
book_OPVRV
.pdf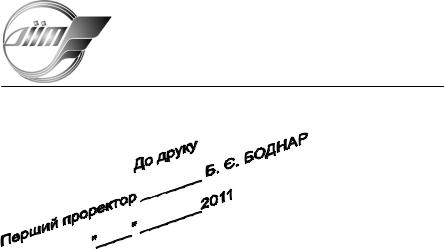
Навчальне видання
Анофрієв Василь Григорович Безовська Лідія Петрівна
ОРГАНІЗАЦІЯ ТА ПЛАНУВАННЯ ВАГОНОРЕМОНТНОГО ВИРОБНИЦТВА
Методичні вказівки до практичних занять і лабораторних робіт
Редактор І. С. Лопатіна
Комп’ютерна верстка Т. В. Шевченко
Формат 60×84 1/16. Ум. друк. арк. 2,33. Обл.-вид. арк. 2,36.
Тираж 75 пр. Зам. № _____.
Видавництво Дніпропетровського національного університету залізничного транспорту імені академіка В. Лазаряна
Свідоцтво суб’єкта видавничої діяльності ДК № 1315 від 31.03.2003
Адреса видавництва та дільниці оперативної поліграфії: 49010, Дніпропетровськ, вул. Лазаряна, 2, www.diitrvv.dp.ua
40
МІНІСТЕРСТВОІНФРАСТРУКТУРИУКРАЇНИ
Дніпропетровський національний університет залізничного транспорту імені академіка В. Лазаряна
Кафедра «Вагони та вагонне господарство»
ОРГАНІЗАЦІЯ ТА ПЛАНУВАННЯ ВАГОНОРЕМОНТНОГО ВИРОБНИЦТВА
Методичні вказівки до практичних занять і лабораторних робіт
Укладачі: В. Г. Анофрієв Л. П. Безовська
Для студентів ІV-V курсів за напрямом підготовки 6.070105 «Рухомий склад залізниць» спеціальності 7(8).07010502 «Вагони та вагонне господарство» денної форми навчання
Дніпропетровськ 2011
1
УДК 629.483/484:658.012.2
Укладачі:
доц. Анофрієв Василь Григорович ст. викл. Безовська Лідія Петрівна
Рецензенти:
головний інженер Д.В. Караблін (ПАТ «Дніпровагонрембуд») канд. техн. наук, доц. Г.В. Поленюк (ДІІТ)
Організація та планування вагоноремонтного виробництва [Текст]: методичні вказівки до практичних занять і лабораторних робіт / уклад.: В. Г. Анофрієв, Л. П. Безовська; Дніпропетр. нац. ун-т залізн. трансп. ім. акад. В. Лазаряна. – Д.: Вид-во Дніпропетр. нац. ун-ту залізн. трансп. ім. акад. В. Лазаряна, 2011. –
39с.
Уметодичних вказівках подані практичні заняття та лабораторні роботи, виконання яких допоможе краще засвоїти теоретичні знання лекційного курсу з дисципліни «Організація та планування вагоноремонтного виробництва».
Іл. 19. Табл. 27. Бібліогр.: 7 назв.
©Анофрієв В. Г., Безовська Л. П., укладання, 2011
©Вид-во Дніпропетр. нац. ун-ту залізн. трансп. ім. акад. В. Лазаряна, редагування, оригінал-макет, 2011
2
ЗМІСТ |
|
Практичне заняття № 1 |
|
ОРГАНІЗАЦІЯ ВИРОБНИЧОГО ПРОЦЕСУ В ЧАСІ .............................................. |
3 |
Практичне заняття № 2 |
|
КАЛЕНДАРНЕ ПЛАНУВАННЯ ПРОСТИХ ВИРОБНИЧИХ ПРОЦЕСІВ. |
|
ВИБІР РАЦІОНАЛЬНОГО ВАРІАНТА ПОСЛІДОВНОСТІ |
|
ОБРОБКИ ВИРОБІВ..................................................................................................... |
5 |
Практичне заняття № 3 |
|
СІТКОВЕ МОДЕЛЮВАННЯ ВИРОБНИЧИХ ПРОЦЕСІВ |
|
І РОЗРАХУНОК ЧАСОВИХ ПАРАМЕТРІВ СІТКОВОГО ГРАФІКА................ |
13 |
Практичне заняття № 4 |
|
ОРГАНІЗАЦІЯ РОБОТИ БЕЗПЕРЕРВНО-ПОТОКОВОЇ |
|
ВИРОБНИЧОЇ ЛІНІЇ (БПЛ)........................................................................................ |
17 |
Практичне заняття № 5 |
|
ОРГАНІЗАЦІЯ РОБОТИ ПЕРЕРВНО-ПОТОКОВОЇ ЛІНІЇ (ППЛ)....................... |
20 |
Лабораторна робота № 1 |
|
ВИВЧЕННЯ МЕТОДІВ НОРМУВАННЯ ОПЕРАЦІЙ............................................ |
22 |
Лабораторна робота № 2 |
|
ОБҐРУНТУВАННЯ МЕТОДІВ РЕМОНТУ РУХОМОГО СКЛАДУ |
|
ТА РОЗРАХУНОК ПАРАМЕТРІВ ОРГАНІЗАЦІЇ ВИРОБНИЦТВА |
|
В ОСНОВНИХ ЦЕХАХ ВРЗ...................................................................................... |
30 |
Лабораторна робота № 3 |
|
СТАТИСТИЧНИЙ АНАЛІЗ ТОЧНОСТІ ТЕХНОЛОГІЧНОГО ПРОЦЕССУ...... |
32 |
Лабораторна робота № 4 |
|
МЕТОДИ СТАТИСТИЧНОГО РЕГУЛЮВАННЯ |
|
ТЕХНОЛОГІЧНИХ ПРОЦЕСІВ................................................................................ |
36 |
39
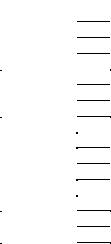
2.2. Нанести значення розмахів Ri на контрольну карту та з’єднати їх за допомогою прямих ліній.
2.3.Показати на контрольній карті суцільною лінією межу технічного допуску δ:
δ=µв −µн.
2.4.Розрахувати значення контрольної межі за формулою
µ1R =0,5 B δ,
де В – коефіцієнт, що залежить від обсягу підгрупи (значення коефіцієнта В наведене в табл. 26).
