
2369
.pdf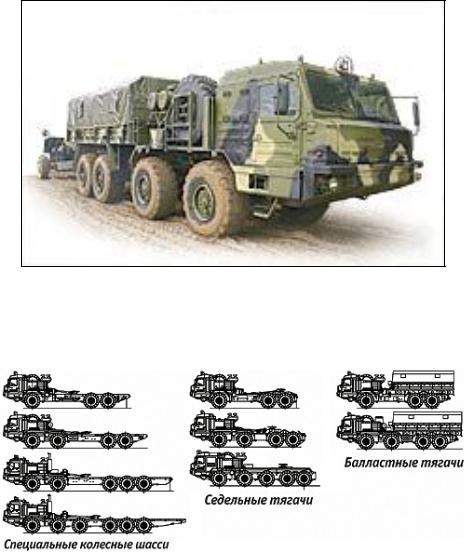
3.5.Автомобили БАЗ
Внастоящее время на Брянском автомобильном заводе серийно выпускаются автомобили семейства «Вощина-1». В это семейство входит пять автомобилей, удовлетворяющих ТТЗ МО (рис. 16). На базе узлов и агрегатов армейских автомобилей были разработаны различные шасси и тягачи для народного хозяйства. Но сегодня уже стало ясно, что для военных потребителей брянских автомобилей требуются машины с более высокими ТТЗ, чем те, которые имеются у армейских модификаций семейства «Вощина-1», поэтому завод в 2005 году начал работу по повышению технических характеристик и расширению модельного ряда шасси и тягачей, поставляемых МО РФ.
Рис. 16. Балластный тягач БАЗ-6306У – представитель семейства «Вощина-1»
Рис. 17. Состав семейства СКШ и КТ ОКР «Вощина-2»
30
Вкачестве базовых для этих работ были взяты шасси и тягачи, используемые в народном хозяйстве. Уже проведены испытания шасси БЗКТ-69096 (10х8) грузоподъемностью 30 т на предмет возможности монтажа на этом шасси комплекса С 300. К этому и другому шасси БЗКТ-6909 грузоподъемностью 22 т уже проявили интерес производители и других видов вооружения. В 2005 году завершились государственные испытания войсковой версии 50-тонного крана КС6973БМ на шасси Брянского автозавода.
Вближайших планах БАЗа – повышение технических характеристик автомобилей в рамках нового семейства автомобилей «Вощина- 2» (рис. 17). Новое семейство будет расширено за счет освоения шасси с колесной формулой 10х10 и 12х12, которые отсутствовали в армейском семействе «Вощина-1». Верхний предел грузоподъемности шасси будет повышен до 40 т. Отдельное внимание при разработке нового семейства будет уделено бортовой информационноуправляющей системе и разработке типоразмерного ряда гидромеханических коробок передач. Эти работы были запланированы для семейства «Вощина-1», но не были выполнены в полном объеме из-за проблем с финансированием.
4.ОБЩАЯ ХАРАКТЕРИСТИКА ГУСЕНИЧНЫХ
ИКОЛЕСНЫХ МАШИН
Гусеничные и колесные машины состоят из десятков механизмов и устройств, которые, в свою очередь, собирают из большого числа деталей. Основными механизмами и устройствами являются: двигатель, трансмиссия, ходовая часть, кузовные конструкции и вспомогательное оборудование (электрооборудование, системы охлаждения, смазки и т. д.). Эксплуатационные качества этих машин определяются подвижностью, поворотливостью и грузоподъемностью. В гусеничных машинах высокую проходимость обеспечивает гусеничный движитель. Колесные машины более быстроходны, а современные конструкции ходовой части и трансмиссии также обеспечивают достаточно высокую проходимость, особенно это относится к машинам специального назначения – тягачам и т. п. [2, 5].
Рост выпуска гусеничной и колесной техники в нашей стране требует освоения новых конструкций в сжатые сроки. Быстрое внедрение современных машин основано на повышении качества технической подготовки производства, включающей конструкторские, тех-
31
нологические и организационные работы. Выполнение технической подготовки производства в минимально короткие сроки, в большей степени, зависит от решения технологических задач, связанных с ними организационных вопросов.
