
переработка нефти-1
.pdfvk.com/club152685050 | vk.com/id446425943
Название «замедленное» в рассматриваемом процессе коксования связано с особыми условиями работы реакционных змеевиков трубчатых печей и реакторов (камер) коксования. Сырье необходимо предварительно нагреть в печи до высокой температуры (470…510°С), а затем подать в необогреваемые, изолированные снаружи коксовые камеры, где коксование происходит за счет тепла, приходящего с сырьем.
Посколькусырьепредставляетсобойтяжелыйостаток,богатыйсмоламииасфальтенами(т.е.коксогеннымикомпонентами),имеетсябольшая опасность, что при такой высокой температуре оно закоксуется
взмеевиках самой печи. Поэтому для обеспечения нормальной работы реакционной печи процесс коксования должен быть «задержан» до тех пор, пока сырье, нагревшись до требуемой температуры, не поступит
вкоксовые камеры. Это достигается благодаря обеспечению небольшойдлительностинагревасырьявпечи(засчетвысокойудельнойтеплонапряженности радиантных труб), высокой скорости движения по трубампечи,специальнойееконструкции,подачитурбулизатораит.д. Опасность закоксовывания реакционной аппаратуры, кроме того, зависит и от качества исходного сырья, прежде всего от его агрегативной устойчивости. Так, тяжелое сырье, богатое асфальтенами, но с низким содержанием полициклических ароматических углеводородов, характеризуетсянизкойагрегативнойустойчивостью,ионобыстрорасслаиваетсявзмеевикахпечи,чтоявляетсяпричинойкоксоотложенияипрогара труб. Для повышения агрегативной устойчивости на современных УЗК к сырью добавляют такие ароматизированные концентраты, как экстракты масляного производства, тяжелые газойли каталитического крекинга, тяжелая смола пиролиза и др.
Процесс замедленного коксования является непрерывным по подаче сырья на коксование и по выходу газообразных и дистиллятных продуктов, но периодическим по выгрузке кокса из камер. Установки замедленного коксования включают в себя следующие два отделения: нагревательно-реакционно-фракционирующее, где осуществляется собственно технологический процесс коксования сырья и фракционированиеегопродуктов;отделениепомеханическойобработкекокса,где осуществляется его выгрузка, сортировка и транспортировка.
Взависимости от производительности УЗК различаются количеством и размерами коксовых камер, количеством и мощностью нагревательных печей. На установках первого поколения приняты печи шатрового типа и две или три камеры коксования с диаметром 4,6м и высотой 27м, работающие поочередно по одноблочному варианту. УЗК последующих поколений преимущественно являются двухблоч-
594
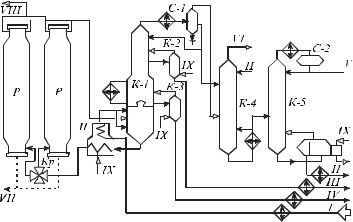
vk.com/club152685050 | vk.com/id446425943
ными четырехкамерными, работающими попарно. На современных модернизированных УЗК используются печи объемно-настильного
ивертикально-факельного пламени и коксовые камеры большего диаметра (5,5…7,0м; высота — 27…30м). В них предусмотрены высокая степень механизации трудоемких работ и автоматизации процесса.
По технологическому оформлению УЗК всех типов различаются между собой незначительно и преимущественно работают по следующейтиповойсхеме:первичноесырье →нагреввконвекционнойсекции печи → нагрев в нижней секции ректификационной колонны теплом продуктовкоксования→нагреввторичногосырьяврадиантнойсекции печи → коксовые камеры → фракционирование.
Технологическая схема УЗК. На рис. 5.5 представлена принци-
пиальная технологическая схема нагревательно-реакционно-фрак- ционирующей секции двухблочной установки замедленного коксования. Сырье — гудрон или крекинг-остаток (или их смесь) нагревают в теплообменниках и конвекционных змеевиках печи и направляют на верхнюю каскадную тарелку колонны К-1. Часть сырья подают на нижнюю каскадную тарелку для регулирования коэффициента рисайкла, под нижнюю каскадную тарелку этой колонны — горячие газы
ипарыпродуктовкоксованияизкоксовыхкамер.Врезультатеконтакта сырья с восходящим потоком газов и паров продуктов коксования сырье нагревается (до температуры390…405°С), при этом низкокипящие его фракции испаряются, а тяжелые фракции паров конденсируются
исмешиваются с сырьем, образуя так называемое вторичное сырье.
