
05 семестр / Книги и методические указания / Петров Соединения вал-ступица
.pdf
21
2.3. Треугольные шлицевые соединения
Эти соединения имеют ограниченное применение при передаче небольших вращающих моментов, характерное использование - крепление рычагов в системах управления, мелкомодульные зубья получают на валах накатыванием, в отверстиях - протягиванием. Треугольные шлицы выполняют по отраслевым нормалям, например, ОСТ 10009273. По нагрузочной способности они равноценны эвольвентным.
Таблица 7 Параметры треугольных шлицевых соединений (по стандарту TGL 5481)
D, мм |
Z |
m |
|
h |
d1, … ° |
|
|
|
мм |
|
|
|
|
|
|
|
|
8 |
28 |
0,27 |
|
0,6 |
47 |
|
|
|
|
|
|
10 |
28 |
0,32 |
|
0,9 |
47 |
|
|
|
|
|
|
12 |
30 |
0,37 |
|
0,9 |
48 |
|
|
|
|
|
|
14 |
31 |
0,42 |
|
1,0 |
48 |
|
|
|
|
|
|
17 |
32 |
0,50 |
|
1,1 |
49 |
|
|
|
|
|
|
20 |
33 |
0,56 |
|
1,3 |
49 |
|
|
|
|
|
|
24 |
34 |
0,65 |
|
1,6 |
49 |
|
|
|
|
|
|
D, мм |
Z |
m |
|
h |
d1, … ° |
|
|
|
мм |
|
|
|
|
|
|
|
|
30 |
35 |
0,80 |
|
1,8 |
50 |
|
|
|
|
|
|
34 |
36 |
0,89 |
|
1,8 |
50 |
|
|
|
|
|
|
40 |
37 |
1,02 |
|
2,0 |
50 |
|
|
|
|
|
|
44 |
38 |
1,10 |
|
2,1 |
51 |
|
|
|
|
|
|
50 |
39 |
1,22 |
|
2,5 |
51 |
|
|
|
|
|
|
55 |
40 |
1,30 |
|
2,6 |
51 |
|
|
|
|
|
|
60 |
42 |
1,37 |
|
2,6 |
51 |
|
|
|
|
|
|
Примечание. Угол профиля отверстия 2d2=60 °.
2.4. Расчёт шлицевых соединении
Шлицевые соединения могут подвергаться нагружению:
1)- только вращающим моментом Т;
2)- вращающим моментом Т и поперечной силой F;
3)- вращающим Т и изгибающим М моментами;
4)- комплексной нагрузкой, объединяющей все вышеупомянутые.

22
Первый вид нагружения имеет место, например, в соединениях трансмиссионных и карданных валов. Второй - наиболее распространенный - в соединениях вала с прямозубыми зубчатыми колёсами, звездочками цепных передач, шкивами ременных передач. Третий - в соединениях торсионных валов подвески автомобиля и торсионного вала со ступицами зубчатых колёс, размещенных в разных корпусах. Четвертый тип нагружения встречается в соединениях прямозубых шестерен с несимметричными ступицами, косозубых, конических зубчатых и червячных колёс с валами.
В зависимости от вида нагружения и конструкции нагрузка может распределяться неравномерно между зубьями (окружная неравномерность) и вдоль зубьев (продольная неравномерность). Окружная неравномерность вызывается поперечными силами, погрешностями обработки и монтажа. Продольная неравномерность обусловлена податливостью деталей, погрешностями монтажа и обработки, конструктивными особенностями шлицевого соединения. Поэтому расчёты шлицевых соединений ведут по т. н. расчётной нагрузке, используя соответствующие коэффициенты нагрузки kсм и kизм.
