
2983
.pdf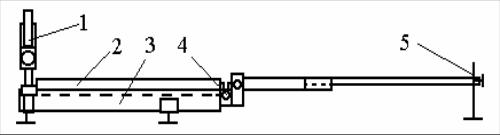
31
испытаний в точках, расположенных на равном расстоянии друг от друга. Испытания ведут по правой полосе наката (1-1,5 м от кромки проезжей части).
3 Измерение прогибомером
3.1 Устройство прибора Длиннобазовый рычажный прогибомер представляет собой
измерительный рычаг, шарнирно закрепленный опорной части. Рычаг состоит из двух плеч, соединяющихся между собой болтами. На одном конце рычага закрепляется измерительный штырь на другом - индикатор часового типа, ножка которого устанавливается на клиновидную опорную подкладку.
Рис. 5.1 Схема длиннобазового рычажного прогибомера: 1 – индикатор для измерения прогиба; 2 – вращающийся рычаг; 3 – неподвижная часть (швеллер); 4 – ось вращения; 5 – измерительная часть
3.2 Методика измерения Груженый двухосный автомобиль со статической нагрузкой на заднюю
ось 100 кН (МАЗ-200, 500, 5335 и др.) располагается на проезжей части по полосам наката (1-1,5 м от края проезжей части).
Прогибомер устанавливают таким образом, чтобы измерительный щуп с подпятником располагался строго между скатами сдвоенного правого колеса груженого автомобиля под центром задней оси. На другом конце рычага под измерительный стержень индикатора часового типа устанавливают клиновидную опорную подкладку. Автомобиль остается на точке до тех пор, пока отсчет по индикатору i0 не будет изменяться на 0,005 мм за 10с. Отсчет записывают в табл.5.1.. Затем автомобиль отъезжает не менее чем на 5 м от прогибомера. Дождавшись пока отсчет на индикаторе i не будет изменяться в течение 10 с более чем на 0,005 мм, записывают его в табл.5.1 Удвоенная разность отсчетов по индикатору до и после съезда автомобиля соответствует

32
упругому прогибу:
li=2(i-i0)
3.3 Обработка результатов измерений Фактический модуль упругости Еф определяем по формуле
Еф = PDl (1−μ2 )
где Р - среднее расчетное давление колеса на покрытие, МПа; D - расчетный диаметр следа колеса автомобиля, см;
l - упругий прогиб дорожной конструкции, см; µ - коэффициент Пуассона, µ=0,3.
Р=Кж·Рш, где Кж – коэффициент жесткости шины, Кж=1,1-1,3 Рш – давление воздуха в шине, МПа.
D =1,13 QP ,
где Q - нагрузка на колесо, кг;
(5.2)
(5.3)
Q=Q3/2, Q3 - нагрузка на заднюю ось автомобиля, кг.
l=li·Киз,
li – прогиб дорожной конструкции, измеренный в процессе линейных испытаний, см;
Кизм - коэффициент изменения прогиба во времени.
Кизм=lср/lki,
lср - прогиб на контрольной точке при состоянии дорожной конструкции принятом за расчетный, см;
lki - прогиб дорожной конструкции на расчетной точке в момент проведения испытаний, см;
Таблица 5.1
Определение модуля упругости дорожной одежды
время |
Место |
Отсчет по |
Прогиб |
Коэффициент |
Упругий |
Модуль |
Прим |
|
ия |
индикатору |
ии при |
прогиба во |
дорожной |
в заданной |
е |
||
|
испытан |
конструкц |
изменения |
прогиб |
упругости |
ечани |
||
и |
|
при |
при |
линейных |
времени, Кизм |
конструкци |
точке Еф, |
|
Дата |
|
нагруже |
загрузке |
испытания |
|
и l, см |
МПа |
|
|
|
нии i0 |
i |
х li, см |
|
|
|
|
|
|
|
|
|
|
|
|
|
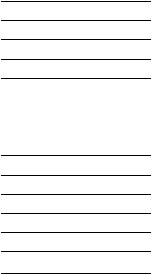
33
Полученное значение фактического модуля упругости сравнивают с возможно минимальным значением требуемого модуля упругости с учетом коэффициента прочности Кпр и необходимости обеспечения требуемой ровности Ks:
Еф ≥ Етр.s = Eтр·Кпр·Кs , |
(5.4) |
где Етр - требуемый модуль упругости, определяемый по табл. 5.2.