Рис. 5.5. Принципиальная технологическая схема двухблочной установки замедленного коксования:
I — сырье; II — стабильный бензин; III — легкий газойль; IV — тяжелый газойль; V — головка стабилизации; VI — сухой газ; VII — кокс; VIII — пары отпарки камер; IX — водяной пар
595
vk.com/club152685050 | vk.com/id446425943
ВторичноесырьеснизаколонныК-1забираютпечнымнасосомина- правляют в реакционные змеевики печей (их две, работают параллельно), расположенные в радиантной их части. В печах вторичное сырье нагревается до 490…510°С и поступает через четырехходовые краны двумя параллельными потоками в две работающие камеры; две другие камеры в это время находятся в цикле подготовки. Входя в низ камер, горячее сырье постепенно заполняет их; так как объем камер большой, время пребывания сырья в них также значительно и там происходит крекинг сырья. Пары продуктов коксования непрерывно уходят из камер в колонну К-1, а утяжеленный остаток задерживается в камере. Жидкий остаток постепенно превращается в кокс.
Фракционирующая часть УЗК включает основную ректификационную колонну К-1, отпарные колонны К-2 и К-3, фракционирущий абсорбер К-4 для деэтанизации газов коксования и колонну стабилизации бензина К-5.
КолоннуК-1разделяютполуглухойтарелкойнадвечасти:нижнюю, которая является как бы конденсатором смешения, а не отгонной секциейколонны;иверхнюю,выполняющуюфункциюконцентрационной секции ректификационных колонн. В верхней части К-1 осуществляют разделение продуктов коксования на газ, бензин, легкий и тяжелые газойли. В колонне К-1 температурный режим регулируется верхним острым и промежуточным циркуляционными орошениями. Легкий и тяжелый газойли выводят через отпарные колонны соответственно
К-2 и К-3.
Газы и нестабильный бензин из сепаратора С-1 направляют в фракционирующий абсорбер К-4. В верхнюю часть К-4 подают охлажденный стабильный бензин, в нижнюю часть подводят тепло посредством кипятильника с паровым пространством. С верха К-4 выводят сухой газ, а снизу — насыщенный нестабильный бензин, который подвергают стабилизации в колонне К-5, где от него отгоняют головку, состоящую из пропан-бутановой фракции. Стабильный бензин охлаждают, очищают от сернистых соединений щелочной промывкой и выводят с установки.
Коксовые камеры работают по циклическому графику. В них последовательночередуютсяциклы:коксование,охлаждениекокса,выгрузка его и разогрев камер. Когда камера заполнится примерно на 70…80% по высоте, поток сырья с помощью переключающих кранов переводят в другую камеру. Заполненную коксом камеру продувают водяным паром для удаления жидких продуктов и нефтяных паров. Удаляемые продукты поступают вначале в колоннуК-1. После того как температу-
596
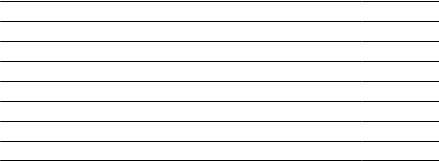
vk.com/club152685050 | vk.com/id446425943
ра кокса понизится до 400…405°С, поток паров отключают от колонны
инаправляютвскруббер(нарисункенепоказан).Водянымпаромкокс охлаждают до 200°С, после чего в камеру подают воду.
После охлаждения кокс из камер выгружают. Для этой операции применяют гидравлический метод. Пласты кокса разрушают струей воды давлением 10…15МПа. Над каждой камерой устанавливают буровые вышки высотой 40 м, предназначенные для подвешивания бурового оборудования. На вышке закрепляют гидродолото, с помощью которого в слое кокса пробуривают центральное отверстие. Затем гидродолото заменяют гидрорезаком, снабженным соплами, из которых подают сильные струи воды, направляемые к стенкам камеры. Гидрорезак перемещается по камере, полностью удаляя со стенок кокс. Далее кокс поступает в отделение внутриустановочной обработки
итранспортировки, где осуществляется дробление, сортировка на три фракции и транспортировка в склады. Ниже приводим типичный цикл работы камер (в ч):
Заполнение камеры сырьем и коксование |
24,0 |
Отключение камеры |
0,5 |
Пропаривание |
2,5 |
Охлаждение водой кокса и слив воды |
4,0 |
Гидравлическая выгрузка кокса |
5,0 |
Закрытие люков и испытание паром |
2,0 |
Разогрев камеры парами нефтепродуктов |
7,0 |
Резервное время |
3,0 |
Итого |
48,0 |
Коксовую камеру, из которой выгружен кокс, спрессовывают и прогревают сначала острым водяным паром, затем горячими парами продуктов коксования из работающей камеры до температуры 360…370°С и после этого переключают в рабочий цикл коксования.