Основным типом машиностроительного производства специальных гусеничных и колесных машин, как уже было сказано, является серийное. Его характерный признак – широкая номенклатура изделий, изготовляемых периодически повторяющимися партиями. Технологические особенности серийного производства изменяются в зависимости от номенклатуры, объема выпуска и трудоемкости изготовления изделий, поэтому различают мелко-, средне- и крупносерийное производство. В мелко- и среднесерийном производстве применяют преимущественно универсальное технологическое оборудование и универсальную оснастку, современные методы получения заготовок и их обработки; в крупносерийном – специальное оборудование и оснастку, агрегатные станки. Организационной формой крупносерийного производства является поточный метод с применением од- но-, многопредметных поточных и автоматических линий.
Современная организация серийного производства связана со стандартизацией, нормализацией и унификацией гусеничных и колесных машин. Это требует внедрения методов массового производства в серийное. Опыт машиностроения показывает, что применение стандартизованных решений сокращает на 30-50 % трудоемкость проектирования машин и подготовки производства и в 3-4 раза сроки освоения новых изделий. Наибольший эффект стандартизации в машиностроении заключается в повышении серийности производства и, в конечном счете, в снижении производственных расходов. С увеличением серийности выпуска машин совершенствуется организация производства, приобретаются приборы, более производительное и совершенное технологическое оборудование, оснастка и инструменты; рабочие места специализируются. Благодаря этому, снижается трудоемкость изготовления и повышается производительность труда.
Одна из характерных особенностей стандартизации при конструировании машин состоит в том, что заданное изделие необходимо разрабатывать, исходя не только из частных технических условий, но и из совокупности признаков, характерных для всего ряда смежных типов и размеров. Детали и узлы конструктивно нормализованного ряда позволяют использовать преемственность повторяющихся конструктивных признаков в машинах. Это обусловливает повышение серийности и применение более эффективных методов производства.
32
Взаимосвязь функциональных, конструктивных и технологических факторов позволяет принимать обобщенные конструктивные и технологические решения, значительно влияющие на сокращение сроков и трудоемкости освоения новых изделий. В процессе изготовления унифицированных деталей и узлов одного и того же конструктивно нормализованного ряда не требуется освоение нового производства при переходе с одной конструкции ряда на другую. Некоторые ограничения в параметры конструируемых деталей, узлов и машин вносит система предпочтительных чисел. Эти ограничения состоят в применении не любых расчетных значений параметров, а лишь тех, которые подчиняются строго определенной закономерности. Конструкция изделия, взятая за базовую конструктивно нормализованного ряда, должна обладать свойством обратимости, т. е. допускать переход с базовой конструкции на конструкцию любого типоразмера и с одной производной на другую при использовании минимального числа новых деталей.
Технологичность конструкции изделия оценивают по четырем основным показателям: трудоемкости изготовления, технологической себестоимости, уровням технологичности конструкции по трудоемкости изготовления и себестоимости, а также по ряду дополнительных показателей, уточняющих результаты оценки по основным показателям. К числу дополнительных показателей технологичности относятся коэффициенты унификации и стандартизации деталей и унификации конструктивных элементов детали. Высокая технологичность конструкции может быть обеспечена только взаимодействием конструкторов и технологов на всех стадиях проектирования.
На этапе разработки эскизного проекта в процессе выбора принципиальной схемы конструкторы совместно с технологами определяют:
формы изделия, возможность использования агрегатов, деталей
иузлов, изготовляемых специализированными производствами;
возможность агрегатирования изделия (расчленения на отдельные унифицированные узлы и агрегаты);
наиболее простые входящие системы; материал и исходные заготовки для главных деталей.
При разработке технического проекта технологичность, главным образом, отрабатывают:
выбором наиболее хорошо обрабатываемых материалов, рациональных заготовок и методов их получения, технологических баз
33
деталей и узлов в соответствии с конструктивными базами и базами сборки;
соблюдением всех требований, предъявляемых к элементам конструкции с точки зрения стандартных норм (соблюдение радиусов, уклонов, фасок, углов, толщин и т. д.);
выполнением требований, предъявляемых к конструкции с точки зрения технологичности при обработке различными методами (правильный выбор баз, удобство обработки, легкость ввода и вывода инструмента, наличие поверхностей для крепления деталей и т. д.);
проведением унификации деталей по исходной заготовке, термообработке, классам точности, шероховатости поверхностей, материалам и т. д.
