
88-1
.pdf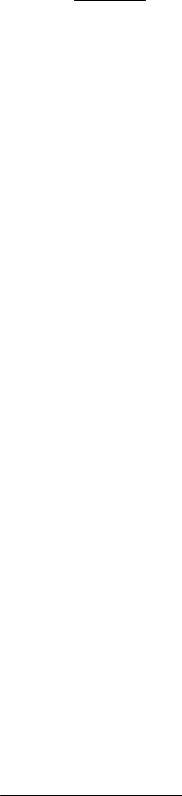
КD = 100 −D′м , 100
где D′м - содержание материала (добавки), % к массе абсолютно сухой плиты табл. 24.
м
Dм = ∑Dm im .
m=1
Справочные значения чистого расхода волокна, рассчитанные по среднеотраслевым значениям показателей S, ρ, W, D приведены в табл.2.
Суммарные отходы волокна (qсум.) определяют по следующим формулам:
- для мокрого способа производства ДВП:
qсум. = qн +qв +qемк. ,
где qн – неиспользуемые отходы ДВП, получаемые при их продольной и поперечной обрезке, %;
qв – отходы волокна со сточными водами, %;
qемк. – отходы волокна, связанные с промывкой емкостей, %. При этом
qн = |
f 100 |
, |
% , |
|
F |
||||
|
|
|
где f – количество неиспользуемых сухих отходов ДВП, получаемых при обрезке, м2;
F – площадь готовых плит, м2.
qв = vст. Ксток. (100 + Wпл. ) , %,
1000 Sпл. ρпл.
где vст. – количество сточных вод, м3/тыс.м2 ;
Ксток – концентрация волокна в сточных водах, кг/м3; Wпл. – абсолютная влажность плиты, %;
11
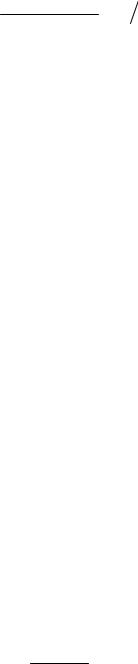
Sпл. – толщина плит, м;
ρпл. – плотность плиты, кг/м3.
Vст. = 70 Sпл. ρпл. ,м3 тыс.м2
100 +Wпл.
Нормативные значения qн, qв, qемк. приведены в табл. 3-5.
- для сухого способа производства ДВП:
для нешлифованных плит:
q′сум.н. = qн +qф, %,
для шлифованных плит:
q′сум.шл. = qн +qф +qш, %,
где qф – потери при сушке, подаче волокна к формирующей установке и формировании ковра, %;
qш –отходы, связанные со шлифованием плит, %.
Нормативные значения qн, qф, qш для плит сухого способа производства приведены в табл. 3, 6, 7.
Значения qш определяют по формуле:
qш = S −Sпл. 100, %,
Sпл.
где S – толщина плиты до шлифования, мм ;
Sпл. – толщина готовой плиты (после шлифования), мм.
12
Выход древесно-волокнистой массы в % от количества сырья, поступающего в размольное отделение цеха ДВП (Рм) определяют по формуле:
– для ДВП мокрого способа производства
Рм = Рпщ Кmn Кмф, %,
где Рпщ – выход массы в % при продолжительности пропаривания щепы 1 мин, при 185 0С и давлении пара 1,1 МПа;
Кmn – коэффициент, учитывающий изменение выхода массы при отклонениях температуры пропаривания щепы в камере дефибратора и продолжительности пропаривания щепы; Кмф – коэффициент, учитывающий изменение выхода массы в
зависимости от количества мелкой фракции щепы «поддона».
Суммарный выход массы при использовании древесины хвойных и лиственных пород (Рм′) определяют по формуле:
Рм′ = ∑В Рпщ iпор. , %, i=1
где iпор. – доля древесины одной породы в общей массе древесины. Нормативные значения Рпщ приведены в табл. 8 для хвойных и
лиственных пород в зависимости от содержания в щепе коры (iкор.) и гнили (iгн.) в % к общей массе сырья.
Нормативные значения Кmn и Кмф приведены в табл. 9, 10.
Для плит сухого способа производства нормативное значение выхода массы (Рм(с)) принимают по табл. 11.
Выход сортированной щепы (Рщ) определяют по формуле:
Рщ =100 −qщ, %,
13
где qщ – отходы древесины при рубке, дезинтегрировании и сортировке щепы, %.
qщ = |
(v р − vс) 100 |
, |
%, |
|
v р |
||||
|
|
|
где vр – объем древесины до рубки, м3; vс – объем щепы после сортировки, м3.