За цим методом наноситься тільки одна межа (однобічне регулювання), тому що контролюється тільки збільшення розсіяння значень параметра.
2.5.Показати на контрольній карті пунктирною лінією контрольну межу
µ1R .
2.6.У разі виходу контрольних точок за межі регулювання (або на межі
регулювання) зробити позначення сигналом – стрілкою.
3. Виконати аналіз ходу технологічного процесу за допомогою карт середніх арифметичних значень та розмахів на підставі відповідних критеріїв
[1, с. 113].
Висновки
Висновки мають містити відповіді на такі запитання:
1.Чи знаходиться процес у контрольованому стані?
2.Чи має місце збільшення розсіяння параметра?
Література
1.Анофрієв, В. Г. Організація і планування вагоноремонтного виробництва: конспект лекцій [Текст] / В. Г. Анофрієв. – Д.: Дніпропетр. держ. техн. ун-т залізн. трансп., 2000. – 139 с.
2.Организация, планирование и управление предприятием машиностроения [Текст]: учеб. для студ. машиностр. специальн. вузов / под ред. И. М. Разумова. – М.: Машиностроение, 1982. – 544 с.
38
Практичне заняття № 1
Тема: Організація виробничого процесу в часі
Мета роботи: вивчення методики розрахунку тривалості виробничих циклів, побудови графіків та особливостей видів руху предметів праці за операціями виробничого процесу.
Для виконання практичного заняття необхідно ознайомитися з теоретичним матеріалом, викладеним в одному з джерел: [1, с. 11-17], [2, с. 37-47], [3, с. 19-23].
Вихідні дані:
–кількість деталей, що треба обробити, n =12 ;
–кількість операцій, виконуваних послідовно, m =3;4;5 (залежно від варі-
анта);
– час виконання i-ї операції однієї деталі, заданий у табл. 1, відповідно до варіанта.
Таблиця 1
Час виконання і-ї операції з обробки однієї деталі
№ |
Час виконання i-ї операції |
|
№ |
Час виконання i-ї операції |
|||||||||||
варі- |
|
з обробки однієї деталі |
|
варі- |
|
з обробки однієї деталі |
|
||||||||
анта |
|
|
|
|
|
|
|
анта |
|
|
|
|
|
|
|
t1 |
|
t2 |
t3 |
t4 |
|
t5 |
t1 |
|
t2 |
t3 |
t4 |
|
t5 |
||
|
|
|
|
|
|
||||||||||
1 |
5 |
|
2 |
1 |
4 |
|
2 |
16 |
2 |
|
4 |
3 |
– |
|
– |
2 |
5 |
|
2 |
3 |
– |
|
– |
17 |
5 |
|
1 |
4 |
3 |
|
– |
3 |
3 |
|
2 |
4 |
1 |
|
2 |
18 |
4 |
|
6 |
1 |
3 |
|
2 |
4 |
2 |
|
1 |
4 |
2 |
|
– |
19 |
6 |
|
3 |
4 |
– |
|
– |
5 |
2 |
|
4 |
1 |
3 |
|
– |
20 |
1 |
|
6 |
4 |
2 |
|
– |
6 |
2 |
|
4 |
3 |
4 |
|
1 |
21 |
5 |
|
4 |
3 |
2 |
|
3 |
7 |
1 |
|
5 |
3 |
– |
|
– |
22 |
1 |
|
5 |
3 |
4 |
|
– |
8 |
5 |
|
2 |
3 |
2 |
|
– |
23 |
4 |
|
5 |
3 |
– |
|
– |
9 |
3 |
|
4 |
2 |
1 |
|
– |
24 |
2 |
|
4 |
1 |
2 |
|
– |
10 |
4 |
|
2 |
3 |
– |
|
– |
25 |
2 |
|
4 |
2 |
1 |
|
2 |
11 |
3 |
|
5 |
4 |
2 |
|
1 |
26 |
2 |
|
1 |
4 |
3 |
|
– |
12 |
5 |
|
1 |
2 |
3 |
|
– |
27 |
2 |
|
5 |
1 |
3 |
|
1 |
13 |
2 |
|
4 |
3 |
– |
|
– |
28 |
3 |
|
2 |
4 |
– |
|
– |
14 |
4 |
|
1 |
3 |
1 |
|
2 |
29 |
4 |
|
2 |
3 |
4 |
|
2 |
15 |
3 |
|
5 |
4 |
– |
|
– |
30 |
2 |
|
3 |
2 |
– |
|
– |
Порядок виконання роботи
1. За вихідними даними, вказаними в табл. 1, побудувати графік обробки n деталей на трьох (чотирьох, п’яти) послідовних операціях (за осями абсцис відкласти час, за осями ординат – номери операцій) у разі таких видів руху:
3
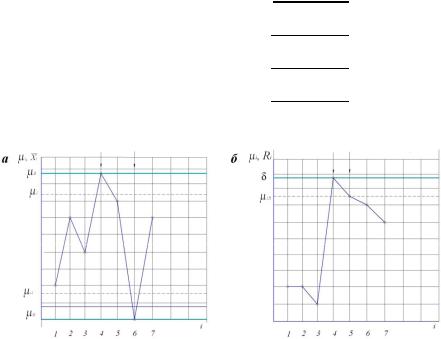
–послідовного;
–паралельно-послідовного (для величини транспортної партії p = 2;3;4;
6);
– паралельного ( p =1;2;3;4;6).
2. Визначити за допомогою формул і графіків тривалість технологічного циклу Ттц для всіх видів руху за умови різних величин транспортної партії
p .
3. Побудувати графік залежності тривалості технологічного циклу Ттц від величини транспортної партії p (для паралельного і паралельнопослідовного видів руху).
Висновки
У висновках необхідно:
– визначити, який із розглянутих видів руху має мінімальну (максимальну) тривалість технологічного циклу Ттц; для яких видів виробництва засто-
совується кожен із розглянутих видів руху; наголосити на перевагах і недоліках цих видів руху;
– порівняти значення тривалості технологічного циклу Ттц при однакових транспортних партіях деталей p ( p = 2;3;4;6) для паралельного та пара-
лельно-послідовного видів руху;
– відстежити яким чином змінюється величина тривалості технологічного циклу Ттц залежно від величини транспортної партії p = 2;3;4;6.
