
3Detali_Mashin_Belan_Kharchenko
.pdfКоэффициент, учитывающий распределения нагрузки между зубьями , в зависимости от окружной скорости и степени точности передачи, определяем по табл. 2.7.
|
|
|
|
|
|
|
|
|
|
|
|
|
|
|
|
|
|
|
|
|
|
|
|
Таблица 2.7 |
|||
|
|
Значение |
|
и |
для косозубых и шевронных передач |
||||||||||||||||||||||
|
|
|
|
|
|
|
|
|
|
|
|
|
|
|
|
|
|
|
|
|
|
|
|
|
|
||
|
|
|
|
|
|
|
|
|
|
|
|
|
|
|
|
|
|
|
|
|
|
|
|
|
|
|
|
|
|
|
|
|
|
|
|
|
|
|
|
|
|
|
|
|
|
|
|
|
|
|
|
|
|
|
|
Степень |
|
|
|
|
|
|
|
|
|
|
|
|
|
|
|
|
|
|
|
|
|
|
|
|
|
|
|
|
|
|
|
|
|
|
|
|
|
|
|
Окружная скорость V, м/с. |
|
||||||||||||||
|
|
|
|
|
|
|
|
|
|
|
|
|
|
||||||||||||||
точности |
|
|
|
|
|
|
|
|
|
|
|
|
|
|
|
|
|
|
|
|
|
|
|
|
|
|
|
|
|
|
|
|
|
|
до1 |
|
|
|
5 |
|
|
|
|
10 |
|
|
15 |
|
|
20 |
|||||
|
|
|
|
|
|
|
|
|
|
|
|
|
|
|
|
|
|
|
|
||||||||
6 |
|
|
|
0,72 |
|
|
|
1 |
|
|
|
|
|
1,02 |
|
|
|
1,03 |
|
1,04 |
|
|
1,05 |
||||
7 |
|
|
|
0,81 |
|
|
|
1,02 |
|
|
|
1,05 |
|
|
|
1,07 |
|
1,10 |
|
|
1,12 |
||||||
8 |
|
|
|
0,91 |
|
|
|
1,06 |
|
|
|
1,09 |
|
|
|
1,13 |
|
- |
|
|
- |
||||||
9 |
|
|
|
1,0 |
|
|
|
1,1 |
|
|
|
|
1,16 |
|
|
|
- |
|
|
- |
|
|
- |
||||
|
|
Примечание: для прямозубых колес |
= 1, = 1 |
|
|||||||||||||||||||||||
|
|
|
|
|
|
|
|
|
|
|
|
|
|
|
|
|
|
|
|
|
|
|
|
|
|||
|
Принимаем |
= 1,1. |
|
|
|
|
|
|
|
|
|
|
|
|
|
|
|
|
|
||||||||
|
|
|
|
|
|
|
|
|
|
|
|
|
|
|
|
|
|
|
|
|
|
|
|
|
|
|
|
|
Коэффициент, учитывающий неравномерность распределения на- |
||||||||||||||||||||||||||
грузки по длине контактных линий |
, определяем по табл. 2.8. |
|
|||||||||||||||||||||||||
|
|
|
|
|
|
|
|
|
|
|
|
|
|
|
|
|
|
|
|
|
|
|
|
|
|
|
|
|
Принимаем |
= 1,08; при |
|
= |
1 |
= |
55 |
|
= 0,95. |
|
|
|
|||||||||||||||
|
|
|
|
|
|
|
|
||||||||||||||||||||
|
|
|
|
|
|
|
|
|
|
|
|
|
|
|
|
1 |
57,9 |
|
|
|
|
|
|||||
|
|
|
|
|
|
|
|
|
|
|
|
|
|
|
|
|
|
|
|
|
|
|
|||||
|
Коэффициент, учитывающий внутреннюю динамическую нагрузку |
||||||||||||||||||||||||||
определяем по табл. 2.9. |
|
|
|
|
|
