
Timofeeva_S_S_Nadezhnost_tekhnicheskikh_sistem_i_tekhnogenny_risk_uchebn_posobie_Irkutsk_Izd-vo_IRNITU_2015_Ch_1_141
.pdfотраслях промышленности в виде гарантированного ресурса, который изготовитель гарантирует потребителю.
Гамма-процентный ресурс – суммарная наработка, в течение которой объект не достигнет предельного состояния с вероятностью g, выраженный в процентах.
Средний ресурс – математическое ожидание ресурса.
Гамма-процентный срок службы – календарная продолжительность эксплуатации, в течение которой объект не достигает предельного состояния с вероятностью g, выраженной в процентах.
Средний срок службы – математическое ожидание срока службы.
Показатели долговечности отсчитывают от ввода в эксплуатацию до окончательного снятия с эксплуатации.
Эти показатели определяются как корни tg уравнения:
(1.1)
где F(t) – функция распределения наработки до отказа (ресурса, срока службы). В частности, гамма-процентную наработку до отказа tg определяют из уравнения
,
где р(t) – вероятность безотказной работы.
Как видно из формулы (1) гамма-процентные показатели равны квантилям соответствующих распределений. Если вероятности, отвечающие этим квантилям, выражают в процентах, то для показателей безотказности обычно задают значения 90; 95; 99; 99,5 % и т. д.
Тогда вероятность возникновения отказа на отрезке [0; tg] будет составлять 0,10; 0,05; 0,01; 0,005 и т. д. Задаваемые значения g для критических отказов должны быть весьма близки к 100 %, чтобы сделать критические отказы практически невозможными событиями. Для прогнозирования потребности в запасных частях, ремонтных мощностях, а также для расчета пополнения и обновления парков машин, приборов и установок могут потребоваться гамма-процентные показатели при более низких значениях g, например, при g = 50 %, что приближенно соответствует средним значениям.
Статистические оценки для гамма-процентных показателей могут быть получены на основе статистических оценок либо непосредственно, либо после аппроксимации эмпирических функций подходящими аналогичными распределениями. Необходимо иметь в виду, что экстраполирование эмпирических результатов за пределы продолжительности испытаний (наблюдений) без привлечения дополнительной информации о физической природе отказа может привести к значительным ошибкам.

Средний ресурс, средний срок службы равны математическим ожиданиям соответствующих случайных величин наработки до отказа ресурса, срока службы.
Среднюю наработку до отказа Т1 вычисляют по формуле:
, (1.2)
где F(t) – функция распределения наработки до отказа;
f(t) – плотность распределения наработки до отказа.
Т1 может быть выражена через вероятность безотказной работы:
, (1.3)
Статистическая оценка для средней наработки до отказа определяется по формуле:
(1.4)
где N – число работоспособных объектов при t = 0;
tj – наработка до первого отказа каждого из объектов.
Показатели безотказности
Вероятность безотказной работы – вероятность того, что в пределах заданной наработки отказ объекта не возникнет.
Вероятность безотказной работы определяется в предположении, что в начальный момент времени (момент начала исчисления наработки) объект находится в работоспособном состоянии. Обозначим через t время или суммарную наработку объекта (в дальнейшем для краткости называем просто наработкой). Возникновение первого отказа – случайное событие, а наработка t от начального момента возникновения этого события – случайная величина. Вероятность безотказной работы р(t) объекта в интервале от 0 до t включительно определяют как:
p(t) = p( ; t), (1.5)
Здесь р(..) – вероятность события, заключенного в скобках. Вероятность безотказной работы р(t) является функцией наработки t. Обычно эту функцию предполагают непрерывной и дифференцируемой.

Если способность объекта выполнять заданные функции характеризуется одним параметром n, то вместо (1.5) имеем формулу:
, (1.6)
где n и n00 – предельные условия работоспособности значения параметров (эти значения, вообще, могут изменяться во времени)
Вероятность безотказной работы р(t) связана с функцией распределения F(t) и плотностью распределения f(t) наработки до отказа:
F(t) = 1 – p(t); , (1.7)
Наряду с понятием вероятность безотказной работы часто используют понятие «вероятность отказа», которое определяется следующим образом. Это вероятность того, что объект откажет хотя бы одни раз в течение заданной наработки, будучи работоспособным в начальный момент времени. Вероятность отказа на отрезке от 0 до t определяют по формуле:
Q(t) = 1 – p(t) = F(t), (1.8) |
|
|
Точечные статистические оценки для вероятности безотказной работы |
от 0 |
|
до t и для функции распределения наработок до отказа |
даются формулами: |
(1.9)
где N – число объектов, работоспособных в начальный момент времени;
n(t) – число объектов, отказавших на отрезке от 0 до t.
