
переработка нефти-1
.pdf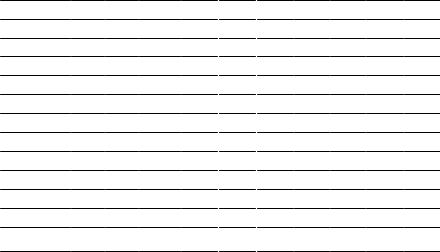
vk.com/club152685050 | vk.com/id446425943
Таблица 3.5 — Состав газов различных процессов
переработки ромашкинской нефти,% мас.
|
|
Газы процессов переработки |
Сжиженные газы |
|||||||||
|
|
|
стабилизации |
|
||||||||
|
|
|
|
|
|
|
|
|
|
|||
Компонент |
|
|
|
ГО |
|
пиро- |
|
|
|
|
|
|
|
АВТ |
|
КР |
дизто- |
ЗК |
КК |
АВТ |
КР |
КК |
|
ЗК |
|
|
|
лиз |
|
|||||||||
|
|
|
|
плива |
|
|
|
|
|
|
|
|
Водород |
– |
|
5,50 |
– |
0,40 |
16,00 |
2,50 |
– |
– |
– |
|
– |
|
|
|
|
|
|
|
|
|
|
|
|
|
Метан |
2,65 |
|
12,50 |
34,00 |
32,50 |
34,40 |
11,00 |
– |
– |
– |
|
– |
Этилен |
– |
|
– |
– |
|
|
|
– |
– |
|
|
3,50 |
|
4,50 |
29,30 |
6,00 |
0,12 |
|
|||||||
Этан |
|
|
|
|
|
|
|
|
|
|
|
5,00 |
13,32 |
|
24,50 |
24,50 |
21,50 |
5,00 |
8,00 |
0,80 |
1,60 |
0,84 |
|
||
Пропилен |
– |
|
– |
– |
|
|
|
– |
– |
|
|
7,50 |
|
4,00 |
10,50 |
22,00 |
23,00 |
|
|||||||
Пропан |
|
|
|
|
|
|
|
|
|
|
|
6,60 |
41,29 |
|
32,00 |
20,50 |
15,00 |
0,20 |
12,50 |
21,70 |
46,90 |
7,89 |
|
||
Изобутилен |
– |
|
– |
– |
|
|
|
– |
– |
|
|
2,15 |
|
2,20 |
1,30 |
6,00 |
19,81 |
|
|||||||
н-Бутилен |
– |
|
– |
– |
|
|
|
– |
– |
|
|
6,60 |
|
4,40 |
1,20 |
14,00 |
18,81 |
|
|||||||
Изобутан |
|
|
|
|
|
– |
|
|
|
|
|
12,90 |
8,02 |
|
11,00 |
21,00 |
7,00 |
14,00 |
14,80 |
26,20 |
17,47 |
|
|||
|
|
|
|
|
|
|
|
|
|
|
|
|
н-Бутан |
24,50 |
14,50 |
– |
8,50 |
0,50 |
4,00 |
48,20 |
21,10 |
4,14 |
|
15,50 |
|
Амилены |
– |
|
– |
– |
– |
– |
– |
– |
– |
|
|
13,25 |
|
3,07 |
|
||||||||||
Изопентан |
|
|
– |
– |
– |
– |
– |
|
|
|
|
2,10 |
5,05 |
|
8,10 |
2,20 |
4,43 |
|
|||||||
н-Пентан |
|
|
– |
– |
– |
– |
– |
|
|
|
|
11,50 |
3,27 |
|
3,50 |
2,00 |
0,90 |
|
|||||||
Гексаны |
1,90 |
|
– |
– |
– |
– |
– |
2,90 |
– |
0,06 |
|
13,00 |
|
|
|||||||||||
и выше |
|
|
||||||||||
|
|
|
|
|
|
|
|
|
|
|
|
|
Примеси |
– |
|
– |
– |
– |
1,50 |
– |
– |
– |
0,09 |
|
0,75 |
Взависимости от химического состава различают предельные
инепредельные газы. Предельные углеводородные газы получаются на установках перегонки нефти и гидрокаталитической переработки (каталитического риформинга, гидроочистки, гидрокрекинга) нефтяного сырья. В состав непредельных газов, получающихся при термодеструктивной и термокаталитической переработке нефтяного сырья (в процессах каталитического крекинга, пиролиза, коксования и др.), входятнизкомолекулярныемоно-,иногдадиолефиныкакнормального, так и изостроения.