|
|
|
|
|
|
|
|
|
|
|
|
|
|||||||||
|
|
|
|
|
|
|
|
|
|
|
|
|
|
|
|
|
|
|
|
|
|
|
|
|
|
|
|
|
Принимаем |
= 1,0 . |
|
|
|
|
|
|
|
|
|
|
|
|
|
|
|
|
|
||||||||
|
|
|
|
|
|
|
|
|
|
|
|
|
|
|
|
|
|
|
|
|
|
|
|
|
|
|
|
|
Определяем расчетное контактное напряжение: |
|
|||||||||||||||||||||||||
|
|
|
|
|
|
|
|
|
|
|
|
|
|
|
|
|
|
|
|||||||||
|
|
|
|
|
|
∙ |
∙ |
∙ ∙ + 1 |
|
|
|
|
|
|
|
|
|||||||||||
|
= 376 ∙ |
|
|
|
|
|
|
|
|
|
|
|
|
|
|
= |
|
|
|
|
|
|
|
||||
|
|
|
|
|
|
|
|
|
|
|
|
|
|
|
|
|
|
|
|
|
|
||||||
|
|
|
|
|
|
|
|
|
2 ∙ 2 |
|
|
|
|
|
|
|
|
|
|
|
|
|
|
||||
|
|
|
|
|
|
|
|
|
|
|
|
|
|
|
|
|
|
|
|
|
|
|
|||||
|
|
|
|
|
|
= 376 ∙ |
|
1,1 ∙ 1,08 ∙ 1,0 ∙ 9831,4 ∙ 4,5 + 1 |
|
(2.29) |
|||||||||||||||||
|
|
|
|
|
|
|
|
||||||||||||||||||||
|
|
|
|
|
|
|
|
|
|
|
|
|
262,1 ∙ 50 |
|
|
|
|
|
|||||||||
|
|
|
|
|
|
|
|
|
|
|
|
|
|
|
|
|
|
|
|
|
|
||||||
|
|
|
|
|
|
= 823,5 МПа. |
|
|
|
|
|
|
|
|
|
|
|
|
|
||||||||
|
Т.к. < 0,85 … 1,05 |
|
∙ |
|
|
= |
0,85 … 1,05 |
|
∙ 789,3 = |
|
|||||||||||||||||
|
|
|
|
|
|
|
|
|
|
|
|
|
|
|
|
|
|
|
|
|
|
|
|
|
|
670,9 … 828,8 МПа, то условие прочности по контактным напряжениям выполнено. При несоблюдении этого условия изменяют 2 или 2 (и, следовательно ).
Выбираем коэффициенты, необходимые для проверки колес по изгибающим напряжениям.
20

|
|
|
Коэффициент, учитывающий распределение нагрузки между зубь- |
||||||||||||||
ями (табл. 2.7): |
= 1,0. |
|
|
|
|
|
|
|
|||||||||
|
|
|
|
|
|
|
|
|
|
|
|
|
|
|
|
|
|
|
|
|
Коэффициент, учитывающий внутреннюю динамическую нагрузку |
||||||||||||||
(табл. 2.9): |
|
= 1,1. |
|
|
|
|
|
|
|
||||||||
|
|
|
|
|
|
|
|
|
|
|
|
|
|
|
|
|
|
|
|
|
|
|
|
|
|
|
|
|
|
|
|
|
|
Таблица 2.8 |
|
|
|
|
|
|
|
|
|
|
|
Значения коэффициента KHB |
|
|
|
||||
|
|
|
|
|
|
|
|
|
|
|
|
|
|
|
|
|
|
|
|
|
|
|
|
|
|
|
|
|
Твердость поверхности зубьев |
|
|
||||
|
|
= |
|
|
|
|
|
HB≤350 |
|
|
HB>350 |
||||||
|
|
|
|
|
|||||||||||||
|
|
1 |
|
|
|
|
|
|
|
|
|
|
|
|
|||
|
|
|
|
|
I |
|
II |
|
III |
I |
|
II |
|
III |
|||
|
|
|
|
|
|
|
|
|
|
|
|
||||||
