
2983
.pdf
21
средней глубине впадин.
Сцепные качества на обследуемом участке принимают за удовлетворительные, если одновременно выполняются требования, предъявленные к покрытию по параметрам шероховатости и коэффициенту сцепления.
3 Определение шероховатости методом песчаного пятна
3.1 Приборы, оборудование и материалы Диск с рукояткой для распределения песка, природный песок в воздушно-
сухом состоянии, мерная емкость объемом не менее 200 см3, линейка, длиной не менее 30 см, щётка-сметка, гипс или быстротвердеющий цемент, вода, технический глицерин.
3.2 Подготовкакизмерениям После предварительной оценки назначают участки для выборочного
контроля. На выбранных участках производят измерения по каждой полосе наката и между ними, одновременно осуществляют измерения по оси проезжей части. Количество измерений для поверхностной обработки и устройства шероховатых поверхностейметодомвтапливанияприведенавтабл. 4.1.
3.3 Порядокпроведенияизмерений
Рис. 4.1. Последовательность выполнения операций I-III по методу "песчаного пятна": 1-поверхность покрытия; 2-песок; 3-диск с рукоятью
Из мерной ёмкости на поверхность покрытия высыпают 200 см3 (250 см3 при крупношероховатой поверхности) природного песка. Круговыми движениямис помощью диска с ручкой, как показано на рис. 4.1, разравнивают его по
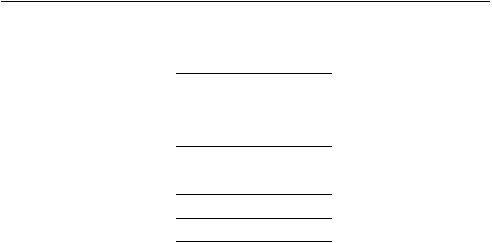
22
поверхности покрытия до тех пор, пока диск не начнет касаться поверхности выступов шероховатости. Затем с помощью линейки производят не менее четырех измеренийдиаметрапесчаногопятна. Данныеизмеренийзаносятвтабл4.2.
Таблица 4.1
Количество измерений по определению шероховатости
Длина участка, м |
Число измерений при глубине неровностей макрошероховатости, мм |
|||
0,3-2,0 |
|
2,1-3,0 |
более 3 |
|
|
|
|||
|
|
|
|
|
|
Поверхностная обработка |
|
||
|
|
|
2 |
|
1,0 |
1 |
|
3 |
|
|
|
|
6 |
|
50,0 |
3 |
|
10 |
|
|
|
|
36 |
|
1000,0 |
18 |
|
60 |
|
|
|
щебня |
|
|
|
Втапливание |
|
||
|
|
|
2 |
|
1,0 |
1 |
|
3 |
|
|
|
|
3 |
|
50,0 |
3 |
|
5 |
|
|
|
|
18 |
|
1000,0 |
9 |
|
30 |
|
|
|
|
|
|
|
Таблица 4.2 |
||
Результаты определения шероховатости |
|||||||||
|
|
|
|
|
|
|
|
|
|
Номер и адрес |
D1, см |
D2, см |
D3, см |
D4,см |
Dcp, см |
Vп, см3 |
Sз, см2 |
Нср, см |
|
участка измерений |
|
|
|
|
|
|
|
|
|
1 ПК |
|
|
|
|
|
|
|
|
|
|
|
|
|
|
|
|
|
|
|
|
|
|
|
|
|
|
|
|
|
|
|
|
|
|
|
|
|
|
|
Среднюю глубину впадин (Нср) определяют по отношению объема песка (Vп), распределенного на поверхности, к занятой им площади (Sз).