Как правило, предельные и непредельные углеводородные газы на НПЗ перерабатываются раздельно вследствие их различного назначения. При фракционировании предельных газов получают следующие узкие углеводородные фракции:
— метан-этановую (сухой газ), иногда этановую, которую используют как сырье пиролиза или в качестве хладоагента на установках глубокой депарафинизации масел и т.д.;
444
vk.com/club152685050 | vk.com/id446425943
—пропановую, используемую как сырье пиролиза, бытовой сжиженный газ и хладоагент для производственных установок;
—изобутановую,являющуюсясырьемустановокалкилирования,производств синтетического каучука;
—бутановуюдляполучениябутадиенаилииспользуемуюкакбытовой сжиженный газ и как компонент автобензинов для регулирования их пусковых свойств;
—изопентановую, которая служит сырьем для производства изопренового каучука и высокооктановым компонентом автобензинов;
—пентановую фракцию – сырье для процессов пиролиза, изомеризации и т.д. Иногда смесь пентанов и более тяжелых углеводородов не разделяют на фракции, а используют как газовый бензин.
На ГФУ непредельных газов из олефинсодержащих потоков выделяются следующие фракции:
—пропан-пропиленовая — сырье процессов полимеризации и алкилирования, нефтехимических производств;
—бутан-бутиленовая–сырьеустановокалкилированиядляпроизводств метилэтилкетона, полиизобутилена, синтетического каучука и др.;
—этан-этиленовая и пентан-амиленовая фракции, используемые как нефтехимическое сырье.
Получаемые на ГФУ фракции углеводородных газов должны по качеству соответствовать техническим условиям на эти нефтепродукты.
До фракционирования углеводородные газы направляются вначале в блоки очистки от сероводорода и осушки.
Нанефте-игазоперерабатывающихзаводахнаибольшеераспростра- нение получили следующие физические процессы разделения углеводородных газов на индивидуальные или узкие технические фракции: конденсация,компрессия,ректификацияиабсорбция.НаГФУэтипроцессы комбинируются в различных сочетаниях.
Компрессияиконденсация—процессысжатиягазакомпрессорами иохлажденияеговхолодильникахсобразованиемдвухфазнойсистемы газа и жидкости. С повышением давления и понижением температуры выход жидкой фазы возрастает, причем сконденсировавшиеся углеводороды облегчают переход легких компонентов в жидкое состояние, растворяя их. Обычно применяют многоступенчатые (2, 3 и более) системы компрессии и охлаждения, используя в качестве хладоагентов воду, воздух, испаряющиеся аммиак, пропан или этан. Разделение сжатых и охлажденных газов осуществляют в газосепараторах, откуда конденсат и газ направляют на дальнейшее фракционирование методами ректификации или абсорбции.
445
vk.com/club152685050 | vk.com/id446425943
Абсорбция — процесс разделения газовых смесей, основанный на избирательном поглощении отдельных компонентов сырья жидким поглотителем — абсорбентом. Растворимость углеводородов в абсорбенте возрастает с повышением давления, ростом молекулярной массы
ипонижением температуры процесса ниже критической температуры абсорбируемого газа.
Абсорбция — обратимый процесс, и на этом основано выделение поглощенного газа из жидкости — десорбция. Сочетание абсорбции с десорбцией позволяет многократно применять поглотитель и выделять из него поглощенный компонент. Для десорбции благоприятны условия, противоположные тем, при которых проводят абсорбцию, то есть повышенная температура и низкое давление. Наилучшим абсорбентом для углеводородных газов являются близкие им по строению
имолекулярноймассежидкиеуглеводороды,напримербензиноваяили керосиновая фракции.
Ректификацияявляется завершающей стадией разделения углеводородныхгазов.Особенностьректификациисжиженныхгазов,посравнению с ректификацией нефтяных фракций, – необходимость разделения очень близких по температуре кипения компонентов или фракций сырья при высокой четкости фракционирования. Так, разница между температурамикипенияэтанаиэтиленасоставляет15°С.Наиболеетрудно разделить бутан-бутиленовую фракцию: температура кипения изо- бутанапринормальномдавлениисоставляет11,7°С,изобутилена—6,9,
бутена — 1…6,29, а н-бутана — 0,5.
