваги та недоліки кулачкових механізмів.
3.Форми елементів вищої пари, що належить вихідній ланці.
4.Основні параметри кулачкових механізмів.
5.Яка різниця між кутами профілю кулачка і фазовими кутами руху штовхача?
6.Які фази руху штовхача ви знаєте?
7.Основні задачі кінематичного аналізу кулачкового механізму.
8.Аналоги швидкості та прискорення.
9.Як здійснюється графічне диференціювання діаграм методом хорд?
10.Як визначаються масштаби діаграм?
11.Як визначити, користуючись діаграмами, швидкість штовхача при заданому куті повороту кулачка?
12.Основна задача кінематичного синтезу кулачкового механізму.
Література
1.Пасіка В.Р. Програма кінематичного дослідження механізмів.
2.Пасіка В.Р. Методичний посібник по розрахунку кінематичних характеристик циклових важільних мехвнізмів ІІ класу з дисципліни «Теорія механізмів та машин». – Львів: Українська Академія Друкарства. – 1998.- 69с.
3.Пасіка В.Р. Програма кінетостатичного дослідження механізмів.
4.Пасіка В.Р.Кінетостатичний аналіз циклових важільних механізмів аналітичними методами (Частина І)/Навчальний посібник.- Львів: Українська Академія Друкарства. – 2000.- 49с.
5.Горов Э.А., Гайдай С.А., Лушников С.В. Типовой лабораторный практикум по теории механизмов и машин.- М.:Машиностроение, 1990.- 160с.
6.Методичні вказівки до лабораторних робіт з теорії механізмів і машин для студентів механічних спеціальностей. Частина І/ Під ред. Б.І.Кіндрацького. – Львів, ДУ «Львівська політехніка», 1994.- 64с.
7.Я.Т.Кіницький. Короткий курс теорії механізмів і машин.- Львів:Афіша,2004.- 272с.
8.Я.Т.Кіницький. Практикум із теорії механізмів і машин.- Львів:Афіша,2004.- 453с.
9.И.И.Артоболевский. Теория механизмов и машин. – М:Наука, 1974.- 640с.
34
Зміст
№ |
Назва роботи |
Стор. |
1. |
Побудова кінематичної схеми за діючою моделлю механізму. |
3 |
2. |
Структурний аналіз моделі важільного механізму |
5 |
3. |
Кінематичне дослідження механізмів ІІ класу за допомогою комп’ютера. |
8 |
4. |
Кінетостатичне дослідження механізмів ІІ класу за допомогою комп’ютера. |
12 |
5. |
Визначення механічних параметрів ланок механізму. |
15 |
6.Експериментальне визначення параметрів евольвентних прямозубих 20 циліндричних зубчастих коліс.
7. Кінематичний аналіз зубчастих механізмів. |
24 |
8.Моделювання процесу виготовлення зубчастих коліс способом обкочування. 28
9. Кінематичний аналіз і синтез плоских кулачкових механізмів. |
31 |
Література |
34 |
35