Опыт отечественной и зарубежной промышленности показал, что
всовременных условиях при необходимости частой смены объектов производства унификация и агрегатирование являются решающими предпосылками не только для сокращения сроков освоения новых изделий, но и для применения наиболее производительных и экономичных методов их изготовления в тех условиях, в которых это ранее исключалось. По мере развития методов конструктивной преемственности стало экономичным выделять ряд узлов и деталей из замкнутого цикла производства и передавать их для изготовления на специализированные заводы.
В последние годы специализация производства способствовала вытеснению традиционного функционального направления в конструировании машин, когда даже детали общего машиностроительного назначения разрабатывали применительно к каждой машине. Сегодня проводится большая работа по унификации деталей общемашиностроительного назначения, а также деталей и узлов смежного производства (топливных насосов, форсунок, пусковых устройств, рукояток, рычагов управления, электрооборудования, катков, резиновых бандажей колес и т. д.). Существует большое число деталей и узлов гусеничных и колесных машин: шаровых пальцев тяг управления, рулевых колес, гидроусилителей, соединительных вилок, коробок передач, редукторов, амортизаторов, которые унифицируют, что позволяет их использовать на машинах различных моделей. Для решения задачи унификации конструкций, например колесных машин, разрабатывают конструктивно-унифицированные ряды двигателей и задних мостов. При этом, зная скоростные характеристики двигателей, передаточные числа передач заднего моста, можно определить конструкции и размерность коробок передач, раздаточных коробок, карданных
34
сочленений, подвесок, колес и шин. Возможность форсирования двигателей в широком диапазоне позволяет на базе цилиндра одной размерности создать автомобильные и тракторные модификации дизелей.
Например, двигатели форсированной и нормальной модификации Ярославского моторного завода устанавливают на автомобили Кременчугского автомобильного завода, а дефорсированной модификации – на тяжелые тракторы Кировского завода. Конструктивноунифицированный ряд деталей и узлов машин Белорусского автомобильного завода позволил всего за два месяца разработать конструкцию и изготовить опытный образец двухосного тягача высокой проходимости.
В результате сравнительного анализа режимов работы основных узлов автомобилей, а также конструктивных разработок было установлено, что ряд деталей и узлов можно использовать в конструкциях тягачей. Например, установлена возможность использования валов, шестерен, муфт и других деталей автомобильных коробок передач в трансмиссиях базовых тягачей. Для тягачей близких типоразмеров в отдельных случаях возможно применение унифицированной коробки передач.
Унификация и агрегатирование предопределяют возможности применения высокопроизводительных методов, резкого повышения производительности труда, снижения себестоимости производства; значительно облегчают работы по типизации технологических процессов и их автоматизированному проектированию. В настоящее время разрабатывают стандарты не только конструкций машин, узлов и деталей (система ЕСКД), но и всей области технологии машиностроения, охватывающей технологические процессы, оснащение и организацию производства (системы ЕСТД и ЕСТПП). Такой комплексный подход опирается на современные достижения науки и техники, экономики и передового опыта. Стандартизация оказывает влияние на разработку типовых процессов в машиностроении, на технологическое оснащение и организацию производства.
Типизация технологических процессов с широкой нормализацией и унификацией деталей и узлов является основой ускорения технологической подготовки производства, создания легко переналаживаемых средств механизации и автоматизации. В основу разработки типовых процессов должна быть положена конструкторскотехнологическая классификация, предусматривающая систематизацию деталей и узлов по основным признакам, как конструкторского,
35
так и технологического подобия. Классификация деталей является первым этапом создания типовой технологии. Для деталей гусеничных и колесных машин ее проводят на основе общесоюзного классификатора промышленной и сельскохозяйственной продукции. Согласно этому классификатору, предусмотрено два класса (40 и 50) деталей: «тела вращения» и «кроме тел вращения». Каждый класс последовательно разделен на 9 подклассов, каждый подкласс – на 9 групп, каждая группа – на 9 подгрупп, каждая подгруппа – на 9 видов. В качестве классификационных признаков для деталей гусеничных и колесных машин выбирают геометрическую форму, конструктивную характеристику отдельных элементов, взаимное расположение элементов, параметрический признак, наименование, выполняемую функцию.