Нормативные значения Pщ приведены в табл. 12.
Отходы при разделке (раскалывании) круглых лесоматериалов (qр) определяют по формуле:
qр = |
(vл −vр) 100 |
, %, |
|
v л |
|||
|
|
где vл – объем круглых лесоматериалов до разделки, м3; vр – объем круглых лесоматериалов после разделки, м3
Выход древесины после разделки (Рр) будет равен:
Рр =100 −qр, %.
Нормативные значения Рр приведены в табл. 13. Условную плотность древесины щепы (ρусл.щ) определяют по формуле:
|
|
|
1 |
|
3 |
ρусл.щ. =ρщ |
|
|
|
|
, кг/м , |
1 |
+0,001 |
W |
|||
|
|
|
|
щ |
|
где ρщ – плотность древесины щепы при ее влажности (Wщ), кг/м3. Значения ρщ определяют по ОСТ 13-74-79 с помощью пикнометра и
весов с верхним пределом взвешивания до 5 кг, ценой деления не более 1 г. Wщ – абсолютная влажность щепы, %.
14
Условную плотность дров для производства плит, дров для отопления, отходов древесных, сырья древесного тонкомерного определяют расчетным путем.
Условную плотность сырья данного породного состава определяют по формуле
В
ρусл.щ. = ∑ρпор. iпор. , кг/м3, i=1
где ρусл. – условная плотность древесины одной породы, кг/м3;
iпор. – доля древесного сырья одной породы в общей массе древесины различных пород.
Если доля древесного сырья породы меньше 5 %, то она суммируется с породой близкой по свойствам.
В свою очередь ρпор. рассчитывается по формуле:
ρпор. = |
|
|
100 |
|
|
|
, кг/м3, |
||
|
|
i |
|
|
|
|
|
||
|
iкор |
+ |
гн |
|
+ |
iздор. |
|
||
|
ρкор |
ρгн |
ρздор. |
||||||
|
|
|
где iкор, iгн, iздор. – соответственно (доля) коры, гнили, здоровой древесины, % к общей массе сырья;
ρкор, ρгн, ρздор. – значения условной плотности коры, гнили, здоровой древесины, кг/м3.
При расчетах ρпор. содержание коры, гнили в древесине по данным цеховых лабораторий принимают равным содержанию коры и гнили в щепе из этого вида сырья.
ρгн = 0,65ρздор. .
Все виды древесного сырья приводятся к одному по ОСТ 13-200-85 «Дрова для гидролизного производства и изготовления древесных плит».
Сырье по этому стандарту принимается с Кпер. = 1.
Пересчет норм расхода древесного сырья на 1 тыс.м2 ДВП производят по формуле:
15
Нд = |
Н |
, м3/тыс.м2, |
|
||
|
Кпер.др. |
где Нд – норма расхода древесного сырья в «дровах», м3/тыс.м2; Кпер.др. – коэффициент пересчета (по табл. 14).
4. Расчет индивидуальных специфицированных норм расхода материалов на производство ДВП
Индивидуальная специфицированная норма расхода материала определяется по формуле:
- для материалов, содержание которых рассчитано в % от абсолютно сухого волокна
где
где
Нмат. = П Кисп. , кг/тыс.м2,
Кисп. – коэффициент, учитывающий используемое качество материала, вводимого в древесно-волокнистую массу, а также количество технологических отходов и потерь.
При мокром способе производства ДВП:
для материалов, вводимых в массу ковра, Кисп. определяют по формуле:
Кисп. = |
(100 |
+qн +qв) Кобр. Dмат. |
Кемк. , |
|
104 |
||
|
|
|
Dмат – дозировка материала, вводимого в древесноволокнистую массу, % к массе абсолютно сухого волокна; Кемк. – коэффициент, учитывающий величину потерь материала,
которые имеют место при промывке емкостей; Кобр. – коэффициент, учитывающий потери при обрезке сырого ковра.
Для материалов, содержание которых в плите определено нормативнотехнической документацией в % к массе плиты (например, антисептиков и других) норма расхода определяется по формулам:
16
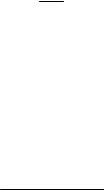
Н′мат |
= |
Sпл. ρпл. Кпот.м. |
105 |
, кг/тыс.м2, |
|
|
|||||
|
|
(100 +Wпл. ) |
|
|
|
Кпот.м. = |
(100 +qн ) (100 +qм) Dм |
Кемк. Кобр. , |
|||
|
|||||
|
|
106 |
|
|
|
где qм – технологические потери материала, %; qм определяется аналогично qв., но вместо Ксток. (концентрация волокна в сточных водах) подставляется Кмат. – концентрация материала в сточных водах, кг/м3;
Dм – содержание материала в процентах к абсолютно сухой плите. Нормативные значения показателей приведены в таблицах: Dмат.(16-23),
Dм (24), Кёмк (25), Кобр. (15).