Література
1.Анофрієв, В. Г. Організація і планування вагоноремонтного виробництва: конспект лекцій [Текст] / В. Г. Анофрієв. – Д.: Дніпропетр. держ. техн. ун-т залізн. трансп., 2000. – 139 с.
2.Организация, планирование и управление предприятием машиностроения: учеб. для студ. машиностр. специальн. вузов [Текст] / под ред. И. М. Разумова. – М.: Машиностроение, 1982. – 544 с.
3.Скиба, И. Ф. Организация, планирование и управление на вагоноремонтных предприятиях [Текст]: учеб. для вузов ж.-д. трансп. / И. Ф. Скиба. –
М.: Транспорт, 1978. – 344 с.
4
µо – це значення середини поля допуску, µо = Хн).
На рис. 19, а наведений приклад побудови карти середніх арифметичних значень, а на рис. 19, б – карти розмахів.
Таблиця 26
Значення коефіцієнтів А і В
Обсяг підгрупи |
Коефіцієнт А |
|
Коефіцієнт В |
3 |
0,423 |
1,45 |
|
4 |
0,500 |
1,56 |
|
5 |
0,553 |
1,63 |
|
6 |
0,592 |
1,68 |
|
7 |
0,622 |
1,72 |
|
8 |
0,646 |
1,75 |
|
9 |
0,667 |
1,78 |
|
10 |
0,684 |
1,81 |
Рис. 19. Карта середніх арифметичних значень (а) та карта розмахів (б)
2. Побудувати карту розмахів (за осями абсцис відкласти номери підгрупи i , а за осями ординат – значення розмахів Ri ). Для цього необхідно:
2.1. Скласти табл. 27 значень розмахів Ri , (використати дані з протоколу вимірювань лабораторної роботи № 3):
Таблиця 27
Значення розмахів результатів вимірювання
№ підгрупи, і |
1 |
2 |
3 |
4 |
… |
… |
… |
… |
|
R 10−3 |
, мм |
|
|
|
|
|
|
|
|
i |
|
|
|
|
|
|
|
|
|
37
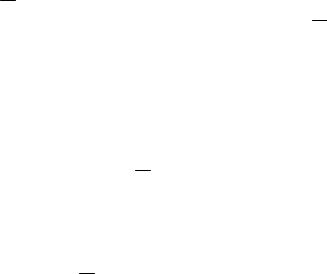
Лабораторна робота № 4
Тема: Методи статистичного регулювання технологічних процесів
Мета роботи: Вивчення теоретичних основ та освоєння на практиці методів статистичного регулювання якості продукції.
Для виконання лабораторної роботи необхідно ознайомитися з теоретич-
ним матеріалом, викладеним у [1, с. 109-114], [2, с. 204-212].
Статистичне регулювання технологічного процесу є коригуванням значень параметрів технологічного процесу за результатами вибіркового контролю параметрів продукції, що виготовляється, з метою забезпечення необхідного рівня якості.
Порядок виконання роботи
1. Побудувати карту середніх арифметичних значень (за осями абсцис відкласти номери підгрупи i , а за осями ординат – середні значення парамет-
ра Хі ). Для цього необхідно:
1.1. Скласти табл. 25 середніх арифметичних значень Хі (дані з протоколу вимірювань лабораторної роботи № 3):
Таблиця 25
Середнє значення результатів вимірювання
|
№ підгрупи, і |
1 |
2 |
3 |
4 |
… |
… |
… |
… |
|
|
|
10−3 , мм |
|
|
|
|
|
|
|
|
|
Хі |
|
|
|
|
|
|
|
|
1.2. Нанести значення Хі на контрольну карту та з’єднати їх за допомогою прямих ліній.
1.3.Показати на контрольній карті суцільною лінією верхню µв й нижню
µн межі технічного допуску δ (дані з протоколу вимірювань лабораторної
роботи № 3).
1.4. Розрахувати верхню µ1 й нижню µ-1 контрольні межі середніх зна-
чень параметра Хі , за яких потрібне коригування (це значення відповідає
максимально припустимій частці браку) за формулами
µ1 =µв −0,5 А δ, µ1 =µн + 0,5 А δ,
де А – коефіцієнт, що залежить від обсягу підгрупи. Коефіцієнти для розрахунку меж регулювання наведені в табл. 26.
1.5.Показати на контрольній карті пунктирною лінією верхню µ1 й нижню µ-1 контрольні межі.
1.6.Показати на графіку суцільною лінією середнє значення параметра
µо, що відповідає випуску продукції найкращої якості (в більшості випадків
36
Практичне заняття № 2
Тема: Календарне планування простих виробничих процесів. Вибір раціонального варіанта послідовності обробки виробів
Мета роботи: Вивчення методів визначення та мінімізація тривалості виконання робіт у конвеєрній системі з двох машин.
Методичні вказівки
Для виконання практичного заняття потрібно розглянути матеріал, ви-
кладений у [1, с. 49-51] і [2, с. 113-120, 286-292].
Робота, виконувана у конвеєрній системі, є послідовністю операцій, кожну з яких виконує відповідна машина. Прикладом конвеєрної системи може служити складальна лінія. Взагалі конвеєрна система може розглядатися як будь-яка сукупність машин, яка виконує всі роботи в одному порядку. Для такої системи зовсім не обов’язково, щоб кожна робота складалася з операцій, виконуваних кожною машиною, або щоб робота розпочиналася та закінчувалася визначеними машинами. Суттєвим є лише те, що процес роботи, пов’язаний із закінченням на одній машині та початком виконання на іншій, має переміщуватися в одному напрямку.
Обмеження, що враховуються під час функціонування системи:
1.Одна машина (верстат) виконує не більше однієї роботи одночасно.
2.Одна робота не може одночасно виконуватися кількома машинами (верстатами). При цьому, для будь-якої i -ї деталі робота на машині (верстаті)
№1 має закінчитися раніше, ніж розпочнеться на машині (верстаті) № 2.
3.Порядок виконання робіт на машинах (верстатах) є однаковим.
Евристичний алгоритм [2]
Згідно з евристичним алгоритмом, порядок обробки виробів у конвеєрній системі визначається відповідно до пріоритету кожного виробу, який може дорівнювати сумарній тривалості всіх операцій з обробки виробу (деталі) – TWORK. Наприклад, для конвеєрної системи з двох машин
TWORKi =ti1 +ti2 .
