
75 группа 2 вариант / Режимы роботы и эксплуатации ТЭС / КУ / Учебное пособие
.pdfнизме. Второй тягодутьевой механизм может быть выведен в резерв, что практикуется при пусках мощных котлов, или в ремонт. В последнем варианте механизм отглушается ремонтными шиберами.
Для регулирования расходов первичного и вторичного воздуха, а также равномерности раздачи воздуха по горелкам в схеме газовоздушного тракта котла устанавливаются запорно-регулирующие шибера:
на общих коробах горячего воздуха;
на воздуховодах подвода воздуха к каждой горелке;
на отводах воздуха и газа в пылесистему.
Производительность тягодутьевых механизмов может изменяться за счет изменения степени открытия направляющих аппаратов (так называемое качественное регулирование). Применение двухскоростных электродвигателей для привода тягодутьевых механизмов позволяет экономить электроэнергию на собственные нужды при пониженных нагрузках котла.
Система газовоздушного тракта котла оборудуется контрольноизмерительными приборами; блокировками; защитами; сигнализацией: звуковой, световой, аварийной, предупредительной.
Всхеме контролируются: токовая загрузка приводных электродвигателей механизмов; давление воздуха на напоре вентиляторов, в общем коробе, перед горелками, в систему пылеприготовления; давление газов в верхней части топки, за основными поверхностями нагрева, "до" и "после" золоуловителей, "до" и "после" дымососов; температура воздуха и газов по всему тракту; содержание кислорода в продуктах сгорания, покидающих топку или в верхней части конвективной шахты. Показания контролируемых параметров выводятся на щит управления котлом и на местные щиты управления оборудованием (РВП, электрофильтры и т.д.).
Всистеме газовоздушного тракта котла вводят блокировки, действующие
на:
закрытие направляющих аппаратов при отключении тягодутьевых механизмов;
перевод приводного электродвигателя тягодутьевого механизма на повышенную скорость, в случае полного открытия его направляющего аппарата;
отключение дутьевого вентилятора, в случае аварийного отключения дымососа, и перевод оставшихся в работе тягодутьевых механизмов на повышенную скорость;
перевод оставшегося в работе дутьевого вентилятора на повышенную скорость, в случае аварийного отключения одного из них;
запрет включения дутьевых вентиляторов, если не включен дымосос, и др.
Для исключения недопустимых режимов работы оборудования системы газовоздушного тракта вводят защиты, действующие на аварийный останов котла, в случае:
недопустимого понижения давления воздуха перед горелками;
аварийного отключения всех дымососов или дутьевых вентиляторов;
недопустимого повышения разряжения в верху топки;
Обо всех недопустимых отклонениях контролируемых параметров, а также о работе защит и блокировок эксплуатационный персонал оповещается
110
звуковой и световой сигнализацией, выведенной на соответствующие рабочие места обслуживающего персонала.
Нормативно-техническими документами регламентируются следующие основные требования к системам газовоздушных трактов котлов:
устройство газоходов должно исключать возможность образования взрывоопасного скопления газов, а также обеспечивать необходимые условия для очистки газоходов от отложений продуктов сгорания;
при расчете конструкций газоплотных котлов необходимо учитывать случаи разряжения и кратковременного резкого повышения давления в топке и газоходах (при "хлопках");
газовоздушный тракт котлов с камерным сжиганием топлива обязательно снабжается взрывными предохранительными устройствами;
перед растопкой и после останова котла топка и газоходы, включая рециркуляционные, должны быть провентилированы дымососами, дутьевыми вентиляторами и дымососами рециркуляции при открытых шиберах газовоздушного тракта не менее 10 мин. С расходом воздуха не менее 25 % от номинального;
при эксплуатации котлов в работу включаются, как правило, все тягодутьевые механизмы. Длительная работа при отключении части тягодутьевых машин допускается при условии обеспечения равномерного газовоздушного и теплового режимов по сторонам котла;
при эксплуатации котлов температура воздуха, поступающего в воздухоподогреватель, поддерживается в соответствии с требованиями ПТЭ;
контроль плотности ограждающих поверхностей котла и газоходов осуществляется путем осмотра и определения присосов воздуха, величина
которых регламентируется ПТЭ.
