
vk.com/club152685050 | vk.com/id446425943
РАБОТА № 2
ИССЛЕДОВАНИЕ МИКРОСТРУКТУРЫ УГЛЕРОДИСТЫХ
СТАЛЕЙ В РАВНОВЕСИНОМ СОСТОЯНИИ
Увеличение ________________________ Травление _________________________
Микро- |
Название и |
Расчет |
Примерная |
Механические |
|||
|
|
||||||
структурные |
содержа- |
свойства |
|
||||
структура |
марка и |
|
|||||
|
|
|
|||||
составляющие |
ния |
|
|
|
|||
стали |
применение |
в, МПа |
δ, % |
НВ |
|||
стали |
углерода |
||||||
|
|
|
|||||
|
|
|
|
|
|
|
|
|
|
|
|
|
|
|
|
|
|
|
|
|
|
|
|
|
|
|
|
|
|
|
|
|
|
|
|
|
|
|
Работу выполнил ____________________ Работу принял _____________________
«________» ____________________________
5
vk.com/club152685050 | vk.com/id446425943
РАБОТА № 3
ИССЛЕДОВАНИЕ МИКРОСТРУКТУРЫ ЧУГУНОВ
Увеличение ______________________ Травление _________________________
Микро- |
Название и |
Примерная |
Механические свойства |
||||
структурные |
марка |
||||||
структура |
|||||||
|
|
|
|
||||
составляю- |
чугуна и его |
|
|
|
|
||
чугуна |
|
|
|
|
|||
щие чугуна |
применение |
|
|
|
|
||
|
в, МПа |
изг, МПа |
δ,% |
НВ |
|||
|
|
|
|
|
|
|
|
|
|
|
|
|
|
|
|
|
|
|
|
|
|
|
|
|
|
|
|
|
|
|
|
|
|
|
|
|
|
|
Работу выполнил ___________________ Работу принял _____________________
«________» ____________________________
6
vk.com/club152685050 | vk.com/id446425943
РАБОТА № 1
АНАЛИЗ ДИАГРАММЫ СОСТОЯНИЯ ЖЕЛЕЗО-ЦЕМЕНТИТ
1. Основные линии и точки диаграммы состояния:
- |
АВСД |
- _______________________________________________ |
- |
AHJECF - _______________________________________________ |
|
- |
HJB |
- _______________________________________________ |
- |
ECF |
- _______________________________________________ |
- |
SE |
- _______________________________________________ |
- |
GS |
- _______________________________________________ |
- |
MO |
- _______________________________________________ |
- |
PSK |
- _______________________________________________ |
|
|
Точка C - ______________________________________________ |
|
|
Точка S - ______________________________________________ |
2. Реакции:
а) перитектическая – ___________________________________________
б) эвтектическая – ___________________________________________
в) эвтектоидная – ___________________________________________
3. Определение и характеристика механических свойств основных структурных составляющих диаграммы:
а) феррит - _____________________________________________________________
б) аустенит - ___________________________________________________________
в) цементит - ___________________________________________________________
г) перлит - _____________________________________________________________
д) ледебурит (выше линии PSK) - _________________________________________
е) ледебурит (ниже линии PSK) - __________________________________________
3
vk.com/club152685050 | vk.com/id446425943
ФГБОУ
Кубанский государственный технологический университет
Кафедра материаловедения и автосервиса
ЖУРНАЛ ЛАБОРАТОРНЫХ РАБОТ ПО ДИСЦИПЛИНЕ
«МАТЕРИАЛОВЕДЕНИЕ»
для студентов специальности
__________________________________
форма обучения ____________________
группа _____________________________
Фамилия, И. О. студента_________________________
________________________________________________
Учебный план выполнен ________________________
Фамилия, И. О. преподавателя_____________________
Дата "_____" _______________ 2016 г.
Краснодар - 2016 г.
1
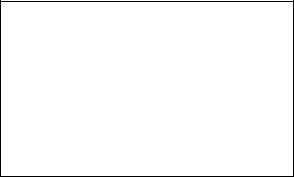
vk.com/club152685050 | vk.com/id446425943
П Р О Т О К О Л
ЗАКАЛКИ СТАЛЬНЫХ ОБРАЗЦОВ
|
Диаметр |
Твердость в исход |
Температур |
Время |
Твердость |
||
Марк |
или |
–ном состоянии |
а закалки, |
нагрева , |
после |
||
толщина |
|
|
°С |
с |
закалки |
||
а |
|
|
|||||
образца |
|
|
|
|
|
|
|
стали |
|
|
|
|
|
|
|
в мм |
НВ |
|
|
|
|
|
|
|
HRCэ |
|
|
HRCэ |
HB |
||
|
|
|
|
|
|||
|
|
|
|
|
|
|
|
|
|
|
|
|
|
|
|
|
|
|
|
|
|
|
|
|
|
|
|
|
|
|
|
11 . Микроструктура закаленной стали :
12 . В ы в о д ы:
Работу выполнил __________________ Работу принял ___________________
«_____» ________________ 200__г.
9

vk.com/club152685050 | vk.com/id446425943
|
|
|
Р А Б О Т А № 4 |
||
|
|
|
ЗАКАЛКА СТАЛИ |
||
1 |
. Определение закалки : |
||||
2 |
. Цель закалки : |
|
|
|
|
3 |
. Критическая скорость закалки : |
||||
4 |
. Диаграмма изотермического распада аустенита : |
||||
|
Т,оС |
аустенит |
|||
|
600 |
|
|
|
Ас1+727оС |
|
|
|
|||
|
|
|
|
|
|
|
400 |
|
|
|
|
|
|
|
|
|
Мн+240оС |
|
200 |
|
|
|
|
|
|
|
|
|
|
|
|
|
|
|
|
5 . Структуры, получаемые при различных скоростях охлаждения и их твердость
Скорость |
Образующаяся структура |
Твердость, НВ |
|
охлаждения |
|||
|
|
||
|
|
|
|
|
Перлит – |
|
|
|
|
|
|
|
Сорбит – |
|
|
|
|
|
|
|
Троостит – |
|
|
|
|
|
|
|
Мартенсит – |
|
|
|
|
|
|
|
7 |
|
vk.com/club152685050 | vk.com/id446425943
6 . Режимы отпуска и протокол испытания на твердость
Вид |
Температура |
Способ контроля |
Твердость |
Микроструктур |
|
отпуска |
нагрева , |
Температуры |
после |
а |
|
|
°C |
(цвет побежалости) |
отпуска |
после |
|
|
|
|
HRC |
HB |
отпуска |
|
|
|
э |
|
|
|
|
|
|
|
|
|
|
|
|
|
|
|
|
|
|
|
|
7 . Влияние температуры отпуска на твердость закаленной стали (столбчатая диаграмма)
|
|
|
|
|
|
|
|
|
|
|
|
|
|
|
|
|
|
|
|
|
|
|
|
|
|
|
|
|
|
|
|
|
|
|
|
|
|
|
|
|
|
|
|
|
|
|
|
|
|
|
|
|
|
|
|
|
|
|
|
|
|
|
|
|
|
|
|
|
|
|
|
|
|
|
|
|
|
|
|
|
|
|
|
100 |
200 |
300 |
400 |
500 |
600 |
||||||
|
|
|
|
|
|
температура отпуска, °C |
8 . В ы в о д ы :
Работу выполнил __________________ Работу принял ___________________
«_____» ________________ 200__г.
11

vk.com/club152685050 | vk.com/id446425943 |
|
6 . Интервал оптимальных закалочных температур |
|
911оС |
аустенит |
Р |
727оС |
|
0,8 2,14 % углерода |
7 |
. Исходные данные : диаметр образца, мм ________________________ |
|
марка стали _______________________________ |
|
структура _________________________________ |
|
твердость, НВ _____________________________ |
8 |
. Оборудование, приборы, инструмент : |
9 . Режим закалки :
-температура закалки
-продолжительность нагрева
-охладитель –
10 . График закалки Т,оС
время
8

vk.com/club152685050 | vk.com/id446425943
Р А Б О Т А № 5
ОТПУСК СТАЛИ
1 . Определение отпуска :
2 . Цели отпуска :
3 . Виды отпуска в зависимости от температуры и получаемые структуры для углеродистых сталей :
Вид отпуска |
Получаемая |
|
структура |
Ас1=727оС
Т,оС
600оС
500оС
400оС
300оС
200оС
100оС
2,14%С 4 . Исходные данные : диаметр образца, мм ___________________________________
марка стали __________________________________________
структура ____________________________________________
твердость ________________HRCэ _____________________HB
5 . Оборудование, приборы, инструменты :
10
vk.com/club152685050 | vk.com/id446425943
ВОПРОСЫ ДЛЯ ПОДГОТОВКИ К ЗАЩИТЕ ЛАБОРАТОРНЫХ РАБОТ
РАБОТА № 1Анализ диаграммы железо-цементит
1.Для каких сплавов построена диаграмма железо-цементит, как эти сплавы называются?
2.В каких координатах строятся диаграммы состояния ?
3.Как взаимодействуют компоненты в сплавах железа и углерода, что представляют собой твердые растворы , эвтектики, химические соединения?
4. .Как взаимодействует углерод с железом?
5.Укажите линии и точки диаграммы, приведите их названия.
6.то представляет собой каждая из структурных составляющих: аустенит, феррит, цементит. Перлит, ледебурит?
7.Что представляет собой перитектическое, эвтектическое, эвтектическое превращения? Как они протекают?
8.Какой цементит называют первичным, вторичным ?
9.Какое изменение происходит в ледебурите ниже линии РSК?
РАБОТА 2 Изучение микроструктуры и свойств углеродистых сталей
1.Какие сплавы называются сталями?
2.Как влияют углерод и постоянные примеси на свойства сталей?
3.Дайте определение основных фаз и структурных составляющих углеродистых сталей (феррит, перлит, цементит, аустенит).
4.Приведите классификацию углеродистых сталей по структуре, способу производства, содержанию углерода, способу раскисления, качеству и назначению.
5.Сталь углеродистая обыкновенного качества (ГОСТ380-90), классификация, маркировка и назначение.
6.Сталь углеродистая качественная (ГОСТ 1054-88), классификация, маркировка и назначение.
7.Сталь углеродистая инструментальная (ГОСТ 1435-90), классификация, маркировка и назначение.
8.Легированные стали: маркировка и назначение.
РАБОТА 3 Изучение микроструктуры и свойств чугунов
1.Какие сплавы называют чугунами?
2.Как классифицируют чугуны в зависимости от формы выделения углерода?
3.Какие чугуны называют белыми, назовите структурные составляющие белых чугунов, их определения. области применения белых чугунов.
4.Серый чугун (ГОСТ 1412-85),классификация по структуре, маркировка, области применения.
5.Высокопрочные чугуны (ГОСТ 7293-85), классификация по структуре, получение. маркировка, области применения.
6.Ковкие чугуны (ГОСТ 1215-79), классификация по структуре, получение, маркировка, области применения.
РАБОТА 4-5 Влияние закалки и отпуска на структуру и свойства углеродистой стали
1.Назовите основные виды термической обработки стали, их назначение и технологию проведения.
2.Диаграмма изотермического превращения аустенита. Мартенситное превращение.
3.Назовите продукты распада аустенита при его охлаждении с различной скоростью.
4.Что называется закалкой стали, назовите виды закалки в зависимости от температуры нашрева.
5.как определить оптимальную температуру нагрева стали под закалку?
6.Охлаждающие среды при закалке и условия их выбора.
7.Что называется критической скоростью закалки?
8.Как определить время нагрева стали под закалку?
9.Назовите способы закалки.
10.Что такое прокаливаемость стали?
11.Что такое отпуск и цели его проведения.
12.Какая структура получается после различных видов отпуска?
13.Что называется улучшением и цели его.
14. Как влияет температура отпуска на твердость стали?
2
vk.com/club152685050 | vk.com/id446425943

vk.com/club152685050 | vk.com/id446425943
Диаграмма железо-цементит |
Кривые охлаждения |
|
Fe |
Fe3C |
|
|
|
|
t, o C |
|
t, o C |
t, o C |
t, o C |
1600 |
|
|
|||
|
|
|
|
|
1400
1200
1000
800
600
1 |
2 |
3 |
4 |
5 |
6 6,67, %С |
|
|
|
|
|
|
|
|
|
|
||||||
|
|
|
|
|
|
|
|
Работу выполнил _______________________ Работу принял _______________________ Дата «____»_______________ _____г.
4
vk.com/club152685050 | vk.com/id446425943
vk.com/club152685050 | vk.com/id446425943
В.Н.Киприянова
КУРС ЛЕКЦИЙ ПО ДИСЦИПЛИНЕ МАТЕРИАЛОВЕДЕНИЕ
Краснодар
2015
1
vk.com/club152685050 | vk.com/id446425943
СОДЕРЖАНИЕ
Предисловие………………………………………………………… 3
Лекция 1 Строение и свойства чистых металлов………………….7
Лекция 2 Формирование структуры литых металлов…………….18
Лекция 3 Строение и свойства сплавов. Диаграммы состояния бинарных сплавов……………………………………………………27
Лекция 4 Механические свойства и способы определения их количественных характеристик……………………………………..39 Лекция 5 Диаграмма состояния железо-углерод………………….. 42 Лекция 6 Углеродистые стали……………………………………….48
Лекция 7 Чугуны………………………………………………….......60
Лекция 8 Термическая обработка-теория термической обработки …………………………………………………………….71
Лекция 9 Технология термической обработки………………….…80
Лекция 10 Химико-термическая обработка………………………..98 Лекция 11 Легированные стали…………………………………….106
Лекция 12 Инструментальные материалы………………………....117 Лекция 13 Легированные стали с особыми свойствами…………..125
Лекция 14 Медь и ее сплавы……………………………………...…135
Лекция 15 Материалы с малой плотностью (легкие материалы)…143 Лекция 16 Неметаллические материалы……………………………158
2
vk.com/club152685050 | vk.com/id446425943
ПРЕДИСЛОВИЕ
Материаловедение – это наука, изучающая строение и свойства
материалов и устанавливающая связь между составом, строением и свойствами
Цель изучения данной дисциплины- познание природы и свойств материалов, используемых в различных областях техники.
Знания, полученные при изучении данной дисциплины необходимы вам для успешного изучения других дисциплин, выполнения курсовых и дипломных проектов, а также в практической деятельности инженера.
Имея дело с машинами, аппаратами. станками, нельзя не знать материалов, из которых они изготовлены.
Эффективность любых конструкцийавтомашин, самолетов, оборудования пищевой промышленности, машиностроения и т.п. в значительной степени определяются свойствами материалов, из которых они изготовлены.
Революционную роль сыграли полученные новые материалы – проводниковые материалы, жидкие кристаллы в электронике, композиционные материалы в авиации и ракетостроении, аморфные сплавы в радиотехнике и электронике.
Курс Материаловедения состоит из 3-х неравных частей. Теория металлов и сплавов Технические сплавы
Неметаллические материалы
Изучив дисциплину Материаловедение, студент должен знать строение и свойства чистых металлов, теоретические вопросы процессов кристаллизации металлов и сплавов, виды взаимодействия компонентов в сплаве, виды диаграмм состояния.
Главная часть курса - Технические сплавымы начнем с изучения железоуглеродистых сплавовсталей и чугунов. Изучим диаграмму состояния железо-углерод, значение которой для материаловедения также велико как периодическая таблица Менделеева для химиков.
В процессе изучения материала мы будем многократно говорить о структуре металлов и ее влиянии на свойства сплавов.
3

vk.com/club152685050 | vk.com/id446425943
Также мы изучим различные виды термической и химико-термической обработок, легированные стали, сплавы меди, алюминия, титана, магния.
Завершающий раздел курсанеметаллические материалы-пластмассы и резины.
Появление новых материалов вызывало целую революцию в ряде отраслей.
Так более 100 лет тому назад различные резцы для обработки материалов на металлорежущих станках изготавливались из обыкновенной углеродистой стали термически обработанной, но стойкость их была невелика и скорость резания не превышала 5м/мин.
Но вот появились быстрорежущие стали с добавками 8-18 % вольфрама и скорости увеличились до 35 м/мин. Это привело к необходимости замены металлорежущих станков на более быстроходные.
В 1933 году был получен новый инструментальный материал т.н. победиттвердый сплав, скорости резания опять возросли и необходима была полная замена металлорежущих станков.
Большой вклад в развитие науки о металлах –материаловедения- внесли русские ученые П.П. Аносов (1799-1815 гг), он впервые установил связь между строением стали и ее свойствами, впервые применил микроскоп для изучения структуры стали.
4

vk.com/club152685050 | vk.com/id446425943
Д.К.Чернов (1839-1921гг)- отец металоведения, так называют его в ученом миреоткрыл полиморфизм стали, он признан во всем мире – основоположником материаловедения.
Среди зарубежных ученых большой вклад в изучение железо-углеродистых сплавов внесли Ле-Шателье (Франция), Аустен (Англия), Осмонд (Франция) и др.
О той огромной роли, которую играют металлы в нашей жизни, писал еще Георг Агриколла , немецкий мыслитель 16 века- в его трудах о металлургии есть такие строчки-« Человек не может обойтись без металлов… если бы не было металлов люди влачили бы самую омерзительную и жалкую жизнь среди диких зверей»
Не случайно этапы в жизни человечества история назвала по преобладающим в то время металлическим материалам: эпоха меди, бронзовый век, железный век.
Богат и разнообразен мир металлов, удивительны и разнообразны их свойства. Ртуть не замерзает даже на морозе, вольфрам не боится самых жарких объятий пламени, серебро и медь отлично проводят электрический ток, а у висмута или олова это дело явно не клеится. Самый легкий металл-литий, а осмийсамый тяжелый, камнем пойдет ко дну, его плотность в 20 с лишним раз выше, чем у воды. Алюминием богата наша планета, а франций настолько редок, что его содержание в земной коре измеряется буквально граммами.
Трудно даже представить, что произошло, если бы исчезло железо, алюминий, медь.
5
vk.com/club152685050 | vk.com/id446425943
Первыми свойствами, с которыми познакомились наши предки, были твердость и прочность, пластичность и металлический блеск.
Важнейшее свойство- прочность- способность сопротивляться разрушению под действием внешних нагрузок. Благодаря этому свойству успешно выдерживают огромные нагрузки и мосты и ж/д составы и самолеты.
Многие узлы современных машин и агрегатов работают в условиях высоких температур и должны обладать такими свойствами как Жаростойкость. При создании жаростойких материалов большая роль принадлежит никелю. Когда одного из металловедов. Занимающихся разработкой большого количества жаростойких сплавов, спросили как это ему удается, он ответил, я просто заменяю в сталях железо на никель.
Важную роль играет ПЛАСТИЧНОСТЬ- способность необратимо изменять свою форму под действием механических нагрузок. На пластической деформации основана обработка металлов давлением. Прокатка, ковка, штамповка, прессованиевсе эти технологические процессы возможны потому, что медь, алюминий сталь, свинец и др обладают пластичностью.
Важная характеристика металлов –ТВЕРДОСТЬ- способность металла сопротивляться внедрению в него более твердого тела. Чем тверже металл, тем он прочнее. Эталоном твердости служит алмаз.
6

vk.com/club152685050 | vk.com/id446425943
Основная |
литература |
1.Материаловедение и технология металлов: учеб. для вузов по машиностроит. спец./ [Фетисов Г.П. и др.]; по ред. Г.П. Фетисова. – Изд.
6-е, доп. – М.: Высш. шк., 2008. – 877 с.
2.Материаловедение и технология конструкционных материалов:
Учебник/ В.Б.Арзамасов, А.Н.Волчков. – М.:, Академия, 2009.- 448 с.
3.Сильман Г.И. Материаловедение: учеб. пособие для вузов по спец. напр. «Металлургия, машиностроение и материалоперераб.» /. – М.:
Академия, 2008 .- 335 с.
4.Гуляев А.П. Металловедение. - М.: Металлургия, 1990.- 541 с.
5.Лахтин Ю.М., Леонтьева В.П. Материаловедение. – М.: Машиностроение, 1990. – 512 с.
Лекция 1
«Строение и свойства чистых металлов»
Почти 3/4 всех существующих в природе элементов являются металлами. Разумеется, не все они находят широкое применение в технике. Некоторые из них встречаются очень редко, они чрезвычайно дороги. Это и редкие -
бериллий, ванадий, уран, драгоценные – серебро, золото, платина и др.
Многие металлы малопригодны к применению, т.к. обладают большой хрупкостью и твердостью (хром, марганец, сурьма), их используют в качестве добавок к другим металлам.
Металлы, из которых изготавливают детали машин, приборов, называют
конструкционными или машиностроительными.
Все металлы делятся на 2 большие группы:
черные
цветные
7

vk.com/club152685050 | vk.com/id446425943
Черные имеют темно-серый цвет, большую
плотность, высокую температуру плавления, относительно высокую твердость. Наиболее типичным представителем является железо.
Цветные имеют характерную окраску – красную, желтую, белую. Они пластичны, обладают малой твердостью, имеют низкую температуру плавления. Типичным представителем является медь.
Черные металлы согласно классификации, предложенной А.П.Гуляевым подразделяются:
Железные металлы – железо, кобальт, никель (ферромагнетики) и близкий к ним марганец Тугоплавкие, с температурой плавления больше, чем у железа (1539о)
Урановые ( актиниды)
Редкоземельные металлы (РЗМ), лантан, церий и др.
Щелочноземельные
Цветные металлы подразделяются:
Легкие металлы – берилий, магний, алюминий, с плотностью меньше 5 г/смз Благородные – серебро, золото, платина и и др. к ним может быть отнесена и
полу благородная медь, обладающие устойчивостью перед коррозией. Легкоплавкие – цинк, кадмий, ртуть, олово , с температурой плавления меньше 1000о.
Что такое металл?
На этот вопрос М.В. Ломоносов отвечал так: «Металлы суть светлые тела, которые ковать можно».
Это простейшее определение не потеряло своего значения и сегодня. Металлы можно охарактеризовать такими свойствами:
• высокая теплопроводность;
8

vk.com/club152685050 | vk.com/id446425943
•электропроводность, которая с понижением температуры повышается, причем некоторые металлы имеют сверхпроводимость;
•пластичность (см. «ковать можно»);
•металлический блеск (см. «суть светлые тела»);
•магнитные свойства;
•постоянная температура кристаллизации.
Все металлы – тела кристаллические
В природе существует два типа построения твердых тел их атомов – тела могут быть кристаллические и аморфные.
Они отличаются по своим свойствам.
Аморфные тела – это такие тела, в которых атомы расположены беспорядочно, хаотически. В отличие от жидкостей они имеют пониженную подвижность частиц.
Примерами аморфных тел могут служить стекло, смолы, воск.
Кристаллические тела – это такие тела, в которых атомы расположены в строго определенном порядке, в строго определенной последовательности. Кристаллические тела остаются твердыми, т.е. сохраняют приданную им форму до вполне определенной температуры, при которой он переходит в жидкое состояние.
9

vk.com/club152685050 | vk.com/id446425943
Все металлы – тела кристаллические
Свойства кристаллов зависят от электронного строения атомов и
характера взаимодействия их в кристалле, от пространственного расположения элементарных частиц,
химического состава, размера и формы кристаллов.
Все эти детали строения кристаллов описывает понятие – СТРУКТУРА В зависимости от размеров, структурных составляющих и методов их выявления различают:
тонкую структуру – описывает расположение частиц в кристалле и электронов в атоме. Изучается дифракционными методами – рентгенографией и т.д.
микроструктуру –состоящую из мелких кристалликов, зерен, ее наблюдают с помощь. оптических или электронных микроскопов.
макроструктуру – изучаемую невооруженным глазом или при небольших увеличениях. Выявляет изломы, раковины, поры.
Под атомно-кристаллической структурой металлов понимают взаимное расположение атомов, существующее в кристалле.
Кристалл состоит из атомов (ионов), расположенных в определенном порядке, который периодически повторяется в трех измерениях.
Для описания атомно-кристаллической структуры пользуются понятием
пространственной или кристаллической решетки.
Кристаллическая решетка представляет собой воображаемую пространственную сетку, в узлах которой расположены атомы.
10

vk.com/club152685050 | vk.com/id446425943
Кристаллическую решетку можно построить, выбрав для этого «строительный блок», многократно повторяя его в трех измерениях. Такая строительная единица в металловедении называется элементарной ячейкой.
КРИСТАЛЛИЧЕСКИЕ РЕШЕТКИ МЕТАЛЛОВ
11

vk.com/club152685050 | vk.com/id446425943
Рис. Модели элементарных ячеек:
а, г – ГПУ (гексагональная плотноупакованная); б, д – ГЦК (гранецентрированная кубическая); в, е – ОЦК (объемноцентрированная кубическая)
Решетку ОЦК имеют вольфрам, хром, молибден
Решетку Г.Ц.К. имеют серебро, золото, никель, медь, ванадий,натрий, платина.
Гексагональную решетку имеют магний, цинк, кадмий, бериллий титан
12

vk.com/club152685050 | vk.com/id446425943
Размеры элементарной ячейки кристаллической решетки оценивают отрезки а,в, с. Их называют периодами решетки.
Период решетки измеряется в нанометрах (нм) 1 нм = 10-9 см = 0,1 А
Период решетки металлов находится в пределах от 0,1 до 0,7 нм
Плотность кристаллической решеткиобъема, занятого атомами,
характеризуется координационным числом – К.
К – число атомов, находящихся на равном и наименьшем расстоянии от данного атома.
Чем выше К, тем больше плотность упаковки.
Для ОЦК К=8 для гцк к=12 для ГПУ К=12
Полиморфизм (аллотропия) – способность металла принимать различные кристаллические формы при разных температурах
Ряд металлов (железо, марганец, титан и др.) в зависимости от температуры и давления могут существовать в состояниях с различными кристаллическими решетками – это явление называется – полиморфизмом
или аллотропия.
13

vk.com/club152685050 | vk.com/id446425943
Кривая охлаждения чистого железа
Анизотропия |
свойств |
кристаллов |
Анизотропия – это зависимость свойств кристалла от направления. Возникает в результате упорядоченного расположения атомов в пространстве.
Свойства кристаллов определяются взаимодействием атомов В кристалле расстояния между атомами в различных
кристаллографических плоскостях различны, поэтому различны и свойства. Например, прочность и пластичность монокристалла меди изменяются
в зависимости от направления 180-350 Мпа, и 10-50 %. Для поликристалла прочность 250 Мпа, пластичность 40%.
В природе кристаллические тела – поликристаллы, т.е. состоят из множества мелких различно ориентированных кристаллов. В этом случае анизотропии
14

vk.com/club152685050 | vk.com/id446425943
нет, т.к. среднестатистическое расстояние между атомами по всем направлениям оказывается примерно одинаковым.
В связи с этим поликристаллические тела считают квазиизотропными (мнимо).
Все аморфные тела – изотропны - свойства у них одинаковы во всех направлениях
ДЕФЕКТЫ КРИСТАЛЛОВ
Строение реальных кристаллов отличается от идеальных. В реальных кристаллах всегда содержатся дефекты, которые подразделяются на точечные, линейные, поверхностные и объемные. Дефекты имеют различные размеры. У точечных размеры близки к атомным, у линейных длина на несколько порядков больше ширины, объемные дефекты (поры, трещины) могут иметь макроскопические размеры.
Точечные дефекты
Одним из распространенных несовершенств кристаллического строения является наличие точечных дефектов: вакансий, дислоцированных атомов и примесей.
Рис.2.1. Точечные дефекты
Линейные дефекты
Основными линейными дефектами являются дислокации. Априорное представление о дислокациях впервые использовано в 1934 году Орованом и Тейлером при исследовании пластической деформации кристаллических материалов, для объяснения большой разницы между практической и теоретической прочностью металла.
Дислокация
Дислокация – это дефекты кристаллического строения, представляющие собой линии, вдоль и вблизи которых нарушено характерное для кристалла правильное расположение атомных плоскостей.
15
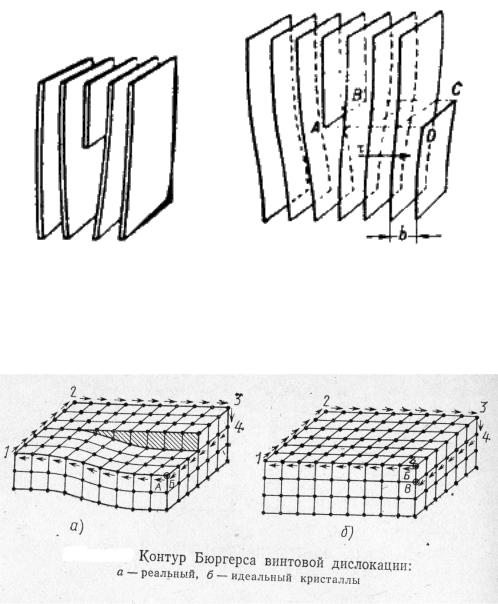
vk.com/club152685050 | vk.com/id446425943
Простейшие виды дислокаций – краевые и винтовые.
Краевая дислокация представляет собой линию, вдоль которой обрывается внутри кристалла край «лишней» полуплоскости.
Рис. 2.2. Краевая дислокация (а) и механизм ее образования (б)
Винтовая дислокация
Другой тип дислокаций был описан Бюргерсом, и получил название
винтовая дислокация
Плотность дислокаций
Свойства кристаллов зависят от количества дефектов, которые формируют понятие «плотность дислокаций». Плотность дислокации – это суммарная длина всех линий дислокации в одном кубическом сантиметре кристалла.
Существует связь между свойствами металла и плотностью дефектов
16

vk.com/club152685050 | vk.com/id446425943
Рис. 13. Зависимость предела прочности от плотности дефектов
Пути повышения прочности металлов
17

vk.com/club152685050 | vk.com/id446425943
Лекция 2
«Формирование структуры литых металлов»
Любое вещество может находиться в трех агрегатных состояниях:
Твердом
Жидком
Газообразном
Переход металла из жидкого состояния в твердое с образованием кристаллической структуры называется первичной кристаллизацией. Образование новых кристаллов в твердом кристаллическом веществе называется вторичной кристаллизацией.
Кристаллы могут зарождаться самопроизвольно – самопроизвольная
кристаллизация.
Или расти на имеющихся готовых центрах кристаллизации –
несамопроизвольная кристаллизация.
Самопроизвольная кристаллизация обусловлена стремлением вещества иметь более устойчивое состояние, характеризуемое уменьшением свободной энергии или термодинамического потенциала.
Чем объяснить существование при одних температурах жидкого, а при других температурах твердого состояния и почему превращение происходит при строго определенных температурах?
В природе все самопроизвольно протекающие процессы, а, следовательно, кристаллизация и плавление обусловлены тем, что новое состояние в новых условиях является энергетически более устойчивым, обладает меньшим запасом энергии. Это можно пояснить примером:
Тяжелый шарик из положения 1 стремиться попасть в более устойчивое положение 2, т.к. в положении 2 потенциальная энергия меньше, чем в положении 1.
18

vk.com/club152685050 | vk.com/id446425943
Возможен переход из одного состояния в другое, если новое состояние в новых условиях является более устойчивым, обладает меньшим запасом энергии.
С изменением внешних условий свободная энергия изменяется по сложному закону различно для жидкого и кристаллического состояний. Характер изменения свободной энергии жидкого и твердого состояний с изменением температуры показан на рис.
Изменение свободной энергии в зависимости от температуры
В соответствии с этой схемой выше температуры ТS вещество должно находиться в жидком состоянии, а ниже ТS – в твердом.
При температуре равной ТS жидкая и твердая фаза обладают одинаковой энергией, металл в обоих состояниях находится в равновесии, поэтому две фазы могут существовать одновременно бесконечно долго.
Температура ТS – равновесная или теоретическая температура кристаллизации.
Для начала процесса кристаллизации необходимо, чтобы процесс был термодинамически выгоден системе и сопровождался уменьшением свободной энергии системы. Это возможно при охлаждении жидкости ниже температуры ТS.
Температура, при которой практически начинается кристаллизация называется фактической температурой кристаллизации.
19

vk.com/club152685050 | vk.com/id446425943
Охлаждение жидкости ниже равновесной температуры кристаллизации называется переохлаждением, которое характеризуется степенью переохлаждения.
Процесс перехода металла из жидкого состояния в твердое можно изобразить графически в координатах температура – время по так называемым кривым охлаждения
Кривая охлаждения
Кривая охлаждения имеет следующий вид:
Д.К. Чернов, изучая структуру литой стали указал, что процесс кристаллизации состоит из двух элементарных процессов:
зарождения мельчайших зародышей или центров кристаллизации
роста кристаллов из этих центров
Этот процесс можно изучать с помощью рассмотрения моделей (схем), что успешно применялось Миркиным И.Л.
20

vk.com/club152685050 | vk.com/id446425943
Предположим, что на некоторой площади за 1 сек возникает 5 центров кристаллизации, которые растут с определенной скоростью. К концу 1-ой сек образовалось 5 зародышей, к концу «-й они выросли и возникло еще 5 зародышей, к концу 2-й они выросли и так далее. Так в результате возникновения зародышей и их роста происходит процесс кристаллизации.
При образовании кристаллы растут свободно, они могут иметь геометрически правильную форму. При столкновении же растущих кристаллов их правильная форма нарушается. В результате этого при после затвердевания кристаллы имеют неправильную форму, их называют
кристаллитами или зернами.
Условия получения мелкозернистой структуры
Стремятся к получению мелкозернистой структуры. Оптимальными условиями для этого являются: максимальное число центров кристаллизации и малая скорость роста кристаллов.
21

vk.com/club152685050 | vk.com/id446425943
Размеры образовавшихся кристаллов зависят от соотношения числа образовавшихся центров кристаллизации и скорости роста кристаллов при температуре кристаллизации.
При равновесной температуре кристаллизации ТS число образовавшихся центров кристаллизации и скорость их роста равняются нулю, поэтому процесса кристаллизации не происходит.
Если жидкость переохладить до температуры, соответствующей т.а, то образуются крупные зерна (число образовавшихся центров небольшое, а скорость роста – большая).
При переохлаждении до температуры соответствующей т.в – мелкое зерно (образуется большое число центров кристаллизации, а скорость их роста небольшая).
Зависимость числа центров кристаллизации (а) и скорости роста кристаллов (б) от степени переохлаждения
22

vk.com/club152685050 | vk.com/id446425943
Размер зерен при кристаллизации зависит и от числа частичек нерастворимых примесей, которые играют роль готовых центров кристаллизации – оксиды, нитриды, сульфиды.
Чем больше частичек, тем мельче зерна закристаллизовавшегося металла.
Стенки изложниц имеют неровности, шероховатости, которые увеличивают скорость кристаллизации.
Мелкозернистую структуру можно получить в результате модифицирования, когда в жидкие металлы добавляются посторонние вещества – модификаторы
По механизму воздействия различают:
Вещества, не растворяющиеся в жидком металле – выступают в качестве дополнительных центров кристаллизации.
Поверхностно - активные вещества, которые растворяются в металле, и, осаждаясь на поверхности растущих кристаллов, препятствуют их росту.
Строение |
металлического |
слитка |
Схема стального слитка, данная Черновым Д.К., представлена на рис. Слиток состоит из трех зон:
1. мелкокристаллическая корковая зона
2. зона столбчатых кристаллов
3. внутренняя зона крупных равноосных кристаллов.
Кристаллизация корковой зоны идет в условиях максимального переохлаждения. Скорость кристаллизации определяется большим числом центров кристаллизации. Образуется мелкозернистая структура.
23

