
образец
.pdf- после чистового точения –
2z 2z
пр. max
пр. min
d |
чер .т |
d |
чис.т |
|
|
|
|||
d |
max |
d |
max |
|
чер .т |
чис.т |
|||
|
|
|||
|
min |
|
min |
18,539 18,359
18,181 18,111
0,358 |
мм |
0,248 |
мм |
- после чернового точения –
2z |
|
d |
заг |
d |
чер .т |
19,821 18,539 1,282 мм |
|||
пр. max |
max |
max |
|||||||
|
|
|
|
|
|
||||
2z |
|
d |
|
заг |
d |
чер .т |
19,021 18,359 0,662 мм |
||
пр. min |
min |
min |
|||||||
|
|
|
|
где индексы заг – относится к заготовке, чер.т – черновому точению, чис.т
– чистовому точению, чер.шл – черновому шлифованию, чис.шл – чистовому шлифованию.
Проверяем правильность расчёта припусков:
Z |
o. max |
Z |
o. min |
T |
T |
|
|
з |
д |
1,816-1,034=0,8-0,018 0,782=0,782
Номинальный припуск при несимметричном расположении поля допуска заготовки:
Zо.н |
Zо. min esз eiд 1,034 ( 0,5) ( 0,018) 1,516 |
|
Номинальный диаметр заданного размера заготовки: |
||
dз.н |
dд. min Zо.н 17,987 1,516 19,503 мм |
|
По приложению [1] принимаем размер круга, округляя его до ближайшего |
||
большего значения, которое предусмотрено сортаментом по ГОСТ: |
||
d |
заг |
20 мм |
|
|
Все результаты расчётов сведены в таблицу 2
11
Вид |
|
|
Элементы |
|
|
т уточнения |
Допуск размер, мкм |
Расчётный |
Расчётный |
Предельный |
Предельные |
размеры |
Диаметр |
||||
обработки |
|
|
припуска, мкм |
|
припуск, |
размер, мм |
размер, мм |
припуска, мм |
|
Исходной |
|||||||
|
|
|
|
|
|
|
мкм |
|
|
|
|
|
|
заготовки |
|||
|
|
|
|
|
|
|
|
|
|
|
|
|
|
|
|
||
|
Квалитет точности |
Шероховатость ,Ra |
|
|
|
|
Коэффициен формы |
|
|
|
|
|
|
|
|
|
|
|
Rz |
h |
|
ε |
Ky |
T |
2Zmin |
dp |
dmin |
dmax |
2Zпр.min |
|
2Zпр.max |
dзаг |
|||
|
|
|
|
|
|
|
|
|
|
|
|
|
|
|
|
||
Заготовка |
|
|
125 |
150 |
18 |
|
|
800 |
|
19,021 |
19,021 |
19,821 |
|
|
|
|
|
Точение |
12 |
6,3 |
63 |
60 |
1 |
|
0,006 |
180 |
2·331 |
18,359 |
18,359 |
18,539 |
0,662 |
|
1,282 |
|
|
черновое |
|
|
|
|
|
|
|
|
|
|
|
|
|
|
|
|
|
Точение |
10 |
3,2 |
20 |
30 |
1 |
|
0,005 |
70 |
2·124 |
18,111 |
18,111 |
18,181 |
0,248 |
|
0,358 |
|
|
чистовое |
|
|
|
|
|
|
|
|
|
|
|
|
|
|
|
20 |
0.3 |
|
|
|
|
|
|
|
|
|
|
|
|
|
|
|
0.4 |
||
Шлифование |
8 |
1,6 |
10 |
20 |
1 |
|
0,003 |
27 |
2·51 |
18,009 |
18,009 |
18,036 |
0,102 |
|
0,145 |
|
|
|
|
|
|
||||||||||||||
черновое |
|
|
|
|
|
|
|
|
|
|
|
|
|
|
|
|
|
Шлифование |
7 |
1,25 |
5 |
12 |
0,4 |
|
0,002 |
18 |
2·11 |
17,987 |
17,987 |
18,005 |
0,022 |
|
0,031 |
|
|
чистовое |
|
|
|
|
|
|
|
|
|
|
|
|
|
|
|
|
|
Итого |
|
|
|
|
|
|
|
|
|
|
|
|
1,034 |
|
1,816 |
|
|
Таблица 2 – Аналитический расчёт припусков и предельных размеров по технологическим переходам на обработку наружного диаметра Ø18h7(-0,018)
12
4 Определение припусков на обработку опытно-статистическим методом На остальные размеры межпереходные припуски определяют табличным
способом.
