
образец
.pdf
Министерство науки и высшего образования РФ
Федеральное государственное автономное образовательное учреждение высшего образования
«Самарский национальный исследовательский университет имени академика С.П. Королева»
Заочное отделение
Института авиационной техники
Кафедра производства летательных аппаратов и управления качеством в машиностроении
Курсовая работа
«Технология механической обработки»
Выполнил: студент группы 3394-150305Z Волков В. С № зачетной книжки: 2016-02592
Проверил: доц. Шаров А.А
Самара 2021
Содержание |
|
|
|
ВВЕДЕНИЕ ........................................................................................................ |
|
3 |
|
1 |
Конструктивно-технологический анализ детали........................................... |
5 |
|
2 |
Чертёж детали.................................................. |
Error! Bookmark not defined. |
|
3 |
Выбор вида специальной заготовки ............................................................... |
|
6 |
4 |
Определение припусков на обработку расчётно-аналитическим методом . 6 |
||
5 |
Определение припусков на обработку опытно-статистическим методом . 13 |
||
6 |
Разработка плана изготовления детали с операционными эскизами ......... |
14 |
|
7 |
Выбор оборудования ..................................................................................... |
|
15 |
8 |
Выбор режущего инструмента ..................................................................... |
|
17 |
9 |
Разработка и оформление чертежа графической технологии.............. |
Error! |
|
Bookmark not defined. |
|
|
|
10 Конструктивная схема станочного приспособления ................................. |
19 |
||
ЗАКЛЮЧЕНИЕ ................................................................................................ |
|
21 |
|
СПИСОК ИСПОЛЬЗОВАННЫХ ИСТОЧНИКОВ ........................................ |
22 |
ВВЕДЕНИЕ Механическая обработка детали - широко распространённый
технологический процесс современного машиностроения.
Механическая обработка находит широкое применение в различных областях машиностроения благодаря возможности получения деталей различной формы и конфигурации с заданными технологическими показателями. Данным методом обрабатывается до 70% всех изготовляемых деталей.
Технология получения и качество заготовок, поступающих для обработки в механических цехах, являются важнейшими факторами, определяющие общий технологический уровень производства и продуктивность механической обработки. Применение заготовок, полученных методами точного литья и точной обработки давлением, обеспечивает значительную экономию в использовании металла и снижение себестоимости продукции. Применение методов получения точных заготовок не только сокращает объем механической обработки, но и обеспечивает возможность выполнения ее высокопроизводительными методами.
Вцелях обеспечения высокой эффективности производства и создания качественной продукции необходима разработка таких технологических процессов, которые позволяют с наименьшими трудовыми и материальными затратами обеспечить изготовление продукции с требуемыми параметрами, характеристиками и свойствами.
Уже на стадии проектирования технологического процесса закладывается качество будущей продукции, её себестоимость и эффективность производства, поэтому очень важно правильное, разумное и рациональное проектирование технологического процесса.
Эффективность того или иного технологического процесса зависит от того, насколько обоснованно был произведён выбор основного инструмента, оборудования, оснастки. А также от методов получения заготовки и режимов обработки.
Вданном курсовом проекте разработан и обоснован технологический процесс изготовления заданной детали с учётом обеспечения высокого качества её получения методами механической обработки на реальном оборудовании и спроектировано сборочное приспособление для расточки отверстия в заданной детали.
3
РЕФЕРАТ Курсовой проект
Пояснительная записка: 24 с., 16 табл., 8 рис. РАСЧЕТНО-АНАЛИТИЧЕСКИЙ, ПРИСПОСОБЛЕНИЕ, ОПЫТНО-
СТАТИСТИЧЕСКИЙ, ОБОРУДОВАНИЕ, ИНСТРУМЕНТ, ПРИПУСК, ЗАГОТОВКА, ДЕТАЛЬ.
Целью данного курсового проекта является разработка экономически целесообразного технологического процесса изготовления качественной детали в соответствии с чертежом.
Объектом исследования является ось.
В курсовом проекте описано назначение и краткое описание детали, проведён её конструктивно технологический анализ, выбран вид и размеры заготовки, разработан маршрутный технологический процесс обработки детали и операционный технологический процесс, выбрано оборудование и режущий инструмент, проведён расчёт режима резания, нормирование, спроектировано специальное станочное приспособление, определена схема базирования детали в приспособлении.
