
книги2 / 122
.pdf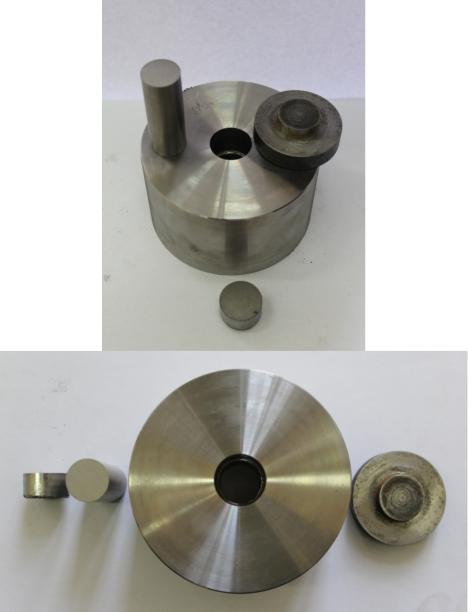
нагружения. Под действием давления гетерофазная механическая смесь подвергается уплотнению при реализации тангенциального перемещения материала при обеспечении интенсивных сдвиговых деформаций. При этом создаются условия, позволяющие инициировать и реализовывать механическую схему нагружения, соответствующую боковому выдавливанию.
На рисунке 6 представлено фото конструкции пресс-формы.
Рис. 6. Пресс-форма ступенчатая цилиндрическая
21
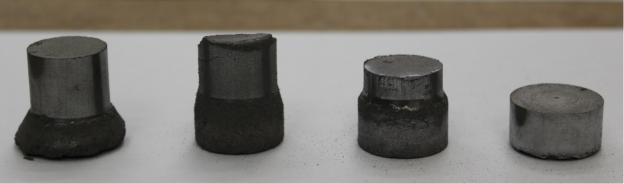
Поэтапная динамика прессования гетерофазной механической смеси на характерных стадиях уплотнения и формообразования, определяющая трехступенчатую схему интенсивного уплотнения увлажненных систем и реализации сдвига на четвертой стадии уплотнения, представлена на рисунке 7 [29].
Рис. 7. Характерные этапы формообразования: 1 – первая стадия уплотнения; 2 – вторая стадия уплотнения; 3 – третья стадия уплотнения; 4 – четвертая стадия уплотнения.
Образцы на четвертой стадии уплотнения имеют строго цилиндрическую поверхность, при этом плотность приближается к плотности теоретического уровня (Q 1 %) Прессование образцов проводилось с использованием ступенчатой прессформы, фиксировалась получаемая структура на третьей и четвертой стадии уплотнения при давлении прессования 1350 и 1600 МПа соответственно.
При прессовании образцов использовался железный распыленный порошок АНС100.29 (металлический порошок фирмы «Höganas», S-26383 Högana, Швеция) с химическим, гранулометрическим составом и технологическими свойствами, приведенными в таблице 1, свойства жидкой фазы представлены в таблице 2.
22
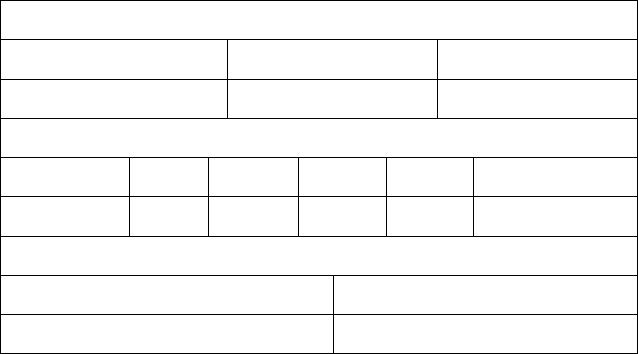
Таблица 1. Железный порошок АНС100.29 (металлический порошок фирмы «Höganas», S-263 83 Höganas, Швеция)
Химический состав, % не более |
|
|
|
||
Fe |
|
C |
|
O2 |
при нагреве в Н2 |
основа |
|
0,024 |
|
0,17 |
|
Гранулометрический состав порошка |
|
|
|
||
Размер, мкм |
250…200 |
200…160 |
100…71 |
71…45 |
Менее 45 |
Содержание, % |
0…2 |
0…12 |
Ост. |
Ост. |
10…30 |
Технологические свойства |
|
|
|
|
|
Насыпная плотность, г/см3 |
|
Текучесть, сек/50 г |
|
||
2,95 |
|
|
25 |
|
|
Таблица 2. Свойства применяемой жидкости
Жидкость |
Плотность (20 °С), г/см3 |
Вязкость (20°С), сП |
|
|
|
Вода (Н2О) |
0,998 |
1,005 |
|
|
|
В экспериментальных исследованиях использовалась коническая («тающая») оснастка, имеющая определенный угол (отличный от 90о) образующей рабочей поверхности, моделирующей изучаемые условия нагружения. Варьирование угла образующей рабочей зоны позволяет изменять условия нагружения, инициирующего и реализующего сдвиг.