Валы гусеничных и колесных машин относятся к подклассам длинных деталей, характеризующихся цилиндрической формой при длине, значительно превышающей основной диаметр: I > 2D. Сюда входят валы: ступенчатые и гладкие (коробок передач, торсионные и др.), пустотелые, эксцентриковые (балансиры, кривошипы), кулачковые, коленчатые. Смещение центров при обработке шатунных шеек коленчатого вала или обточка кулачков и эксцентриков распределительных валов не изменяет основную схему технологического процесса деталей этого подкласса.
Цилиндрические, конические и червячные зубчатые колеса, чашки дифференциалов, ведущие колеса, опорные и направляющие катки гусеничных машин, ступицы колесных машин, тормозные барабаны, корпуса и фланцы планетарных коробок, кольца включения, фрикционные диски и др. относятся к подклассам коротких деталей. Их характерным признаком является соотношение высоты и основного диаметра: h<=2D. Главными поверхностями обработки деталей этого подкласса являются торцы, цилиндрические наружные и внутренние поверхности, обрабатываемые на различных станках токарной группы. Схемы типовых процессов различаются специфичностью обработки зубьев колес и фасонных поверхностей. Цилиндры гидроамортизаторов и тормозной системы, трубы задних мостов, втулки балансиров и цапф и др. относятся к различным подклассам деталей (длинных или коротких) класса тел вращения. Их общей характеристикой является соотношение между внешним наибольшим диаметром цилиндра и высотой детали.
Рычаги, вилки, шатуны, стойки, кронштейны относятся к подклассам деталей класса «кроме тел вращения», у которых наружная
36
поверхность образована сочетанием элементов различной геометрической формы. Например, к рычагам и вилкам относятся детали, у которых раздвоение плеч происходит за пределами ступенчатой части и основных базовых отверстий. Основным базовым отверстием рычага считается отверстие, расположенное не на плечах и являющееся главным установочным отверстием. В гусеничных и колесных машинах к этим подклассам относятся рычаги рулевого управления, рычаги подвески, вилки переключения передач, вилки карданных валов, рычаги амортизаторов, балки передней оси колесных машин и др. Обрабатываемыми поверхностями таких деталей обычно являются площадки на концах стержня и отверстия на этих площадках.
К подклассу корпусных деталей относятся литые или сварные детали коробчатого типа разнообразной формы, которые представляют собой основу для пространственного координирования в кинематической связи деталей и узлов, монтируемых в них. Характерная особенность корпусов механизмов – наличие одного или нескольких базовых (основных) отверстий, которые являются опорными для монтируемых в корпусе деталей и узлов и определяют их положение относительно друг друга. В гусеничных и колесных машинах – это корпуса коробок передач и редукторов ведущего, промежуточного и заднего мостов и др. Особенностью технологии обработки всякой корпусной детали является обработка плоскостей и основных отверстий, сверление мелких отверстий и нарезание в них резьбы.
Типовые технологические процессы разрабатывают на основе анализа, систематизации и обобщения опыта, технологических решений с учетом достижений технологии машиностроения и передового производственного опыта. В типовых процессах предусматривается применение высокопроизводительного специализированного оборудования, средств механизации и автоматизации; использование прогрессивных методов выполнения и обработки заготовок.