vk.com/club152685050 | vk.com/id446425943
Жидкий металл под корковой зоной находится в условиях меньшего переохлаждения. Число центров ограничено и процесс кристаллизации реализуется за счет их интенсивного роста до большого размера.
Дендрит
Рост кристаллов во второй зоне имеет направленный характер. Они растут перпендикулярно стенкам изложницы, образуются древовидные кристаллы – дендриты .
Растут дендриты с направлением, близким к направлению теплоотвода.
Так как теплоотвод от незакристаллизовавшегося металла в середине слитка в разные стороны выравнивается, то в центральной зоне образуются крупные дендриты со случайной ориентацией.
Зоны столбчатых кристаллов в процессе кристаллизации стыкуются, это явление называется транскристаллизацией.
Для малопластичных металлов и для сталей это явление нежелательное, так как при последующей прокатке, ковке могут образовываться трещины в зоне стыка.
В верхней части слитка образуется усадочная раковина, которая подлежит отрезке и переплавке, так как металл более рыхлый.
ПРЕВРАЩЕНИЯ В ТВЕРДОМ СОСТОЯНИИ
Атомы элемента могут образовывать любую кристаллическую решетку. Однако устойчивым, а, следовательно, и реально существующим типом
24

vk.com/club152685050 | vk.com/id446425943
является решетка, обладающая наиболее низким запасом свободной энергии.
Так, вольфрам, хром и др имеют ОЦК решетку, медь, серебро и др. – ГЦК.
Однако в ряде случаев при изменении температуры может оказаться, что для того же металла более устойчивой будет другая решетка, чем была при другой температуре.
Существование одного металла в нескольких кристаллических формах называется ПОЛИМОРФИЗМОМ или АЛЛОТРОПИЕЙ.
Аллотропические формы обозначают буквами греческого алфавита.
Превращение одной аллотропической формы в другую при нагреве чистого металла сопровождается поглощением тепла и происходит при постоянной температуре – горизонтальный участок на термической кривой.
Такие металлы как железо, кобальт, олово, марганец, титан и др. имеют полиморфные превращения.
ПРАВИЛО ФАЗ или ЗАКОН ГИББСА
Постоянная температура при кристаллизации или, что тоже самое – наличие площадки на кривой охлаждения, объясняется, доказывается
важнейшим физико-химическим законом, так называемым, правилом фаз или законом Гиббса.
Правило фаз – это закон, выражающий соотношение между числом фаз Ф, числом компонентов К, внешних переменных В и числом степеней свободы для равновесной температуры.
25
vk.com/club152685050 | vk.com/id446425943
Чтобы успешно пользоваться этим правилом необходимо дать понятия
этим |
величинам. |
ФАЗА – это однородная часть системы, ограниченная от другой части системы поверхностью раздела при переходе через которую свойства изменяются скачкообразно.
КОМПОНЕНТАМИ системы называют химические соединения или элементы, из которых может быть образована любая система. Это может быть один металл или элементы сплава.
ЧИСЛОМ СТЕПЕНЕЙ СВОБОДЫ – или ВАРИАНТНОСТЬЮ СИСТЕМЫ называют количество факторов ( концентрация, температура, давление), которые можно произвольно изменять без изменения числа фаз системы.
Математически выражение правила фаз имеет вид:
С = К - Ф + 1 , где
К – количество компонентов, образующих систему
Ф- число фаз в системе
В – число внешних переменных
Применяя правило фаз к металлам, можно во многих случаях принять изменяющимся только один внешний фактор – температуру, т.к. давление мало влияет на фазовое равновесие сплавов в твердом и жидком состояниях.
Тогда правило фаз примет вид:
С = К – Ф + 1
Математически - степень свободы – это разность между числом
переменных и уравнений, в которые входят эти переменные Если С =0, то такое равновесие называется НОНВАРИАНТНЫМ.
При нонвариантном равновесии сплав из данного числа фаз может существовать только в совершенно определенных условиях - при постоянной температуре. На кривой охлаждения – площадка.
26

vk.com/club152685050 | vk.com/id446425943
Если С = 1, то система называется МОНОВАРИАНТНОЙ, система находится не в равновесии, следовательно, температура меняется – на кривой перегиб
Лекция 3
«Строение и свойства сплавов. Диаграммы состояния бинарных сплавов»
В промышленности преимущественное распространение находят не чистые металлы, а сплавы металлов с металлами или металлов и неметаллов.
Металлическим сплавом называют вещество, полученное сплавлением двух или более компонентов.
Термин «сплав» в настоящее время имеет более широкое значение, чем во время его появления. Если раньше промышленные материалы, содержащие несколько элементов, получали преимущественно путем сплавления, то сейчас многие материалы получают и другими технологическими способами, например, порошковой металлургией, при электролизе, при плазменном напылении и др.
Роль сплавов в технике неизмеримо более велика, чем чистых металлов, т.к. они обладают более высоким комплексом свойств, которые можно широко менять в зависимости от состава.
Компоненты – это составляющие сплава.
27

vk.com/club152685050 | vk.com/id446425943
В сплавах элементы могут различно взаимодействовать между собой, образовывая различные по химическому составу и кристаллическому строению фазы.
Из однородного жидкого раствора может образоваться: однородный твердый раствор, механическая смесь или эвтектика или кристаллическое химическое соединение.
Виды взаимодействия компонентов в сплаве
В зависимости от характера взаимодействия компонентов различают сплавы:
механические смеси; химические соединения; твердые растворы.
Механические смеси
Сплавы механические смеси образуются, когда компоненты не способны к взаимному растворению в твердом состоянии и не вступают в химическую реакцию с образованием соединения.
Образуются между элементами значительно различающимися по строению и свойствам.
Сплав состоит из кристаллов, входящих в него компонентов. В сплавах сохраняются кристаллические решетки компонентов.
28

vk.com/club152685050 | vk.com/id446425943
Твердые растворы
Твердые растворыэто фазы, кристаллические решетки которых состоят из атомов отдельных компонентов.
В твердых растворах один из компонентов сплава сохраняет свою кристаллическую решетку, а атомы другого, располагаясь в решетке первого компонента (растворителя), изменяя ее размеры (периоды).
Т.о. твердые растворы имеют один тип решетки и представляют собой одну фазу.
Различают твердые растворы внедрения и замещения. Они являются фазами переменного состава.
При образовании твердого раствора замещения атомы растворенного компонента замещают часть атомов растворителя в узлах его кристаллической решетки.
29
vk.com/club152685050 | vk.com/id446425943
При образовании твердого раствора внедрения атомы растворенного компонента располагаются в междоузлиях (пустотах) кристаллической решетки компонента растворителя.
Твердый раствор – гомогенная система, внутри его нет поверхности раздела.
Многие металлы могут в той или иной степени растворяться один в другом в твердом состоянии. Так, в алюминии может растворяться до 5,5% меди, а в меди до 39 % цинка.
Твердым раствором называется вещество, кристаллическая решетка которого состоит из атомов отдельных компонентов.
Твердые растворы с неограниченной растворимостью могут образовываться при соблюдении следующих условий:
Компоненты должны обладать одинаковыми по типу кристаллическими решетками Различие в атомных размерах компонентов не должно превышать 9-15%
Компоненты должны принадлежать к одной и той же группе периодической системы элементов.
Например, серебро-золото, медь-никель, молибден-вольфрам
Твердые растворы внедрения могут возникать только в тех случаях, когда диаметр атома растворенного компонента невелик. Это углерод, азот, водород. И они могут быть только ограниченной концентрации, поскольку число пор в решетке ограничено.
Химические соединения Химические соединения – они образованы по закону нормальной
валентности. При образовании химических соединений соотношение чисел атомов элементов соответствует стехиометрической пропорции, что может быть выражено простой формулой АnВm.
Химические соединения имеют следующие характерные особенности:
кристаллическая решетка хим. соед. отличается от решеток компонентов, образующих их.
30

vk.com/club152685050 | vk.com/id446425943
Свойства его резко отличаются от свойств исходных компонентов
Они имеют постоянную температуру плавления
Образование их сопровождается значительным тепловым эффектом.
В отличие от твердых растворов хим. соединения обычно образуются между компонентами, имеющими большое различие в электронном строении.
Соединение одних металлов с другими носят общее название –
интерметаллиды. Например, Mg2 Sn.
Эвтектика Эвтектика – это механическая смесь микроскопически мелких частиц.
Механическая смесь двух компонентов А и В образуется тогда, когда они не способны к взаимному растворению в твердом состоянии и не вступают в химическую реакцию с образованием соединения.
ДИАГРАММЫ СОСТОЯНИЯ
Диаграммы состояния – это графическое изображение состояния (фазового состав, структуры) любого сплава системы в зависимости от температуры и концентрации.
Зная ее можно представить полную картину формирования структуры любого сплава, определить оптимальную температуру заливки сплавов для получения литых деталей, сделать заключение о возможностях и условиях обработки давлением, определить режим термической обработки.
Диаграмма состояния – это паспорт сплава.
Она представляет собой собрание и обобщение результатов всех наблюдений, касающихся температур плавления и кристаллизации, структуры сплавов при различных температурах и всех процессах, протекающих в сплавах при их охлаждении.
31

vk.com/club152685050 | vk.com/id446425943
Экспериментальное построение диаграмм состояния возможно благодаря тому, что любое фазовое превращение сплава отмечается изменением физико-механических свойств, либо тепловым эффектом.
Диаграмма состояние показывает устойчивое состояние, обладающее минимальным запасом свободной энергии. Они называются диаграммами равновесия.
Построение диаграммсложный процесс. Сегодня арсенал средств для этого значительно увеличился. Это и электронная микроскопия, вакуумная техника и многое другое.
Прообраз первой диаграммы дал Д.К.Чернов. Вторая диаграмма была построена в 1875 году Р.Аустеном – медь-серебро.
Расчетные методы построения диаграмм состояния менее трудоемки. нежели экспериментальные.
Диаграммы состояния строят в координатах температура – концентрация
Типы диаграмм состояния
Диаграмма состояния сплавов, компоненты которой неограниченно взаимно растворимы друг в друге
32

vk.com/club152685050 | vk.com/id446425943
ПРАВИЛО ОТРЕЗКОВ
Оно состоит из двух частей.
1 – правило концентрацийпозволяет определить составы (концентрации) фаз
2- правило рычага – определяет количественные соотношения фаз в процессе кристаллизации для любого сплава системы
1 часть
Чтобы определить концентрацию компонентов в фазах через заданную точку, характеризующую состояние сплава, проводят горизонталь (коноду) до пересечения с линиями, ограничивающими данную область: проекции точек пересечения на ось концентраций дадут составы фаз.
Состав жидкой фазы покажет проекция точки пересечения горизонтали с линией ликвидуса. Другая точка пересечения покажет состав твердой
фазы.
33

vk.com/club152685050 | vk.com/id446425943
2 часть
Чтобы определить количественное соотношение фаз, через заданную точку проводят горизонталь. Отрезки этой линии между заданной точкой и точками, определяющими составы фаз ОБРАТНО ПРОПОРЦИОНАЛЬНЫ КОЛИЧЕСТВАМ ЭТИХ ФАЗ.
Диаграмма состояния сплавов, компоненты которых нерастворимы друг в друге в твердом состоянии
Диаграмма состояния сплавов, компоненты которых нерастворимы друг в друге в твердом состоянии
34

vk.com/club152685050 | vk.com/id446425943
Диаграмма состояния с ограниченной растворимостью компонентов в твердом виде
Диаграмма состояния с ограниченной растворимостью компонентов в твердом виде
35

vk.com/club152685050 | vk.com/id446425943
Диаграмма состояния с устойчивым химическим соединением
Диаграмма состояния с ограниченной растворимостью и, так называемой, перитектической реакцией
36
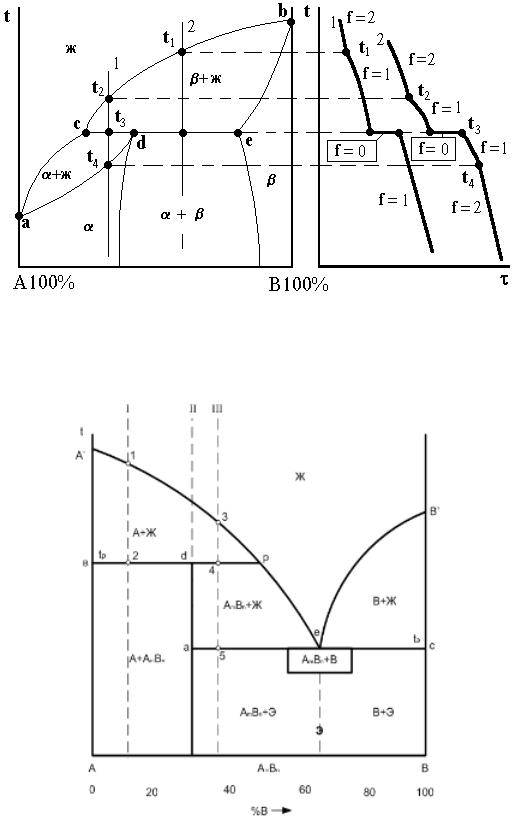
vk.com/club152685050 | vk.com/id446425943
Диаграмма состояния с хим. соединением, образующимся по перитектической реакции
Связь между свойствами сплавов и типом диаграммы состояния
Так как вид диаграммы, также, как и свойства сплава, зависит от того, какие соединения или какие фазы образовали компоненты сплава, то
37
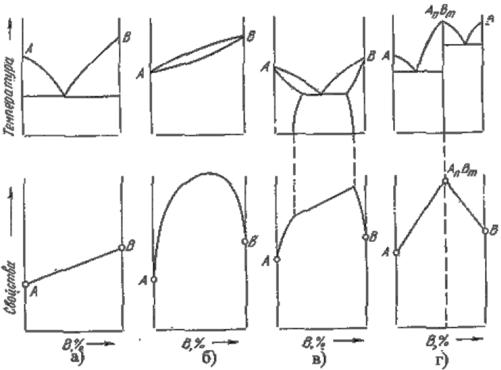
vk.com/club152685050 | vk.com/id446425943
между ними должна существовать определенная связь. Эта зависимость установлена Курнаковым.
Связь между свойствами сплавов и типом диаграммы состояния
При образовании механических смесей свойства изменяются по линейному закону. Значения характеристик свойств сплава находятся в интервале между характеристиками чистых компонентов.
При образовании твердых растворов с неограниченной растворимостью свойства сплавов изменяются по криволинейной зависимости, причем некоторые свойства, например, электросопротивление, могут значительно отличаться от свойств компонентов.
При образовании твердых растворов с ограниченной растворимостью свойства в интервале концентраций, отвечающих однофазным твердым растворам, изменяются по криволинейному закону, а в двухфазной области – по линейному закону. Причем крайние точки на прямой являются свойствами чистых фаз, предельно насыщенных твердых растворов, образующих данную смесь.
38
vk.com/club152685050 | vk.com/id446425943
Лекция 4
«Механические свойства и способы определения их количественных характеристик»
Основными механическими свойствами являются прочность, упругость,
вязкость, твердость.
Зная механические свойства, конструктор обоснованно выбирает соответствующий материал, обеспечивающий надежность и долговечность конструкций при их минимальной массе.
В зависимости от условий нагружения механические свойства могут определяться при:
статическом нагружении – нагрузка на образец возрастает медленно и плавно.
динамическом нагружении – нагрузка возрастает с большой скоростью, имеет ударный характер.
повторно, переменном или циклическим нагружении – нагрузка в процессе испытания многократно изменяется по величине или по величине и направлению.
Для получения сопоставимых результатов образцы и методика проведения механических испытаний регламентированы ГОСТами.
При статическом испытании на растяжение: ГОСТ 1497 получают характеристики прочности и пластичности.
Прочность – способность материала сопротивляться деформациям и разрушению.
Испытания проводятся на специальных машинах, которые записывают диаграмму растяжения, выражающую зависимость удлинения образца (мм) от действующей нагрузки Р, т.е.
Но для получения данных по механическим свойствам перестраивают: зависимость относительного удлинения от напряжения
39

vk.com/club152685050 | vk.com/id446425943
Проанализируем процессы, которые происходят в материале образца при увеличении нагрузки.
Участок оа на диаграмме соответствует упругой деформации материала, когда соблюдается закон Гука. Напряжение, соответствующее упругой предельной деформации в точке а, называется пределом пропорциональности.
Предел пропорциональности ( ) – максимальное напряжение, до которого сохраняется линейная зависимость между деформацией и напряжением.
Так как практически невозможно установить точку перехода в неупругое состояние, то устанавливают условный предел упругости, – максимальное напряжение, до которого образец получает только упругую деформацию. Считают напряжение, при котором остаточная деформация очень мала
(0,005…0,05%).
В обозначении указывается значение остаточной деформации.
Предел текучести характеризует сопротивление материала небольшим пластическим деформациям.
40
vk.com/club152685050 | vk.com/id446425943
Взависимости от природы материала используют физический или условный предел текучести.
Физический предел текучести – это напряжение, при котором происходит увеличение деформации при постоянной нагрузке (наличие горизонтальной площадки на диаграмме растяжения). Используется для очень пластичных материалов.
Но основная часть металлов и сплавов не имеет площадки текучести.
Условный предел текучести– это напряжение вызывающее остаточную деформацию
Вточке в в наиболее слабом месте начинает образовываться шейка – сильное местное утомление образца.
Предел прочности – напряжение, соответствующее максимальной нагрузке, которую выдерживает образец до разрушения (временное сопротивление разрыву).
Образование шейки характерно для пластичных материалов, которые имеют диаграмму растяжения с максимумом.
Предел прочности характеризует прочность как сопротивления значительной равномерной пластичной деформации. За точкой В, вследствие развития шейки, нагрузка падает и в точке С происходит разрушение.
При испытании на растяжение определяются и характеристики пластичности.
Пластичность –– способность материала к пластической деформации, т.е. способность получать остаточное изменение формы и размеров без нарушения сплошности.
Это свойство используют при обработке металлов давлением.
Характеристики:
относительное удлинение -
и Ln и Lk – начальная и конечная длина образца.
41

vk.com/club152685050 | vk.com/id446425943
Лекция 5
«Диаграмма состояния железо-углерод»
Диаграмма состояния железо – углерод дает основное представление о строении железоуглеродистых сплавов – сталей и чугунов.
Начало изучению диаграммы железо – углерод положил Чернов Д.К. в 1868 году. Чернов впервые указал на существование в стали критических точек и на зависимость их положения от содержания углерода.
Железо образует с углеродом химическое соединение: цементит – Fe3C. Каждое устойчивое химическое соединение можно рассматривать как компонент, а диаграмму – по частям. Так как на практике применяют металлические сплавы с содержанием углерода до 6,67 %, то рассматриваем часть диаграммы состояния от железа до химического соединения цементита, содержащего 6,67 %углерода.
42

vk.com/club152685050 | vk.com/id446425943
Диаграмма состояния железо-углерод
Компоненты и фазы железоуглеродистых сплавов
Компонентами железоуглеродистых сплавов являются железо, углерод и цементит.
1. Железо – переходный металл серебристо-светлого цвета. Имеет высокую температуру плавления – 1539o С
Кривая охлаждения чистого железа имеет следующий вид
Железо технической чистоты обладает невысокой твердостью (80 НВ) и прочностью (предел прочности – , и высокими характеристиками
43
vk.com/club152685050 | vk.com/id446425943
пластичности (относительное удлинение – =40%,). Свойства могут изменяться в некоторых пределах в зависимости от величины зерна.
Железо характеризуется высоким модулем упругости, наличие которого проявляется и в сплавах на его основе, обеспечивая высокую жесткость деталей из этих сплавов.
Железо со многими элементами образует растворы: с металлами – растворы замещения, с углеродом, азотом и водородом – растворы внедрения.
2. Углерод относится к неметаллам. Обладает полиморфным превращением, в зависимости от условий образования существует в форме графита с гексагональной кристаллической решеткой (температура плавления – 3500 0С, плотность – 2,5 г/см3) или в форме алмаза со сложной кубической решеткой с координационным числом равным четырем (температура плавления – 5000 0С).
В сплавах железа с углеродом углерод находится в состоянии твердого раствора с железом и в виде химического соединения – цементита (Fe3C), а также в свободном состоянии в виде графита (в серых чугунах).
Компоненты и фазы железоуглеродистых сплавов
3. Цементит (Fe3C) – химическое соединение железа с углеродом (карбид железа), содержит 6,67 % углерода.
Аллотропических превращений не испытывает. Кристаллическая решетка цементита состоит из ряда октаэдров, оси которых наклонены друг к другу.
Температура плавления цементита точно не установлена (1250, 1550o С). При низких температурах цементит слабо ферромагнитен, магнитные свойства теряет при температуре около 217o С.
Цементит имеет высокую твердость (более 800 НВ, легко царапает стекло), но чрезвычайно низкую, практически нулевую, пластичность. Такие свойства являются следствием сложного строения кристаллической решетки.
Цементит – соединение неустойчивое и при определенных условиях распадается с образованием свободного углерода в виде графита. Этот
процесс имеет важное практическое значение при структурообразовании чугунов.
44
vk.com/club152685050 | vk.com/id446425943
Фазы железоуглеродистых сплавов
В системе железо – углерод существуют следующие фазы: жидкая фаза, феррит, аустенит, цементит.
1.Жидкая фаза. В жидком состоянии железо хорошо растворяет углерод в любых пропорциях с образованием однородной жидкой фазы.
2.Феррит (Ф) (C) – твердый раствор внедрения углерода в -железо.
Феррит имеет переменную предельную растворимость углерода: минимальную – 0,006 % при комнатной температуре (точка Q), максимальную – 0,02 % при температуре 727o С (точка P). Углерод располагается в дефектах решетки.
При температуре выше 1392o С существует высокотемпературный феррит () ( (C), с предельной растворимостью углерода 0,1 % при температуре 1499o С (точка J)
Свойства феррита близки к свойствам железа. Он мягок (твердость – 130 НВ, предел прочности 250МПА–) и пластичен (относительное удлинение –40%), магнитен до 768o С.
3. Аустенит (А) (С) – твердый раствор внедрения углерода в -железо.
Углерод занимает место в центре гранецентрированной кубической ячейки.
Аустенит имеет переменную предельную растворимость углерода: минимальную – 0,8 % при температуре 727o С (точка S), максимальную – 2,14 % при температуре 1147o С (точка Е).
Аустенит имеет твердость 200…250 НВ, пластичен (относительное удлинение –), парамагнитен.
При растворении в аустените других элементов могут изменяться свойства и температурные границы существования.
4. Цементит – характеристика дана выше.
В железоуглеродистых сплавах присутствуют фазы: цементит первичный (ЦI), цементит вторичный (ЦII), цементит третичный (ЦIII). Химические и физические свойства этих фаз одинаковы. Влияние на механические свойства сплавов оказывает различие в размерах, количестве и расположении этих выделений. Цементит первичный выделяется из жидкой фазы в виде крупных
45
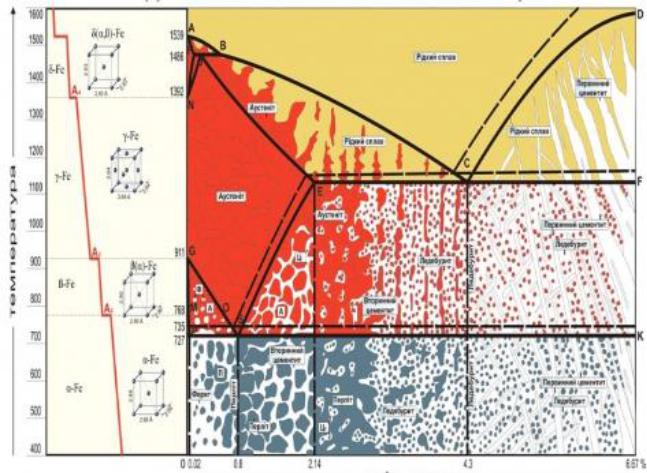
vk.com/club152685050 | vk.com/id446425943
пластинчатых кристаллов. Цементит вторичный выделяется из аустенита и располагается в виде сетки вокруг зерен аустенита (при охлаждении – вокруг зерен перлита). Цементит третичный выделяется из феррита и в виде мелких включений располагается у границ ферритных зерен.
Диаграмма состояния железо-углерод
Процессы при структурообразовании железоуглеродистых сплавов
Линия АВСD – ликвидус системы. На участке АВ начинается кристаллизация феррита (), на участке ВС начинается кристаллизация аустенита, на участке СD – кристаллизация цементита первичного.
Линия AHJECF – линия солидус. – конец кристаллизации
46

vk.com/club152685050 | vk.com/id446425943
На линии HJB при постоянной температуре 14990С идет перитектическое превращение, заключающееся в том, что жидкая фаза реагирует с ранее образовавшимися кристаллами феррита (), в результате чего образуется аустенит LB +Фн→AJ
На участке JЕ заканчивается кристаллизация аустенита. На участке ECF при постоянной температуре 1147o С идет эвтектическое превращение, заключающееся в том, что жидкость, содержащая 4,3 % углерода превращается в эвтектическую смесь аустенита и цементита первичного:
Эвтектика системы железо – цементит называется ледебуритом (Л), по имени немецкого ученого Ледебура, содержит 4,3 % углерода.
При температуре ниже 727o С в состав ледебурита входят цементит первичный и перлит, его называют ледебурит превращенный (ЛП).
По линии GS превращение аустенита в феррит, обусловленное полиморфным превращением железа. По линии PG превращение аустенита в феррит заканчивается.
47
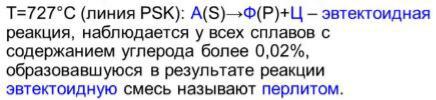
vk.com/club152685050 | vk.com/id446425943
По линии ES начинается выделение цементита вторичного из аустенита, обусловленное снижением растворимости углерода в аустените при понижении температуры.
По линии МО при постоянной температуре 768o С имеют место магнитные
превращения.
Процессы при структурообразовании железоуглеродистых сплавов
По линии PSK при постоянной температуре 727o С идет эвтектоидное превращение, заключающееся в том, что аустенит, содержащий 0,8 % углерода, превращается в эвтектоидную смесь феррита и цементита вторичного:
По механизму данное превращение похоже на эвтектическое, но протекает в твердом состоянии.
Эвтектоид системы железо – цементит называется перлитом (П), содержит 0,8 % углерода.
Название получил за то, что на полированном и протравленном шлифе наблюдается перламутровый блеск.
Перлит может существовать в зернистой и пластинчатой форме, в зависимости от условий образования.
По линии PQ начинается выделение цементита третичного из феррита, обусловленное снижением растворимости углерода в феррите при понижении температуры.
Лекция 6
«Углеродистые стали»
Сталь – основной материал, широко применяемый в машиностроении, строительстве и других отраслях. Она сравнительно недорога и производится в больших количествах.
48

vk.com/club152685050 | vk.com/id446425943
Влияние углерода и постоянных примесей на свойства стали
C увеличением в стали углерода возрастает твердость, временное сопротивление, предел текучести, но уменьшается относительное удлинение, относительное сужение, удельная вязкость.
При содержании в стали углерода более 1% ее твердость возрастает, а временное сопротивление уменьшается. Это объясняется выделением по границам бывшего зерна аустенита вторичного цементита, образующего сплошную сетку. При испытаниях на растяжение в этой сетке возникают высокие напряжения и цементит, будучи хрупким разрушается.
Увеличение содержания углерода сверх 0,4% и уменьшение ниже 0,3% приводит к ухудшению обрабатываемости резанием.
Увеличение содержания углерода снижает технологическую пластичность стали при горячей и в особенности при холодной обработке давлением, ухудшает свариваемость.
Углеродистые стали
Углеродистая сталь – многокомпонентный сплав, содержащий кроме железа и углерода ряд постоянных или неизбежных примесей: Mn , Si, S, P, O, N, H
49

vk.com/club152685050 | vk.com/id446425943
и др. которые оказывают влияние на ее свойства. Эти же примеси, только в больших количествах содержатся и в чугунах.
Структура стали, после медленного охлаждения состоит из феррита и цементита.
ВЛИЯНИЕ МАРГАНЦА И КРЕМНИЯ
Содержание кремния в виде примеси составляет обычно до 0,4%, марганца – до 0,5-0,8%.
Марганец и кремний переходят в сталь в процессе ее раскисления при выплавке. Они раскисляют сталь, т.е с кислородом закиси железа FeO , в виде окислов переходят в шлак. Раскисление улучшает свойства сталей. Кремний, дегазируя металл, повышает плотность слитка.
Кремний сильно повышает предел текучести стали.
Марганец повышает прочность стали, не снижая ее пластичности. Марганец уменьшает вредное влияние серы и кислорода.
ВЛИЯНИЕ СЕРЫ Сера является вредной примесью. Образуя с железом химическое
соединение FeS и реагируя с железом оно образует легкоплавкую эвтектику с температурой плавления 988 оС. Эвтектика образуется даже при очень малых количествах серы. Кристаллизуясь из жидкости, эвтектика располагается по границам зерен, при нагреве стали до температур прокатки или ковки (10001200о) эвтектика расплавляется, нарушая связь между зернами.
В местах расположения эвтектики возникают надрывы и трещины. Это явление называется красноломкость
FeS + Mn = Mn + Fe
Т.е. марганец уменьшает красноломкость
50

vk.com/club152685050 | vk.com/id446425943
Сернистые соединения сильно снижают механические свойства, особенно ударную вязкость и пластичность.
Содержание серы не должно превышать 0,035 – 0,06 %
ВЛИЯНИЕ ФОСФОРА Фосфор – вредная примесь.
Содержание его не должно превышать 0,025 – 0,045 %.
Растворяясь в феррите, фосфор сильно искажает кристаллическую решетку, увеличивает временное сопротивление и снижает пластичность и вязкость.
Фосфор обладает большой склонностью к ликвации.
ВЛИЯНИЕ АЗОТА, КИСЛОРОДА и ВОДОРОДА
Азот и кислород присутствуют в стали в виде хрупких неметаллических включений (например, окислов FeO SiO2 Al O3 , нитридов, и др. ). Они являются концентратами напряжений, сильно понижают предел выносливости, вязкость.
Очень вредным является растворенный в стали водород, который сильно охрупчивает сталь. Он приводит к образованию в катанных заготовках и крупных поковках флокенов. Это очень тонкие трещины овальной или округлой формы, имеющие в изломе вид пятен – хлопьев серебристого цвета. Флокены резко ухудшают свойства сталей. Металл, имеющий флокены нельзя использовать в промышленности.
КЛАССИФИКАЦИЯ УГЛЕРОДИСТЫХ СТАЛЕЙ
1. по химическому составу они могут быть:
-низкоуглеродистыми ( менее 0,3 % С) -среднеуглеродистые ( 0,3-0,6 % С)
51

vk.com/club152685050 | vk.com/id446425943
-высокоуглеродистые ( свыше 0,7 % С)
2. по качеству:
-стали обыкновенного качества -качественные -высококачественные
Под качеством стали понимают совокупность свойств, определяемых металлургическим процессом ее производства.
Это и однородность химического состава, строения, свойств, а также ее технологичность – все это зависит от содержания в стали газов – кислорода, азота и водорода, а также таких вредных примесей как сера и фосфор.
Нормы содержания
Стали обыкновенного качества содержат до 0,06% серы и 0,07 % фосфора Качественные стали - не более 0,04 % серы и 0,03 % фосфора Высококачественные - не более 0,025 % серы и 0,025 % фосфора Особовысококачественные - не более 0,015 % серы и 0,025 % фосфора
3. По способу производства: стали подразделяются на: Бессемеровскую Мартеновскую Кислородно-конвертерную Электростали
4.По способу раскисления и характеру затвердевания -Спокойные (СП)
-Полуспокойные (ПС) -Кипящие (КП)
Раскисление – это процесс удаления из жидкого металла кислорода, проводимый для предотвращения хрупкого разрушения стали при горячей деформации.
Спокойные стали – раскисляют марганцем, кремнием, алюминием. Они содержат мало кислорода и затвердевают спокойно без газовыделений.
52

vk.com/club152685050 | vk.com/id446425943
Кипящие стали – раскисляют только марганцем. Перед разливкой в них содержится повышенное количество кислорода, который при затвердевании, частично взаимодействия с углеродом, удаляется в виде СО. Выделение пузырей СО создает впечатление кипения стали, с чем и связано ее название.
Кипящие стали дешевы и практически без кремния, но с повышенным количеством газообразных примесей.
Полуспокойные стали – промежуточные между кп и сп.
5. По назначению стали подразделяются на:
-конструкционные – (идущие для изготовления деталей машин и приборов, конструкций, подвергающихся механическим нагрузкам). Основное требование, предъявляемое к ним – конструкционная прочность. Как правило, они содержат до 0,6 % С -инструментальные – ( идущие для изготовления инструментов) Главное
требование – высокая твердость и износостойкость. Содержание углерода в них как правило более 0,6% С.
На долю углеродистых сталей приходится 80% от общего объема . Это объясняется тем, что данные стали относительно дешевы и сочетают удовлетворительные механические свойства с хорошей обрабатываемость резанием и давлением.
Углеродистые стали выпускаются обыкновенного качества и высококачественные.
Эти стали выпускают по ГОСТ 380-94.
Они наиболее дешевы, в них допускается повышенное содержание вредных примесей, а также газонасыщенность и загрязненность неметаллическими включениями.
Углеродистую сталь обыкновенного качества изготавливают следующих марок:
Ст0 Ст1кп |
Ст2кп |
Ст3кп |
Ст4 кп |
Ст5пс |
Ст6 пс |
Ст1 пс |
Ст2пс |
Ст3пс |
Ст4пс |
Ст5сп |
Ст6сп |
Ст1сп |
Ст2сп |
Ст3сп |
Ст4сп |
Ст5Гпс |
|
|
|
Ст3Гпс |
|
|
|
|
|
Ст3Гсп |
|
|
|
Буквы Ст – обозначают «сталь», цифра – условный номер марки в зависимости от химического состава, кп,сп, пс – степень раскисления.
|
Марка стали |
|
Массовая доля элементов |
|
|
53

