
Технология синтеза мономеров / Основы и технологии мономеров Платэ
.pdf81
ЧАСТЬ ВТОРАЯ
МОНОМЕРЫ ДЛЯ ПОЛИМЕРОВ, ПОЛУЧАЕМЫХ
ПО РЕАКЦИЯМ ПОЛИМЕРИЗАЦИИ
Глава 3
ОЛЕФИНОВЫЕ МОНОМЕРЫ
Олефиновые мономеры применяются для получения полиолефинов, которые занимают доминирующее положение в структуре потребления пластических масс.
Первое место по объему производства среди полиолефинов принадлежит полиэтилену низкой плотности, используемому для изготовления упаковочных материалов, тары, труб, конструкционных деталей. Полиэтилен высокой и средней плотности занимает второе место , из него изготовливают трубы, в том числе крупногабаритные, разного рода емкости, пленки, волокна, электроизоляционные материалы в радиотехнике и т.д. Третье место по объему производства принадлежит полипропилену. Его применяют для изготовления литьевых конструкционных деталей, используемых в основном в автомобилестроении, в производстве бытовых приборов, упаковки, а также для выработки волокон и канатов.
Кроме рассмотренных традиционных полиолефинов применяются также гомо- и сополимеры высших (начиная с С4) олефинов различных типов. Такие полимеры как полиизобутилен, полибутен, поли-4-метилпентен-1 имеют важное промышленное значение, хотя рост производства этих полимеров сдерживается высокой стоимостью мономеров (по сравнению с низшими олефинами).
Изобутилен – широкораспространенный синтетический каучук сам по себе, а сополимер изобутилена с бутадиеном применяется в резиновой и шинной промышленности под названием "бутилкаучук".
Полибутен относится к группе линейных частично кристаллических полиолефинов. Он характеризуется отличным сочетанием прочности, гибкости и стойкости к растрескиванию под напряжением, что позволяет ему иногда конкурировать с такими ведущими полимерами как полиэтилен и полипропилен.
Изотактический полибутен был впервые получен в 1959 г. Дж. Натта. Гомополимер бутена-1, синтезируемый в присутствии каталитических систем
82
Циглера-Натта, имеет т. пл. 399 К. Сополимеризацией бутена-1 с пропиленом, пентеном-1, 4-метилпентеном получают сополимеры с температурой плавления от 373 до 513 К в зависимости от видов и содержания звеньев сополимера.
Поли-4-метилпентен-1 в некоторых отношениях является уникальным полимером. Применение стереоспецифических металлорганических катализаторов позволило получить поли-4-метилпентен-1 с т. пл. 513 К. Он обладает самой низкой из полимеров высших олефинов плотностью (83 кг/м3) и, несмотря на высокую степень кристалличности (до 65%), имеет высокую прозрачность в противоположность полиэтилену и полипропилену (коэффициент светопропускания до 90%). Высокие механические показатели поли-4- метилпентена-1 сохраняются при высоких температурах. Например, при 373 К его механические свойства близки к свойствам полиэтилена низкой плотности при 293 К. По сопротивлению к ударным нагрузкам он превосходит такие прозрачные аморфные пластики, как полистирол и полиметилметакрилат.
Высшие полиолефины используют в различных областях. Так, полибутен применяют в производстве труб, пленок, тары (мешки для упаковки удобрений, реактивов, взрывчатых веществ), деталей электронных приборов, покрытия кабелей, как один из компонентов асфальтовых покрытий и т.д. Поли-4- метилпентен-1 как один из лучших материалов для точного литья используется в электротехнике, электронике (изоляционный материал, корпуса электронных реле и др.), автомобилестроении (светильники), пищевой промышленности (посуда, подносы), медицине (шприцы, ампулы, стерилизуемая посуда), оптике (линзы и другие оптические детали). Модули на основе половолоконных мембран из этого полимера – отличный мембранный разделитель кислорода и азота при комнатной температуре.