Кпр - коэффициент прочности, зависящий от типа дорожной одежды и категории дороги.
Ks - коэффициент, учитывающий необходимость обеспечения требуемой ровности дорожной одежды.
Таблица 5.2 Определение требуемого модуля упругости в зависимости от интенсивности
движения
Перспективная интенсивность |
Требуемые модули упругости, МПа |
||
движения, приведенная к нагрузке |
|
при малой скорости |
|
динамические |
статические Ес |
||
100 кН на ось, на полосу, авт/сут |
Eтр |
нагружения, Eтр.ос |
|
1 |
2 |
3 |
4 |
10 |
145 |
127 |
120 |
20 |
168 |
148 |
137 |
30 |
184 |
163 |
146 |
50 |
199 |
177 |
156 |
100 |
222 |
195 |
173 |
200 |
245 |
216 |
183 |
300 |
260 |
230 |
199 |
500 |
276 |
243 |
210 |
1000 |
299 |
263 |
227 |
2000 |
336 |
296 |
243 |
3000 |
336 |
296 |
254 |
5000 |
354 |
311 |
265 |
10000 |
376 |
330 |
280 |
Таблица 5.3
Определение коэффициента прочности дорожной одежды
Тип одежды и покрытия |
Категория дороги |
Кпр |
|
|
|
Дорожные одежды капитального типа с |
I, II, IIIп, Ic |
1,0 |
усовершенствованным покрытием |
|
|
III, IVп, IIc |
0,94 |
|
Одежды облегченного типа с |
III, IV, IVп, II |
0,90 |
усовершенствованным покрытием |
|
|
|
|
|
Переходные дорожные одежды |
IV, V, IIc, IIIc |
0,63 |

34
Таблица 5.4 Определение коэффициента обеспечения ровности дорожной одежды
Перспективная интенсивность |
Требуемая ровность дорожных одежд Srp, см/км |
|
|||||||
движения, приведенная к нагрузке 100 |
|
|
|
|
|
|
|
|
|
кН на ось, на одну полосу, авт/сут |
90 |
110 |
|
130 |
150 |
165 |
180 |
≥200 |
|
|
|
|
|
|
|
|
|
|
|
10 |
- |
- |
|
- |
- |
- |
- |
0,62 |
|
20 |
- |
- |
|
- |
- |
- |
0,71 |
0,67 |
|
30 |
- |
- |
|
- |
- |
0,75 |
0,74 |
0,71 |
|
50 |
- |
- |
|
- |
- |
0,76 |
0,75 |
0,72 |
|
100 |
1,10 |
1,03 |
|
0,91 |
0,86 |
0,82 |
0,80 |
0,76 |
|
200 |
1?15 |
1,09 |
|
1,01 |
0,94 |
0,91 |
0,88 |
- |
|
300 |
1,18 |
1,15 |
|
1?03 |
1,01 |
0,97 |
0,94 |
- |
|
500 |
1,23 |
1,20 |
|
1,17 |
1,15 |
1,08 |
1,04 |
- |
|
≥1000 |
1,38 |
1,34 |
|
1,30 |
1,26 |
1,18 |
1,11 |
- |
|
Q = M Kп q 2H / S |
|
|
|
(5.5) |
|||||
Кп |
= 0,5(l +l, |
/ l), |
|
|
|
(5.6) |
где М- масса падающего груза, кг;
q - ускорение свободного падения, 9,81 м/с2;
Кп - коэффициент, учитывающий потерю энергии при сбрасывании груза; l, l’ - вертикальные деформации дорожной одежды от первого и второго
ударов груза (после подскока) при одном и том же сбрасывании, см;
S - показатель, характеризующий жесткость амортизатора, равный деформации амортизатора от статического действия груза массой М, м.
Величину S определяют при ежегодных тарировках установки, которую обычно принимают в пределах 0,04-0,043 см.
Допустимая величина Qq=6·104±5·103 Н.