Нср = |
Vп |
(4.1) |
|
Sз |
|||
|
|
Для определения средней высоты выступов (Rz) вначале устанавливают среднюю приведенную высоту выступов шероховатости (Rср). Для этого оконтуривают поверхность, занятую песком, удаляют его из впадин шероховатости с помощью щетки и смазывают очищенную поверхность покрытия техническим глицерином. Приготавливают жидкое тесто из гипса или быстродействующего цемента (ориентировочно соотношение гипса и воды – 3:1 и распределяют его по исследуемой поверхности слоем 1-1,5 см. Через 5-7 минут слепок отделяют от покрытия

23
и выдерживают 10-15 минут до затвердения. После этого определяют объем песка, необходимый для заполнения впадин шероховатости слепка (VB) (методом "песчаного пятна"), численно равный объему шероховатости покрытия, и рассчитывают (Rср)
Rср |
= |
Vв |
(4.2) |
|
|
S з |
|
Среднюю высоту выступов шероховатости (Rz) определяем но формуле
R |
z |
= H |
ср |
+ R |
= |
Vп +Vв |
(4.3) |
|
|||||||
|
|
ср |
|
Sз |
|||
|
|
|
|
|
|
|
Макрошероховатостя покрытия, имеющие Кш>0,5 называются шипованными. В зависимости от средней высоты выступов Rz и глубины впадин Нср дается классификация шероховатым покрытиям, которая определяет область их применения на различных категориях дорог. В соответствии с полученными значениями по табл. 4.3. определяем, к какому типу шероховатости относится данное покрытие.
|
|
|
Таблица 4.3 |
Типы шероховатости дорожных покрытий |
|
||
|
|
|
|
Тип шероховатых |
Условные |
Параметры шероховатости |
|
покрытий |
обозначения |
Средняя высота |
Средняя глубина впадин |
|
|
выступов Rz , мм |
Нср, мм |
Гладкие |
Гл |
>0,1≤0,5 |
>0,02≤0,25 |
Мелкошероховатые |
Мшер |
>0,5≤3,0 |
>0,25≤1,5 |
Мелкошипованные |
Мшип |
|
>1,5≤2,5 |
Среднешероховатые |
Сшер |
>3,0≤6,0 |
> 1,0≤3,0 |
Среднешипованные |
Сшип |
|
> 3,0≤5,0 |
Крупношероховатые |
Кшер |
>6,0≤9,0 |
>2,0≤4,5 |
|
|
|
>4,5≤7,0 |
Крупношипованные |
Кшип |
|
|
|
|
|
|
На основании проведенных измерений сделать заключение о соответствии полученных значений нормативным требованиям, предъявляемым для шероховатой поверхности участка дороги.
Минимально допустимые в течение всего срока службы значения коэффициентов продольного сцепления и средней глубины впадин шероховатости приведены в табл. 4.4.

24
Таблица 4.4 Минимально допустимые значения коэффициентов продольного
сцепления и шероховатости
Условия |
|
|
|
|
|
Коэффициент |
Средняя глубина |
|
движения |
Характеристики участков дорог |
сцепления |
впадин |
|||||
|
|
|
|
|
|
|
макрошероховатости |
|
|
|
|
|
|
|
|
Нср, мм, для дрог в |
|
|
|
|
|
|
|
|
различных |
|
|
|
|
|
|
|
|
климатических зонах |
|
|
|
|
|
|
|
|
|
|
|
|
|
|
|
|
0,28 |
I и V |
II и IV |
Легкие |
Участки прямые или кривые радиусом |
0,30 |
0,35 |
|||||
|
1000 м и более, горизонтальные или с |
|
(0,60) |
(0,70) |
||||
|
продольным уклоном не более 30 %, с |
|
|
|
||||
|
элементами |
поперечного профиля, |
|
|
|
|||
|
установленными |
|
для |
дорог |
|
|
|
|
|
соответствующих категорий, и с |
|
|
|
||||
|
укрепленными |
обочинами |
без |
|
|
|
||
|
пересечений в одном уровне и |
|
|
|
||||
|
примыканий, |
при |
коэффициенте |
|
|
|
||
|
загрузки не более 0,3 |
|
|
|
|
|
||
|
|
0,30 |
|
|
||||
|
Участки на кривых в плане радиусами |
