
- •Характеристики двигателей с искровым зажиганием
- •Испытания двигателей внутреннего сгорания
- •1.1. Лаборатория для испытаний двигателей
- •1.2. Оборудование и приборы для испытаний двигателей
- •1.3. Испытуемый двигатель
- •2. Общие положения по организации проведения лабораторных работ
- •2.1. Правила выполнения работ
- •2.2. Вопросы технической безопасности при проведении лабораторных работ
- •2.3. Содержание отчета по лабораторной работе
- •Условия и порядок проведения испытаний
- •2.5. Обработка результатов испытаний
- •2.6. Приведение параметров двигателя к стандартным атмосферным условиям
- •3. Лабораторная работа № 1
- •4. Лабораторная работа № 2
- •5. Лабораторная работа №3
- •6. Лабораторная работа №4
- •Характеристики двигателей с искровым зажиганием
- •107023, Г. Москва, б. Семеновская ул., 38
1.2. Оборудование и приборы для испытаний двигателей
1.2.1. Измерение мощности двигателя
Для измерения мощности в лаборатории используется электрический тормоз постоянного тока. Такие тормоза отличаются плавностью и широкими пределами регулирования скоростных и нагрузочных режимов, поэтому они находят преимущественное применение, особенно для исследовательских целей.
Общее устройство электрической балансирной машины постоянного тока показано на рис 3. Ее корпус (статор) 1 на шариковых подшипниках 14 установлен на стойки 3. В боковые крышки статора вмонтированы шариковый и роликовый подшипники 13 вала 4 якоря (ротора) 2, смазку к которым подают через капельницы 7. Статор и ротор, имея общую ось вращения, могут совершать угловые перемещения независимо друг от друга.
|
Рис. 3. Электрическая балансирная машина постоянного тока 1 – корпус (статор); 2 – якорь (ротор); 3 – стойки; 4 – вал; 5 – железная основа якоря; 6 – обмотка якоря; 7 – капельницы; 8 –станина; 9 – полюсные сердечники; 10 – обмотка возбуждения; 11 – неподвижные держатели; 12 – коллектор; 13 – роликовый подшипник; 14 – шариковый подшипник.
|
При работе электрической балансирной машины в моторном режиме (определение механических потерь, пуск двигателя или его обкатка) в результате взаимодействия магнитных полей якоря и статора на последнем возникает реактивный момент, который, будучи направлен в сторону, противоположную вращению якоря, стремится повернуть статор около оси якоря. Поэтому крутящий момент, необходимый для прокручивания вала испытуемого двигателя, измеряют по реакции статора.
|
Рис. 4. Схема квадрантного динамометра 1 – маятник; 2 – кулак-квадрант; 3, 7 – ленты; 4 – стрелка; 5 – большой кулак; 6 –зубчатая рейка; 8 – положение маятника в отсутствии нагрузки; 9 – балансир; 10 – зубчатое колесо. |
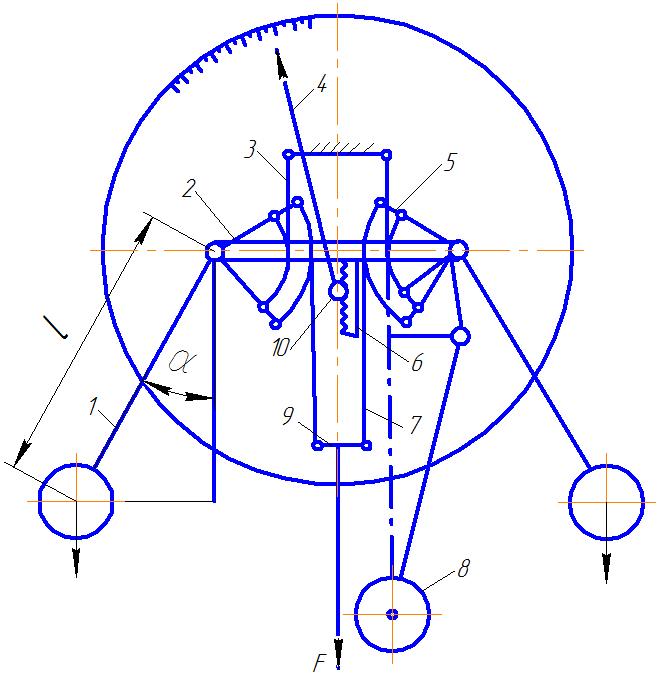
ри работе балансирной машины в режиме генератора (режим торможения) в обмотке якоря возникает электродвижущая сила, которая вызывает ток в цепи якоря. Ток своим магнитным полем противодействует вращению якоря, а, следовательно, и вращению вала испытуемого двигателя. При этом статор стремится повернуться в направлении вращения якоря.