4

1 Конструктивно-технологический анализ детали Целью конструктивно-технологического анализа является выявление
недостатков данной конструкции по сведениям, содержащимся в чертежах и технологических требованиях, а также возможное улучшение технологичности рассматриваемой конструкции.
Технологичность детали – это совокупность свойств конструкции детали, проявляемых в возможности оптимальных затрат труда, средств, материала и времени при технической подготовке ее производства, изготовлении, эксплуатации, ремонте и обеспечении технологичности сборочной единицы, в состав которой она входит.
Чертеж детали содержит все необходимые сведения, дающие полное представление о детали, то есть все проекции, совершенно четко объясняющие ее конфигурацию, и возможные способы получения заготовки. Разрезы и сечения показывать на чертеже не требуется, так как конструкция детали полностью понятна из двух стандартных видов. На чертеже указаны все размеры с необходимыми отклонениями, требуемая шероховатость обрабатываемых поверхностей.
Заданная деталь высоко технологична, так как содержит стандартные конструкторские элементы, такие как отверстие, расточку и т. д. Точность и шероховатость также обеспечивают точность обработки и контроля.
Получение детали прокатом - самый рациональный способ изготовления детали при объёме выпуска 3300 шт..
Конструкция детали подразумевает возможность применения типовых и стандартных технологических процессов ее изготовления.
Так как в задание на курсовое проектирование используется одна деталь, то в качестве количественных показателей технологичности могут рассматриваться такие параметры, как масса детали, коэффициент использования материала.
Коэффициент использования материала определяется по формуле:
Мд КИМ
0,22 |
кг |
Мд 0,22 Мз 0,93
0,24
кг
По данному коэффициенту технологический процесс соответствует требованиям ЕСТПП, т.к КИМ ≤0,25…0,8.
5
2 Выбор вида специальной заготовки Метод получения заготовки оказывает существенное влияние на технико-
экономические показатели технологического процесса изготовления детали. Правильный его выбор позволяет снизить трудоемкость механической обработки, повысить коэффициент использования материала, снизить материалоемкость конструкции.
На выбор метода получения заготовки влияют материал детали, его назначения и технические требования к изготовлению, объем выпуска, конфигурация, форма поверхностей и размеры.
Требования, предъявляемые к заготовкам, обрабатываемых на металлорежущих станках:
С целью снижения себестоимости детали заготовка должна быть по форме и размерам максимально приближенной к детали.
Черновые поверхности используемые на первой механической операции в качестве технологической базы должны быть чистыми и ровными, без штрихов, литейных уклонов.
Вид заготовки устанавливаем в результате анализа чертежа детали, ее материала и технических требований к изготовлению, габаритов и массы, объема выпуска, на основе технико-экономического сравнения нескольких вариантов.
Вид заготовки (прокат), из которой должна изготавливаться заданная деталь, указана в рабочем чертеже детали.
3 Определение припусков на обработку расчётно-аналитическим методом По приложению [1] определяем допуск для заданного размера детали –
Ø18h7 – составляет Тд = 18 мкм. Так как h7 относится к основному валу, то верхнее отклонение esд = 0, нижнее отклонение eiд = -18 мкм.
Устанавливаем технологический маршрут обработки заданной поверхности
– наружный диаметр Ø18h7(-0,018).
Для заданной шероховатости Ra = 1,25 обработка состоит из чернового и чистового точения, чернового и чистового шлифования.
В качестве заготовки принимаем прокат горячекатаный обычной точности диаметром больше шейки с максимальным диаметром 18 мм на величину припуска, для которого по приложению [1] в диапазоне диаметров 10…19 мм верхнее отклонение esз = 0,3 мм, нижнее отклонение eiз = -0,5 мм, допуск составит:
Т з esз eiз 0,3 ( 0,5) 0,8 мм
По каждому переходу устанавливаем по приложению [1] точность и шероховатость, а по приложению [1] допуск на обрабатываемую поверхность по принятой точности.