Ректификацию сжиженных газов приходится проводить при повышенных давлениях в колоннах, поскольку для создания жидкостного орошения необходимо сконденсировать верхние продукты колонн в обычных воздушных и водяных холодильниках, не прибегая к искусственному холоду.
Конкретныйвыборсхемы(последовательности)разделения,температуры, давления и числа тарелок в колоннах определяется составом исходной газовой смеси, требуемой чистотой и заданным ассортиментом получаемых продуктов.
На НПЗ для разделения нефтезаводских газов применяются преимущественно 2 типа газофракционирующих установок, в каждый из которыхвходятблокикомпрессиииконденсации:ректификационный— сокращенно ГФУ и абсорбционно-ректификационный — АГФУ. На рис. 3.22 и 3.23 приведены принципиальные схемы ГФУ для разделения предельных газов и АГФУ для фракционирования жирного газа
истабилизации бензина каталитического крекинга (на схемах не пока-
446
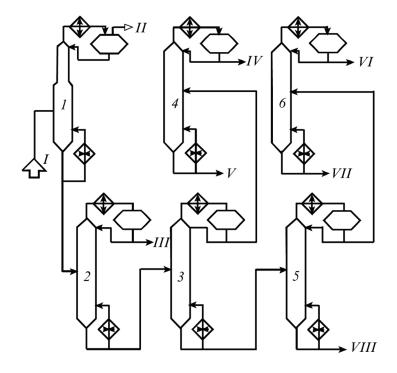
vk.com/club152685050 | vk.com/id446425943
заны блоки сероочистки, осушки, компрессии и конденсации). В блоке ректификации ГФУ (рис. 3.22) из углеводородного газового сырья сначала в деэтанизаторе 1 извлекают сухой газ, состоящий из метана
иэтана. На верху колонны 1 поддерживают низкую температуру пода- чейорошения,охлаждаемоговаммиачномконденсаторе-холодильнике. Кубовый остаток деэтанизатора поступает в пропановую колонну 2, где разделяетсянапропановуюфракцию,выводимуюсверхаэтойколонны,
исмесь углеводородов С4 и выше, направляемую в бутановую колонну 3. Ректификатом этой колонны является смесь бутанов, которая в изобутановой колонне 4 разделяется на изобутановую и бутановую фракции. Кубовый продукт колонны 3подается далее в пентановую колонну 5, где в виде верхнего ректификата выводится смесь пентанов, которая визопентановойколонне6разделяетсянан-пентаниизопентан.Нижний продукт колонны 5 — фракция С6 и выше — выводится с установки.
Рис. 3.22. Принципиальная схема газофракционирующей установки (ГФУ):
1 — деэтанизатор; 2 — пропановая колонна; 3 — бутановая колонна; 4 — изобутановая колонна; 5 — пентановая колонна; 6 — изопентановая колонна; I — сырье; II — сухой газ; III — пропановая фракция; IV — изобутановая фракция; V — бутановая фракция; VI — изопентановая фракция; VII — пентановая фракция; VIII — фракция С6 и выше
447
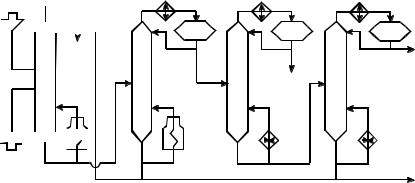
vk.com/club152685050 | vk.com/id446425943
|
|
|
|
Рис. 3.23. Принципиальная схема абсорбционно-газофункционирующей установки (АГФУ):
1—фракционирующийабсорбер;2—стабилизационнаяколонна;3—пропановаяколонна;4—бу- тановая колонна; I — очищенный жирный газ; II — нестабильный бензин; III — сухой газ; IV — пропанпропиленовая фракция; V — бутан-бутиленовая фракция; VI — стабильный бензин
Для деэтанизации газов каталитического крекинга на установках АГФУ (рис. 3.23) используется фракционирующий абсорбер 1. Он представляет собой комбинированную колонну абсорбер–десорбер.