Котел должен быть немедленно остановлен и отключен при следующих отклонениях в работе системы газовоздушного тракта:
при недопустимых отклонениях контролируемых параметров системы и отказе в работе защиты, когда аварийное отклонение параметра подтверждается прямыми и косвенными признаками;
при взрыве в топке или загорании горючих отложений в газоходах и зо-
лоулавливающей установке.
Котел должен быть остановлен по распоряжению технического руководителя ТЭС, в случае прекращения работы золоуловителей на пылеугольном котле.
2.3.7. Схема регулирования температуры перегретого пара
Исходя из условий надежности и экономичности работы основного оборудования ТЭС температура перегретого (первичного и вторичного) пара за котлом должна поддерживаться в заданном диапазоне. В настоящее время для паротурбинных установок, работающих на сверхкритических параметрах, номинальная температура перегретого пара за котлом принята на уровне 545 С; перед турбиной 540 С.
На ТЭС с поперечными связями, в зависимости от величины потери давления в паропроводах от котла до турбины, номинальная температура перегретого пара за котлом может устанавливаться на 5-10 С выше, чем перед
111
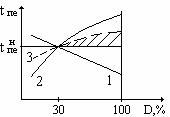
турбиной. В то же время при надежной работе автоматики, хорошем техническом состоянии оборудования, высокой квалификации оперативного персонала номинальная температура острого пара перед турбиной может быть установлена (администрацией станции) на уровне 560 С.
На этих же уровнях поддерживается и номинальная температура вторичного пара.
Вреальных условиях эксплуатации режим работы котла никогда не протекает стабильно; разнообразные причины непрерывно вызывают изменения тех или иных начальных факторов, и даже при равномерной нагрузке котла температура перегретого пара может меняться. В этой связи устанавливаются допустимые ее отклонения от номинального значения.
Всоответствии с требованиями ГОСТ 3619-82 для котлов среднего давления (Рпе = 4 МПа) колебания перегретого пара от номинального значения не должны превышать +10 С, –15 С, а для котлов, работающих при давлении более 9 МПа, + 5 С, –10 С.
Необходимость регулирования температуры перегретого пара вызвана тем, что она при эксплуатации барабанных котлов находится в сложной зависимости от режимных факторов и конструктивных характеристик котла.
К режимным факторам, влияющим в целом на температуру перегретого пара, следует отнести: паропроизводительность котла; величину избытков воздуха в топке; разрежение (давление) в топке; вид сжигаемого топлива или соотношение сжигаемых топлив; качество подготовки топлива (тонина помола; влажность; однородность состава и т.п.); температуру питательной воды; положение ядра факела в топке; температуру горячего воздуха; величину рециркуляции дымовых газов. Значение указанных режимных факторов регламентируются режимными картами, составленными по результатам испытаний конкретных котлов, которыми руководствуется оперативный персонал при управлении котлом.
Конструктивные характеристики закладываются при проектировании и изготовлении котла, а также могут быть изменены в процессе реконструкции котельного агрегата. Оперативный персонал практически не может воздействовать на конструктивные характеристики котла, что и отличает их от режимных факторов.
