
переработка нефти-1
.pdfvk.com/club152685050 | vk.com/id446425943
В одноступенчатых нагнетателях всасывающие патрубки часто располагают вдоль оси машины, обеспечивая равномерный осевой подвод газа к рабочему колесу.
Корпуса воздушных машин изготовляют из чугуна, толщина стенок
взависимости от размеров и давления составляет 15...30 мм, толщина фланцев в 1,3...1,5 раза больше толщины стенок.
Рабочие колеса многоступенчатых компрессоров в большинстве случаев радиального типа с покрывными дисками (рис. 2.219 и 2.221);
водноступенчатых нагнетателях применяют как радиальные, так и осерадиальные колеса (последние чаще без покрывного диска) с фрезерованными лопатками. Лопатки радиальных колес также часто выполняют фрезерованными из основного диска; покрывной диск крепят шипами,сделанныминалопатках,или заклепками, проходящими через лопатки и основной диск. Толщина заклепок 3...8 мм, шаг 25...50 мм.
Рабочие колеса центробежных многоступенчатых компрессоров (ЦКМ)изготовляютизлегированныхсталей(34ХН1М,34ХНЗМидр.), легкихсплавовнаосновеалюминия(АК6,АК8,Д16)ититана.Допустимая окружная скорость для колес стационарных ЦКМ, изготовленных излегированныхсталей,300...320,изалюминиевыхититановыхсплавов
400...450 м/с.
Вавиационных нагнетателях для осерадиальных колес без покрывных дисков с радиальными лопатками на выходе, изготовленных из специальных сталей, допускается окружная скорость 500...550 м/с. Допустимые окружные скорости для литых колес — до 250 м/с.
Валы изготовляют из углеродистых сталей 35, 40, 45; колеса насаживают на вал с натягом после разогрева в электропечах до температуры
450...470 К.
ВкачествеопорстационарныхЦКМприменяютподшипникискольжения;вавиационныхнагнетателяхивнекоторыхсерияхвентиляторов наряду с подшипниками скольжения применяют подшипники качения. Последние проще в эксплуатации, однако менее долговечны. Кроме того, подшипники скольжения, которые смазывают маслом, обладают значительнобольшейдемпфирующейспособностью,чтоособенноважно для гибких валов. Один из подшипников делают опорно-упорным, другой опорным. Температура подшипников не должна превышать 65...70°С; ее контролируют ртутными термометрами, реже терморезисторами. Корпусы подшипников скольжения в большинстве случаев отливают заодно с нижней половиной корпуса машины, крышки делают отдельно, чтобы подшипник можно было вскрыть не поднимая верхней половины корпуса машины.
314
vk.com/club152685050 | vk.com/id446425943
Диффузоры в основном изготовляют в виде общего неподвижного элемента, который называется диафрагмой. В машинах, имеющих горизонтальный разъем, диафрагма также имеет разъем. Диафрагмы делают из чугуна. В целях уменьшения перетока газа между вращающимися частями и неподвижными элементами устанавливают лабиринтные уплотнения на покрывных дисках колес и на уплотнительных втулках между колесами; за последней ступенью часто помещают разгрузочный поршень,навнешнейповерхностикотороготакженаходитсялабиринтное уплотнение.
Для предотвращения утечек вредных для окружающей среды газов (аммиак, природный газ, фреон и др.) корпус делается герметичным: перед выходом вала из корпуса устанавливают сальник. Он может быть выполнен в виде графитового торцового уплотнения с масляной камерой.
Число ступеней в одном корпусе компрессора обычно не превышает восьми. Ограничение числа колес связано с возрастанием прогиба вала, так как его длина увеличивается, а диаметр вала ограничен конструктивными соображениями, прежде всего размерами колес.
Охлаждениеприменяютглавнымобразомвнешнее—впромежуточ- ных охладителях; внутреннее охлаждение используют в случаях, когда нежелательновыпадениевлагиизсжимаемогогаза.Иногдаиспользуют охлаждение впрыском, однако при этом возникает опасность коррозии и эрозии. Промежуточный охладитель обычно выполняют в виде кожухотрубного аппарата, по межтрубному пространству которого идет газ, а по трубкам вода. Для улучшения теплообмена вода делает один или несколько ходов, газ движется поперек трубок.
Трубки диаметром 10...20 мм изготовляют из меди, латуни, а при газах, вызывающих коррозию,применяютлегированнуюсталь.Эффективны охладители с оребренными трубками; ребра латунные, медные, алюминиевые или стальные. Скорость воды в трубках 1...3 м/с, подогревводывпределах6...12°С.Корпусохладителявыполняетсясварным или литым из чугуна.