|
0,4 |
|
|
|
|
1,15 |
|
1,04 |
|
1,0 |
1,33 |
|
1,08 |
|
1,02 |
||
|
0,6 |
|
|
|
|
1,24 |
|
1,06 |
|
1,02 |
1,50 |
|
1,14 |
|
1,04 |
||
|
0,8 |
|
|
|
|
1,30 |
|
1,08 |
|
1,03 |
- |
|
1,21 |
|
1,06 |
||
|
1,0 |
|
|
|
|
|
- |
|
1,11 |
|
1,04 |
- |
|
1,29 |
|
1,09 |
|
|
1,2 |
|
|
|
|
|
- |
|
1,15 |
|
1,05 |
- |
|
1,36 |
|
1,12 |
|
|
1,4 |
|
|
|
|
|
- |
|
1,18 |
|
1,07 |
- |
|
- |
|
1,16 |
|
|
1,6 |
|
|
|
|
|
- |
|
1,22 |
|
1,09 |
- |
|
- |
|
1,21 |
|
|
1,8 |
|
|
|
|
|
- |
|
1,25 |
|
1,11 |
- |
|
- |
|
- |
|
|
2,0 |
|
|
|
|
|
- |
|
1,30 |
|
1,14 |
- |
|
- |
|
- |
Данные приведенные в столбце I, относятся к передачам с консольным расположением зубчатого колеса, II- к передачам с несимметричным расположением колес по отношению к опорам, III-к передачам с симметричным расположением.
Таблица 2.9
Значения коэффициентов KHV и KFV
|
|
|
|
|
|
KHV |
|
||
|
Твердость |
|
Окружная скорость, V, м/с |
||||||
Передача |
поверхности |
KFV |
до 5 |
|
10 |
|
15 |
|
20 |
|
зубьев, HB |
|
|
|
Степень точности |
|
|||
|
|
|
|
8 |
|
7 |
|
||
Прямозубая |
≤350 |
1,4 |
1,05 |
|
- |
|
- |
|
- |
|
>350 |
1,2 |
1,1 |
|
- |
|
- |
|
- |
Косозубая и |
≤350 |
1,2 |
1,0 |
|
1,01 |
|
1,02 |
|
1,05 |
шевронная |
>350 |
1,1 |
1,0 |
|
1,05 |
|
1,07 |
|
1,10 |
21
Определяем коэффициент, учитывающий неравномерность распределения нагрузки по длине контактных линий:
|
1,5 ∙ |
1,5 ∙ 0,95 |
|
|
= 1 + |
|
= 1 + |
|
= 1,18, |
|
|
|||
|
|
8 |
|
|
|
|
здесь S = 8 - индекс схемы (тот же, что и в формуле 2.14). Определяем коэффициент, учитывающий наклон зуба:
|
0 |
10,1420 |
|
|
= 1 − |
|
= 1 − |
|
= 0,9276. |
|
|
|||
|
140 |
|
140 |
|
|
|
|
Определяем приведѐнное число зубьев колеса:
|
= |
2 |
= |
86 |
= |
86 |
= 90,2. |
|
|
|
|||||
2 |
|
3 |
310,1420 |
0,954 |
|
||
|
|
|
(2.30)
(2.31)
(2.32)
По |
табл. |
2.10, |
в |
зависимости |
|
|
от |
|
= 90,2, |
принимаем ко- |
||||||||||||
|
|
|
|
|
|
|
|
|
|
|
|
|
|
|
|
|
2 |
|
|
|
|
|
эффициент |
|
= 3,605 учитывающий форму зуба и концентрацию на- |
||||||||||||||||||||
|
|
|
2 |
|
|
|
|
|
|