5.4 Измерение краткровременным нагружением 5.4.1 Установка УДН
Установка (рис.5.2) динамического нагружения УДН предназначена для измерения модуля упругости при передаче кратковременной нагрузки через жесткий штамп. Принцип ее работы заключается в следующем: груз массой М=100 ±5 кг сбрасывается по направляющей с высоты Н=80-100 см на пружину, что создает кратковременное усилие в течение Т=0,02-0,03 с, которое через штамп действует на дорожную одежду.
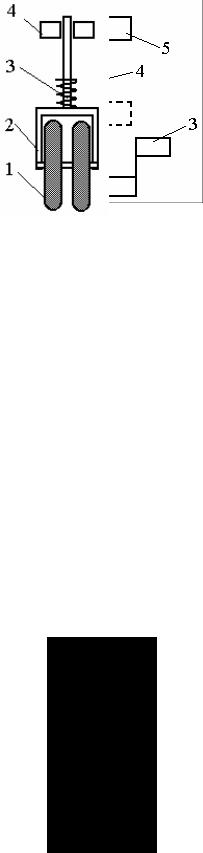
35
Рис. 5.2 Принципиальная схема установки динамического нагружения 1 – штамп; 2 – пружина; 3 – виброграф; 4 – направляющая; 5 - груз
Измерение упругой деформации фиксируется вибрографом. Наибольшее динамическое усилие, соответствующее нагрузке группы А (Qq=5·104 H), определяют по формуле (5.5).
5.4.2 Установка УДН-НК Принципиальное отличие установки УДН-НК (рис.5.3) от УДН состоит в
том, что усилие от сбрасываемого груза массой 250 кг передастся на покрытие не через жесткий штамп, а через сдвоенные пневматические колеса.
Установка крепится сзади грузового автомобиля и, как правило, входит в состав передвижных лабораторий. Ее производительность при 20 испытаниях на 1 км составляет 10 км/ч. В момент испытания автомобиль останавливается. При переезде от одной точки к другой колеса установки находятся в контакте с покрытием. В транспортном положении их поднимают.
Рис. 5.3 Принципиальная схема установки УДНК-НК: 1 – сдвоенные пневматические колеса; 2 – обойма для крепления колес; 3 – амортизирующее
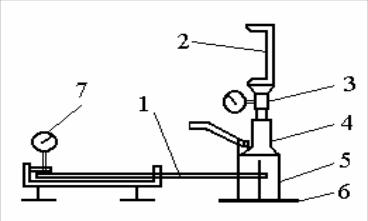
36
устройство; 4 – груз
Величину динамического усилия Qф, развиваемого установкой, определяют по формуле, приведенной в п 3.1. Периодически необходимо производить тарировку колес с вычислением показателя их жесткости δ1.
5.5Метод штамповых испытаний
5.5.1Устройство установки
Рис. 5.4 Схема установки для штамповых испытаний дорожной одежды: 1 – прогибомер; 2 – рама; 3 – динамометр; 4 – домкрат; 5 – опорные стойки; 6 – штамп
При испытании жестким штампом нагрузка на поверхность осуществляется через круглый жесткий штамп 6. Усилие создается домкратом 4, упираемым в раму груженого автомобиля 2 или другого транспортного средства, способного обеспечить усилие до 50 кН, измеряемое механическим динамометром 3. Прогиб дорожной конструкции фиксирует индикатор, установленный на прогибомере на расстоянии не менее 4 D от штампа и колес автомобиля. Если домкрат передает нагрузку на штамп через три опорные стойки 5, то измерительный стержень прогибомера 1 устанавливается в центре штампа. Если нагрузка передается непосредственно от домкрата, минуя стойки, то в стенке домкрата устраивается прорезь и стержень прогибомера устанавливается в нее. При этом индикатор часового типа располагается непосредственно около домкрата, а на расстояние, равное 4 -м диаметрам штампа, выносится ножка прогибомера.
5.5.2 Проведение испытаний
37
Перед началом испытаний автомобиль устанавливают на опоры, которые подставляют под раму недалеко от задних колес таким образом, чтобы расстояние между опорами и жестким штампом было не менее 1,5 м. Штамп устанавливается на испытуемый слой после тщательного выравнивания его поверхности с помощью тонкого слоя песка (1-5 мм). Затем производят нагружение штампа и выдерживают под максимальной нагрузкой в течение 2 минут с последующей разгрузкой.