Фирма «Броун-Вовери» (Швейцария) выпускала ЦКМ с охлаждением газа после каждой ступени, что приближает процесс сжатия к изотермному и повышает КПД машины (рис. 2.222). Охлаждение осуществляется в трубчатых охладителях, расположенных над компрессором и под ним. Такие конструкции иногда называют изотермкомпрессорами. Осевое усилие воспринимается разгрузочным поршнем и упорным подшипником. Для регулирования расхода газа установлен направляющий аппарат с поворотными лопатками.
315
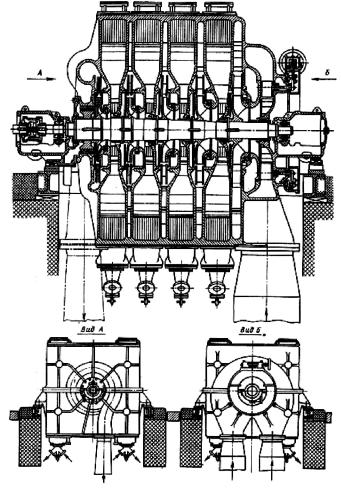
vk.com/club152685050 | vk.com/id446425943
Рис. 2.221. Центробежный компрессор фирмы «Броун-Бовери»
Компрессоры рассмотренного типа выпускают на расходы воздуха
25000...200000м3/ч при степени сжатия 6,5...8.
В компрессоростроении широко развита унификация узлов и деталей, что снижает трудоемкость изготовления и стоимость машин. Так, в СКБК разработаны восемь баз для конструирования ЦКМ на различные рабочие давления. Каждая база характеризуется определенным диаметром рабочих колес и может включать конструкции корпусов с горизонтальным или вертикальным разъемом.
Например,уагрегататретьейбазыдиаметррабочихколес380мм,корпусы агрегатов с горизонтальным разъемом предназначены для макси-
316
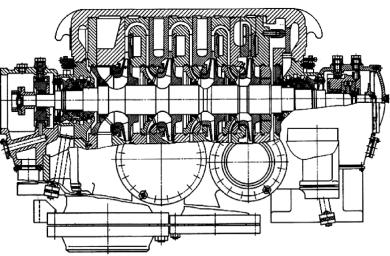
vk.com/club152685050 | vk.com/id446425943
мального рабочего давления 4МПа, корпус с вертикальным разъемом – для давления 38МПа. На этой базе в СКБК разработан однокорпусный азотныйагрегатЗЦКК-160/6мощностью1250кВт,однокорпусныйвоз- душный агрегат ЗВЦ 1-95/6-28 мощностью 3150кВт, двухкорпусный фреоновый агрегат 33 ЦКК-105/1,8-8 мощностью 500кВт. Корпусы этой базы используют в двух- и трехкорпусных кислородных агрегатах
43ЦКК-250/15,543ЦКК400/40,543ЦК2440/35,углеводородныхагре- гатах 43 ЦКО-160/15.
На рис. 2.222 показан продольный разрез одного корпуса компрессорасгоризонтальнымразъемом,вкоторомрасположенычетыреступени сжатия. Для машины с рабочим давлением 1МПа корпус изготовляют из чугуна, для давления 4МПа — из стали. Рабочий газ проходит последовательно через всасывающую камеру, рабочее колесо, диффузор и через направляющий аппарат поступает во 2-ю ступень компрессора. Привод компрессора осуществляется электродвигателем с частотой вращения 18000 мин–1.
Основными элементами конструкции являются корпус с подводящими коммуникациями, ротор и узлы подшипников скольжения с жидкостной смазкой маслом. Внутри корпуса расположены диафрагмы, несущие лопатки диффузоров и направляющие аппараты промежуточных ступеней. Диффузоры с фрезерованными лопатками выполнены из стали марки 12Х18Н9Т или стали 20. Литые направляющие аппараты изготовлены из медистого чугуна с последующим старением. Проставки и диафрагмы выполнены из стали 20.