У разі застосування правила minTWORK запуск виробів до конвеєрної системи здійснюється відповідно до збільшення величини TWORK, а за правилом maxTWORK запуск відбувається відповідно до зменшення величини TWORK. Якщо величини TWORK для різних виробів рівні, то першим обробляють виріб із меншим (minTWORK) або більшим (maxTWORK) порядковим номером.
Алгоритм Джонсона [1]
1. Знайдемо всі деталі, для яких час обробки на першому верстаті є меншим, ніж на другому (ti1 <ti2 ), та впорядковуємо їх за зростанням ti1.
|
1 |
1 |
|
За рівного часу обробки на першому верстаті ti |
=ti+1 |
у першу чергу |
|
|
|
|
|
|
|
|
5 |
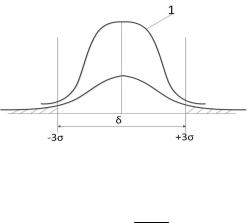
призначаємо деталь, для якої час обробки на другому верстаті є меншим
(ti2 <ti2+1).
2. Деталі, для яких час обробки на першому верстаті є більшим, ніж на другому (ti1 >ti2 ), впорядкуємо за зменшенням ti2 .
За рівного часу обробки на другому верстаті ti2 =ti2+1 в останню чергу призначаємо деталь, для якої час обробки на першому верстаті є меншим
(t1 <t1+ ).
ii 1
3.Спочатку обробляють деталі першої групи, а потім – другої.
Вихідні дані
Заданий час обробки ti1 та ti2 для 11 деталей на двох верстатах (спочатку
деталь обробляється на верстаті № 1, потім – на верстаті № 2), вказаний у табл. 2 залежно від варіанта:
Таблиця 2
Час обробки однієї деталі на двох послідовних операціях
№ |
№ |
1 |
2 |
3 |
4 |
5 |
6 |
7 |
8 |
9 |
10 |
11 |
|
варіанта |
дет. |
||||||||||||
|
|
|
|
|
|
|
|
|
|
|
|||
|
|
|
|
|
|
|
|
|
|
|
|
|
|
1 |
ti1 |
4 |
4 |
6 |
1 |
4 |
7 |
2 |
9 |
1 |
3 |
5 |
|
ti2 |
2 |
6 |
7 |
4 |
3 |
8 |
5 |
7 |
7 |
6 |
2 |
||
|
|||||||||||||
2 |
ti1 |
6 |
2 |
3 |
7 |
2 |
6 |
3 |
2 |
7 |
8 |
1 |
|
ti2 |
2 |
6 |
4 |
5 |
4 |
4 |
6 |
5 |
1 |
3 |
9 |
||
|
|||||||||||||
3 |
ti1 |
6 |
3 |
2 |
5 |
9 |
7 |
4 |
5 |
3 |
8 |
2 |
|
ti2 |
4 |
7 |
6 |
3 |
5 |
2 |
8 |
9 |
6 |
5 |
7 |
||
|
|||||||||||||
4 |
ti1 |
8 |
4 |
2 |
1 |
5 |
7 |
3 |
1 |
6 |
2 |
6 |
|
ti2 |
2 |
3 |
7 |
3 |
1 |
2 |
4 |
4 |
2 |
8 |
7 |
||
|
|||||||||||||
5 |
ti1 |
4 |
5 |
1 |
9 |
6 |
1 |
3 |
8 |
2 |
3 |
1 |
|
ti2 |
3 |
6 |
2 |
7 |
5 |
4 |
4 |
7 |
3 |
2 |
3 |
||
|
|||||||||||||
6 |
ti1 |
2 |
7 |
4 |
5 |
8 |
6 |
9 |
1 |
5 |
1 |
2 |
|
ti2 |
6 |
4 |
6 |
2 |
6 |
3 |
4 |
7 |
3 |
3 |
5 |
||
|
6
де ω – поле розсіювання контрольованого параметра.
Для закону нормального розподілу (див. рис. 18) крива має вигляд (1), а розсіювання параметра фіксується у межах ±3σ, тобто поле ω = 6·σ. Величина σ характеризує гущину групування розмірів навколо номінального, тобто чим більшим є σ, тим більшим є поле розсіювання й нижчою точність процесу, та навпаки.
Рис. 18. Нормальний закон розподілу відхилення діаметра циліндричних роликів
Визначити показник стабільності розсіювання, що характеризує зміну показників розсіювання з перебігом часу, за допомогою коефіцієнта kс:
де kр(t1) – показник розсіювання для періоду часу t1 (I група); kр(t2 ) – показник розсіювання для періоду часу t2 (IV група).
Висновки
У висновках необхідно відповісти на такі запитання:
1.За якими показниками перевірялася точність процесу?
2.Чи налагоджений верстат на випуск якісної продукції?
3.Які заходи необхідно впровадити, якщо обладнання не налагоджено?
Література
1.Анофрієв, В. Г. Організація і планування вагоноремонтного виробництва: конспект лекцій [Текст] / В. Г. Анофрієв. – Д.: Дніпропетр. держ. техн. ун-т залізн. трансп., 2000. – 139 с.
2.Организация, планирование и управление предприятием машиностроения: учеб. для студ. машиностр. специальн. вузов [Текст] / под ред. И. М. Разумова. – М.: Машиностроение, 1982. – 544 с.
3.Скиба, И. Ф. Организация, планирование и управление на вагоноремонтных предприятиях [Текст]: учеб. для вузов ж.-д. трансп. / И. Ф. Скиба. –
М.: Транспорт, 1978. – 344 с.
35
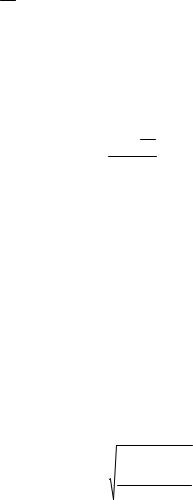
3. Після отримання результатів вимірювання зробити їх обробку:
– у рядку Хі записується результат, одержаний від ділення рядка «Сума»
на обсяг підгрупи, тобто середнє значення результатів вимірювання;
– у рядку Хіmax записуємо максимальне значення Хі у поданій підгрупі,
ав рядку Хіmin – мінімальне;
–у рядку Ri (розмах) записується різниця Хіmax − Ximin .
4. Знайти величину поля допуску δ та заданий центр налаштування Хн,
використовуючи дані про допуск деталі з попередньої таблиці. 5. Обчислити рівень налаштування процесу за формулою
kн = Хн δ− Хі
Урахувати, що для отримання результатів у мм, дані протоколу необхідно розділити на 1000.
