
Лекции / Лекция 5
.pdf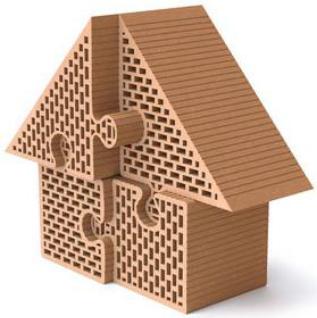
«Архитектура, как музыка в камне, звучит в веках» (Мордвинов А.Г.)
Лекция №5
СТРОИТЕЛЬНАЯ
КЕРАМИКА
1.Общие сведения и классификация
2.Сырье для производства керамики
3.Основы производства керамических изделий
4.Способы улучшения внешнего вида керамических изделий
5.Стеновые материалы и изделия
6.Изделия для внешней и внутренней облицовки
7.Специальные керамические материалы и изделия
1. Общие сведения и классификация
В понятие строительная керамика входит огромное количество материалов и изделий с различными свойствами и назначением, которые используются при строительстве жилых, общественных и промышленных зданий. Керамикой (от греч. keramos – глина и keramikos – гончарное искусство) принято называть изделия из обожжённой глины. Материал (тело), из которого состоят керамические изделия после обжига, в технологии керамики называют керамическим черепком или просто черепком. Керамический черепок представляет собой искусственный камень, образовавшийся во время обжига в результате спекания керамических масс при соответствующей температуре.
Пр и м е ч а н и е ‒ Другая версия ‒ керамика (греч. keramike – гончарное искусство, от keramos
‒глина) ‒ наименование любых изделий, выполненных из глины или содержащих глину смесей, обожженных в печи или высушенных на солнце, т.е. все гончарные изделия, терракота, майолика, фаянс, фарфор, кирпич и др.
Изделия строительной керамики классифицируют по структуре образующегося после обжига черепка, составу масс, назначению и другим признакам. По структуре черепка керамические изделия различают:
1
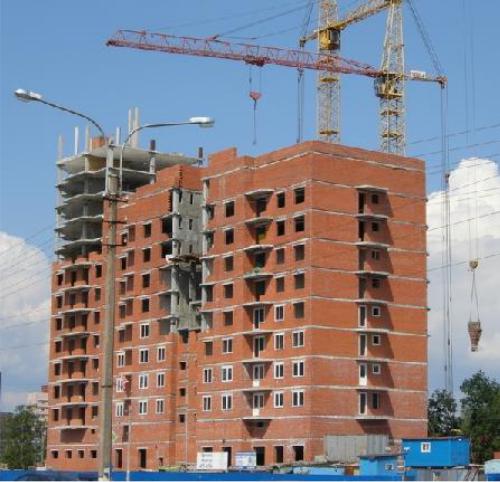
пористые – водопоглощение по массе превышает 5%, преимущественно 8…20%.
Кним относят кирпич и камни керамические, черепицу, фаянсовые изделия;
плотные (со спёкшимся черепком) – водопоглощение составляет менее 5%, чаще 2…4%. Такой черепок практически водонепроницаем. К изделиям с плотным черепком относят плитки для пола, керамический гранит, клинкер, фарфоровые изделия. Однако абсолютно плотные керамические изделия не выпускаются, так как испаряющаяся вода затворения, вводимая в глиняное тесто, всегда оставляет некоторое количество микро-, макропор и капилляров.
Условно керамику подразделяют на «грубую», имеющую неоднородное строение, и «тонкую» – с мелкокристаллическим однородным строением. Граница между ними проходит по диаметру частиц 0,1…0,2 мм. К грубой керамике относится большая часть строительных материалов (кирпич, черепица, огнеупоры). К тонкой керамике относят фарфор, полуфарфор, фаянс, майолику.
По назначению керамику подразделяют на художественно-декоративную, хозяйственную, техническую и строительную (рис. 5.1).
Рис. 5.1. Строительство современного кирпичного здания
П р и м е ч а н и е ‒ 1. Фарфор представляет собой особый вид гончарного изделия. Настоящий фарфор получают из специальных сортов глины, полевых шпатов и кварца или кварцевых заменителей. В основе своей фарфор белый (иногда с голубоватым оттенком), с низким водопоглощение (до
2
0,2%), в тонких слоях просвечивающийся, обладает стекловидным спекшимся черепком, при ударе издает высокий мелодичный звук.