Сополимеризацией олефинов между собой, а также с диенами или с гетеросодержащими мономерами можно получать полиолефины с заданными свойствами. Так, сополимеризацией этилена с небольшими количествами пропилена или бутилена можно повысить стойкость к растрескиванию, эластичность и улучшить реологические свойства полиэтилена, сохранив при этом практически весь комплекс остальных свойств. Сополимер этилена и пропилена с добавкой диена представляет собой относительно недорогой каучук, также широко используемый в различных областях. В промышленном масштабе производятся сополимеры этилена с гексеном, с алкилакрилатами и с винилацетатом, сополимеры пропилена с винилхлоридом и многие другие.
3.1.НИЗШИЕ ОЛЕФИНЫ
Книзшим олефинам относятся этилен, пропилен и бутены, изобутилен. При нормальных условиях все они являются газами. Показатели основных физических свойств олефинов представлены в табл. 3.1.
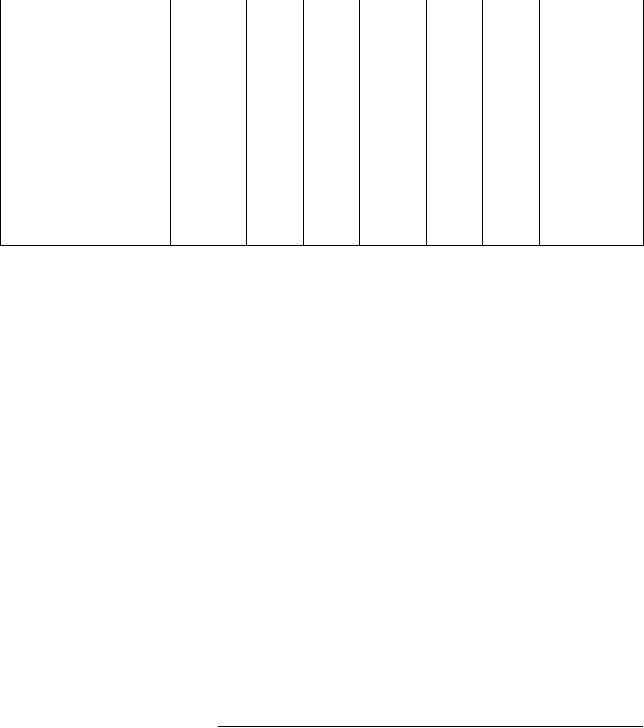
83
Таблица 3.1.
Физические свойства низших олефинов
Олефин |
Молеку- |
Т.пл, |
Т.кип, |
3 |
Т.кр, |
Ркр, |
q, кДж/кг |
лярная |
К |
К |
d, г/cм |
К |
МПа |
||
|
масса |
|
|
|
|
|
|
Этилен (C2H4) |
28,05 |
103,8 |
169,3 |
1,251 |
282,9 |
5,15 |
47260 |
Пропилен (C2H6) |
42,08 |
87,7 |
225,3 |
1,877 |
364,9 |
4,68 |
45880 |
Бутен-1 (C4H8) |
56,10 |
87,6 |
266,7 |
2,503 |
419,2 |
4,10 |
45380 |
цис-Бутен-2 |
56,10 |
134,1 |
276,7 |
2,503 |
430,0 |
4,22 |
45380 |
|
|
|
|
|
|
|
|
транс-Бутен-2 |
56,10 |
167,4 |
273,9 |
2,503 |
428,0 |
4,22 |
45380 |
|
|
|
|
|
|
|
|
Изобутилен |
56,10 |
132,6 |
266,0 |
2,503 |
417,7 |
4,04 |
45380 |
П р и м е ч а н и е : Т.кр – критическая температура, Ркр – критическое давление, q - теплотворная способность.
Этилен был получен впервые И.Дейманом в 1795 г. путем отщепления воды от этанола концентрированной серной кислотой. Это бесцветный газ с т.
кип. 169,3 К.
Пропилен был получен Рейнольдсом спустя 50 лет после открытия этилена. Это также бесцветный горючий газ с едва ощутимым запахом. На организм оказывает наркотическое действие.