Подготовительные операции УЗК занимают 24…34 ч. В отличие от непрерывных нефтехимических процессов, в реакционных камерах УЗК химические превращения осуществляются в нестационарном режиме с периодическими колебаниями параметров процесса, прежде всего температуры и времени. Продолжительность термолиза в жидкой фазе изменяется от максимального значения с начала заполнения камеры до минимального к моменту переключения на подготовительный цикл. На характер изменения температурного режима по высоте
597
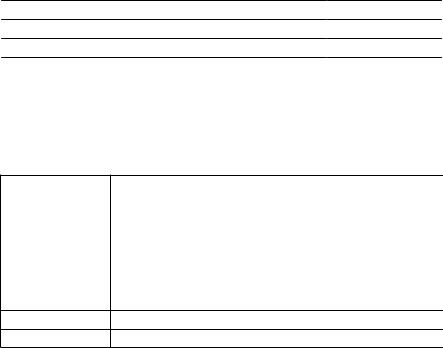
vk.com/club152685050 | vk.com/id446425943
и сечению камеры оказывает влияние эндотермичность суммарного процесса термолиза, а также величина потерь тепла в окружающую среду. Это обстоятельство обусловливает непостоянство качества продуктов коксования по времени, в том числе кокса по высоте камеры. Так,верхнийслойкоксахарактеризуетсявысокойпористостью,низкой механической прочностью и высоким содержанием летучих веществ (т.е. кокс недококсован). Установлено, что наиболее прочный кокс с низким содержанием летучих находится в середине по высоте и сечению камеры.
В модернизированных крупнотоннажных УЗК (типа 21-10/1500) для создания условий, гарантирующих получение стабильного по качествуэлектродногококса,предусмотренподводдополнительноготепла в коксовые камеры в виде паров тяжелого газойля коксования. Для этойцеличастьтяжелогогазойля,отбираемогосаккумулятора К-1,по- сленагревавспециальныхзмеевикахпечидотемпературы 520°Сподаютвкамерывместесовторичнымсырьем.Подачаперегретоготяжелого газойля в камеры продолжается и после прекращения подачи сырья в течение 6 ч.
Технологический режим установки
Температура входа сырья в камеры,°С |
490…510 |
Температура выхода паров из камеры,°С |
440…460 |
Давление в коксовой камере, МПа |
0,18…0,4 |
Коэффициент рециркуляции |
1,2…1,6 |
Втабл.5.5приведенматериальныйбалансУЗКприкоксованииразличных видов сырья.
Таблица 5.5 —
Показатель
Мазут
Полугудрон
Выход продуктов при замедленном коксовании различных видов сырья
|
Качество сырья коксования |
|
Выход на сырье, |
|
|||||||||
|
|
|
|||||||||||
|
|
|
% мас. |
|
|
||||||||
|
|
|
|
|
|
|
|
|
|
|
|
||
Выходсырья, от% нефти |
Плотность, кг/м3 |
Коксуемость,% |
Вязкостьусловная 100при |
Разгонка по |
|
потерииГаз |
Бензин |
Коксовый дистиллят |
Кокс |
|
|||
300при°С |
350при°С |
400при°С |
500при°С |
|
|
||||||||
|
|
|
С ° |
Богданову, пе- |
|
|
|
|
|
|
|||
|
|
|
регоняется,% |
|
|
|
|
|
|
||||
46 |
950 |
9 |
5,2 |
10 |
21 |
— |
— |
|
9,5 |
7,5 |
68 |
15 |
|
40 |
965 |
13 |
6 |
8,5 |
13 |
16 |
46 |
|
10 |
12 |
56 |
22 |
|
|
|
|
|
|
|
|
|
|
|
|
|
|
|
598
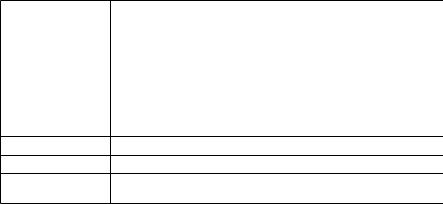
vk.com/club152685050 | vk.com/id446425943
Показатель
Гудрон
Крекинг-остаток
Крекинг-остаток утяжеленный
Продолжение таблицы 5.5
|
Качество сырья коксования |
|
Выход на сырье, |
|
|||||||||
|
|
|
|||||||||||
|
|
|
% мас. |
|
|
||||||||
|
|
|
|
|
|
|
|
|
|
|
|
||
Выходсырья, от% нефти |
Плотность, кг/м3 |
Коксуемость,% |
Вязкостьусловная 100при |
Разгонка по |
|
потерииГаз |
Бензин |
Коксовый дистиллят |
Кокс |
|
|||
300при°С |
350при°С |