2. Строительная керамика является древнейшим строительным материалом и насчитывает не одну тысячу лет. Здания и сооружения из керамического кирпича строили ещё в III…I тысячелетиях до нашей эры. Принято считать, что возраст керамического кирпича как строительного материала составляет более 5 тыс. лет. Сведения о нем есть даже в Библии и Ветхом завете. В Белоруссии кирпич в виде плинфы (плоский кирпич) использовался при строительстве СпасоЕвфросиньевского монастыря в г. Полоцке (ХII в.). Из черепицы выполнялось покрытие кровли двор- цово-замкового ансамбля Радзивиллов в г. Несвиже (ХVI в.) и других строительных сооружений. В настоящее время керамика тоже продолжает оставаться одним из основных строительных материалов, применяемых практически во всех конструктивных элементах зданий и сооружений. Вряд ли какой-либо другой вид фасада настолько гармонично объединяет окружающий нас ландшафт и архитектуру, как из натурального кирпича или других керамических материалов и изделий. И, тем не менее, из кирпича сегодня строят меньше, чем, например, 50 лет назад.
По назначению строительные керамические материалы и изделия подразделяют на: стеновые, для внешней и внутренней облицовки, санитарно-технические, кровельные, заполнители для бетонов и специальную керамику.
2. Сырье для производства керамики
Основным сырьём для производства керамических изделий являются глины различного химико-минералогического состава и генетического происхождения, их смеси и соединения с минеральными и органическими добавками – отощающими, пластифицирующими, флюсующими, порообразующими и другими (ГОСТ 9169 и 7032).
Глины образовались в результате выветривания изверженных полевошпатовых горных пород. Процесс выветривания горной породы заключается в механическом разрушении и химическом разложении. Механическое разрушение происходило в результате воздействия попеременных температур и воды, химическое разложение – при воздействии на полевой шпат воды и углекислоты.
В результате образовались минералы – водные алюмосиликаты различного со-
става:
каолинит (по названию местности в Китае – Као-Линь, где впервые нашли такую глину). Чистый каолинит (Al2O3∙2SiO2∙2H2O) имеет белоснежный вид, а при наличии в нем примесей (кварца, полевого шпата, оксидов металлов) – серо-жёлтый и другие цвета. Глины с преобладающим содержанием каолинита (каолины), имеют светлую окраску, слабо набухают при взаимодействии с водой, характеризуются тугоплавкостью, мало пластичны и мало чувствительны к сушке. После обжига сохраняют белый цвет;
монтмориллонит Al2O3∙4SiO2∙nH2O – по цвету белый с сероватым оттенком. Глины, содержащие монтмориллонит, обладают высокими сорбционными свойствами, при смачивании водой сильно набухают, весьма пластичны, при формовании склонны
3
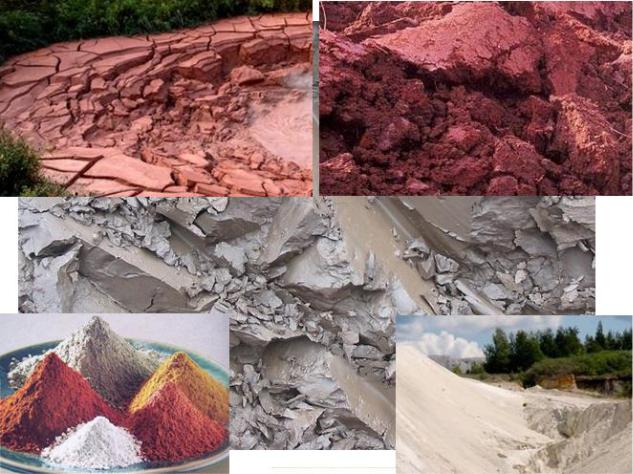
к свилеобразованию, чувствительны к сушке и обжигу с проявлением искривления изделий и растрескивания;
галлуазит Al2O3∙2SiO2∙3H2O ‒ по составу близок к каолиниту, от которого отличается более высоким содержанием воды. Цвет белый, серый, голубоватый. Имеет низкую формуемость, выражающуюся в растрескивании изделий в процессе формования и сушки. Изделия из галлуазита должны сохнуть медленно, чтобы упредить усадочные процессы.