0,35 |
0,40 |
|||||
Затруднен |
250-1000 м; на спусках и подъемах с |
|
(0,70) |
(0,80) |
||||
ные |
уклонами от 30 до 60 %. Участки в |
|
|
|
||||
|
зонах сужений проезжей части (при |
|
|
|
||||
|
peконструкции), а также участки |
|
|
|
||||
|
дорог, отнесенные к легким условиям |
|
|
|
||||
|
движения, при коэффициенте загрузки |
|
|
|
||||
|
0,3-0,5 |
|
|
|
|
|
|
|
|
|
|
|
|
0,32 |
|
|
|
Опасные |
Участки |
с |
видимостью |
менее |
0,40 |
0,45 |
||
|
расчетной |
(для |
|
соответствующих |
|
|
|
|
|
категорий дорог); на спусках и |
|
|
|
||||
|
подъемах с уклонами более 50% при |
|
|
|
||||
|
длине более 100м; участки в зонах, |
|
|
|
||||
|
пересечений на одном уровне, а также |
|
|
|
||||
|
участки, отнесенные к легким и |
|
|
|
||||
|
затрудненным |
условиям, |
при |
|
|
|
||
|
коэффициенте загрузки свыше 0,5 |
|
|
|
||||
|
|
|
|
|
|
|
|
|
Сцепление при оценке качества покрытий следует считать удовлетворительным при условии соблюдения обоих параметров. Без скобок приведены значения для шероховатых поверхностей, в скобках – для шипованных.
25
4 Определение сцепных свойств установкой ПКРС-2У
Сплошной контроль сцепных свойств дорожных покрытий осуществляют установкой ПКРС – 2У или другими приборами, показания которых могут быть приведены к показаниям данной установки. Измерения производят по левой полосе наката каждой полосы движения автодороги. Количество измерений на каждом километре зависит от однородности поверхности покрытия и колеблется в пределах от 2 до 6. Дорожное покрытие должно быть искусственно увлажнено таким образом, чтобы обеспечить на покрытии расчетную пленку воды толщиной 1 мм. Под расчетной пленкой следует понимать условную величину, являющуюся отношением расхода воды к площади увлажнения. Измерительное колесо оборудуется шиной с протектором без рисунка размером 6,45-13 дюймов при внутреннем давлении воздуха в ней 0,17 ± 0,01 Мпа (1,7 ± 0,1 кгс/см2). Вертикальная нагрузка на прицепное колесо должна быть в пределах 2943 ± 30 Н.
4.1 Порядок проведения измерений За 500 м до начала измерений водитель включает дальний свет фар и
маяковые огни или табло "Измерение".
Набирает скорость 60 км/ч ± 3, которая поддерживается постоянной. За 50 м до нажатия педали блокировки колеса прицепа включается лентопротяжный механизм. В момент блокировки колеса непосредственно перед прицепным устройством подается вода для создания расчетной водной пленки толщиной 1мм. Колесо блокируется нажатием на тормозную педаль. Время торможения 2-3 с. При проведении измерений фиксируется температура окружающей среды и приводятся к расчетной температуре + 20 °С путем введения поправок согласно табл. 4.5.
Таблица 4.5
Температурные поправки
Температура, °С |
0 |
+5 |
+10 |
+15 |
+20 |
+25 |
+35 |
+40 |
Поправка |
-0,06 |
-0,04 |
-0,03 |
-0,02 |
0 |
+0,01 |
+0,02 |
+0,02 |
|
|
|
|
|
|
|
|
|
4.2 Обработка результатов измерений
Величину коэффициента сцепления определяют по тарировочной линейке
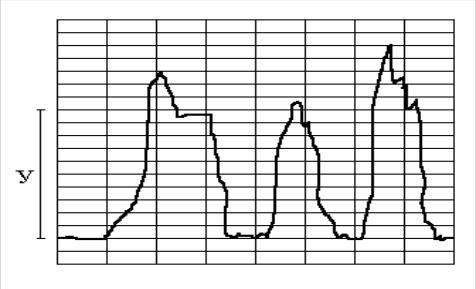
26
по расстоянию от нулевой линии до средней линии измерения (У). Первый всплеск в замерах не учитывается, так как он получается в начальный момент торможения колеса, когда оно полностью не заблокировано.