400при°С |
500при°С |
|
|
||||||||
|
|
|
С ° |
Богданову, пе- |
|
|
|
|
|
|
|||
|
|
|
регоняется,% |
|
|
|
|
|
|
||||
33 |
990 |
16 |
9 |
1,5 |
5 |
15 |
36 |
|
11 |
16 |
49 |
24 |
|
28 |
1012 |
7,3 |
20 |
8 |
13 |
23 |
56 |
|
13,2 |
6,8 |
49 |
31 |
|
27 |
1024 |
23 |
8,5 |
5 |
11 |
25 |
45 |
|
11 |
7 |
47 |
36 |
|
|
|
|
|
|
|
|
|
|
|
|
|
|
|
5.3.4. Особенности технологии производства игольчатого кокса
Сцельюинтенсификацииэлектросталеплавильныхпроцессоввпоследние годы широко применяют высококачественные графитированные электроды, работающие при высоких удельных токовых нагрузках (30…35Ом/см2).Зарубежныйиотечественныйопытпоказывает,чтополучить такие электроды возможно лишь на основе специального малозольногоималосернистого,такназываемогоигольчатого,кокса.Только игольчатыйкоксможетобеспечитьтакиенеобходимыесвойстваспециальных электродов, как низкий коэффициент термического расширенияивысокаяэлектропроводимость.Потребностиметаллургиивтаких сортах коксов за рубежом и в бывшем СССР непрерывно возрастают.
Игольчатыйкокспосвоимсвойствамсущественноотличаетсяотрядовогоэлектродного:ярковыраженнойанизотропиейволокон,низким содержанием гетеропримесей, высокой удельной плотностью и хорошей графитируемостью.
Наиболеетрадиционноесырьедляпроизводстваигольчатогококса— это малосернистые ароматизированные дистиллятные остатки термического крекинга, газойлей каталитического крекинга, экстрактов масляного производства, тяжелой смолы пиролиза углеводородов, атакжекаменноугольнойсмолы.Аппаратурноеоформлениеустановки коксованиядляполученияигольчатогококсатакоеже,какнаобычных УЗК.Температурныйрежимкоксованияприпроизводствеигольчатого кокса примерно такой же, как при получении рядового кокса, только несколько выше кратность рециркуляции и давление в реакторах. Прокалка игольчатого кокса, по сравнению с рядовым, проводится при более высоких температурах (1400…1500°С).
599
vk.com/club152685050 | vk.com/id446425943
Производство игольчатого кокса требует обязательного наличия на НПЗ установки термического крекинга дистиллятного сырья
иУЗК. Имеющиеся на заводе ароматизированные остатки пропускаютчерезтермическийкрекингподповышеннымдавлением(6…8МПа) с целью дальнейшей ароматизации и повышения коксуемости остатка. Далее дистиллятный крекинг-остаток (ДКО) направляют на УЗК. Из сернистых гудронов ДКО для производства игольчатого кокса можно получить путем термического крекирования гудрона, вакуумной перегонки крекинг-остатка и последующей гидроочисткой тяжелого крекингового вакуумного газойля. Для этой цели можно использовать также процесс деасфальтизации остатков, в частности процесс «Добен»: полученный деасфальтизат далее подвергается гидроочистке
итермическому крекингу дистиллятного сырья.
5.3.5.Процессы получения нефтяных пеков термоконденсацией остатков
В последние годы все более актуальной становится проблема получения заменителя каменноугольного пека, применяющегося во все возрастающих количествах в ряде отраслей промышленности. Острота этой проблемы обусловливается непрерывным ростом дефицита и повышенной канцерогенностью пеков каменноугольного происхождения.