Внедрение типовых технологических процессов позволяет лучше оснастить мелкосерийное производство, создать в средне- и мелкосерийном производстве предметно-замкнутые участки, а в ряде случаев - переменно-поточные автоматические линии. На основании типового технологического процесса, разработанного для деталипредставителя, можно составить конкретный технологический процесс любой детали, входящей в определенный вид. Метод групповой технологии ставит задачи, аналогичные типизации процессов. За основу построения групповых технологических процессов взята сложная комплексная деталь, состоящая из ряда элементарных поверхно-
37
стей. Другие детали, объединенные в группу, должны иметь полное или частичное сочетание таких же поверхностей, что и у комплексной. Различие методов типовой и групповой обработки заключается в том, что типизация технологического процесса предусматривает создание деталепроцессов, а групповой метод – деталеопераций. Типовая технология характеризуется общностью технологического процесса, а групповая – общностью оборудования и оснастки, необходимых для выполнения определенной операции или полного изготовления детали.
Недостатком типовых технологических процессов является слабая загрузка части оборудования в линиях, поэтому в условиях мелко- и среднесерийного производства применяют легкопереналаживаемое оборудование, например, с программным управлением и др. При отсутствии на заводах такого оборудования расширяют технологические возможности имеющихся станков посредством применения приспособлений: многошпиндельных сверлильных головок с регулируемым расположением шпинделей, трехили четырехшпиндельных фрезерных головок и др. На таких станках при небольшой переналадке обрабатывают разные детали, имеющие конструктивные отличия, но входящие в один вид.
Для полной загрузки оборудования в линиях создают групповые операции обработки деталей нескольких видов или даже подклассов. Групповые операции предусматривают наличие станков, общих для нескольких линий обработки деталей разных видов. Станки должны быть установлены таким образом, чтобы обслуживать данные поточные линии. Для наибольшего использования типовых и групповых технологических процессов и обеспечения возможности создания поточных линий с замкнутым циклом применяют комплексный метод подготовки производства, основанный на разработке типовых технологических процессов и групповых операций, общих для нескольких видов деталей, а также на создании легкопереналаживаемых приспособлений и оборудования для типовых и групповых технологических процессов. Типизация позволяет сократить множество неоправданно действующих технологических процессов изготовления деталей, привести их к оптимальному количеству.
Проектирование типовых технологических процессов должно производиться для процессов, построенных по технологической последовательности, на основании типовых представителей; для групповых методов обработки – на основании комплексных деталей. Типизация технологических процессов тесно связана с серийностью,
38
производства, стабильностью конструкции и технологии изготовления деталей различных изделий, с повышением производительности труда. Устойчивость конструктивных и технологических признаков деталей является основой использования преимуществ типизации технологических процессов.
Реализация типовых процессов в конкретных условиях того или иного предприятия встречает трудности, особенно при мелкосерийном и единичном производстве. Одной из трудностей является детализация типовых процессов. Затруднения возникают также при классификации и группировании деталей. Применение электронновычислительных машин (ЭВМ) и их дальнейшее развитие позволяет устранить отмеченные недостатки.
Одним из главных путей увеличения объема и ускорения выпуска гусеничных и колесных машин в условиях серийного производства является комплексная механизация и автоматизация технологических процессов. При этом важной проблемой является «гибкость» производства, связанная с переналадкой технологических процессов, которая включает переналадку технологического оборудования, приспособлений, транспортных средств, схем управления и т. п., в связи с переходом на изготовление машин новых конструкций.
Одним из основных направлений автоматизации и ускорения переналадки оборудования является использование станков с ЧПУ. Создание металлорежущих станков этого типа было вызвано потребностью заводов в технологически гибком автоматизированном оборудовании, позволяющем изготавливать различные изделия. С развитием электронной техники широкое распространение получают новые системы управления по заданной программе с записью на перфолентах или без записи на программоносителе, непосредственно связанные с ЭВМ.
Числовое программное управление сначала использовалось только для автоматизации рабочих и холостых перемещений узлов станка. Однако ЧПУ позволяет автоматизировать и вспомогательные элементы обработки - смену инструмента, выбор режимов. Так появились многооперационные станки с ЧПУ, на которых выполняют различные виды обработки (сверление, растачивание отверстий, фрезерование, нарезание резьбы и т. п.). Основным принципом построения многооперационных станков является выполнение возможно большего числа технологических переходов на одном станке за одну установку заготовки с максимальной автоматизацией и мобильностью переналадки.
39