
4842
.pdf21
Лабораторная работа № 4
ОПРЕДЕЛЕНИЕ ТОЧНОСТИ РАЗМЕРОВ ЗАГОТОВОК И ГОТОВЫХ ДЕТАЛЕЙ
Цель работы: практическое ознакомление слушателей с методом статистического контроля точности обработки деталей на деревообрабатывающих станках.
Работа проводится группами студентов по 3 человека в каждой. Каждая группа с помощью точного измерительного прибора (микрометра или штангенциркуля) определяет размеры деталей, указанные в задании.
Общие сведения: Точность обработки – это степень соответствия обработанной детали ее номинальному размеру и заданной форме. То или иное отклонение от заданного размера или формы является характеристикой погрешностей обработки. Погрешности, которые обычно имеют место при обработке деталей, могут быть систематическими или случайными. Систематические погрешности делятся на два вида:
1.Погрешности, остающиеся постоянными в процессе обработки партии
деталей;
2.Погрешности, закономерно изменяющиеся в процессе обработки.
Кпервым относят погрешности обработки, являющиеся следствием геометрических погрешностей станка, инструмента или приспособления.
Ко вторым относятся погрешности, вызванные постепенным износом режущего инструмента в процессе работы, нагревом станка и режущего инструмента.
Случайные погрешности характеризуются рассеиванием размеров деталей в партии. К числу случайных погрешностей могут быть отнесены погрешности, вызываемые неоднородностью материала, неодинаковой величиной припусков, колебанием режимов обработки.
При определении результирующей погрешности точности обработки используется статистический метод, основанный на законе больших чисел. Все случайные погрешности подчиняются определенной закономерности. Проблема определения случайных событий разрешена Гауссом, который вывел закон нормального распределения событий.
Этот закон отвечает формуле

22
|
|
1 |
|
|
x 2 |
|
|
Y |
|
|
2 2 , |
||||
|
|
|
|
||||
|
|
2 |
|||||
|
|
|
|
|
|
где – среднеквадратичное отклонение от среднего значения группирования размеров);
Y – частота появления погрешности;
ℓ – основание натурального логарифма;
X – погрешность размера, отсчитываемая от центра группирования. Среднее значение, или центр группирования размеров,
Мср XZ ,
n
(4.1)
(центр
(4.2)
где X – среднее значение интервала;
Z – число замеров заготовок, находящихся в данном интервале; n – количество всех размеров.
Величина М совпадает с центром группирования, около которого, в основном, располагаются значения размеров партии.
Но это среднее арифметическое дает представление о средней точности обработки, но не выражает пределов их колебания.
Поэтому определяется среднеквадратичное отклонение
|
|
|
|
|
|
X M 2 Z |
. |
(4.3) |
|
n 1 |
||||
|
|
|
Знаки ± показывают, что отклонение может быть как в ту, так и в другую сторону от центра группирования М.
При сравнении двух средних арифметических, выраженных в равных единицах, недостаточно знать среднее квадратичное отклонение. Вводится еще понятие коэффициента изменчивости
V |
100 |
, % . |
(4.4) |
|
|||
|
Mср |
|
Полученный результат среднего арифметического М не может точно характеризовать величину данного свойства, так как если мы получим несколько очень больших или очень малых результатов измерения, то они повлияют на величину М. Вводится еще понятие средней ошибки среднего арифметического, которая позволяет по частному значению среднего арифметического судить об общей его величине
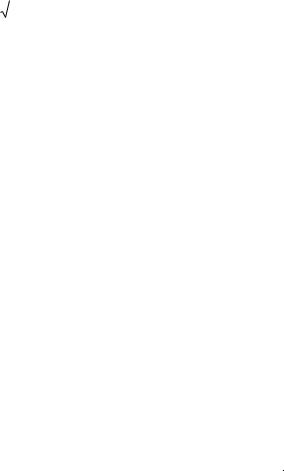
23
m |
|
|
. |
(4.5) |
|||
|
|
|
|
||||
|
|
|
|
||||
|
n |
||||||
|
|
|
|
|
|
||
Среднюю ошибку можно выразить в процентах от среднего |
|||||||
арифметического: |
|
|
|
|
|
|
|
P |
100m |
, % . |
(4.6) |
||||
|
|||||||
|
Mср |
|
|
|
Это показатель точности. Он характеризует надежность результатов опыта. Показатель точности должен быть меньше 5 %.