Все изомеры бутилена газообразны, но легко сжижаются.
3.1.1.Сырье для производства низших олефинов
Внастоящее время в структуре производства этилена 64% приходится на крупнотоннажные установки пиролиза, ~ 17% - на малотоннажные установки газового пиролиза,~ 11% составляет пиролиз бензина и 8% падает на пиролиз этана.
Важным источником сырья для получения олефинов являются углеводородные газы НПЗ. В табл. 3.2 приведены выход и состав газов в различных процессах переработки нефти.
Таблица 3.2
Выход и состав газов нефтепереработки
Процессы |
Выход, |
|
Содержание, % (мас.) |
|
|
||
%(на |
|
|
|
||||
|
|
|
|
|
|
||
|
сырье) |
CH4 |
C2 |
C3 |
C4 |
C5 |
H2 |
Автотермическая |
1,7-4,0 |
- |
3,3-11,7 |
25-51,7 |
24-48 |
8,1-20,8 |
- |
|
|
|
|
|
|
|
|
84
газификация |
|
|
|
|
|
|
|
|
|
|
|
|
|
|
|
Термический |
4,0-8,0 |
0,8-19,5 |
31,3-41,1 |
21,3-26,1 |
8,2-11,1 |
0,8-2,5 |
- |
крекинг |
|
|
|
|
|
|
|
Каталитический |
10,0-16,0 |
0,4-6,4 |
5,8-9,2 |
18,4-25,6 |
42,7-49,8 |
11,9-21,4 |
- |
крекинг |
|
|
|
|
|
|
|
Каталитический |
8,0-12,0 |
12,3-17,4 |
30-36 |
29,5-31 |
5,3-14 |
0,3-3,5 |
4-21,0 |
риформинг |
|
|
|
|
|
|
|
Вторичная |
1,9-2,8 |
- |
1,1-3,2 |
27,4-34,6 |
43,2-47,4 |
4,8-19,1 |
- |
перегонка |
|
|
|
|
|
|
|
Коксование |
8,0-10,0 |
35 |
22 |
14,5 |
15 |
- |
- |
Гидроочистка |
2,0-7,0 |
30,4 |
28,5 |
17,5 |
10,4 |
4,6 |
13,5 |
|
|
|
|
|
|
|
|
Наибольшее количество углеводородов С2, являющихся источником получения этилена, содержится в газах термического крекинга – до 41,1% (мас.).
Источником получения пропилена является фракция С3, которая содержится в газах первичной перегонки – ~52%, вторичной перегонки - ~ 35% и термического крекинга - ~ 26% (мас.).
Наибольшее количество бутан-бутиленовой фракции содержится в газах каталитического крекинга – до ~ 50%, вторичной перегонки – 47,4%% и автотермической газификации – до 48% (мас.).
Кроме того, сырьем для получения бутиленов может служить бутанбутиленовая фракция каталитического риформинга, в которой этилен и пропилен находятся в небольших количествах, а изобутан и н-бутан составляют ~ 60%.
Внастоящее время на нефтеперерабатывающих заводах России сырьем для нефтехимии служат в основном газы термического и каталитического крекинга. Суммарный выход газов термического и каталитического крекинга колеблется от 2 до 5% в расчете на перерабатываемую нефть (на нужды нефтехимии в настоящее время идет 45-70% газов термического и каталитического крекинга).
Чтобы увеличенить ресурсы углеводородного сырья для НПЗ, используют газы первичной и вторичной перегонки, гидроочистки и других процессов переработки нефти и нефтяных дистиллятов.
Врезультате компримирования газа первичной перегонки получается ~ 19% сухого газа и 80% конденсата, следующего фракционного состава (в %(
мас.)):
С2Н6 |
………… |
0,7 |
н-С4Н10…….. |
28,5 |
С3Н8 |
………… |
11,9 |
С5 и выше ….. |
51,2 |
изо-С4Н10 …… |
7,7 |
|
|
В табл. 3.3 приведены потенциальные ресурсы углеводородного сырья на НПЗ типовой мощностью 12 млн. т. нефти/год.