Рис. 5.2. Разновидности глин
П р и м е ч а н и е ‒ Высокодисперсные глинистые породы с преобладающим содержанием монтмориллонита называют бентонитами. Содержание в них частиц размером менее 0,001 мм достигает 85…90%.
Химический состав глин выражается содержанием и соотношением различных оксидов, зависит от минерального состава и колеблется в широких пределах. По химическому составу глины разделяют на мономинеральные (состоящие из одного минерала) и полиминеральные (состоящие из нескольких минералов). Примером мономинеральных глин являются каолиновые глины, состоящие полностью из минерала каолинита. Основными компонентами глин являются глинозем Al2O3, кремнезем SiO2, оксиды щелочных и щелочноземельных металлов K2O, Na2O, CaO, MgО и оксиды Fe и Ti.
4
Помимо указанных соединений в состав глин могут входить органические вещества, растительные и животные остатки. В обычных глинах полиминерального состава содержится глинистых минералов 45…60%, кварца – 25…35%, карбонатов – 2…8% и органических примесей от 2…4% и более.
Изменение химического состава глин заметно отражается на их свойствах, а соответственно и на технических характеристиках изделий. С увеличением глинозёма повышается пластичность и огнеупорность глин, а с повышением содержания кремнезёма пластичность глин снижается, увеличивается пористость, снижается прочность изделий. Оксиды калия и натрия являются сильными плавнями, оксиды Fe2O3 и TiO2 свыше 2% придают глине после обжига красноватый цвет, а при 5% и выше – темнокрасный. CaO и MgО являются сильными плавнями при t>1000 . Наличие в составе оксидов железа снижает огнеупорность глин, щелочей – ухудшает их формуемость.
Глины отличаются тонкой дисперсностью. Размер частиц глинистых минералов не превышает 0,005 мм и благодаря своей гидрофильности и огромной удельной поверхности они активно поглощают и удерживают воду. Именно глинистые минералы придают глине такие свойства как пластичность при увлажнении, прочность при высыхании и способность к спеканию при обжиге.
Другие компоненты, входящие в состав глин, такие как минералы кварца, карбонатов кальция и магния и т. п., тоже, хотя и в меньшей степени, влияют на её технологические свойства и качество готовых изделий. Полезными примесями в глинах являются оксиды щелочных металлов (K2O, Na2O), которые понижают температуру обжига изделий и придают им большую прочность.
П р и м е ч а н и е ‒ Присутствие в глинах тонкодисперсного известняка придает светлую окраску и понижает огнеупорность глин, а камневидные включения известняка являются причинами появления «дутиков» и трещин в керамических изделиях.
Качественными характеристиками глин для производства керамических изделий строительного назначения являются пластичность, набухание, связующая способность, спекаемость, огнеупорность, усадка при сушке и обжиге и др.
Пластичность глин характеризуется их способностью образовывать при затворении водой тесто, которое под воздействием внешних нагрузок может принимать определенную форму и сохранять её после устранения этих нагрузок. По степени пластичности различают глины:
высокопластичные содержат в своем составе до 3…5% песка и называются жирными, поскольку в замоченном состоянии дают осязательное ощущение жирного вещества и скользкие на ощупь. Они легко формуются, но имеют высокую водопотребность (более 28%) и, как следствие, дают большую усадку при сушке (10…15%) и растрескиваются;
малопластичные (тощие) – содержание песка составляет до 30%. На ощупь та-
кие глины шероховатые, с матовой поверхностью, и при трении пальцем легко крошат-
5
ся, отделяя землистые пылинки. Они плохо поддаются формовке, требуют мало воды затворения (менее 20%) и, как следствие, дают небольшую усадку (5…7%). Для повышения пластичности глин применяют операцию вылеживания их во влажном состоянии на воздухе, вымораживание, обработку паром. В результате происходит разрыхление, повышается дисперсность;
средней пластичности – водопотребность 20…28%, усадка при сушке 7…10%.
Различают также умеренно пластичные и непластичные глины, не образующие пластичного теста. Пластичность зависит от минералогического состава и дисперсности глин.
Набухание – способность глин увеличиваться в объёме при перемешивании с водой. Зависит от зернового и минералогического состава. Монтмориллонитовые глины набухают сильнее, чем каолинитовые.