При реализации программ исследований применялось следующее оборудование: испытательная машина УМ-50 (изучение уплотнения структуры), прибор ПМТ-3 (измерение твердости), микроскоп МИМ-8, световой микроскоп «OLIMPUS» (изучение микроструктуры), электронные аналитические весы (определение массы навески и
23
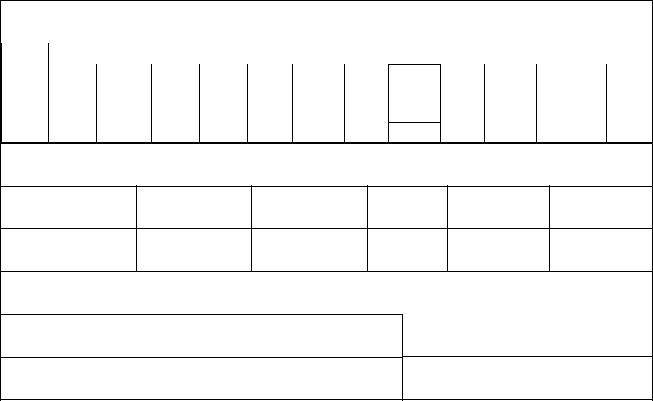
прессовки), микрометр (измерение линейных размеров прессовки), цифровой фотоаппарат (фотографирование образцов и структуры), ЭВМ (статистическая обработка результатов, выполнение расчетов).
При подготовке механической смеси была использована композиция (таблица 3), состоящая из порошка АНС100.29 и порошкового графита (0,11 % по масс. доле).
Таблица 3. Железный порошок АНС100.29 (металлический порошок фирмы «Höganas», S-263 83 Höganas, Швеция)
Химический состав, % не более
|
|
|
|
|
|
Элементы, % |
|
|
|
|
||
Co |
Cu |
Cr |
Mn |
Si |
Ni |
Al |
Ti |
P |
C |
S |
О2 при |
Fe |
|
|
|
|
|
|
|
|
|
|
|
нагреве |
|
|
|
|
|
|
|
|
|
0,002 |
|
|
в H2 |
|
0,01 |
0,005 |
0,002 |
0,08 |
0,04 |
0,05 |
0,025 |
0,03 |
0,11 |
0,009 |
0,17 |
Ост. |
|
Гранулометрический состав порошка |
|
|
||
Размер, мкм |
250…200 |
200…160 |
100…71 |
71…45 |
Менее 45 |
Содержание, % |
0…2 |
0…12 |
Ост. |
Ост. |
10…30 |
|
Технологические свойства |
|
|
||
Насыпная плотность, г/см3 |
|
Текучесть, сек/50 г |
|
||
|
2,95 |
|
|
25 |
|
Массовое соотношение основных элементов смеси составило 85:15, что соответствует физической моделе поглощения (растворения) жидкостью порового воздуха при нагружении и использовании давлений высокого уровня [51].
24
Приготовление смеси осуществлялось согласно требованиям международного стандарта ИСО.10067. В сухую смесь из железного порошка и графита, помещенную в стакан смесителя, заливалась вода, и производилось перемешивание механической смеси в течение 10 минут до образования гомогенной структуры.
Размеры рабочей зоны пресс-формы (высота и диаметр) выбирались таким образом, чтобы обеспечить при уплотнении следующие условия [52]: pxyz/pср 1, где pxyz – прикладываемое давление в любой точке уплотненного образца; pср – среднее давление уплотнения.
Масса навески составляла 29 грамм, погрешность взвешивания не превышала 0,001 грамма. Прессование образцов осуществлялось на гидравлическом прессе усилием 1000 кН.
Спекание отпрессованных образцов проводилось в проходной конвейерной печи модели СК3-6. 95.1 в среде эндогаза на производственных мощностях ООО «Димитровградский завод порошковой металлургии», температура спекания 1100 оС.
Металлографические исследования структуры металла, а также подготовка к испытаниям отпрессованных и спеченных образцов проведены в соответствии с ГОСТ 6032-2003 «Стали и сплавы коррозионностойкие. Методы и испытания на стойкость к межкристаллитной коррозии» [53].