Під час розрахунку коефіцієнта kн середні значення беремо зі стовпця «в», при цьому значення kн будуть максимальними. Якщо за стовпцем «в» отримані значення kн відповідають нормам (±5 %), то й за стовпцем «а» цей
коефіцієнт теж відповідатиме нормам.
6. Розрахувати зміщення центра розсіювання, що оцінюється за коефіцієнтом kц:
|
|
|
|
kц = |
Хn |
− |
X o |
, |
|||
|
|
|
|
|
δ |
||||||
|
|
|
|
|
|
|
|
|
|||
де |
X n |
|
– середнє значення показника в останній перед наступним налашту- |
||||||||
ванням обладнання пробі з партії оброблених деталей (IV група); |
|||||||||||
|
|
Хо |
– середнє значення показника в першій миттєвій пробі з партії обро- |
||||||||
блених деталей (I група). |
|
|
|
|
|
|
|
||||
|
7. Обчислити середнє квадратичне відхилення σ, що характеризує вели- |
||||||||||
чину поля фактичного розсіювання розмірів, за формулою |
|||||||||||
|
|
|
|
|
∑n (Xi − |
|
)2 |
||||
|
|
|
|
|
Xi |
||||||
|
|
|
|
σ = |
і=1 |
, |
|||||
|
|
|
|
|
|
n −1 |
|
|
|||
де |
Хі – відхилення від діаметра роликів (дані вимірювання – стовпці «а» і |
||||||||||
«в»); |
|
|
|
|
|
|
|
|
Хі – середнє значення результатів вимірювання;
n – обсяг підгрупи.
8. Визначити ступінь відповідності поля розсіювання до поля допуску за допомогою показника розсіювання kр:
kp = ωδ = 6δσ ≤1,
34
Продовження табл. 2
№ |
№ |
1 |
2 |
3 |
4 |
5 |
6 |
7 |
8 |
9 |
10 |
11 |
|
варіанта |
дет. |
||||||||||||
|
|
|
|
|
|
|
|
|
|
|
|||
|
|
|
|
|
|
|
|
|
|
|
|
|
|
7 |
ti1 |
5 |
8 |
3 |
7 |
4 |
2 |
7 |
3 |
6 |
4 |
2 |
|
ti2 |
6 |
2 |
4 |
5 |
2 |
3 |
2 |
7 |
5 |
3 |
8 |
||
|
|||||||||||||
8 |
ti1 |
4 |
5 |
3 |
7 |
1 |
5 |
9 |
3 |
1 |
8 |
6 |
|
ti2 |
3 |
8 |
4 |
5 |
2 |
7 |
7 |
6 |
4 |
5 |
3 |
||
|
|||||||||||||
9 |
ti1 |
2 |
4 |
2 |
8 |
7 |
3 |
9 |
2 |
7 |
7 |
3 |
|
ti2 |
4 |
8 |
5 |
4 |
2 |
5 |
5 |
7 |
8 |
1 |
7 |
||
|
|||||||||||||
10 |
ti1 |
2 |
6 |
1 |
2 |
7 |
3 |
8 |
6 |
1 |
2 |
1 |
|
ti2 |
1 |
3 |
3 |
7 |
8 |
1 |
7 |
4 |
4 |
5 |
2 |
||
|
|||||||||||||
11 |
ti1 |
2 |
8 |
1 |
8 |
2 |
3 |
6 |
1 |
7 |
4 |
1 |
|
ti2 |
7 |
4 |
2 |
5 |
5 |
5 |
4 |
3 |
2 |
6 |
7 |
||
|
|||||||||||||
12 |
ti1 |
4 |
4 |
2 |
1 |
2 |
7 |
5 |
1 |
2 |
7 |
5 |
|
ti2 |
1 |
2 |
5 |
5 |
6 |
3 |
1 |
4 |
4 |
4 |
7 |
||
|
|||||||||||||
13 |
ti1 |
2 |
6 |
5 |
1 |
9 |
7 |
7 |
2 |
5 |
4 |
8 |
|
ti2 |
9 |
7 |
6 |
4 |
2 |
1 |
9 |
7 |
8 |
3 |
4 |
||
|
|||||||||||||
14 |
ti1 |
9 |
7 |
4 |
2 |
3 |
1 |
9 |
7 |
1 |
2 |
7 |
|
ti2 |
3 |
4 |
3 |
5 |
4 |
2 |
5 |
6 |
5 |
7 |
8 |
||
|
|||||||||||||
15 |
ti1 |
9 |
2 |
3 |
8 |