Связующая способность глин определяется их возможностью связывать частицы непластичных материалов (песка, шамота и др.) и образовывать при высыхании достаточно прочные изделия заданной формы (сырец). Более высокой связностью обладают глины с повышенным содержанием глинистых частиц.
Сушка и обжиг керамических изделий сопровождается уменьшением объёма, называемым усадкой. Усадку выражают в процентах от первоначального размера изделий. Различают воздушную, огневую и полную усадку керамических изделий.
Воздушная усадка происходит при сушке сырых керамических изделий в результате удаления влаги и сближения глинистых частиц. В зависимости от вида глин она может достигать 10%.
Огневая усадка происходит в процессе обжига керамических изделий в результате плавления и действия сил поверхностного натяжения, что сближает глинистые частицы. В зависимости от вида глин она составляет 2…8%, но может достигать и 14%. Огневая усадка возрастает с увеличением содержания глинистой фракции. Сильно запесоченные глины могут и не давать усадки и даже обнаруживать в обжиге «рост».
Полная усадка, это сумма величин воздушной и огневой усадок и может достигать 8…18%. Учитывается полная усадка при формовании сырых изделий с целью получения готовой продукции нужных размеров.
Спекаемость глин – это способность при обжиге уплотняться с образованием твердого камнеподобного черепка. Спекание глин происходит вследствие склеивания твердых частиц жидкой расплавленной фазой – силикатными расплавами. Результатом процесса спекания является уплотнение обжигаемого материала и, как следствие, уменьшение открытой пористости. Степень спекания контролируется водопоглощением черепка. Спекшийся черепок должен иметь водопоглощение не более 5%. В зависимости от температуры спекания различают низкотемпературные (температура спека-
ния до 1100°С), среднетемпературные (1101…1300°С) и высокотемпературные гли-
ны (выше 1300°С).
6
Огнеупорность глин характеризуется способностью противостоять, не расплавляясь, воздействию высоких температур. Различают огнеупорные глины (с показателем огнеупорности 1580°С) тугоплавкие (1350…1580°С) и легкоплавкие (до 1350°С). Огнеупорность глин тем выше, чем меньше у них примесей. У чистого каолинита она составляет 1870°С. Понизить огнеупорность глин можно добавкой плавней (флюса).
При производстве керамических изделий в глины, как правило, вводят различные добавки. По назначению их подразделяют на отощающие, порообразующие, пластифицирующие, специальные и плавни.
Отощающие добавки вводят, как правило, в жирные глины. Они уменьшают количество воды затворения, что сокращает размеры усадки при сушке и обжиге, облегчают формовочный процесс и устраняют брак. В качестве таких добавок используют кварцевый песок, шамот (глина, обожженная до потери пластичности), дегидратированную глину (продукт частичного удаления химически связанной воды), бой фарфора и фаянса, золу, молотые шлаки и др.
Порообразующие добавки вводят с целью снижения плотности и теплопроводности керамических изделий. Они одновременно являются и отощающими добавками. По виду воздействия на керамический черепок различают выгорающие добавки (древесные опилки, угольный порошок, торфяная пыль и т. п.) и диссоциирующие – с выделением газа, например, СО2 (молотый мел, доломит и др.).
Пластифицирующие добавки вводят в тощие глины с целью повышения их пластичности. Например, поверхностно-активные вещества СДБ (0,1...0,3%), ЛСТ, высокопластичные бентонитовые глины и другие вещества.
Иногда в глины вводят специальные добавки. Например, с целью повышения кислотостойкости вводят песчаные смеси, затворённые жидким стеклом. Для придания определенного цвета керамическому черепку вводят оксиды металлов, для улучшения качества изделий – пирофосфаты и полифосфаты натрия и т. д.
Плавни вводят в керамические массы с целью понижения температуры спекания. К ним относят материалы, которые в процессе обжига взаимодействуют с глинистым веществом с образованием более легкоплавких соединений, чем глинистое вещество. Для этого используют стеклобой, полевые шпаты, перлит, мел, доломит, тальк и др.
3. Основы производства керамических изделий
Несмотря на многообразие керамических материалов и изделий по виду сырья, технологии, свойствам, формам и назначению, основные технологические операции по их изготовлению являются общими и состоят из добычи сырьевых материалов, подготовки формовочной массы, процессов формования, сушки и обжига. Отдельной операцией является подготовка корректирующих добавок.