Производят проверку устойчивости жесткой системы, для чего осуществляют легкие постукивания металлическим предметом по швеллеру прогибомера или по опорной балке. При этом стрелка индикатора должна слегка покачиваться, но оставаться на том же месте.
Испытания проводят ступенчатым нагруженном (3-5 ступеней) до достижения расчетного значения: 0,5 МПа на поверхности основания; 0,2 МПа на подстилающем слое и песках; 0,5-1 МПа на связных грунтах земляного полотна (большее значение - при влажности грунта менее 0,7 WT). Время нагружения от одной ступени до другой составляет 10-20 с. На каждой ступени выдерживается пауза в течение 30 с. Разгрузка осуществляется также ступенчато с выдерживанием тех же временных параметров.
Отсчеты по индикатору снимают на каждой ступени (при нагружении и разгрузке) после истечения временной паузы. Перед снятием отсчетов легко постукивают по швеллеру прогибомера или опорной балке.
5.5.3 Обработка результатов измерения Упругую деформацию конструкции определяют по разности отсчетов и
строят график зависимости упругой деформации от удельной нагрузки. График должен представлять плавную кривую выпуклую вверх - для зернистых материалов и вниз -для связных грунтов.
Модуль упругости для слоистой системы, а также для связных грунтов и материалов однородной конструкции определяют по формуле
Eу = 0,25 π p D (1 − μ2 )/ l , |
(5.7) |
где р- максимальное (расчетное) давление от штампа; D - диаметр жесткого штампа; μ - коэффициент Пуассона (для грунтов земляного полотна μ=0,35, для материалов оснований μ=0,25, для вычисления общего модуля упругости μ=0,3); l - упругая деформация, соответствующая данной нагрузке.
38
После определения модуля упругости его значения сравнивают с нормативным и делают выводы о состоянии испытываемой конструкции.
Контрольные вопросы
1Какова цель и сроки проведения испытаний дорожных конструкций на прочность?
2Конструкция и методика измерений с помощью длиннобазового прогибомера.
3Устройство установок для испытаний кратковременным нагружением и их применение.
4Метод штамповых испытаний.
Практическая работа № 6 ВИЗУАЛЬНАЯ ОЦЕНКА СОСТОЯНИЯ АВТОМОБИЛЬНЫХ ДОРОГ
1 Цель работы
Визуальное обследование конструктивных элементов участка автомобильной дороги, отнесение каждого элемента и всей автодороги в целом к соответствующему уровню содержания, назначение ремонтных мероприятий и описание технологии их проведения.
2 Общие сведения
Визуальную оценку состояния автомобильных дорог проводят ежемесячно при определении уровня содержания и первом этапе комплексной оценки качества дороги. По ее результатам определяют транспортноэксплуатационные характеристики автомобильной дороги, назначают участки для более детального (инструментального) обследования, дают заключение об уровне содержания обследуемого участка.
При визуальном осмотре производят простейшие измерения величины разрушений или дефектов, определяется их площадь, а также площадь загрязнения различных элементов дороги.
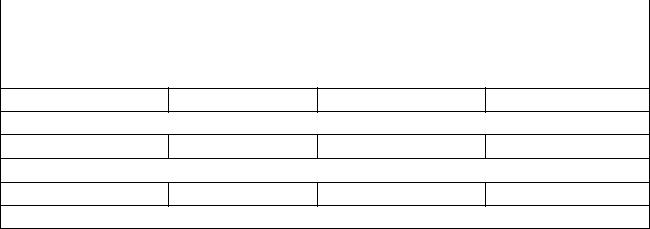
39
Результаты обследования заносятся в заранее заготовленные таблицы и журналы карандашом. При необходимости внесения исправлений не допускается стирание записей. Их зачеркивают, а рядом или сверху делают новую.
По результатам обследования каждый элемент относят к соответствующему уровню, который может быть допустимым, средним и высоким. Возможна балльная оценка, которая соответственно составляет 3,4 и 5. При недопустимом уровне содержания выставляется оценка 0.
Если хотя бы один конструктивный элемент оцениваемого участка дороги относят по уровню содержания к недопустимому, то и весь участок оценивается как не соответствующий уровню содержания.