По приложению [1] устанавливаем последовательность обработки: для концевых торцов шероховатость Ra = 6,3 мкм достигается черновым и чистовым подрезанием; для торцов выступающих шеек Ra = 1,6 мкм достигается черновым и чистовым подрезанием; для вала диаметром 40 мм шероховатость Ra = 1,6 мкм достигается черновым и чистовым точением для отверстия диаметром 25 шероховатость Ra = 0,8 мкм достигается сверлением черновым и чистовым. фрезерование поверхности шероховатость Ra = 1,6 мкм достигается черновым и чистовым фрезерованием. Заготовка – прокат обычной точности.
Для диапазона диаметров до 30 мм и длине заготовки в диапазоне до 120 мм припуск на диаметр составляет на черновое точение 1,2 мм, на чистовое точение 0,25 мм, на черновое шлифование после термообработки 0,3 мм, на чистовое шлифование после чернового шлифования 0,06 мм.
По приложению [1] устанавливаем припуски на сторону на линейные размеры (торцы): для диапазона диаметров 30…50 мм и длине вала в диапазоне 30…50 мм припуск на сторону составляет на черновое подрезание 1,4±0,3 мм, на чистовое подрезание 0,8-0,34 мм;
Для диапазона 6…18 мм и длине вала до 30 мм припуск на сторону составляет на черновое подрезание 1,2±0,25 мм, на чистовое подрезание составляет 0,6-0,28 мм. Номинальный (суммарный) припуск определяется суммированием припусков на отдельных переходах.
Для диапазона до 30мм и длине до 120 мм припуск на черновое фрезерование 1,5мм, на чистовое 0,7мм и шлифование чистовое 0,3 мм.
Заготовка – прокат обычной точности.
Номинальный размер по чертежу |
|
|
|
|
Припуски, мм |
|
|
|
|
Расчетный размер, мм |
Принятый размер, мм |
||
|
|
|
|
|
|
|
|
|
|
|
|||
Предварительное точение напуска |
Черновое точение |
Чистовое точение |
Черновое фрезерование |
|
Чистовое фрезерование |
Черновое сверление |
Чистовое сверление |
Черновое шлифование |
Чистовое шлифование |
Номинальный припуск |
|||
|
|
|
|
|
|
|
|
|
|
|
|
|
|
35 |
|
|
|
1,5 |
|
0,7 |
|
|
|
0,3 |
2,5 |
35+2·2,5=40 |
40 |
|
|
|
|
|
|
|
|
|
|
|
|
|
|
25 |
|
|
|
|
|
|
1,2 |
0,8 |
|
0,3 |
2,3 |
25+2,3=27 |
27 |
22 |
|
1,2 |
0,6 |
|
|
|
|
|
|
|
1,8 |
22+2·1,8=25,6 |
26 |
35 |
|
1,4 |
0,8 |
|
|
|
|
|
|
|
2,2 |
35+2·2,2=39,2 |
40 |
16 |
2,19 |
1,2 |
0,25 |
|
|
|
|
|
0,3 |
0,06 |
4 |
16+4=20 |
20 |
14 |
4,19 |
1,2 |
0,25 |
|
|
|
|
|
0,3 |
0,06 |
6 |
14+6=20 |
20 |
13
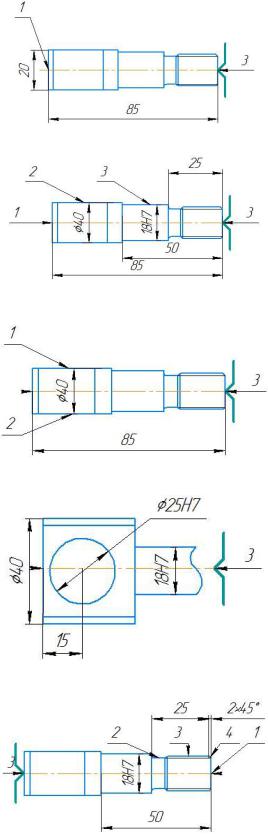
5 Разработка плана изготовления детали с операционными эскизами