Карьерная глина в естественном состоянии, как правило, не пригодна для изготовления керамических изделий. Поэтому проводится ее предварительная обработка
7
(естественная, механическая и др.) с целью получения необходимых технологических характеристик перед подготовкой формовочной массы. Подготовка формовочной массы заключается в дроблении, удалении вредных примесей, помоле глин и добавок, гомогенизации и при необходимости в сушке. Различают сухую подготовку (сырье размалывается и смешивается в сухом состоянии) и влажную (с добавлением воды).
П р и м е ч а н и е ‒ Естественная обработка подразумевает собой вылеживание предварительно добытой глины в течение 1…2 лет при периодическом увлажнении атмосферными осадками или искусственном замачивании и периодическом замораживании и оттаивании.
По способу формования керамических изделий различают прессованные, литые, экструдированные, штампованные и др. Выбор способа формования определяется, прежде всего, пластичностью формовочной массы, а пластичность во многом зависит от количества воды, содержащейся в смеси.
Прессованные изделия в зависимости от состава и влажности прессуемой массы тоже получают двумя способами – сухого и полусухого прессования. При сухом способе прессования влажность формуемой массы составляет 2...6%. Такие смеси (пресспорошки) получают путем предварительного смешивания и размола исходных компонентов с последующим обезвоживанием. Затем на автоматических прессах (коленорычажных или гидравлических) под высоким давлением (16…55 МПа) из пресспорошков формуют изделия, сушат до остаточной влажности 0,1…0,3% и обжигают. Прессованию полусухим способом чаще всего подвергают малопластичные порошкообразные смеси и составы с содержанием влаги 8...12%.
При литьевом способе (шликерном) глинистые компоненты распускают в воде до коллоидного состояния, а отощающие добавки и плавни диспергируют до частиц менее 0,06 мм. Рафинирование компонентов, их смешивание и гомогенизация шликерной массы происходит в водной суспензии с содержанием воды 30…33%. Полученную смесь разливают по формам (например, под размер плиток), высушивают и обжигают. Шликер применяют также для отливки сложных по конфигурации и тонкостенных изделий (санитарно-техническая, декоративная, химически стойкая керамика и др.). Литьевым способом формовки довольно трудно получить изделия идеального качества и абсолютно одинаковой толщины.
П р и м е ч а н и е ‒ Шликерная масса используется как непосредственно для изготовления изделий (литьевой способ), так и для приготовления пресспорошков (сухой способ). Для получения порошков глинистую суспензию обезвоживают, как правило, в башенных распылительных сушилках при температуре 350…450°С до остаточного водосодержания 5…9%. В результате получают однородный порошок влажностью 6±1% и размером зерен 0,24…0,32 мм сферической формы. Шликерный способ применяют также в технологии фарфоровых и фаянсовых изделий, облицовочных плиток.
Наиболее прогрессивной технологией в настоящее время считается экструдирование. Влажность формуемой массы при этом колеблется от 18 до 28%. Изделия фор-
8
муются выдавливанием массы через специальное отверстие экструдера при помощи матрицы-мундштука, которое обеспечивает изделиям форму, толщину и ширину. Далее происходит нарезка изделий по длине специальными ножами (тонкой проволокой). Экструзия позволяет получать изделия (плитки) сложной геометрической формы. Существуют и другие способы формования керамических изделий – например, штампование (оттиск). Таким способом, например, получают пазовую штампованную черепицу и другие изделия.
Сушка сырых керамических изделий является весьма ответственным этапом в технологическом процессе, так как трещины возникают в основном в процессе сушки изделий, а при обжиге лишь окончательно выявляются. Сушат отформованные изделия в туннельных или камерных сушилках при температуре теплоносителя 120…150 в течение от нескольких минут до 72-х часов в зависимости от свойств сырья и влажности сырца. Обычно достаточным является высушивание сырых изделий до остаточной влажности не более 2…5%.