Для получения достоверных оценок объем выборки N должен быть достаточно велик.
Определение безотказной работы в соответствии с формулами (1.5) и (1.6) относится к объектам, которые должны функционировать в течение некоторого конечного отрезка времени. Для объектов одноразового (дискретного) применения вероятность безотказной работы определяют как вероятность того, что при срабатывании объекта отказ не возникает.
Гамма-процентная наработка до отказа – наработка, в течение которой отказ объекта не возникает с вероятностью g, выраженное в процентах.
Средняя наработка до отказа – математическое ожидание наработки объекта до первого отказа.
Средняя наработка на отказ – отношение наработки восстанавливаемого объекта к математическому ожиданию числа его отказов в течение этой наработки.
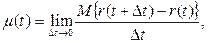
Суть и содержание и формула для расчета этих параметров уже рассмотрены ранее.
Интенсивность отказов – показатель надежности невосстанавливаемых изделий, условная плотность, вероятности возникновения отказа объекта при условии, что до рассматриваемого момента времени отказ не возник.
Интенсивность отказов определяют по формуле:
(1.10)
Для высоконадежных систем p(t) » 1, так что интенсивности отказов приближенно равна плотности распределения наработки до отказа.
Статистическая оценка для интенсивности отказов имеет вид:
(1.11)
где использованы те же обозначения, что и в формуле (1.9).
Параметр потока отказов – параметр надежности восстанавливаемых объектов, равный отношению математического ожидания числа отказов восстанавливаемого объекта за достаточно малую наработку к значению этой наработки.
Параметр потока отказов m(t) определяют по формуле:
(1.12)
где Dt – малый отрезок наработки;
r(t) – число отказов, наступивших от начального момента времени до достижения наработки t. Разность r(t + Dt) – r(t) представляет собой число отказов на отрезке Dt.
Наряду с параметром потока отказов в расчетах и обработке экспериментальных данных часто используют осредненный параметр потока отказов.
(1.13)
По сравнению с формулой (12) здесь рассматривается число отказов за конечный отрезок [t1, t2], причем t1 £ t £ t2. Если поток отказов стационарный, то параметры, определяемые по формуле (1.12) и (1.13), от t не зависят.
Статистическую оценку для параметра потока отказов m(t) определяют по формуле:
(1.14)
которая по структуре аналогична формуле (1.13). Для стационарных потоков можно применять формулу:
(1.15)
где – оценка для средней наработки на отказ.
Показатели ремонтнопригодности и сохраняемости
Вероятность восстановления – вероятность того, что время восстановления работоспособного состояния объекта не превысит заданное значение.
Гамма-процентное время восстановления – время, в течение которого восстановление работоспособного объекта будет осуществлено с вероятностью g, выраженной в процентах.
Среднее время восстановления – математическое ожидание времени восстановления работоспособного состояния объекта после отказа. Иначе, среднее время вынужденного нерегламентированного простоя, вызванного отысканием и устранением одного отказа.
Интенсивность восстановления – условная плотность вероятности восстановления работоспособного состояния объекта, определяемая для рассматриваемого момента времени при условии, что до этого момента восстановление не было завершено.
Средняя трудоемкость восстановления – математическое ожидание трудоемкости восстановления объекта после отказа.
Гамма-процентный срок сохраняемости – срок сохраняемости, достигаемой объектом с заданной вероятностью g, выраженной в процентах.
Средний срок сохраняемости – математическое ожидание срока сохраняемости.
Комплексные показатели надежности.
Показателем, определяющим долговечность системы, объекта, машины, может служить коэффициент технического использования.
Коэффициент технического использования – отношение математического ожидания суммарного времени пребывания объекта в работоспособном состоянии за некоторый период эксплуатации к математическому ожиданию
суммарного времени пребывания объекта в работоспособном состоянии и всех простоев для ремонта и технического обслуживания:
Коэффициент технического использования, взятый за период между плановыми ремонтами и техническим обслуживанием, называется коэффициентом готовности, который оценивает непредусмотренные остановки машины и что плановые ремонты и мероприятия по техническому обслуживанию не полностью выполняют свою роль.