Рис. 4.2. Диаграмма самописца при изменении сцепления
Результаты расшифровки диаграммы самописца, а также значения поправок заносятся в табл. 4.6.
|
|
|
|
|
Таблица 4.6 |
|
Результаты измерений |
|
|
|
|
||
|
|
|
|
|
|
|
Номер |
Величин |
Тормозное |
Измеренный |
Температурная |
Значение |
|
измерени |
а У, мм |
усилие, кН |
коэффициент |
поправка, Δφt |
коэффициента |
|
я |
|
|
сцепления, φi |
|
сцепления с учетом |
|
|
|
|
|
|
температурной |
|
|
|
|
|
|
поправки, φ=φi+Δφt |
|
1 |
|
|
|
|
|
|
|
|
|
|
|
|
|
2 |
|
|
|
|
|
|
|
|
|
|
|
|
|
3 |
|
|
|
|
|
|
|
|
|
|
|
|
|
Среднее |
|
|
|
|
|
|
|
|
|
|
|
|
|
Полученные значения коэффициента сцепления сравниваем с данными табл. 4.4, приведенной в п. 3.3.

27
5 Определение коэффициента сцепления прибором ППК-МАДИ- ВНИИБД
5.1 Устройство прибора
Устройство прибора ППК-МАДИ-ВНИИБД (ТУ 78.1.004-87) показано на рис. 4.3.
Рис. 4.3. Схема прибора ППК-МАДИ-ВНИИБД: 1 – имитаторы; 2 – пружина; 3 – подвижный груз; 4 – подвижная муфта; 5 – толкающие тяги; 6 – опорная штанга
5.2 Подготовка прибора к работе
Прибор с помощью регулировочных винтов устанавливается таким образом, чтобы нижняя плоскость резиновых имитаторов находилась на расстоянии 15 ± 3 мм от дорожного покрытия. Измерительная шайба должна находится в верхнем положении. Перед первичным намерением или если прибор длительное время не эксплуатировался, необходимо произвести его калибровку. Для этого под резиновые имитаторы подкладываются стальные шлифованные пластины, при этом расстояние между нижней плоскостью имитатора и пластиной должно быть равно 7 – 13 мм. Далее поверхность пластин увлажняется объемом воды не менее 200 см2 и сбрасывается груз. Если в течении 5 сбрасываний показания измерительной шайбы не выходят за
28
пределы рисок, обозначающих величину коэффициента сцепления от 0,08 до 0,11 на шкале прибора, прибор считается откалиброванным. В противном случае необходимо произвести регулировку прибора путем изменения натяжения центральной пружины специальным винтом.
5.2 Порядок проведения измерений
Участок контроля состояния дорожного покрытия выбирается с учетом мест концентрации ДТП.
Перед проведением измерений увлажняют поверхность покрытия под имитаторами. Размер полосы увлажнения должен быть не менее 15×30 см, для чего необходимо израсходовать 200 см3 воды. Не позднее чем через 3 с необходимо нажать на кнопку сброса груза. По шкале снимают отсчет, на котором остановилась регистрирующая шайба, толкаемая муфтой. Данный отсчет характеризует сцепные качества покрытий.
При повторном измерении на одном и том же месте величина коэффициента сцепления, показываемая прибором, может меняться из-за изменения вязкости водной пленки в результате ее загрязнения. В случае если измерение проводят на заранее очищенном покрытии, эти изменения незначительны.
Для получения устойчивых значений коэффициента сцепления достаточно произвести пять измерений с интервалами 5–10 с. Далее определить среднее значение измеренной величины.
6 Контрольные вопросы
1Чем характеризуется макрошероховатость покрытия?
2Когда и как определяют сцепные свойства покрытия?
3Как проводят измерения шероховатости методом песчаного пятна?
4Какова методика определения сцепных свойств установкой ПКРС-2У?
5Устройство прибора ППК-МАДИ-ВНИИБД.
