
Sb96252
.pdfТехнологическая оснастка в основном универсальная, однако, во многих случаях (особенно в крупносерийном производстве) создается высокопроизводительная специальная оснастка. Большое значение имеет универсальносборная, переналаживаемая технологическая оснастка, позволяющая существенно повысить коэффициент оснащенности серийного производства.
Вкачестве исходных заготовок используется горячий и холодный прокат, литье в песчаные формы и под давлением, точное литье, поковки. Требуемая точность достигается как методами автоматического получения размеров, так и методами пробных ходов и промеров с частичным применением разметки.
Средняя квалификация рабочих выше, чем в массовом производстве, но ниже, чем в единичном. Наряду с рабочими высокой квалификации, работающими на сложных универсальных станках, и наладчиками используются рабочие-операторы, работающие на настроенных станках.
Взависимости от объема выпуска и особенностей изделий обеспечивается полная взаимозаменяемость, неполная, групповая.
Технологическая документация и техническое нормирование подробно разрабатываются для наиболее сложных и ответственных заготовок при одновременном применении упрощенной документации и опытностатистического нормирования простейших заготовок.
1.4. Методы достижения заданной точности обработки
Под точностью детали понимается ее соответствие требованиям чертежа: по размерам, геометрической форме, правильности взаимного расположения обрабатываемых поверхностей и по степени их шероховатости.
Заданную точность обработки заготовки можно достигнуть одним из двух принципиально отличных методов: пробных ходов и промеров, а также методом автоматического получения размеров на настроенных станках.
1.4.1. Метод пробных ходов и промеров
Сущность метода заключается в том, что к обрабатываемой поверхности заготовки, установленной на станке, подводят режущий инструмент и с короткого участка заготовки снимают пробную стружку. После этого станок останавливают, делают пробный замер полученного размера, определяют величину его отклонения от чертежного и вносят поправку в положение инструмента, которую отсчитывают по делениям лимба станка. Затем вновь производят пробную обработку («ход») участка заготовки, новый пробный
11
замер полученного размера и при необходимости вносят новую поправку в положение инструмента. Таким образом, путем пробных ходов и промеров устанавливают правильное положение инструмента относительно заготовки, при котором обеспечивается требуемый размер. После этого выполняют обработку заготовки по всей ее длине. При обработке следующей заготовки всю процедуру установки инструмента пробными ходами и промерами повторяют.
В методе пробных ходов и промеров часто применяют разметку. В этом случае на поверхность исходной заготовки специальными инструментами (чертилками, штангенрейсмусом и др.) наносят тонкие линии, показывающие контур будущей детали, положение центров будущих отверстий или контуры выемок и окон. При последующей обработке рабочий стремится совместить траекторию перемещения режущего лезвия инструмента с линией разметки и обеспечить тем самым требуемую форму обрабатываемой поверхности.
Метод пробных ходов и промеров имеет следующие достоинства:
•На неточном оборудовании он позволяет получить высокую точность обработки. Рабочий высокой квалификации посредством пробных промеров
иходов может определить и устранить погрешность заготовки.
•При обработке партии мелких заготовок исключается влияние износа режущего инструмента на точность выдерживаемых при обработке размеров. При пробных промерах и ходах определяют и вносят необходимую поправку в положение инструмента, связанную с его износом.
•При неточной заготовке возможно правильно распределить припуск и предотвратить появление брака. Из маломерной заготовки при разметке часто удается выкроить контур обрабатываемой заготовки и получить годное изделие.
•Метод освобождает рабочего от необходимости изготовления сложных
идорогостоящих приспособлений типа кондукторов, поворотных и делительных приспособлений и др. Положение центров отверстий и взаимное расположение обрабатываемых поверхностей предопределяется разметкой.
Вместе с тем метод пробных ходов и промеров имеет ряд существенных недостатков:
•Зависимость достигаемой точности обработки от минимальной толщины снимаемой стружки. При токарной обработке доведенными резцами эта толщина не меньше 0,005 мм, а при обработке заточенными резцами она составляет 0,02 мм. При работе пробными ходами рабочий не может внести в размер заготовки поправку менее толщины снимаемой стружки, а следова-
12
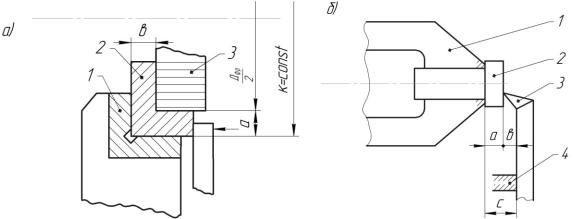
тельно, и гарантировать получение размера с погрешностью, меньшей этой толщины.