|
|
|
|
|
|
|
|
|
|
|
|
|
пряжений. |
|
|
|
|
|
|
|
|
|
|
|
|
|
|
|
|
|
|
|
|
|
|
Для шестерни: |
|
|
|
|
|
|
|
|
|
|
|
|
|
|
|
|||||||
|
|
|
= |
|
|
1 |
= |
|
19 |
|
= |
|
|
19 |
|
= 19,9. |
|
|
|
(2.33) |
||
|
|
|
|
|
|
|
|
|
|
|
|
|
|
|||||||||
|
1 |
|
3 |
|
310,1420 |
0,954 |
|
|
|
|
|
|
||||||||||
|
|
|
|
|
|
|
|
|
|
|
||||||||||||
|
|
|
|
|
|
|
|
|
|
|
|
|
|
|
|
|
|
|
|
Таблица 2.10 |
||
|
|
|
Значения коэффициента |
|
|
для внешнего зацепления |
|
|||||||||||||||
|
|
|
|
|
|
|
|
|
|
|
|
|
|
|
|
|
|
|
|
|
||
|
|
|
|
|
|
|
|
|
|
без смещения |
|
|
|
|
|
|
|
|||||
|
|
|
|
|
|
|
|
|
|
|
|
|
|
|
|
|
|
|
|
|
|
|
или |
|
17 |
|
|
20 |
|
22 |
|
|
24 |
|
|
26 |
|
28 |
|
30 |
|||||
|
|
|
|
|
|
|
|
|
|
|
||||||||||||
|
|
|
|
|
|
|
|
|
|
|
|
|
|
|
|
|
|
|
|
|
|
|
|
|
|
|
|
|
|
|
|
|
|
|
|
|
|
|
|
|
|
|
|
|
|
|
|
4,3 |
|
|
4,08 |
|
3,98 |
3,92 |
|
|
3,88 |
|
3,84 |
|
3,8 |
|||||||
|
|
|
|
|
|
|
|
|
|
|
|
|
|
|
|
|
|
|
|
|
|
|
или |
|
35 |
|
|
40 |
|
45 |
|
|
50 |
|
|
65 |
|
80 |
|
≥100 |
|||||
|
|
|
|
|
|
|
|
|
|
|
||||||||||||
|
|
|
|
|
|
|
|
|
|
|
|
|
|
|
|
|
|
|
|
|
|
|
|
|
|
|
|
|
|
|
|
|
|
|
|
|
|
|
|
|
|
|
|
|
|
|
|
3,75 |
|
|
3,7 |
|
3,66 |
3,65 |
|
|
3,62 |
|
3,61 |
|
3,6 |
|||||||
|
|
|
|
|
|
|
|
|
|
|
|
|
|
|
|
|
|
|
|
|
|
|
По табл. 2.10 принимаем |
= 4,1. |
|
|
|
|
|
|
|
||||||||||||||
|
|
|
|
|
|
|
|
|
|
1 |
|
|
|
|
|
|
|
|
|
|
|
|
Определяем расчѐтное изгибающее напряжение в зубьях колеса:
22
|
|
|
∙ |
∙ |
|
∙ ∙ |
∙ |
|
||
|
= |
|
|
|
|
2 |
|
= |
|
|
|
|
|
|
|
|
|
|
|||
2 |
|
|
|
2 |
∙ |
|
|
|
|
|
|
|
|
|
|
|
|
|
|||
|
|
|
|
= |
1 ∙ 1,18 ∙ 1,1 ∙ 0,93 ∙ 3,605 ∙ 9831,4 |
(2.34) |
||||
|
|
|
|
|
|
|
50 ∙ 3 |
|
||
|
|
|
|
= |
285,2 МПа. |
|
||||
|
|
|
|
|
|
|
Расчетное изгибающее напряжение в зубьях шестерни:
|
|
|
|
|
4,08 |
|
|
|
|
= |
∙ |
1 |
= 285,2 ∙ |
|
= 322,8 МПа. |
(2.35) |
|
|
3,605 |
|||||||
1 |
2 |
|
|
|
|
|||
|
|
|
2 |
|
|
|
|
Т.к. соблюдаются требования:
2 < 1,1 ∙ 2 = 1,1 ∙ 310 = 341 МПа;
1 =< 1,1 ∙ 1 = 341 МПа, то условие прочности по изгибающим напряжениям выполнено.