vk.com/club152685050 | vk.com/id446425943
|
Углерод |
|
Марганец |
|
Кремний |
|
|
|
|||
Ст0 |
Не более 0,23 |
|
- |
|
- |
Ст1кп |
0,06-0,12 |
|
0,25-0,50 |
|
Не более 0,05 |
Ст1пс |
-«- |
|
-«- |
|
0,05-0,15 |
Ст1сп |
-«- |
|
-«- |
|
0,15-0,30 |
Ст2кп |
0,09-0,15 |
|
0,25-0,50 |
|
Не более 0,05 |
Ст2пс |
-«- |
|
-«- |
|
0,05-0,15 |
Ст2сп |
-«- |
|
-«- |
|
0,15-0,30 |
Ст3кп |
0,14-0,20 |
|
0,30-0,60 |
|
Не более 0,05 |
Ст3пс |
-«- |
|
0,40-0,65 |
|
0,05-0,15 |
Ст3сп |
-«- |
|
0,40-0,65 |
|
0,15-0,30 |
Ст3Гпс |
-«- |
|
0,8-1,1 |
|
не более 0,15 |
Ст3Гсп |
-«- |
|
0,8-1,1 |
|
0,15-0,30 |
Ст4кп |
0,18-0,27 |
|
0,40-0,70 |
|
Не более 0,05 |
Ст4пс |
|
|
|
|
0,05-0,15 |
Ст4сп |
|
|
|
|
0,15-0,30 |
Ст5пс |
0,28-0,37 |
|
0,5-0,8 |
|
0,05-0,15 |
Ст5сп |
0,28-0,37 |
|
-«- |
|
0,15-0,30 |
Ст5Гпс |
0,22-0,30 |
|
0,8-1,2 |
|
не более 0,15 |
Ст6пс |
0,38-0,49 |
|
0,5-0,8 |
|
0,05-0,15 |
Ст6сп |
-«- |
|
0,5-0,8 |
|
0,15-0,30 |
В стали марки Ст0 – массовая доля марганца и кремния не нормируется Массовая доля серы в стали всех марок, кроме Ст0, должна быть не более 0,050 %, фосфора – не более 0,040 %.
УГЛЕРОДИСТЫЕ СТАЛИ ОБЫКНОВЕННОГО КАЧЕСТВА
Из сталей обыкновенного качества изготавливается горячекатанный рядовой прокат: балки, швеллеры, уголки прутки, а также листы, трубы, поковки.
Эти стали в состоянии поставки широко применяются в строительстве для сварных, клепанных и болтовых конструкций, реже – для изготовления малонагруженных деталей машин (валы, оси, зубчатые колеса и др.)
Кипящие стали, содержащие повышенное количество кислорода, имеют порог хладноломкости на 30-40 градусов выше, чем стали спокойные. Поэтому для ответственных сварных конструкций, а также работающих при низких климатических температурах применяют спокойные стали.
54

vk.com/club152685050 | vk.com/id446425943
С повышением процента углерода свариваемость стали ухудшается. Поэтому стали марок СТ5 и Ст6 применяют для элементов конструкций, не подвергаемых сварке.
-Хорошая – при С менее 0,3%С -Удовлетворительная – от 0,3 до0,35 %С -Огра Свариваемость:
ниченная – 0,4-0,5%С -Плохая – при С более0,5%С
УГЛЕРОДИСТЫЕ КАЧЕСТВЕННЫЕ СТАЛИ
ГОСТ 1050-88
Эти стали выплавляют с соблюдением более строгих условий в отношении состава шихты и ведения плавки и разливки. К ним предъявляют более высокие требования по хим. Составу и структуре.
Содержание серы - не более 0,04 % фосфора – не более 0,035-0,04 %
Различают следующие марки качественных углеродистых сталей:
08, 10, 15, 20, 25, 30, 35, 40, 45, 50, 55, 60, 65
Цифра – показывает среднее содержание углерода в сотых долях процента Спокойные стали маркируются без индекса, полуспокойные и кипящие с индексомпс или кп.
Низкоуглеродистые стали (С менее 0,25%)
55

vk.com/club152685050 | vk.com/id446425943
05кп, 08,10,10кп – обладают невысокой прочностью и высокой пластичностью
Ϭ = 330-340 Мпа, δ= 33-31 %
Их без термической обработки применяют для малонагруженных деталей,. Эти стали в основном производят в виде тонкого листа, их можно использовать в автомобилестроении для деталей сложной формы, они легко штампуются из-за малого содержания углерода в них. Глубокая вытяжка из листа этих сталей применяется при изготовлении консервных банок, эмалированной посуды и др.
Стали 15,15кп,20,25 (Ϭ =380-460 Мпа, δ =27-23 % ) применяют либо без термообработки или в нормализованном состоянии, а также для деталей упрочняемых цементацией. Они пластичны, хорошо свариваются и штампуются. Их используют для изготовления крепежных деталей, валиков, осей.
Среднеуглеродистые стали (0,3-0,5%С)
56
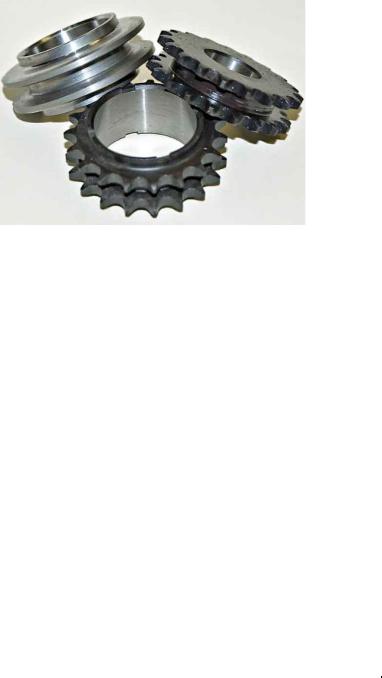
vk.com/club152685050 | vk.com/id446425943
30,35,40,45,50,55 – применяются после термической обработки для самых разнообразных деталей во всех отраслях машиностроения – небольшие валы, шатуны, зубчатые колеса и детали, испытывающие циклические нагрузки.
Так поле улучшения (закалка и высокий отпуск) сталь марки 45 имеет Ϭ = 600-700Мпа.
ХИМИЧЕСКИЙ СОСТАВ И МЕХАНИЧЕСКИЕ СВОЙСТВА УГЛЕРОДИСТОЙ КАЧЕСТВЕННОЙ СТАЛИ
Марка |
Содержание |
Механические свойства, не менее |
|
||
стали |
углерода |
|
|
|
|
|
|
|
|
|
|
|
|
|
|
|
НВ |
|
|
МПа |
МПа |
% |
|
08 |
0,05-0,01 |
330 |
200 |
33 |
131 |
10 |
0,07-0,14 |
340 |
210 |
31 |
143 |
15 |
0,12-0,19 |
380 |
230 |
27 |
149 |
20 |
0,17-0,24 |
420 |
250 |
25 |
163 |
30 |
0,27-0,35 |
500 |
300 |
21 |
179 |
40 |
0,37-0,45 |
580 |
340 |
19 |
217 |
50 |
0,47-0,55 |
640 |
380 |
14 |
241 |
60 |
0,57-0,65 |
690 |
410 |
12 |
255 |
70 |
0,67-0,75 |
730 |
430 |
9 |
269 |
Высокоуглеродистые стали
57

vk.com/club152685050 | vk.com/id446425943
60,65,70 –в основном используются для изготовления пружин и рессор, высокопрочной проволоки с высокой упругостью и износостойкостью. Их подвергают закалке и среднему отпуску.
Инструментальные углеродистые стали ГОСТ 1435-90
У7, У8, У8АГ, У9, У10, У11, У12, У13
Маркируются буквой У и цифрами, показывающими среднюю массовую долю углерода в десятых долях %.
Г – повышенная массовая доля марганца
Данные стали классифицируют:
1. По химическому составу -качественные -высококачественные (серы 0,02 фосфора 0,02 )
В марках высококачественных сталей добавляется буква «А» У7А, У8А, У8Г, У9А, У10А, У11А, У12А, У13А 2. По назначению для продукции всех видов, кроме п.2
для патентированной проволоки и ленты для продукции всех видов, технология которой предусматривает многократный нагрев 3.По состоянию материала Без термообработки
Термически обработанная –Т
58

vk.com/club152685050 | vk.com/id446425943
Нагартованная – Н 4. По способу дальнейшей обработки
а. Для горячей обработки давлением б. Для холодной механической обработки
Пример условного обозначения: У12-3-б-Т ГОСТ 1435-90
Сталь марки У12, 3 группыдля продукции, технология изготовления которой предусматривает многократный нагрев, подгруппы б – для холодной механической обработки, термически обработанная.
Стали данной группы имеют небольшую прокаливаемость , из них изготавливают инструмент небольших размеров. Твердость их снижается при нагреве до 190-200 градусов С.
Это фрезы, зенкеры, ножовки, напильники, бритвы, острый хирургический инструмент.
Высококачественные стали имеют тоже назначение, что и качественные, но для инструмента с более тонкой режущей кромкой.
Автоматные стали ГОСТ 1414-75
Это стали с улучшенной обрабатываемостью резанием. Достигается это введением в конструкционную сталь серы, свинца, фосфора. Эти добавки и образуемые ими включения создают как бы внутреннюю смазку, снижающую в зоне резания трение между инструментом и стружкой и облегчающие измельчение стружки.
Автоматные стали маркируют буквой «А»- автоматная, присутствие свинца обозначается С» «. Цифра – среднее содержание углерода в сотых долях процента Например, А11, А12, А20, А30, А35, А40Г, содержащих соответственно
углерода –0,11%, 0,12%, 0,2%, 0,3%, 0,4%
Буква Г –указывает на присутствие марганца.
АС14, АС40, АС35
Содержание Рв=0,15-0,35% Марганца 0,7-1,55%
Серы 0,08-0,3%
Фосфора 0,050 0,15%
59

vk.com/club152685050 | vk.com/id446425943
Эти стали широко применяются на автомобильных заводах для изготовления многих деталей двигателей.
При обработке автоматных сталей отсутствует налипание металла на инструмент, поверхность резания получается гладкая, блестящая.
Однако, как известно, сера и фосфор снижают качество стали. Автоматным сталям свойственна анизотропия механических свойств, пониженная вязкость, пластичность и особенно сопротивление усталости. Это обстоятельство, а также низкая их коррозионная стойкость ограничивают их применение для изготовления ответственных деталей машин.
Стали А11, А12, А20 используют для крепежных деталей, а также малонагруженных деталей сложных форм.
Химический состав автоматных сталей
|
Марка |
|
|
Содержание элементов |
|
|
|
|
|
|
|
|
|
|
|
|
||||
|
|
|
|
|
|
|
|
|
|
|
|
|
|
|
||||||
|
стали |
|
|
|
|
|
|
|
|
|
|
|
|
|
|
|
|
|
|
|
|
|
|
|
|
|
|
|
|
|
|
|
|
|
|
|
|
|
|
|
|
|
|
|
|
С |
|
|
Mn |
|
|
Si |
|
|
S |
|
|
P |
|
|
Pb |
|
|
|
|
|
|
|
|
|
|
|
|
|
|
|
|
|
|
|
|
|
|
|
А11 |
|
|
0,07-0,15 |
|
|
0,1 |
|
|
0,8-1,2 |
|
|
0,15-0,25 |
|
|
0,10 |
|
|
- |
|
|
|
|
|
|
|
|
|
|
|
|
|
|
|
|
|
|
|
|
|
|
|
А20 |
|
|
0,17-0,24 |
|
|
0,7-1,0 |
|
|
0,15-0,35 |
|
|
0,08-0,15 |
|
|
0,06 |
|
|
- |
|
|
|
|
|
|
|
|
|
|
|
|
|
|
|
|
|
|
|
|
|
|
|
А30 |
|
|
0,27-0,35 |
|
|
0,7-1,0 |
|
|
0,15-0,35 |
|
|
0,08-0,15 |
|
|
0,06 |
|
|
- |
|
|
|
|
|
|
|
|
|
|
|
|
|
|
|
|
|
|
|
|
|
|
|
А40Г |
|
|
0,37-0,45 |
|
|
1,2-1,55 |
|
|
0,15-0,35 |
|
|
0,18-0.3 |
|
|
0,05 |
|
|
- |
|
|
|
|
|
|
|
|
|
|
|
|
|
|
|
|||||||
|
|
|
|
|
|
|
|
|
|
|
|
|
|
|
|
|
|
|
|
|
|
АС14 |
|
|
0,1-0,17 |
|
|
1,0-1,3 |
|
|
0,12 |
|
|
0,15-0,20 |
|
|
0,05 |
|
|
0,15-0,3 |
|
|
|
|
|
|
|
|
|
|
|
|
|
|
|
|
|
|
|
|
|
|
Применение автоматных сталей позволяет в 2-3 раза снизить расход инструмента и до 30% повысить производительность.
Лекция 7
«ЧУГУНЫ»
Чугуны - это сплавы железа, содержащие от 2,14 до 6,67% углерода.
Чугуны – более дешевый материал, чем стали.
Они обладают пониженной температурой плавления, хорошими литейными свойствами. За счет этого из чугунов можно делать отливки более сложных форм, чем из сталей.
60

vk.com/club152685050 | vk.com/id446425943
Чугуны плохо деформируются (в обычных условиях не поддаются ковке). Благодаря сочетанию высоких литейных свойств с достаточно высокой прочностью и износостойкостью, а также относительной дешевизне чугуны широко применяются в машиностроении.
Детали машин, полученные из чугунных отливок, значительно дешевле, чем детали, изготовленные обработкой резанием из горячекатанных стальных профилей или из поковок или штамповок.
Значительная часть выплавляемого чугуна переплавляется в сталь по классической схеме – руда -чугун- сталь
В зависимости от того, в каком состоянии находится углерод в сплавах, различают следующие виды чугунов:
белые - углерод или часть его находится в связанном состоянии
серые- углерод или часть его находится в виде графита пластинчатой формы
высокопрочные - графит шаровидной формы
ковкие - графит в виде хлопьев
Возможные формы графита в чугунах.
1- пластинчатый,
2- мелкопластинчатый (вермикулярный),
61

vk.com/club152685050 | vk.com/id446425943
3- хлопьевидный,
4- шаровидный графит.
В структуре чугунов с графитом различают включения графита и металлическую основу, которая может быть - ферритная, ферритоперлитная или перлитная.
Влияние компонентов и скорости охлаждения на свойства чугунов
На образование той или иной структуры оказывает влияние его химический состав и скорость охлаждения отливки.
Углерод в обычных серых чугунах содержится в пределах 2,7-3,7 %. Выделение графита увеличивается с повышением % углерода в чугунах.
Кремний, как и углерод способствует процессу графитизации. Содержание кремния в чугунах колеблется от 0,3 до 5%.
Марганец растворяется в чугунах, образуя твердые растворы. Марганец препятствует процессу графитизации и способствует отбелу чугуна. Содержание его обычно колеблется в пределах 0,5-0,8 %.
62

vk.com/club152685050 | vk.com/id446425943
Фосфор не оказывает влияния на процесс графитизации, фосфор повышает хрупкость чугунов за счет образования фосфидовхимических соединений.
Фосфор повышает жидкотекучесть чугунов, в художественных отливках его до 1%.В ответственных отливках- 0,2-0,3%
Сера - вредная примесь, ухудшает литейные свойства. Содержание ее в чугунах до 0,12 %.
Влияние скорости охлаждения на структуру чугунов
Структурные диаграммы чугуна. Зависимости структуры от содержания углерода и кремния, и толщины отливки (стенки). 1 - белые, 2 - половинчатые, 3 - серые перлитные, 4 - серые перлито - ферритные, 5 - ферритные серые чугуны.
Белый чугун
Такое название он получил по виду излома, который имеет белый, блестящий вид. Углерод в белом чугуне находится в связанном состоянии, в виде цементита. Фазовые превращения в нем происходят согласно диаграмме состояния железо-углерод.
В зависимости от содержания углерода белые чугуны могут быть
доэвтектическими ( перлит +цементит + ледебурит),
эвтектическими (ледебурит)
заэвтектическими ( цементит и ледебурит)
63

vk.com/club152685050 | vk.com/id446425943
Микроструктуры белых чугунов
Эти чугуны имеют очень большую твердость (НВ 450-550) из-за присутствия в них большого количества цементита. Как следствие этого, они очень хрупкие и для изготовления деталей машин не используются.
Применение белого чугуна:
Отливки из белого чугуна служат для получения деталей из ковкого чугуна. Из белых чугунов изготавливают отливки простой формы, обладающие высокой износостойкостью – валки листовых прокатных станов, шаровые мельничные колеса, тормозные колодки, буровые шарошки и другие детали, работающие в условиях износа.
Серый чугун
Такое название чугун получил по виду излома, который имеет серый цвет.
В структуре серого чугуна весь углерод или его часть находится в виде графита.
Графит - это аллотропическая модификация чистого углерода ( другой модификацией является алмаз - это редкая форма в сплавах не встречается.
Кристаллическая решетка графита - гексагональная, слоистая, что делает графит малопрочным и мягким (не превышает 3НВ).
Процесс образования в чугунах графита называется графитизацией.
Серые чугуны обладают хорошими литейными свойствами, хорошо обрабатывается резанием, сопротивляется износу, обладает высокой демпфирующей способностью - т.е. способностью гасить вибрации - 2-4 раза выше, чем у сталей.
Все эти свойства обусловили применение серого чугуна для изготовления:
станин различного оборудования
коленчатых и распределительных валов тракторных и автомобильных двигателей
64

vk.com/club152685050 | vk.com/id446425943
в станкостроении - базовые корпусные детали, кронштейны, зубчатые колеса, направляющие
в автомобилестроении -блоки цилиндров, гильзы. поршневые кольца, распределительные валы, головки цилиндров, диски сцепления
ГОСТ 1412-85 Чугун с пластинчатым графитом для отливок
Для изготовления отливок предусмотрены следующие марки:
СЧ10 СЧ15 СЧ20 СЧ25 СЧ30 СЧ35
По требованию потребителей допускаются марки –
СЧ18 СЧ21 СЧ24
Цифра -величина минимального временного сопротивления при растяжении
в МПА 10-1
Обозначение: СЧ10 ГОСТ 1412-85
|
|
|
|
Серый чугун |
|
|
Марка |
|
|
Применение |
|
|
|
|
|
|
|
|
|
|
|
||
|
Сч10 |
|
|
неответственное литье, печное литье, канализационные |
|
|
|
|
|
трубы, строительные колонны, фундаментные плиты, |
|
|
|
|
|
крышки, кожуха, корпуса |
|
|
|
|
|
|
|
|
Сч15 Сч18 |
|
|
машиностроительные отливки, станины, корпуса, шкивы |
|
|
Сч20 |
|
|
|
|
|
|
|
|
|
|
|
Сч25 Сч30 |
|
|
ответственные отливки |
|
|
|
|
|
||
|
Сч35 |
|
|
|
|
|
|
|
|
|
|
Наименее прочные чугуны на ферритной основе.
Серый чугунэто "сталь, испорченная графитом", графит имеет ничтожную прочность, играет роль надрезов, трещин, разопрочняющих чугун.
Серому литейному чугуну (на любой основе) свойственны почти полное отсутствие относительного удлинения и очень низкая ударная вязкость.
65

vk.com/club152685050 | vk.com/id446425943
Помимо отрицательных сторон пластинчатого графита необходимо знать и положительную его роль:
графит улучшает обрабатываемость резанием, т.е. образуется ломкая стружка
улучшает антифрикционные свойства, играя роль смазки
благодаря графиту быстро гасятся вибрации (микро пустоты заполненные графитом)
делает чугун нечувствительным к концентрациям напряжений.
Серый чугун повышенной прочности имеет перлитную основу и более мелкие, завихренные пластины графита. Прочность их обеспечивается модифицированиеим.
Модификаторами служат ферросилиций, силикокальций, их добавляют в количестве 0,1-0,3 % от массы чугуна прямо в ковш при заливке.
Высокопрочные чугуны
Высокопрочным называют чугуны, в которых графит имеет шаровидную форму. Его получают присадкой в жидкий чугун небольших добавок щелочных или щелочноземельных металлов, чаще всего это магний в количестве 0,03-0,07%. По содержанию остальных элементов высокопрочный чугун не отличается от серого.
66

vk.com/club152685050 | vk.com/id446425943
Шаровидный графит является менее сильным концентратором напряжений, чем пластинчатый графит и поэтому значительно меньше ослабляет металлическую основу. Высокопрочный чугун обладает более высокими механическими свойствами. Он имеет хорошие литейные свойства, хорошо обрабатывается резанием, гасит вибрации, имеет высокую износостойкость, удовлетворительно сваривается.
По ГОСТ 7293-85 производится 8 марок высокопрочных чугунов.
ГОСТ 7293-85 Чугун с шаровидным графитом для отливок
Марки: ВЧ35,ВЧ40, ВЧ45, ВЧ50, ВЧ60, ВЧ70,ВЧ80, ВЧ100
Обозначение: ОТЛИВКА ВЧ 60 ГОСТ 7293-85
Цифра – минимальное значение временного сопротивления при растяжении в Мпа 10-1 Марка чугуна определяется его временным сопротивлением при растяжении
и условным пределом текучести.
Высокопрочные чугуны |
|
|
|
|
|
|
||
|
|
|
|
|
|
|
|
|
|
Марка чугуна |
|
|
|
Временное |
|
Условный предел |
|
|
|
|
|
|
сопротивление при |
|
текучести |
Мпа |
|
|
|
|
|
растяжении Мпа кг/мм2 |
|
кг/мм2 |
|
|
|
|
|
|
|
|
|
|
|
|
|
|
|
||||
|
ВЧ35 |
|
|
|
350 (35) |
|
220 (22) |
|
|
|
|
|
|
|
|
|
|
|
ВЧ40 |
|
|
|
400(40) |
|
250(25) |
|
|
|
|
|
|
|
|
|
|
|
ВЧ45 |
|
|
|
450(45) |
|
310(31) |
|
|
|
|
|
|
|
|
|
|
|
ВЧ50 |
|
|
|
500(50) |
|
320(32) |
|
|
|
|
|
|
|
|
|
|
|
ВЧ100 |
|
|
|
1000(100) |
|
700(70) |
|
|
|
|
|
|
|
|
|
|
Высокопрочные чугуны обладают высоким пределом текучести, выше, чем у стальных отливок.
Химический состав ВЧ следующий: 3,1-3,2%С, 2,6-2,9 % кремния, 0,6-0,8
%Мп, до 0,12%Р, до 0,03% серы, 0,02-0,03% магния.
67

vk.com/club152685050 | vk.com/id446425943
Сочетая в себе высокие физико-механические свойства, высокопрочный чугун может быть использован взамен обычного серого чугуна, кованной и литой стали, а также сплавов на основе меди во многих отраслях машиностроения. Это - шпиндели карусельных станков, детали кузнечнопрессового оборудования, изложницы для разливки стали, штампы, коленчатые валы, поршневые кольца, картеры, кронштейны, подшипники качения, детали ходовой части тепловозов., подъемно-транспортные устройства, корпуса паровых турбин и др.
Ковкие чугуны
Ковкими называют чугуны, в которых графит имеет хлопьевидную форму.
Ковкие чугуны – условное название более пластичного по сравнением с серым чугуна. Их получают в результате специального графитизирующего отжига доэвтектического белого чугуна.
68

vk.com/club152685050 | vk.com/id446425943
При производстве ковкого чугуна очень важно, чтобы отливки белого чугуна, подвергаемого отжигу, были тонкостенными (не более 40-50мм) , в противном случае в сердцевине при кристаллизации будет выделяться пластинчатый графит и чугун станет непригодным для отжига.
График отжига белого чугуна для получения ковкого
Химический состав белого чугуна, отжигаемого на ковкий чугун, выбирается в пределах:
2,5-3,0 %С 0,7-1,5 % кремния, 0,3- 1,0 % Мп , серы менее 0,12%, Р менее
0,18%
Для ускорения отжига чугун модифицируют алюминием, выполняют отжиг в защитной атмосфере. В этом случае длительность процесса отжига уменьшается до 24-60 часов.
Металлическая основа ковкого чугуна может быть ферритной. Либо перлитной. Излом ферритного ковкого чугуна – бархатисто черный вследствие большого количества графита.
При перлитной основе (отсутствует выдержка ниже эвтектоидного интервала температур), излом у такого чугуна – светлый – сталистый.
69

vk.com/club152685050 | vk.com/id446425943
По ГОСТ 1215-79 ковкие чугуны маркируют:
КЧ37-12
Первая цифра – временное сопротивление в кг/мм2, вторая – относительное удлинение в %
Обозначение - Отливка КЧ30-6–Ф ГОСТ 1215-79
Отливка КЧ60-3-П ГОСТ 1215-79
Ф – обозначает – ферритного класса
П – обозначает -перлитного класса Марки ковких чугунов:
КЧ30-6, КЧ33-8, КЧ35-10, КЧ37-12, КЧ 45-7, КЧ50-5, КЧ55-4, КЧ60-3, КЧ65-3
Из отливок ковкого чугуна изготавливают детали, работающие при ударных и вибрационных нагрузках
Марка чугуна |
Применение |
|
|
|
|
КЧ37-12, КЧ35-10 (Ф Детали, эксплуатируемые при основа) высоких динамических и
статических нагрузках – картеры редукторов, ступицы, крюки, скобы
70

vk.com/club152685050 | vk.com/id446425943
КЧ30-6, КЧ33-8 (Ф Менее ответственные детали – основа) головки, хомутики, гайки, глушители,
фланцы, муфты
КЧ50-5, КЧ 55-4 (П Вилки карданных валов, звенья и основа) ролики цепей конвейера, втулки,
муфты, тормозные колодки
Ковкие чугуны широко применяются в сельскохозяйственном, автомобильном, текстильном машиностроении, в судо, -котло,- вагоно и дизелестроении.
Недостаток – высокая стоимость из-за длительного отжига.
|
Чугун |
|
|
Ϭв |
|
δ |
% |
|
НВ |
|
|
|
|
|
|
|
|||||
|
|
|
|
МПа |
|
|
|
|
|
|
|
|
|
|
|
|
|
|
|||
|
КЧ 30-6 |
|
|
300 |
|
6 |
|
|
100-163 |
|
|
|
|
|
|
|
|
|
|||
|
КЧ 37-12 |
|
|
370 |
|
12 |
|
|
110-163 |
|
|
|
|
|
|
|
|
|
|||
|
КЧ 60-3 |
|
|
600 |
|
3 |
|
|
200-269 |
|
Лекция 8 «Термическая обработка
Теория термической обработки»
Термической или тепловой обработкой называются процессы, связанные с нагревом, выдержкой и охлаждением с целью изменения структуры сплава и получения необходимых свойств.
ТО самый распространенный в современной технике способ изменения свойств металлов и сплавов.
ТО может быть применения как промежуточная операция для улучшения технологических свойств ( обрабатываемости резанием, давлением и т.д.) и как окончательную операцию для придания сплаву комплекса свойств, которые обеспечивают необходимые эксплуатационные характеристики изделия .
71

vk.com/club152685050 | vk.com/id446425943
Чем ответственнее конструкция, тем больше в ней термически обработанных деталей.
ЦЕЛЬЮ ТО – является изменение свойств металла путем изменения его структуры.
ОСНОВНЫЕ ФАКТОРЫ ТО – температура и время.
Поэтому режим любой термообработки можно представить графически в координатах температура и время
По этому графику можно определить температуру нагревания, время нагрева, выдержки, охлаждения, общую производительность производственного цикла. График может быть и более сложного вида. Но по форме этого графика нельзя сказать, с каким видом ТО мы имеем дело.
72

vk.com/club152685050 | vk.com/id446425943
ВИД ТЕРМИЧЕСКОЙ ОБРАБОТКИ ОПРЕДЕЛЯЕТСЯ НЕ ХАРАКТЕРОМ ИЗМЕНЕНИЯ ТЕМПЕРАТУРЫ ВО ВРЕМЕНИ, А ТИПОМ ФАЗОВЫХИ СТРУКТУРНЫХ ИЗМЕНЕНИЙ В МЕТАЛЛЕ.
Термическая обработка ТО - заключается только в термическом воздействии на металл.
Термомеханическая ТМО – заключается в сочетании термического воздействия и пластической деформации
Химико-термическая обработка ХТО- |
в сочетании термического и |
химического воздействия. |
|
•Отжиг (первого рода) – термическая операция, состоящая в нагреве металла, имеющего неустойчивое состояние в результате предшествующей обработки, и приводящая металл в более устойчивое состояние.
73

vk.com/club152685050 | vk.com/id446425943
•Отжиг (второго рода) – нагрев металла выше температуры превращения с последующим достаточно медленным охлаждением для получения структурно устойчивого состояния сплава.
•Закалка – нагрев металла выше температуры превращения с последующим достаточно быстрым охлаждением для получения структурно неустойчивого состояния сплава.
•Отпуск – нагрев закаленного сплава ниже температуры превращения для получения более устойчивого структурного состояния .
Химико-термическая обработка – нагрев сплава в соответствующих химических реагентах для изменения состава и структуры поверхностных слоев. В данном случае используется способность металлов растворять различные, окружающие их поверхность элементы, атомы которых, при повышенных температурах, могут диффундировать в металлы.
Термомеханическая (термопластическая) обработка – деформация и последующая термическая обработка, сохраняющая в той или иной форме результаты наклепа
В системе железо-углеродистых сплавов приняты следующие обозначения критических температур.
Нижняя критическая точка – Ас1 соответствует линии PSK при охлаждении – Аr1
Верхняя критическая точка – Асз соответствует линии GOS при охлаждении – Аr 3
74
vk.com/club152685050 | vk.com/id446425943
Температура линии SE – обозначается Асm
РОСТ ЗЕРНА АУСТЕНИТА ПРИ НАГРЕВЕ
Зародыши аустенита при нагреве выше Ас1 образуются на границе раздела феррит-карбид. При таком нагреве число зародышей всегда велико и начальное зерно аустенита мелкое.
При дальнейшем повышении температуры и увеличении выдержки происходит рост зерна.
Способность зерна аустенита к росту неодинакова даже у сталей одного марочного состава и зависит от условий выплавки.
По склонности к росту зерна различают два типа сталей:
наследственно мелкозернистые наследственно крупнозернистые
В наследственно мелкозернистых сталях при нагреве до высоких температур (1000-1050оС) зерно увеличивается незначительно, однако при более высоком нагреве наступает бурный рост зерна.
В наследственно крупнозернистых сталях наоборот сильный рост зерна наблюдается даже при незначительном перегреве выше Ас1
75

vk.com/club152685050 | vk.com/id446425943
ПРЕВРАЩЕНИЕ АУСТЕНИТА ПРИ НЕПРЕРЫВНОМ ОХЛАЖДЕНИИ
Нагреем эвтектоидную сталь до аустенитного состояния. При медленном охлаждении ее на линии эвтектоидного превращения происходит полный распад аустенита с образованием перлита
А Ф+Ц
Это превращение идет диффузионно и состоит из следующих этапов:
перестройка решетки альфа железа в гамма железо
выделение из твердого раствора мельчайших частиц цементита
укрупнение частиц цементита в пластинки, размер которых измеряется от долей мм до микронов
76

vk.com/club152685050 | vk.com/id446425943
При ускорении охлаждении до 15-50 оС/сек диффузия протекает в меньшей степени и образуется более дисперсная смесь феррита и цементита, размеры пластинок достигают десятых долей микрометра. Такая структура называется СОРБИТ.
При ускорении охлаждения до 50-100 оС/с возможности диффузии еще более ограничиваются, а третий этап приостанавливается в самом начале. В результате пластины получаются еще более мелкие, такая мельчайшая смесь феррита и цементита была названа ТРООСТИТ.
77

vk.com/club152685050 | vk.com/id446425943
При ускорении охлаждения до 150-200оС/с успевает завершиться лишь перестройка решетки гамма в альфа., процесс диффузии произойти не успевает, углерод остается в альфа железе. Атомы углерода искажают решетку, она становится вытянутой – тетрагональной. Такой пересыщенный твердый раствор углерода в альфа железе называется МАРТЕНСИТОМ.
Структура ПЕРЛИТА, получающаяся при медленном охлаждении,
называется равновесной (как и все структуры, получаемые на диаграмме состояния)
Структуры перлита, сорбита и троостита, получающиеся при ускоренном и быстром охлаждении, называются неравновесными.
Увеличение скорости охлаждения вызывает понижение критических точек по отношению к их положению на диаграмме равновесия
РАСПАД АУСТЕНИТА. ДИАГРАММА ИЗОТЕРМИЧЕСКОГО ПРЕВРАЩЕНИЯ.
Превращение аустенита в перлит заключается в распаде П на Ф-Ц смесь.
При А1 аустенит и перлит будут находиться в равновесии, т.к. их свободные энергии равны. Для того, чтобы превращение А в П было устойчиво, необходимо некоторое переохлаждение, при котором свободная энергия П будет ниже свободной энергии А. превращение идет при температуре Аr1, которая ниже А1.
Мартенситное превращение начинается при температуре 240°С Мн и заканчивается при отрицательных температурах Мк.
Для описания кинетики превращения переохлажденного аустенита пользуются экспериментально построенными диаграммами время- температура-степень распада или диаграммами изотермического превращения аустенита, то есть превращения, протекающего при постоянной температуре.
Диаграмму строят в координатах температура-время (логарифм времени)
78

vk.com/club152685050 | vk.com/id446425943
Для изучения изотермического превращения аустенита небольшие образцы стали нагревают до состояния аустенита, а затем быстро охлаждают (переохлаждают) до температур ниже А1 (700,600,500,400,300 оС) и выдерживают при этих температурах до полного распада аустенита. Степень распада определяют различными методами (микроскопическими, магнитными и др.). Результаты исследований при постоянной
температуре характеризует кривая, показывающая количество распавшегося аустенита в зависимости от времени распада.
В течение некоторого промежутка времени Н1, Н2, Нз – распад экспериментально не фиксируется. Этот период называется инкубационным.
По истечении этого периода аустенит начинает распадаться с образованием более стабильных структур.
В области повышенных температур распад протекает с образованием структуры ФиЦ (перлитное превращение)
Скорость распада в начале быстро увеличивается, потом постепенно замедляется. Через некоторое время (К1К2Кз) процесс распада заканчивается.
Точки соединяют плавными линиями Первая кривая – показывает начало распада аустенита Вторая – конец распада
Область, лежащая левее первой кривой, определяет продолжительность инкубационного периода, здесь находится переохлажденный аустенит, не претерпевший распада
79