№ операции, |
Наименование |
Оборудование, |
Инструмент |
||
Операционный эскиз |
операции, |
приспособления |
|
||
|
Содержание |
|
|
|
|
|
переходов |
|
|
|
|
|
|
|
|
|
|
010 |
Токарная |
Токарно- |
|
|
Подрезной |
|
1. Установить и |
винторезный |
|
отогнутый резец |
|
|
закрепить |
|
(с пластинами |
||
|
|
|
|
||
|
2. Подрезать |
станок |
с |
ЧПУ |
из |
|
торец на проход. |
16К20Ф3. |
|
|
быстрорежущей |
|
(1) |
|
|
стали) |
|
|
|
|
|
||
|
3. Снять деталь и |
3-хкулачковый |
ГОСТ 18871-73 |
||
|
уложить деталь в |
патрон. |
|
|
|
|
тару |
|
|
|
|
|
|
|
|
|
|
015 |
Токарная |
Токарно- |
|
|
Сверло |
|
1. Установить и |
винторезный |
|
Центровочное |
|
|
закрепить |
|
Ø2 ГОСТ 14952- |
||
|
|
|
|
||
|
2. Центровать |
станок |
с |
ЧПУ |
75 |
|
Отверстие (1) |
16К20Ф3. |
|
|
Резец |
|
3.Обтачить |
|
|
проходной |
|
|
|
|
|
||
|
поверхность (2) |
3-хкулачковый |
прямой ГОСТ |
||
|
и (3) |
патрон. |
|
|
18869-73 |
|
4. Снять деталь и |
|
|
|
|
|
уложить деталь в |
|
|
|
|
|
тару |
|
|
|
|
020 |
Фрезерная |
Вертикально- |
|
Концевая фреза |
|
|
1. установить и |
фрезерный станок |
с |
||
|
закрепить |
6Р11Ф3. |
|
|
цилиндрическим |
|
2. фрезеровать |
|
|
|
хвостиком |
|
поверхность (1) |
3-хкулачковый |
ГОСТ 17025-71 |
||
|
и (2) |
патрон. |
|
|
|
|
3. снять деталь и |
|
|
|
|
|
уложить деталь в |
|
|
|
|
|
тару |
|
|
|
|
|
|
|
|
|
|
025 |
Сверлильная |
Радиально- |
|
Сверло |
|
|
1. установить и |
сверлильный |
|
спиральное с |
|
|
закрепить |
станок 2554. |
|
цилиндрическим |
|
|
2. сверлить |
|
|
|
хвостиком Ø40 |
|
отверстие Ø25Н7 |
3-хкулачковый |
ГОСТ 4010-77. |
||
|
3. Разсверливать |
патрон. |
|
|
|
|
отверстие Ø25Н7 |
|
|
|
|
|
4. снять деталь и |
|
|
|
|
|
уложить деталь в |
|
|
|
|
|
тару |
|
|
|
|
|
|
|
|
|
|
030 |
Токарная |
Токарно- |
|
|
Сверло |
|
1. установить и |
винторезный |
|
Центровочное |
|
|
закрепить |
станок с ЧПУ |
|
Ø2 ГОСТ 14952- |
|
|
2. центровать |
16К20Ф3. |
|
|
75 |
|
Отверстие (1) |
|
|
|
Токарный |
|
3. расточить |
3-хкулачковый |
проходной |
||
|
поверхность (2) |
патрон. |
|
|
прямой резец |
|
4. нарезать |
|
|
|
ГОСТ 18869-73. |
|
резьбу на |
|
|
|
Токарный |
|
поверхности (3) |
|
|
|
резьбовой резец |
|
5. проточить |
|
|
|
с пластиной из |
|
|
|
|
|
|
14
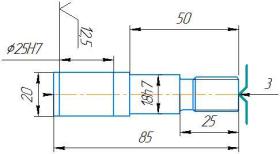
|
фаски 2×45° (4) |
|
быстрорежущей |
|
6. снять деталь и |
|
стали ГОСТ |
|
уложить деталь в |
|
18876-73 |
|
тару |
|
|
035 |
Шлифовальная |