Подготовка образцов для металлографических исследований заключалась в следующем: были вырезаны фрагменты из исходных цилиндрических заготовок (d×h=10×5(мм)), при этом исследовалась поверхность, перпендикулярная плоскости фрагмента (рис. 8).
25
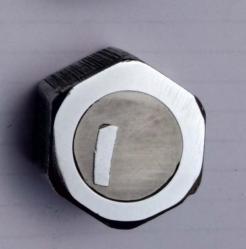
Рис. 8. Шлиф для металлографических исследований
Вырезанные фрагменты были подвергнуты полированию, при этом достигаемая шероховатая поверхность не превышала по Ra<= 0,8 мкм.
Всоответствии со Стандартом [53] был реализован метод АМУ – наиболее часто и презентативно используемый при испытании на стойкость МКК сталей ферритного класса в растворе серной кислоты и сернокислой меди в присутствии металлической меди.
Обработанные фрагменты образцов были выдержаны в кипящем растворе: а) 50 грамм сернокислой меди (CuSO4∙5H2O) на 1000 см3 H2O; б) 250 см3 серной кислоты (H2SO4).
До загрузки в колбу с раствором была добавлена медная стружка в количестве, обеспечивающем всесторонний контакт с испытуемыми образцами при отсутствии собственного контакта (обеспечено селективной загрузкой медной стружки и созданием конверсионной прослойки).
Висследованиях использована стеклянная колба с обратным холодильником. Окончательно заполнение колбы было приведено из расчета, чтобы обеспечить (4...8) см3 раствора на 1 см2 по поверхности фрагментов со стружкой, при этом уровень раствора выдерживался в течение всего испытания на (1,0...1,5) см выше поверхности образцов со стружкой.
На рисунке 9 представлен стенд термической обработки образцов
вкипящем растворе серной кислоты.
26
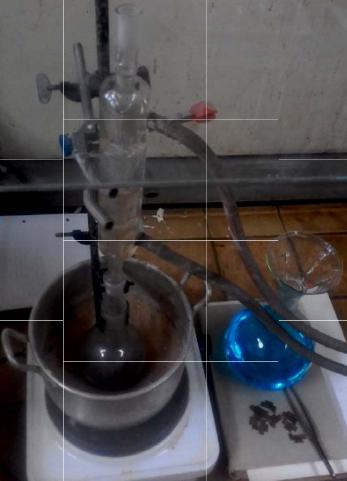
Рис. 9. |
тенд термическо |
обработки образцов |
|
|
Продолжительность |
выдержки исследуемых |
материал ов в |
кипящем |
|
растворе составляла 8 |
часов. Затем образцы были промы ы в проточной |
|||
воде и просуш ны.* |
|
|
|
|
М таллографические иссл дования |
по |
определению |
глубины |
|
межзеренного разрушен ия (контролируе |
ый параметр ме коррозионного |
разру шения) б ыли проведены на металлографическом мик оскопе ИМ-7
в отраженном |
свете на: |
1. Нетравленых |
образц х (изучение структуры |
|||
металла). 2. Т авленых образцах (выяв ения качества |
границ зерен) в |
|||||
центральной |
заводской |
лаборатории |
(ЦЗЛ) |
ООО |
«Ульяновский |
|
автомобильны |
завод».* * |
|
|
|
|
|
|
|
|
|
|||
* Данные испытания были проведены на кафедре |
«Химия, |
технологии композиционных |
||||
материалов и промышленная экология» УлГТУ с участием профессора М.А. Бузаевой. |
||||||
** Лаборатория металлографии при участии ведуще о инженер |
О.Н. Мочаловой. |
|||||
|
|
|
27 |
|
|
|
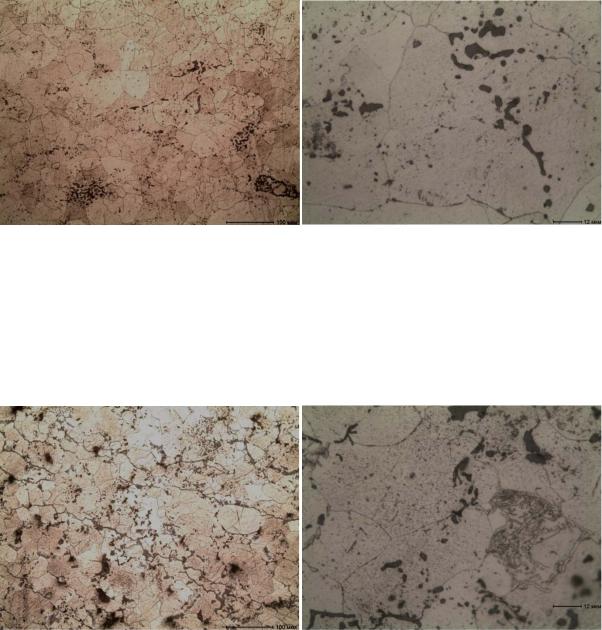
На рисунке 10 представлены фото шлифов фрагментов образцов до испытаний. Отмечена ферритная и перлитная составляющая (ф еррит, зерно 5-го балла, имеют скопления вклю чений; с поверхности: феррит + перлит), а также единичные вклю чения структурно свободного цементита.