6Подготовка прибора и проведение измерений.
7Минимально допустимые значения коэффициентов продольного сцепления и шероховатости.
29
Практическая работа № 5 ОПРЕДЕЛЕНИЕ ПРОЧНОСТИ ДОРОЖНЫХ КОНСТРУКЦИЙ
1 Цель работы
Ознакомление с приборами и оборудованием для определения модуля упругости конструкций, испытание одним из приборов, обработка результатов с выводами о работоспособности испытываемой конструкции.
2 Общие сведения
В процессе работы дорожная одежда подвергается многократному воздействию динамических и статических нагрузок. Ее работоспособность и долговечность во многом зависят от возможности сопротивления сдвигу в грунте и слабосвязанных конструктивных слоях, прочности на растяжение при изгибе и общей жесткости дорожной одежды. Определение упругого прогиба позволяет дать объективную характеристику всем трем факторам и оценить состояние дорожной конструкции. Упругий прогиб определяют методами статического и кратковременного нагружения. Между этими методами можно установить удовлетворительную зависимость для изменения прогибов в пределах 0,1≤ lq≤ 1,0 мм.
lcm = (0,3h/h1 – 1,1)lq, (5.1)
где h - толщина слоев из материалов, содержащих органическое вяжущее; h1 - наиболее распространенная толщина слоев из указанных материалов,
равная 100 мм.
В расчетах для данных методов принимаются различные расчетные диаметры следа колеса, м2:
при динамическом нагружении - 0,37. при статической нагрузке - 0,33.
При испытаниях среднее удельное давление колеса на покрытие должно составлять 0,6 МПа. Допускается снижение нагрузки в пределах 30 % (в целях уменьшения затрат на испытание, компактности и меньшей энергоемкости испытательного оборудования). При этом для получения достоверных результатов необходимо знать фактические усилия с точностью 2-3 %.
30
При испытаниях методом статического нагружения используют рычажный прогибомер и штамп. Для кратковременного нагружения применяют установки УДН, УДН-Н, УДН-HK, ДИНА-3М и другие.
Перед проведением испытаний необходимо произвести внешний осмотр и назначить однообразные участки. Каждый такой участок на всем своем протяжении должен иметь одинаковые грунт земляного полотна, конструкцию дорожной одежды, тип местности по условиям увлажнения и интенсивность движения. Протяженность однообразных участков не может быть менее 0,5 и более 3 км. На каждом участке на расстоянии 1-1,5 м от кромки проезжей части краской в виде круга диаметром 0,1-0,15 м закрепляют точку, на которой ежедневно будут проводить испытания до получения максимальных значений модуля упругости. Испытания начинают в наиболее неблагоприятный период года для работы конструкции дорожной одежды. В районах с зимним периодом - в момент начала снеготаяния при наступлении устойчивой положительной температуры, в южных районах - с наступлением устойчивой влажной погоды. Испытания на контрольных точках проводят с чередованием времени: один день - в первой половине дня; на следующий день - во второй половине со смещением не менее чем на 4 часа.
Испытания на контрольных точках следует назначать при протяженности обследуемого участка более 10 км. На более коротких участках приведение к расчетному модулю упругости осуществляют по табл. 5.2.
Испытания на контрольных точках осуществляют в течение всего периода ослабления дорожной одежды и заканчивают после увеличения прочности в течение 5-7 дней.
Линейные испытания начинают с момента устойчивого снижения прочности дорожных одежд по результатам испытаний на контрольных точках. Их начинают с южного или западного конца обследуемой дороги. Количество испытаний на характерном участке назначается в зависимости от среднего ожидаемого расчетного модуля упругости, состояния дорожной одежды, оцененной в баллах, и технической категории обследуемой дороги.
Количество испытаний может быть назначено в пределах 20 на 1000 м однообразного участка. В каждой точке производится одно испытание. Если на отрезке менее 100 м отмечено резкое снижение прочности (просадки, густая сетка трещин и т.д.), то необходимо произвести не менее 15 уточняющих