vk.com/club152685050 | vk.com/id446425943
При переохлаждении аустенита до 240оС или ниже Мн происходит превращение А в Мартенсит. Диффузионные процессы полностью подавляются.
Лекция 9 «Технология термической обработки стали»
ОТЖИГ
Традиционно сложившееся понятие «отжиг» охватывает несколько отличающихся друг от друга по режиму операций термообработки, объединенных единой целью – привести сталь в термодинамически равновесное состояние с минимальной плотностью дислокаций, по возможности низкой твердости и высокой пластичности.
ТЕРМИЧЕСКАЯ ОБРАБОТКА СПЛАВОВ, НЕ СВЯЗАННАЯ С ФАЗОВЫМИ ПРЕВРАЩЕНИЯМИ В ТВЕРДОМ СОСТОЯНИИ (ОТЖИГ 1 РОДА)
Этот вид отжига в зависимости от температурных условий устраняет химическую и физическую неоднородность, созданную предшествующими обработками, не связан с фазовыми превращениями, его можно проводить при температурах ниже или выше температур фазовых превращений.
Отжиг 1 рода
80
vk.com/club152685050 | vk.com/id446425943
ГОМОГЕНИЗАЦИОННЫЙ ОТЖИГ или ДИФФУЗИОННЫЙ ОТЖИГ
В реальных условиях кристаллизации расплава имеет место внутрикристаллическая ликвация: сердцевина кристалла обогащена тугоплавким компонентом, а наружные части сплава, а наружные – менее тугоплавким.
Внутрикристаллическая ликвация затрудняет последующую обработку давлением, т.к. снижает пластичность стали.
Диффузионным отжигом называют длительную выдержку сплавов при высоких температурах, в результате которой уменьшается ликвационная неоднородность твердого раствора.
Дендритная ликвация повышает склонность стали, обрабатываемой давлением, к хрупкому разрушению, она понижает пластичность, вязкость стали.
При высокой температуре протекают диффузионные процессы, не успевшие завершиться при первичной кристаллизации.
Диффузионному отжигу подвергают слитки легированных сталей, слитки алюминиевых сплавов.
В стальных слитках в результате диффузионного отжига достигается более равномерное распределение элементов в объеме зерен твердого раствора.
Его ведут при температуре 1100-1300 ° С с выдержкой 20-50 часов, затем медленное охлаждение.
РЕКРИСТАЛЛИЗАЦИОННЫЙ ОТЖИГ
Это нагрев деформированных полуфабрикатов или деталей выше температуры рекристаллизации.
Этот вид отжига производится с целью устранения наклепа холоднодеформированного металла.
Напомню, что наклепанный металл очень тверд и хрупок, его кристаллическая решетка вследствие высокой плотности дислокаций и наличия большого количества дефектов, находится в неравновесном состоянии.
81
vk.com/club152685050 | vk.com/id446425943
Наклеп приходится устранять. Для этого требуется нагрев, стимулирующий диффузионные процессы.
Цель рекристаллизационного отжига – понижение прочности и восстановление пластичности деформированного металла, получение заданного размера зерна.
Скорость охлаждения здесь не имеет большого значения – обычно на воздухе.
Температура рекристаллизации зависит от состава сплава и связана с температурой его плавления уравнением:
Трек. = а х Т пл., где
Тпл – температура плавления сплава в К
А –коэффициент, зависящий от состава сплава
У углеродистых сплавов – 0,4 у легированных – 0,8
Для углеродистых сталей рекристаллизационный отжиг проводится при температуре 600-700°С.
ОТЖИГ ДЛЯ СНЯТИЯ ОСТАТОЧНЫХ НАПРЯЖЕНИЙ
Применяется для отливок, сварных изделий, деталей после обработки
резанием, т.е. деталях, в которых возникли остаточные напряжения. Они могут вызвать деформацию деталей в процессе эксплуатации, могут привести к преждевременному короблению или разрушению конструкции.
Температура отжига колеблется от 160 до 700°с последующим медленным охлаждением.
В стальных и чугунных отливках значительное снижение остаточных напряжений происходит в процессе выдержки при т-ре 450°С. Выдержка от нескольких до десятков часов в зависимости от массы.
Отжиг для снятия сварных напряжений происходит при т-ре 650-700°С.
Многие детали прецизионных станков (ходовые винты, высоконагруженные зубчатые колеса, червяки) проходят отжиг после
82

vk.com/club152685050 | vk.com/id446425943
основной механической обработки при т-ре 570-600°С в течение 2-3 часов, и после окончательного шлифования – при т-ре 160-180°С и выдержке – 2-2,5 часа.
ОТЖИГ ВТОРОГО РОДА
ТЕРМИЧЕСКАЯ ОБРАБОТКА СПЛАВОВ, СВЯЗАННАЯ С ФАЗОВЫМИ ПРЕВРАЩЕНИЯМИ.
Цели отжига 2-го рода
-снижение твердости
-повышение пластичности
-получение однородной мелкозернистой структуры,
-полное снижение внутренних напряжений
-улучшение обрабатываемости резанием
Это нагрев стали выше критических температур Асз и Ас1, выдержки и медленным охлаждении вместе с печью.
В результате этого фазовые превращения приводят к достижению практически равновесного состояния. После отжига 2-рода получаются структуры, указанные в диаграмме состояния железо-цементит.
Следовательно, цель отжига 2-рода-снижение твердости, повышение пластичности и получение однородной мелкозернистой структуры. Одновременно при нем полностью снимаются остаточные напряжения.
83

vk.com/club152685050 | vk.com/id446425943
При изотермическом отжиге – выдержка происходит при температуре 650°С в другой печи, затем идет охлаждение на спокойном воздухе.
При этом уменьшается длительность процесса, структура становится более однородной. Он улучшает обработку резанием, чистоту поверхности, уменьшает деформации. Его используют для поковок (валы, шестерни, зубчатые колеса, муфты и др. детали небольших размеров).
СФЕРОИДИЗИРУЮЩИЙ ОТЖИГ ИНСТРУМЕНТАЛЬНЫХ СТАЛЕЙ (СФЕРОИДИЗАЦИЯ)
Высокая твердость инструментальных сталей затрудняют их механическую обработку резанием.
Наименьшую твердость имеют стали со структурой зернистого перлита, когда цементит перлита имеет округлую форму – отсюда и название отжига – сфероидизирующий.
Сфероидизирующий отжиг – это нагрев инструментальных сталей (эвтектоидных и заэвтектоидных) до температуры на 30-50° выше температуры Ас1 (727°) и последующим медленным вместе с печью охлаждением.
При сфероидизирующем отжиге идет распад аустенита с образованием феррито-цементитной смеси, сфероидизация, коагуляция карбидов.
Зернистый перлит имеет более низкую твердость и прочность, но более высокую пластичность.
Перлит пластинчатый имеет: |
σв=820Мпа, |
δ =15%, |
200-220НВ |
Перлит зернистый имеет: |
σв=630Мпа, |
δ=20%, |
160-170НВ |
84

vk.com/club152685050 | vk.com/id446425943
Нагрев стали выше на 30-50°С критической температуры Ас1 называется еще неполным отжигом.
Для доэвтектоидных сталей он применяется для улучшения обрабатываемости резанием. Здесь идет лишь частичная перекристаллизация А П.
НОРМАЛИЗАЦИЯ
Нормализацией называется вид термической обработки, заключающейся в нагреве стали до температур выше критических, выдержке и охлаждении на спокойном воздухе.
Доэвтектоидные стали нагревают до температуры выше на 30-50оС линии Асз, а заэвтектоидные – выше температуры Асm.
Нормализация – более экономичный, чем отжиг вид обработки, т.к. меньше времени затрачивается на охлаждение стали. Нормализацию иногда называют ускоренным отжигом.
Нормализация вызывает полную фазовую перекристаллизацию,
устраняет крупнозернистую структуру, полученную при литье, прокатке, ковке и ли штамповке.
Охлаждение на воздухе приводит к распаду аустенита при более низких температурах, что повышает дисперсность феррито - цементитной смеси.
85
vk.com/club152685050 | vk.com/id446425943
Это приводит к получению после нормализации более высокой прочности
и твердости, чем после отжига.
Назначение нормализации различно в зависимости от состава стали:
Для низкоуглеродистых сталей нормализация проводится вместо отжига для увеличении производительности обработки.
Для среднеуглеродистых сталей, когда от материала изделия не требуется высоких прочностных свойств – нормализация применяется вместо закалки и высокого отпуска. Механические свойства будут при этом несколько ниже, но вероятность появления трещин – меньше.
Дефекты при отжиге и нормализации
При отжиге и нормализации могут возникнуть следующие дефекты.
Окисление- при нагреве в пламенных печах поверхность стальных деталей взаимодействует с печными газами. В результате металл окисляется и на деталях образуется окалина – химическое соединение металла с кислородом. С увеличением температуры и времени выдержки окисление резко возрастает.
Окалина вызывает не только угар – потерю металла на окалину, но и повреждает поверхность детали, затрудняется дальнейшая обработка ее режущим инструментом.
Окалину удаляют травлением в растворе серной кислоты, очищают в дробеструйных установках
Обезуглероживание - это выгорание углерода с поверхности детали, происходит при окислении стали. Обезуглероживание резко снижает прочностные свойства стали, способствует образованию трещин и короблению.
Для предотвращения окисления и обезуглероживания – применяют безокислительные (защитные) газы, которые вводят в рабочее пространство печи.
При нагреве стали выше определенных температур и длительной выдержке в ней происходит быстрый рост зерен, ведущий к возникновению крупнокристаллической структуры. Это явление
называется перегревом.
86
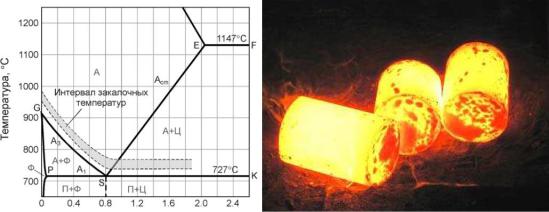
vk.com/club152685050 | vk.com/id446425943
Перегрев ведет к понижению пластических свойств стали. Он может быть исправлен повторным правильным нагревом – отжигом и нормализацией.
Пережог – получается в результате длительного пребывания металла в печи при высокой температуре, близкой к температуре плавления.
Физическая сущность пережога состоит в том, что кислород из окружающей атмосферы при высокой температуре проникает вглубь нагреваемого металла и окисляет границы зерен. В результате механическая связь между зернами ослабевает, металл теряет пластичность и становится хрупким.
Пережог является неисправимым браком
ЗАКАЛКА СТАЛИ
Исторически сложившееся понятие «закалка» предполагает такую термообработку, при которой сталь приобретает неравновесную структуру, что прежде всего выражается в повышении твердости стали.
Закалкой называется вид термообработки, состоящий в нагреве стали до температуры выше критических точек Асз или Ас1, выдержке при этой температуре для завершения фазовых превращений и последующем быстром охлаждении.
Для углеродистых сталей - чаще всего - это охлаждение проводят в воде, для легированных – в масле.
Закалка не является окончательной операцией термообработки. Чтобы уменьшить хрупкость и напряжения, вызванные закалкой и получить
87

vk.com/club152685050 | vk.com/id446425943
требуемые механические свойства – сталь после закалки подвергают отпуску
Цель закалки –получение высокой твердости, прочности, износостойкости.
Доэвтектоидные стали нагревают до температуры Асз+30-50°
Эвтектоидные и заэвтектоидные – до температур Ас1+30-50°
Стали, содержащие менее 0,3 % углерода практически не закаливаются.
При закалке фиксируются переходные структуры, главным представителем которых является мартенсит.
Нагрев доэвтектоидных сталей до температуры Ас1 +30-50° – называется неполной закалкой. Т.к. выше Ас1структура Ф+А, при охлаждении аустенит переходит в мартенсит, а феррит с твердостью 80НВ – остается.
Для заэвтектоидных сталей – неполная закалка является и полной, т.к. цементит имеет твердость 800НВ. И нет необходимости от него избавляться, нагревая сталь до области одного аустенита.
88

vk.com/club152685050 | vk.com/id446425943
Скорость нагрева и время выдержки зависят от химического состава стали, размеров, массы и конфигурации закаливаемых деталей, типа нагреваемых печей и нагревательной среды.
Чем больше размеры и сложнее конфигурация, тем медленнее происходит нагрев.
Скорость нагрева и продолжительность выдержки определяют экспериментально или пользуются специально разработанными таблицами. Например, при 800° 1 мм диаметра сечения нагревается 1 минуту.
Оборудованием при нагреве служат нагревательные термические печи или печи-ванны, которые подразделяются на электрические и топливные, обогреваемые за счет сгорания топлива (газа, мазута, угля).
Нагрев должен производиться как можно быстрее, однако время нагрева должно быть достаточным, чтобы равномерно прогреться и получить аустенитную структуру
Скорость охлаждения при закалке регулируется средой охладителей, которые могут быть:
сильные –100-500°/с
умеренные –10-100°/с
слабые 1-10°/с
В качестве закалочных сред используют воду, водные растворы солей, щелочей, масло, расплавленные соли.
89

vk.com/club152685050 | vk.com/id446425943
Если принять охлаждающую способность воды при 20оС за единицу, то охлаждающая способность:
масло –0,17-0,44
расплавленного свинца – 0,05
воздуха – 0,03
Различают следующие виды закалок:
А) Закалка в одном охладителе
Нагретую до определенной температуры деталь погружают в закалочную среду, где она остается до полного охлаждения. Применяется для деталей простой формы из углеродистой стали.
Б) Закалка в двух средах
Нагретую деталь сначала охлаждают в воде до температуры несколько выше Мн, а затем быстро переносят в другую среду (масло, воздух), где она охлаждается до температуры 20о. Во второй закалочной среде уменьшаются внутренние напряжения, связанные с превращением Аустенита в мартенсит. Применяется при закалке высокоуглеродистых сталей и требует высокой квалификации термиста.
В) Ступенчатая закалка
Нагретая деталь охлаждается в среде, имеющей температуру несколько выше Мн (250о) и выдерживают в ней до выравнивания температуры по всему сечению. Затем окончательно охлаждают на воздухе, где идет превращение аустенита в мартенсит. При этой закалке уменьшаются объемные напряжения, коробление, опасность возникновения трещин.
Г) Изотермическая закалка
Выполняется также, как и ступенчатая, но выдержка в закалочной среде более продолжительная. Данной закалке подвергаются в основном легированные стали.
Дефекты, возникающие при закалке 1. Окисление и обезуглероживание
90
vk.com/club152685050 | vk.com/id446425943
Оно происходит при нагреве в пламенных или электрических печах без контролируемых (защитных) атмосфер. Нагрев в соляных ваннах или расплавленном свинце предохраняет поверхность детали от окисления и обезуглероживания.
2. Передержка и перегрев
Проявляется в укрупнении зерна аустенита и, следовательно, укрупнении игл мартенсита. Это способствует охрупчиванию и появлению при закалке трещин. Устраняется повторной закалкой.
3.Недостаточная твердость
Может быть вызвана недогревом или недостаточно интенсивным охлаждением
4.Образование «мягких пятен»
«Паровая рубашка», захват клещами, сохранение приставшей окалины, включения феррита – все это способствует образованию мягких пятен.
5.Трещины – образуются после окончательного охлаждения. Склонность к образованию трещин растет с увеличением содержания углерода в стали, повышению температуры закалки и скорости охлаждения. Кроме этого способствуют появлению трещин резкое изменение сечений изделий, подрезы, выступы, углубления. При конструировании – необходимо избегать их.
6. Деформация и коробление
ВНУТРЕННИЕ НАПРЯЖЕНИЯ ПРИ ЗАКАЛКЕ
Закаленная сталь всегда находится в структурно напряженном состоянии. Внутренние напряжения, возникающие при закалке бывают:
тепловые
структурные
Тепловые возникают вследствие неравномерного охлаждения поверхности и сердцевины изделия, т.е. они вызваны перепадом температур по сечению изделия.
Структурные – возникают в результате превращения аустенита в мартенсит. Так, мартенсит обладает наибольшим удельным объемом из
91
vk.com/club152685050 | vk.com/id446425943
всех прочих состояний. Величина их тем больше, чем выше температура закалки и скорость охлаждения.
Снимаются последующим видом термообработки – отпуском.
ЗАКАЛИВАЕМОСТЬ И ПРОКАЛИВАЕМОСТЬ СТАЛИ
Под закаливаемостью – понимают способность данной стали
приобретать высокую твердость в результате закалки.
Она зависит в основном от содержания углерода в стали, чем его больше, тем выше твердость стали после закалки.
Под прокаливаемостью – понимают степень проникновения закалки во внутренние слои изделия, т.е. способность образовывать мартенситную или троостито-мартенситную структуру на определенную глубину.
Прокаливаемость стали зависит от устойчивости переохлажденного аустенита. Чем выше устойчивость переохлажденного аустенита, тем выше прокаливаемость.
Практически для углеродистой стали полную прокаливаемость получают прутки диаметром 25 мм или 1 дюйм, т.е. если валик будет иметь диаметр 25 мм, то он полностью прокалится. Это примерная ориентация.
92

vk.com/club152685050 | vk.com/id446425943
ПОВЕРХНОСТНАЯ ЗАКАЛКА СТАЛИ
Часто на практике нужна лишь поверхностная твердость, т.к. у ряда изделий износ составляет лишь доли мм. А твердость в сердцевине не только не нужна, но и нежелательна.
В этих случаях применяют так называемую поверхностную закалку.
При поверхностной закалке на некоторую заданную глубину закаливается только поверхностный слой, тогда как сердцевина изделия остается незакаленной.
Назначение поверхностной закалки:
повышение твердости, износостойкости, предела выносливости
93

vk.com/club152685050 | vk.com/id446425943
сердцевина при этом остается вязкой, хорошо воспринимающей ударные нагрузки.
Различают следующие виды поверхностной закалки:
-поверхностную закалку с индукционным нагревом -газовую поверхностную закалку
Закалка с индукционным нагревом
Впервые индукционный нагрев для термической обработки был предложен в 1935 году Вологдиным. В 1937 году этот процесс был применен на Зиле для упрочнения многих деталей автомобиля.
Индукционный нагрев происходит вследствие теплового действия тока, индуктируемого в изделии, помещенном в переменное магнитное поле.
Для нагрева изделие устанавливают в индуктор, представляющий собой один или несколько витков пустотелой водоохлаждающей медной трубки.
Переменный ток, протекая через индуктор, создает переменное магнитное поле.
В результате индукции в поверхностном слое возникают вихревые токи и происходит выделение джоулевого тепла. Ток проходит в основном в
94
vk.com/club152685050 | vk.com/id446425943
поверхностном слое проводника. Это явление называется – поверхностным эффектом.
Источниками электропитания служат машинные и реже ламповые генераторы.
Для каждого типа детали изготавливают отдельный индуктор, конфигурация которого соответствует форме закаленной детали.
ВЧ-закалка является высокопроизводительным и экономически выгодным способом лишь при серийном и массовом производстве, когда в индукторе обрабатывают большое количество деталей.
возможность получения слоя заданной глубины
высокая производительность
получение высокой твердости
отсутствие окалины и незначительное коробление
возможность полной автоматизации процесса
возможность закалки любых поверхностей и деталей различной конфигурации.
При газовой поверхностной закалке поверхность детали нагревается ацетилено-кислородным пламенем, а затем охлаждается водой.
Кроме ацетилено-кислородного пламени могут быть использованы и другие горючие газы – метан и др. Температура в вершине внутреннего конуса при этом достигает 3100оС.
Как закалочную машину можно использовать токарный станок, а в качестве закалочной горелки – обычную сварочную горелку со специальными многопламенным наконечником.
В патрон токарного станка закрепляется закаливаемая деталь – вал, в суппорте закрепляется горелка. Суппорт перемещается вдоль медленно вращающейся детали, нагревает ее, а затем производят душевое охлаждение.
Здесь закаливают обычно крупные детали.
НЕДОСТАТКИ ГАЗОВОЙ ЗАКАЛКИ:
95

vk.com/club152685050 | vk.com/id446425943
Неравномерность прогрева, а, следовательно, и закалки не высокая производительность процесса
ОТПУСК СТАЛИ
Отпуском называется вид термической обработки, состоящей в нагреве закаленной стали до температур ниже критической Ас1, выдержке при заданной температуре и последующем охлаждении.
Отпуск является окончательной операцией термической обработки, в результате которой сталь получает требуемые свойства.
Отпуск полностью или частично устраняет внутренние напряжения, возникающие после закалки. Эти напряжения снимаются тем полнее, чем выше температура отпуска.
Скорость охлаждения также оказывает большое влияние на величину остаточных напряжений. Чем медленнее охлаждение, тем меньше остаточные напряжения.
При отпуске неравновесная структура, состоящая из мартенсита и аустенита остаточного в более устойчивое состояние. Этот переход связан с диффузионным распадом твердого раствора на феррито-цементитную смесь и протекает тем полнее, чем выше температура нагрева.
Температура нагрева при отпуске оказывает основное влияние на свойства отпущенной стали.
Различают следующие виды отпуска:
Низкий отпуск достигается нагревом до температуры 150—250° С, выдержкой при этой температуре и последующим охлаждением на воздухе. При выдержке во время отпуска в указанном интервале температур мартенсит закалки превращается в мартенсит отпуска, при этом внутренние
96
vk.com/club152685050 | vk.com/id446425943
напряжения частично снимаются и остаточный аустенит превращается в мартенсит отпуска. В результате низкого отпуска сталь сохраняет высокую твердость, а иногда твердость повышается за счет распада остаточного аустенита; устраняется закалочная хрупкость. Такой отпуск применяют для режущего инструмента и изделий, которым необходима высокая твердость. Превращение мартенсита закалки в мартенсит отпуска способствует стабилизации размеров детали, что необходимо для измерительного инструмента, изготовляемого из инструментальной стали. Этому инструменту также дают низкий отпуск.
Средний отпуск производят при 300—500° С. Твердость стали заметно понижается, вязкость увеличивается. Средний отпуск применяют для пружин, рессор, а также инструмента, который должен иметь значительную прочность и упругость при средней твердости.
Высокий отпуск происходит при 500—600° С, его основное назначение — получить наибольшую вязкость при достаточных пределах прочности и упругости стали. Применяют этот вид отпуска для деталей из конструкционных сталей, подвергающихся действию высоких напряжений, особенно при ударной нагрузке Для деталей различных машин и станков обычно применяют термическую обработку, состоящую в закалке с последующим высоким отпуском при температуре, обеспечивающей получение сорбита отпуска и хорошего
сочетания |
прочностных |
и |
пластических |
свойств. |
Такая термическая обработка |
называется «улучшением |
стали». |
Нагрев при отпуске можно производить в тех же печах, которые применяют для других видов термической обработки, но он требует более равномерной температуры и более точного контроля.
УЛУЧШЕ́НИЕ СТА́ЛИ, двойная термическая обработка — закалка на мартенсит с последующим высоким отпуском для получения однородной дисперсной структуры сорбита, обеспечивающей хорошее сочетание прочности, пластичности, ударной вязкости и критической температуры перехода из вязкого в хрупкое состояние.
97
vk.com/club152685050 | vk.com/id446425943
Лекция 10
«Химико-термическая обработка»
ХТО называется термическая обработка, заключающаяся в сочетании термического и химического воздействия с целью изменения состава, структуры и свойств поверхностного слоя стали.
При ХТО происходит поверхностное насыщение стали элементами ( С,N, Al, Cr, SI и др.) путем его диффузии в атомарном состоянии из внешней среды (твердой, газовой, жидкой) при высокой температуре.
При ХТО получается большая разность между составом и свойствами поверхностного слоя и сердцевины
ХТО включает три последовательные стадии (элементарные процессы):
ДИССОЦИАЦИЯ – распад молекул и образовании активных насыщающих элементов
2СО = СО2+ С
2NH3 = 3 H2 + 2 N
Степень распада молекул газа в % называется степенью диссоциации
АБСОРБЦИЯ – захват поверхностью металла свободных атомов насыщающегося
элемента. Происходит на гране газ – металл. Развитию процесса абсорбции способствует возможность диффундирующего элемента образовывать с основным металлом твердые растворы или химические соединения.
ДИФФУЗИЯ – проникновение насыщающего элемента вглубь металла. Процесс диффузии возможен только при наличии растворимости диффундирующего элемента в основном металле и высокой температуре. Количественно процесс диффузии характеризуется так называемым коэффициентом диффузии Д, зависит от температуры, чем выше температура, тем больше и полнее идет процесс диффузии Продолжительность ХТО определяется требуемой глубиной диффузионного слоя
Рассмотрим основные виды ХТО
ЦЕМЕНТАЦИЯ
Цементацией называется процесс насыщения поверхностного слоя стали углеродом.
Цель цементации – получение твердой и износостойкой поверхности при сохранении вязкой пластичной сердцевины.
98

vk.com/club152685050 | vk.com/id446425943
Цементации подвергаются стали, содержащие углерода 0,12-0,23 %
Цементацию проводят при температурах выше критической Ас3 , т.е.920950 градусов, при которой сталь находится в аустенитном состоянии, растворяющим углерод в больших количествах.
Толщина цементованного слоя от 0,5 до 3 мм
Время выдержки зависит от требуемой толщины цементованного слоя и составляет от 6 до 24 часов.
В зависимости от вида карбюризатора (вещества, содержащего углерод) различают следующие основные виды цементации:
твердая
газовая
жидкостная
ЦЕМЕНТАЦИЯ В ТВЕРДОМ КАРБЮРИЗАТОРЕ
Насыщающая среда – древесный уголь (дубовый или березовый) или торфяной кокс + активизаторы: углекислые барий ВаСО3, кальцинированная сода в количестве 10-40% от массы угля.
Изделия укладывают в специальные железные ящики. На дно которых насыпают карбюризатор, сверху деталей снова – карбюризатор, ящик закрывается крышкой, имеющей отверстие для выхода газов, обмазывают огнеупорной глиной и помещают в печь, нагретую до температуры 920 – 950 оС. Продолжительность выдержки от 5 лр 15 часов в зависимости от размеров ящика.
После цементации ящики охлаждают на воздухе до 400-500оС далее ящики раскрывают.
99
vk.com/club152685050 | vk.com/id446425943
ГАЗОВАЯ ЦЕМЕНТАЦИЯ
Это процесс насыщения углеродом в среде углеродосодержащих газов.
Чаще всего – это природный газ, состоящий почти целиком из метана - СН4 и пропан бутановых смесей
Температура цементации – 910-930оС
Время выдержки – 6-12 часов
Толщина слоя – до 1.5 мм
Газовую цементацию проводят в различных печах (шахных, муфельных и др.) через которые пропускают газ.
Газовая цементация применима для условий массового производства деталей.
Преимущества ее:
возможность получения заданной концентрации в слое
сокращение длительности процесса
возможность обеспечения полной автоматизации производства
упрощение последующей термообработки, которая осуществляется сразу из цементационной печи
ТЕРМИЧЕСКАЯ ОБРАБОТКА ПОСЛЕ ЦЕМЕНТАЦИИ
Окончательные свойства цементованных изделий достигаются после термической обработки, выполненной после цементации.
Нормализация – для уменьшения величины зерна, неизбежно вырастающего в результате нагрева до 950оС., устранения карбидной сетки цементованного слоя
Закалка – для увеличения твердости поверхностного слоя, 58-62НRCэ, структура – мелкодисперсный мартенсит
Низкий отпуск – снимает внутренние закалочные напряжения и оставляет высокую твердость мартенсита.
АЗОТИРОВАНИЕ
100
vk.com/club152685050 | vk.com/id446425943
Азотированием называется процесс диффузионного насыщения поверхностного слоя стали азотом при нагреве ее в атмосфере аммиака.
Цель азотирования – повышение твердости поверхностного слоя
износостойкости
предела выносливости
сопротивления коррозии (в таких средах как вода, пар и др.)
Твердость азотированного слоя выше, чем цементованного и сохраняется при нагреве до 600-650оС , тогда как мартенсит сохраняет свою твердость только до температуры 200-250оС
Азотированию подвергают шестерни, цилиндры, пресс-формы, коленчатые валы, штампы.
В сплавах железа с азотом образуется ряд твердых растворов ( азота в альфа-железе, твердые растворы на основе нитридов железа.
Азотирование проводят в атмосфере аммиака.
Азотированию подвергают среднеуглеродистые легированные стали, которые после азотирования получают высокую твердость и износостойкость. Кроме нитридов железа, твердость которых невелика, наиболее сильно повышают твердость вольфрам, хром, молибден, ванадий.
Классическая сталь для азотирования – 38Х2МЮА
Азотирование углеродистых сталей повышает их коррозионную стойкость.
Температура азотирования – 520-600оС
Толщина азотированного слоя - до 0,6 мм
продолжительность процесса зависит от требуемой толщины азотированного слоя.
ЦИАНИРОВАНИЕ
Цианированием называется процесс диффузионного насыщения поверхностного слоя стали одновременно углеродом и азотом при температуре 820-950оС в расплавленных цианистых солях.
101
vk.com/club152685050 | vk.com/id446425943
Цели цианирования – повышение поверхностной твердости, прочности, износостойкости, коррозионной стойкости, предела выносливости. Различают:
1. СРЕДНЕТЕМПЕРАТУРНОЕ ЦИАНИРОВАНИЕ
Это нагрев до 820-860оС в расплавленных цианистых солях (NaCNKCN) продолжительность процесса – от 30 до 90 мин далее закалка непосредственно из цианистой ванны и низкий отпуск. Применяется для мелких деталей.
2. ВЫСОКОТЕМПЕРАТУРНОЕ ЦИАНИРОВАНИЕ
Это нагрев до температуры 930-950оС в расплавленных цианистых солях продолжительность процесса 1, 5 часа-6 часов Зеркало ванны для предотвращения угара цианистых солей покрывают слоем графита.
После цианирования также проводят закалку и низкий отпуск. Преимущества цианирования перед цементацией - уменьшение времени – повышение производительности, больше износостойкость, коррозионная стойкость, меньше коробление.
Недостатки – высокая стоимость, ядовитость цианистых солей, необходимы меры по охране труда.
НИТРОЦЕМЕНТАЦИЯ
Нитроцементация – это процесс диффузионного насыщения поверхностного слоя стали одновременно углеродом и азотом при температуре 840-860оС в газовой среде, состоящей из науглероживающего газа и аммиака.
Продолжительность процесса – 4-10 часов
Цели – те же, что и при цианировании
Установлено, что при одновременной диффузии углерода и азота ускоряется\ диффузионный процесс.
Температура при нитроцементации ниже, чем при цементации, что положительно.
Толщина слоя – 0,2-0,8 мм
После нитроцементации следует закалка и низкий отпуск, твердость – 58-
64НRCэ.
102
vk.com/club152685050 | vk.com/id446425943
Нитроцементации подвергают детали сложной конфигурации, склонные к короблению.
Наиболее широко применяется на автомобильных и тракторных заводах. В частности на Вазе 94,5% деталей, проходящих ХТО, подвергаются нитроцементации.
БОРИРОВАНИЕ
Борирование – это вид ХТО, заключающийся в диффузионном насыщении поверхностного слоя стали бором при нагреве в соответствующей среде.
Цель борирования – повышение поверхностной твердости, износостойкости, коррозионной стойкости, окалиностойкости до 800оС и теплостойкости.
Борирование выполняется при электролизе расплавленной буры
Na2B4O7. Но может быть и газовым в среде диборана или хлористого бора, либо без электролиза в ваннах с расплавленными солями.
Температура процесса 930-950оС
Время выдержки – 2-6 часов
Толщина слоя очень небольшая – 0,1-0.2 мм
Диффузионный слой состоит из боридов,обладающих высокой твердостью.
Борированию подвергают втулки насосов, диски, штампы, детали прессформ и др.
ДИФФУЗИОННАЯ МЕТАЛЛИЗАЦИЯ
Диффузионная металлизация – это насыщение поверхностного слоя стали алюминием, хромом, цинком, кремнием и др.
Различают следующие основные способы диффузионной металлизации:
погружение в расплав металла
диффузия из расплавленных солей, содержащих диффундирующий элемент
путем испарения диффундирующего элемента из газовой среды Различают следующие виды диффузионной металлизации.
АЛИТИРОВАНИЕ
103
vk.com/club152685050 | vk.com/id446425943
Это диффузионное насыщение поверхностного слоя металла алюминием
Цель алитирования – повышение окалиностойкости (до 900оС) , при этом образуется плотная пленка окислов Аl2O3, предохраняющая металл от окисления, повышения коррозионной стойкости.
Алитирование осуществляется погружением деталей в расплавленный алюминий (660оС)
толщина слоя 0,2-1 мм
структура алитированного слоя - твердый раствор алюминия в альфажелезе.
Алитированию подвергают чехлы термопар, топливники газогенераторных машин, детали разливочных ковшей и др. детали, работающие при высоких температурах.
ХРОМИРОВАНИЕ
Это насыщение поверхностного слоя хромом.
Цель – повышение окалиностойкости до 800оС, коррозионной стойкости в морской воде и азотной кислоте, увеличения твердости и износостойкости
Диффузионный слой состоит из твердого раствора хрома в альфа-железе, карбидов хрома
толщина слоя – 0,1-0,15 мм
Хромированию подвергают детали паросилового оборудования, пароводяной арматуры, клапаны, вентили, детали, работающие на износ в агрессивных средах.
СИЛИЦИРОВАНИЕ
Это насыщение поверхностного слоя кремнием
Цель – повышение коррозионной стойкости в морской воде, азотной и серной кислотах, износостойкости.
Силицированный слой состоит из твердого раствора кремния в альфажелезе
Толщина слоя – 0,3-1мм
При низкой твердости износостойкость силицированного слоя велика.
104

vk.com/club152685050 | vk.com/id446425943
Силицированию подвергают детали химического оборудования, бумажной и нефтяной промышленности – валики насосов, трубопроводы, арматура, гайки, болты и др.
ТЕРМОМЕХАНИЧЕСКАЯ ОБРАБОТКА (ТМО)
Это широко применяемый в машиностроении эффективный способ упрочнения металлов. Он позволяет повысить механические свойства по сравнению с полученными при обычной закалке и отпуске.
ТМО заключается в сочетании пластической деформации стали в аустенитном состоянии с ее закалкой.
Цель ТМО - получение высокой твердости в сочетании с высокой вязкостью и устранение отпускной хрупкости.
Формирование структуры закаленной стали происходит в условиях повышенной плотности дислокаций, обусловленных наклепом.
Пластическое деформирование при ТМО производят прокаткой, ковкой, штамповкой и другими способами обработки металлов давлением.
В процессе пластической деформации аустенита возникает наклеп, обуславливающий создание мелкоблочной структуры, затем немедленно следует закалка, фиксирующая особо тонкую структуру, созданную наклепом. Образуется высокодисперсный мартенсит.
Различают два основных способа ТМО, в зависимости от того, в каком температурном интервале производится пластическая деформация:
ВТМОвысокотемпературная термомеханическая обработка НТМО – низкотемпературная термомеханическая обработка
При ВТМО сталь деформируют при температуре выше Ас3.
Степень деформации составляет 20-30%. после деформации немедленно следует закалка во избежании развития процесса рекристаллизации.
|
После ТМО: Ϭ = 220-300 Мпа δ =6-8 % |
|
|
После закалки и отпуска |
Ϭ = 200 –220 Мпа δ = 3-4 % |
105
vk.com/club152685050 | vk.com/id446425943
При НТМО сталь деформируют в зоне существования переохлажденного аустенита (400600оС). Температура должна быть выше Мн, но ниже температуры рекристаллизации. Степень деформации – 75-95%.
Механические свойства при НТМО выше, чем при ВТМО
|
Ϭ = 260-300 Мпа δ = 6% |
Проведение НТМО более сложно по сравнению с ВТМО. Требует более мощные деформирующие средства, т.к. аустенит при 400 оС менее пластичен.
Сочетание высокой прочности и пластичности при НТМО позволяет использовать ее при изготовлении высокопрочных пружин, рессор и подвесок.
Лекция 11
«Легированные стали»
Углеродистые стали, которые мы изучали, во многих случаях не отвечают высоким требованиям, предъявляемым к материалам современной техники. Они доступны, относительно не дороги, технологичны (хорошо обрабатываются, свариваются), но зачастую не отвечают всему
комплексу свойств, предъявляемых к современным материалам.
Наибольшее распространение для изготовления ответственных деталей и конструкций в машиностроении, энергетике, строительстве и на транспорте имеют легированные стали.
Легированные стали – это стали, в которые для получения определенных свойств специально введены элементы, называемые легирующими. Например, хром, никель, вольфрам, алюминий и др.
Легирующие элементы изменяют химический состав, строение и свойства стали: повышают прочность, твердость при сохранении высокой пластичности, увеличивают прокаливаемость стали. Легированные стали могут обладать такими свойствами как жаропрочность, жаростойкость, коррозионной стойкостью, особыми электрическими или магнитными свойствами.
При этом нужно иметь в виду, что основные преимущества легированных сталей проявляются только после правильно выбранной термической обработки, которой обязательно должны быть подвергнуты легированные стали.
106