Зубья шлицевых соединений работают на изгиб, срез, смятие и износ. Лимитирующими критериями работоспособности являются смятие и износостойкость.
|
|
|
|
|
|
|
|
|
23 |
Расчёт на смятие |
|
|
|
|
|||||
σ |
см |
= |
|
103 Тkдkсм |
≤[σ] |
= |
σТ |
, |
МПа, |
|
|
||||||||
|
|
|
|
см |
|
nТ |
|||
|
|
|
|
l SF |
|
|
|||
где |
|
Т - номинальный вращающий момент в Нм; |
|||||||
|
|
|
kд - коэффициент динамичности нагрузки (при знакопеременной на- |
||||||
грузке kд =2, |
|
при частом реверсировании kд =2,5); |
kсм - коэффициент концентрации нагрузки; l - рабочая длина соединения в мм;
SF - удельный суммарный статический момент площади рабочих поверхностей соединения относительно геометрической оси вала в мм3/мм;
σТ - предел текучести материала;
nТ=1,25 … 1,4 (большее значение для закаленных поверхностей) - за-
пас прочности по σТ.
SF =0,5dсрhZ
Здесь dср - средний диаметр шлицевого соединения в мм; h - высота зуба в мм;
Z - число зубьев. Коэффициент концентрации нагрузки
kСМ = k3 kпр kп
Здесь k3 - коэффициент, учитывающий окружную неравномерность (табл.8); kпр - коэффициент, учитывающий продольную неравномерность распреде-
ления нагрузки;
kп - коэффициент, учитывающий концентрацию нагрузки, обусловленную погрешностями изготовления (при нагружении только вращающим моментом и твердости
≤350 НB kп=1; при твердости ≥350 НB kп=1,1...1,6 в зависимости от точности изготовления; при комплексном нагружении kп= kпр).
24
Таблица 8
Коэффициенты окружной неравномерности распределения нагрузки
|
|
|
|
|
ψ = |
|
dср |
|
|
|
|
|
|
|
|
|
|
dw cosαw |
|
|
|
|
|
||
|
|
|
|
|
|
|
|
|
|
|
|
|
|
0,30 |
0,35 |
0,40 |
0,45 |
0,50 |
0,55 |
|
0,60 |
0,65 |
0,70 |
0,75 |
|
|
|
|
|
|
|
|
|
|
|
|
|
|
k3 |
1,6 |
1,7 |
1,8 |
1,9 |
2,0 |
|
2,1 |
|
2,2 |
2,4 |
2,7 |
3,0 |
k3 |
1,1 |
1,2 |
1,4 |
1,6 |
1,9 |
|
2,2 |
|
2,5 |
3,0 |
3,7 |
4,5 |
Здесь dw- начальный диаметр зубчатого колеса;
αw - угол зацепления.
Коэффициент, учитывающий продольную неравномерность распределения нагрузки при нагружении только вращающим моментом, а также при симметричных ступицах зубчатых колёс принимается kпр=kкр, где kкр - коэффициент концентрации нагрузки от закручивания вала (табл. 9). При нессиметричных ступицах kпр устанавливается по ГОСТ 21425-75 (см, например, учебное пособие Н.Д. Кулакова Расчёт шлицевых соединений, МАМИ, 1979г.)