Вверхней части фракционирующего абсорбера происходит абсорбция,
тоестьпоглощениеизгазовцелевыхкомпонентов(С3 ивыше),авнижней — частичная регенерация абсорбента за счет подводимого тепла.
ВкачествеосновногоабсорбентанаАГФУиспользуетсянестабильный бензин каталитического крекинга. Для доабсорбции унесенных сухим газом бензиновых фракций в верхнюю часть фракционирующего абсорбера подается стабилизированный (в колонне 4) бензин. Абсорбер оборудован системой циркуляционных орошений для съема тепла абсорбции (на рис. 3.23 не показана). Тепло в низ абсорбера подается с помощью «горячей струи». С верха фракционирующего абсорбера 1
выводится сухой газ (С1–С2), а с низа вместе с тощим абсорбентом выводятся углеводороды С3 и выше. Деэтанизированный бензин, насыщенный углеводородами С3 и выше, после подогрева в теплообменнике подается в стабилизационную колонну 2, нижним продуктом которого является стабильный бензин, а верхним — головка стабилизации. Из нее (иногда после сероочистки) в пропановой колонне 3 выделяют пропан-пропиленовую фракцию. Кубовый продукт пропановой колонны разделяется в бутановой колонне 4 на бутан-бути-
леновую фракцию и остаток (С5 и выше), который объединяется со стабильным бензином.
Втабл. 3.6 и 3.7 приведен технологический режим ректификационных колонн установок ГФУ и АГФУ.
448
vk.com/club152685050 | vk.com/id446425943
Таблица 3.6 — |
Технологический режим колонн ГФУ |
|
|||
|
|
|
|
|
|
Ректификационная колонна* |
Давление, МПа |
Температура,°С |
|||
|
|
||||
верха |
низа |
||||
|
|
|
|||
|
|
|
|
|
|
Деэтанизатор (1) |
|
2,6...2,8 |
25...30 |
110...115 |
|
|
|
|
|
|
|
Пропановая (2) |
|
1,2...1,4 |
62...68 |
145...155 |
|
|
|
|
|
|
|
Бутановая(3) |
|
2,0...2,2 |
58...65 |
110...115 |
|
|
|
|
|
|
|
Изобутановая (4) |
|
1,0...1,2 |
65...70 |
80...85 |
|
|
|
|
|
|
|
Пентановая (5) |
|
0,3...0,4 |
75...80 |
120...125 |
|
Изопентановая (6) |
|
0,35...0,45 |
78...85 |
95...100 |
* Общее число тарелок — от 390 до 720. |
|
|
|
|||
Таблица 3.7 — |
Технологический режим колонн АГФУ |
|
||||
|
|
|
|
|
|
|
Параметр |
|
|
Ректификационные колонны |
|
||
|
|
|
|
|
|
|
|
1 |
2 |
3 |
|
4 |
|
|
|
|
||||
Давление, МПа |
|
1,35 |
0,93 |
1,73 |
|
0,59 |
Температура,°С: |
|
|
|
|
|
|
|
|
|
|
|
|
|
верха |
|
35 |
78 |
44 |
|
48 |
|
|
|
|
|
|
|
питания |
|
40 |
150 |
86 |
|
61 |
|
|
|
|
|
|
|
низа |
|
130 |
218 |
107 |
|
106 |
|
|
|
|
|
|
|
Число тарелок |
|
60 |
60 |
60 |
|
60 |
|
|
|
|
|
|
|
Флегмовое число |
|
— |
2 |
3 |
|
3 |
|
|
|
|
|
|
|
Известно, что затраты при ректификации определяются преимущественно флегмовым числом и числом тарелок в колонне. Для близкокипящих компонентов с малой относительной летучестью эти параметры особенно велики. Поэтому из общих капитальных и эксплуатационных затрат на газофракционирование существенная (около половины) часть приходится на разделение фракций i-С4–н-С4 и i-С5–н-С5. В этой связи на НПЗ часто ограничиваются фракционированием предельных газов без разделения фракций С4 и выше.
3.4. Оборудование электрообессоливающих установок
На нефтеперерабатывающих заводах Российской федерации в настоящее время эксплуатируется около 100 электрообессоливающих установок(ЭЛОУ)трехосновныхтиповвзависимостиоттипаэлектродегидраторов и их связи с нефтеперегонными установками.