3 ПРЕДВАРИТЕЛЬНЫЙ РАСЧЕТ ВАЛОВ И ВЫБОР ПОДШИПНИКОВ
В результате предварительного расчѐта определяют наименьший диаметр вала (см. Рис. 4.1 и Рис. 4.2), который является диаметром выходного конца вала. За расчѐтный диаметр вала принимают ближайшее большее значение из стандартного ряда чисел (см. табл. 2.5). Из этой же таблицы выбирают все другие расчѐтные размеры, если на эти параметры отсутствует соответствующие стандарты.
3.1Определение диаметров валов
Основными материалами для валов и осей служат углеродистые и легированные стали. Для осей и валов, диаметры которых определяются, в основном, жѐсткостью, применяют углеродистые конструкционные стали Ст4, Ст5 без термообработки. В ответственных и тяжело нагруженных конструкциях, когда основным критерием является прочность, используют термически обрабатываемые среднеуглеродистые и легированные стали 40, 45, 40Х, 40ХН и др.
Предварительный расчѐт валов производится только на кручение.
Для компенсации изгибающих напряжений и других неучтѐнных факторов, принимают значительно пониженные значения допускаемых напряжений кручения, например [τ] = (15...30) МПа. Меньшие значения
23

допускаемых напряжений кручения принимают для быстроходных валов, большие значения - для тихоходных валов.
Определяем диаметр ведущего вала:
|
3 |
|
|
∙ 103 |
|
3 |
285,17 ∙ 103 |
|
|
1 ≥ |
1 |
|
= |
|
|
= 41,94 мм. |
|
|
0,2 ∙ |
|
0,2 ∙ 20 |
|||||
|
|
|
|
|
|
|||
|
Принимаем по таблице 2.5 стандартное значение диаметра вала: |
|||||||
|
= 45 мм. |
|
|
|
|
|
|
|
1 |
|
|
|
|
|
|
|
|
|
Определяем диаметр ведомого вала: |
|
||||||
|
|
|
|
|
|
|
|
|
|
3 |
|
|
∙ 103 |
|
3 |
1288,4 ∙ 103 |
|
|
2 ≥ |
2 |
|
= |
|
|
= 59,88 мм. |
|
|
0,2 ∙ |
|
0,2 ∙ 30 |
|||||
|
|
|
|
|
|
Принимаем по таблице 2.5 стандартное значение диаметра вала:
2 = 60 мм.
3.2Выбор подшипников
Подшипники являются опорами валов и вращающихся осей. Они воспринимают нагрузки, приложенные к валу или к оси.
Поскольку промышленностью выпускаются подшипники с посадочными диаметрами кратными 5 мм, то полученное значение посадочного диаметра под подшипник dп„ принимают кратным 5 мм (ближайшее значение).
Посадочные диаметры под подшипники ведущего и ведомого ва-
лов:
П1 ≥ 1 + 5 = 45 + 5 = 50 мм.П2 = 2 + 5 = 60 + 5 = 65 мм.
Посадочный диаметр под зубчатое колесо:
≥ П2 + 5 = 65 + 5 = 70 мм.
По посадочным диаметрам П1и П2 выбираем радиальные шариковые подшипники (рис. 3.1) из табл. 3.1.
.
.
.
.
24
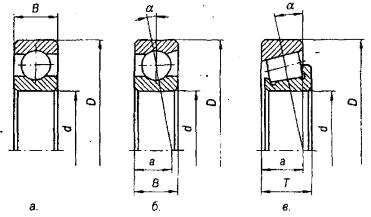
Рис. 3.1. Подшипники качения однорядные а – шариковый радиальный; б – шариковый радиально-упорный;
в – роликовый радиально-упорный.