Пекпредставляетсобойбитуминозныйматериалчерногоилибурого цвета с блестящим раковистым изломом. При нормальных условиях — обычно твердое вещество, а при нагревании выше температуры размягчения переходит в вязко-текучее состояние. Пеки в зависимости от применения классифицируются на следующие группы:
I — пеки-связующие,применяемыеприизготовлениисамообжигаю- щихся или обожженных анодов, графитированных электродов, электроугольных изделий и конструкционных материалов на основе графита;
II — пропитывающие;
III— брикетные пеки-связующие (для частичного брикетирования углей перед их коксованием, литейных коксобрикетов, коксобрикетов для цветной металлургии);
IV — волокнообразующие;
V — специальные пеки;
VI — сырье коксования.
Наиболее крупномасштабными потребителями пеков (как и нефтяных коксов) являются производства анодов и графитированнных
600
vk.com/club152685050 | vk.com/id446425943
электродов.Рольпека-связующегоприизготовленииуглеродистыхиз- делийзаключаетсявследующем.Специальноподготовленныйтвердый наполнитель—шихтаизфракцийразличногопомолакоксов—смеши- ваетсявобогреваемомсмесителесопределеннымколичествомсвязующего. Смешение осуществляется в заданное время, в течение которого пек расплавляется, обволакивает тонкой пленкой частицы наполнителя, проникает в его поры, и в конечном итоге образуется углеродная масса. Полученная в переделе смешения масса поступает на передел прессования, где из нее выпрессовываются изделия заданной формы иразмеров.Спрессованныесырые(зеленые)заготовкизатемпроходят передел обжига, в результате чего получаются обожженные изделия определенной формы и размеров. На этой стадии в ряде производств (обожженных анодов, коксобрикетов и др.) заканчивается процесс изготовления yглеродистого изделия. Многие углеродистые изделия (графитированные электроды, конструкционные материалы, электрощетки и др.), кроме стадии обжига, подвергаются еще высокотемпературной графитации и механической обработке. Роль связующего на стадии обжига заключается в создании прочной связи между частицами наполнителя за счет образования кокса из связующего (коксовый мостик). Таким образом, пек при изготовлении углеродистых изделий выполняет две основные функции:
—на переделах смешения и прессования он связывает частицы твердогонаполнителяиобеспечиваетмассеопределенныепластические и прессовые свойства;
—на переделе обжига пек проявляет свои спекающие свойства за счет образования прочной коксовой связи.
Исходя из двух основных технологических функций — связующей
испекающей способности – к пекам предъявляются следующие общие требования: пек в зависимости от назначения должен обладать определенной температурой размягчения, плотностью, вязкостью, коксовым остатком, иметь наиболее удовлетворительный химический состав
иудовлетворятьпотребителяпосодержаниюсеры,зольныхкомпонентов и влаги, а также быть стабильным при хранении, не токсичным
идешевым. При этом спекающая его способность в большей степени оценивается его коксуемостью, коксовым остатком и содержанием α-
иβ-фракций, а связующая способность — преимущественно температурой размягчения, плотностью, вязкостью и содержаниемα-фракций. Нефтеперерабатывающая промышленность располагает широкими сырьевыми ресурсами для производства пеков. В настоящее время во многих странах мира с развитой нефтепереработкой разрабатываются
601

vk.com/club152685050 | vk.com/id446425943
иинтенсивно строятся новые установки по производству нефтяных пеков термоконденсацией ТНО.
Внашейстраненаучно-исследовательскиеработывмасштабелабора- торных,пилотныхиопытно-промышленныхустановоксиспытаниемпо- лученныхобразцовнефтяныхпековупотребителейпроведенывУГНТУ (Л.В. Долматовым, З.И. Сюняевым), БашНИИ НП (И.Р.Хайрутдиновым) совместно со специалистами НПЗ и отраслевых НИИ (ВАМИ, ГосНИИЭП) и др. Разработанные в результате этих работ требования приведенывтабл.5.6.Извсехпродуктоввяжущимииспекающимисвойствами в наибольшей степени обладают нефтяные остатки, ресурсы которых достаточно велики. Так, для получения электродных связующих
ипропитывающихпековнаиболееблагоприятнымсырьемсчитаютсявысокоароматизированные смолы пиролиза и малосернистые дистиллят- ныекрекинг-остатки.Дляполучениябрикетныхсвязующихматериалов, в том числе нефтяных спекающих добавок (НСД), можно использовать недефицитные нефтяные остатки: асфальты деасфальтизации, крекингостаткивисбрекингагудронаидр.Однаковсеониобладаютнизкимизначениямикоксуемости(10…25%мас.поКонрадсону)итемпературойразмягчения,низкимсодержаниемасфальтеновикарбеновипоэтомунемогутбытьиспользованывкачествепековбездополнительнойтермической обработки.Процесстермоконденсациинефтяныхостатковсполучением пеков(пекование)потехнологическимусловиямпроведениявомногом подобентермическомукрекингуивисбрекингу,ноотличаетсяпониженной температурой (360…420°С) и давлением (0,1…0,5 МПа), а по продолжительности термолиза (0,5…10 ч) и аппаратурному оформлению – замедленному коксованию.
