
- •1 Физическая технология топлив
- •1.1 Подготовка нефти к переработке
- •1.1.1 Описание работы электрообессоливающей установки (элоу) (рисунок 1)
- •1.2 Первичная переработка нефти
- •1.2.1 Описание работы установки авт-1 (рисунок 2)
- •1.2.2 Описание работы установки элоу-ат-6 (рисунок 3)
- •1.2.3 Описание работы установки элоу-атв-6 (рисунок 4)
- •1.2.4 Описание работы установки элоу-авт-4 по переработке газового конденсата (рисунок 5)
- •3 Химическая технология топлив и углеродных материалов
- •3.1 Термические процессы
- •3.1.1 Описание работы установки термического крекинга нефтяных остатков (рисунок 6)
- •3.1.2 Описание работы установки замедленного коксования (рисунок 7)
- •3.1.3 Описание работы установки термоконтактного коксования (рисунок 8)
- •3.1.4 Описание работы установки термического пиролиза легкого углеводородного сырья (рисунок 9)
- •3.2 Каталитические процессы
- •3.2.1 Каталитический крекинг а) Описание работы установки г-43-102 каталитического крекинга вакуумного газойля (рисунок 10)
- •Б) Описание работы установки г- 43-107 по переработке вакуумного газойля (рисунок 11)
- •3.2.2 Описание работы установки каталитического риформинга (рисунок 12)
- •3.2.3 Описание работы установки гидроочистки нефтяных дистиллятов (л-24-7) (рисунок 13)
- •3.2.4 Описание работы установки гидрокрекинга вакуумного газойля (рисунок 14)
- •I вариант гидрокрекинга - бензиновый, II вариант – дизельный
- •3.3 Получение индивидуальных продуктов
- •3.3.1 Описание технологической схемы сернокислотного алкилирования изобутана олефинами (рисунок 15)
- •3.3.2 Полимеризация (олигомеризация) пропан-пропиленовой фракции (рисунок 16)
- •3.3.3 Каталитическая изомеризация легких парафинов нормального строения (рисунок 17)
- •3.3.4 Производство метилтретбутилового эфира (мтбэ) (рисунок 18)
- •3.4 Переработка твердых топлив
- •3.4.1 Полукоксование твердых топлив (рисунок 19)
- •3.4.2 Газификация каменного угля (рисунок 20)
- •3.5 Производство нефтяных масел
- •3.5.1 Процесс деасфальтизации гудрона в сжиженном пропане (рисунок 21)
- •3.5.2 Селективная очистка масляного сырья фенолом (рисунок 22)
- •3.5.3 Селективная очистка масел фурфуролом (рисунок 23)
- •3.5.4 Депарафинизация масляного сырья в кетон-ароматическом растворителе (рисунок 24)
- •3.5.5 Депарафинизация масляного сырья комплексообразованием с карбамидом (рисунок 25)
- •3.5.6 Адсорбционная очистка масел (контактная очистка) (рисунок 26)
- •Список используемых источников
- •Содержание
- •Редактор л.А. Маркешина
- •450062, Республика Башкортостан, г. Уфа, ул. Космонавтов, 1
3.4.2 Газификация каменного угля (рисунок 20)
Газификация - высокотемпературный процесс взаимодействия углерода топлива с окислителями, проводимый с целью получения горючих газов (Н2, СО, СН4). В качестве окислителей, которые иногда называют газифицирующими агентами, используют кислород (или обогащенный им воздух), водяной пар, диоксид углерода либо смеси указанных веществ. В зависимости от соотношения исходных реагентов, температуры, продолжительности реакции и других факторов можно получать газовые смеси самого разного состава.
В настоящее время выявились следующие наиболее экономически эффективные области применения рассматриваемого метода: газификация сернистых и многозольных топлив с последующим сжиганием полученных газов на мощных тепловых электростанциях; газификация твердых топлив для крупномасштабного производства заменителей природного газа; газификация твердых топлив с целью получения синтез-газа, газов-восстановителей и водорода для нужд химической, нефтехимической и металлургической промышленности.
В газогенераторе Lurgi исходный уголь (размер частиц 5-30 мм) из бункера 2 периодически загружают в шахту 7 газогенератора, снабженную водяной рубашкой 12. При помощи охлаждаемого вращающегося распределителя 5 и перемешивающего устройства 6 топливо равномерно распределяется по сечению аппарата. Парокислородное дутье подают под вращающуюся колосниковую решетку 11, на которой находится слой золы. Этот слой способствует равномерному распределению газифицирующего агента. При вращении колосниковой решетки избыточное количество золы с помощью ножей 8 сбрасывают в бункер 14. Образующийся в аппарате газ проходит скруббер 10, где предварительно очищается от угольной пыли и смолы (в случае необходимости смолу можно возвратить в шахту газогенератора). Вращение распределителя 5 и колосниковой решетки 11 осуществляется от электродвигателей 4 и 9.
В шахте газогенератора поддерживают давление ~3 МПа, поэтому, чтобы обеспечить безопасную загрузку топлива и выгрузку золы, каждый из бункеров 2 и 14 снабжают двумя конусообразными затворами (1, 3, 13 и 15). При загрузке топлива в бункер 2 затвор 1 открыт, а затвор 3 закрыт. Для передачи топлива в шахту затвор 1 закрывают, по обводной газовой линии соединяют бункер с шахтой газогенератора (для выравнивания давления) и открывают затвор 5. Перед следующей загрузкой топлива в бункер 2 закрывают затвор 3, сбрасывают газ в линию низкого давления, продувают бункер азотом или водяным паром, а затем открывают затвор 1. Аналогично осуществляют выгрузку золы из бункера 14. Типичный газогенератор Lurgi имеет диаметр 4—5 м, высоту 7-8 м (без бункеров) и производительность по углю 600-1000 т в сутки.