3 |
2 |
6 |
8 |
1 |
5 |
2 |
|
ti2 |
2 |
4 |
1 |
4 |
4 |
3 |
5 |
9 |
3 |
6 |
9 |
||
|
|||||||||||||
16 |
ti1 |
6 |
1 |
9 |
7 |
4 |
6 |
8 |
4 |
1 |
4 |
5 |
|
ti2 |
2 |
5 |
3 |
5 |
6 |
1 |
3 |
9 |
3 |
7 |
3 |
||
|
|||||||||||||
17 |
ti1 |
8 |
9 |
7 |
1 |
3 |
8 |
8 |
7 |
1 |
4 |
2 |
|
ti2 |
3 |
8 |
5 |
2 |
6 |
5 |
7 |
3 |
7 |
6 |
5 |
||
|
7
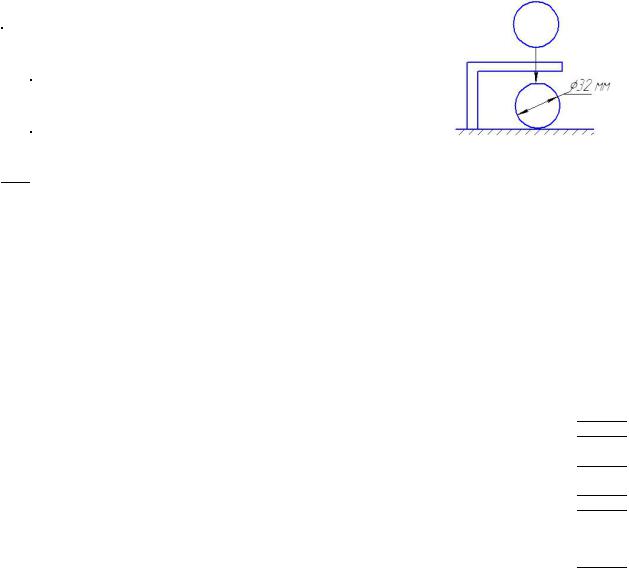
Продовження табл. 2
№ |
№ |
1 |
2 |
3 |
4 |
5 |
|
6 |
|
7 |
8 |
9 |
10 |
11 |
|
|
варіанта |
дет. |
|
|
|
|
|||||||||||
|
|
|
|
|
|
|
|
|
|
|
|
|
|
|
||
|
|
|
|
|
|
|
|
|
|
|
|
|
|
|
|
|
18 |
ti1 |
1 |
6 |
8 |
7 |
2 |
|
1 |
|
6 |
6 |
5 |
2 |
1 |
|
|
ti2 |
4 |
5 |
5 |
4 |
3 |
|
2 |
|
5 |
1 |
3 |
4 |
3 |
|
|
|
|
|
|
|
|
||||||||||||
19 |
ti1 |
5 |
4 |
6 |
7 |
5 |
|
2 |
|
6 |
8 |
3 |
5 |
9 |
|
|
ti2 |
4 |
8 |
7 |
5 |
3 |
|
6 |
|
2 |
3 |
5 |
2 |
4 |
|
|
|
|
|
|
|
|||||||||||||
|
|
|
|
|
||||||||||||
20 |
ti1 |
2 |
8 |
4 |
5 |
6 |
|
4 |
|
3 |
6 |
3 |
7 |
5 |
|
|
ti2 |
5 |
3 |
2 |
6 |
4 |
|
3 |
|
7 |
8 |
4 |
3 |
2 |
|
|
|
|
|
|
|
|||||||||||||
|
|
|
|
|
||||||||||||
21 |
ti1 |
7 |
4 |
5 |
3 |
8 |
|
9 |
|
2 |
6 |
5 |
4 |
3 |
|
|
ti2 |
8 |
3 |
3 |
5 |
5 |
|
4 |
|
4 |
9 |
9 |
6 |
6 |
|
|
|
|
|
|
|
|
||||||||||||
22 |
ti1 |
6 |
7 |
4 |
8 |
3 |
|
3 |
|
6 |
2 |
5 |
4 |
2 |
|
|
ti2 |
5 |
4 |
7 |
3 |
5 |
|
6 |
|
4 |
7 |
8 |
5 |
8 |
|
|
|
|
|
|
|
|
||||||||||||
23 |
ti1 |
9 |
3 |
2 |
7 |
5 |
|
4 |
|
2 |
6 |
4 |
3 |
3 |
|
|
ti2 |
8 |
5 |
7 |
2 |
6 |
|
2 |
|
3 |
7 |
9 |
6 |
8 |
|
|
|
|
|
|
|
|
||||||||||||
24 |
ti1 |
6 |
3 |
5 |
2 |
4 |
|
7 |
|
8 |
5 |
3 |
6 |
4 |
|
|
ti2 |
9 |
4 |
8 |
5 |
3 |
|
2 |
|
4 |
7 |
6 |
3 |
5 |
|
|
|
|
|
|
|
|
||||||||||||
25 |
ti1 |
6 |
3 |
8 |
5 |
7 |
|
3 |
|
2 |
9 |
6 |
8 |
5 |
|
|
ti2 |
8 |
7 |
5 |
2 |
9 |
|
8 |
|
4 |
7 |
5 |
2 |
3 |
|
|
|
|
|
|
|
|
||||||||||||
26 |
ti1 |
2 |
4 |
6 |
5 |
2 |
|
7 |
|
4 |
3 |
5 |
8 |
4 |
|
|
ti2 |
4 |
3 |
2 |
7 |
6 |
|
5 |
|
5 |
4 |
6 |
3 |
9 |
|
|
|
|
|
|
|
|
||||||||||||
27 |
ti1 |
8 |
3 |
5 |
9 |
7 |
|
4 |
|
2 |
8 |
6 |
3 |
9 |
|
|
ti2 |
4 |
6 |
3 |
8 |
6 |
|
5 |
|
7 |
9 |
5 |
4 |
6 |
|
|
|
|
|
|
|
|
||||||||||||
28 |
ti1 |
7 |
4 |
3 |
6 |
8 |
|
8 |
|
5 |
6 |
4 |
9 |
3 |
|
|
ti2 |
4 |
7 |
6 |
3 |
5 |
|
2 |
|
8 |
9 |
6 |
5 |
7 |
|
|
|
|
|
|
|
|
8
табл. 24). У протоколі фіксуються результати вимірювань групи з 20 роликів (4 групи з 5 роликів). У стовпці «а» записується відхилення, що відповідає максимальному значенню діаметра ролика, у стовпці «в» – відхилення, що відповідає мінімальному значенню діаметра ролика.