Кругло- |
ПП 600х63х305 |
|
1.установить и |
шлифовальный |
ГОСТ 2424-83 |
|
закрепить |
станок КШ-3М |
|
|
деталь |
|
ПП 25х20х8 |
|
2 шлифовать |
3-хкулачковый |
ГОСТ 2424-83 |
|
наружную |
патрон. |
|
|
поверхность |
|
|
|
18h7 |
|
|
|
3 шлифовать |
|
|
|
отверстие 25H7 |
|
|
|
4 снять деталь и |
|
|
|
уложить деталь в |
|
|
|
тару |
|
|
040 |
Слесарная |
Верстак |
Напильник |
|
Острые кромки |
|
ГОСТ 1465-80 |
|
притупить |
|
|
|
радиусом 1 мм |
|
|
Таблица 4 - Маршрутно-технологический процесс 6 Выбор оборудования
Выбор типа станка прежде всего определяется его возможностью обеспечить выполнение технических требований, предъявляемых к обрабатываемой детали в отношении точности ее размеров, формы и класса шероховатости поверхностей. Если по характеру обработки эти требования можно выполнить на различных станках, выбирают станок, наиболее полно отвечающий следующим требованиям:
1)Соответствие основных размеров обрабатываемой детали габаритам рабочего стола станка.
2)Возможно более полное использование станка по мощности и по
времени.
3)Наименьшие затраты времени на обработку.
Таблица 5 - Токарно-винторезный станок с ЧПУ 16К20ФЗ
Характеристики |
Параметры |
Неибольший диаметр обрабатываемой заготовки: |
|
над станиной |
400 мм |
над суппортом |
220 мм |
Наибольший диаметр прутка, проходящего через |
53 мм |
отверстие шпинделя |
|
Наибольшая длинна, обрабатываемой заготовки |
1000 мм |
Шаг нарезаемой резьбы (метрической) |
до 20 |
Частота вращения шпинделя |
12,5 – 2000 |
|
об/мин |
Число скоростей шпинделя |
22 |
Наибольшее перемещение суппорта |
|
15
продольное |
900 мм |
поперечное |
250 мм |
Мощность электродвигателя главного привода |
10 кВт |
Габаритные размеры (без ЧПУ): |
|
длина |
3360 мм |
ширина |
1710 мм |
высота |
1750 мм |
Масса |
4000 кг |
Таблица 6 - Вертикально-фрезерный станок 6Р11Ф3 |
|
|
|
Размеры рабочей поверхности стола, мм |
250х1000 |
Наибольшее перемещение стола, мм |
|
продольное |
630 |
поперечное |
300 |
вертикальное(установочное) |
350 |
Пределы подач стола, мм/мин |
|
продольной и поперечной |
1-10000 |
вертикальной |
1-10000 |
Ускоренное перемещение стола, мм/мин |
|
продольной и поперечной |
10 |
вертикальной |
10 |
Частота вращения шпинделя, мин-1 |
|
количество ступеней, шт |
18 |
пределы,мин-1 |
50-2500 |
Конус шпинделя 7:24 |
ISO50 |
Мощность электродвигателей |
|
главного, кВт |
5,5 |
подачи(момент), Нм |
11,8 |
Дискретность, мкм |