6
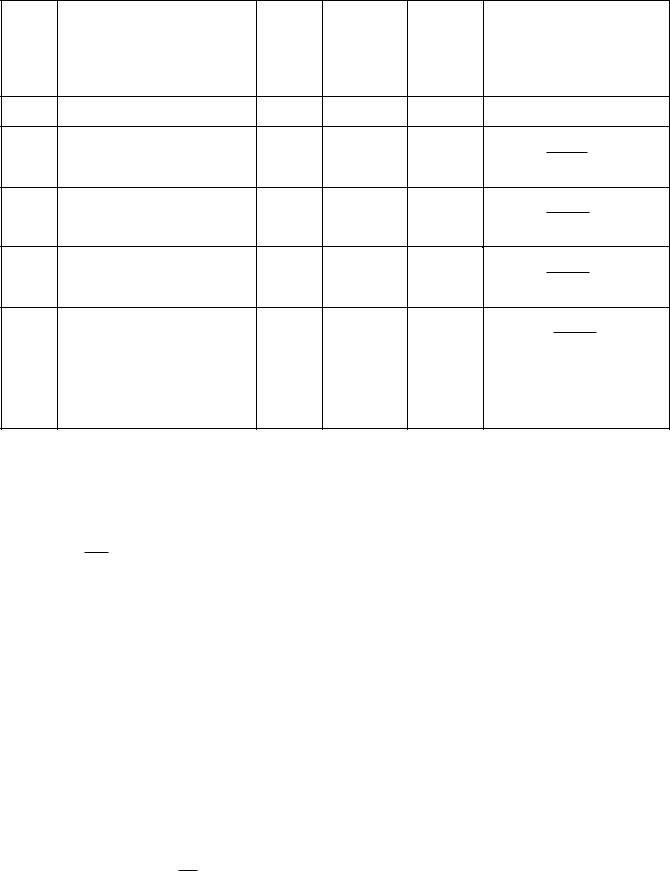
Принятые значения заносим в таблицу 1
Ном |
Вид обработки |
Квали |
Шерохо |
Допуск |
ер |
|
тет |
ватость |
Т,мм |
пере |
|
точно |
Ra |
|
хода |
|
сти |
|
|
|
Заготовка |
14 |
|
0,8 |
1 |
Точение черновое |
12 |
6,3 |
0,180 |
2 |
Точение чистовое |
10 |
3,2 |
0,070 |
3 |
Шлифование черновое |
8 |
1,6 |
0,027 |
Коэффициент
уточнения
|
|
|
0,8 |
4,44 |
|
1 |
0,180 |
||||
|
|
|
|||
|
|
|
|
|
|
|
0,180 |
2,57 |
|
2 |
0,070 |
||||
|
|
|
|||
|
|
|
|
||
|
|
|
0,070 |
2,59 |
|
3 |
0,027 |
||||
|
|
|
|||
|
|
|
|
4 |
Шлифование чистовое |
7 |
1,25 |
0,018 |
|
|
|
0,027 |
1,5 |
|
4 |
0,018 |
||||
|
|
|
|||
|
|
|
|
Итого |
1 4,44 2,57 |
|
2,59 1,5 44,4 |
Таблица 1- Последовательность обработки поверхности Проверяем правильность составления технологического процесса
обработки.
Для каждого перехода определяем коэффициент уточнения по формуле:
i Ti 1
Ti
где Т(i-1) – допуск на размер или другой рассматриваемый параметр точности детали, получаемый на предшествующей технологической операции (переходе);
Тi – допуск на размер или другой рассматриваемый параметр точности детали, получаемый на выполняемой технологической операции (переходе).
Определяем общий коэффициент уточнения:
i k
0 i 1
где k – количество переходов.
Для заготовки коэффициент уточнения не рассчитывается.
Проверяем правильность выбора технологических переходов:
0 44,4 to Tз 44,4
Тд
где εто – требуемое уточнение.