vk.com/club152685050 | vk.com/id446425943
Рассматривая легированные стали необходимо прежде всего выяснить как легирующие элементы взаимодействуют с основными компонентами стали – железом и углеродом.
С железом – легирующие элементы могут образовывать следующие фазы:
твердые растворы
интерметаллиды (соединения металла с металлом)
С углеродом - они могут образовывать специальные карбиды.
По влиянию на полиморфизм железа легирующие элементы делятся на две группы:
Элементы, расширяющие гамма-область
1группа - никель, марганец, кобальт, медь
Элементы, сужающие гамма область и расширяющие альфа область
2 группа - Cr, W, V, Si, Al, Ti
Самые сильные аустенизаторы – никель и марганец.
При большом содержании в стали легирующих элементов 1 группы - аустенитная структура стали сохраняется до нормальных температур.
Это стали – аустенитного класса.
При легировании стали элементами 2 группы – в структуре их будет феррит – стали ферритного класса.
107
vk.com/club152685050 | vk.com/id446425943
До сих пор мы не учитывали влияния углерода.
Легирующие элементы могут сдвигать точку Е диаграммы состояния железо-углерод влево и в структуре стали появится ледебурит – типичная структура чугунов, так получаются стали ледебуритного класса ( например, быстрорежущие стали)
Перлитная структура может быть не при 0,8% углерода, а меньше, так как точка S диаграммы также может сдвигаться влево.
Мы рассмотрели случаи, когда структуры получаются при очень медленном охлаждении, т.е. отожженные, равновесные.
Таким образом, по структуре в отожженном состоянии легированные стали делятся на следующие классы:
Перлитный (доэвтектоидные, эвтектоидные и заэвтектоидные)
Ферритный
Полуферритный
Аустенитный
Полуаустенитный
Легированные стали можно классифицировать по структуре в нормализованном состоянии:
Они делятся на 3 класса:
Перлитный
Мартенситный
Аустенитный
Все Л.Э. по взаимодействию с углеродом делятся на 2 группы
1.Карбидообразующие
2.Некарбидообразующие
К 1-м относят (по степени возрастания активности) Fe Mn Cr Mo N V Ti Nb Ко 2-м относят – Ni Co Cu Si
108

vk.com/club152685050 | vk.com/id446425943
При легировании карбидообразующими элементами – повышается твердость и прочность стали (по з-ну Курнакова)
При легировании элементами, входящими в состав твердого раствора – изменяются физические и химические свойства.
Легированные стали можно классифицировать по химическому составу:
хромистые
марганцовистые
хромомарганцовистые
хромокремнистые
хромо-никеле-вольфрамовые и другие
В зависимости от количества в них легирующих элементов они могут быть
низколегированные ( до 3% Л.Э.)
среднелегированные ( от 3 до 10% Л.Э.)
высоколегированные ( свыше 10% Л.Э.)
По эксплуатационным признакам ( назначению) легированные стали классифицируют:
конструкционные (для изготовления деталей машин)
а) работающие в условиях обычных температур
б) работающие при повышенных температурах
инструментальные (различный инструмент и оснастка)
а) режущий инструмент
б) штампы
vk.com/club152685050 | vk.com/id446425943
в) измерительный инструмент
стали и сплавы с особыми свойствами
а) нержавеющие
б) с высоким электросопротивлением
в) с особым тепловым расширением
г) магнитные
д) жаропрочные и жаростойкие
МАРКИРОВКА ЛЕГИРОВАННЫХ СТАЛЕЙ
Обозначение марок легированных сталей производится по буквенноцифровой системе Л.Э. обозначаются следующими буквами:
Ni -Н |
Ti -Т |
Cu -Д |
Cr -Х |
Co -К |
Nb - Б |
W -В |
Si -С |
бор- Р |
V -Ф |
Mn- Г |
P -П |
Mo- М |
Al -Ю |
|
Каждая марка состоит из букв и цифр. Первые цифры марки указывают среднее содержание углерода в сотых долях процента.
Цифры, стоящие за буквами, обозначают среднее содержание данного легирующего компонента в целых долях %..
При содержании элемента менее 1% цифра отсутствует. При содержании элемента около 1% - стоит цифра 1.
НАПРИМЕР,
30ХГСНА, 12Г2, ХВ5, Х12М. 10Х18Н9Т, 9ХС, 25Н3, 3Х2В8Ф
Нестандартные обозначения:
ШХ15, Р18, ЭИ179, ЕХ3
(соответственно шарикоподшипниковая, быстрорежущая, магнито-мягкая, магнито-твердая )
Конструкционные легированные стали
Конструкционные легированные стали, применяемые при обычных температурах
Конструкционными называются стали, применяемые для изготовления деталей машин, конструкций и сооружений. Стали, применяемые в
конструкциях и сооружениях, называются строительными. Четкой границы по химическому составу между строительной и
110
vk.com/club152685050 | vk.com/id446425943
машиностроительными сталями нет. Конструкционными могут быть как углеродистые, так и легированные стали. Содержание углерода в этой группе не превышает 0.6 %.
Основные легирующие элементы конструкционных сталей являются хром, никель, кремний, марганец. Для дополнительного улучшения механических свойств вводят молибден, вольфрам, ванадий, титан и др.
Большинство сталей этой группы относят к перлитному классу, в равновесном состоянии – в группу – доэвтектоидных.
Конструкционные стали подразделяются:
строительные, низколегированные стали
машиностроительные – цементируемые
машиностроительные – улучшаемые
рессорно-пружинные
износостойкие (аустенитная)
шарикоподшипниковые
мартенситностареющие высокопрочные стали
Строительные низколегированные стали
Это стали, содержащие не более 0,22%С и сравнительно небольшое количество недефицитных легирующих элементов. Они хорошо свариваются, это значит, что они не образуют при сварке холодных и горячих трещин. По сравнению с углеродистыми они имеют более высокие значения пределов прочности и текучести при сохранении хорошей пластичности, меньшей склонности к старению и хладноломкости.
19Г
14Г2 |
Это сварные нефтегазопроводы, газопроводные трубы, |
|
17ГС |
строительные фермы, мосты, вагоны, рамы. |
|
14ХГС |
|
|
15ХГСНД |
|
|
35ГС |
|
|
25Г2С |
стали для армирования железобетонных конструкций |
|
|
σ в = 600Мпа |
δ =14% |
Машиностроительные цементируемые легированные стали
Углерода в них содержится 0,1-0,25%
После цементации, закалки и низкого отпуска цементованный слой должен иметь 58-62 НRСэ, сердцевина – 20-40НRСэ
111
vk.com/club152685050 | vk.com/id446425943
Хромистые стали
15Х 20Х - изделия простой формы, небольших размеров – кулачки, втулки,
пальцы, зубчатые колеса
σ в =700-800Мпа |
δ =11-12% |
|
|
|
Хромоникелевые стали |
12ХН3А |
Это детали ответственного назначения, испытывающие |
|
12Х2Н4А |
в эксплуатации значительные динамические нагрузки |
|
20Х2Н4А |
|
|
σ в =950 –1300Мпа |
δ =9-14% |
Одновременное легирование хромом и никелем повышает прочность и пластичность стали и увеличивает вязкость сердцевины.
12Х2Н4ВА
18Х2Н4МА -для тяжелонагруженных деталей, зубчатых колес, коленчатых валов, осей и др
Хромомарганцовистые стали
Применяются во многих случаях взамен дорогих хромоникелевых, они менее устойчивы против перегрева и поэтому в них добавляют титан.
18ХГТ
25ХГТ
25ХГМ зубчатые колеса автомобилей (коробки передач), валы
Для увеличения прокаливаемости в них добавляют никель.
Машиностроительные улучшаемые легированные стали
Улучшаемые– это стали используемые после закалки и высокого отпуска С=0,3-0,5%
Температура закалки 820-880°С ВО=550-650°С.
Известные нам углеродистые улучшаемые стали марок 35,40,45 используют для изделий небольших сечений, работающих при невысоких нагрузках.
Хромистые стали
30Х для средненагруженных деталей, валы, оси, рычаги
40Х
112
vk.com/club152685050 | vk.com/id446425943
50Х крупные шестерни, валы
σв =950-1000Мпа δ =12%
Хромомарганцовистые стали
30ХГ
40ХГ
30ХГТ
достаточно высокая прочность и прокаливаемость, но пониженная вязкость
Хромо-марганце-кремниевые стали 20ХГС 25ХГС 30ХГМ
хорошая прочность и свариваемость, применяется в виде листов и труб для ответственных сварочных конструкций, например, в самолетостроении
σ в =1650Мпа δ =9%
Хромо-никелевые стали
30ХНА
30ХН3А
Высокая прокаливаемость, вязкость, крупные изделия сложной конфигурации, работающие при вибрационных и динамических нагрузках.
40ХН2МА
30Х2Н2МФА
Рессорно-пружинные стали
Рессорно-пружинные стали должны иметь особые свойства в связи с условиями работы пружин и рессор. Они служат для смягчения ударов, толчков, действующих на конструкцию в процессе работы. Поэтому основные требования к этим сталям заключаются в следующем:
-высокие пределы упругости и выносливости при достаточной пластичности и сопротивлении хрупкому разрушению
Содержание углерода в них –0,5-0,7%
Термообработка – закалка и средний отпуск
В качестве легирующих элементов в них чаще всего – кремний.
113

vk.com/club152685050 | vk.com/id446425943
55С2
60С2А
70С3А
для изготовления пружин вагонов. Многих автомобильных рессор
σв =1800 Мпа σ изг =1600Мпа
60С2ХФА
50ХФА крупные высоконагруженные пружины и рессоры
Дополнительное легирование хромом, марганцем, вольфрамом. никелем увеличивает прокаливаемость кремнистых сталей., уменьшает склонность их к обезуглероживанию, снижающие предел выносливости.
Если пружины и рессоры работают в условиях сильных динамических нагрузок, то применяют стали с никелем- 60С2Н2А
Для изготовления автомобильных рессор широко применяют сталь – 50ХГА, превосходящую по технологическим свойствам кремнистые стали.
Для клапанных пружин рекомендуют сталь марки 50ХФА, она не склонна к перегреву и обезуглероживании.
Оптимальная твердость рессор для получения максимального предела выносливости 42-48НРСэ
Долговечность пружин и рессор снижается при наличии на поверхности различных дефектов – забоин, рисок, царапин, играющих роль концентраторов напряжений.
114

vk.com/club152685050 | vk.com/id446425943
Срок службы пружин и рессор может быть повышен гидроабразивной и дробеструйной обработкой (поверхностным наклепом)
Шарикоподшипниковые стали
Кольца, ролики, шарики работают в условиях, которые требуют от стали высокой твердости, износостойкости, сопротивления контактной усталости.
В качестве шарикоподшипниковых сталей наиболее часто применяют высокоуглеродистые хромистые стали, а для больших сечений - хромомарганцовистые стали. прокаливающие на большую глубину.
ШХ6 хрома 0,6%
ШХ9 хрома 0,9%
ШХ15 хрома 1,5%
ШХ15СГ хрома 1,5% углерода 0,9-1,1 %
Термическая обработка шарикоподшипниковых сталей - закалка + низкий отпуск. Закалка от830-860оС в масле , отпуск 150-160 оС в течение 1 ч. Это обеспечивает ей твердость 62НРСэ.
Структура стали должна представлять отпущенный мартенсит, очень мелкоигольчатый с равномерно распределенными в ней карбидами.
115

vk.com/club152685050 | vk.com/id446425943
К данным сталям предъявляют высокие требования по содержанию неметаллических включений, которые являются концентраторами напряжений. Недопустима карбидная неоднородность.
Детали подшипников, работающие в агрессивных средах - морской воде,
азотной кислоте - изготавливают из стали 9Х18 |
(нержавеющая |
высокоуглеродистая). |
|
116

vk.com/club152685050 | vk.com/id446425943
Лекция 12
«Инструментальные материалы»
Инструментальные материалы подразделяются на:
стали (углеродистые, легированные)
твердые сплавы
сверхтвердые материалы
Наиболее распространенная группа инструментальных материалов – инструментальные стали – предназначены для изготовления инструментов 4- х групп:
режущих
измерительных
штампов холодного и горячего деформирования (служат для деформирования металла в холодном или горячем состоянии)
Основные требования, предъявляемые к инструментальным сталям:
высокая твердость
износостойкость
теплостойкость – способность сохранять высокую твердость при повышенных температурах или красностойкость.
Инструментальные стали подразделяются на следующие группы:
117
vk.com/club152685050 | vk.com/id446425943
1.ИНСТРУМЕНТАЛЬНЫЕ СТАЛИ ПОНИЖЕННОЙ ПРОКАЛИВАЕМОСТИ
Это углеродистые или легированные стали с малым процентом легирующих компонентов.
Марки их мы уже проходили –У7, У8, У9, У10, У11, У12, У13
Х05, Х06, 65ХФ, 85ХФ
При конструировании инструмента необходимо избегать острых углов, резких переходов.
Все стали данной группы закаливаются в воде
Углеродистые инструментальные стали (ГОСТ 1435).
Содержат 0,65…1,35% углерода.
Стали У7…У13А – обладают высокой твердостью, хорошо шлифуются, дешевы и недефицитны.
Из сталей марок У7, У8А изготавливают инструмент для работы по дереву и инструмент ударного действия, когда требуется повышенная вязкость – пуансоны, зубила, штампы, молотки.
Стали марок У9…У12 обладают более высокой твердостью и износостойкостью – используются для изготовления сверл, метчиков, фрез.
Сталь У13 обладает максимальной твердостью, используется для изготовления напильников, граверного инструмента.
Для снижения твердости и создания благоприятной структуры, все инструментальные стали до изготовления инструмента подвергают отжигу.
Для заэвтектоидных сталей проводят сфероидизирующий отжиг, в результате которого цементит вторичный приобретает зернистую форму. Регулируя скорость охлаждения можно получить любой размер зерен.
Окончательная термическая обработка – закалка с последующим отпуском.
Закалку для доэвтектоидных сталей проводят полную, а для заэвтектоидных – неполную. Структура закаленных сталей или мартенсит, или мартенсит и карбиды.
118
vk.com/club152685050 | vk.com/id446425943
Температура отпуска выбирается в зависимости от твердости, необходимой для инструмента.
Для инструментов ударного действия, требующих повышенной вязкости, из сталей У7, У8 отпуск проводят при температуре 280…300oС, что обеспечивает твердость HRC 56…58.
Для напильников, метчиков, плашек отпуск проводят при температуре 150…200oС, при этом обеспечивается получение максимальной твердости
— НRC 62…64.
Основными недостатками углеродистых инструментальных сталей является их невысокая прокаливаемость (5…10 мм), низкая теплостойкость (до 200oС), то есть инструменты могут работать только при невысоких скоростях резания.
ИНСТРУМЕНТАЛЬНЫЕ СТАЛИ ПОВЫШЕННОЙ ПРОКАЛИВАЕМОСТИ
Это легированные стали, содержащие 1-3 % легирующих элементов. инструмент закаливают в масле, поэтому он может иметь более сложную форму, уменьшается опасность возникновения трещин при закалке.
Это стали марок:
Х -850°/200° 64-61 НRСэ
9ХС – 800°/150° 65-65НRСэ
ХГСВФ –800°\180° 63-61 НRСэ
ХГ-800о\150° 63-61 НRСэ
ХВГ – 800о\150° 65-62 НRСэ
ХВ5-800/150° 65-62НRСэ
Однако эти стали не обладают теплостойкостью, она у них составляет 250°С
БЫСТРОРЕЖУЩИЕ СТАЛИ
Это стали, предназначенные для изготовления инструмента, работающего при высоких скоростях резания.
119
vk.com/club152685050 | vk.com/id446425943
Это сталь, в отличие от других сталей, обладают высокой красностойкостью, т.е. способностью сохранять мартенситную структуру, а соответственно и твердость при температуре 500-600°С. У ранее рассматриваемых сталей твердость начинает падать при температуре 200о, так как мартенсит распадается на феррито-цементитную смесь.
Применение быстрорежущих сталей позволяет увеличить в 2-4 раза скорости резания и 10-30 раз увеличивает стойкость инструмента
Основной легирующий элемент, обеспечивающий красностойкость стали
– это вольфрам и его химический аналог – молибден, а также хром, в таком количестве, при котором они связывают почти весь углерод в специальные карбиды. Теплостойкость увеличивается в присутствии кобальта и ванадия.
Марки быстрорежущих сталей: |
|
|
||
Р18 |
Р6М5 |
Р9Ф5 |
Р9К5 |
Р10К5Ф5 |
Р9 |
Р6М3 |
Р14Ф4 |
Р9К10 |
|
Быстрорежущие стали относятся к ледебуритному карбидному классу Состав стали Р18: 18 % вольфрама, 4 % хрома, 1 % углерода 1 % ванадия
Структура литой б\р стали – сложная эвтектика – ледебурит, располагающаяся по границам зерен.
В отожженном состоянии - легированный феррит + карбиды.
В деформированном состоянии – эвтектика дробится и равномерно распределяются карбиды.
После отжига (860-880°) – для улучшения обрабатываемости стали – структура – сорбитообразный перлит.
Для придания стали теплостойкости инструменты подвергают закалке и
многократному отпуску.
Температура закалки – 1270-1280°С для стали марки Р18 Температура закалки – 1210-1230°С для стали марки Р6М5
Высокая температура закалки - для более полного растворения вторичных карбидов и получения аустенита, легированного хромом, молибденом, вольфрамом и ванадием. при закалке аустенит переходит в мартенсит, охлаждающая среда – масло.
120
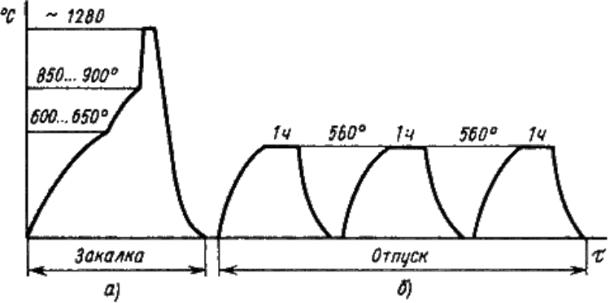
vk.com/club152685050 | vk.com/id446425943
Структура после закалки – высоколегированный мартенсит, нерастворенные карбиды и остаточный аустенит. (25-30% Аост.)
Остаточный аустенит понижает режущие свойства и поэтому присутствие его в режущем инструменте – не допустимо. Поэтому инструмент после закалки подвергают трехкратному отпуску при температуре 560°С. при этом остаточный аустенит переходит в мартенсит и увеличивает твердость стали.
Медленный нагрев – чтобы не было трещин.
Быстрый нагрев – чтобы не было окалины
Высокая температура – чтобы измельчить карбиды
При охлаждении на воздухе – фиксируются аустенитное поле и карбиды
На быстрорежущие стали имеется Гост 19265 –73 – всего предусмотрено 14 марок. Данные стали дефицитны и дороги за счет вольфрама, поэтому разрабатываются безвольфрамовые быстрорежущие стали.
СТАЛИ ДЛЯ ИЗМЕРИТЕЛЬНЫХ ИНСТРУМЕНТОВ
Они должны обладать:
высокой твердостью
износостойкостью
121
vk.com/club152685050 | vk.com/id446425943
сохранять постоянство размеров
Обычно используют высокоуглеродистые хромистые стали
Х, ХВГ,12Х1, ШХ15
Их подвергают закалке в масле с возможно более низкой температуры – 840850° - чтобы не было остаточного аустенита, который при переходе в мартенсит вызывает небольшое изменение объема и линейных размеров.
После закалке ведется отпуск или старение, и дальнейшая обработка холодом
ШТАМПОВЫЕ СТАЛИ ХОЛОДНОГО ДЕФОРМИРОВАНИЯ
Они должны отвечать следующим требованиям:
высокой твердостью
износостойкостью
прочностью в сочетании с вязкостью
теплостойкостью
Это стали следующих марок :
Х12Ф1
Х12М высокохромистые стали ледебуритного класса,
Недостаток - трудность обработки резанием
Лучшие в этом плане –Х6ВФ, 7ХГ2ВМ
ШТАМПОВЫЕ СТАЛИ ДЛЯ ДЕФОРМИРОВАНИЯ В ГОРЯЧЕМ СОСТОЯНИИ
Требования, предъявляемые данным сталям:
высокие механические свойства при высоких температурах
окалиностойкость и разгаростойкость ( выдерживать многократные нагревы и охлаждения без образования разгарочных трещин)
высокая износостойкость и теплостойкость
хорошую прокаливаемость (штампы имеют большие размеры)
Марки сталей 5ХНМ, 5ХГМ
4Х5В2ФС
3Х2В8Ф
122
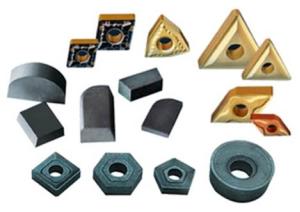
vk.com/club152685050 | vk.com/id446425943
ТВЕРДЫЕ СПЛАВЫ
Твердыми сплавами называют сплавы, изготовленные методами порошковой металлургии и состоящие из карбидов тугоплавких металловвольфрама, титана, тантала и сцементированных (связанных) кобальтом.
Инструмент, оснащенный твердым сплавом может работать с более высокими скоростями резания.
Для их изготовления берут порошки карбидов вольфрама, титана, смешивают со связкой – кобальт, прессуют, придавая им заданную форму и спекают при высоких (1500-2000°С). Поэтому названы – металлокерамические.
Твердость их очень велика, они не подвергаются механической обработке, только шлифуют. Из твердого сплава изготавливают пластинки, которые затем крепят на державку инструмента.
При высокой твердости сплав обладает повышенной хрупкостью и при работе с ударами может выкрашиваться.
ТВЕРДЫЕ СПЛАВЫ
ГОСТ 3882-74 Твердые сплавы 3 групп
ВОЛЬФРАМОВЫЕ –ВК3,ВК6,ВК8, ВК10,ВК20,ВК25
Теплостойкость их 800оС
ТИТАНО-ВОЛЬФРАМОВЫЕ –Т30К4, Т15К6, Т14К8, Т5К10
Теплостойкость их 900-1000оС
ТИТАНО-ТАНТАЛО-ВОЛЬФРАМОВЫЕ - ТТ7К10, ТТ8К6, ТТ10К8
они отличаются большей прочностью и лучшей сопротивляемостью вибрациям и выкрашиванию.
СВЕРХТВЕРДЫЕ МАТЕРИАЛЫ
К ним относят алмаз, твердость которого в 6 раз выше твердости карбидов вольфрама и в 8 раз выше быстрорежущей стали.
123

vk.com/club152685050 | vk.com/id446425943
80 % добываемых природных алмазов и все синтетические алмазы используются в качестве инструментальных материалов.
Основное количество алмазов используется в виде алмазного порошка для изготовления алмазно-абразивного инструмента – шлифовальных кругов, притиров, хонов, надфилей и др., для обработки особо твердых металлов и горных пород. Большое значение имеют заточные круги для твердосплавного инструмента, это увеличивает производительность труда и срок службы инструмента. Повышение стойкости твердосплавного инструмента обеспечивается высокой чистотой (отсутствие зазубрин, мелких трещин) лезвия инструмента.
Алмазный инструмент изготовляется в виде алмазосодержащих кругов с бакелитовой или металлической связкой.
Также изготавливают алмазные резцы (для обработки корпусов часов), фильеры (для волочения проволоки из высокотвердых и драгоценных металлов) и др.
Алмазным инструментом обрабатывают цветные материалы и их сплавы, пластмассы, керамику.
Преимущества имеют синтетические алмазы они обладают меньшей хрупкостью и стоимостью.
Алмаз теплостоек до 800°С, далее превращается в графит.
Большей универсальностью обладает инструмент из поликристаллического нитрида бора, называемого кубическим нитридом бора. КНБ получают спеканием микропорошков нитрида бора при высоких температурах и давлении. КНБ выпускают под названием
124
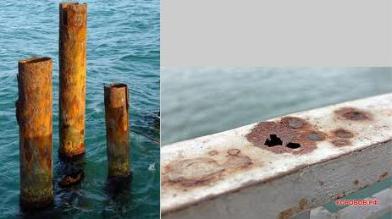
vk.com/club152685050 | vk.com/id446425943
ЭЛЬБОР. По твердости он не уступает алмазу, но превосходит его по теплостойкости – 1200°С.
Отсутствие у него химического сродства с железом позволяет его использовать более эффективно при обработке закаленных сталей.
Лекция 13 «Легированные стали с особыми свойствами»
ЛЕГИРОВАННЫЕ СТАЛИ И СПЛАВЫ
СОСОБЫМИ СВОЙСТВАМИ
Специальные стали – это высоколегированные (свыше 10%) стали,
обладающие особыми свойствами – коррозионной стойкостью, жаростойкостью, износостойкостью и др.
Коррозионно-стойкие (нержавеющие) стали
Углеродистые и низколегированные стали подвержены коррозии, т.е. разрушаются от химического воздействия окружающей среды.
Коррозией – называется разрушение металла под действием окружающей среды, в результате ее химического или электрохимического воздействия.
Ущерб, причиняемый коррозией может быть:
-прямым
-косвенным
Прямой включает в себя стоимость замены подвергшихся коррозии частей машин и др. Если проржавела крыша дома, труба парового отопления, кузов автомобиля, их меняют или ремонтируют.
125
vk.com/club152685050 | vk.com/id446425943
Для восстановления пораженных коррозией машин и конструкций ежегодно расходуется 20-25 млн тонн металла.
Косвенный ущерб от коррозии – это простой оборудования в результате аварий, увеличение расхода топлива, материалов.
По внешнему виду коррозия обычно проявляется в потере металлического блеска и появления на поверхности металла продуктов коррозии - ржавчины бурого цвета, а также резком падении механических свойств.
В зависимости от свойств окружающей среды различают следующие виды коррозии:
химическую – протекающую под действием на металл газов и не электролитов (нефть и нефтепродукты)
электрохимическую –вызываемую действием электролитов: кислот, щелочей и солей. К ней также относят атмосферную и почвенную коррозию.
Легированные стали с особыми свойствами
Электрохимическая коррозия может быть нескольких видов:
Если металл однороден (твердый раствор), то наблюдается равномерная коррозия, протекающая примерно с одной скоростью по всей поверхности металла.
В неоднородном металле, что является наиболее частым, коррозия носит локальный характер. Эту локальную коррозию подразделяют на:
точечную
пятнистую
с язвами
Эти очаги являются концентраторами напряжений. Наиболее опасна так называемая интеркристаллитная коррозия, распространяющаяся по границам зерен, она быстро развивается по границам зерен вглубь металла, резко снижая механические свойства. Сталь, пораженная ею теряет металлический звук.
Существует коррозия под напряжением – она возникает под действием одновременно коррозионной среды и напряжений растяжения.
126
vk.com/club152685050 | vk.com/id446425943
Разновидностью ее является коррозионное растрескивание, образование в металле тонкой сетки трещин, проходящих по объему зерна при воздействии коррозии и напряжений.
Сталь, устойчивую против электрохимической коррозии, называют КОРРОЗИОННО-СТОЙКИМИ или НЕРЖАВЕЮЩИМИ
Антикоррозионными свойствами сталь обладает в том случае, если она легированна большим количеством хрома или хрома и никеля. Таким образом, коррозионно-стойкие стали можно разделить на 2 основных класса:
Хромистые стали, имеющие после охлаждения на воздухе ферритную, мартенситно-ферритную или мартенситную структуру
Хромо-никелевые - имеющие аустенитную, аустенито-мартенситную или аустенито-ферритную структуру.
Хромистые нержавеющие стали
Содержание хрома в них должно быть не менее 12 %. При меньшем его содержании сталь не способна сопротивляться коррозии, т.к. ее электродный потенциал становится отрицательным. Наибольшую коррозионную стойкость сталь достигает после соответствующих термической (закалка + высокий отпуск)и механической (шлифование и полирование) обработок.
Сталь обладает лучшей стойкостью против коррозии только при условии, что все содержание хрома в стали приходится на долю твердого раствора. В этом случае он образует на поверхности плотную защитную окисную пленку Сr2Oз.
Эти стали должны содержать малый процент углерода, так как увеличение процента углерода приводит к образованию карбидов, уменьшающих количество хрома в твердом растворе и соответственно понижает коррозионную стойкость.
Наиболее распространенные марки нержавеющих хромистых сталей:
12Х13 – сталь мартенситного класса, закалка от 1000-1100о в масле и отпуска (700-750о) и полировки.
Это сталь устойчива в слабоагрессивных средах (вода, пар), применяется для деталей с повышенной пластичностью ( клапаны гидравлических прессов,
предметы домашнего обихода) σв =600-660Мпа |
δ = 16-20% |
127
vk.com/club152685050 | vk.com/id446425943
20Х13
30Х13-карбюраторные иглы
40Х13 – сталь также мартенситного класса, применяется после закалки от 1000-1050о и отпуска (180-200о) и шлифования и полирования. Это хирургический инструмент, бытовой режущий инструмент, шарикоподшипники, работающие в агрессивных средах. 52-55НРСэ.
12Х17 – более коррозионно-стойка ( кислоты и др. среды), ферритного класса.
15Х28 применяется для химического и пищевого оборудования. Однако она не пригодна для изготовления сварных конструкций.
При нагреве происходит обеднение периферийной зоны зерен хромом, что приводит к межкристаллитной коррозии. Это наиболее опасный вид коррозионного разрушения по границам аустенитных зерен. Для предотвращения его в сталь вводят титан. Он связывает углерод и исключает образование карбидов хрома.
08Х17Т – для сварных конструкций.
Хромо-никелевые нержавеющие стали
Они содержат большое количество хрома и никеля, мало углерода и относятся к аустенитному классу. Кроме аустенита в них находятся карбиды хрома.
12Х18Н9- для получения аустенитной структуры ее закаливают в воде от 1100-1150ос, при этом достигается высокая коррозионная стойкость при сравнительно малой прочности. Для повышения ее сталь подвергают холодной пластической деформации (наклепу) и применяют в виде холоднокатанного листа ленты. 17Х18Н9
Так же как и сталь ферритного класса она вследствие обеднения зерен хромом (выделяются карбиды хрома) склонна к межкристаллитной коррозии. Для ее предотвращения сталь дополнительно легируют титаном или уменьшают процент хрома.
Например, 12Х18Н9Т или 04Х18Н9- для изготовления химической аппаратуры
Большим достоинством хромо-никелевых сталей аустенитного класса является их хорошая технологичность в отношении ОМД и сварки.
128
vk.com/club152685050 | vk.com/id446425943
12Х18Н10Т – используется в криогенной технике для транспортировки и хранения жидких газов, резервуаров, топливных баков. Но эти стали очень дороги , поэтому дефицитный никель может быть заменен марганцем : 10Х14Г14Н4Т
08Х22Н6Т
12Х21Н5Т – это стали аустенито-ферритного класса, более прочны, чем аустенитные
09Х15Н8Ю – аустенито-мартенситного класса, высокая коррозионная стойкость + хорошие механические свойства + хорошая свариваемость
Высоколегированные кислотостойкие стали
06ХН28МДЮ – кислотостойкая сталь Для более тяжелых условий применяют сплавы никеля и меди – монель, Никеля и хрома – инконель Никеля и молибдена - хастеллой
ЖАРОСТОЙКИЕ СТАЛИ
При высоких температурах сплавы вступают во взаимодействие с окружающей газовой средой. Что вызывает газовую коррозию (окисление) и разрушение металла.
Для изготовления конструкций, работающих в условиях повышенных температур (400-900°) применяют специальные жаростойкие стали.
Под жаростойкостью или окалиностойкостью - принято понимать способность материала противостоять коррозионному разрушению под действием воздуха и др. газов при высоких температурах.
Жаростойкость принято характеризовать температурой начала интенсивного окалинообразования, когда на поверхности стали образуется сначала тонкая пленка окислов, которая с течением времени увеличивается и образуется окалина.
Если окисная пленка пористая – окисление происходит интенсивно
Если – плотная – окисление замедляется или даже совершенно прекращается.
129
vk.com/club152685050 | vk.com/id446425943
Для получения плотной (защитной) окисной пленки сталь легируют хромом, кремнием или алюминием.
Степень жаростойкости зависит от количества легирующих элементов.
15Х5 хрома 5% |
- жаростойкость до 700°12Х17 - хрома 17% - |
до 900° |
|
15Х28 -хрома 28% |
до 1100-1150° |
Чем выше содержание хрома – тем выше жаростойкость.
Важно. Что жаростойкость, столь существенно зависящая от состава, не
зависит от структуры сплава.
Так, жаростойкость ферритных сталей (чисто хромистых) и аустенитных ( хромо-никелевых) практически одинакова.
Например,12Х17 и 12Х18Н9 – жаростойкость их 900°
Еще большей жаростойкостью обладают сплавы на никелевой основе с хромом и алюминием. ХН70Ю
Жаропрочные стали и сплавы К жаропрочным относят стали и сплавы, способные работать в
нагруженном состоянии при высоких температурах в течение определенного времени и обладающие при этом достаточной жаростойкостью.
На уменьшение прочности стали влияет не только само повышение температуры, но и длительность воздействия нагрузки.
В результате этого сталь «ползет» и это явление названо ползучестью.
Ползучесть – это деформация, непрерывно увеличивающаяся и завершающаяся разрушением под действием постоянной нагрузки при длительном воздействии температуры.
Жаропрочность характеризуется пределом ползучести.
Это напряжение, вызывающее заданную по значению деформацию
(обычно от 0,1 до 1%) за промежуток времени (100, 300, 500, 1000 часов) при заданной температуре.
130
vk.com/club152685050 | vk.com/id446425943
Кроме этого жаропрочность характеризуется пределом длительной
прочности.
Это напряжение, вызывающее разрушение при данной температуре за данный интервал времени.
Факторы, способствующие повышению жаростойкости:
Высокая температура плавления основного металла
наличие в сплаве твердого раствора и мелкодисперсных частиц
пластическая деформация, вызывающая наклеп
высокая температура рекристаллизации
рациональное легирование
термическая обработка и термомеханическая обработка
Жаропрочные стали классифицирую по одному признаку, температуре эксплуатации:
Основой котлостроения являются перлитные жаропрочные стали.
Они применяются при температурах до 580 °C. Технологичны, недороги. Содержат 0,25-0,3 % С и легирующие элементы: хром, молибден, ванадий.
Марки: 12Х1МФ, 25Х2М1Ф.
Из перлитных жаропрочных сталей изготавливают трубы пароперегревателей, паропроводов и других частей теплоэнергетических установок, а также валы и цельнокованые роторы, плоские пружины, крепеж.
Мартенситные жаропрочные стали прочнее и выдерживают температуру до 650 °C. Это так называемые сильхромы (например, 40Х10С2М), легированные хромом и кремнием, а также 11Х11Н2В2МФ, 15Х11МФ, 18Х12ВМБФР. Последние имеют МПа.
Сильхромы стойки к окислению в парах и топочных газах. Их закаливают
с |
1000 |
°C |
и |
отпускают |
при |
700 °C. Применяют для клапанов ДВС.
Они плохо свариваются и труднее перлитных сталей обрабатываются резанием.
131
vk.com/club152685050 | vk.com/id446425943
Аустенитные жаропрочные стали работают до 700 °C.
Подразделяются на однофазные (12Х18Н10Т), стали с карбидным
упрочнением и стали с интерметаллидным упрочнением. Стали аустенитного класса подразделяются на :
неупрочняемые (нестареющие)
09Х14Н16Б – закалка с охлаждением на воздухе.
упрочняемые (стареющие), сложнолегированные 40Х15Н7Г7Ф2МС- для лопаток газовых турбин, закалка с 1050-1200 ° с последующим длительным старением 600-800 °
При более высоких температурах применяют жаропрочные сплавы на никелевой основе, например,
ХН77ТЮР для лопаток турбин, жаростойкость их до 1200о
Жаропрочных сплавов очень много. Но в основном они секретны.
CТАЛИ И СПЛАВЫ С ОСОБЫМИ ЭЛЕКТРОМАГНИТНЫМИ СВОЙСТВАМИ
Магнито-твердые стали и сплавы
К магнитотвердым относят материалы с высокой коэрцетивной силой, мало изменяющейся во времени. Эти материалы служат для изготовления постоянных магнитов.
Для получения высокой коэрцетивной силы более эффективной оказалась не нормальная решетка ОЦК (альфа-железо), а искаженная тетрагональная решетка альфа железа в мартенсите.
Поэтому эти стали закаливают на мартенсит с минимальным количеством остаточного аустенита. Это могут быть высокоуглеродистые и легированные стали с высокодисперсной неравновесной структурой.
Для наиболее слабых магнитов применяют инструментальные стали У10У12, они прокаливаются на небольшую глубину и применяются для изготовления магнитов с размерами сечения 4-7 мм.
Для изготовления наиболее сильных магнитов используют хромистые стали с 1% хрома и 3% хрома.
132
vk.com/club152685050 | vk.com/id446425943
ЕХ
ЕХ3
ЕХ5К5 - кобальта 5%, хрома 5%. имеет более высокие магнитные свойства
Магнитные сплавы имеют очень высокую твердость, но хрупки, поэтому обрабатываются только шлифованием. Магниты из этих сплавов изготавливают либо литьем, либо спеканием из порошков.
В последнее время широко распространены железо-никель-алюминиевые сплавы для постоянных магнитов 11-14%алюминия, 22-34% никеля, с добавками меди, кремния, кобальта. По магнитной мощности они превосходят стальные.
Ални- железо-алюминий и никель
Алниси-+ кремний
Алнико + кобальт и медь
Викаллой - 52% кобальта, 14% ванадия остальное - железо
Магнитомягкие стали и сплавы
Они должны отличаться очень малой коэрцетивной силой, что необходимо для уменьшения потерь энергии при их перемагничивании.
Для получения магнитной мягкости необходимо:
максимальное приближение к равновесному состоянию
максимально крупное зерно
исключить источники, вызывающие искажение решетки и дробление
блоков Таким образом, наиболее подходящими являются чистые металлы, в первую
очередь железо - феррит - техническое железо. Это могут быть и сплавы на основе никеля и кобальта, железо-никелевые сплавы - пермаллои.
Электротехническое железо (Армко-железо)
Марки его Э, ЭА,ЭАА Содержит не более 0,04%С, зерно по возможности крупное, специальный отжиг.
Кремнистые стали - электротехнические стали
Э11, Э12
133
vk.com/club152685050 | vk.com/id446425943
Э21,Э22 - динамные стали, для изготовления деталей динамомашин, генераторов тока
Э31,Э32
Э41,Э42 - трансформаторные стали- для изготовления сердечников трансформаторов 1-я цифра - % кремния
2-я цифра - гарантированные электрические и магнитные свойства Эти стали изготавливаются в виде листов Железо-никелевые сплавы -пермаллои- содержат 45-80% никеля ,
дополнительно хром, кремний, молибден. Их применяют в аппаратуре связи.
Немагнитные стали
Относятся к высоколегированным сталям аустенитного класса, т.к. только решетка гамма железа не магнитна.
Эти стали применяются в электрических машинах взамен менее прочных и дорогих цветных металлов.
Наиболее распространенные марки:
ЭИ269 - углерода 0,5-0,6%, марганца - 4-5,5%, никеля 20%
55Г9Н9Х3
45Г17Ю3
Сплавы высокого электросопротивления
Они делятся на следующие группы:
сплавы для реостатов
сплавы для нагревательных элементов
Они должны отличаться высоким электросопротивлением (низкой электропроводностью). Поэтому они представляют собой сплавы - твердые растворы, а не чистые металлы.
Наиболее распространенные сплавы для реостатов:
Манганин - МНМц3 - 3%никеля, 12%марганца остальное медь
Константан - МНМц40-1,5 - 40% никеля 1.5% марганца остальное медь
Копель - МНМц43-0,5 - 435никеля, 0,5% марганца, остальное медь
Сплавы для нагревательных элементов, поскольку они работают при очень высоких температурах в окислительной среде. должны быть одновременно и окалиностойкими, т.е. не окисляться и не прогорать.
В их составе всегда присутствует хром и алюминий.
134