Таблица 9
Коэффициент концентрации нагрузки от закручивания вала
Наружный |
|
|
|
|
|
|
|
Отношение l/D |
|
|
|
|
|
|
||||
диаметр шлиц |
|
|
|
|
|
|
|
|
|
|
|
|
|
|
|
|
|
|
|
1,0 |
|
1,5 |
|
|
2,0 |
|
|
2,5 |
|
3,0 |
|||||||
|
|
|
|
|
|
|
|
|
|
|
|
|
|
|
|
|
|
|
серия |
D, мм |
|
|
|
|
|
|
|
Коэффициент kкр |
|
|
|
|
|
|
|||
|
1 |
|
2 |
1 |
|
2 |
|
1 |
|
2 |
|
1 |
|
2 |
1 |
|
2 |
|
|
|
|
|
|
|
|
|
|
|
|
|
|
|
|
|
|
|
|
легкая |
30…50 |
1,5 |
|
1,2 |
2,0 |
|
1,3 |
|
2,6 |
|
1,5 |
|
3,3 |
|
1,8 |
3,9 |
|
1,9 |
|
|
|
|
|
|
|
|
|
|
|
|
|
|
|
|
|
|
|
58…120 |
1,8 |
|
1,3 |
2,6 |
|
1,4 |
|
3,4 |
|
1,7 |
|
4,2 |
|
2,0 |
5,1 |
|
2,2 |
|
|
|
|
|
|
|
|
|
|||||||||||
|
|
|
|
|
|
|
|
|
|
|
|
|
|
|
|
|
|
|
средняя |
32…50 |
1,9 |
|
1,3 |
2,8 |
|
1,5 |
|
3,7 |
|
1,8 |
|
4,6 |
|
2,1 |
5,5 |
|
2,3 |
|
|
|
|
|
|
|
|
|
|
|
|
|
|
|
|
|
|
|
св. 112 |
2,8 |
|
1,5 |
4,1 |
|
1,9 |
|
5,5 |
|
2,5 |
|
6,8 |
|
2,7 |
8,2 |
|
3,1 |
|
|
54…112 |
2,4 |
|
1,4 |
3,5 |
|
1,7 |
|
4,8 |
|
2,1 |
|
5,8 |
|
2,4 |
7,0 |
|
2,8 |
|
|
|
|
|
|
|
|
|
|
|
|
|
|
|
|
|
|
|
тяжелая |
35…65 |
2,7 |
|
1,5 |
4,1 |
|
1,9 |
|
5,3 |
|
2,2 |
|
6,8 |
|
2,7 |
8,0 |
|
3,1 |
|
|
|
|
|
|
|
|
|
|
|
|
|
|
|
|
|
|
|
св. 102 |
3,1 |
|
1,7 |
4,7 |
|
2,1 |
|
6,2 |
|
2,5 |
|
7,8 |
|
3,0 |
9,3 |
|
3,5 |
|
|
72…102 |
2,9 |
|
1,6 |
4,3 |
|
2,0 |
|
5,6 |
|
2,4 |
|
7,0 |
|
2,8 |
8,5 |
|
3,3 |
|
|
|
|
|
|
|
|
|
|
|
|
|
|
|
|
|
|
|

25
Примечание.
Здесь коэффициент kкр приведен для двух случаев:
1- до приработки соединения (.для расчёта на смятие) и
2- после приработки для соединений, работающих с переменным нагрузоч-
ным режимом. При постоянном режиме после приработки |
kпр=1. |
||||||
l |
- длина ступицы. |
|
|||||
Расчёт на износостойкость. |
|
||||||
σ |
|
= 10 |
3 Тkизн ≤[σ] |
|
|||
|
изн. |
|
|
l |
|
изн., МПа |
|
|
|
|
|
S F |
|
||
Здесь, |
помимо известных из расчёта на смятие, |
коэффициент концентрации на- |
|||||
грузки |
kизн |
= k3′ |
kпр и [σ ]изн -допускаемое напряжение. |
k3′- берется по данным табл. 8,
kпр - аналогично расчёту на смятие.
[σ ]изн =20…100 МПа при твердости ≤ 350 НВ и [σ ]изн =50 …150 МПа при твер-
дости ≥ 350 НВ.
Изложенная выше методика расчёта на смятие и износостойкость по ГОСТ 21425-75 распространяется На прямобочные шлицевые соединения валов с зубчатыми колёсами, муфтами и аналогичными деталями, В других случаях, для эвольвентных, треугольных шлицевнх соединений, а также приближенно расчёт ведут по средним напряжениям смятия
σсм = ξ10l 3 ТSF ≤[σ]см , МПа,
где ξ = 0,8…0,9 коэффициент, учитывающий неравномерность распределения нагрузки по зубьям;
[σ]см - среднее допускаемое напряжение смятия (таблица 10).