Для измерения крутящего и тормозного моментов, развиваемых двигателем, служит динамометр. Одним из наиболее совершенных и наиболее применяемых является механический квадрантный динамометр (рис. 4).
Он имеет два маятника, укрепленных на кулаках-квадрантах, которые подвешены на тонких стальных лентах. Под влиянием силы F, которая передается от рычага статора тормоза, маятники совершают сложное движение, отклоняясь от положения равновесия. Балансир, к которому приложена сила F, смещается при этом вниз. При перемещении балансира связанная с ним зубчатая рейка поворачивает стрелку, по положению которой производится отсчет показаний динамометра.
По измеренной с помощью динамометра силе F определяется крутящий момент, развиваемый двигателем, Н·м:
Ме =.Р.l ,
где Р – показания весового механизма динамометра, Н;
– плечо тормоза,
м (для большинства существующих
конструкций
= 0,7162 м).
Тогда эффективная мощность двигателя, кВт:
,
где n – частота вращения коленчатого вала, мин-1.
1.2.2. Измерение расхода воздуха
При определении коэффициента наполнения двигателя или коэффициента избытка воздуха необходимо знать величину часового расхода воздуха, потребляемого двигателем.
Для измерения расхода воздуха возможно использование двух счетчиков:
1) ротационный газовый счетчик типа РГ;
2) термоанемометрический расходомер воздуха.
В первом случае ко впускному трубопроводу двигателя эластичным переходником присоединен ресивер 4 (рис. 5), который необходим для гашения колебаний воздуха. На ресивере 4 установлен газовый счетчик 3 и труба 2 с тонким капроновым фильтром 1.
|
Рис. 5. Схема установки для измерения расхода воздуха: 1 – капроновый фильтр; 2 – труба; 3 - газовый счетчик; 4 – ресивер. |
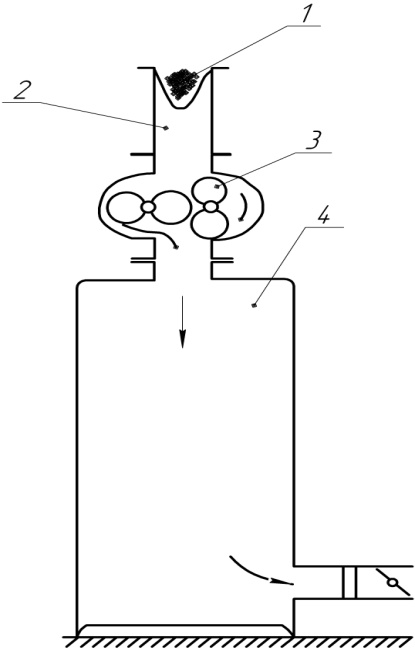
В этом случае расход воздуха (кг/ч) определится по формуле
,
где ΔVв – объем воздуха, проходящий через газовый счетчик за один
оборот роторов, м3;
nсч – число оборотов ротора;
τ – время измерения числа оборотов, с;
ρв – плотность воздуха, кг/м3.
Газовые расходомеры этого типа имеют очень малые гидравлические сопротивления, поэтому плотность воздуха внутри счетчика принимают равной плотности окружающей среды.
В случае, если испытывается двигатель, оборудованный системой электронного управления, информация о расходе воздуха может быть получена от штатного расходомера через диагностический разъем. Широкое распространение получил термоанемометрический расходомер воздуха.
Чувствительный элемент датчика построен по принципу терморезистивного анемометра и выполнен в виде платиновой нагреваемой нити. Нить нагревается электрическим током, а с помощью термодатчика ее температура измеряется и поддерживается постоянной.
Если через датчик поток воздуха увеличивается, то платиновая нить начинает охлаждаться, и система управления датчиком увеличивает ток нагрева нити до тех пор, пока температура ее не восстановится до первоначального уровня. Таким образом, величина тока нагрева нити пропорциональна расходу воздуха. Вторичный преобразователь датчика преобразует ток нагрева нити в выходное напряжение постоянного тока.