•Появление брака по вине рабочего, от внимания которого в значительной степени зависит достигаемая точность обработки.
•Низкая производительность обработки из-за больших затрат времени на пробные ходы, промеры и разметку.
•Высокая себестоимость обработки детали вследствие низкой производительности обработки в сочетании с высокой квалификацией рабочего, требующей повышенной оплаты труда.
Метод пробных промеров и ходов используется, как правило, при единичном и мелкосерийном производстве изделий, в опытном производстве, а также в ремонтных и инструментальных цехах. При серийном производстве этот метод находит применение для получения годных деталей из неполноценных исходных заготовок («спасение» брака по литью и штамповке).
В условиях крупносерийного и массового производства метод пробных ходов и промеров используется главным образом при шлифовании, так как позволяет без труда компенсировать износ абразивных инструментов, часто протекающий неравномерно и вызывающий потерю точности обработки.
1.4.2. Метод автоматического получения размеров на настроенных станках
При обработке заготовок по методу автоматического получения размеров станок предварительно настраивается так, чтобы требуемая от заготовки точность достигалась автоматически, т. е. почти независимо от квалификации и внимания рабочего.
Рис. 1.4
Например, при фрезеровании заготовки 2 до размеров a и b (рис. 1.4, а) стол фрезерного станка предварительно устанавливают по высоте таким образом, чтобы опорная поверхность неподвижной губки 1 тисков отстояла от
13
оси вращения фрезы на расстояние K Dф0 2 a. При этом боковую по-
верхность фрезы 3 удаляют (поперечным перемещением стола) от вертикальной поверхности неподвижной губки на расстояние b. Эту предварительную настройку станка производят по методу пробных ходов и промеров. После такой настройки выполняют обработку всей партии заготовок без их промежуточных промеров (исключая выборочные контрольные промеры) и без дополнительных перемещений стола станка в горизонтальном и вертикальном направлениях. Так как в процессе обработки размеры К и b остаются неизменными, то и точность размеров а и b сохраняется одинаковой для всех заготовок, обработанных с данной настройкой станка.
При подрезке на токарном станке торца заготовки 2 (рис. 1.4, б) размер а заготовки определяется расстоянием с от торца зажимного приспособления 1 до поверхности упора 4, ограничивающего перемещение подрезного резца 3, а также расстоянием b от поверхности упора 4 до вершины режущего лезвия резца. При постоянстве этих размеров, устанавливаемых в процессе предварительной настройки станка, точность размера а сохраняется неизменной.
Рассмотренные примеры показывают, что при использовании метода автоматического получения размеров на настроенных станках задача обеспечения требуемой точности обработки переносится с рабочего-оператора на настройщика, выполняющего предварительную настройку станка; на инструментальщика, изготовляющего специальные приспособления, и на технолога, назначающего технологические базы и размеры заготовки.
К преимуществам метода автоматического получения размеров относятся:
•Повышение точности обработки и снижение брака. Точность обработки не зависит от минимально возможной толщины снимаемой стружки (так как припуск на обработку устанавливают заведомо больше этой величины) и от квалификации и внимательности рабочего.
•Рост производительности обработки за счет устранения потерь времени на предварительную разметку заготовки и осуществление пробных ходов
ипромеров. Кроме того, специалист, работающий на настроенном станке по упорам, а не пробным промерам, производит работу более уверенно и спокойно; что способствует меньшей утомляемости.
•Рациональное использование рабочих высокой квалификации. Работу на настроенных станках могут производить ученики и малоквалифицирован-
14
ные рабочие-операторы; высококвалифицированные рабочие выполняют настройку станков и обслуживают одновременно по 8–12 станков.
•Повышение экономичности производства. Высокая производительность труда, снижение брака, уменьшение потребности в высококвалифицированной рабочей силе способствуют снижению производственных затрат.
Метод автоматического получения размеров на настроенных станках широко применяется в условиях серийного и массового производства. Использование этого метода в условиях мелкосерийного производства ограничивается экономическими соображениями:
•потери времени на предварительную настройку станков могут превзойти выигрыш времени от автоматического получения размеров;
•затраты на изготовление однородных и точных исходных заготовок могут не окупиться при малых количествах выпускаемой продукции;
•тщательная технологическая подготовка производства с подробной разработкой технологических процессов и схем настройки станков неосуществима в условиях мелкосерийного и многономенклатурного производства.
1.5. Концентрация и дифференциация операций
Концентрацией (укрупнением) операций называется соединение не-
скольких простых технологических переходов в одну сложную операцию. Технологический процесс, построенный по принципу концентрации операций, состоит из небольшого числа сложных операций.