Таблица 3.1
Подшипники шариковые радиальные однорядные Средняя серия ГОСТ 8338-75
Условное |
|
Размеры, мм |
|
Грузоподъемность, кН |
|||
|
|
|
|
Динамическая, |
Статическая, |
||
обозначение |
d |
D |
B |
r |
|||
С |
С0 |
||||||
|
|
|
|
|
|||
300 |
10 |
35 |
11 |
1 |
8,06 |
3,75 |
|
301 |
12 |
37 |
12 |
1,5 |
9,75 |
4,65 |
|
302 |
15 |
42 |
13 |
1,5 |
11,4 |
5,4 |
|
303 |
17 |
47 |
14 |
1,5 |
13,5 |
6,65 |
|
304 |
20 |
52 |
15 |
2,0 |
15,9 |
7,8 |
|
305 |
25 |
62 |
17 |
2,0 |
22,5 |
11,4 |
|
306 |
30 |
72 |
19 |
2,0 |
28,1 |
14,6 |
|
307 |
35 |
80 |
21 |
2,5 |
33,2 |
18,0 |
|
308 |
40 |
90 |
23 |
2,5 |
41,0 |
22,4 |
|
309 |
45 |
100 |
25 |
2,5 |
52,7 |
30,0 |
|
310 |
50 |
110 |
27 |
3,0 |
65,8 |
36,0 |
|
311 |
55 |
120 |
29 |
3,0 |
71,5 |
41,5 |
|
312 |
60 |
130 |
31 |
3,5 |
81,9 |
48,0 |
|
313 |
65 |
140 |
33 |
3,5 |
92,3 |
56,0 |
|
|
|
|
|
25 |
|
|

Продолжение табл. 3.1
314 |
70 |
150 |
35 |
3,5 |
104,0 |
63,0 |
315 |
75 |
160 |
37 |
3,5 |
112,0 |
72,5 |
316 |
80 |
170 |
39 |
3,5 |
124,0 |
80,0 |
316К5 |
80 |
170 |
39 |
3,5 |
130,0 |
89,0 |
317 |
85 |
180 |
41 |
4,0 |
133,0 |
90,0 |
318 |
90 |
190 |
43 |
4,0 |
143,0 |
99,0 |
319 |
95 |
200 |
45 |
4,0 |
153,0 |
110,0 |
319К5 |
95 |
200 |
45 |
4,0 |
161,0 |
120,0 |
320 |
100 |
215 |
47 |
4,0 |
174,0 |
132,0 |
|
|
|
|
|
|
Таблица 3.2 |
|
|
Основные параметры выбранных подшипников |
||||||
|
|
|
|
|
|
|
|
|
Условное |
Размеры, мм |
Грузоподъемность, кН |
||||
Вал |
обозначение |
d |
D |
B |
Динамическая, |
Статическая, |
|
|
подшипника |
С |
С0 |
||||
|
|
|
|
||||
Ведущий |
310 |
50 |
110 |
27 |
65,8 |
36,0 |
|
(1) |
|||||||
|
|
|
|
|
|
||
Ведомый |
313 |
65 |
140 |
33 |
92,3 |
56,0 |
|
(2) |
|||||||
|
|
|
|
|
|
4КОНСТРУКТИВНЫЕ РАЗМЕРЫ ВАЛА - ШЕСТЕРНИ, ВЕДОМОГО ВАЛА И ЗУБЧАТОГО КОЛЕСА
Как правило, шестерню и ведущий вал выполняют как одно целое (см. Рис. 4.1), т.е. в виде вала-шестерни.
Рис. 4.1. Конструкция ведущего вала
26

Ранее даны рекомендации по определению: диаметров вершин шестерни da1 (см. Рис. 4.1) и колеса da2 (см. Рис. 4.2); ширины шестерни b1 и ширины колеса b2; диаметров выходных концов ведущего dH1 и ведомого dH2 валов; посадочных диаметров под подшипники на ведущем dп1 и ведомом dп2 валах; посадочного диаметра под колесо dK2, на ведомом валу.
Рис. 4.2. Конструкция ведомого вала и зубчатого колеса
Подобраны подшипники (таблица 3.2) для ведущего и ведомого валов, а следовательно известны ширины этих подшипников B1 и В2, (у радиально-упорных подшипников монтажная высота Т).
Высоту tцил (tкон) заплечика при цилиндрической форме конца вала (Рис. 4.3), координату г фаски подшипника и размер f (мм) фаски колеса на промежуточном валу принимают по таблице 4.1 в зависимости от диаметра выходного конца вала dв (мм). Цилиндрическая поверхность выходного конца вала является посадочной поверхностью под полумуфту (шкив или звѐздочку).