|
|
26 |
|
|
|
|
|
|
|
|
|
|
Таблица 10 |
|
|
|
|
|
|
|
Тип |
Условия |
|
|
[σ]см , МПа |
|
|
соединения |
работы |
|
|
|
|
|
|
При отсутствии |
|
с термообработкой |
|||
|
|
|
термообработки |
|
|
|
|
|
|
|
|
|
|
неподвижное |
а |
|
30 ... 50 |
|
40 |
... 70 |
|
|
|
|
|
|
|
|
б |
|
60 … 100 |
|
100 |
... 140 |
|
|
|
|
|
|
|
|
в |
|
80 ... 120 |
|
120 |
... 200 |
|
|
|
|
|
|
|
подвижное |
а |
|
15 ... 20 |
|
20 |
... 35 |
не под нагрузкой |
|
|
|
|
|
|
б |
|
20 ... 30 |
|
30 |
... 60 |
|
|
|
|
||||
|
|
|
|
|
|
|
|
в |
|
25 … 40 |
|
40 |
... 70 |
подвижное |
а |
|
- |
|
3 … 10 |
|
под нагрузкой |
|
|
|
|
|
|
б |
|
- |
|
5 … 15 |
||
|
|
|
||||
|
в |
|
- |
|
10 |
... 20 |
|
|
|
|
|
||
Примечание: |
а - тяжелые, |
б - средние, в - хорошие условия эксплуатации. |
2.5. Примеры расчётов Пример 1
Проверить работоспособность прямобочного шлицевого соединения
b −8 ×36 × 42H12 / d11×7D9 / k7 ГОСТ 1139-80 вала со ступицей полумуфты.
Рабочая длина l=40мм, вал стальной σТ =500 МПа, вращающий момент Т=500 Нм при знакопеременной нагрузке.
Решение.
Проверку производим на смятие и износостойкость. Средний диаметр соединения dср = 0,5(D + d) = 0,5(42 + 36) = 39мм.
Удельный статический момент площади по табл. 3 SF =343 мм2.
Коэффициенты окружной неравномерности распределения нагрузки при нагру-
жении только вращающим моментов k3 = k3′ =1. Коэффициент продольной неравно-
мерности распределения нагрузки при l / D ≈1 для средней серии соединения (табл. 9)
kпр = kкр =1,9.
Коэффициент неравномерности распределения нагрузки, обусловленной погреш-
ностью изготовления при нагружении только вращающим моментом kn =1. Коэффици-
ент концентрации нагрузки при расчёте на смятие kсм = k3 kпр kn =1 1,9 1 =1,9 . Коэф-
фициент динамичности нагрузки при знакопеременном нагружении kд = 2. Коэффициент
27
концентрации нагрузки при расчёте на износостойкость kизн = k3′ kпр =1 1,9 =1,9 . Запас
прочности по пределу текучести для незакаленных поверхностей nT =1,25. . Допускаемое
напряжение смятия [σ]см =σТ / nT |
=500 /1,25 = 400 МПа. Допускаемое напряжение при |
||||||||||||
расчёте на износостойкость берем |
[σ]изн =100 МПа. |
|
|
|
|||||||||
Напряжение смятия в соединении |
|
|
|
|
|||||||||
σ |
см |
= |
103 Т kсм kд |
= |
103 500 1,9 2 |
=139 <[σ] |
|
= 400 МПа |
|||||
|
|
|
|
|
|||||||||
|
|
lSF |
|
|
|
40 343 |
|
см |
|
||||
|
|
|
|
|
|
|
|
|
|
||||
Проверка на износостойкость соединения |
|
|
|
||||||||||
σ = |
103 Т kизн |
= |
103 500 1,9 |
= 70 <[σ] =100 |
|
МПа |
|||||||
|
|
|
|||||||||||
|
|
|
lS F |
|
40 343 |
см |
|
|
|
||||
|
|
|
|
|
|
|
|
Пример 2.
для вала диаметром 40 мм подобрать неподвижное шлицевое соединение со ступицей в двух вариантах: прямобочного и эвольвентного профиля. Материал вала - сталь 45 улучшенная, рабочая длина ступицы l=55 мм, вращающий момент Т=800Нм при средних условиях работы.
Решение.
По ГОСТ 1139-80 (табл. 3) выбираем прямобочное соединение легкой серии
Z × d × D =8 ×36 × 40 удельный суммарный статический момент площади SF =182 мм2.