Рис. 17. Схема контролю відхилення діаметра циліндричного ролика
|
|
|
|
|
|
|
|
|
|
|
|
|
|
|
|
|
|
|
Таблиця 24 |
|||||
|
Протокол перевірки відхилення діаметра циліндричних роликів |
|
|
|
||||||||||||||||||||
|
|
|
|
|
|
|
|
Протокол №___ Дата заповнення |
|
|
|
|
|
|
||||||||||
|
|
|
|
|
|
|
Цех – ___________ «__»______20__р. |
|
|
|
|
|
|
|||||||||||
|
Обладнання |
|
|
|
|
Деталь |
|
|
|
|
Операція |
|
|
|
||||||||||
|
|
|
|
|
|
|
|
|
|
|
|
|
Схема вимірю- |
|
|
|
|
|
№ |
|
||||
Найменування |
Тип |
|
Найменування |
|
вання парамет- |
|
Найменування |
|
опе- |
|||||||||||||||
|
|
|
|
|
|
|
|
|
|
|
|
|
рів, допуск |
|
|
|
|
|
рації |
|||||
шліфувальний |
|
|
|
циліндричний |
|
див. рис.16, |
|
шліфування |
|
|
|
|
||||||||||||
АШ343 |
|
|
|
ролик |
|
+0,016 |
|
ролика |
|
6 |
|
|
||||||||||||
верстат |
|
|
|
|
|
|
підшипника |
|
dн =32−0,004 |
|
за діаметром |
|
|
|
|
|||||||||
|
|
|
|
|
|
|
|
|
|
|
|
|
|
|
|
|
|
|
|
|
||||
Вимірюван- |
|
|
|
|
|
|
Прийнятий |
Загаль- |
|
Загальний |
Порядок |
|||||||||||||
|
Узгодив |
|
|
|
початковий |
ний обсяг |
|
|
обсяг |
відбору |
||||||||||||||
ня проводив |
|
|
|
|
|
|
||||||||||||||||||
|
|
|
|
|
|
розмір, мм |
групи |
|
підгрупи |
групи |
||||||||||||||
|
|
|
|
|
|
|
|
|
|
|
||||||||||||||
|
|
|
|
|
|
|
|
|
|
32 |
|
20 |
|
|
5 |
Безперервний |
|
|||||||
№ групи |
|
|
1 |
|
|
|
|
|
2 |
|
|
|
|
|
3 |
|
4 |
|
|
|
||||
Параметр |
|
|
а |
|
|
|
в |
|
а |
|
в |
|
а |
|
в |
а |
|
в |
|
|||||
|
|
|
1 |
|
|
|
|
|
|
|
|
|
|
|
|
|
|
|
|
|
|
|
|
|
Вимірю- |
2 |
|
|
|
|
|
|
|
|
|
|
|
|
|
|
|
|
|
|
|
|
|
||
3 |
|
|
|
|
|
|
|
|
|
|
|
|
|
|
|
|
|
|
|
|
|
|||
вання |
|
|
|
|
|
|
|
|
|
|
|
|
|
|
|
|
|
|
|
|
|
|||
4 |
|
|
|
|
|
|
|
|
|
|
|
|
|
|
|
|
|
|
|
|
|
|||
|
|
|
|
|
|
|
|
|
|
|
|
|
|
|
|
|
|
|
|
|
|
|
|
|
|
|
|
5 |
|
|
|
|
|
|
|
|
|
|
|
|
|
|
|
|
|
|
|
|
|
Сума |
|
|
|
|
|
|
|
|
|
|
|
|
|
|
|
|
|
|
|
|
|
|
||
|
|
|
|
|
|
|
|
|
|
|
|
|
|
|
|
|
|
|
|
|
|
|
|
|
|
Хі |
|
|
|
|
|
|
|
|
|
|
|
|
|
|
|
|
|
|
|
|
|
|
|
Хіmax |
|
|
|
|
|
|
|
|
|
|
|
|
|
|
|
|
|
|
|
|
|
|
||
Хіmin |
|
|
|
|
|
|
|
|
|
|
|
|
|
|
|
|
|
|
|
|
|
|
||
|
Ri |
|
|
|
|
|
|
|
|
|
|
|
|
|
|
|
|
|
|
|
|
|
|
|
|
|
|
|
|
|
|
|
|
|
|
|
|
|
|
|
|
|
|
|
|
|
33 |

3.Здійснити розрахунок параметрів потокової організації виробництва згідно з методикою, викладеною у [2].
4.Викреслити схему розміщення об’єктів виробництва на позиціях і коліях потоку.
Висновки
Довести доцільність вибору потокової організації виробництва та конкретного варіанта значень показників потоку, які розраховані за вихідними даними.
Література
1.Анофрієв, В. Г. Організація і планування вагоноремонтного виробництва: конспект лекцій [Текст] / В. Г. Анофрієв. – Д.: Дніпропетр. держ. техн. ун-т залізн. трансп., 2000. – 139 с.
2.Анофрієв, В. Г. Розрахунок параметрів потокової організації вагоноремонтного виробництва на персональній ЕОМ: методичні вказівки № 522 до курсового та дипломного проектування для студентів IV-V курсів спеціальності «Рухомий склад та спеціальна техніка залізничного транспорту» [Текст] / В. Г. Анофрієв, В. В. Соборницька. – Д.: Дніпропетр. держ. техн. ун-т залізн. трансп., 1999. – 28 с.
3.Скиба, И. Ф. Организация, планирование и управление на вагоноремонтных предприятиях [Текст]: учеб. для вузов ж.-д. трансп. / И. Ф. Скиба. –
М.: Транспорт, 1978. – 344 с.
Лабораторна робота № 3
Тема: Статистичний аналіз точності технологічного процессу
Мета роботи: Вивчення методів конторолю й оцінки показників точності та стабільності технологічних операцій.
Для виконання лабораторної роботи необхідно ознайомитися з теоретич-
ним матеріалом, викладеним у [1, с. 108-109], [2, с. 204-212], [3, с. 283-289].
Під час виконання цієї роботи необхідно встановити точність налаштування верстата, який виконує шліфування циліндричних роликів. Для цього через певний час (наприклад, через одну годину) перевіряють відхилення від діаметра групи роликів (4 групи з 5 роликів), щоб оцінити вплив верстата на розмір ролика, що піддається шліфуванню.
Порядок виконання роботи
1.Здійснити контроль відхилення від діаметра циліндричних роликів підшипників кочення, що встановлюються на шийці осі колісної пари, за схемою рис. 17.
2.Перевірити параметр роликів (відхилення від діаметра) у двох взаємно перпендикулярних напрямках в одному перетині за допомогою приладу В901 (408М), а результати вимірювання занести до протоколу вимірювань (див.
32
Закінчення табл. 2
№ |
№ |
1 |
2 |
3 |
4 |
5 |
6 |
7 |
8 |
9 |
10 |
11 |
|
варіанта |
дет. |
||||||||||||
|
|
|
|
|
|
|
|
|
|
|
|||
|
|
|
|
|
|
|
|
|
|
|
|
|
|
29 |
ti1 |
6 |
3 |
2 |
5 |
9 |
7 |
4 |
5 |
3 |
8 |
2 |
|
ti2 |
3 |
6 |
5 |
2 |
4 |
1 |
8 |
8 |
5 |
4 |
6 |
||
|
|||||||||||||
30 |
ti1 |
4 |
8 |
4 |
7 |
6 |
3 |
4 |
8 |
7 |
9 |
9 |
|
ti2 |
3 |
7 |
6 |
3 |
8 |
5 |
8 |
9 |
6 |
5 |
7 |
||
|
Порядок виконання роботи
1.За вихідними даними, вказаними в табл. 2, й урахуванням обмежень на виконання робіт верстатами, побудувати графік послідовності обробки деталей на двох верстатах (за осями абсцис відкласти час, за осями ординат – номери верстатів) у разі порядків обробки:
– випадкового (згідно з порядком запуску, наведеним у вихідних даних, табл. 2);
– визначеного евристичним методом із застосуванням правила minTWORK;
– визначеного евристичним методом із застосуванням правила maxTWORK;
– визначеному алгоритмом Джонсона.