3 Порядок проведения обследований
При проведении измерений используются: мерная лента или курвиметр, металлическая линейка, мел или вешки.
Группа студентов разбивается на две бригады и первоначального производит предварительную оценку одного километра дороги (каждая бригадапо 500 м). Определяются границы наихудших участков длиной по 100 м, которые фиксирует мелом или вешками. Длину участков определяют с помощью курвиметра или мерной ленты.
Каждый стометровый участок разбивается на 10 м фиксацией на нем дефектов и привязкой к пикетам. Величину разрушения или загрязнения измеряют металлической линейкой. Данные заносят в табл. 6.1.
|
|
|
Таблица 6.1 |
Результаты определения дефектов и разрушений |
|
||
|
|
|
|
Местоположение |
Вид разрушения |
Рисунок разрушения, |
Уровень содержания |
дефекта (разрушения) |
(деформации, |
его размеры и площадь |
элемента дороги на |
ПК |
загрязнения) |
|
данном участке |
|
|
|
|
Проезжая часть
Земляное полотно
Искусственные сооружения
Обустройство и обстановка

40
5 Обработка результатов
Оценку уровня содержания для различных элементов дороги производят согласно табл. 6.2 – 6.6.
|
|
|
|
Таблица 6.3 |
|
Оценка уровня содержания элементов дороги |
|
|
|||
|
|
|
|
|
|
Эксплуатационная |
|
Уровень содержания |
|
|
|
категория дорог |
|
|
|
|
|
допустимый |
средний |
|
высокий |
|
|
|
|
|
|
|
|
|
Проезжая |
часть |
|
|
|
Наличие полос загрязнения у кромок покрытия шириной до 0,5 м |
|
||||
|
(в процентах от площади покрытия) |
|
|
||
I |
нет |
нет |
|
нет |
|
II |
3 % |
1,5 % |
|
нет |
|
III |
5 % |
3 % |
|
нет |
|
IV |
8 % |
5 % |
|
3 % |
|
V |
10 % |
8 % |
|
5 % |
|
Максимальный |
просвет под 3 м рейкой |
в местах заделки |
повреждений |
|
|
|
не более 7 мм |
5 мм |
|
3 мм |
|
Наличие |
необработанных мест |
вылеживания битума на |
1000м2 |
|
|
I |
до 7 м2 |
до 5 м2 |
|
нет |
|
II |
10 м2 |
7 м2 |
|
5 м2 |
|
III |
15 м2 |
10 м2 |
|
7 м2 |
|
IV |
20 м2 |
15 м2 |
|
10 м2 |
|
V |
25 м2 |
20 м2 |
|
15 м2 |
|
Выбоины |
не более 15x60x5 (длина х ширину) на 1000 м2 |
|
|||
I |
0,3 м2 (в весенний |
нет |
|
нет |
|
|
период 1 5 м2) |
|
|
|
|
II |
1 м2 (3 м2) |
0,3 м2 (1,5 м2) |
|
нет |
|
III |
1,5 м2 (4,5 м2) |
1 м2 (3 м2) |
|
0,3 м2 (1,5 м2) |
|
IV |
2 м2 (6 м2) |
1,5м2 (4,5 м2) |
|
1 м2(3 м2) |
|
V |
2,5 м2 (7 м2) |
2м2 (6 м2) |
|
1,5м2 (4.5м2) |
|
Отдельные |
раскрытые трещины |
, на покрытии до 1000 м2 |
|
||
I |
0,5 см |
0,3 см |
|
нет |
|
II |
0,7 см |
0,5 см |
|
0,3 см |
|
III |
1 см |
0,7 см |
|
0,5 см |
|
IV |
1,3 см |
1 см |
|
0,7 см |
|
V |
1,5 см |
1,3 см |
|
1 см |
|
Гребенка |
, нарушение профиля |
(от общей площади |
) |
|
|
III |
до 5 % |
до 3 % |
|
нет |
|
IV |
до 10 % |
до 5 % |
|
до 3 % |
|
V |
до 15 % |
до 10 % |
|
до 5 % |
|
|
Колейность на переходном покрытии |
|
|
||
III |
до 2 см |
до 1 см |
|
нет |
|
IV |
до 3 см |
да 2 см |
|
нет |
|