Порядок выполнения работы
1.Произвести 50 – 100 замеров указанных в задании размеров деталей. Полученные результаты записать в табл. 4.1.
|
|
|
Таблица 4.1 |
|
|
Результаты замеров |
|
|
|
|
|
|
|
|
№ п/п |
Размер детали |
№ п/п |
Размер детали |
|
|
|
|
|
|
1 |
|
6 |
|
|
|
|
|
|
|
2 |
|
7 |
|
|
|
|
|
|
|
3 |
|
8 |
|
|
|
|
|
|
|
4 |
|
9 |
|
|
|
|
|
|
|
5 |
|
и т. д. |
|
|
2. Из полученных результатов выделить наибольший и наименьший размеры Xmax и Xmin. Разбить все полученные размеры на классы. Число классов должно быть более 6. Определить величину классового промежутка
|
|
|
К |
X max X min |
, |
|
|
|
|
||
|
|
|
|
|
|
|
|
|
|
||
|
|
|
|
|
N |
|
|
|
|
||
где N – число классов. |
|
|
|
|
|
|
|
|
|
||
3. Произвести группирование размеров по табл. 4.2. |
|
|
|||||||||
|
|
|
|
|
|
|
|
|
|
|
Таблица 4.2 |
|
|
Результаты обработки материалов |
|
|
|||||||
|
|
|
|
|
|
|
|
|
|
|
|
№ |
Граница |
Средний |
Число |
|
XZ |
|
X-M |
|
(X-M)2 |
(X-M)2Z |
|
класса |
класса |
размер |
замеров |
|
|
|
|
|
|
|
|
|
|
|
|
|
|
|
|
|
|
|
|
1 |
|
|
|
|
|
|
|
|
|
|
|
|
|
|
|
|
|
|
|
|
|
|
|
2 |
|
|
|
|
|
|
|
|
|
|
|
|
|
|
|
|
|
|
|
|
|
|
|
3 |
|
|
|
|
|
|
|
|
|
|
|
|
|
|
|
|
|
|
|
|
|
|
|
и т.д. |
|
|
|
|
|
|
|
|
|
|
|
|
|
|
|
|
|
|
|
|
|
|
|
|
|
|
n |
|
XZ |
|
|
|
|
|
X M 2 Z |
|
|
|
|
|
|
|
|
|
|
|
|
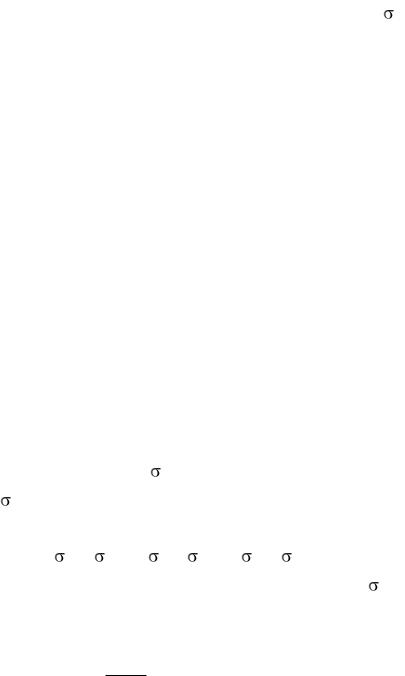
24
4. Пользуясь приведенными выше формулами, определить М, , и Р.
5.Построить фактическую кривую распределения. Для этого на оси абсцисс откладывается средний размер каждого класса (Х). На перпендикулярах, восстановленных из точек, соответствующих средним размерам каждого класса, отмечается точками высота, соответствующая частоте повторения размеров данного класса. Нанесенные таким образом точки последовательно соединить отрезками прямых, в результате чего получится ломаная линия. Эта линия называется экспериментальной кривой распределения.
6.Построить кривую нормального распределения, которая характеризуется двумя параметрами: средним размером партии М, определяющим центр группирования размеров, и средним квадратичным отклонением, определяющим величину поля рассеивания. В пределах М ±36 лежат практически 100 % всех размеров. Кривая нормального распределения строится на том же графике, что и экспериментальная кривая.
На оси абсцисс отмечается значение среднего размера М. Вправо и влево от точки М откладывается значение Х.