vk.com/club152685050 | vk.com/id446425943
Наиболее употребительные сплавы этой группы:
Фехраль (Х13Ю4) -углерода менее0,15% предельная рабочая температура 1000°
Лекция 14
«Медь и ее сплавы»
Медь чаще других металлов встречается в виде самородков, иногда достигающих весьма больших размеров. Естественно это один из первых металлов, с которым познакомился человек.
Значение меди и ее сплавов в деятельности человека было столь велико, что это нашло отражение в названии целых эпох в развитии человечества (медный век, бронзовый).
Медь и ее сплавы, обладающие ценными техническими свойствами, широко применяются и в наше время.
По электропроводности Си занимает 2 место после серебра и поэтому является одним из важнейших материалов для проводников
По теплопроводности Си также уступает только серебру и ее широко используют в теплообменниках.
Сплавы меди отличаются достаточной коррозионной стойкостью, высокими технологическими свойствами, имеют приятный цвет и полируются до сильного блеска.
Медь и ее сплавы хорошо обрабатывается давлением , из них производят все виды полуфабрикатов, получаемых обработкой металлов давлением: плиты, листы, ленту, фольгу, поковки, штамповки, трубы, профили, проволоку.
Медь и ее сплавы хорошо свариваются всеми видами сварки, легко поддаются пайке.
135
vk.com/club152685050 | vk.com/id446425943
При ее обработке резанием особых затруднений не возникает.
К недостаткам меди можно отнести ее высокую плотность, склонность к окислению при повышенной температуре, ее высокую стоимость и дефицитность.
Меди в земной коре сравнительно немного (0,01%), но известны богатые ее месторождения
Свойства меди
Тпл.=1083°
Тип решетки -ГЦК
плотность -8,95 г/смз
Т кипения 2360°
Чистейшая медь обладает небольшой прочностью и высокой пластичностью.
Техническая медь имеет следующие марки:
|
М00 |
Си не менее |
99,99% |
|
М0 |
- |
99,95% |
|
М1 |
- |
99,9% |
|
М2 |
- |
99,7% |
|
М3 |
- |
99,5% |
Механические свойства технической меди |
|||
|
|
в =220-260Мпа |
=40-45% |
Области применения меди
Они очень разнообразны: Сu широко используется в электротехнике: это провода высоковольтных линий электропередач, воздушных линий связи, троллейбусные провода, коллекторные шины для электромашин, токопроводящие шины.
Это всевозможные теплообменники, водоохлаждаемые поддоны, кристаллизаторы, обеспечивающие интенсивный отвод тепла от расплава.
136
vk.com/club152685050 | vk.com/id446425943
Влияние примесей на свойства меди
Присутствующие в меди примеси существенно влияют на ее свойства.
По характеру взаимодействия примесей с медью их можно разделить на следующие группы:
Примеси, образующие с медью твердые растворы. Это никель, цинк,
сурьма, олово, алюминий, фосфор и др. Они улучшают механические свойства, но резко снижают (особенно сурьма и фосфор) электро и теплопроводность.
Примеси практически не растворимые в меди: это свинец, висмут, и
др. и образующие легкоплавкие эвтектики. Они располагаются по границам зерен и затрудняют обработку давлением. На электропроводность они не оказывают большого влияния, а влияют на механические и технологические свойства. (Висмут - хладноломкость, свинец-горячеломкость)
Примеси, образующие с медью хрупкие химические соединения - это
кислород, сера, располагающиеся по границам зерен (Си2О, Си2S)
На электропроводность они не влияют. Сера улучшает обрабатываемость резанием.
Кислород образует с медью оксид меди и вызывает так называемую "водородную болезнь" - так как при нагреве меди в атмосфере, содержащей водород, он реагирует с Си2О по реакции, протекающей с увеличением объема. Это создает в металле большое давление и вызывает появлением микротрещин.
Сплавы меди
Различают две основные группы медных сплавов: ЛАТУНИ - сплавы меди и цинка и БРОНЗЫ - сплавы меди с другими элементами, в числе которых, но только наряду с другими может быть и цинк.
Сплавы меди маркируются следующим образом: Латуни - буквой Л и цифра, указывающая содержанием в ней меди. Например, Л96, Л80, Л59, остальное - цинк.
Бронзы - Брбронзы, а далее элемент: олово - 0, свинец -С, алюминий -А,
бериллий -Б, марганец -Мц, кремний -К, железо - Ж, никель -Н, фосфор - Ф, а далее цифра, показывающая процент этого элемента.
Например, БрА9, БрО10, ЛАН 59-1-1, ЛС60-3
137

vk.com/club152685050 | vk.com/id446425943
ЛАТУНИ
Механическая прочность латуней выше, чем у меди, они хорошо обрабатываются резанием, большое их преимущество - пониженная стоимость, т.к. цинк дешевле меди.
Латуни лучше, чем медь обрабатываются давлением и литьем.
Al Ni Fe вводят в латунь для улучшения ее механических свойств Sn Mn вводят в латунь для повышения коррозионной стойкости Pb - для улучшения обработки резанием
По технологическому признаку латуни могут быть:
-литейные ( для фасонных отливок, их поставляют в виде чушек) -деформированные ( их поставляют в виде прутков, проволоки, труб, листов )
Как видно из диаграммы состояния различают однофазные альфа-латуни, содержащие до 39% цинка (вердый раствор цинка в меди). В сплавах, содержащих от 39 до 50% цинка образуется бэтта фаза (твердый раствор цинка в электронном соединении СиZn)
Латуни, содержащие более 45% - не применяются.
2-х фазные латуни имеют более высокую прочность и износостойкость, чем однофазные альфа-латуни.
Альфа-латуни- Л96 -томпак, Л80 (полутомпак) и Л70
138
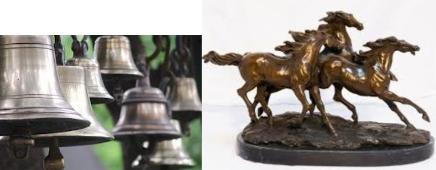
vk.com/club152685050 | vk.com/id446425943
σ = 240-320Мпа |
δ =50-52% |
Двух-фазные латуни -Л62, Л59 имеют σ=360-390 Мпа δ =44-49% они малопластичны, их подвергают ГОД Латуни упрочняются в процессе деформирования.
Для снятия наклепа применяют рекристаллизационный отжиг при температуре 500-700°С Латуни плохо обрабатываются резанием, для улучшения их
обрабатываемости в них добавляют свинец, их называют автоматными латунями.(ЛС59-1)
Олово улучшает коррозионную стойкость латуней. (ЛО60-2) - морская
латунь
ЛМцС58-2-2 - антифрикционные детали, втулки ЛМцЖ55-3-1 - гребные винты
Бронзы
Из бронз еще в древности делали оружие, орудия труда, предметы обихода. Бронза более прочна и коррозионностойка, чем медь. Благодаря отличным литейным свойствам из нее стали отливать пушки, колокола и статуи.
Современные оловянные бронзы значительно тверже меди, они хорошо заполняют форму при литье и обрабатываются резанием, отличаются высокой коррозионной стойкостью. Бронзу используют при изготовлении арматуры газовых и водопроводных линий в химическом машиностроении и др. отраслях Малый коэффициент трения и устойчивость к износу делает их
незаменимыми при изготовлении вкладышей подшипников скольжения, червячных колес, шестерен ответственных деталей машин и приборов.
Оловянные бронзы
Это сплавы меди и олова, содержащие олова до 12 %.
Как видно из диаграммы состояния медь-олово, олово растворимо в меди до 12%, далее возникают механические смеси, химические соединения и свойства бронз резко ухудшаются.
139

vk.com/club152685050 | vk.com/id446425943
В реальных условиях охлаждения структура бронзы состоит из альфатвердого раствора и дельта-фазы (близкой к химическому соединению). Оловянные бронзы склонны к ликвации, они имеют резко выраженное дендритное строение Сплавы более богатые оловом (более 12%) очень хрупки.
Маркируют бронзы буквами Бр и цифрой, показывающей процент олова. Например, БрО10, БрО6 Бронза марки Бр010 имеет в = 200Мпа =10%
Обработке давлением можно подвергать бронзы, содержащие не более 5-6 % олова. Они проходят рекристаллизационный отжиг (600-650оС) для придания готовым полуфабрикатам (листам, лентам) требуемых свойств.
Оловянные бронзы дороги. Для их удешевления в них добавляют свинец, цинк (свинец улучшает обрабатываемость), можно добавлять до 1 % фосфора, он повышает механические и антифрикционные свойства.
Оловянные бронзы имеют прекрасные литейные свойства, очень жидкотекучи - это прекрасный литейный материал. Из нее изготавливают всевозможные вентили и др. детали. Она хорошо сопротивляется коррозии. Но имеет два но!!!
Если ее медленно охлаждать, то растворимость ее пойдет по пунктиру, т.е.
твердый раствор будет распадаться с выделением химического
140
vk.com/club152685050 | vk.com/id446425943
соединения. Поэтому бронзы нужно отливать в кокиль или применять центробежное литье.
Олово - это дорогостоящий материал и дефицитный.
Бр03Ц7С5Н3- втулки, подшипники, арматура в морской воде
Бр04Ц3- токоведущие контакты, пружины
Алюминиевые бронзы
Содержат до 10% алюминия, представляют собой - твердый раствор алюминия в меди и являются однофазными структурами.
алюминиевые бронзы, содержащие до 6-8% алюминия обрабатываются давлением в холодном и горячем состоянии
Бронзы, содержащие 8-10 % алюминия обрабатываются давлением только при высоких температурах, они обладают лучшими литейными свойствами и их применяют для фасонного литья.
Они устойчивы против коррозии.
|
БрА9Ж4 - |
σ=550 Мпа |
δ = 15% фасонное литье |
|
БрАЖ9-4 |
σ=850Мпа |
δ =5% прутки поковки |
БрА5 -мелкая разменная монета
Данные бронзы обладают высокими механическими свойствами. повышенной жаропрочностью и антикоррозионной стойкостью. По сопротивлению коррозии они в 12 раз устойчивее оловянных бронз. в 2-3 раза - нержавеющих сталей
БрАЖМц10-3-1.5 -детали химической аппаратуры
Кремнистые бронзы
Кремнистые бронзы превосходят оловянистые по механическим свойствам. они являются более дешевыми. устойчивы против коррозии.
обладают высокой пластичностью. Содержание кремния в них до 3 %.
БрК3Мц1 -ленты. проволока, пружины. сварные резервуары в пищевой промышленности
После прокатки и отжига имеют |
в = 380 Мпа |
= 45% |
141
vk.com/club152685050 | vk.com/id446425943
Бериллиевые бронзы
Они содержат 2-2.5 % бериллия. Из всех известных бронз они обладают наилучшим комплексом свойств. Хорошо свариваются, обрабатываются давлением. в них удачно сочетаются - электропроводность, коррозионная стойкость, упругость, прочность.
Из нее изготавливают особо ответственные детали - сильфоны, мембраны, пружины, пружинистые контакты (при работе не дают искр), детали электронной техники
Бериллиевые бронзы подвергают термической обработке - закалке и старению. В результате термообработке значительно улучшаются механические свойства.
При закалке фиксируется пересыщенный альфа раствор. При старении (отпуске) упрочняющие частицы.
|
После закалки - (760-780°) |
в |
=500 Мпа |
|
=45% |
|
После старения -(300-350°) |
в |
=1300Мпа |
|
=1,5 |
БрБ2
БрБ1,5
Свинцовые бронзы
Содержат до 30 % свинца. Свинец и медь не растворимы друг в друге, поэтому структура - твердая медь и мягкий свинецобеспечивают хорошие антифрикционные свойства применяются для изготовления вкладышей подшипников
БрС30 |
в =60Мпа |
= 40% |
142

vk.com/club152685050 | vk.com/id446425943
Лекция 15
«Материалы с малой плотностью (легкие материалы)»
Материалы с малой плотностью
Это материалы, широко применяемые в авиации, ракетной и космической технике, автомобиле - и судостроении. строительстве и др. отраслях. Применение легких материалов дает возможность:
снизить массу конструкции
увеличить грузоподъемность летательных аппаратов без снижения скорости и дальности полета
повысить скорость движения автомобилей, судов. ж/д транспорта
К основным конструкционным легким материалам относят алюминий, титан, магний. бериллий и сплавы на их основе, а также пластмассы.
143

vk.com/club152685050 | vk.com/id446425943
Особенно перспективны материалы, которые дают возможность снизить массу конструкции при одновременном повышении их прочности и жесткости.
Основным критерием при выборе материала в этом случае является удельная прочность и удельная жесткость.
Наибольшей удельной прочностью и жесткостью обладают сплавы титана, бериллия, композиционные материалы - из них изготавливают высоконагруженные детали.
Сплавы на основе алюминия, магния и пластмассы идут для изготовления мало - и средненагруженных деталей.
Алюминий и его сплавы
Алюминий второй, самый распространенный после железа металл в современной технике.
плотность его 2,7 г/см 3 ( в три раза легче железа)
температура плавления - 660°решетка его - гранецентрированный куб
Алюминий обладает высокой электропроводностью (57% от электропроводности меди)
Алюминий обладает хорошей теплопроводностью и теплоемкостью.
Алюминий и его сплавы
Алюминий быстро окисляется на воздухе, покрываясь тонкой пленкой окиси – Аl2О3, которая в отличие от окиси железа не пропускает
кислород в толщу металла, что обеспечивает его защиту от коррозии. Механические свойства алюминия сравнительно невысокие
144
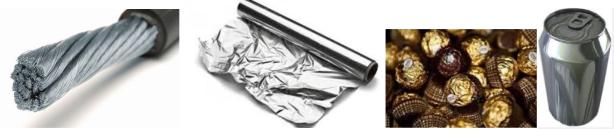
vk.com/club152685050 | vk.com/id446425943
σ = 90-180 |
Мпа |
твердость 20-40НВ, но он имеет высокую пластичность |
δ =35-40%, что дает возможность прокатывать его в очень тонкие листы. |
||
Алюминий |
хорошо |
обрабатывается давлением, сваривается, но плохо |
обрабатывается резанием.
Первичный алюминий (ГОСТ 11069-74) делят на 3 группы
1. Алюминий особой чистоты А999 (А = 99,999%)
2. Алюминий высокой частоты (4 марки -А995,А99,А97,А95)
3. Алюминий технической частоты (А85,А8,А7,А6,А5А0, соответственно алюминия 99,85,99,8,99,7,99,6,99,5 и 99,0%)
ПРИМЕНЕНИЕ АЛЮМИНИЯ
В виду низкой прочности алюминий применяют для ненагруженных деталей и элементов конструкций, когда от материала требуется легкость, свариваемость, пластичность. Так из него изготавливают рамы, двери, трубопроводы, фольгу, цистерны для перевозки нефти и нефтепродуктов, посуду и др.
Благодаря высокой теплопроводности он используется для различных теплообменников в промышленных и тепловых холодильниках.
Высокая электропроводность алюминия способствует его широкому применению для конденсаторов, проводов, кабелей, шин и др.
Алюминий имеет высокую отражательную способность, поэтому его используют для прожекторов, рефлекторов, экранов телевизоров.
Алюминий применяют в металлургии, где используется его большое сродство к кислороду, для получения в чистом виде дорогих и редких металлов - хрома, ванадия и др.
Низкие сорта алюминия используются для раскисления стали.
Соединения алюминия безвредны для человека, поэтому он широко используется в пищевой промышленности - обертки конфет. сыра и др. продуктов, для аппаратуры молочных и пивоваренных предприятий.
145

vk.com/club152685050 | vk.com/id446425943
СТРОЕНИЕ И СВОЙСТВА АЛЮМИНИЕВЫХ СПЛАВОВ
Классификация алюминиевых сплавов по диаграмме состояния: а - двойная система, 1 - сплавы, не упрочняемые термической обработкой, 2 - сплавы, упрочняемые термической обработкой.
В качестве конструкционных материалов алюминий широко применяется в виде сплавов с такими металлами и неметаллами как медь, марганец, магний, кремний, железо. никель титан и др.
Алюминиевые сплавы сочетают в себе лучшие свойства чистого алюминия и повышенные прочностные характеристики легирующих добавок.
Так, Fе Ni Ti - повышают жаропрочность алюминиевых сплавов
Cu Mn Mg - обеспечивают упрочняющую термообработку
В результате легирования и термической обработки удается в несколько раз повысить прочность (с 100 до 500 Мпа ) и твердость (НВ с 20 до 150)
По технологическому признаку алюминиевые сплавы делятся на три группы:
деформированные
литейные
получаемые методом порошковой металлургии (САП-спеченные алюминиевые порошки и САСспеченные алюминиевые сплавы)
146

vk.com/club152685050 | vk.com/id446425943
В свою очередь деформированные алюминиевые сплавы делятся на :
-упрочняемые термообработкой
неупрочняемые термообработкой
Легирующие элементы образуют с алюминием твердые растворы ограниченной растворимости и промежуточные фазы.
Термическая обработка - закалка на пересыщенный твердый раствор + естественное или искусственное старение
Деформированные алюминиевые сплавы применяют для получения листов, ленты, фасонных профилей. проволоки и различных деталей штамповкой, прессованием, ковкой.
Деформированные алюминиевые сплавы. не упрочняемые термической обработкой
К ним относят сплавы Амц и Амг - сплавы алюминия с марганцем и алюминия с магнием ( магния до 6 %)
Они характеризуются невысокой прочностью, но хорошей до 40% пластичностью, высокой коррозионной стойкостью, хорошей свариваемостью.
Сплавы типа Амц и Амг применяют для изделий получаемых глубокой вытяжкой, сваркой, от которых требуется высокая коррозионная стойкость - трубопроводы для бензина и масла. сварные баки. а также заклепки, переборки корпусов и мачт судов, лифты, узлы подъемных кранов, рамы вагонов. кузова автомобилей. и др.
Амц - 1-1,6 % марганца
Амг2 - 2 % магния 0,2-0,6 марганца
Амг5 - 5 % магния 0,3-0,8 марганца
147
vk.com/club152685050 | vk.com/id446425943
Это однофазные структуры - твердые растворы Упрочнение их возможно только путем холодной деформации.
Деформированные сплавы, упрочняемые термической обработкой
К данной группе относят следующие виды сплавов:
-дуралюмины
-авиали
-высокопрочные алюминиевые сплавы
-ковочные алюминиевые сплавы
-жаропрочные алюминиевые сплавы
Они имеют в своем составе по 3-4 и более компонентов, но всегда содержат медь.
ДУРАЛЮМИНЫ Дуралюмины - это сплавы алюминия на основе меди и магния, в которые для повышения коррозионной стойкости вводят марганец.
Марки дуралюминов Д16, Д18,Д1 -цифра условный номер сплава по
ГОСТу. |
|
|
Д1: меди -3,8-4,8 % |
σ= 400Мпа δ=20% |
95НВ |
магния - 0,4-0,8 %
марганца - 0,4-0,8 % Д16: меди- 3,8-4,9 %
|
магния -1,2-1,8 % σ =440Мпа |
δ =18% 105НВ |
марганца 0,3-0,9 %
Железовредная примесь для дуралюминов
Железо снижает эффект упрочнения при закалке
Способность их упрочняться можно показать на диаграмме состояния алюминиймедь
Медь образует с алюминием твердый раствор переменной растворимости.
Если двухфазный сплав нагреть до 500-540 о, то частицы СиА
растворяются в алюминии и сплав приобретает однофазную структуру твердого раствора. Быстрое охлаждение его (закалка) не дает
148

vk.com/club152685050 | vk.com/id446425943
возможность выделится фазе СuАl2 из твердого раствора, что позволяет получить упрочнение сплава.
Состояние пересыщенного твердого раствора неустойчиво и в нем самопроизвольно начинается выделение избыточной меди. В результате продолжительного выдерживания при комнатной температуре спустя 4-5 суток прочность сплава увеличивается до 400Мпа, одновременно уменьшается пластичность -- это называется естественное старение.
Рентгеноструктурный анализ показал, что упрочнение является следствием изменений в тонком кристаллическом строении. Сразу после закалки начинается диффузия атомов меди к некоторым участкам. Эти скопления меди образуются в местах скопления дислокаций. Впервые эти образования обнаружили одновременно француз Гинье и англичанин Престон, в честь их эти зоны назвали зонами Гинье-Престона.
при нагревании до 150-200° диффузия атомов идет активнее, поэтому процесс идет за несколько часов. Это будет искусственное старение.
Обязательным компонентом дуралюминов является марганец. повышающий коррозионную стойкость сплава.
температурный интервал закалочных температур очень мал
Д1 505510 о |
|
Д6 495-505 о |
|
Д16 495-505 |
|
Без термообработки - σ=220 Мпа |
δ=15-17% |
149
vk.com/club152685050 | vk.com/id446425943
После термообработки свойства мало изменяются, но после старения они увеличиваются: σ =420-470Мпа δ = 15-17%
Применение дуралюминов
детали машин, конструкции в виде листов, лент, прутков, профилей. Дуралюмины широко применяются в авиации
Д1лопасти воздушных винтов
Д18 - шпангоуты, нервюры, тяги управления
Их используют для строительных конструкций, кузовов грузовых автомобилей
Д18 - один из основных заклепочных сплавов
Дуралюмины не обладают необходимой коррозионной стойкостью, поэтому их плакируют чистым алюминием.
Дуралюмины удовлетворительно обрабатываются резанием в закаленном и состаренном состоянии, хуже - в отожженном состоянии
Свариваются точечной сваркой и не свариваются сваркой плавлением, вследствие склонности к образованию трещин.
Сплавы авиали (АВ)
Они уступают дуралюминам в прочности, но более пластичны как в горячем, так и в холодном состоянии. Из них изготавливают листы, трубы, используемые для элементов конструкций, несущих умеренные нагрузкикованные детали двигателей, рамы, двери. Их используют для легких конструкций, требующих гибки и других деформаций при монтаже.
|
Химический состав их следующий - Си - 0,1-0,5% Мg =0,5-0,9% |
|
Мп- 0,15-0,35% Si - 0,5-1,2% |
σ= 260Мпа δ =15%
Авиали закаливают с 515 -525оС с охлаждением в воде и подвергают естественному старению.
Алюминиевые сплавы для ковки и штамповки (АК)
150
vk.com/club152685050 | vk.com/id446425943
|
АК6 |
- 1.8-2.6 % Си |
0,4-0,8 % Мg |
0,4-0,8 Мп ) |
0,7-1,2 % Si |
|
АК8 |
- 3,9-4,8 % Си |
0,4-0,8 % Мg |
0,4-0,8 Мп ) |
0,7-1,2 % Si |
По составу они близки к дуралюминам, но содержат больший процент кремния.
Данные сплавы отличаются высокой пластичностью, удовлетворительными литейными свойствами, позволяющими получить качественные слитки.
АК6 - это детали сложной формы и средней прочности - подмоторные рамы, фитинги, крепежные детали
АК8 - тяжелонагруженные штампованные деталиподмоторные рамы, стыковые узлы, лопасти винтов вертолетов
Ковку и штамповку проводят при температуре 450-470о
Закаливают при 520о с охлаждением в воде и проводят старение.
Алюминий и его сплавы
Высокопрочные алюминиевые сплавы (В) |
|
σ=600-700 Мпа и близким к нему пределом текучести. |
δ=8% ниже, чем у |
дуралюминов. |
|
Си=1,4-2% Мg=1,8-2,8% Мп=0,2-0,6% Zn=5-7% 0,1%Cr
Применяется для высоконагруженных конструкций, работающих в условиях напряжения сжатия - обшивки и лонжероны самолетов
В95, В96
Они еще менее коррозионно-устойчивые, чем дуралюмины. Их закаливают от 460-470о в воде и искусственно состаривают.
ЛИТЕЙНЫЕ АЛЮМИНИЕВЫЕ СПЛАВЫ
Они содержат почти те же легирующие компоненты, что и деформированные алюминиевые сплавы. но в значительно большем количестве ( до 9-11% по отдельным компонентам).
Они предназначены для изготовления фасонных отливок. Литье алюминиевых сплавов производят в земляные формы или в кокиль, литьем под давлением. Разливку ведут при температуре 6800760о
Маркируют их буквами АЛ и цифра - условный номер сплава.
Выпускают 35 марок литейных алюминиевых сплавов в зависимости от химического состава. например, алюминий-кремний, алюминий-магний
151

vk.com/club152685050 | vk.com/id446425943
Сплавы на основе алюминия и кремния называются - силумины
АЛ2- 10-13% кремния |
σ =130Мпа |
δ=2% |
50НВ - |
малонагруженные детали (корпуса приборов. кронштейны) |
|||
АЛ4 -8-10% кремния 0,3% магния 0,3% Мп |
σ =200Мпа δ =4% 75НВ - |
||
корпуса компрессоров. картеры, блоки |
|
|
|
АЛ9 - 6-8% кремния,0,2-0,4 Мп σ =220Мпа δ =2% |
50НВ - головки |
||
цилиндров, поршни |
|
|
|
|
|
|
|
Для улучшения механических свойств, силумины, содержащие более 50 кремния модифицируют натрием. при этом измельчается структура силуминов и сплав становится более пластичным.
Силумины тщательно контролируют с целью обнаружения различных дефектов - газовые раковины, поры, трещины, рыхлоты.
АЛ17 - цинковый силумин. содержит кроме кремния еще и цинк
Титан и его сплавы
"Металлом века" заслуженно называют сегодня титан, этот металл, обнаруженный в 1790 году, долгие годы оставался загадкой, промышленное производство которого начато после ВОВ, титан известен сегодня каждому.
Титан иногда называют |
еще "вечным" металлом и поэтому глубоко |
символичным является то, |
что именно из титана изготовлен в Москве |
монумент в честь покорителей космоса. Что же представляет собой этот металл?
152