С течением времени нить загрязняется, что приводит к смещению градуировочной характеристики датчика. Для очистки нити от грязи после выключения двигателя (при выполнении определенных условий) нить прожигается до 900 – 1000°C импульсом тока в течение 1 секунды. Импульс управления прожигом формируется блоком управления.
1.2.3. Измерение давления
Для измерения давлений при испытаниях двигателя используют два типа приборов – механические и жидкостные.
Так, в системе смазки двигателя давление измеряют с помощью механического манометра, имеющего шкалу до 5 бар.
Схема механического манометра показана на рис.6.
Трубка Бурдона 1, воспринимая давление, деформируется, при этом угловое перемещение конца трубки прямо пропорционально избыточному давлению, что дает возможность получить равномерную шкалу. Свободный конец трубки Бурдона 1 с помощью тяги 2 и зубчатого сектора 3 через шестеренку 4 связан со стрелкой 5. На оси укреплена спиральная пружина 6, необходимая для устранения свободного хода в механизме. Передающий механизм увеличивает небольшие деформации трубки 1 в заметные перемещения стрелки 5.
|
Рис. 6. Схема манометра 1 – Трубка Бурдона; 2 – Тяга; 3 – Зубчатый сектор; 4 – Шестеренка; 5 – Стрелка; 6 – Спиральная пружина. |
В простейшем исполнении пьезометр представляет собой U-образную трубку, заполненную примерно до половины (до нулевых меток шкалы) водой или другой жидкостью.
Пьезометры применяются для измерения избыточного давления, вакуума и разности давлений.
1.2.4. Измерение температуры
Приборы для измерения температуры по принципу действия делятся на механические и электрические. Механические приборы – жидкостные (обычно ртутные) и манометрические термометры – используют для измерения низких температур (до 423 К). Из электрических наибольшее применение нашли температурно-зависимый полупроводниковый резистор и термоэлектрический термометр.
Для измерения температуры охлаждающей жидкости, температуры воздуха во впускном трубопроводе, температуры моторного масла используется полупроводниковый резистор (рис. 7).
Датчик температуры предназначен для преобразования температуры в напряжение постоянного тока. Он представляет собой полупроводниковый стабилитрон, который запитывается постоянным рабочим током от стабилизированного источника блока управления, выходное напряжение датчика изменяется в зависимости от температуры среды. С увеличением температуры выходное напряжение датчика увеличивается.
|
Рис. 7. Датчик температуры охлаждающей жидкости системы охлаждения двигателя: 1 – электрические соединения; 2 – корпус; 3 – уплотнительное кольцо; 4 – резьбовое соединение; 5 – измерительный резистор (термистор); 6 – охлаждающая жидкость. |

1.2.5. Измерение частоты вращения
Для измерения частоты вращения коленчатого вала и роторов газового счетчика используется индуктивный датчик (рис. 8)
Датчик представляет собой стержневой магнит с намотанной поверх него обмоткой, который заключен в корпус из высокопрочной пластмассы.
|
Рис. 8. Индуктивный датчик. 1 – магнит; 2 – корпус; 3 – кронштейн крепления; 4 – магнитопровод; 5 - обмотка; 6 – диск синхронизации.
|
1.2.6. Измерение расхода топлива
|
Рис. 9. Схема объемного способа измерения расхода топлива: 1,2,3,4 – стеклянные мерные емкости разного объема.
|
При объемном способе, схема которого приведена на рис. 9, используются мерные колбы, состоящие из нескольких стеклянных шаров различной емкости, соединенных между собой тонкими трубками, которые повышают точность замера.
Объем шаров между рисками тарируют. Нижняя трубка соединяется с трехходовым краном, который соединен с трубкой, идущей от топливного бака, и с трубкой, идущей к двигателю. Объем шара выбирается таким, чтобы испытуемый двигатель расходовал топливо из него за время не менее 20 с.
Трехходовый кран дает возможность осуществлять подачу топлива из бака или из мерной колбы, а также подавать топливо в двигатель и одновременно заполнять мерные колбы.
Положение трехходового крана (рис. 9):
а – подача топлива из бака в двигатель, мерные колбы перекрыты;
б – наполнение мерных колб из бака, одновременно топливо поступает в двигатель;
в – подача топлива из мерных колб в двигатель (производится замер расхода топлива), топливный бак перекрыт.
Расход топлива определяется по формуле
,
кг/ч,
где ΔV – объем одной или нескольких мерных емкостей, см 3; ρт – плотность топлива, г/см 3; τ – время расхода топлива из мерной емкости,с.