Значения Кобр. и Кемк. расчетным путем получают по формуле
Кобр. = ВВо ,
где
где
Во – ширина ковра до обрезки продольной кромки, мм; В – ширина ковра после обрезки продольной кромки,мм.
Коэффициент Кемк. определяют по формуле
К = Qмат. −qпром. , емк. Qмат.
Qмат. – количество материала, израсходованного на производство плит за межпрофилактический цикл, кг;
qпром. – количество отходов материала, имеющих место при промывках емкостей, предусмотренных технологией производства за межпрофилактический цикл, кг.
При сухом способе производства ДВП:
для материалов, смешиваемых с волокном
17
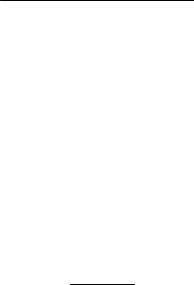
Кисп. = (100 +qн +qф4 +qш ) Dм Кемк..
10
При расчете коэффициента Кисп.. для нешлифованных плит qш = 0. Дозировки материалов выражают в абсолютно сухом веществе (Dм) или
в товарном ( Dмт ) исчислении. Соответственно в результатах расчета получают: Нмат. – норму расхода материала в абсолютно сухом исчислении; Нтм – норму расхода материала в товарном исчислении.
Пересчет Dм в Dмт производят по формуле
Dмт = 100КDм ,% ,
где К – содержание абсолютно сухого вещества в материале, %.
Аналогично пересчитывают нормы расхода материала.
Результаты расчётов сводят в таблицу 3.1.
Таблица 3.1
Сводная таблица расчётных значений
N |
Наименование параметра |
Усл. обозн. |
Ед. изм. |
Значение |
п/п |
|
|
|
|
|
|
|
|
|
1 |
2 |
3 |
4 |
5 |
1. |
Индивидуальные специализированные |
|
м3сырья |
|
|
нормы расхода древесного сырья: |
|
тыс.м2ДВП |
|
1.1 |
для сырья тонкомерного, отходов |
Нт |
|
|
|
лесозаготовок, дров |
|
|
|
|
|
|
|
|
1.2 |
для отходов лесопиления и |
Но |
|
|
|
деревообработки |
|
|
|
|
|
|
|
|
1.3 |
для щепы, тонкомерных деревьев и сучьев |
Нщ |
|
|
|
|
|
|
|
1.4 |
для отходов ЦБП |
|
|
|
|
|
|
|
|
2. |
Нормообразующие расчёта по п. 1 |
|
|
|
|
|
|
|
|
2.1 |
Чистый расход абс. сухого волокна |
П |
кг/тыс.м2 |
|
|
|
|
|
|
2.2 |
Суммарные отходы волокна для ДВП |
qсум |
% |
|
|
мокрого способа |
|
|
|
|
18 |
|
|
|
Продолжение таблицы 3.1
1 |
2 |
3 |
4 |
5 |
2.3 |
Суммарные отходы волокна для ДВП |
q′сум |
% |
|
|
сухого способа |
|
|
|
|
|
|
|
|
2.4 |
Выход ДВ-массы, поступающей в |
Рм |
% |
|
|
размольное отделение для ДВП мокрого |
|
|
|
|
способа |
|
|
|
|
|
|
|
|
2.5 |
Отходы при разделке круглых |
qр |
% |
|
|
лесоматериалов |
|
|
|
|
|
|
|
|
2.6 |
Выход древесины после разделки |
Рр |
% |
|
2.7 |
Расход древесного сырья с учётом |
Нд |
м3/тыс.м2 |
|
|
коэффициента пересчёта |
|
|
|
|
|
|
|
|
3. |
Индивидуальная специфицированная |
|
|
|
|
норма расходов материалов |
|
|
|
|
|
|
|
|
3.1 |
Норма для материалов, содержание |
Нмат |
кг/тыс.м2 |
|
|
которых рассчитано в % абс. сух. волокна |
|
|
|
|
|
|
|
|
3.2 |
Норма для материалов, содержание |
′ |
кг/тыс.м2 |
|
|
|
Н мат |
|
|
|
которых определено НТД в % к массе ДВП |
|
|
|
|
|
|
|
|
ПРАКТИЧЕСКАЯ РАБОТА № 4
Технические требования к ДСтП на синтетических смолах по европейскому стандарту
Древесностружечные плиты изготавливают методом горячего прессования из смеси специально изготовленных древесных частиц со связующим на основе синтетических смол. Процесс изготовления ДСтП является практически непрерывным, высокоавтоматизированным.