Рисунок 20 - Газогенератор Lurgi для газификации каменного угля
3.5 Производство нефтяных масел
3.5.1 Процесс деасфальтизации гудрона в сжиженном пропане (рисунок 21)
Назначение процесса – удаление смолисто-асфальтеновых веществ, полициклоароматических соединений из гудрона (полугудрона) с целью снижения коксуемости и получения сырья для процессов гидрокрекинга, каталитического крекинга, производства остаточных масел.
В качестве растворителей используют пропан, бутан, легкий бензин.
Продукты – деасфальтизат (идет на селективную очистку, гидрокрекинг, каталитический крекинг) и асфальт (компонент котельного топлива, битумов).
Сырьё насосом 1 через паровой подогреватель 2 подается вверх колонны деасфальтизации 3. Из емкости 21 насосом 22 через теплообменник 23 в низ деасфальтизационной колонны 3 подаётся пропан. Колонна 3 сверху оборудована встроенным паровым подогревателем для регулирования качества деасфальтизата.
Сверху 3 раствор деасфальтизата проходит клапан-регулятор 4, (давление снижают с 4,0 до 2,5 МПа), затем подается в горизонтальный испаритель высокого давления 5. Сверху 5 отводится пропан, а снизу раствор деасфальтизата, содержащий 20% пропана, поступает в горизонтальный испаритель низкого давления 6. Сверху 6 удаляется пропан. Деасфальтизат с 3 % пропана поступает в отпарную колонну 7. Снизу 7 деасфальтизат насосом 8 через холодильник 9 откачивается в товарный парк. Сверху 7 пары воды и пропана идут в конденсатор смешения 14.
С низа деасфальтизационной колонны 3 раствор асфальта поступает в печь 10, где нагревается до температуры 260-280 оС, затем в сепаратор 11, сверху которого отводится пропан, а снизу асфальт, содержащий до 2% пропана, через клапан-регулятор 12 подается в отпарную колонну 13. Снизу 13 асфальт насосом 15 прокачивается через холодильник 16 и отводится в товарный парк. Сверху 13 пары воды и пропана поступают в конденсатор смешения 14, куда подаётся холодная вода. Сверху 14 пропан отводится в каплеотбойник 17, затем сжимается в компрессоре 18, охлаждается в конденсаторе-холодильнике 19 и собирается в емкости 21. Сверху 5, 6, 11 пропан поступает в пропановую линию, после компремирования охлаждается в конденсаторе-холодильнике 20 и также собирается в емкости 21. В емкость 21 предусмотрена подача свежего пропана.
Кратность пропана к сырью в зависимости от качества сырья 3-8 : 1. Температура в колонне деасфальтизации: верха – 65-85 оС, низа – 55-65 оС. Температура ввода сырья – 130-170 оС.
Рисунок 21 – Принципиальная технологическая схема деасфальтизации гудрона в сжиженном пропане
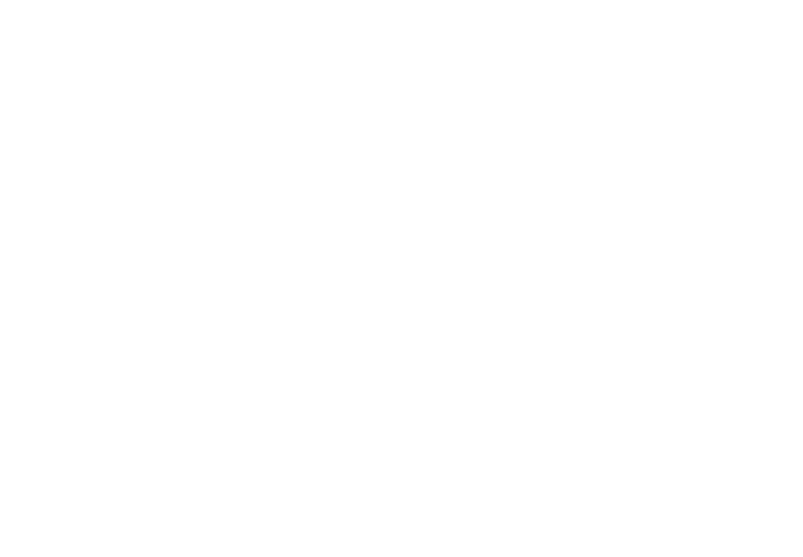
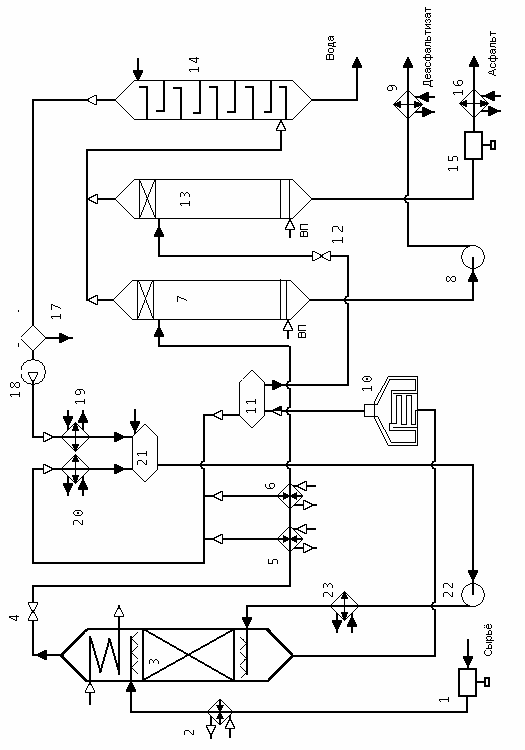