Для ведущего вала (для dв1 = 45 мм): t = 2,8 мм, г = 2,8 мм, f = 1,6 мм.
27

Определяем диаметр буртика под подшипник:
Б1 |
= П1 |
+ 2 ∙ = 50 + 2 ∙ 2,8 = 55,6 мм. |
. |
|
|
|
Принимаем Б1 = 55 мм.
Рис. 4.3. Концы валов цилиндрические
Таблица 4.1
Рекомендуемые размеры заплечиков и размеры фасок, мм
d |
17-22 |
24-30 |
32-38 |
40-44 |
45-50 |
|
Длина, l |
50 |
60 |
80 |
110 |
110 |
|
исп.1 |
||||||
|
|
|
|
|
||
Длина, l |
36 |
42 |
58 |
82 |
82 |
|
исп.2 |
||||||
|
|
|
|
|
||
tцил |
3,0 |
3,5 |
3,5 |
3,5 |
4,0 |
|
tкон |
1,5 |
1,8 |
2,0 |
2,3 |
2,3 |
|
r |
1,5 |
2,0 |
2,5 |
2,5 |
3,0 |
|
f |
1,0 |
1,0 |
1,2 |
1,2 |
1,6 |
|
D |
52-58 |
60-65 |
67-75 |
80-85 |
90-95 |
|
Длина, l |
110 |
140 |
140 |
170 |
170 |
|
исп.1 |
||||||
|
|
|
|
|
||
Длина, l |
82 |
105 |
105 |
130 |
130 |
|
исп.2 |
||||||
|
|
|
|
|
||
tцил |
4,5 |
4,6 |
5,1 |
5,6 |
5,6 |
|
tкон |
2,5 |
2,7 |
2,7 |
2,7 |
2,9 |
|
r |
3,0 |
3,5 |
3,5 |
4,0 |
4,0 |
|
f |
2,0 |
2,0 |
2,5 |
2,5 |
3,0 |
28

Для ведомого вала (для 2 = 60 мм): t = 3мм, r = 3мм, f = 2мм.
Определяем посадочный диаметр под колесо:
|
= |
П2 |
+ 2 ∙ = 65 + 2 ∙ 3 = 71 мм. |
(4.2) |
2 |
|
|
|
Принимаем dK2 = 70 мм.
Определяем диаметр буртика под подшипник:
Б2 = К2 + 3 ∙ = 70 + 3 ∙ 2 = 76 мм. |
(4.3) |
Принимаем Б2 = 75 мм.
Чтобы поверхности вращающихся деталей редуктора не задевали за внутренние поверхности стенок его корпуса, между ними оставляют зазор «а», мм (Рис. 6.1), который определяют по формуле:
≈ 3 |
|
|
|
+ 3, |
(4.4) |
||
|
|
|
где LP - расстояние между внешними поверхностями деталей передач определяем по формуле:
|
|
|
|
|
1 |
+ |
63,9 |
|
268,1 |
|
|
|
|
= |
|
+ |
|
2 |
= 160 + |
|
+ |
|
= 326 мм. |
(4.5) |
|
|
|
|
|
|
|
|||||||
|
|
|
|
|
2 |
|
2 |
|
2 |
|
|
|
|
|
|
|
|
|
|
|
|
|
Тогда: = 3 + 3 = 9,88 мм. Принимаем = 10 мм; и 1 = a = 10.
Расстояние между торцами подшипников валашестерни:
= в1 + 2 ∙ 1 = 55 + 2 ∙ 10 = 75 мм. |
(4.6) |
Длина ступени валашестерни под уплотнение крышки с отверстием и подшипник:
1 = B2 + 2 + = 33 + 22 + 8 = 63 мм, |
(4.7) |
где B2- ширина подшипника ведомого вала (табл. 3.2); h2 - высота крышки с уплотнением подшипника ведомого вала; l - длина участка вала, выступающая за внешнюю плоскость крышки подшипника (Рис. 6.1);
29