7

Что гарантирует достижение требуемой точности обработки поверхности. |
||||||||||
Минимальный припуск на диаметр определяется по формуле: |
||||||||||
2 Z |
|
2 R |
|
h |
|
|
|
|
|
|
|
|
|
|
|
|
2 |
|
2 |
|
|
|
i min |
|
z (i 1) |
(i 1) |
|
|
(i 1) |
|
i |
|
где Rz(i-1) , h(i-1) – соответственно высота неровностей профиля и глубина дефектного поверхностного слоя на предшествующем переходе; принимаем для заготовки по приложению [1] для проката обычной точности для диапазона диаметров до 30 мм Rz(i-1) = 125 мкм, h(i-1) = 150 мкм, после механической обработки принимаем по приложению [1];
ΔΣ(i-1)– суммарные отклонения расположения поверхности на предшествующем переходе;
εi – погрешность установки заготовки на выполняемом переходе.
Для серого и ковкого чугунов, а также для цветных металлов и сплавов после первого технологического перехода и для стали после термической обработки слагаемое h исключают из расчёта.
Суммарные отклонения расположения поверхности для заготовки при обработки в трехкулачковом патроне закреплении определяются по формуле:
|
|
|
к |
|
|
где |
Σк |
– отклонение оси детали от прямолинейности (кривизна); |
||
определяется по формуле: |
||||
|
к |
|
к |
l |
|
|
|
||
где |
к – отклонение оси детали от прямолинейности, мкм на 1 мм длины; |
принимают по приложению [1], для проката обычной точности и длине заготовки в диапазоне до 120 мм к = 0,5 мкм/мм;
l = 35 мм – вылет заготовки из патрона по чертежу. Подставляя принятые значения в формулу получим:
к |
|
0,5 35 18 мкм = 0,018мм |
|||
Остаточные пространственные отклонения на операциях механической |
|||||
обработки определяют по формуле: |
|||||
|
ост |
К |
у |
|
заг |
|
|
|
где kу – коэффициент уточнения формы; их значения принимаем по приложению [1].
Подставляем принятые значения kу в формулу . После чернового точения:
|
чер .т |
0,06 18 1,1мкм 0,001мм |
|
|
После чистового точения:
чис.т 0,05 18 0,9мкм 0,001мм
После чернового шлифования:
8
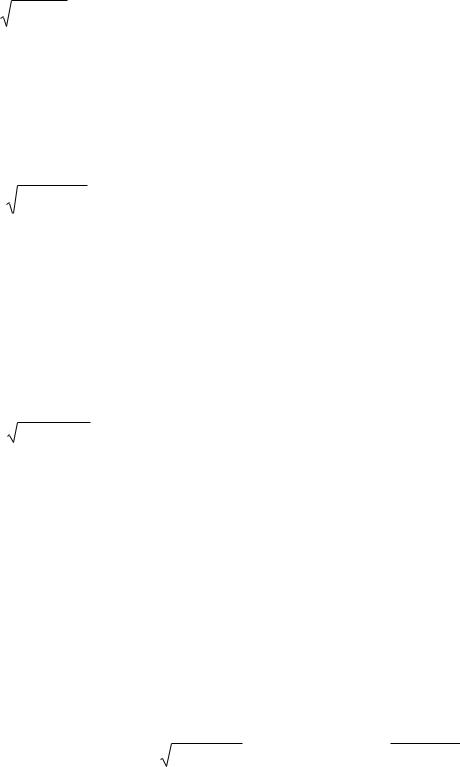
|
чер .ш |
0,03 18 0,5мкм 0,001мм |
|
|
|
|
|
После чистового шлифования: |
|
||
|
чис.ш |
0,02 18 0,4мкм 0,0004 |
мм |
|
|
|
Погрешность установки при обработке в трёхкулачковом самоцентрирующем пневматическом патроне определяется по формуле:
|
б |
з |
|
2 |
2 |
где εб – погрешность базирования; при черновом и чистовом точении, черновом и чистовом шлифовании наибольшего диаметра заготовка базируется в центрах, в этом случае εб = 0.
εз – погрешность закрепления; при закреплении в трёхкулачковом самоцентрирующем пневматическом патроне εз = 0.
Погрешность закрепления определяется по формуле:
з |
|
2 |
2 |
рад |
ос |
где εрад – радиальная составляющая; по приложению [1] при установке в пневматическом патроне по чисто обработанной поверхности в диапазоне диаметров 30…50 мм εрад = 35 мкм;
εос – осевая составляющая; по приложению [1] при установке в пневматическом патроне по чисто обработанной поверхности в диапазоне диаметров 30…50 мм εос = 40 мкм.