По ГОСТ 6033-60 (табл. 5) выбираем эвольвентное соединение D × m = 40 × 2 , средний
диаметр |
dср = D −1,1m = 40 −1,1 2 =37,8 |
мм, высота зуба |
h = 0,8 m = 0,8 2 =1,6 мм |
||
удельный |
суммарный |
статический |
момент |
площади |
|
SF = 0,5dср h Z = 0,5 37,8 |
1,6 1,8 =545 |
мм2. Среднее допускаемое напряжение смятия |
|||
(табл. 10) |
[σ]см =100 МПа |
для средних условий работы, коэффициент неравномерности |
распределения нагрузки принимаем |
ξ=0,8. |
|
|||||
Проверка на смятие прямобочного соединения |
|||||||
σ |
|
= |
103 Т |
= |
103 800 |
=100 =[σ] |
=100 МПа, |
|
|
0,8 182 55 |
|||||
|
см |
ξ SF l |
|
см |
|
||
эвольвентного соединения |
|
|
|||||
σ |
|
= |
103 Т |
= |
103 800 |
=33,3 <[σ] |
=100 МПа. |
|
|
0,8 545 55 |
|||||
|
см |
ξ SF l |
|
см |
|
Расчеты убедительно подтверждают преимущество эвольвентного шлицевого соединения.
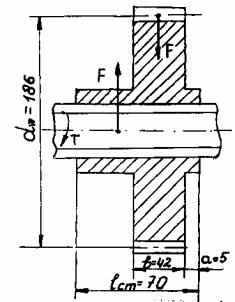
|
|
|
|
|
|
28 |
|
|
Пример 3. |
|
|
|
|
|
|
||
Проверить |
работоспособность |
прямобочного |
шлицевого |
соединения |
||||
d −10 ×72 |
H 7 |
×78 |
×12 |
F10 |
(легкая серия) шестерни с промежуточным валом коробки |
|||
|
e8 |
|||||||
|
f 7 |
|
|
|
|
|
передач трактора.
Шестерня прямозубая, размеры узла и схема нагружения показаны на эскизе.
Материал шестерни - сталь 20ХГНР цементированная, материал вала - сталь 40Х,
закаленная, σ=750 МПа.
Вращающий момент Т=1370 Нм, коэффициент режима нагружения µр=0,5, коэффициент числа циклов kц = 1,75, коэффициент динамичности нагрузки k=2,85 принят равным коэффициенту запаса муфты сцепления трактора.
Решение. |
|
|
|
|
|
|
|
|
Средний диаметр соединения dср = 0,5(D + d) = 0,5(78 + 72) = 75 мм. |
Удельный |
|||||||
суммарный статический момент площади (табл. 3) |
SF |
= 750 мм2. |
|
|||||
Запас прочности по пределу текучести nТ |
=1,4 для закаленных рабочих поверх- |
|||||||
ностей. Допускаемое напряжение смятия |
|
|
|
|||||
[σ]см =σТ / nТ |
|
= 750 /1,4 = 536 МПа. |
|
|
|
|||
Коэффициент |
|
|
|
|
|
|
|
|
|
dср |
75 |
= 0,43 |
|
|
|
||
ψ = |
|
|
= |
|
|
|
|
|
dW cos dW |
|
186 cos 20° |
|
|
|
|||
Коэффициент |
окружной неравномерности |
распределения нагрузки |
(табл. 8) |
kЗ=1,9. Коэффициент неравномерности распределения нагрузки от закручивания вала
(табл. 9) kкр=1,8 при l / D = 70 / 78 ≈1.