1 |
Масса станка (с электро- и гидрооборудованием), кг |
3900 |
Таблица 7 -Радиально-сверлильный станок 2554 |
|
|
|
Характеристики |
Параметры |
Наибольший условный диаметр сверления в стали |
50 мм |
Расстояние от оси шпинделя до образующей колонны |
375-1600 мм |
Расстояние от нижнего торца шпинделя до рабочей |
450-1600 мм |
поверхности плиты |
|
Наибольшее перемещение: |
|
Вертикальное |
750 мм |
Горизонтальное |
1225 мм |
Конус Морзе отверстия шпинделя |
5 |
Число скоростей шпинделя |
21 |
Частота вращения шпинделя |
20 – 2000 |
|
об/мин |
16

|
Число подач шпинделя |
|
|
12 |
|
Подача шпинделя |
|
|
0,056 – 2,5 |
|
|
|
|
мм/об |
|
Наибольшая сила подачи |
|
|
20 МН |
|
Мощность электродвигателя привода главного движения |
|
5,5 кВт |
|
|
Габаритные размеры |
|
|
|
|
Длина |
|
|
2665 мм |
|
Ширина |
|
|
1020 мм |
|
Высота |
|
|
3430 мм |
|
Масса |
|
|
4700 кг |
|
Таблица 8 - Техническая характеристика станка КШ-3М |
|
||
|
Наибольший диаметр заготовки, мм |
100 |
|
|
|
Наибольшая длина заготовки, мм |
360 |
|
|
|
Наибольший диаметр шлифуемого отверстия , мм |
1590 |
|
|
|
Пределы частот вращения шпинделя minоб/мин |
1680 |
|
|
|
Пределы частот вращения шпинделя maxоб/мин |
2180 |
|
|
|
Класс точности станка по ГОСТ 8-82, (Н,П,В,А,С) |
С |
|
|
|
Мощность двигателя, кВт |
10 |
|
|
|
Масса, кг |
1850 |
|
7 Выбор режущего инструмента Режущие инструменты работают в условиях больших нагрузок, высоких
температур, трения и износа, поэтому инструментальные материалы должны удовлетворять особым эксплуатационным требованиям. Материал рабочей части иметь достаточную твердость и высокие допускаемые напряжения на изгиб, растяжение, сжатие и кручение.
Высокие прочностные свойства необходимы, чтобы инструмент обладал сопротивляемостью соответствующим деформациям в процессе резанья, а достаточная вязкость инструмента позволяла воспринимать ударную динамическую нагрузку. Важнейшей характеристикой является износостойкость. Чем выше износостойкость, тем медленнее изнашивается выше его стойкость по выдерживанию размеров. Это значит, что детали, последовательно обработанные одним и тем же инструментом, будут иметь минимальный разброс размеров.
Все виды режущего инструмента состоят из двух основных частей - рабочей части, содержащей лезвия и выглаживатели, и крепежной части, предназначенной для установки и крепления режущего инструмента в технологическом оборудовании или приспособлении.