Коэффициент готовности – вероятность того, что объект окажется в работоспособном состоянии в произвольный момент времени, кроме планируемых периодов, в течение которых применение объекта по назначению не предусматривается. Физический смысл коэффициента готовности – это вероятность того, что в прогнозируемый момент времени изделие будет исправно, т. е. оно не будет находиться во внеплановом ремонте.
Коэффициент оперативной готовности – вероятность того, что объект окажется в работоспособном состоянии в произвольный момент времени, кроме планируемых периодов, в течение которых применение объекта по назначению не предусматривается, и, начиная с этого момента, будет работать безотказно в течение заданного интервала времени.
Классификация показателей. В зависимости от способа получения показатели подразделяют на расчетные, получаемые расчетными методами;
экспериментальные, определяемые по данным испытаний; эксплуатационные,
получаемые по данным эксплуатации.
В зависимости от области использования различают показатели надежности нормативные и оценочные.
Нормативными называют показатели надежности, регламентированные в нормативно-технической или конструкторской документации.
К оценочным относят фактические значения показателей надежности опытных образцов и серийной продукции, получаемые по результатам испытаний или эксплуатации.
По надежности их элементов
Классификация технических систем
Технологическая система представляет собой совокупность взаимосвязанных средств технологического оснащения, предметов производства исполнителей для выполнения в регламентированных условиях производства заданных технологических процессов или операций.
К предметам производства относятся: материал, заготовки, полуфабрикаты и изделия, находящиеся в соответствии с выполняемым технологическим процессом в стадии хранения, транспортирования, формообразования, обработки, сборки, ремонта, контроля и испытаний.
К регламентированным условиям производства относятся регулярность поступления предметов производства, параметры энергоснабжения, параметры окружающей среды и другие.
Технологические системы (ТС) являются частью производственной системы
и, как любая другая система, имеют свою структуру и функционируют в определенных условиях.
Состав и структура технологической системы, условия производства, режим работы регламентируются конструкторской и другой технической документацией. Изменение этой документации приводит к соответствующему изменению технологической системы.
Все технологические системы можно разделить на четыре иерархических уровня:
•технологические системы операций;
•технологические системы процессов;
•технологические системы производственных подразделений;
•технологические системы предприятий.
Технологическая система операции обеспечивает выполнение одной заданной технологической операции.
Технологические системы процесса включают в себя в качестве подсистемы совокупность технологических операций, относящиеся к одному методу (обработки, формообразования, сборки или контроля) и к одному наименованию изготовляемой продукции. При наличии автоматизированной системы управления технологическим процессом (АСУТП) ее технические средства входят в состав технологической системы этого процесса.
Технологическая система производственного подразделения состоит из технологических систем процессов и/или операций, функционирующих в рамках данного подразделения.
Технологическая система предприятия состоит из технологических систем его производственных подразделений.
Различают следующие виды технологических систем:
•последовательная технологическая система – технологическая система, все подсистемы которой последовательно выполняют различные части заданного технологического процесса;
•параллельная технологическая система – технологическая система,
подсистемы которой параллельно выполняют заданный технологический процесс на заданную технологическую операцию;
•комбинированная технологическая система – технологическая система,
структуру которой может быть представлена в виде объединения последовательных и параллельных систем более низкого уровня;
•технологическая система с жесткой связью – технологическая система, в
которой отказ хотя бы одной подсистемы вызывает немедленное прекращение функционирования технологической системы в целом;
•технологическая система с нежесткой связью подсистем – технологическая система, в которой отказ одной из подсистем не вызывает немедленного прекращения функционирования технологической системы в целом.
По уровню автоматизации различают:
•механизированная технологическая система – ТС, средства технологического оснащения которой состоят из механизированно-ручных и механизированных технических устройств;
•автоматизированная технологическая система – ТС, средства технологического оснащения которой состоят из автоматизированно-ручных и автоматизированных устройств;
•автоматическая технологическая система – ТС, средства технологического оснащения которой состоят из автоматических устройств.
По уровню специализации ТС классифицируют:
•специальная технологическая система – ТС для изготовления или ремонта изделия одного наименования и типоразмера;
•специализированная технологическая система – ТС для изготовления или ремонта группы изделий с общими конструктивными и технологическими признаками;
•универсальная технологическая система – ТС для изготовления или ремонта изделий с различными конструктивными и технологическим признаками.