Прежде всего, нужно изучить характеристики сырья и связующего для производства древесностружечных плит, их отличительные особенности, выяснить сравнительную степень пригодности различных видов сырья и связующих для изготовления плит с точки зрения их качества, свойств, производительности процесса, свойств получаемых плит.
Европейский стандарт EN 312, определяющий технические требования к ДСтП, состоит из следующих частей:
–312-1. Общие требования ко всем типам ДСтП.
–312-2. Требования к ДСтП общего назначения - марки Р2.
19
–312-3. Требования к ДСтП для интерьера и мебели - марки РЗ.
–312-4. Требования к конструкционным ДСтП - марки Р4.
–312-5. Требования к конструкционным влагостойким ДСтП - марки Р5.
–312-6. Требования к особо прочным ДСтП - марки Р6.
–312-7. Требования к особо прочным влагостойким ДСтП - марки Р7.
Таким образом, европейский стандарт определяет шесть марок ДСтП для шести условий эксплуатации. Соответственно этому различаются и требования к физико-механическим свойствам плит.
В таблице 4.1 приведены их нормативные показатели для лабораторных условий: при относительной влажности воздуха 65 % и температуре воздуха 20 °С.
Общие требования к товарным ДСтП всех типов, перечисленные в первой части стандарта, определяются следующими показателями (они установлены для относительной влажности воздуха 65 % и температуры 20 °С):
Допуск по толщине как для отдельной плиты, так и для их партии составляет для шлифованных ДСтП ±0,3 мм, для нешлифованных от -0,3 до +1,7 мм; допуски по длине и ширине плиты составляют ±5 мм (метод испытания описан в стандарте EN 324-1). Прямолинейность кромок по стандарту должна быть 1,5 мм/м, а перпендикулярность сторон 2,0 мм/м (метод испытания EN 324-2). Влажность плит при вышеназванных окружающих условиях должна быть, согласно методу испытания EN 322, в пределах 5-13 %.
Таблица 4.1. Требования стандарта EN 312 к физико-механическим свойствам ДСтП
Марка |
|
|
Номинальная толщина плиты, мм |
|
|
||||
ДСтП |
|
|
|
|
|
|
|
|
|
3-4 |
4-6 |
6-13 |
13-20 |
20-25 |
25-32 |
32-40 |
40 |
||
|
|
|
|
|
|
|
|
|
|
|
|
Предел |
прочности |
при изгибе, МПа (ЕN310) |
|
|
|||
|
|
|
|
|
|
|
|
|
|
Р2 |
14 |
14 |
12,5 |
11,5 |
|
10 |
8,5 |
7 |
5,5 |
|
|
|
|
|
|
|
|
|
|
РЗ |
13 |
15 |
14 |
13 |
|
11,5 |
10 |
8,5 |
7 |
|
|
|
|
|
|
|
|
|
|
Р4 |
15 |
17 |
17 |
15 |
|
13 |
11 |
9 |
7 |
|
|
|
|
|
|
|
|
|
|
Р5 |
20 |
19 |
18 |
16 |
|
14 |
12 |
10 |
9 |
|
|
|
|
|
|
|
|
|
|
Р6 |
- |
- |
20 |
18 |
|
16 |
15 |
14 |
12 |
|
|
|
|
|
|
|
|
|
|
Р7 |
- |
- |
22 |
20 |
|
18,5 |
17 |
16 |
15 |
|
|
|
|
|
|
|
|
|
|
|
|
Модуль |
упругости |
при изгибе, МПа (EN 310) |
|
|
|||
|
|
|
|
|
|
|
|
|
|
РЗ |
1800 |
1950 |
1800 |
1600 |
|
1500 |
1350 |
1200 |
1050 |
|
|
|
|
|
|
|
|
|
|
Р4 |
1950 |
2200 |
2300 |
2150 |
|
1900 |
1700 |
1500 |
1200 |
|
|
|
|
|
|
|
|
|
|
Р5 |
2550 |
2550 |
2550 |
2400 |
|
2150 |
1900 |
1700 |
1550 |
|
|
|
|
|
|
|
|
|
|
|
|
|
|
|
20 |
|
|
|