2.Для кожного графіка обчислити загальний час виконання обробки 11 деталей на двох верстатах – визначити тривалість виробничого циклу обробки.
Приклад побудови графіків обробки деталей на двох верстатах
Таблиця 3
Вихідні дані
№ |
1 |
2 |
3 |
4 |
5 |
6 |
7 |
|
дет. |
||||||||
|
|
|
|
|
|
|
||
ti1 |
3 |
5 |
1 |
3 |
4 |
1 |
4 |
|
ti2 |
2 |
4 |
4 |
5 |
2 |
2 |
5 |
1. Випадковий порядок обробки деталей
Графік обробки семи деталей у разі випадкового порядку їх обробки на верстаті № 1 та № 2 (згідно з вихідними даними) має вигляд, показаний на рис. 1. Цифри над відрізками – номери робіт, під відрізками вказаний час закінчення обробки деталі за поточним часом.
9

Рис. 1. Графік послідовності обробки деталей у разі випадкового порядку обробки
Як видно з рис. 1, перерви в обробці деталей на другому верстаті складають: t1пер =3 хв, t2пер =3 хв.
Загальний час виконання робіт можна визначити графічно за формулою
nn
Т= ∑ti2 +∑tiпер →min ,
n |
|
і=1 |
i=1 |
пер |
– сумарний час простою (перерви) другого верстата; |
||
де ∑ti |
|||
і=1 |
|
|
|
T = 24 +6 =30 хв.
Перша сума залежить тільки від вихідних даних і не залежить від порядку виконання робіт. Тому для скорочення часу перерв, тобто зменшення загального часу виконання робіт, необхідно зменшити суму інтервалів простою другого верстата.
2. Евристичний алгоритм, що застосовує правило minTWORK
Табл. 3 з вихідними даними доповнюємо двома рядками: в одному записуємо загальну тривалість обробки деталей обома верстатами (Σ), а в іншому вказуємо послідовність обробки деталей згідно з правилом minTWORK і позначаємо римськими цифрами. У результаті отримуємо табл. 4.
Таблиця 4
Послідовність обробки виробів за правилом minTWORK
№ дет. |
1 |
2 |
3 |
4 |
5 |
6 |
7 |
ti1 |
3 |
5 |
1 |
3 |
4 |
1 |
4 |
ti2 |
2 |
4 |
4 |
5 |
2 |
2 |
5 |
Σ |
5 |
9 |
5 |
8 |
6 |
3 |
9 |
minTWORK |
II |
VI |
III |
V |
IV |
I |
VII |
Послідовність обробки деталей, отриману за правилом minTWORK, наведено на рис. 2.
10
позицій, тобто Q ≥ 2, і мінімального розміру транспортної партії k = 1. Тоді мінімальна кількість виробів, що має випускатися на потоці, складає
Nріч = 2 1 ТFн.річ .
Це нерівняння можна використовувати під час вирішення питання щодо доцільності впровадження потокового методу на конкретній дільниці виробництва. Знаючи змінний або місячний фонд часу роботи потокової лінії та простій об’єктів у ремонті, можна знайти мінімальний випуск їх, доцільний для організації потокового виробництва.
Вихідні дані
У табл. 23 наведені дані з річної програми ремонту та простою у ремонті вагонів у вагоноскладальному цеху ВРЗ.
Таблиця 23
Річна програма та простій вагонів у ремонті у вагоноскладальному цеху ВРЗ
варіанта№ |
Типвагона |
Річна |
ремонтуВид |
Простійу ремонті ,Тгод |
варіанта№ |
|
Річна |
ремонтуВид |
Простійу ремонті ,Тгод |
|
Nріч |
||||||||
|
|
|
|
|
|
про- |
|
|
|
|
|
програма |
|
|
|
Тип |
грама |
|
|
|
|
ремонту |
|
|
|
ремон- |
|
|
|
|
|
вагонів |
|
|
|
вагона |
ту ва- |
|
|
|
|
Nріч |
|
|
|
|
гонів |
|
|
1 |
ЦМК |
300 |
КР-2 |
128 |
16 |
критий |
6000 |
КР |
8 |
2 |
ЦМК |
350 |
КР-2 |
136 |
17 |
піввагон |
5500 |
КР |
8 |
3 |
ЦМК |
900 |
КР-1 |
64 |
18 |
платформа |
7000 |
КР |
8 |
4 |
ЦМО |
1000 |
КР-1 |
72 |
19 |
критий |
7000 |
КР |
7 |
5 |
ЦМО |
1100 |
КР-1 |
78 |
20 |
піввагон |
6000 |
КР |
9 |
6 |
ЦМО |
1200 |
КР-1 |
84 |
21 |
платформа |
5000 |
КР |
9 |
7 |
ЦМК |
400 |
КР-2 |
144 |
22 |
критий |
6500 |
КР |
8 |
8 |
ЦМО |
750 |
КР-1 |
100 |
23 |
піввагон |
7000 |
КР |
7 |
9 |
ЦМО |
450 |
КР-2 |
156 |
24 |
платформа |
6000 |
КР |
7 |
10 |
ЦМК |
950 |
КР-1 |
96 |
25 |
критий |
7500 |
КР |
8 |
11 |
ЦМК |
850 |
КР-1 |
110 |
26 |
піввагон |
8000 |
КР |
8 |
12 |
ЦМО |
1050 |
КР-1 |
112 |
27 |
платформа |
5500 |
КР |
6 |
13 |
ЦМК |
250 |
КР-2 |
168 |
28 |
критий |
8000 |
КР |
9 |
14 |
ЦМК |
200 |
КР-2 |
184 |
29 |
піввагон |
7500 |
КР |
8 |
15 |
ЦМО |
500 |
КР-2 |
172 |
30 |
платформа |
6500 |
КР |
6 |
Порядок виконання роботи
1.Визначити річний фонд часу Fнг [2].
2.Обґрунтувати доцільність упровадження потокового методу ремонту вагонів, застосовуючи відповідне нерівняння і таблицю вихідних даних, згідно із заданим варіантом.
31