vk.com/club152685050 | vk.com/id446425943
Титан-металл серебристо белого цвета. плотность его 4.5г/смз
Он вдвое легче, но и вдвое прочнее железа, в 6 раз прочнее алюминия
В земной коре его много -0,63%.
Лишь три технически важных металла – алюминий, железо и магний распространены больше, чем титан. количество титана в земной коре в несколько раз превышает запасы ( меди, цинка, свинца, серебра, золота, платины, хрома, вольфрама, молибдена, никеля , олова, сурьмы) вместе взятых.
Коррозионную прочность титана можно сравнить только с серебром и
золотом. На пластинке из титана за 10 лет пребывания в морской воде не появилось и следов коррозии. На его поверхности легко образуется окисная пленка - поэтому высокая коррозионная стойкость.
Ему нипочем океанские глубины, межпланетный вакуум, сверхнизкие температуры космического пространства, жар аэродинамического нагрева.
Титан можно обрабатывать давлением и резанием, сваривать в среде аргона. изготавливать детали литьем, обработка резанием его затруднена.
Титан имеет очень высокую удельную прочность.
Широкое применение титана сдерживается его высокой стоимостью, которая обусловлена сложностью извлечения его из руд.
В отличие от многих металлов титан
обладает значительным электросопротивлением. если электропроводность серебра принять за 100%. меди 94%, алюминия 60%, железо 15%, титана -3,8%. Это свойство очень важно для радиоэлектроники и электротехники.
Поставляется титан в виде листов, труб, прутков, поковок, штамповок.
153
vk.com/club152685050 | vk.com/id446425943
Технический титан изготавливается 3-х марок:
ВТ1-00 ( 99,53% Т )
ВТ1-0 ( 99,48% Т )
ВТ1-1 ( 99,44% Т )
Вредными примесями для титана являются : азот, углерод, кислород и водород, они снижают пластичность и свариваемость, повышают твердость, ухудшают сопротивление коррозии.
Технический титан имеет: |
σ = 300-500 МПА |
|
δ = 20-30% |
Чем больше примесей, тем больше прочность и меньше пластичность титана.
Сплавы на основе титана
Для получения сплавов титан легируют алюминием, молибденом, ванадием, марганцем, хромом, железом, ниобием и др.
Удельная прочность титановых сплавов выше, чем у легированных сталей.
Легирующие элементы оказывают большое влияние на температуры полиморфного превращения титана.
|
Так, алюминий, кислород, азот - повышают температуру и расширяют - |
|
область. их называют -стабилизаторами. |
|
Молибден, ванадий, марганец, хром, железо - понижают температуру |
|
полиморфного превращения. их называют стабилизаторами. |
Все промышленные сплавы титана содержат алюминий.
Титан и его сплавыВ соответствии со структурой различают следующие сплавы титана:
1. |
α-сплавы . |
Структура их α - твердые растворы л.э. в титане. основной |
|||||
легирующий элемент - алюминий. |
|
|
|
||||
ВТ5 - 5% алюминия |
σв = 750-900 Мпа |
δ =10% |
|
||||
2. α + β -сплавы. Структура их - α |
и β твердые растворы. кроме алюминия. |
||||||
они содержат 2-4% |
|
стабилизаторов |
|
|
|||
ВТ6 ( 6% алюминия, 4% ванадия) |
|
σв =900-1070Мпа |
δ =6-9% |
||||
3. |
β -сплавы |
структура их β |
- твердый раствор. Содержат большое |
||||
количество |
стабилизаторов. |
|
|
|
|||
ВТ32 ( 2% алюминия, 8% молибдена, 8% ванадия ,1% хрома, 1% железа ) |
|||||||
σв |
= 800-900 Мпа |
|
δ =6-15% |
|
|
|
Термическая обработка титановых сплавов
Титановые сплавы в зависимости от состава и назначения можно подвергать:
154
vk.com/club152685050 | vk.com/id446425943
-отжигу
-закалке и старению
-химико-термической обработке
Титан и альфа сплавы титана не подвергаются упрочняющей термообработке, их подвергают рекристаллизационному отжигу от температуры 650 -850°, это обеспечивает повышение пластичности.
альфа +бетта сплавы титана могут быть упрочнены закалкой с последующим старением. при быстром охлаждении протекает сдвиговое мартенситное превращение. мартенсит здесьпересыщенный твердый раствор легирующего элемента в альфа-титане. Температура закалки 750950 °
Для увеличения износостойкости сплавы титана азотируют.
Применение титановых сплавов
Титановые сплавы как высокопрочные конструкционные материалы широко применяют с следующих областях:
Авиации и ракетостроении - это корпуса двигателей, обшивки самолетов, баллоны для газов, сопла, диски и лопатки турбин, детали крепежа фюзеляжа. В самолете ТУ 154 несколько тысяч важнейших деталей сделано из сплавов титана
Морское и речное судостроение - гребные винты, обшивки подводных лодок. судов, торпед
Химической промышленности - оборудование для таких сред как хлор, кислоты, вентили для агрессивных жидкостей и т.п.
Криогенной технике
Сплавы титана обладают эффектом памяти - нитинол - сплавы титана с никелем. Изделие можно изогнуть. скрутить, а потом выпрямить. При нагреве оно воспроизведет свою форму.
Несмотря на то, что сплавы дороги, применение их в промышленности экономически выгодно, так. корпус химического реактора из нержавеющей стали служит 6 месяцев, а из сплавов титана - 10 лет
змеевик медный оцинкованный служит 10 месяцев, а титановый - 10 лет
Применяют и биметаллы стальтитан
155
vk.com/club152685050 | vk.com/id446425943
Магний и его сплавы
Магний также, как и алюминий и титан относится к материалам с малой плотностью.
Магний - металл серебристо-белого цвета, (под действием окисления поверхность магния тускнеет и становится матовой) не имеет полиморфных превращений и кристаллизуется в плотноупакованную гексагональную решетку.
Плотность магния - 1,7 г/смз
Магний в 1,5 раза легче алюминия, в 4,5 раза - железа, в 5 раз легче.
Температура плавления магния - 651 °С
Магний обладает способностью легко воспламеняться. Вспыхивая, магний ярким светом, выделяя большое количество тепла. Поэтому
магний находит широкое применение в пиротехнике, в военном деле при производстве сигнальных ракет, зажигательных бомб.
Магний нельзя гасить водой, т.к. будет взрыв.
Легкая воспламеняемость магния способствовала тому, что многие считают, что изделия из магния опасны в пожарном отношении. Это не так.
Магниевая пыль, стружка, порошок - они действительно опасны, а изделия, слитки - не опасны. чем больше масса, тем тепло быстрее растекается по всей массе материала. Магний имеет очень хорошую теплопроводность.
Магний плохо сопротивляется коррозии - деталь толщиной 3 см будет полностью "съедена" морем за 3 месяца. Поэтому магний и его сплавы нужно защищать от коррозии.
Магний и его сплавы |
|
|
|
|
Литой магний имеет |
σв |
=120Мпа |
δ =5% |
30НВ |
Деформированный |
σв |
= 250 Мпа |
δ=10% |
50НВ |
(прутки) |
|
|
|
|
Технический магний выпускается 3-х марок:
МГ90 ( 99,9% магния)
МГ95 (99,95 %)
МГ96 (99,96%)
156
vk.com/club152685050 | vk.com/id446425943
Магний может быть использован в химической промышленности, в металлургии как раскислитель, легирующий элемент и т.п.
Как конструкционный материал чистый магний не применяется, а для этой цели используются сплавы магния
Сплавы магния
Достоинством магниевых сплавов является их высокая удельная прочность. = 250-400 Мпа. По степени прочности на единицу своего веса они превосходят легированные стали и композиции на основе алюминия, уступая в этом лишь титановым сплавам
Поэтому сплавы магния употребляются для изготовления наиболее металлоемких деталей двигателя, корпуса компрессоров, коробок скоростей, корпуса приборов. В самолетах типа Ту154 насчитывается более 2-х тонн деталей из магниевых сплавов.
Магниевые сплавы очень хорошо поглощают вибрацию
Их удельная вибрационная прочность почти в 100 раз выше, чем у лучших алюминиевых сплавов, в 20 раз лучше, чем у алюминиевых сплавов
Магниевые сплавы хорошо обрабатываются резанием
Они обладают высокой хладностойкостью. От внезапного похолодания внезапно разрушаются многие конструкциимосты. магистральные трубопроводы. суда. при морозе сталь делается хрупкой, хладноломкой.
Основным легирующим элементом в магниевых сплавах является алюминий ( до 10%) затем цинк (5-6%), марганец (до 2,5%)
Магний и его сплавы По технологическому признаку сплавы магния можно разделить на 2 группы:
-литейные -МЛ
-деформированные -МД
Литейные магниевые сплавы - МЛ5,МЛ6,МЛ10 , в их составе магний, алюминий, цинк.
Высокие литейные свойства, применяют для нагруженных крупногабаритных изделий, корпуса, конструкции в автомобилях - особенно гоночных. приборостроении.
Деформируемые магниевые сплавы МА1, МА2 -изготавливаются в виде горячекатанных листов, прутков, профилей, поковок, штамповок.
Сплавы, имеющие гексагональную решетку низкопластичны, поэтому ОМД ведут при повышенных температурах.
157

vk.com/club152685050 | vk.com/id446425943
Химический состав их близок к литейным. МА1 имеет σв =210Мпа
Лекция 16
«НЕМЕТАЛЛИЧЕСКИЕ МАТЕРИАЛЫ»
Древние философы разделили весь мир на три царства: минеральное, растительное и животное. Но человек создал еще и четвертое - царство искусственных материалов и, пожалуй, самым удивительным изобретением человека стали пластмассы.
Представьте, что из окружающего нас мира исчезли бы пластмассы.
Тогда не стало бы не только привычных вещей в нашем доме, но и космических полетов, сверхзвуковых самолетов, глубоководных батискафов, современных телевизоров, всякого рода бытовых мелочей - полиэтиленовых мешочков, крышей - всего не перечислишь. Просто говоря, без пластмасс техника и наш быт вернулись бы в начало двадцатого века.
О значении пластмасс в развитии материального производства красноречиво говорит тот факт, что уже в 60-е годы мировой объем производства пластмасс значительно превысил выпуск цветных металлов.
Сейчас пластмассы не просто с успехом заменяют многие металлы, но и сами стали незаменимыми материалами во многих самых различных отраслях техники, пищевой промышленности, строительстве. сельском хозяйстве и т.п.
Обладая целым рядом ценных свойств. пластмассы играют важную роль в деле снижения веса машин и улучшения их качественных показателей.
158
vk.com/club152685050 | vk.com/id446425943
Применение пластмасс как конструкционных материалов экономически целесообразно. По сравнению с металлами переработка пластмасс менее трудоемкая, число операций в несколько раз меньше, а отходов получается немного. пластмассовые детали как правило не нуждаются в отделочных операциях.
Итак, перечислим основные достоинства пластмасс:
малая плотность (в большинстве 1 - 1,5 г/смз у пенопластов - 0,015)
высокая устойчивость к атмосферным воздействиям и агрессивным средам - высокая коррозионная стойкость
хорошие диэлектрические и электро и теплоизоляционные свойства, свето и - радиопрозрачность
высокая морозостойкость
в большинстве низкий коэффициент трения
декоративность
простота изготовления сложных и сложноармированных изделий ( обычно литьем под давлением или прессованием с минимальной последующей обработкой.
Преимущества пластмасс обеспечили им применение в машиностроении и это не смотря на некоторые их недостатки:
низкая теплостойкость (порядка 100°С)
малая жесткость
низкая механическая прочность, хрупкость
склонность к старению
небольшая по сравнению с металлами вязкость
ПЛАСТМАССАМИ - называются искусственно изготавливаемые материалы, состоящие в основном или полностью из высокомолекулярных соединений (полимеров) и обладающие при определенных условиях (температура, давление) пластичностью, что дает возможность формировать из них изделия.
В состав пластмасс входят:
159
vk.com/club152685050 | vk.com/id446425943
Связующие вещества (полимеры)
наполнители
пластификаторы
красители
специальные добавки
Рассмотрим основные составляющие пластмасс.
Итак, пластмассы изготавливаются на основе полимеров - это основная составляющая пластмасс (иногда составляет 100%)
Полимерами называются вещества с большой молекулярной массой, у которых молекулы состоят из одинаковых групп атомов-звеньев.
Каждое звено представляет собой измененную молекулу исходного низкомолекулярного вещества - мономера
При получении полимера молекулы мономеров объединяются друг с другом и образуют длинные линейные молекулы или макромолекулы, в которых атомы соединены ковалентными связями.
Полимеры встречаются в природе - это натуральный каучук, целлюлоза, слюда, асбест, графит. Однако ведущей группой являются синтетические полимеры, получаемые в процессе химического синтеза из низкомолекулярных соединений Своеобразие свойств полимеров обусловлено структурой их макромолекул. По форме макромолекул полимеры делятся:
Линейные макромолекулы полимера представляют собой длинные зигзагообразные цепочки, они обеспечивают эластичность материала, они являются наиболее подходящими для получения волокон и пленок.
Разветвленные макромолекулы полимера, отличаются наличием боковых ответвлений
Все полимеры по отношению к нагреву подразделяются на две группы:
термопластичные
термореактивные
160
vk.com/club152685050 | vk.com/id446425943
Термопластичные полимеры при нагревании размягчаются. даже плавятся, при охлаждении - затвердевают: этот процесс обратим., т.е. никаких дальнейших химических превращений материал не претерпевает.
Термореактивные полимеры на первой стадии при нагревании размягчаются, затем вследствие протекания химических реакций затвердевают и в дальнейшем остаются твердыми. примером их могут служить эпоксидные и др. смолы.
Основные составляющие пластмасс
Основным компонентом пластмасс является связующее вещество или полимер, о нем мы уже говорили. простые пластмассы - это полимеры без добавок, сложные - это смеси полимеров с различными добавками - наполнителями, пластификаторами, стабилизаторами и др.
Наполнители - добавляют в количестве 40-70% по массе для повышения механических пластмасс. снижения стоимости и др.
Это органические и неорганические вещества в виде порошков (древесная мука, сажа, слюда, тальк, графит), волокон - (хлопчатобумажных, стеклянных, асбестовых), листов ( бумага, ткани, древесный шпон). наполнителями могут служить различные газы.
Наполнители усиливают механическую прочность, так введение в
термопласты коротких стекловолокон в количестве 20-30% по массе позволяет значительно повысить прочностные свойства материалов, их жесткость. Стеклопластики по твердости почти не уступают стали, но примерно в 4 раза легче ее. О прочности их говорит тот факт, что из них делают пуленепроницаемые защитные жилеты.
Особое значение наполнители играют в снижении горючести пластмасс. Общеизвестно пожароопасность пластмасс, поэтому без специальных наполнителей, повышающих теплостойкость пластмасс никак не обойтись. К ним относятся: асбест, гидроокись алюминия и др.
С помощью наполнителей можно регулировать плотность пластмасс - это делается с помощью газонаполнения.
Стабилизаторы - различные органические вещества,, которые вводят для сохранения структуры молекул и стабилизации свойств. добавки стабилизаторов замедляют старение пластмассы.
161

vk.com/club152685050 | vk.com/id446425943
Пластификаторы - вещества. вводимые для придания пластичности пластмассам, их добавляют в количестве 10-20% для уменьшения хрупкости и улучшения формуемости. пластификаторами являются вещества, которые уменьшают межмолекулярное взаимодействие и хорошо совмещаются с полимерами. В качестве пластификаторов могут быть эфир, олеиновая кислота, стеарин и др.
Специальные добавки - смазочные материалы, красители, добавки для уменьшения статических зарядов, защиты от плесени и др.
СВОЙСТВА ТЕРМОПЛАСТИЧНЫХ ПЛАСТМАСС
|
Материал |
|
Прочнос |
|
Пластичность |
|
Максимальная |
|
|
|
|
|
|
||||
|
|
|
ть |
|
% |
|
температура |
|
|
|
|
МПа |
|
|
|
эксплуатации |
|
|
|
|
|
|
|
|
оС |
|
|
Полиэтилен |
|
|
|
|
|
|
|
|
низкой плотности |
|
10-18 |
|
300-1000 |
|
60-75 |
|
|
0,94 |
|
|
|
|
|
|
|
|
высокой |
|
18-52 |
|
100-600 |
|
70-80 |
|
|
плотности 0,94 |
|
|
|
|
|
|
|
|
Полипропилен |
|
26-38 |
|
700-800 |
|
100 |
|
|
|
|
|
|
|
|
|
|
|
Полистирол |
|
40-60 |
|
3-4 |
|
50-70 |
|
|
|
|
|
|
|
|
|
|
|
жесткий |
|
50-65 |
|
20-50 |
|
65-85 |
|
|
|
|
|
|
|
|
|
|
|
пластикат |
|
10-40 |
|
50-350 |
|
50-55 |
|
|
|
|
|
|
|
|
|
|
|
Фторопласт-4 |
|
20-40 |
|
250-500 |
|
250 |
|
|
|
|
|
|
|
|
|
|
|
Фторопласт -3 |
|
37 |
|
160-190 |
|
150 |
|
|
|
|
|
|
|
|
|
|
|
Органическое |
|
80 |
|
5-6 |
|
65-90 |
|
|
стекло |
|
|
|
|
|
|
|
|
без наполнителя |
|
60-65 |
|
80-120 |
|
135 |
|
|
|
|
|
|
|
|
|
|
|
с 30%волокон |
|
90 |
|
3.5 |
|
145 |
|
|
|
|
|
|
|
|
|
|
|
Капрон |
|
|
|
|
|
|
|
|
|
|
|
|
|
|
|
|
|
сухой |
|
70-85 |
|
50-130 |
|
80-100 |
|
|
|
|
|
|
|
|
|
|
|
насыщенный |
|
100-125 |
|
4 |
|
80-100 |
|
|
водой |
|
|
|
|
|
|
|
СВОЙСТВА ТЕРМОРЕАКТИВНЫХ ПЛАСТМАСС
|
Материал |
|
Прочность |
|
Пластичность |
|
Максимальная температура |
|
|
|
|
|
|
||||
|
|
|
МПа |
|
% |
|
эксплуатации оС |
|
|
|
|
|
|
|
162 |
|

vk.com/club152685050 | vk.com/id446425943
фенолоформальдегидные |
15-35 |
1-5 |
200 |
|
|
|
|
полиэфирные |
42-70 |
2 |
95-120 |
|
|
|
|
эпоксидные |
28-70 |
3-6 |
150-175 |
|
|
|
|
кремнийорганические |
22-42 |
5-10 |
350 |
|
|
|
|
Порошковые |
30-60 |
1-3 |
100-200 |
пластмассы |
|
|
|
Волокниты |
30-90 |
1-3 |
120-140 |
|
|
|
|
Гетинаксы |
60-70 |
- |
125 |
|
|
|
|
Текстолиты |
65-100 |
1-3 |
90-105 |
|
|
|
|
Стеклотекстолиты |
200-600 |
1-3 |
200-400 |
|
|
|
|
Пористые пластмассы |
0,5-2,5 |
- |
- |
|
|
|
|
МЕХАНИЧЕСКИЕ СВОЙСТВА ТЕРМОПЛАСТИЧНЫХ ПЛАСТМАСС
Термопластичные пластмассы в отличие от реактивных нашли более широкое применение и производятся в больших количествах. Значительная часть термопластов перерабатывается в пленку, волокна, и изделия из волокна, которые трудно или вовсе невозможно изготовить из термореактивных полимеров.
Ктермопластам относят:
-полиэтилен, может быть высокого и низкого давления, нерастворим ни в одном из известных растворителей. Применяется для изготовления труб, литых и прессованных несиловых деталей (вентили, контейнеры), полиэтиленовых пленок для изоляции проводов и кабелей, чехлов, остекления теплиц, он может служить покрытием на металлах для защиты от коррозии, влаги и т.д.
Недостатком является подверженность его старению
полистирол - по диэлектрическим характеристикам близок к полиэтилену, удобен для механической обработки, легко окрашивается Из него изготавливают детали для радиотехники, телевидения , приборов, корпуса, ручки, сосуды для воды и химикатов
163
vk.com/club152685050 | vk.com/id446425943
поливинилхлорид - разновидность его - винипласт- имеет высокую механическую прочность и упругость. Из него изготавливают трубы для подачи агрессивных газов, жидкостей и воды, защитные покрытия для электропроводки, детали для вентиляционных установок, теплообменников. защитные покрытия для металлических емкостей. строительные облицовочные плитки.
фторопласт-4- обладает очень низким коэффициентом трения, который
Не зависит от температуры. Его трудно перерабатывать из-за отсутствия пластичности. Из него изготавливают трубы для химикатов, вентили, краны, насосы, уплотнительные прокладки, антифрикционные покрытия на металлах.
Волокно и пленки из него не горят, химически стойки, применяются для емкостей, рукавов, спецодежды.
полиамиды - это группа пластмасс с широко известными названиями - капрон, нейлон, анид, и др. Они стойки к щелочам, бензину, имеют низкий коэффициент трения, продолжительное время могут работать на истирание, способны поглощать вибрацию. К недостаткам можно отнести - гигроскопичность и подверженность старению из-за окисляемости.
Из полиамидов изготавливают шестерни, втулки, подшипники, болты, гайки, шкивы, детали ткацких станков, буксирные канаты. Их используют в электротехнике. медицине. применяют их и как антифрикционные покрытия металлов.
поликарбонат - выпускается под названием дифлон- по прочности на разрыв близок к винипласту, отличается высокой ударной вязкостью.
Из него изготавливают шестерни, подшипники, автодетали. радиодетали, его используют в криогенной технике для работы в среде сжиженных газов. Дифлон применяют и в виде гибких прочных пленок.
органическое стекло - прозрачный аморфный термопласт, называется иногда -полиметилметакрилат. Материал в два раза легче минеральных стекол, пропускает 75% ультрафиолетовых лучей ( минеральные - 0,5%). при 80оС оргстекло начинает размягчаться, при 105-150оС появляется пластичность, что позволяет формировать из него различные изделия. Критерием, определяющим пригодность органического стекла для эксплуатации, является не только их прочность, но и появления на поверхности и внутри материала мелких трещин - т.н. "серебра". Этот дефект снижает прозрачность и прочность стекла. Причиной появления
164
vk.com/club152685050 | vk.com/id446425943
"серебра" являются внутренние напряжения, возникающие в связи с низкой теплопроводностью и высоким температурным коэффициентом линейного расширения материала.
Оргстекло стойко к действию разбавленных кислот. щелочей, растворяется в эфирах. К недостатком - относят невысокую его поверхностную твердость.
Максимальная рабочая температура при неполном прогреве стекла - 100о
оргстекло используется в самолетостроении и автомобилестроении. светотехнические детали, оптические линзы, защитные щитки на металлорежущих станках.
МЕХАНИЧЕСКИЕ СВОЙСТВА ТЕРМОРЕАКТИВНЫХ ПЛАСТМАСС
Термореактивные пластмассы (реактопласты) получают на основе эпоксидных, полиэфирных, полиуретановых, фенолоформальдегидных и кремнийорганических полимеров.
Пластмассы применяют в отвержденном виде. Они имеют сетчатую структуру и поэтому при нагреве не плавятся, устойчивы против старения и не взаимодействуют с топливом и смазочными материалами.
Реактопласты нерастворимы, способны лишь набухать в отдельных растворителях, водостойки и поглощают не более 0,1-0,5% воды. Эти пластмассы пригодны для изделий больших размеров.
Реактопласты после отверждения имеют низкую ударную вязкость и поэтому используются с наполнителями.
Преимущества наполненных термореактивных пластмасс:
большая стабильность механических свойств
относительно малая зависимость их от температуры, скорости деформирования, и длительности действия нагрузки.
большая, чем у термопластов надежность
лучшая несущая способность в рабочем интервале температур
Волокниты - это пластмассы, у которых наполнителем служат волокна, имеют повышенную прочность, а гласное ударную вязкость.
Волокниты, наполненные асбестовым волокном, сочетают теплостойкость до 200° с высоким коэффициентом трения в паре со сталью и поэтому применяются в тормозных устройствах.
165
vk.com/club152685050 | vk.com/id446425943
Изделия из волокнитов прессуют при повышенных давлениях. из-за низкой текучести материала применение волокнитов ограничено изделиями простой формы.
Слоистые пластики - представляют группу самых прочных и универсальных по применению конструкционных пластмасс. Листовые наполнители, уложенные слоями, придают материалам анизотропность.
По виду наполнителя слоистые пластики подразделяются на следующие виды:
текстолиты - материалы с х/б тканями
гетинаксы - с бумажным наполнителем
древесно-слоистые пластики - с древесным шпоном
стеклотекстолиты - с тканями из стеклянного волокна
Наименее прочными являются гетинаксы, максимальную прочность имеют стеклотекстолиты.
Из всех слоистых пластиков текстолиты отличаются самым прочным сцеплением между полимером и наполнителем и лучше поглощают вибрацию.
Обычно слоистый пластик имеет около 50% полимера , при меньшем его содержании материал более экономичный. но менее прочен и неводостоек.
Гетинаксы-в зависимости от свойств составляющих применяются как электроизоляционные или строительно-декоротивные материалы, применяемые для облицовки производственных помещений, салонов самолетов, ж/д вагонов.
Текстолиты- используют для разнообразных средненагруженных трущихся деталей, включая зубчатые колеса и кулачки. он хорошо сопротивляется износу, не схватывается со стальными деталями.
Стеклотекстолиты - сочетают малую плотность (1,6-1,9) с высокой прочностью и жесткостью. Наивысшую прочность обеспечивает эпоксидная связка, минимальную - кремнийорганические полимеры.
Стеклотекстолиты по способности поглощать вибрации превосходят стали, сплавы титана и алюминия, поэтому они имеют хорошую выносливость при переменных нагрузках. По тепловому расширению они близки к сталям.
Слоистые пластики со стеклянным или полимерным волокном в течение десятков секунд выдерживают температуру свыше 3000о. В поверхностных слоях разрушается полимер, оплавляется наполнитель и образуется тугоплавкий кокс, который защищает более глубокие слои материала. эта особенность лежит в основе применения пластмасс в качестве теплозащитных материалов.
166
vk.com/club152685050 | vk.com/id446425943
Термореактивные полимеры используют в виде клеев, а также при изготовлении оболочковых форм для отливок, различной технологической оснастки, абразивного инструмента.
Максимальную прочность обеспечивают фенолоформальдегидные клеи, теплостойкость - клеи на основе кремнийорганических полимеров. Склеивание производят там, где клеевая пленка работает на срез - при приклеивании тормозных обкладок, фиксации болтов и шпилек, закреплении вкладышей подшипников.
Газонаполненные пластмассы
Это легкие и сверхлегкие материалы, которые получают вспениваем эмульсии и раствора мономера (полимера) воздухом или газом. Либо вспениваем газообразными продуктами, образующимися в процессе отверждения полимера. Либо вспениванием размягченного полимера газом под давлением 10-25 Мпа при 140-160о
Структура их представляет твердый полимер, которое образует стенки элементарных ячеек или пор с распределеннной в них газовой фазой - наполнителем.
Такая структура обеспечивает чрезвычайно малую массу и высокие теплоизоляционные характеристики.
Различают:
-пенопласты
-поропласты
Упенопластовмикроскопические ячейки заполненные газом. не сообщаются между собой (плотность до 0,3мг/мз)
Упоропластов - ячейки сообщаются между собой (плотность более 0,3мг/мз) Газонаполненные пластмассы получили широкое распространение и широко применяются для теплоизоляции кабин, контейнеров. холодильников. в строительстве, являясь легким заполнителем, повышают прочность силовых конструкций. Мягкие пластичные поролоны используют для амортизаторов, губок.
167
vk.com/club152685050 | vk.com/id446425943
168
vk.com/club152685050 | vk.com/id446425943
Министерство образования и науки РФ
ФГБОУ ВПО «Кубанский государственный технологический университет»
Кафедра материаловедения и автосервиса
В.Н.Киприянова, С.А.Кобзева
ТЕРМИЧЕСКАЯ ОБРАБОТКА УГЛЕРОДИСТЫХ СТАЛЕЙ
МЕТОДИЧЕСКОЕ УКАЗАНИЕ К ЛАБОРАТОРНЫМ РАБОТАМ По дисциплине «Материаловедение»
для студентов всех форм обучения, направлений бакалавриата:
131000, 140100, 140400, 141200, 151000, 190700, 220700, 221700,240100
Краснодар
2012
vk.com/club152685050 | vk.com/id446425943
Составители: канд. техн. наук, доц. В.Н. Киприянова канд. техн. наук, доц. С.А. Кобзева
Под редакцией д-ра техн. наук, профессора В.П. Артемьева
УДК 620.22
Методическое указание к лабораторным работам по дисциплине «Материаловедение» для студентов всех форм обучения, направлений бакалавриата:
131000,140100,140400,141200,151000.190700,220700,221700, 240100
/ Сост.: В.Н. Киприянова, С.А. Кобзева; Кубанский гос. технол. ун-т. Каф. материаловедения и автосервиса. – Краснодар: Изд. КубГТУ, 2012 – с.24
Изложены теоретические основы и методика проведения 3 лабораторных работ, выполняемых студентами при изучении курса «Материаловедение, раздела «Термическая обработка углеродистых сталей»
Рецензенты: д-р техн. наук, профессор А.Г. Соколов Канд.техн.наук, профессор В.Г.Корниенко
2
vk.com/club152685050 | vk.com/id446425943
СОДЕРЖАНИЕ ПРЕДИСЛОВИЕ…………………………………………………………….....4
Лабораторная работа 5 ВЛИЯНИЕ ЗАКАЛКИ НА СТРУКТУРУ И СВОЙСТВА
СТАЛИ………………………………………………………………………….5
Лабораторная работа 6 ВЛИЯНИЕ ОТПУСКА НА СТРУКТУРУ И СВОЙСТВА
ЗАКАЛЕННОЙ СТАЛИ………………………………………………………12
Лабораторная работа 7 ОПРЕДЕЛЕНИЕ ТВЕРДОСТИ МЕТАЛЛОВ……………………………….16
СПИСОК ЛИТЕРАТУРЫ…………………………………………………….23
3
vk.com/club152685050 | vk.com/id446425943
ПРЕДИСЛОВИЕ
Цель предлагаемого методического указания – оказать помощь в подготовке к лабораторным занятиям по курсу "Материаловедение", развить у студентовбакалавров навык самостоятельной работы, в том числе исследовательской.
Прежде чем приступить к выполнению работы, нужно заранее ознакомиться с ее содержанием, т.е. с элементами теории, заданием и методикой проведения. Таким образом, изучив лекционный материал и данные руководства, студент обязан добросовестно подготовиться к проведению лабораторной работы.
После выполнения работы бакалавр составляет отчет по форме, приведенной в журнале лабораторных работ, который выдают ему одновременно с этим руководством. Преподаватель принимает работу в конце занятия, опрашивает студента по отчету, практической части и теории, относящейся к выполняемой работе. Контрольные вопросы помещены в конце работы.
Во время работы в лаборатории студент обязан строго соблюдать правила техники безопасности.
1.ПЕРЕД ВЫПОЛНЕНИЕМ ЛАБОРАТОРНОГО ПРАКТИКУМА ВСЕ СТУДЕНТЫ ПРОХОДЯТ ИНСТРУКТАЖ НА РАБОЧЕМ МЕСТЕ (В ЛАБОРАТОРИИ).
2.Не разрешается трогать приборы, установки и органы их управления, предварительно не ознакомившись с устройством и правилами работы на них, а также включать и трогать оборудование, не относящееся к выполняемой работе.
3.При неисправности оборудования следует немедленно прекратить работу на нем и сообщить об этом лаборанту или преподавателю.
4.Все детали приборов необходимо перемещать плавно, без рывков и больших усилий.
5.При измерении твердости образец должен устойчиво стоять на столе или в призме. Место контакта с индентером надо выбирать в средней части поверхности образца, которая должна быть ровной, плоской, расположенной горизонтально
4
vk.com/club152685050 | vk.com/id446425943
Лабораторная работа №5
ВЛИЯНИЕ ЗАКАЛКИ НА СТРУКТУРУ И СВОЙСТВА УГЛЕРОДИСТОЙ СТАЛИ
Цель работы – изучить теорию и практику закалки углеродистой стали и влияние закалки на структуру и свойства.
Задание и порядок выполнения работы
1.Ознакомиться с теоретическими положениями, изложенными в работе, уяснить основные превращения, которые происходят в стали при быстром охлаждении.
2.Для углеродистой стали, указанной преподавателем марки, назначить режим закалки (температуру и продолжительность нагрева, скорость охлаждения).
3.Произвести закалку по выбранному режиму.
4.Определить твердость закаленной стали.
5.Изучить и зарисовать микроструктуру стали после закалки.
Приборы и материалы Муфельная печь, клещи, бак с охлаждающей жидкостью, прибор Роквелла,
образцы углеродистой стали.
Основы теории
Закалка состоит в нагреве стали до температуры выше критической точки AС1 или AС3, выдержке при этой температуре для завершения фазовых превращений и последующем быстром охлаждении со скоростью выше критической.
Для углеродистых сталей охлаждение чаще всего проводят в воде, а для легированных – в масле или других средах.
Цель закалки – получение высокой твердости, прочности, износостойкости. Закалка не является окончательной операцией термической обработкой. Чтобы
уменьшить хрупкость и напряжения, вызванные закалкой, сталь после закалки подвергают отпуску.
Одним из основных превращений в железоуглеродистых сплавах является превращение аустенита в перлит (при охлаждении):
Fеγ(С) → Feα(С) + Fe3C. Это превращение состоит из двух процессов:
1)перекристаллизации Fеγ→ Feα
2)диффузии углерода в объемах аустенита, заканчивающейся выделением углерода
ввиде зерен цементита.
Температура распада аустенита с образованием ферритно-цементитной смеси и
полнота этого процесса зависят от скорости охлаждения. Структуру стали после охлаждения ее с различными скоростями можно определить с помощью диаграммы изотермического превращения переохлажденного аустенита, или так называемой С- образной диаграммы (рис. 1). При весьма малой скорости охлаждения V1 распад аустенита происходит при температуре, близкой к равновесной (727°С). Образующаяся при этом структура представляет собой механическую смесь довольно крупных пластин феррита и цементита, называемую перлитом.
5

vk.com/club152685050 | vk.com/id446425943
Увеличение скорости охлаждения (V2) сопровождается понижением температуры начала распада аустенита, т.е. ведет к его переохлаждению. Образующаяся при распаде переохлажденного аустенита смесь феррита и цементита состоит из более мелких частиц, чем перлит. Такая структура получила название
сорбита закалки.
Рис. 1. Диаграмма изометрического распада аустенита стали У8 с наложенными на нее кривыми охлаждения.
Если скорость охлаждения увеличить (V3), то появится еще более тонкая структура распада аустенита – троостит закалки.
Таким образом, перлит, сорбит, троостит являются продуктами распада аустенита при его охлаждении с различными скоростями и представляют собой механические смеси феррита и цементита. Различие этих структур состоит только в степени дисперсности составляющих их фаз. Увеличение дисперсности механических смесей сопровождается увеличением их твердости. Примерные скорости охлаждения при получении указанных структур и значения их твердости приведены на рис. 1 и в таблице 1.
|
|
|
Таблица 1 |
|
скорость |
Примерная скорость |
Образующаяся |
Примерная твердость |
|
охлаждения, |
||||
охлаждения |
структура |
по Бринеллю, НВ |
||
град/с |
||||
|
|
|
||
V1 |
~0,5 /вместе с печью/ |
Перлит |
I50-200 |
|
|
|
|
|
|
V2 |
~50 /в струе воздуха/ |
Сорбит |
250-300 |
|
V3 |
~100 /в масле / |
Троостит |
300-400 |
|
V4 |
~300 /в воде/ |
Мартенсит |
до 650 |
|
|
|
|
|
6