Обжиг является важной и завершающей стадией технологического процесса производства керамических изделий и может длиться до 60 часов. Суммарные затраты на обжиг достигают 40% себестоимости готовых изделий. Температура обжига для различных изделий строительной керамики составляет от 900 до 1800 . Под воздействием высоких температур происходят структурные изменения в массе изделий, кристаллическая решётка молекул глины распадается, глина теряет пластичность, происходит, так называемый процесс спекания глины. Результатом процесса обжига (спекания) является образование новых кристаллических и аморфных фаз, уплотнение обжигаемого материала (усаживание) и, как следствие, уменьшение его открытой пористости. При обжиге сырца образуется искусственный каменный материал (черепок), который в отличие от сырой керамической массы не размывается водой и обладает относительно высокой прочностью.
В зависимости от назначения обжиг изделий ведется до различной степени спекания. Спекшимся считается черепок с водопоглощением менее 5% (фарфор, клинкер). Однако большинство строительных изделий (кирпич, камни, некоторые виды облицовочных плиток) обжигаются до получения черепка с неполным спеканием.
П р и м е ч а н и е ‒ Процесс обжига керамических изделий подразделяется, как правило, на три периода – прогрев сырца, собственно обжиг и регулируемое охлаждение. Интервал температур обжига для кирпича, камней и керамзита составляет 900…1100 , клинкерного кирпича, плиток для пола, фаянса – 1100…1300 , фарфоровых изделий, керамогранита – 1300…1500 , огнеупорной ке-
рамики – 1300…1800.
4. Способы улучшения внешнего вида керамических изделий
Цвет черепка керамических изделий чаще всего определяется составом исходного сырья (содержанием в глине оксидов железа) и варьируется от светло-желтого до
9
темно-красного с множеством промежуточных тонов. Кроме того, используя различные смеси глин, можно получить светло- и темно-серые вариации. При этом цвет неглазурованных изделий, как правило, практически однороден по всей толщине и не имеет декоративного рисунка, а различия в окраске достигаются добавлением красящих пигментов.
Для улучшения внешнего вида керамических изделий и устойчивости к внешним воздействиям прибегают к различным технологическим приемам (декорированию) – механической обработке лицевой поверхности, двухслойному формованию, поверхностному и объемному окрашиванию, глазурованию, ангобированию, сериографии, шелкографии, торкретированию, газопламенному и плазменному напылению, искусственному состариванию (галтовке), живописи, УФ-печати и др.
Механическая обработка заключается в использовании специальных приспособлений (щеток, разнообразных скребков, пневматических роликов, ножей, высокоскоростных режущих лезвий, мундштуков с рисунками на внутренней поверхности и др.), позволяющих получать рельефный рисунок в процессе или после формования изделий. Декоративный эффект при этом достигается за счет частичного снятия верхнего слоя глиномассы или глазури, обнажения более глубоких слоев, в т. ч. глазури другого цвета. Для придания блеска глазурованным и не глазурованным изделиям может производиться полировка поверхности.
Глазурование – это нанесение на лицевую поверхность изделий тонкого блестящего стекловидного (эмалевидного) водонепроницаемого слоя толщиной 0,1…0,3 мм, закрепленного обжигом. Глазурь закрывает поры, сглаживает шероховатости поверхности, придавая ей гладкий и блестящий вид. По составу и физическим свойствам глазури представляют собой разновидности стёкол. В их составе кварцевый песок, глина, полевой шпат, тальк, соли и оксиды различных металлов (калия, лития, бора, свинца, олова и др.). Для получения глазурного состава все компоненты размалывают в порошок, разводят водой и в виде суспензии наносят на поверхность обожженных или необожженных изделий перед обжигом путем поливания, окунания или пульверизации. В процессе обжига глазурь расплавляется, растекается по поверхности и при охлаждении превращается в стекловидный слой. Различают прозрачные и непрозрачные (глухие), глянцевые, матовые, белые, цветные, тугоплавкие, легкоплавкие и другие глазури.
Ангобирование керамических изделий имело широкое распространение ещё в античном мире. На Руси такое покрытие называлось «побела». Ангобирование – это нанесение на лицевую поверхность изделий тонкого цветного слоя (толщиной 1,0…1,5 мм) из глинистой суспензии, состоящей из беложгущихся, цветных глин или смеси глин, флюсующих добавок, заполнителя и пигментов, с последующим обжигом. Для лучшего сцепления ангоба с поверхностью в его состав вводят органическое связующее. В отличие от глазури ангоб не дает при обжиге расплава, т. е. не образует стекловидного слоя, и поэтому цветная поверхность получается матовой и может быть,
10