Концентрация операций может осуществляться:
•объединением в одной операции предварительных (черновых, промежуточных) и окончательных (чистовых) переходов;
•объединением в одной операции нескольких простых переходов;
•заменой нескольких установов позициями;
•заменой простых одноинструментальных переходов сложными совмещенными переходами с многоинструментальной и многолезвийной обработкой одной или нескольких поверхностей.
Достоинства концентрации операций:
•Повышается точность взаимного расположения поверхностей, обрабатываемых на одном установе.
•Повышается производительность обработки за счет совмещения во времени нескольких технологических переходов и сокращения основного времени.
15
•Повышается производительность за счет сокращения затрат вспомогательного времени (в первую очередь на установку и снятие заготовок, на смену инструмента, на включение и выключение станка).
•Сокращается длительность производственного цикла за счет уменьшения межоперационного пролеживания, связанного с уменьшением общего числа технологических операций.
•Сокращается объем незавершенного производства, что приводит к повышению оборачиваемости оборотных средств.
•Упрощается календарное планирование производства.
При построении операций по принципу концентрации возрастают требования к точности и технологическим возможностям станков и к квалификации рабочих.
Дифференциацией (раздроблением) операций называется построение операций из небольшого числа простых технологических переходов. Технологический процесс, построенный по принципу дифференциации операций, состоит из большого числа простых операций.
Впроизводстве используются оба принципа построения технологических процессов, которые выбираются технологами в зависимости от конкретных условий производства.
Достоинства дифференциации операций в первую очередь связаны с возможностью отделения сложной и точной чистовой обработки, требующей высокой квалификации рабочих и высокоточных станков, от предварительной неточной обработки, которая может быть осуществлена простейшими и высокопроизводительными способами на простых и дешевых станках рабочими средней квалификации.
Степень дифференциации зависит от серийности производства, и в условиях крупносерийного производства может стать экономически целесообразным построение технологического процесса из большого числа простейших операций.
Вусловиях единичного и мелкосерийного производств обычно проектируются концентрированные операции, выполняемые высококвалифицированными рабочими. В условиях крупносерийного и массового производств применяется дифференциация операций.
1.6. Типовые и групповые технологические процессы
При всем разнообразии деталей приборостроительного производства среди них можно обнаружить большое количество деталей аналогичной кон-
16
фигурации, близких по точности, материалам, требованиям, предъявляемым к качеству обработки их основных поверхностей, а также сравнительно мало отличающихся по размерам. Вместе с тем очень часто такие детали изготавливаются на разных предприятиях, в разных цехах (а иногда и в одном цехе), на различном оборудовании из разных исходных заготовок, различными технологическими методами при неодинаковой производительности и экономичности обработки.
1.6.1. Сущность типизации и классификации
Типизация обеспечивает устранение многообразия технологических процессов обоснованным сведением их к ограниченному числу типов. Осуществление типизации технологических процессов для сходных по конфигурации и технологическим особенностям деталей предусматривает их изготовление по одинаковым технологическим процессам, основанным на применении наиболее совершенных способов обработки, обеспечивающих достижение наивысшей производительности и экономичности производства.
Типовой технологический процесс в соответствии с [2] разрабатывается в конкретных производственных условиях типового представителя группы изделий, обладающих общими конструктивно-технологическими признаками.
Работа по типизации технологических процессов начинается с проведения классификации. В основу классификации положены связи между конструктивными элементами деталей и возможными технологическими методами их обработки.
Механическая и любая другая обработка деталей приборов связана с формообразованием и изменением свойств поверхностей деталей. Поэтому первым признаком классификации деталей является форма обрабатываемых поверхностей.
Вся обработанная поверхность детали представляет систему отдельных поверхностей. Вторым признаком классификации деталей является сочетание обрабатываемых поверхностей (их взаимное расположение, точность обработки и размеры отдельных поверхностей, соотношение размеров между поверхностями и т. п.).
Конфигурация детали обобщает ряд ее признаков: отношение длины детали к ее диаметру, взаимное расположение поверхностей и др. От конфигурации детали зависит выбор технологических методов, оборудования, приспособлений, инструментов, режимов резания и т. д. Поэтому третий признак классификации – конфигурация деталей.
17
Четвертый признак классификации деталей – род материала, вид заготовок и термической обработки, так как эти признаки в значительной степени определяют технологический процесс обработки детали, выбор методов обработки, оборудования и оснастки.
Поскольку при прочих равных условиях крупные и мелкие детали не могут обрабатываться одинаково, при классификации учитываются признаки габаритных размеров деталей и поверхностей, что является пятым признаком классификации.