Таблица 9 - Токарный отрезной резец из быстрорежущей стали, ГОСТ
18874-73
L, мм |
l, мм |
H |
B, мм |
a, мм |
r, мм |
D, мм |
|
|
|
|
|
|
|
170 |
60 |
|
20 |
6 |
0,8 |
60 |
|
|
|
|
|
|
|
17
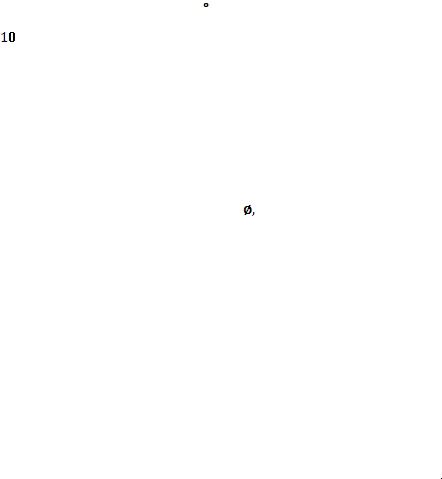
Таблица 10 - Токарный проходной прямой резец с пластинами из быстрорежущей стали, ГОСТ 18869-73
|
L, мм |
|
l, мм |
|
|
H |
B, мм |
|
φ, |
|
r, мм |
|
m |
|||||||||||
|
|
|
|
|
|
|
|
|
|
|
|
|
|
|
|
|
|
|
|
|
|
|
|
|
|
60 |
|
30 |
|
|
|
|
|
|
10 |
|
|
75 |
|
|
|
0,5 |
|
|
3 |
||||
|
|
|
|
|
|
|
|
|
|
|
|
|
|
|
|
|
|
|
|
|||||
|
Таблица 11 - Токарный резьбовой резец с пластиной из быстрорежущей |
|||||||||||||||||||||||
стали ГОСТ 18876-73 |
|
|
|
|
|
|
|
|
|
|
|
|
|
|
|
|
|
|
|
|||||
|
|
|
|
|
|
|
|
|
|
|
|
|
|
|
|
|
|
|
|
|
|
|||
|
L, мм |
|
|
l, мм |
|
|
|
H |
|
B, мм |
|
|
Шаг |
|
|
m |
|
|||||||
|
|
|
|
|
|
|
|
|
|
|
|
|
|
|
|
|
|
|
|
|
|
|||
|
120 |
|
40 |
|
|
20 |
|
12 |
|
|
|
0,75-3 |
|
|
3 |
|
|
|||||||
|
|
|
|
|
|
|
|
|
|
|
|
|
|
|||||||||||
|
Таблица 12 - Сверло спиральное с цилиндрическим хвостиком, ГОСТ 4010- |
|||||||||||||||||||||||
77 |
|
|
|
|
|
|
|
|
|
|
|
|
|
|
|
|
|
|
|
|
|
|
|
|
|
|
|
|
|
|
|
|
|
|
|
|
|
|
|
|
|
|
|
|
|
|
|||
|
L, мм |
|
|
|
|
|
|
|
|
l, мм |
|
|
|
|
|
|
|
|
мм |
|
||||
|
|
|
|
|
|
|
|
|
|
|
|
|
|
|
|
|
|
|
|
|
||||
|
151 |
|
|
|
|
|
75 |
|
|
|
|
|
|
25 |
|
|
|
|
|
|||||
|
|
|
|
|
|
|
|
|
||||||||||||||||
|
Таблица 13 - Концевая фреза с цилиндрическим хвостиком, ГОСТ 17025-71 |
|||||||||||||||||||||||
|
|
|
|
|
|
|
|
|
|
|
|
|
|
|
|
|
|
|||||||
|
d, мм |
|
|
|
|
L, мм |
|
|
l, мм |
|
|
|
|
|
|
Число зубьев |
||||||||
|
|
|
|
|
|
|
|
|
|
|
|
|
|
|
|
|
|
|
|
|
|
|
||
|
18 |
|
|
|
|
92 |
|
|
|
|
32 |
|
|
|
|
|
|
|
6 |
|
|
|
||
|
|
|
|
|
|
|
|
|
|
|
||||||||||||||
|
Таблица 14 - Шлифовальный диск ПП ГОСТ 2424-83 |
|
|
|
|
|
||||||||||||||||||
|
|
|
|
|
|
|
|
|
|
|
|
|
|
|
|
|
||||||||
|
|
D, мм |
|
|
|
|
|
T, мм |
|
|
|
|
|
|
H, мм |
|
||||||||
|
|
|
|
|
|
|
|
|
|
|
|
|
|
|
|
|
|
|
|
|||||
|
|
25 |
|
|
|
|
|
|
20 |
|
|
|
|
|
|
|
8 |
|
|
|||||
|
|
|
|
|
|
|
|
|
||||||||||||||||
|
Таблица 14 - Шлифовальный диск ПП ГОСТ 2424-83 |