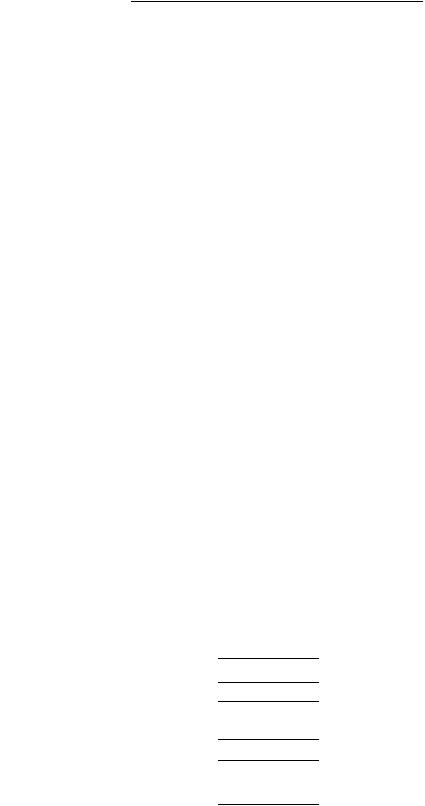
85
Таблица 3.3
Сырьевые ресурсы для производства олефинов |
|
|
||
|
|
Выход фракции |
|
|
Углеводородное сырье |
|
|
||
|
|
|
|
|
тыс. т |
%(на сырье) |
% (на нефть) |
|
|
|
|
|||
|
|
|
|
|
Газы первичной перегонки |
383 |
3,2 |
3,2 |
|
"Жирный" газ термокрекинга |
520 |
22,5 |
4,3 |
|
"Жирный" газ каталитического крекинга |
193 |
15,4 |
1,6 |
|
Газы каталитического риформинга |
118 |
5,7 |
0,99 |
|
Газы вторичной перегонки |
62,2 |
2,5 |
0,52 |
|
Газы гидроочистки |
1,44 |
- |
- |
|
Пропан-пропиленовая |
1,63 |
1,9 |
- |
|
фракция после алкилирования |
|
|
|
|
Отработанная бутан-бутиленовая фракция по- |
36,2 |
43,8 |
0,32 |
|
сле алкилирования |
|
|
|
|
Газ с установки стабилизации |
44,6 |
14,5 |
0,37 |
|
|
|
|
|
|
Низшие жидкие углеводороды : |
|
|
|
|
в автотермической газификации |
31,0 |
0,50 |
0,25 |
|
с термокрекинга |
57,6 |
2,0 |
0,48 |
|
с риформинга |
232,0 |
14,2 |
1,9 |
|
с установки стабилизации |
34,6 |
11,5 |
0,29 |
|
Всего |
1715,3 |
|
14,3 |
|
Таким образом, потенциальные ресурсы углеводородного сырья на нефтеперерабатывающем заводе составляют ~ 14,3 %.
Одним из основных процессов получения нефтехимического сырья на НПЗ служит каталитический крекинг. В табл. 3.4 приведен материальный баланс этого процесса.
Таблица 3.4
Материальный баланс процесса каталитического крекинга при разных режимах
Компоненты |
|
Выход, % (на сырье) |
|
||
713-723 К |
718-723 К |
748-753 К |
753-758 К |
||
|
|||||
"Жирный" газ |
11,0 |
14,7 |
18,5 |
18,5 |
|
в том числе оле- |
2,34 |
3,5 |
4,0 |
6,1 |
|
фины |
|||||
|
|
24,0 |
|
||
Бензин |
22,5 |
24,0 |
15,5 |
||
Легкий газойль |
37,5 |
37,0 |
32,0 |
39,9 |
|
Тяжелый газойль |
25,0 |
19,0 |
19,5 |
20,0 |
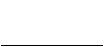
86
Кокс |
4,0 |
5,3 |
6,0 |
6,1 |
Всего |
100,0 |
100,0 |
100,0 |
100,0 |
Из таблицы видно, что максимальный выход олефинов может достигать 6,1% (в расчете на переработанное сырье).