Х=М±d ,
где d – доля .
Для построения кривой достаточно вычислить значения абсцисс и координат для ±0,5 , ±1 , ±1,5 , ±2 , ±2,5 , ±3 .
Значение Х отмечается на графике как в долях , так и в мм. Наибольшая высота кривой будет в точке М. Она определяется по формуле
0,4n ,
где К – величина классового промежутка, n – число замеров.
Ординаты, соответствующие абсциссами 0,5; 1; 1,5; 2; 2,5; 3, вычисляются по формуле
y hH ,
где h – числовой коэффициент (берется из табл. 4.3); H – наибольшая высота кривой.
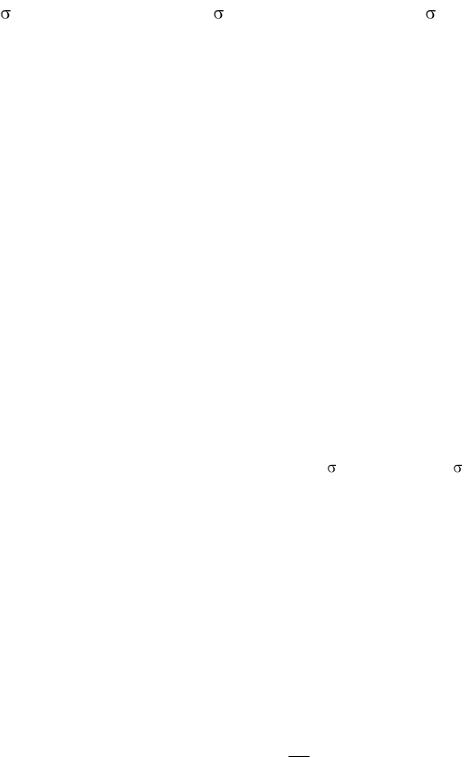
25
|
|
|
|
|
Таблица 4.3 |
|
|
|
|
|
|
|
|
в долях |
h |
в долях |
h |
в долях |
h |
|
|
|
|
|
|
|
|
0,1 |
0.995 |
1,1 |
0,546 |
2,1 |
0,110 |
|
0,2 |
0.980 |
1,2 |
0,487 |
2,2 |
0,089 |
|
0,3 |
0,956 |
1,3 |
0,430 |
2,3 |
0,071 |
|
0,4 |
0,923 |
1,4 |
0,375 |
2,4 |
0,056 |
|
0,5 |
0,883 |
1,5 |
0,325 |
2,5 |
0,044 |
|
0,6 |
0,835 |
1,6 |
0,278 |
2,6 |
0,034 |
|
0,7 |
0,738 |
1,7 |
0,236 |
2,7 |
0,028 |
|
0,8 |
0,726 |
1,8 |
0,198 |
2,8 |
0,020 |
|
0,9 |
0,667 |
1,9 |
0,164 |
2,9 |
0,015 |
|
1,0 |
0,607 |
2,0 |
0,135 |
3,0 |
0,011 |
|
|
|
|
|
|
|
|
Результаты вычислений значений абсцисс и ординат сводятся в табл. 4.4.
|
|
|
|
|
|
Таблица 4.4 |
|
|
Результаты расчетов |
|
|
||
|
|
|
|
|
|
|
Отклонение от М |
|
Значение абсцисс, мм |
Значение |
|||
|
|
|
|
|
|
ординат Y |
в долях |
в мм |
|
X1=M+d |
|
X2=M-d |
|
|
|
|
|
|
|
|
0,5 |
|
|
|
|
|
|
|
|
|
|
|
|
|
1,0 |
|
|
|
|
|
|
|
|
|
|
|
|
|
1,5 |
|
|
|
|
|
|
|
|
|
|
|
|
|
2,0 |
|
|
|
|
|
|
|
|
|
|
|
|
|
2,5 |
|
|
|
|
|
|
|
|
|
|
|
|
|
3,0 |
|
|
|
|
|
|
|
|
|
|
|
|
|
По найденным значениям X и Y строится кривая.
7.Определить процент годных деталей, а также процент исправимого и неисправимого брака.
i Fб 100 , %,
Fs
где Fs – величина площади под кривой нормального распределения; Fб – часть площади под кривой, лежащей в пределах поля допуска.