|
|
|
|
|
||||||||||||||||||
|
|
|
|
|
|
|
|
|
|
|
|
|
|
|
|
|
||||||||
|
|
D, мм |
|
|
|
|
|
T, мм |
|
|
|
|
|
|
H, мм |
|
||||||||
|
|
|
|
|
|
|
|
|
|
|
|
|
|
|
|
|
|
|
|
|||||
|
|
600 |
|
|
|
|
|
|
63 |
|
|
|
|
|
|
|
305 |
|
|
|||||
|
|
|
|
|
||||||||||||||||||||
|
Таблица 16 - Развертка машинная цельная ГОСТ 1672-80 |
|
||||||||||||||||||||||
|
|
|
|
|
|
|
|
|
|
|
|
|
|
|
|
|
||||||||
|
d, мм |
|
|
|
|
L, мм |
|
|
l, мм |
|
|
|
|
|
|
Число зубьев |
||||||||
|
|
|
|
|
|
|
|
|
|
|
|
|
|
|
|
|
|
|
|
|
|
|||
|
25 |
|
|
|
|
268 |
|
|
|
68 |
|
|
|
|
|
|
|
8 |
|
|
|
|||
|
|
|
|
|
|
|
|
|
|
|
|
|
|
|
|
|
|
|
|
|
|
|
|
|
18
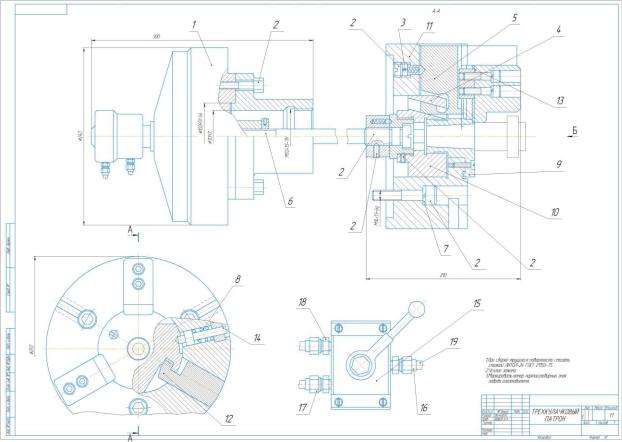
8 Конструктивная схема станочного приспособления
Рисунок 7 – Трехкулачковый патрон 9 Описание работы приспособления
Правильность выбора приспособлений способствует повышению производительности труда, точности обработки, улучшению условий труда. В токарной операции в качестве приспособления используют трехкулачковый патрон. Приспособление токарное предназначено для операций 010,015,030, выполняемой на станке 16К20Ф3.Приспособление УНП(Универсальное наладочное приспособление) с пневмаприводом, с простым силовым механизмом, одноконтактное. Заготовка устанавливается поверхностью ø40 в кулачки c упором в торец. Закрепление осуществляется с помощью пневмапривода трехсторонним - С образным прихватом . Заготовка лишена 6-ти степеней свободы
Расчет зажимных усилий при закреплении заготовок универсальных пневма патронах.
Определяем требуемое усилие закрепления заготовки
=Pz× Kзап ,
где:
Рz – сила резания (Рz=2000)
Кзап – коэффициент запаса (Кзап=1,8)
19
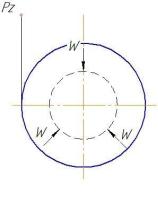
=2000
1,8= 3600 Н
Определим расчетный диаметр пневматического цилиндра Dп Dп=
где:
р- давление сжатого воздуха (р=0.39 МПа)
n- коэффициент полезного действия пневмоцилиндра, учитывающий потери в пневмоцилиндре (n=0,85)
Dп= = 117,61 мм
Принимаем стандартный диаметр пневмоцилиндраDц=150 мм Определяем требуемое усилие закрепления заготовки
2
р
2
5855 Н
Так как >
, то надежность закрепления обеспечивается.
Рисунок 8 – Схема усилия закрепления
20