|
а) |
б) |
Рис. 10. С руктура: феррит, зерно 5 балла + скопления включений |
||
|
фото 10, 11), с поверхности феррит + перлит: а) ×200; б) ×1000 |
|
На |
рисунке 11 редставлены структуры, |
имеющие единичные |
включ |
ения структурносвободного цементита. |
|
а) |
б) |
|
Рис. 11. Структура: феррит, зерно 6 |
алла + включения |
скоплениями |
и по границам зерна + единичные вклю чения структурно |
свободного |
|
цементита: а) ×200 ; б) ×1000 |
|
28
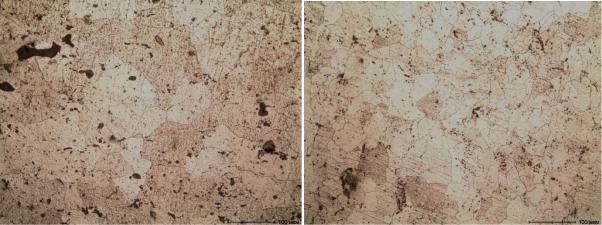
Был пров ден ана из структуры образцов пятой ста ии уплотнения (давление прессования составил 1550...1600 МПа). С целью установления локализации образования дефе тов стр ктуры, в том числе и трещин, иссле ованию подверглись характерные зоны образцов:
а) приконтактная (с деформирующ м инструментом); б) срединная (по образцу).
На рисунке 12 пр едставлено фото микроструктуры «сердцевины» металла образца исследуемой поверхности фрагментов образцов.
Рис. 12. Микроструктура «сердцевины» металла образца исследуемой поверхности (×200)
Определялась |
ма симальная глубина раз |
рушения |
по гр ницам |
|||
смежных зере , выявл емая в |
6-ти полях зрени |
я (признаком стойкости |
||||
структуры к М КК явл ется разрушение границ |
зерен на максимальную |
|||||
глубину h<= 30 мкм). |
|
|
|
|
||
Анализ представленных структур (после испы таний по |
режиму АМУ) |
|||||
позволяет |
сделать |
сл дующие |
выводы: |
структуры, соответствующие |
||
последней |
стадии |
прессования |
(q≥1500 МПа) в |
основном металле, не |
||
подвержены межкристаллитной коррози |
(рис. 1 |
3), при которой глубина |
||||
проникновения трещин ы в межзеренную зону не п |
ревышала 0,025 мкм. |
29
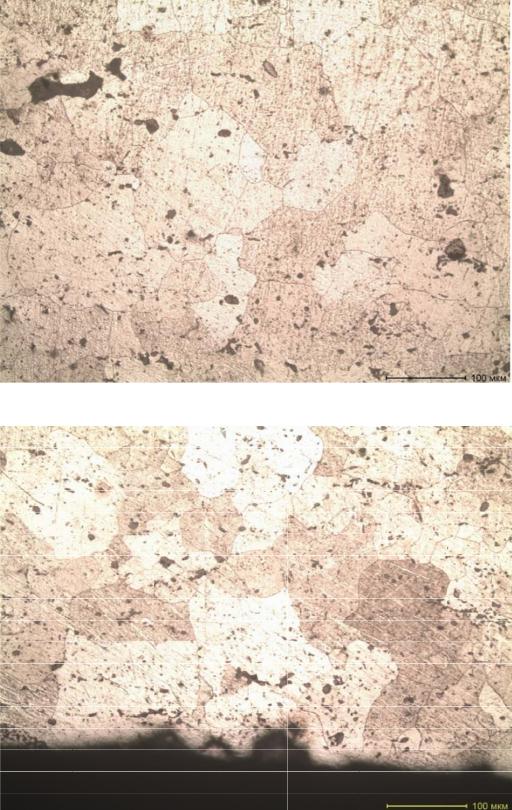
а)
б)
Рис. 13. Структуры, соответствующие последней стадии прессования (q≥ 500 МП ) в основном металле:
а) «сердцевина»; б) поверхность обр зца (×200)
30