Рис. 2.222. Унифицированный 4-ступенчатый корпус центробежного компрессора СКБК
317
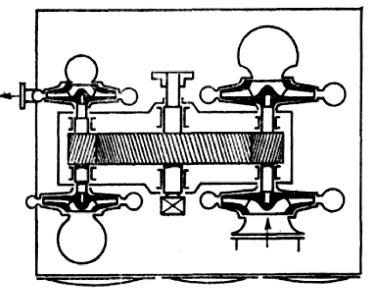
vk.com/club152685050 | vk.com/id446425943
Между ступенями расположены лабиринтные уплотнения с латунной (Л63) или алюминиевой (Д1) втулкой и одиннадцатью гребнями.
Роторсостоитизвала(сталь40Х),накоторомспомощьюустановочных винтов закреплены четыре рабочих колеса. Колеса всех ступеней изготовлены из легированной стали с фрезерованными на основном диске лопатками. Покрывной диск припаивают к основному припоем ПЖК-1000. Возможно изготовление колес со штампованными лопатками, припаянными к основному и покрывному дискам. Число рабочих лопаток варьируется в зависимости от типа агрегата. После пайки все колеса подвергают дефектоскопии и статической балансировке, а ротор после сборки вала с рабочими колесами – динамической балансировке.
Ротор опирается на два гидродинамических подшипника скольжения с самоустанавливающимися подушками. Смазка — жидкостная маслом. Корпус и вкладыши подшипника выполнены из стали 20. Рабочие поверхности покрыты баббитом Б83. Для предотвращения утечек рабочего газа и его загрязнения маслом между подшипниками ипроточнойчастьюмашиныустановленымасляныеловушкииобоймы уплотнения.
Представляет интерес конструкция четырехступенчатого компрессора фирмы «Демаг», имеющая два ротора, вращающиеся с разной частотой, и внешние перепуски газа из ступени в ступень (рис. 2.223).
Рис. 2.223. Схема двухроторного четырехступенчатого нагнетателя фиры «Демаг» (Германия)
318
vk.com/club152685050 | vk.com/id446425943
2.8.Конструкционные материалы, применяемые для изготовления оборудования нефтегазопереработки
2.8.1.Требования, предъявляемые к конструкционным материалам
для технологической аппаратуры и их выбор
Специфические условия работы технологической аппаратуры, характеризуемые диапазоном давлений от глубокого разрежения (вакуума) до избыточных давлений порядка 250МПа и выше, большим интервалом рабочих температур (от –254 до +1000°С и выше) при агрессивном воздействии среды, предъявляют высокие требования к выбору конструкционных материалов проектируемой аппаратуры.
Нарядусобычнымитребованиямивысокойкоррозионнойстойкости
вопределенных агрессивных средах к конструкционным материалам, применяемым в технологическом аппаратостроении, одновременно предъявляются также требования высокой механической прочности, жаростойкости и жаропрочности, сохранения удовлетворительных пластических свойств при высоких и низких температурах, устойчивости при знакопеременных или повторных однозначных нагрузках (циклической прочности), малой склонности к старению и др.
Врасчетах на прочность технологической аппаратуры конструктору часто приходится учитывать общую равномерную по поверхности коррозию металлов и сплавов, для чего необходимо знать проницаемость материала в мм/год при заданных рабочих условиях агрессивной среды (концентрация, температура, давление). Она учитывается при выборе величины прибавки на коррозию к рассчитанной толщине стенки аппарата. В ряде случаев при конструировании технологической аппаратуры необходимо учитывать также и другие виды коррозионного разрушения материалов. Например, в химических аппаратах, выполненных из кислотостойкой стали и находящихся под постоянным повышенным давлением, при совместном действии коррозионной среды и растягивающих напряжений в ряде случаев наблюдается коррозионное растрескивание металла, происходящее обычно внезапно без видимых изменений материала. Это явление не имеет места при наличии
вметалле напряжений сжатия. Кроме того, коррозионное растрескивание происходит в небольшом количестве агрессивных сред и зависит от величины давления и температуры. Известно, что ускоренное растрескивание аппаратуры из кислостойких сталей, находящейся под постоянно действующей нагрузкой, имеет место в растворах NaCl, MgCl2,
319
vk.com/club152685050 | vk.com/id446425943
ZnCI2,LiCL,H2S,морскойводеит.д.Латуниобнаруживаютсклонность к коррозионному растрескиванию в среде аммиака.
Для технологической аппаратуры химических и нефтехимических производств преимущественно применяются конструкционные материалы, стойкие и весьма стойкие в агрессивных средах. Материалы пониженной стойкости применяются в исключительных случаях, когда доказана целесообразность использования их вместо стойких, но более дорогих и дефицитных материалов.