Подставляем принятые значения в формулы и получим для чернового растачивания:
|
|
|
35 |
2 |
40 |
2 |
|
|
|
|
|
||
|
з |
|
|
|
|
|
53
мкм
На остальных переходах при обработке за одну установку εз = 0 После расчёта и принятия значений элементов припуска определяем
минимальные припуски по каждому переходу, подставляя принятые значения в формулу .
Для чистового шлифования: |
||||||
2 Z |
|
2 R |
чис.ш |
|
|
2 10 1 2 11мкм |
|
|
|
чис.ш |
|
||
|
i min |
z |
|
|
|
Для
2 Z
чернового шлифования: |
||||||
|
2 R |
|
h |
|
|
|
|
|
чер .ш |
|
чер .ш |
чер |
|
i min |
z |
|
|
|
|
.ш
2 20 30 1 2 51мкм
Для чистового точения: |
|
|
||||||||
2 Z |
|
2 R |
|
|
h |
|
|
|
||
|
|
|
чер .т |
|
|
чер .т |
чер |
|||
|
i min |
z |
|
|
|
|
|
|
|
|
Для чернового точения: |
|
|
||||||||
2 Zi min |
|
заг |
h |
заг |
|
2 |
|
|||
2 Rz |
|
|
заг |
.т |
63 |
60 |
1 2 124мкм |
2 |
i2 2 125 150 182 532 2 331мкм
Расчётный (минимальный) размер по каждому переходу определяют, начиная с конечного (в данном случае чертёжного) размера. Для последнего
9
перехода (готовой детали) он равняется минимальному размеру детали. Для остальных переходов он определяется последовательным сложением расчётного размера и минимального припуска на предшествующем переходе:
- после чистового шлифования -
d |
p |
|
17,987мм
- после чернового шлифования -
d |
p |
|
17,987 +
2
0,011
=18,009мм
- после чистового точения -
d |
p |
|
18,009 +
2
0,051
=18,111 мм
- после чернового точения -
d |
p |
|
18,111+
2 0,124
=18,359 мм
- для заготовки -
d |
p |
|
18,359 +
2
0,331
=19,021 мм
Определяем предельные размеры для каждого перехода.
Минимальный предельный размер для каждого перехода равен расчёт-
ному:
dmin d p
Максимальный предельный размер на каждом переходе определяется путём сложения к минимальному размеру значение допуска на обработку на этом же переходе:
- после чистового шлифования –
dmчисax.шл dmчисin .шл Т чис.шл 17,987 0,018 18,005мм
- после чернового шлифования –
d |
чер.шл |
d |
чер.шл |
Т |
чер .шл |
|
|
|
|||
|
max |
|
min |
|
|
18,009 0,027 18,036мм
- после чистового точения –
d |
чис.т |
d |
чис.т |
Т |
чис.т |
|
|
|
|||
|
max |
|
min |
|
|
18,111 0,070 18,181мм
- после чернового точения –
d |
чер.т d чер.т Т чер.т 18,359 0,180 18,539мм |
|||||||
|
max |
|
min |
|
|
|
|
|
- для заготовки – |
|
|
||||||
d |
заг |
d |
заг |
Т |
заг |
19,021 |
0,800 |
19,821мм |
max |
min |
|
||||||
|
|
|
|
|
|
|
Предельные значения припусков zпр.max определяются как разность наибольших предельных размеров предыдущего и текущего переходов, а zпр.min определяются как разность их наименьших предельных размеров:
- после чистового шлифования –
2z |
пр. max |
d чер .шл d чис.шл 18,036 18,005 0,031мм |
|
|
max |
max |
|
2z |
пр. min |
d чер .шл d чис.шл 18,009 17,987 0,022 мм |
|
|
min |
min |
- после чернового шлифования –
2zпр. max dmaxчис.т dmaxчер .шл 18,181 18,036 0,145 мм 2zпр. min dminчер .шл dminчис.шл 18,111 18,009 0,102 мм
10