Так, на одном из НПЗ (Ново-Уфимском) были проведены опытнопромышленные испытания по получению нефтяного пека и намечена длявнедрениявпроизводствоэтойтехнологииреконструкцияустановкитермическогокрекингагудронасвакуумнойперегонкой(см.рис.5.3) с дооборудованием ее реактором пекованияР-1и трубчатой печью П-3 по схеме (рис. 5.6).
Ниже приводятся данные по выходу продуктов пекования из гудрона 5,% мас.:
газы |
8,5 |
бензин |
15,0 |
суммарный газойль |
40,0 |
пек |
36,5 |
5Данные И.Р.Хайрутдинова и А.Ф.Ишкильдина.
602
vk.com/club152685050 | vk.com/id446425943
Таблица 5.6 — Требования к нефтяным пекам
|
|
Связующие |
|
Брикетные |
|
||||
Показатель |
|
|
|
|
|
|
из ваку- |
|
из кре- |
анодные |
|
электрод- |
пропиты- |
из смолы |
|
ум- |
|
кингового |
|
|
|
|
|
||||||
|
|
|
ные |
вающие |
пиролиза |
|
отогнан- |
|
гудрона и |
|
|
|
|
|
|
|
ного ДКО |
|
асфальта |
Температура раз- |
|
|
|
|
|
|
|
|
|
мягчения,° С |
85±5 |
|
|
|
|
|
|
|
|
по К и С |
|
75…80 |
60…90 |
— |
|
— |
|
— |
|
по К и Ш |
— |
|
— |
— |
50…70 |
|
50…70 |
|
50…70 |
Плотность пик- |
|
|
|
|
|
|
|
|
|
нометрическая, |
|
|
|
|
|
|
|
|
|
кг/м3, не менее |
1250 |
|
— |
— |
— |
|
— |
|
— |
Выход летучих ве- |
|
|
57...60 |
|
|
|
|
|
|
ществ,% мас. |
— |
|
58…64 |
— |
|
70…74 |
|
— |
|
Коксовый оста- |
|
|
|
|
|
|
|
|
|
ток,% мас. |
85 * |
|
— |
— |
25…40 |
|
— |
|
25…35 |
Вязкость при |
|
|
|
|
|
|
|
|
|
140°С, Па·с, |
2,5±5 |
|
— |
— |
— |
|
— |
|
— |
не более |
|
|
|
||||||
|
|
|
|
|
|
|
|
||
Групповой химсо- |
|
|
|
|
|
|
|
|
|
став,% мас. |
|
|
|
|
|
|
|
|
|
γ-фракция |
|
|
|
|
|
|
|
|
|
(мальтены) |
— |
|
— |
— |
50…55 |
|
76…66 |
|
— |
β-фракция |
|
|
|
|
|
|
|
|
|
(асфальтены) |
— |
|
— |
— |
20…25 |
|
22…30 |
|
— |
α2-фракция |
|
|
|
|
|
|
|
|
|
(карбены) |
— |
|
— |
— |
18...22 |
|
— |
|
— |
α1-фракция |
|
|
|
|
|
|
|
|
|
(карбоиды) |
< 4 |
|
— |
— |
0…2 |
|
— |
|
— |
α-фракция |
|
|
|
|
|
|
|
|
|
(карбены+ |
|
|
|
|
|
|
|
|
|
карбоиды) |
> 25 |
|
> 25…25 |
> 17…22 |
— |
|
2…4 |
|
— |
Содержание,% |
|
|
|
|
|
|
|
|
|
мас., |
|
|
|
|
|
|
|
|
|
не более |
|
|
|
|
|
|
|
|
|
серы ** |
1 |
|
— |
— |
— |
|
— |
|
— |
золы |
0,3 |
|
— |
— |
0,5 |
|
0,5 |
|
0,5 |
влаги |
4 |
|
— |
— |
0,5 |
|
0,5 |
|
0,5 |
*По методике ВАМИ.
**Содержание серы в брикетных связующих для плавки чугуна в вагранках — 2,5%, а для плавки руд цветных металлов — не ограничивается.
603