Исполнитель в технологической системе – человек, осуществляющий в технологической системе трудовую деятельность по непосредственному изменению и/или определению состояния предметов производства, техническому обслуживанию или ремонту средств технологического оснащения.
Технологические системы состоят из подсистем и элементов.
Подсистемы технологической системы – ТС, выделяемая по функциональному или структурному признаку из технологических систем более высокого уровня.
Элемент технологической системы – часть ТС, условно принимаемая неделимой на данной стадии ее анализа. Примерами элементов ТС являются машина, приспособление, инструмент.
Технологические системы могут находиться в работоспособном и неработоспособном состояниях.
В технологических системах могут происходить функциональные и параметрические отказы.
Функциональный отказ проявляется в полном или частичном прекращении ее функционирования. Примером частичного прекращения функционирования может служить поломка одного из инструментов при обработке деталей на автоматической линии. При этом может продолжаться выпуск продукции, но без обработки соответствующих поверхностей деталей. К функциональным отказам следует относить и факты превышения сроков запланированных перерывов в работе, т. е. превышение регламентированного времени смены инструмента, установки, заготовки (партии заготовок), заданных перерывов на отдых обслуживающего персонала.
Параметрический отказ технологической системы выражается в выходе параметров функционирования отдельных ее элементов за допустимые пределы. Например, выход значений показателей качества деталей за поле допуска на обработку, снижение ритма выпуска ниже заданного уровня, нерегламентированное изменение режимов обработки, превышение материальных и трудовых затрат, недопустимое загрязнение окружающей среды, причиной которого является процесс функционирования рассматриваемой системы.
Основными показателями надежности технологических систем являются
установленный ресурс, установленный срок службы, вероятность безотказной работы ТС по параметрам продукции, техническая наработка технологического комплекса до подладки, коэффициент использования технологической системы. Эти показатели аналогичны ранее рассмотренным.
В настоящее время в связи с увеличением сложности технических систем, многообразием и ответственностью решаемых задач проблема обеспечения надежности решается на основе разработки и внедрения программ обеспечения надежности (ПОН) и стандартизации в области надежности.
Расчеты надежности – расчеты, предназначенные для определения количественных показателей надежности. Они проводятся на различных этапах разработки, изготовления и эксплуатации объектов.
На этапе проектирования расчет надежности производится с целью прогнозирования (предсказания) ожидаемой надежности проектируемой системы. Такое прогнозирование необходимо для обоснования предполагаемого проекта, а также для решения организационно-технических вопросов:
–выбора оптимального варианта структуры объекта;
–способа резервирования элементов;
–глубины и методов контроля;

–количества запасных элементов;
–периодичности профилактики.
На этапе испытаний и эксплуатации расчеты надежности проводятся для оценки количественных показателей надежности. Такие расчеты носят, как правило, характер констатации. Результаты расчетов в этом случае показывают, какой надежностью обладали объекты, прошедшие испытания или используемые в некоторых определенных условиях эксплуатации. На основании этих расчетов разрабатываются меры по повышению надежности, определяются слабые места объекта, даются оценки его надежности и влияния на нее отдельных факторов.
Многочисленные цели расчетов привели к большому их разнообразию. На рис. 1.3 изображены основные виды расчетов.
Рис. 1.3. Классификация расчетов надежности
Элементный расчет – определение показателей надежности объекта, обусловленных надежностью его комплектующих частей (элементов). В результате такого расчета оценивается техническое состояние объекта (вероятность того, что объект будет находиться в работоспособном состоянии, средняя наработка на отказ и т. п.).
Расчет функциональной надежности – определение показателей надежности выполнения заданных функций (например, вероятность того, что система подачи топлива в двигатели будет работать заданное время, в заданных режимах эксплуатации с сохранением всех необходимых параметров топливообеспечения). Поскольку такие показатели зависят от ряда действующих факторов, то, как правило, расчет функциональной надежности более сложен, чем элементный расчет.
Выбирая на рис. 1.3 варианты перемещений по пути, указанному стрелками, могут быть получены новые виды расчета.
Выбор того или иного вида расчета надежности определяется заданием на расчет надежности. На основании задания и последующего изучения работы устройства (по его техническому описанию) составляется алгоритм расчета надежности, т. е. последовательность этапов расчета и расчетные формулы.