449
vk.com/club152685050 | vk.com/id446425943
Первыйтип—отдельностоящиеЭЛОУ,построенныев1940–1950гг. мощностью 0,6…1,2 млн т/год. Обессоливание нефти осуществляют
водну-две электрические ступени в 12 вертикальных электродегидраторах объемом по 30 м3 каждый. Нефть нагревается водяным паром. ТакиеЭЛОУнесвязаныжесткосАВТ,поэтомунефтьпослеподготовки охлаждают и сбрасывают в резервуар, откуда она сырьевым насосом АВТ подается на перегонку.
Второй тип — двухступенчатые ЭЛОУ производительностью 2…3млнт/год, обычно комбинированные с установками АТ или АВТ. В их состав входят шаровые электродегидраторы объемом 600м3 по одному аппарату в ступени. В большинстве случаев нефть подогревается за счет тепла продуктов перегонки нефти, а обессоленная нефть не охлаждается и, минуя промежуточный резервуар, поступает на прием сырьевого насоса АВТ.
Третий тип — двухили трехступенчатые блоки ЭЛОУ, комбинированные с АТ или АВТ с горизонтальными электродегидраторами, расчитанные на давление до 1,8 МПа и температуру до 160°С. В отличие от второго типа здесь отсутствует сырьевой насос. Такие блоки входят
всостав установок ЭЛОУ-АВТ или АТ мощностью 3…9 млн т/год. Характеристика электродегидраторов приведена в табл. 3.8.
Вертикальные электродегидраторы вследствие их малого объема устанавливают параллельно по 6…12 аппаратов, что усложняет их обслуживание и затрудняет равномерное распределение потоков нефти и воды.
Шаровые электродегидраторы имеют значительно больший объем, но низкое расчетное давление (0,6…0,7 МПа) в них препятствует осуществлению их жесткой связи с перегонными установками. Даже при таком давлении, учитывая большой их диаметр, толщина стенки корпуса составляет 24мм. Кроме этого, из-за больших габаритов возникают транспортные проблемы при их доставке. Поэтому их сборку и монтаж осуществляют на месте из отдельных сегментов.
Шаровойэлектродегидраторпоказаннарисунке3.24.Внемимеется трисырьевыхвводаисоответственнотрипарыэлектродов.Расстояние между верхним и нижним электродами 150 мм. Перед входом в первую ступень нефть смешивается с водой непосредственно в трубопроводе. Количествоподаваемойводысоставляет 10…25%.Водавобразованной эмульсиирастворяетсоли.Далеечастичнообессоленнаянефтьпоступает вовторуюступень,попутивкоторуюсмешиваетсясводнойпромывкой. Вовторойступенипроисходитокончательноеобезвоживаниеиобессоливание.Дляобессоливаниятяжелойнефтиприменяюттретьюступень
450

Таблица 3.8 — |
Характеристика электродегидраторов |
|
|
|
|||
|
|
|
|
|
|
|
|
|
|
|
|
Тип электродегидратора |
|
|
|
|
|
|
|
|
|
|
|
|
|
верти- |
шаровой |
горизонталь- |
|
|
|
|
|
кальный |
ный |
|
|
|
|
Показатель |
|
|
|
|
|
||
|
|
|
|
|
|
|
|
|
|
|
2ЭГ160 |
2ЭГ160/3 |
2ЭГ160-2 |
2ЭГ200-2Р |
|
|
|
|
|
||||
|
|
|
|
(1ЭГ160) |
|||
|
|
|
|
|
|
|
|
|
|
|
|
|
|
|
|
Объем, м3 |
|
30 |
600 |
160 |
160 |
160 |
200 |
Диаметр, м |
|
3 |
10,5 |
3,4 |
3,4 |
3,4 |
3,4 |
|
|