В табл. 3.5 приведен состав газа, получаемого в процессе каталитического крекинга.
Таблица 3.5
Состав газа при каталитическом крекинге
|
713-723 К |
748-753 К |
718-723 К |
753-758 К |
||||
Компоненты |
|
|
|
|
|
|
|
|
Выход, |
Выход, |
Выход, |
Выход, |
Выход, |
Выход, |
Выход, |
Выход, |
|
|
% (на |
% (на |
% (на |
% (на |
% (на |
% (на |
% (на |
% (на |
|
газ) |
нефть) |
газ) |
нефть) |
газ) |
нефть) |
газ) |
нефть) |
Сероводород |
11,6 |
1,27 |
8,9 |
1,6 |
- |
- |
3,9 |
0,7 |
|
|
|
|
|
|
|
|
|
Водород |
0,9 |
0,1 |
0,9 |
0,17 |
- |
- |
2,5 |
0,4 |
Метан |
10,4 |
1,14 |
8,7 |
1,6 |
7,8 |
1,2 |
5,3 |
1,0 |
Этан-этилен |
9,5 |
1,04 |
7,5 |
1,4 |
11,3 |
1,6 |
11,5 |
2,1 |
Пропилен |
10,7 |
1,17 |
11,3 |
2,1 |
12,0 |
1,8 |
20,6 |
3,8 |
|
|
|
|
|
|
|
|
|
Пропан |
10,2 |
1,12 |
12,4 |
2,3 |
15,9 |
2,3 |
11,8 |
2,2 |
|
|
|
|
|
|
|
|
|
Бутаны |
39,7 |
6,3 |
50,3 |
10,3 |
43,0 |
6,0 |
40,4 |
8,3 |
Пентан |
10,8 |
1,19 |
10,6 |
1,96 |
14,8 |
2,2 |
10,2 |
1,8 |
Из таблицы видно, что содержание этан-этиленовой фракции в газе достигает 11,5% и пропилена - 20,6%, или - в пересчете на переработанную нефть - соответственно 2,1 и 3,8%.
3.1.2. Получение этилена
Этилен стал широко использоваться в качестве мономера перед Второй мировой войной в связи с необходимостью получения высококачественного изоляционного материала, способного заменить поливинилхлорид. После разработки метода полимеризации этилена под высоким давлением и изучения диэлектрических свойств получаемого полиэтилена началось его производство сначала в Великобритании, позднее и в других странах.
В настоящее время этилен - важное техническое сырье для производства полиэтилена высокого и низкого давления, этилен-пропиленовых каучуков и сополимеров со стиролом и винилацетатом, а также для производства стирола, этиленоксида и других продуктов.
87
Основным промышленным методом получения этилена является пиролиз жидких дистиллятов нефти или низших насыщенных углеводородов. Реакция проводится в трубчатых печах при 1023-1173 К и давлении 0,3 МПа. При использовании в качестве сырья прямогонного бензина выход этилена составляет ~ 30%. Одновременно с этиленом образуется также значительное количество жидких углеводородов, в том числе ароматических. При пиролизе газойля выход этилена составляет 15-25%. Наибольший выход этилена - до 50% - достигается при использовании в качестве сырья легких насыщенных углеводородов: этана, пропана, бутана. Пиролиз проводят в присутствии водяного пара. (см.
раздел 1.1.5).
Высокотемпературное дегидрированием этана
Дегидрирование этана проводят при температуре ~ 1173 К ии ~0,05 МПа. Катализатором процесса служит металлический никель (5%) на оксиде хрома
(95%):
С2Н6 С2Н4 + Н2.
Этан используют в смеси с азотом. Газ, выходящий из реактора, содержит ~33% этилена, небольшое количество ароматических углеводородов и 0,3% ацетилена.