Станок обеспечивает требуемую точность деталей, когда соблюдается следующее условие:
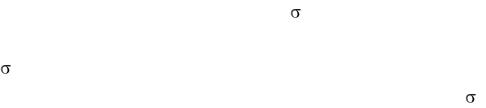
26
δ > 6 ,
где δ – допуск в мм на изготовление детали;
–среднее квадратичное отклонение.
Втех случаях, когда максимальная погрешность «6 » велика и превышает δ, станок не обеспечит взаимозаменяемость деталей, его необходимо подвергнуть ремонту и тщательной регулировке или заменить другим, более точным.
8.Написать отчет.
Содержание отчета
1.Понятие о точности обработки.
2.Виды и причины возникновения погрешностей.
3.Результаты измерений и вычисления статистических характеристик.
4.Графики кривых.
5.Анализ результатов и выводы.
27
Лабораторная работа № 5
ПЛОТНОСТЬ, ВЛАЖНОСТЬ И ПРЕДЕЛ ПРОЧНОСТИ ПРИ РАСТЯЖЕНИИ ШПОНА
Цель работы: освоить методы определения плотности, влажности и предела прочности при растяжении шпона согласно стандартам.
Приборы и материалы: весы с погрешностью взвешивания не более 0,01 г; шкаф сушильный; эксикатор; кальций хлористый; штангенциркуль с погрешностью измерения не более 0,1 мм; микрометр или толщиномер с погрешностью измерения не более 0,01 мм; машина испытательная с погрешностью измерения нагрузки не более 1 %; образцы шпона лущеного не менее трех на каждый вид испытания.
Общие сведения: Шпон строганый изготавливают из древесины следующих пород: березы, бука, граба, груши, клена, красного дерева, липы, ольхи, ореха, осины, тополя, ивы, бархатного дерева, вяза, дуба, ильма, карагача, каштана, ясеня, лиственницы, сосны.
В зависимости от текстуры древесины шпон подразделяют на виды: радиальный (Р), полурадиальный (ПР), тангентальный (Т), тангентальноторцовый (ТТ).
В зависимости от качества древесины, размеров по длине и ширине шпон подразделяют на первый и второй сорт. Основными сортообразующими пороками древесины являются сучки, грибковые поражения, химические окраски, поражения насекомыми, трещины, пороки строения, механические повреждения.
Шпон строганый изготавливают обрезным и прирезным. Размеры обрезного шпона устанавливают по стандарту, а прирезного – по согласованию с потребителем. Влажность шпона должна составлять (8±2) %.
Шпон строганый выпускают: длиной от 900 мм (для 1-го сорта) и 400 мм (для 2-го сорта) с градацией 50 мм; шириной 120 мм (для 1-го сорта) и 60 мм (для 2-го сорта) с градацией 10 мм. Установлена следующая толщина: 0,4; 0,6; 0,8; 1,0 мм с предельным отклонениием ±0,05 мм.
Параметр шероховатости поверхности Rmmaxi должен быть не более 200 мкм для дуба, ясеня, ильма, лиственницы, сосны и крупнорассеянососудистых пород, а для древесины остальных пород – не более 100 мкм.
28
Строганый шпон подвергают следующим основным методам испытания по определению:
внешнего вида шпона визуально;
толщины шпона с погрешностью измерения не более 0,01 мм;
длины и ширины шпона с погрешностью измерения не более 1,0 мм для ширины и не более 10,0 мм для длины;
шероховатости шпона;
влажности шпона;
волнистости шпона с погрешностью измерения не более 1,0 мм;
косины листа шпона с погрешностью измерения не более 0,5 мм.
Шпон лущеный вырабатывают из древесины клена, ясеня, ильма, дуба,
липы, осины, тополя, ели, пихты, кедра, лиственницы. Однако на практике его делают преимущественно из древесины березы и в меньшей мере из древесины ольхи.
В зависимости от качества древесины и обработки шпон подразделяют на пять сортов: Е (элита), I, II, III, IV – для лиственных пород и ЕХ (элита), IХ, IIХ, IIIХ, IVХ – для хвойных пород.