При выборе материалов для аппаратов, работающих под давлением при низких и высоких температурах, необходимо учитывать, что механические свойства материалов существенно изменяются в зависимости от температуры. Как правило, прочностные свойства металлов и сплавов повышаются при низких температурах и понижаются при высоких.
Пристатическомприложениинагрузкиважнымихарактеристиками для оценки прочности материала являются предел текучести σТ (или условный предел текучести σ0,2 или σ1,0) и предел прочности σВ. Упругие свойства металлов характеризуются значениями модуля упругости Е и коэффициентом Пуассона µ.
Указанные характеристики являются основными при расчетах на прочность деталей аппаратуры, работающей под давлением при низких (от –40 до –254°С), средних (от +200 до –40°С) и высоких (выше +200°С) температурах.
Для работы при низких температурах по нормам Госгортехнадзора следуетвыбиратьметаллы,укоторыхпорогхладоломкостилежитниже заданнойрабочейтемпературы.Однаковхимическойпромышленности на протяжении многих лет безаварийно эксплуатируется при рабочих температурах до –40°С большое количество аппаратов, трубопроводов, арматуры, насосов и другого оборудования, изготовленных из углеродистой стали обыкновенного качества и из серого или ковкого чугуна, т.е. из материалов, имеющих ударную вязкость KCU при указанной температуре менее 2 Дж/см2.
Поэтому при выборе металла для работы при низких температурах следует исходить не только из величины ударной вязкости, но также учитывать величину и характер приложенной нагрузки (статическая, динамическая, пульсирующая),наличие и характерконцентраторовнапряжений и чувствительность металла к надрезам, начальные напряжения в конструкции, способ охлаждения металла (за счет содержащегося в аппарате хладоносителя или за счет окружающей среды).
При статическом приложении нагрузки в ряде случаев допускается изготовление аппаратов из металлов, приобретающих хрупкость при
320
vk.com/club152685050 | vk.com/id446425943
пониженныхрабочихтемпературах,нонеимеющихдефектов,нарушающих однородность структуры и способствующих концентрации напряжений. Технология изготовления аппаратов из таких материалов должна исключать возможность возникновения высоких начальных напряжений в конструкции. К таким аппаратам можно отнести свободно опирающиеся емкости для жидких и газообразных продуктов, содержащихся в них под небольшим избыточным давлением, металлоконструкции неответственного назначения и др.
При динамическом приложении нагрузки кроме указанных выше характеристик необходимо учитывать также и величину ударной вязкости аН. Для многих углеродистых и легированных сталей ударная вязкость при низких температурах (обычно ниже –10°С) резко понижается, что исключает применение этих материалов в таких условиях. Ударная вязкость для большинства цветных металлов и сплавов (медь
иее сплавы, алюминий и его сплавы, никель и его сплавы), а также хромоникелевых сталей аустенитного класса при низких температураx, как правило, уменьшается незначительно и пластические свойства этих материалов сохраняются на достаточно высоком уровне, что и позволяет применять их при рабочих температурах порядка до –254°С.
Для оборудования, подверженного ударным или пульсирующим нагрузкам и предназначенного для работы при низких температурах, следует применять металлы и сплавы с ударной вязкостью KCU не ниже 3 Дж/см2 при рабочих температурах. Для деталей, имеющих концентраторы напряжений (болты, шпильки), рекомендуются материалы, у которых при рабочей температуре величина ударной вязкости KCU не менее 4Дж/см2.
При высокой температуре наблюдается значительное снижение основных показателей, характеризующих прочностные свойства металлов и сплавов. Кроме того, поведение металлов под нагрузкой при высоких температурах резко отличается от их поведения при нормальной температуре внутри производственных помещений. Предел прочности
ипредел текучести зависят от времени пребывания под нагрузкой
искорости нагружения, так как с повышением температуры металл из упругого состояния переходит в упругопластическое и под нагрузкой непрерывно деформируется (явление ползучести). Температуры, при которыхначинаетсяползучесть,уразныхметалловразличны.Дляуглеродистых сталей обыкновенного качества ползучесть наступает уже при температурах выше 375°С, для низколегированных сталей — при температурах выше 525°С, для жаропрочных— при еще более высоких температурах.
321
vk.com/club152685050 | vk.com/id446425943
Сувеличениемвременипребыванияметаллаподнагрузкойхарактеристики прочности уменьшаются тем значительнее, чем выше температураэксплуатацииоборудования.Поэтомуприрасчетенапрочностьаппаратов, работающих длительное время при высоких температурах, допускаемыенапряженияопределяютпоотношениюкусловномупределу ползучести от или по пределу длительной прочности. Для химической аппаратуры допускаемая скорость ползучести принимается в пределах 7...10мм/мм ч (5...10% в год), для крепежных деталей — 9...10мм/мм ч
(7...10% в год).