vk.com/club152685050 | vk.com/id446425943
В основе распада аустенита на указанные механические смеси лежат диффузионные процессы, требующие для своего осуществления определенного времени. Можно настолько повысить скорость охлаждения, что диффузионные процессы станут невозможными, и тогда распад аустенита не успеет произойти. В этом случае из аустенита образуется новая структура, называемая мартенситом. При превращении аустенита в мартенсит происходит лишь бездиффузионная перестройка кристаллической решетки γ-железа в α-железо. Атомы углерода, растворенные в аустените, остаются в решетке α-железа и сильно ее искажают, так как известно, что растворимость углерода в γ-железе выше, чем в α-железе. Таким образом, мартенсит представляет собой пересыщенный раствор углерода в α- железе. Кристаллическая решетка мартенсита не кубическая, как у α-железа, а тетрагональная (рис. 2).
Рис. 2. Кристаллическая решетка мартенсита.
Чем больше углерода в стали, тем больше степень тетрагональности решетки мартенсита. Вследствие сильного искажения кристаллической решетки мартенсит имеет высокую твердость (600-650 НВ).
Минимальная скорость охлаждения, обеспечивающая образование из аустенита мартенситной структуры, называется критической скоростью закалки – Vкр. Размер этой скорости зависит от химического состава стали.
Для мартенсита характерна особая микроструктура (pис. 3).
Рис. 3. Микроструктура (фотография и схема) углеродистой стали после закалки,
400.
Кристаллы мартенсита представляют собой "пластины", расположенные параллельно или пересекающиеся под определенным углом. В плоскости шлифа они имеют вид игл ("игольчатый" мартенсит).
Для соблюдения режима закалки необходимо правильно определить: 1. температуру нагрева стали,
7
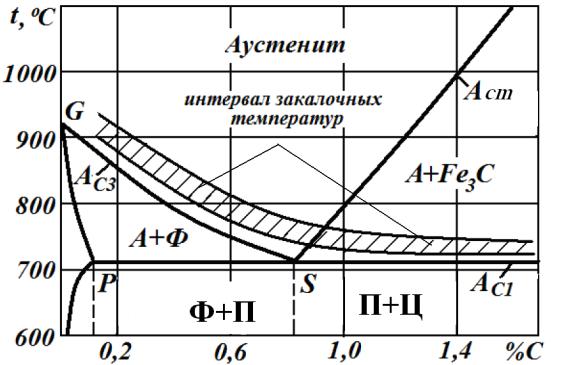
vk.com/club152685050 | vk.com/id446425943
2.время нагрева и выдержки в печи,
3.среду охлаждения.
ВЫБОР ТЕМПЕРАТУРЫ ЗАКАЛКИ По температуре нагрева закалка может быть:
полной,
неполной.
Нагрев стали на 30-50°С выше АC3 с последующей закалкой на мартенсит называется полной закалкой. Доэвтектоидные стали всегда подвергают полной закалке. Структура после полной закалки доэвтектоидных сталей – мартенсит.
Ели сталь под закалку нагревать до температур, лежащих, между линиями АC1 – АC3 или АC1 – Асm (рис. 4), то в результате получим структуру в виде смеси мартенсит + феррит в доэвтектодных сталях и мартенсит + цементит – в заэвтектоидных. Такая закалка называется неполной.
В доэвтектоидных сталях неполная закалка недопустима, так как феррит, сохранившийся в структуре, снижает твердость закаленной стали и ухудшает механические свойства после отпуска. В заэвтектоидных сталях оптимальная температура закалки, наоборот, лежит в интервале между Ас1 и Аcm. Наличие в закаленной заэвтектоидной стали избыточного цементита повышает твердость и износоустойчивость стали. Нагрев же выше Аcm опасен и не нужен, так как он не повышает твердости, наоборот, твердость даже несколько падает вследствие растворения избыточного цементита; при таком нагреве растет зерно аустенита, увеличивается возможность возникновения больших закалочных напряжений.
Рис. 3. Диаграмма состояния Fe-Fe3C с указанием температур закалки.
ВРЕМЯ НАГРЕВА Продолжительность нагрева стали при закалке должна быть достаточной для
прогрева изделия по сечению и завершения фазовых превращений, но не слишком большой, чтобы не вызвать роста зерна и обезуглероживания поверхностных слоев стали.
8
vk.com/club152685050 | vk.com/id446425943
Для ориентировочного определения продолжительности нагрева можно пользоваться данными, приведенными в таблице 2.
Таблица 2 Ориентировочная продолжительность нагрева изделий в различных печах для
закалки от 800-850°С
|
Продолжительность нагрева, с |
||
Нагрев |
на 1мм сечения или толщины изделия |
||
|
Круглое |
Квадратное |
Прямоугольное |
В электропечи |
40-50 |
50-60 |
60-75 |
В пламенной печи |
35-40 |
45-50 |
55-60 |
В соляной ванне |
12-15 |
15-18 |
18-22 |
В свинцовой ванне |
6-8 |
8-10 |
10-12 |
СРЕДА ОХЛАЖДЕНИЯ Охлаждение при закалке должно обеспечивать получение структуры
мартенсита в пределах заданного сечения изделия (определенную прокаливаемость) и отсутствие закалочных дефектов: трещин, коробления и т.д. Наиболее желательны высокая скорость охлаждения (выше критической скорости закалки) в интервале температур A3 – МH для подавления распада переохлажденного аустенита в области перлитного и промежуточного превращения и замедленное охлаждение в интервале температур мартенситного превращения MH – МK. Обычно для закалки используют воду, водные растворы солей и щелочей, масла. В таблице 3 приведена относительная интенсивность охлаждения в различных средах.
Таблица 3 Относительная интенсивность охлаждения закалочных сред
Охлаждающая среда |
Относительная интенсивность |
и её температура |
охлаждения |
|
|
Вода, 20°С |
1,0 |
|
|
Вода, 40° |
0,7 |
|
|
Вода, 80°С |
0,2 |
|
|
10%-й раствор NaCl в воде, 20°С |
3,0 |
|
|
10%-й раствор NaOH в воде, 20°С |
2,0 |
|
|
50%-й раствор NaOH в воде, 20°С |
2,0 |
|
|
Масло минеральное, 20-200°С |
0,3 |
|
|
Вода как охлаждающая среда имеет следующие недостатки:
высокая скорость охлаждения в области температур мартенситного превращения нередко приводит к образованию закалочных дефектов;
с повышением температуры воды резко снижается ее закалочная способность. Масло как охлаждающая среда имеет следующие недостатки:
повышенная воспламеняемость (температура вспышки 165 300 С);
низкая охлаждающая способность в интервале перлитного превращения;
необходимость замены после определенного срока (густеет);
повышенная стоимость.
Преимущества масла:
9
vk.com/club152685050 | vk.com/id446425943
небольшая Vохл в мартенситном интервале температур и как следствие, уменьшение закалочных дефектов;
постоянство закаливающей способности в широком интервале температур
(20 150 С).
Минеральное масло обычно применяют для легированных сталей.
Наиболее высокой к равномерной охлаждающей способностью отличаются водные растворы NaCl и NaOH, которые хорошо зарекомендовали себя на практике..
При выборе охлаждающей среды необходимо учитывать закаливаемость и прокаливаемость стали.
Закаливаемость – способность стали приобретать высокую твердость при закалке.
Закаливаемость определяется содержанием углерода (чем больше углерода, тем выше твердость). Стали с содержанием углерода менее 0,20 % не закаливаются.
Прокаливаемость – способность получать закаленный слой с мартенситной и троосто-мартенситной структурой, обладающей высокой твердостью, на определенную глубину.
Впроцессе закалки могут возникнуть дефекты:
–закалочные трещины (наружные или внутренние) образуются вследствие высоких внутренних напряжений – неисправимый брак!;
–деформация и коробление – в результате внутренних напряжений, вызванных неравномерным охлаждением и фазовыми превращениями;
–мягкие пятна – образуются в местах, где имелась окалина, загрязнения, участки с обезуглерожинной поверхностью;
–низкая твердость – в результате несоблюдения режимов закалки – подвергаются высокому отпуску и повторной закалке;
–перегрев – образование крупного зерна в стали и как следствие, падение пластичности, образование трещин. Подвергают повторному отжигу и термической обработке;
–пережог – нагрев еще до более высоких температур и длительной выдержке. Сопровождается окислением, частичным оплавлением, и как следствие, металл становится хрупким. Неисправимый брак!
КОНТРОЛЬНЫЕ ВОПРОСЫ
1.Что называется закалкой стали?
2.С какой целью проводят закалку стали?
3.Из каких основных процессов состоит превращение аустенита в перлит?
4.С какой целью строят диаграммы изотермического превращения аустенита (С- образные диаграммы)?
5.Назовите продукты распада аустенита при его охлаждении с различной скоростью.
6.Что представляют собой перлит, сорбит, троостит? Каковы их свойства?
7.Что такое мартенсит и в чем сущность и особенности мартенситного превращения?
8.Какова микроструктура мартенсита и его свойства?
9.Что называется критической скоростью закалки?
10
vk.com/club152685050 | vk.com/id446425943
10.Что называется полной закалкой и неполной?
11.До какой температуры следует нагревать под закалку доэвтектоидные стали, заэвтектоидные?
12.Как определить продолжительность нагрева стали при закалке, на какие факторы она оказывает влияние?
13.Какие требования предъявляются к охлаждающим средам при закалке? 14.Каковы недостатки воды как охлаждающей среды?
15.Какая охлаждающая среда имеет наибольшую интенсивность охлаждения?
16.Что такое прокаливаемость стали?
17.Что такое закаливаемость?
18.Перечислите дефекты, которые могут возникнуть при закалке.
11
vk.com/club152685050 | vk.com/id446425943
Лабораторная работа №6
ВЛИЯНИЕ ОТПУСКА НА СТРУКТУРУ И СВОЙСТВА ЗАКАЛЕННОЙ СТАЛИ
Цель работы – изучить теории и практику отпуска закаленной стали, его влияние на ее структуру и свойства.
Задание и порядок выполнения работы
1.Ознакомиться с теоретическими положениями, изложенными в работе, уяснить основные превращения, которые происходят в закаленной стали при отпуске.
2.Для данных образцов закаленной стали назначить режимы трех видов отпуска (низко-, средне- и высокотемпературного).
3.Произвести отпуск закаленной стали по выбранным режимам.
4.Определить твердость отпущенной стали по методу Роквелла и построить график изменения твердости отпущенной стали в зависимости от температуры отпуска.
Приборы и материалы Муфельная печь, клещи, бак с охлаждающей жидкостью, прибор Роквелла,
закаленные образцы стали.
Основы теории
Отпуск состоит в нагреве закаленной стали до температуры ниже АC1, выдержке при заданной температуре и последующим охлаждением с определенной скоростью.
Отпуск является окончательной операцией термической обработкой, в результате которой сталь получает требуемые механические свойства. Отпуск полностью или частично устраняет внутренние напряжения, возникающие при закалке. Эти напряжения снимаются тем полнее, чем выше температура отпуска. Так, осевые напряжения в цилиндрическом образце из стали, содержащей 0,3%С, в результате отпуска при 550 °С уменьшаются с 600 до 80 МПа.
Скорость охлаждения при отпуске оказывает большое влияние на величину остаточных напряжений. Чем медленнее охлаждение, тем меньше остаточные напряжения. Быстрое охлаждение в воде создает новые термические напряжения. Охлаждение на воздухе дает напряжения на поверхности изделия в семь раз меньшие, а в масле – в 2,5 раза меньше по сравнении с напряжениями при охлаждении в воде.
При отпуске неравновесная структура, состоящая из мартенсита и остаточного аустенита, переходит в более устойчивое состояние. Этот переход связан с диффузионным распадом твердых растворов на ферритно-цементитную смесь и протекает тем полнее, чем выше температура нагрева. Температура отпуска оказывает, таким образом, основное влияние на свойства отпущенной стали.
Превращения при нагреве закаленной стали
12
vk.com/club152685050 | vk.com/id446425943
В общем случае структура закаленной стали может состоять из мартенсита, остаточного аустенита и других структурных составляющих. В данном случае представляют интерес мартенсит и остаточный аустенит как метастабильные фазы. Их переход в стабильные фазы феррита и цементита может протекать только путем диффузии, поэтому при низких температурах они практически не распадаются.
Нагрев сталей со структурой из мартенсита и остаточного аустенита до Тн в интервале 80 - 200 °С ведет к частичному выделению углерода из мартенсита. Углерод образует очень мелкие кристаллики ε - карбида (в несколько атомных слоев), который по составу близок к Fe2C. В результате формируется структура отпущенного мартенсита (Мотп). Она состоит из смеси мартенсита с уменьшенной пересыщенностью углеродом (My) и ε - карбида, когерентно связанного с решеткой
My.
При Тн в интервале 200 - 300 °С Аост. превращается в MОТП-: идет процесс снижения содержания углерода в My и увеличение количества карбидной фазы.
При температуре нагрева в интервале 300 - 400 °С содержание С в решетке Feα становится практически равновесным, а частицы Fe2C превращаются в Fe3C и окончательно обосабливаются от матрицы Feα
Благодаря осуществлению всех процессов, протекающих в интервале температур 80 - 400 °С, формируется структура - тростит отпуска (Тотп). Он представляет собой структуру из мелких округлой формы частиц цементита, равномерно распределенных в феррите.
При Тн более 400° С диффузионные процессы активизируются настолько, что цементитные образования укрупняются путем распада одних - более мелких, потому менее устойчивых, и роста других. При этом образуется более грубая, чем тростит, смесь глобулярного цементита и феррита - сорбит отпуска (Сотп.).
При Тн, близких к АI образуется еще более грубая смесь зернистого цементита и феррита, называемая зернистым перлитом.
Образование структур отпуска с зернистым цементитом улучшает многие свойства стали. Сталь с зернистым цементитом, по сравнению со сталью с пластинчатым цементитом, имеет более высокие пределы текучести, ударной вязкости и поперечного сужения при практически одинаковых значениях твердости и предела прочности из-за различий границ между Ф и Ц по форме и суммарной площади.
Различают следующие три вида отпуска:
Низкотемпературный (низкий) отпуск предусматривает нагрев до температур 150-250°С. При этом происходит частичное выделение избыточного углерода из мартенсита, сопровождающееся уменьшением его тетрагональности. После низкого отпуска получают структуру отпущенного мартенсита. За счет снижения внутренних напряжений при низком отпуске повышается прочность и несколько улучшается вязкость стали без заметного снижения ее твердости.
Низкий отпуск применяет при обработке инструмента из углеродистых и легированных сталей, для которых необходима высокая твердость (580-600 НВ) и износостойкость – токарных и строгальных резцов, фрез, зенкеров, сверл, измерительного инструмента и т.д.
13
vk.com/club152685050 | vk.com/id446425943
Среднетемпературный (средний) отпуск выполняют при 350-450°С и назначают главным образом для пружин в рессор, а также для штампов. Такой отпуск обеспечивает высокие пределы упругости и выносливости. При среднем отпуске происходит распад отпущенного мартенсита на ферритно-цементитную смесь высокой дисперсности, называемую трооститом отпуска; твердость его 350-
400 НВ.
Высокотемпературный (высокий) отпуск включает нагрев закаленной стали до температуры 500-650°С. При этом происходит укрупнение выделений цементита. Образующуюся структуру называют сорбитом отпуска. Высокий отпуск почти полностью снимает внутренние напряжения и значительно повышает ударную вязкость и пластичность стали, прочность и твердость при этом несколько снижаются.
Сочетание закалки с последующим высоким отпуском называют улучшением, так как при этом сталь приобретает оптимальное сочетание механических свойств: высокую пластичность, прочность и вязкость. Высокий отпуск применяют при термообработке разнообразных изделий из углеродистых и легированных конструкционных сталей.
Отличие сорбита и троостита отпуска от аналогичных структур, получаемых при закалке, состоит в том, что в первом случае цементит имеет зернистую форму, а во втором – пластинчатую. Это обусловливает получение в отпущенной стали более высоких механических свойств, чем в закаленной, имеющей такую же структуру.
Продолжительность выдержки при отпуске составляет обычно 1 – 2,5 часа и зависит от габаритов изделия; с их увеличением назначают более длительный отпуск.
В интервале 200-300°С на шлифованной поверхности образца возникает тонкий слой окислов (цвета "побежалости"), по которым можно приближенно оценить температуру нагрева (таблица 1).
|
|
|
|
|
|
|
Таблица 1 |
|
Цвета |
побежалости |
(в |
зависимости |
от |
температуры |
образца |
||
и толщины слоя окалины) |
|
|
|
|
|
|
||
|
Цвета побежалости |
|
Температура, °С |
|
Толщина слоя |
|
|
|
|
|
|
окалины, мм |
|
|
|||
|
|
|
|
|
|
|
|
|
|
Соломенно-желтый |
|
220-240 |
|
0,045 |
|
|
|
|
Оранжевый |
|
240-260 |
|
0,0550 |
|
|
|
|
Красно-фиолетовый |
|
260-280 |
|
0,065 |
|
|
|
|
Синий |
|
|
280-300 |
|
0,070 |
|
|
Для проведения низкого отпуска образец необходимо поместить в печь, нагретую до температуры не ниже 400°С, и выдержать там до появления соломенножелтого цвета, при среднетемпературном отпуске нагрев ведут до появления синего цвета, а при высокотемпературном образец выдерживают при выбранной температуре в течение часа.
После отпуска поверхность образца зачищают и измеряют твердость на приборе Роквелла: по полученным данным строится график изменения твердости в зависимости от температуры отпуска.
14
vk.com/club152685050 | vk.com/id446425943
КОНТРОЛЬНЫЕ ВОПРОСЫ
1.Что называется отпуском?
2.С какой целью проводят отпуск?
3.Какое влияние оказывает скорость охлаждения при отпуске на остаточные напряжения в стали?
4.Какие процессы происходят в сталях при нагревании ниже критических температур?
5.Перечислите основные виды отпуска.
6.Какая структура получается после низко-, средне- и высокотемпературного отпуска?
7.Какова цель низко-, средне- и высокотемпературного отпуска?
8.Какие детали подвергаются низко-, средне- и высокотемпературному отпуску?
9.Чем объясняется понижение твердости закаленной стали по мере повышения температуры отпуска?
10.Что называется улучшением стали?
11.Каково различие сорбита отпуска от сорбита закалки?
12.От чего зависит продолжительность отпуска?
15

vk.com/club152685050 | vk.com/id446425943
Лабораторная работа №7
ОПРЕДЕЛЕНИЕ ТВЕРДОСТИ МЕТАЛЛОВ
Цель работы – освоить методики определения твердости вдавливанием на приборах Бринелля и Роквелла, выбрать условия испытаний для различных материалов, установить связь твердости с другими механическими свойствами.
Задание и порядок выполнения работы
1.Ознакомиться с сущностью методов измерения твердости по Бринеллю и Роквеллу.
2.Измерить твердость трех образцов стали, выбрав по табл. 1 и 3 условия испытания; на двух образцах отожженной стали различной толщины измерить твердость на приборах Бринелля и Роквелла; на образце закаленной стали произвести измерение твердости по Роквеллу. Результаты испытаний занести в протокол, сравнить полученные результаты.
3.Определить пределы прочности отожженных образцов стали, зная их твердость по Бринеллю.
Приборы и материалы Автоматический рычажный пресс Бринелля, прибор типа Роквелла, лупа, стали
после различных видов термической обработки.
Основы теории Твердостью называют свойство материала оказывать сопротивление
пластической деформации при контактном воздействии в поверхностном слое. Это одна из наиболее распространенных характеристик, определяющих качество металлов и сплавов, их применимость в различных конструкциях и условиях работы. Широкое распространение методов измерения твердости объясняется многими причинами:
1)между твердостью и другими механическими свойствами (главным образом пределом прочности), существует количественная зависимость;
2)простота измерения;
3)быстрота оценки качества полуфабрикатов независимо от размеров и формы заготовки;
4)возможностью оценки качества готовых изделий;
5)отсутствием разрушения металла (детали);
6)возможность измерения твердости на деталях небольшой толщины, а также в очень тонких слоях, не превышающих десятых долей миллиметра .
Часто только по твердости определяют готовность полуфабрикатов и готовых изделий. Так, например, все виды режущего, мерительного инструмента, цементованные, цианирование, азотированные детали контролируют только на
справедливо для некоторых способов измерения твердости
16

vk.com/club152685050 | vk.com/id446425943
твердость. Определение твердости является почти единственным методом контроля качества штампов и металла для холодной штамповки. Твердость металла при необходимости определяют не только при комнатной температуре, но и при повышенной.
Твердость металлов измеряют при помощи воздействия на поверхность металла наконечника, изготовленного из малодеформирующегося металла (закаленная сталь, алмаз, твердый сплав). Существует несколько способов измерения твердости, различающихся по характеру воздействия наконечника. Твердость можно измерять вдавливанием, царапанием, ударом или по отскоку наконечника-шарика. Наибольшее применение получило измерение твердости вдавливанием. В этом случае твердость характеризует сопротивление материалов местной пластической деформации, возникшей при внедрении в него более твердого тела – индентора. Наиболее распространенными способами определения твердости вдавливанием являются методы Бринелля и Роквелла.
Определение твердости по методу Бринелля Сущность метода (ГОСТ 9012-59) заключается во вдавливании стального
шарика диаметром D в образец под действием нагрузки P и измерением диаметра отпечатка d после снятия испытательной нагрузки (рис.1, а).
|
а |
б |
Рис.1. Измерение твердости по Бринеллю: а – схема испытания; б – прибор для измерения твердости: 1- столик, 2 – маховик; 3 – грузы, 4 – индентор (шарик), 5 – электродвигатель.
Испытуемый образец устанавливают на столик прибора (рис.1, б), затем с помощью маховика столик поднимают (поднимать столик следует до упора); затем нажатием кнопки включают двигатель. В течение определенного времени к образцу прикладывается выбранная нагрузка, после снятия которой, столик с образцом отводится, и на образце с помощью специальной лупы измеряют диаметр отпечатка (цена деления лупы – 0,1 мм).
При определении твердости по Бринеллю индентором служит стальной закаленный шарик диаметром 2,5; 5,0 или 10 мм. Твердость по Бринеллю
17

vk.com/club152685050 | vk.com/id446425943
обозначается цифрами, характеризующими величину твердости и буквами НВ, например 185 НВ.
Число твердости по Бринеллю НВ определяется как отношение нагрузки к площади отпечатка:
НВ |
2Р |
|
|
10 |
6 |
|
|
|
|||
D |
|
d |
|
||
D |
2 |
2 |
|
||
|
|
|
|
(1)
В практике определения твердости не делают вычислений по формуле (1), а пользуются таблицей, составленной для установленных диаметров шариков, отпечатков и нагрузок (табл. 2).
При выборе диаметра шарика и нагрузки следует руководствоваться данными табл.1, при этом для получения сопоставимых результатов при измерении твердости образцов из одного материала, имеющих разную толщину, необходимо, чтобы отношение Р/D2 оставалось неизменным.;
При измерении твердости на приборе Бринелля необходимо выполнить следующие требования:
1)поверхность образца должна быть плоской, чтобы края отпечатка были отчетливо видны при измерении его диаметра; давление прикладывается перпендикулярно поверхности образца. Поверхность образца в зоне нагружения должна быть свободной от окалины и других посторонних веществ;
2)расстояние от центра отпечатка до края образца не должно быть менее чем 2,5d, а расстояние между центрами соседних отпечатков – 4d;
3)диаметры отпечатков должны находиться в пределах 0,2D<d<0,6D;
4)минимальную толщину образцов выбирают не менее десятикратной глубины отпечатка; на обратной стороне испытуемого образца не должно быть заметно следов деформаций.
Как видно, большинство этих требований направлено на устранение влияния
различных искажающих факторов и только при выполнении этих требований можно получить достоверные и воспроизводимые значения твердости
Образцы с твердостью более 450 НВ на приборе Бринелля испытывать запрещается.
Таблица 1 Условия испытаний при измерении твердости по Бринеллю
|
Интервал |
Толщина |
Соотноше ние междуP и D2 |
Диаметр шарикаD, мм |
Нагрузка кг,P |
Выдержка под |
|
|
|
|
|||
металлы |
твердости |
образца, |
|
|
|
нагрузкой, |
|
НВ |
мм |
|
|
|
с |
|
|
|
|
|
|
|
|
|
6 – 3 |
|
10 |
3000 |
|
Черные |
140 – 450 |
4 – 2 |
P=30D2 |
5 |
750 |
10 |
|
|
менее 2 |
|
2,5 |
187,5 |
|
|
|
более 6 |
|
10 |
1000 |
|
Черные |
≤140 |
6 – 3 |
P=10D2 |
5 |
250 |
10 |
|
|
менее 3 |
|
2,5 |
62,5 |
|
|
|
6 – 3 |
|
10 |
3000 |
|
Цветные |
≥130 |
4 – 2 |
P=30D2 |
5 |
750 |
30 |
|
|
более 2 |
|
2,5 |
187,5 |
|
18
vk.com/club152685050 | vk.com/id446425943
|
|
|
9 - 3 |
|
10 |
1000 |
|
Цветные |
35 |
– 130 |
6 – 3 |
P=10D2 |
5 |
250 |
30 |
|
|
|
2 – 3 |
|
2,5 |
62,5 |
|
|
8 |
– 35 |
Более 6 |
|
10 |
250 |
|
Цветные |
8 |
– 35 |
6 – 3 |
P=2,5D2 |
5 |
62,5 |
60 |
|
8 |
– 35 |
менее 3 |
|
2,5 |
25,6 |
|
Между числом твердости по Бринеллю НВ и пределом прочности при
растяжении в (МПа) существуют соотношения: |
|
|
сталь (НВ = 125 – 175)…………………………………... в ≈ 3,4 |
НВ; |
|
сталь (НВ = 175 – 450)…………………………………... в ≈ 3,5 |
НВ; |
|
серый чугун……………………………………………… в ≈ (НВ-40)/6; |
||
алюминий и алюминиевые сплавы (НВ = 20 – 45)…… |
в ≈ 3,3 |
– 3,6 НВ; |
дуралюмин: отожженный…………………………. |
в ≈ 3,6 |
НВ; |
после закалки и старения…………... |
в ≈ 3,5 |
НВ; |
медь, латунь, бронза отожженная……………………… |
в ≈ 5,5 |
НВ; |
наклепанная……………………... |
в ≈ 4,0 |
НВ. |
Таблица 2 Соотношение чисел твердости, определенных различными методами
|
|
При испытании вдавливанием |
|
|
|||
|
стального |
алмазного конуса или стального шарика |
алмазной |
||||
Диаметр |
шарика |
на приборе Роквелла при различных |
|||||
пирамиды |
|||||||
отпечатка, |
10/3000 на |
|
нагрузках |
|
|
||
|
|
|
на приборе |
||||
мм |
приборе |
150 кг |
60 кг |
100 |
кг |
||
Виккерса |
|||||||
|
Бринелля |
(конус) |
(конус) |
(шарик) |
|||
|
HV |
||||||
|
НВ |
HRC |
HRA |
HRB |
|||
|
|
||||||
2,20 |
780 |
72 |
84 |
- |
|
1124 |
|
2,30 |
712 |
68 |
82 |
- |
|
1022 |
|
2,40 |
653 |
64 |
80 |
- |
|
868 |
|
2,50 |
601 |
60 |
78 |
- |
|
746 |
|
2,60 |
555 |
56 |
77 |
- |
|
650 |
|
2,70 |
524 |
52 |
75 |
- |
|
587 |
|
2,80 |
477 |
49 |
74 |
- |
|
534 |
|
2,90 |
444 |
46 |
73 |
- |
|
474 |
|
3,00 |
415 |
43 |
72 |
- |
|
435 |
|
3,10 |
388 |
41 |
71 |
- |
|
401 |
|
3,20 |
363 |
39 |
70 |
- |
|
380 |
|
3,30 |
341 |
36 |
68 |
- |
|
344 |
|
3,40 |
321 |
33 |
67 |
- |
|
320 |
|
3,50 |
302 |
31 |
66 |
- |
|
303 |
|
3,60 |
285 |
29 |
65 |
- |
|
285 |
|
3,70 |
269 |
27 |
64 |
- |
|
270 |
|
3,80 |
255 |
25 |
63 |
- |
|
255 |
|
3,90 |
241 |
23 |
62 |
102 |
240 |
||
4,00 |
229 |
21 |
61 |
100 |
228 |
19

vk.com/club152685050 | vk.com/id446425943
4,10 |
217 |
19 |
60 |
98 |
217 |
4,20 |
207 |
15 |
59 |
95 |
208 |
4,30 |
197 |
13 |
58 |
93 |
197 |
4,40 |
187 |
11 |
57 |
91 |
186 |
4,50 |
179 |
8 |
56 |
90 |
178 |
Определение твердости по методу Роквелла Сущность метода заключается во вдавливании наконечника с алмазным
конусом или со стальным шариком в испытуемый образец под действием последовательно прилагаемых предварительной Р0 и основной Р1 нагрузок и измерением глубины отпечатка, а точнее разности между глубиной отпечатков, полученных от вдавливания наконечника под действием основной нагрузки и от вдавливания под предварительной нагрузкой (рис. 2,а).
а б Рис.2. Измерение твердости по Роквеллу: а – схема испытания; б – прибор для
измерения твердости: 1- столик, 2 – маховик; 3 – груз, 4 – шкала-индикатор, 5 – масляный регулятор, 6 – шток с индентором, 7 – рукоятка.
Рис.3. общий вид прибора Роквелла Испытуемый образец устанавливают на столик прибора (рис.2, б), поворотом
маховика по часовой стрелке столик поднимают таким образом, чтобы наконечник мог вдавливаться в поверхность установленного образца; при дальнейшем подъеме
20
vk.com/club152685050 | vk.com/id446425943
столика начинают вращаться стрелки на циферблате. Подъем столика продолжают до тех пор, пока малая стрелка не примет вертикального положения, указываемого на циферблате красной точкой. Это означает, что наконечник вдавился в образец под действием определенной (предварительной) нагрузки, равной 10 кг. Предварительное нагружение проводят для того, чтобы исключить влияние упругой деформации и различной степени шероховатости поверхности образца на результаты измерений.
Когда образец получает предварительную нагрузку 10 кг, большая стрелка на циферблате принимает вертикальное положение или близкое к нему. Для точности измерения необходимо, чтобы большая стрелка указывала на цифру «0» на черной шкале циферблата. Если положение большой стрелки не совпадает точно с цифрой «0», то, не меняя величины предварительного нагружения и, следовательно, не вращая маховик, поворачивают шкалу индикатора (круг циферблата) таким образом, чтобы цифра «0» на черной шкале циферблата переместилась и совпала с большой стрелкой, отклонение которой от вертикали допускается в пределах ±5 единиц шкалы.
Затем освобождают рукоятку 2 и она плавно перемещается до упора. Такое перемещение рукоятки сообщает испытуемому образцу через рычаг основную нагрузку, определяемую грузом, привешенным к рычагу. При этом нагружении большая стрелка перемещается по циферблату против часовой стрелки. Время приложения основной нагрузки 5 – 7 с. Затем рукоятку прибора плавно переводят в исходное состояние и тем самым снимают дополнительную нагрузку, но оставляют предварительную. Большая стрелка перемещается по циферблату по часовой стрелке. Цифра, на которую указывает на шкале циферблата большая стрелка, представляет число твердости по Роквеллу. Эту цифру записывают и, поворачивая маховик против часовой стрелки, опускают столик прибора с образцом, снимая тем самым предварительную нагрузку.
Прибор измеряет разность между глубиной отпечатков, полученных от вдавливания наконечника под действием основной нагрузки и от вдавливания под предварительной нагрузкой. Каждое деление (единица шкалы) индикатора соответствует глубине вдавливания в 0,002 мм.
Испытания повторяют на одном образце четыре раза, принимая среднее из трех последних.
Существуют три шкалы измерения твердости по методу Роквелла – А, В, С. Они отличаются прикладываемой нагрузкой и индентором (закаленный стальной шарик с диаметром 1, 59 мм или алмазный конус с углом при вершине 120º) и служат для определения твердости различных материалов (табл. 3) – от мягких цветных металлов до твердых сплавов (от 100 НВ до 1000 НВ).
Твердость по Роквеллу обозначается цифрами, характеризующими величину твердости и буквами HR с указанием шкалы твердости. Например, 61 HRC – твердость 61 по шкале С.
1)Шкала А. Измерения проводятся алмазным конусом с общей нагрузкой 60 кг (600 Н), в этом случае также пользуются черной шкалой, обозначают НRА. Шкалу HRA применяют для испытания твердых сплавов, тонкого листового материала, а также для определения твердости малых поверхностных слоев.
21
vk.com/club152685050 | vk.com/id446425943
2)Шкала В. Измерения проводятся стальным закаленным шариком с общей нагрузкой 100 кг (1000 Н). Измеряют твердость отожженной стали и цветных металлов. Значение твердости оценивают по красной шкале "В" и обозначают
HRB.
3)Шкала С. Измерения проводятся алмазным конусом с общей нагрузкой 150 кг (1500 Н) для определения твердости: закаленной и отпущенной стали – с твердостью больше 450 НВ; материалов средней твердости (больше 230 НВ); поверхности слоев толщиной более 0,5 мм (например, цементированного). Значения твердости оценивают по черной шкале и обозначают HRC.
Таблица 3 Условия испытаний при измерении твердости на приборе Роквелла
шкала |
Обозначен |
Наконечн |
Нагрузка, |
Цвет |
Предел измерений |
||
ие чисел |
цифербла |
|
|
||||
ик |
кг |
НВ |
HR |
||||
твердости |
та |
||||||
|
|
||||||
|
|
|
|
|
|
|
|
А |
HRA |
конус |
60 |
черный |
360-1000 |
70-85 HRA |
|
В |
HRB |
шарик |
100 |
красный |
100-240 |
47-105 HRB |
|
С |
HRC |
конус |
150 |
черный |
240-700 |
20-67 HRC |
Пользуясь таблицей 3, зная примерно твердость материала, легко выбрать индентор и прикладываемую нагрузку, например: углеродистая эвтектоидная сталь в отожженном состоянии характеризуется значением твердости ~200 НВ. Т.к. предел измерений твердости 100-240 НВ соответствует шкале «В» по Роквеллу, измерение твердости указанного материала будем производить при нагрузке 100 кг с помощью закаленного стального шарика.
При измерении твердости на приборе Роквелла необходимо выполнить следующие требования:
1)образец должен иметь тщательно зашлифованную плоскую поверхность, противоположная параллельная поверхность должна быть также ровной, зачищенной;
2)образец должен устойчиво лежать на столике прибора;
3)расстояние от центра отпечатка до края образца или до центра другого отпечатка должно быть не менее 1,5 мм при вдавливании конуса и не менее 4 мм при вдавливании шарика;
4)минимальную толщину образцов выбирают не менее десятикратной глубины отпечатка.
Числа твердости по Роквеллу можно приблизительно пересчитать на числа
твердости по Бринеллю с помощью диаграмм и таблицы (см. табл. 2), построенных на основании многочисленных экспериментальных работ. Зависимость между этими числами, не имеет линейного характера.
Преимущества метода Роквелла:
возможность определения твердости материалов с твердостью более 450 НВ;
измерение твердости требует меньших временных затрат;
результат измерения считывается по шкале;
на поверхности детали остается меньший отпечаток;
возможность определения твердости тонких поверхностных слоев (толщиной более 0,5 мм).
22
vk.com/club152685050 | vk.com/id446425943
КОНТРОЛЬНЫЕ ВОПРОСЫ
1.Что называется твердостью?
2.Чем объясняется широкое распространение измерения твердости в технике?
3.Как измеряют твердость на приборе Бринелля?
4.От чего зависит выбор диаметра индентора при испытаниях по Бринеллю?
5.Каково предельное значение твердости материала, которую можно измерить на приборе Бринелля?
6.Какова зависимость между пределом прочности и твердостью по Бринеллю для отожженной стали и других материалов?
7.Как измеряют твердость на приборе Роквелла?
8.Чем определяется выбор наконечника при испытаниях по Роквеллу?
9.Перечислите преимущества измерения твердости методом Роквелла.
10.Перечислите требования, которые необходимо соблюдать при измерении твердости по методам Бринелля и Роквелла.
Литература
1.Материаловедение и технология металлов: учеб. для вузов по машиностроит. спец./ [Фетисов Г.П. и др.]; по ред. Г.П. Фетисова. – Изд. 6-е, доп. – М.: Высш. шк.,
2008. – 877 с.
2.Материаловедение и технология конструкционных материалов: Учебник/ В.Б.Арзамасов, А.Н.Волчков. – М.:, Академия, 2009.- 448 с.
3.Сильман Г.И. Материаловедение: учеб. пособие для вузов по спец. напр. «Металлургия, машиностроение и материалоперераб.» /. – М.: Академия, 2008 .- 335 с.
23