К шпону сорта Е предъявляют высокие требования: не допускаются частично сросшиеся сучки и отверстия от выпавших сучков, грибные поражения и химические окраски, ложное ядро, трещины, прорости, червоточины, наклон волокон, кармашки, засмолок и дефекты обработки. Здоровые сросшиеся сучки допускают с ограничениями. У последующих сортов требования к качеству соответственно снижаются.
Лущеный шпон выпускают длиной от 800 до 1200 мм с градацией 100 мм и от 1300 до 3750 мм с градацией 100 мм; шириной от 150 до 750 мм с градацией 50 мм и от 800 до 3750 мм с градацией 100 мм. Толщина шпона лиственных пород может быть 0,55; 0,75; 0,95; 1,15 мм и от 1,25 до 4,0 мм с градацией 0,25 мм. Толщина шпона из хвойных пород может быть от 1,2 до 4,0 мм с градацией 0,4 мм и от 4,0 до 6,5 мм с градацией 0,5 мм.
Влажность шпона составляет (6±2) %. Предел прочности при растяжении шпона согласно требованиям стандарта представлен в табл. 5.1.
29
Таблица 5.1 Нормы предела прочности при растяжении лущеного шпона лиственных и
хвойных пород
|
Предел прочности при |
||
Порода древесины |
растяжении, МПа |
||
|
|
|
|
|
вдоль волокон |
поперек волокон |
|
|
|
|
|
Береза |
75,0 |
2,5 |
|
|
|
|
|
Осина, ольха, бук, клен, ильм, |
60,0 |
1,5 |
|
липа, тополь |
|||
|
|
||
|
|
|
|
Ель, сосна, лиственница, пихта, |
50,0 |
1,0 |
|
кедр |
|
|
|
|
|
|
Лущеный шпон подвергают следующим основным методам контроля по определению:
дефектов обработки и размеров пороков древесины;
длины и ширины шпона;
толщины шпона;
шероховатости поверхности шпона;
косины листа шпона;
предела прочности при растяжении;
влажности шпона.
Отбор образцов для физико-механических испытаний производят по стандарту.
Порядок выполнения работы
1. Определение предела прочности при растяжении. Определение предела прочности при растяжении лущеного шпона производят на образцах: 200×20×S
– при растяжении вдоль волокон; 240×120×S – при растяжении поперек волокон; 240×140×S – при растяжении под углом 45º. К концам образцов из лущеного шпона приклеивают шпон, или тонкую фанеру, или клеевую ленту длиной, равной ширине образцов, и шириной 30 мм. Для испытаний отбирают не менее трех образцов без пороков влажностью 8 %. Отклонение от номинальных размеров образцов не должно быть более: ±0,5 мм – по ширине;
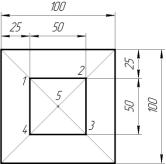
30
±1,0 мм – по длине, а в пределах одного образца не более ±0,1 мм. На середине длины образца измеряют его толщину с погрешностью не более ±0,01 мм и ширину с погрешностью не более ±0,1 мм.
Образец устанавливают в захваты машины с таким расчетом, чтобы его продольная ось совпадала с осями головок машины. Время действия равномерно возрастающей нагрузки на образец до полного его разрушения должно составлять: (60±30) с – при испытании образцов вдоль волокон; (30±15) с – при испытании образцов поперек волокон и под углом 45o. Образцы, разрушение которых произошло не в рабочей части, в расчет не принимаются, и они должны быть заменены. Величину разрушающей нагрузки и результаты всех замеров заносят в табл. 5.2.
2. Определение плотности шпона. Для определения плотности шпона используют три образца размером 100×100×S мм. Образцы маркируют, взвешивают с погрешностью не более 0,01 г, а затем определяют их линейные размеры. Толщину образца измеряют в пяти точках, указанных на рис. 5.1, с погрешностью измерения не более 0,01 мм.
Рис. 5.1. Схема замера толщины образца для определения плотности шпона
За толщину образца принимают среднее арифметическое результатов пяти измерений.
Длину и ширину образца измеряют в двух местах параллельно долевой и продольной кромкам образца с погрешностью не более 0,1 мм. За длину и ширину образца принимают среднее арифметическое результатов двух измерений. Результаты измерений и взвешивания записывают в табл. 5.3.
3. Определение влажности шпона. Для определения влажности шпона используют три образца любых размеров массой не менее 3 г. При определении влажности образцы взвешивают с погрешностью не более 0,01 г. Взвешенные