Кроме указанных основных признаков на построение технологического процесса большое влияние оказывают условия его осуществления. К таким условиям относятся: объем производственного задания и размеры отдельных партий обрабатываемых заготовок; производственная обстановка (оборудование, наличие инструмента, возможности инструментального цеха, расположение оборудования и т. п.).
За основу технологической классификации принимают классы, которые подразделяются на подклассы, группы и подгруппы. Разбивка классов на группы и подгруппы заканчивается типом. При этом типовая технологическая операция характеризуется единством содержания и последовательности технологических переходов для группы изделий с общими конструктивными и технологическими признаками [1].
1.6.2. Групповые технологические процессы
Метод групповой обработки, созданный проф. С. П. Митрофановым [5], является развитием идей типизации технологических процессов. За основу метода так же, как и при типизации технологических процессов, принимается технологическая классификация заготовок, заканчивающаяся формированием группы.
Построение технологической классификации заготовок для групповой обработки существенно отличается от классификации заготовок, необходимой для типизации технологических процессов. Если при типизации технологических процессов в общий класс объединяются заготовки по принципу общности их конфигурации, технологического маршрута и содержания отдельных операций, то при групповой обработке под классом понимается совокупность деталей, характеризуемая общностью типа оборудования, необходимого для обработки заготовки в целом или отдельных ее поверхностей.
Таким образом, при групповой обработке создают классы заготовок по видам обработки (изготавливаемые на токарных, револьверных, фрезерных,
18

сверлильных станках, а также получаемые литьем, холодной и горячей штамповкой и т. п.). Создание классов является предварительным этапом подготовки групповой обработки. Основной задачей является формирование групп.
Основным признаком для объединения заготовок в группы по отдельным технологическим операциям является общность обрабатываемых поверхностей или их сочетаний.
В связи с тем, что из большого количества отдельных поверхностей при их различных сочетаниях может быть образована разнообразная конфигурация заготовок, в состав группы могут и действительно часто включаются заготовки различной конфигурации (рис.1.5, 1.6). В этом смысле понятие группы значительно шире понятия типа заготовок, являющегося основой построения типового процесса.
Под типом понимается совокупность конструктивно подобных заготовок, отличающихся только размерами; заготовки одного типа имеют одинаковый технологический маршрут и содержание отдельных операций, что не является обязательным для группы заготовок.
Рис. 1.5
Рис. 1.6
При формировании группы заготовок учитываются следующие признаки:
19
•общность элементов, составляющих конфигурацию заготовки, а, следовательно, и общность поверхностей, подлежащих обработке (цилиндрическая наружная, цилиндрическая внутренняя, коническая поверхности, фаски, резьба, канавка, торцовые поверхности и т. п.);
•точность и шероховатость обрабатываемых поверхностей;
•однородность исходной заготовки и обрабатываемого материала, позволяющая осуществление обработки одинаковыми способами и общими режущими инструментами;
•близость размеров исходных заготовок, позволяющая их обрабатывать на одном и том же оборудовании, в однотипных приспособлениях;
•серийность выпуска заготовок и трудоемкость их обработки.
Групповой технологической операцией называется общая для группы
различных по конструктивным признакам заготовок операция, выполняемая с определенной групповой оснасткой, обеспечивающей обработку заготовки на данном оборудовании.
Групповым технологическим процессом называется совокупность груп-
повых технологических операций, обеспечивающих обработку различных заготовок группы по общему технологическому маршруту. При групповом технологическом маршруте некоторые заготовки могут пропускать отдельные операции.
Группа заготовок создается для выполнения операции на одном и том же станке при его неизменной наладке. В отдельных случаях при переходе к обработке другой заготовки данной группы допускается незначительная подналадка станка, однако она должна быть осуществлена с минимальной затратой времени (замена сверл, перестановка линейных и диаметральных упоров и т. п.).
Схему групповой наладки станка разрабатывают для наиболее сложной заготовки группы, включающей в себя все поверхности, встречающиеся в остальных заготовках. Если среди более простых заготовок группы встречаются отдельные поверхности (например, конус, фаска), отсутствующие в других заготовках, то эти поверхности искусственно добавляют в чертеж. Такая усложненная заготовка называется комплексной.
На рис. 1.7 приведена схема создания комплексной заготовки искусственным объединением отдельных поверхностей более простых заготовок группы. Настройка станка, осуществленная для комплексной заготовки, дает возможность без серьезной переналадки обработать любую заготовку группы. Создание комплексных заготовок удобно для групповой наладки станков
20