|
|
|
|
|
|
Длина (высота), м |
|
5 |
— |
18,6 |
18,6 |
18,6 |
23,4 |
|
|
|
|
|
|
|
|
Расчетное давление, МПа |
0,4…0,6 |
0,6…0,7 |
1,8(1,0) |
1,8 |
1,8 |
1,8 |
|
|
|
|
|
|
|
|
|
Рабочая температура, °С |
90 |
100 |
160 |
160 |
160 |
160 |
|
|
|
|
|
|
|
|
|
Число электродов |
|
2 |
3 пары |
2 |
3 |
3 |
3 |
Система ввода нефти |
В зону между |
В зону между |
В подэлектрод- |
В зону между |
Совместно в зону |
Раздельно взону |
|
|
|
электродами |
электродами |
ную зону |
нижнимисред- |
между нижним и |
между нижним и |
|
|
|
|
|
ним электрода- |
средним электро- |
среднимэлектро- |
|
|
|
|
|
ми |
дами и подэлек- |
дами и подэлек- |
|
|
|
|
|
|
тродную зону |
тродную зону |
|
|
|
|
|
|
|
|
com/id446425943.vk | com/club152685050.vk
451
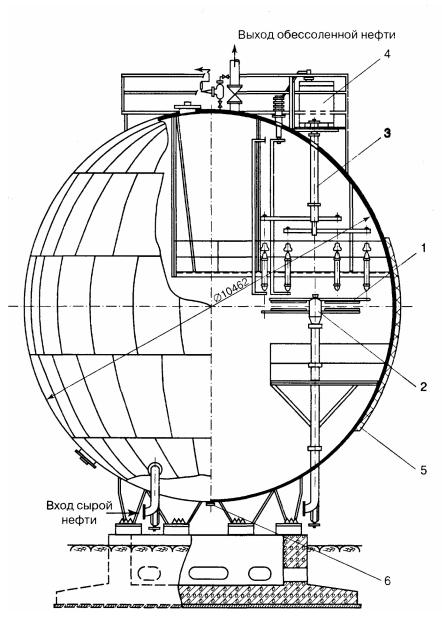
vk.com/club152685050 | vk.com/id446425943
Рис. 3.24. Шаровой электродегидратор емкостью 600 м3:
1 — электроды; 2 — распределительная головка; 3 — устройство для регулирования расстояния между электродами; 4 – трансформатор; 5 – теплоизоляция; 6 — штуцер
452
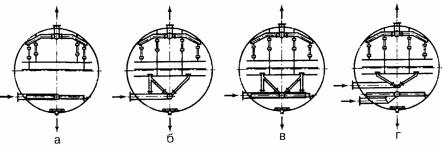
vk.com/club152685050 | vk.com/id446425943
Современные блоки ЭЛОУ комплектуются высокоэффективными горизонтальными электродегидраторами, работающими под давлением 1,8МПа и скомбинированные с установками АВТ и АТ. Горизонтальные электродегидраторы, перечисленные в таблице 3.8, имеют конструктивныеотличияпочислуирасположениюэлектродовиместу ввода нефти. На рис. 3.25 приведены их модификации, а на рис. 3.26 представлен поперечный разрез типового электродегидратора типа ЭГ.
Для смешения нефти с водой и деэмульгатором применяют смесители различных конструкций. Наиболее распространенным является смесительныйклапан,которыйпозволяетрегулироватьинтенсивность перемешивания воды с нефтью в широких пределах. Недостатком его является то, что смешение осуществляется за счет перепада давления на потоке нефти, изменяющегося от 0,05 до 0,2 МПа. Этого недостатка лишен тангенциальный смеситель, показанный на рисунке 3.27. Он устанавливается в технологическом трубопроводе и представляет собой цилиндрическую смесительную камеру с конфузорами на входе и выходе. Степень смешения регулируется перепадом давления на линии подачи воды. Перепад давлений на линии нефти не превышает
0,01 МПа.
Кроме электродегидраторов на установках ЭЛОУ используется различное технологическое оборудование – теплообменные аппараты, промежуточныеемкости,запорно-регулирующаяипредохранительная арматура, насосные агрегаты, а также электротехническое оборудование (трансформаторы, реактивные катушки и др.).
От степени подготовки нефти для ее дальнейшей переработки во многом зависит надежность работы технологического оборудования, эксплуатируемого в условиях более высоких давлений и температур.
Рис. 3.25. Модификации горизонтальных электродегидраторов:
а — 2ЭГ160; б — 2ЭГ160/3; в — 2ЭГ160-2; г — 2ЭГ160-2М
453