Понижение механических свойств при высоких температурах обусловлено происходящими в металле структурными и фазовыми превращениями. К структурным изменениям такого рода можно отнести явление графитизации углеродистой и молибденовой сталей, образование ферритной фазы в хромоникелевых сталях и др., присущие последним при длительной работе металла в условиях высокой температуры. В ряде случаев стабильность структуры стали в течение длительного срока службы оборудования удается обеспечить путем термической обработки стали. В большинстве случаев для аппаратуры, предназначенной для работы при высоких температурах, применяются специальные марки жаропрочных сталей, характеризуемых достаточной механической прочностью и стабильностью структуры при высоких температурах.Нарядусжаропрочностьюэтиметаллыдолжныобладать жаростойкостью, т.е. способностью противостоять коррозионному воздействию среды в условиях длительной работы материала при высоких температурах.Принепрерывномпроцессеокалинообразованиярабочее сечение металла уменьшается, что приводит к повышению рабочего напряжения и ухудшению условий безопасной эксплуатации оборудования.
Некоторые детали аппаратуры (болты, шпильки, пружины и др.) вследствие повышения пластичности металла при высоких температурах работают в условиях постепенного снижения напряжений, вызванных первоначально приложенной нагрузкой (затягом), при сохранении геометрических размеров (явление релаксации напряжений). Расчет таких деталей следует производить на предварительную нагрузку (затяг), обеспечивающую на заданный период времени остаточную нагрузку, необходимую для нормальной работы конструкции.
При выборе конструкционных материалов для технологической аппаратуры необходимо также учитывать физические свойства материалов (теплопроводность, линейное температурное расширение), а также некоторыедругиесоображениятехнико-экономическогопорядка,такие
322
vk.com/club152685050 | vk.com/id446425943
как технология изготовления аппаратуры, дефицитность и стоимость материала, наличие стандарта или утвержденных технических условий на его поставку, освоенность материала промышленностью и др.
Создаваемая конструкция технологической аппаратуры должна быть не только технически совершенной, отвечающей всем требованиям современного уровня машиностроения, но и технологичной в изготовлении, экономичной. Так как стоимость изделия в значительной мере определяется стоимостью примененных для его изготовления материалов, то при всех прочих равных условиях предпочтение должно быть отдано более дешевым и менее дефицитным материалам.
Втехнологическом аппаратостроении основным способом выполнения металлических неразъемных соединений является сварка и в ряде случаев пайка. Хорошая свариваемость металлов является одним из основных и необходимых условий, определяющих пригодность материала для создаваемой конструкции. Необходимо также стремиться
кмаксимально возможному, без ущерба для конструкции, сокращению номенклатуры применяемых марок материалов и типоразмеров.
Аппаратуру не рекомендуется изготовлять целиком из дорогостоя- щихидефицитныхматериалов.Технико-экономическаянецелесообраз- ность применения монолитных толстолистовых высоколегированных сталей и цветных металлов не вызывает сомнения. Коррозии обычно подвержена лишь внутренняя поверхность аппаратов. Для обеспечения амортизационного срока службы аппарата достаточен слой коррозионностойкого металла толщиной в несколько миллиметров. Таким образом, представляется целесообразным изготовлять аппаратуру для активных коррозионных сред из двухслойного проката, облицовочный слой которого может быть выполнен из требуемого коррозионностойкого металла или сплава. Например, вместо монолитной толстолистовой нержавеющей стали 12Х18Н10Т или 10X17Н13М2Т целесообразно применять двухслойную листовую сталь 16ГС+12Х18Н10Т или Ст3сп5+10Х17Н13М2Т.
Внастоящеевремяметаллургическойпромышленностьюосвоенряд новых марок высоколегированных сталей с малым содержанием никеля, которые и рекомендуется применять в технологическом аппаратостроении в качестве заменителей дефицитных хромоникелевых сталей или сталей с большим содержанием никеля. К таким сталям относятся
08Х22Н6Т, 08Х21Н6М2Т и др.
Для активных коррозионных сред наиболее целесообразно изготовление технологической аппаратуры из неметаллических материалов: природных кислотоупоров, керамики, фарфора, стекла, углеграфито-
323