По другому способу этилен получают парциальным окислением этана воздухом при 1073-1123 К. Предварительно этан нагревают до 923 К, а кислород - до 823 К, затем их смешивают в камере смешения в отношении 3:1. Из камеры смешения они с большой скоростью поступают в основной аппарат - камеру сжигания, которая заполнена кольцами Рашига. Благодаря небольшому времени контактирования образование углерода и формальдегида сводится к минимуму. Отходящий из камеры сжигания газ, содержит примерно: 33% (об.) этилена, 26% водорода, 14% этана. 11,5% оксида углерода, 7,5% метана, 4,2% азота и небольшое количество пропана, диоксида углерода и кислорода. Выход этилена составляет ~80% от теоретического.
Этот способ не нашел широкого промышленного применения.
Синтез этилена из метана
Сокращение добычи нефти в ближайшие годы и одновременное увеличение выработки моторного топлива (в перспективе) неизбежно приведет к уменьшению количества нефтяных фракций, используемых для нужд нефтехимической промышленности. Для компенсации сокращения традиционной сырьевой базы необходимо искать альтернативные виды сырья. Одним из таких источников является природный газ.
88
Получение этилена из метана может осуществляться тремя путями: через синтез-газ, через метанол и прямой димеризацией метана в этилен.
Превращение метана в этилен даже при очень высоких температурах ограничивается установлением термодинамического равновесия реакции. Значительные степени конверсии достигаются только при проведении реакции с участием окислителей. Использование окислителя, в свою очередь, затрудняет подбор катализатора для этой реакции, так как катализатор, эффективно активируя метан, должен одновременно слабо активировать кислород, чтобы предотвратить глубокое окисление метана. Это обстоятельство не позволяет применять для данной реакции такие эффективные катализаторы активации углеводородов, как, например, металлы платиновой группы.
Во избежание этой сложности, процесс проводят в две стадии: на первой - чистый метан димеризуют с использованием кислорода катализатора, а на второй - катализатор реокисляют кислородсодержащим газом. Разработаны двухстадийный периодический и одностадийный непрерывный способы окислительной димеризации метана. Окислительную димеризацию чистого метана проводят при температуре 973–1073 К в присутствии катализаторов - твердых оксидов с нанесенными на них благородными металлами. Наиболее активным катализатором оказался диоксид тория. Степень конверсии метана составляет ~ 50% при селективности (по этилену) 8%.
Окислительную димеризацию метана по двухстадийной схеме с более высокой селективностью по этилену проводят в присутствии оксидных катализаторов, из которых наиболее активными являются оксидные марганцевые катализаторы: NaMnO4/MgO-SiO2 и Mn3O4/SiO2 Выход углеводородов С2 на этих системах при 1073 К составляет 13-15%. Более высокий выход углеводородов С2 достигается при использовании в качестве окислителя гемиоксида азота и катализатора, содержащего 12,5% NaMnO4/МgО: при 1073 К и соотношении СН4:N2О=1:1; выход этилена составляет ~12 % .
Способ реализован в опытно-промышленном масштабе и имеет хорошие перспективы для промышленного использования.
Синтез этилена из метанола
Фирмы "Мобил" (США), "Хехст" (ФРГ) и некоторые другие разработали способ получения этилена и пропилена из метанола в присутствии высокоселективных цеолитсодержащих катализаторов. Процесс проводят при 873-973 К. Суммарный выход смеси этилена и пропилена составляет 70-80% и собственно этилена – 30-60%.
Для сравнения при пиролизе нафты, протекающем при 1123 К, эти показатели составляют соответственно 44-50% и 26-36%.
Способ реализован в опытно-промышленном масштабе и предложен к промышленному применению.
89
Дегидратация этанола
Это один из наиболее старых процессов.
Дегидратация этанола осуществляется в соответствии со схемой
CH3CH2OH CH2=CH2 + H2O.
Промышленное получение этилена дегидратацией ферментативного этанола началось раньше, чем его производство в процессе крекинга. Этот процесс может быть экономически эффективным в странах с большими запасами растительного сырья: в Бразилии, Индии, в некоторых странах Африки. В странах с развитой нефтехимической промышленностью используют обратную реакцию: гидратацию этилена до этанола.