Коэффициент концентрации в связи со смещением поперечной нагрузки относи-
тельно середины ступицы берется по графику |
ke = f (ε;ψ) из ГОСТ 21425-75. При |
|||||||
ε = |
е |
= |
a + 0,5 b |
= |
5 + 0,5 42 |
= 0,371 |
и ψ = 0,43 , kе =1,7 . |
|
l |
l |
70 |
||||||
|
|
|
|
|

29
При расположении зубчатого венца со стороны незакручиваемого участка вала коэффициент продольной неравномерности нагрузки принимается как больший из двух значений kкр и kе. Следовательно, kпр − kкр =1,8. Коэффициент неравномерности распре-
деления нагрузки в связи с погрешностями изготовления, учитывая низкую точность изго-
товления и отсутствие приработки, kп =1,45.
Коэффициент концентрации нагрузки при расчёте на смятие kсм = k3 kпр kп =1,9 1,8 1,45 = 4,96
Проверка на смятие
σ |
см |
= |
103 Т kсм kд |
|
= |
103 1370 4,96 2,85 |
=368 <[σ] |
|
=536 МПа. |
||
|
|
|
|||||||||
|
|
|
SF l |
|
750 70 |
см |
|
||||
|
|
|
|
|
|
|
|
||||
Допускаемое условное напряжение при базовом числе циклов нагружений по |
|||||||||||
ГОСТ 21425-75 для закаленных зубьев [σ]усл =185 МПа. |
|
|
|||||||||
Коэффициент переменности нагрузки kН |
= 3 µР = 3 |
0,5 = 0,794 . Коэффициент |
|||||||||
долговечности |
kдолг = kН kЦ =0,794 1,75 =1,39. |
Коэффициент, учитывающий условия |
|||||||||
смазки kC =1 |
для средних условий. Коэффициент, учитывающий условия закрепления |
||||||||||
ступицы на валу kOC =1,25 |
при небольших осевых смещениях. (Коэффициенты kC и kOC |
||||||||||
берутся по ГОСТ 21425-75). |
|
|
|
|
|
|
Коэффициент условий работы kP = kC kOC =1 1,25 =1,25.
Допускаемое напряжение при расчёте на износостойкость
[σ] |
= |
[σ]усл |
= |
|
185 |
=106,5 МПа |
|
|
|||||
см |
|
kдолг kР |
|
1,39 1,25 |
||
|
|
|
Коэффициент окружной неравномерности распределения нагрузки по табл.8 при ψ = 0,43 k3′ =1,5.
Коэффициент концентрации нагрузки при расчёте на износостойкость kизн = k3′ kпр =1,5 1,8 = 2,7
Проверка на износостойкость
σ = |
103 Т kизн |
= |
103 1370 2,7 |
= 70 <[σ] =106,5 |
МПа |
|
|
||||
|
SF l |
|
750 70 |
изн |
|
|
|
|
|

30
3. ПРОФИЛЬНЫЕ СОЕДИНЕНИЯ
Упрофильных соединений передача вращающего момента осуществляется за счёт некруглой формы поверхностей сопрягаемых деталей. Профильные соединения подразделяются на призматические, преимущественно с квадратным валом, соединения с круглым валом и лыской, и собственно профильные соединения (фасонно-профильные).
Для достижения равнопрочности на кручение в призматическом соединении необходимо, чтобы диаметр окружности, вписанный в квадрат соответствовал диаметру круглого вала, а это значительно повышает диаметральный размер соединения. Недостатками призматических соединений являются также технологическая сложность изготовления отверстия и большая концентрация напряжений в углах квадратного отверстия. Призматические соединения и соединения на лыске по нагрузочной способности значительно уступают шлицевым соединениям, поэтому находят применение как неподвижные и малонагруженные для посадки маховичков, рукояток, педалей управления и т.п.
Упрофильных соединений рабочие поверхности образованы циклоидальными кривыми. Соединения бывают цилиндрическими и коническими, последние способны передавать осевую силу, но сложнее в производстве.
Для профильных соединений характерны хорошее центрирование, незначительная концентрация напряжений, высокая надежность и технологичность, в частности возможность точной обработки рабочих поверхностей высокой твердости. Недостатками этих соединений являются необходимость в специальном технологическом оборудовании, большие распорные силы и большие напряжения смятия, чем у шлицевых соединений.
а≈0,0035D R≈0,728D r≈0,272D