Фирма "Юнион Карбайд" (США) разработала процесс получения этанола из синтез-газа на родиевом катализаторе:
2CO + 4H2 CH3CH2OH + H2O.
Однако селективность по этанолу составляет всего 33,5% в пересчете на превращенный оксид углерода. Кроме этанола образуются метан (49,6%), ацетальдегид (2,6%), уксусная кислота (6,5%).
Этанол может быть получен также гомологизацией метанола на кобальтовых или родиевых катализаторах:
CH3OH + CO + 2H2 CH3CH2OH + H2O.
Дегидратацию осуществляют в жидкой или газовой фазе в присутствии кислотных катализаторов (серная или фосфорная кислота, ароматические сульфокислоты, кислые соли, например сульфаты и фосфаты, хлорид цинка, хлорид алюминия и др.). Катализаторами дегидратации могут служить также оксиды алюминия и тория, фосфорный и фталевый ангидриды. При использовании в качестве катализатора фосфорной кислоты оптимальной является температура 483-493 К, а серной кислоты - 433-453 К. Газофазную дегидратацию этанола проводят в присутствии оксида алюминия или тория, пемзы, пропитанной пирофосфорной кислотой при 523-623 К. Этилен, получаемый дегидратацией этанола в присутствии оксида алюминия, содержит в качестве примесей водород, метан и бутадиен. Достаточно чистый этилен можно получить дегидратацией этанола на пемзе, пропитанной пирофосфорной кислотой при 553-573 К. Выход этилена в процессе составляет ~ 90% при фактическом отсутствии примесей.
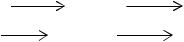
90
3.1.3.Получение пропилена
Внастоящее время в промышленности используют следующие методы получения пропилена:
-из нефтезаводских и крекинг-газов;
-из продуктов синтеза Фишера-Тропша и из газов коксования;
-из углеводородов С2-С4 и высших углеводородов.
Выделение пропилена из нефтезаводских газов и крекинг-газов
На нефтеперерабатывающих заводах пропиленсодержащие газы образуются при получении бензина в процессах крекинга и риформинга. Обычно выход газа составляет 4,5-5,5% (мас.) в расчете на общее количество перерабатываемой сырой нефти. Образующаяся газовая смесь, как правило, имеет следующий состав (в % (мол.)):
N2, О2, СО …………… 4,1 |
Пропан…………….9,4 |
Водород………………..6,1 |
Пропилен …………8,9 |
Метан…………………39,1 |
Бутаны…………….2,6 |
Этан …………………..17,5 |
Пентаны………...…1,4 |
Этилен………………….7,3 |
Сероводород………3,0 |
|
Диоксид углерода ..0,6 |
Выделение пропилена проводится следующим образом.
Из компримированных нефтезаводских газов абсорбцией этаноламином удаляют кислые газы (в основном Н2S и СО2), затем газ промывают щелочью и после охлаждения адсорбцией на цеолитах удаляют воду. Методом низкотемпературного фракционирования смесь разделяют на этан, этилен, пропан, пропилен и топливный газ. Этан и пропан подвергают дальнейшему крекингу в присутствии водяного пара для получения этилена и пропилена. После компрессии и охлаждения газы снова направляют на установку для разделения газов. Разделение пропана и пропилена осуществляется низкотемпературной дистилляцией.
Выделение пропилена из продуктов синтеза Фишера-Тропша (процесс фирмы "Сасол")
Синтез Фишера-Тропша – метод каталитического гидрирования оксида углерода с образованием смеси углеводородов. В зависимости от катализатора и условий, в которых осуществляется синтез, процесс протекает по схеме (1)
или (2):
nCO + 2nH2 -H2O |
CnH2n |
H2 |
CnH2n+2 , |
(1) |
H2 |
||||
2nCO + nH2 -CO2 |
CnH2n |
|
CnH2n+2 . |
(2) |