Основной конструктивной характеристикой, влияющей на температуру пе-
|
регретого пара, является так называемая |
||||
|
регулировочная |
характеристика |
па- |
||
|
роперегревателя |
(рис. 2.18). |
Она |
||
|
характеризует изменения температуры пе- |
||||
|
регретого |
пара |
в |
радиационных, |
|
|
конвективных и радиационно-конвективных |
||||
|
поверхностях нагрева пароперегревателя в |
||||
|
зависимости от паровой нагрузки котла. Из |
||||
Рис. 2.18. Регулировочная харак- |
рис. 2.18 следует, что с увеличением паро- |
||||
производительности котла (Д) температура |
|||||
теристика пароперегревателя |
перегретого пара (tпе) в радиационной сту- |
||||
|
пени пароперегревателя |
снижается |
(кри- |
вая 1), а в конвективной – растет (кривая 2). Это объясняется тем, что определяющими факторами радиационного теплообмена являются температура и
112
излучающая способность факела, которые слабо зависят от нагрузки котла, и поэтому увеличение расхода пара через радиационную ступень пароперегревателя приводит к снижению его температуры. Теплообмен в конвективной части перегревателя зависит от скорости газов и температурного напора, которые растут интенсивнее расхода пара при увеличении нагрузки котла. В результате количество тепла на килограмм пара и, следовательно, температура пара в конвективной части пароперегревателя с ростом паропроизводительности котла растут.
При соответствующем подборе размеров поверхностей радиационных и конвективных частей пароперегревателя можно добиться того, что температура перегретого пара в широком диапазоне нагрузок будет оставаться постоянной. В практических условиях радиационно-конвективная поверхность пароперегревателей барабанных котлов выбирается такой, чтобы в регулировочном диапазоне нагрузок от 30 до 100 % обеспечивался незначительный рост температуры перегретого пара (кривая 3) выше номинальной (tпен), в целях расширения регулировочного диапазона и обеспечения номинальных параметров пара при некотором ухудшении технического состояния поверхностей нагрева котла (загрязнение поверхности нагрева; вырезка части змеевиков при ремонте и т.п.) и неблагоприятных изменениях режимных факторов (влажности топлива; температуры питательной воды и горячего воздуха и т. п.). И в этих случаях для снятия излишнего перегрева пара и поддержания температуры на заданном уровне используют схемы регулирования, которыми оборудуются котельные установки.
Различают три способа регулирования температуры перегретого пара: паровой, при котором воздействуют на паровую среду преимущественно путем охлаждения пара в пароохладителях; газовый, при котором изменяют тепловосприятие пароперегревателя со стороны газов; комбинированный, при котором используются несколько способов регулирования.
Паровое регулирование в тракте пара высокого давления получило широкое применение и осуществляется главным образом в двух вариантах: с использованием для охлаждения пара впрыскивающих и поверхностных пароохладителей. Для промежуточного перегрева пара этот способ регулирования имеет ограниченное применение (к примеру, в качестве аварийных впрысков), по причине снижения экономичности работы паротурбинной установки.
Надежность и экономичность схемы парового регулирования температуры перегретого пара во многом определяется местом установки и типом применяемого пароохладителя или пароохладителей. В принципе пароохладитель может быть установлен за пароперегревателем, в рассечку между ступенями пароперегревателя, либо на стороне насыщенного пара.
При установке пароохладителя на выходе из пароперегревателя обеспечивается надежное поддержание заданной температуры острого пара перед турбиной, но сам пароперегреватель в его выходной части остается незащищенным от высокой температуры, и потому для регулирования температуры перегретого пара котлов неблочных ТЭС такой метод практически не применяется. На котлах блочных паротурбинных установок устанавливаются впрыскивающие пароохладители на выходе из пароперегревателя и используются
113
для регулирования температуры острого пара перед турбиной только в режимах пуска энергоблока.
Установка пароохладителей на стороне насыщенного пара приводит к наибольшей инерционности регулирования. Причем в этом случае могут использоваться только поверхностные пароохладители, поэтому в настоящее время такие схемы применяются только в котлоагрегатах малой мощности.
Для современных энергетических котлов наиболее рациональной и распространенной схемой регулирования температуры перегретого пара являются схемы с установкой пароохладителей в рассечку, т. е. между ступенями пароперегревателя. Причем для расширения диапазона регулирования температуры устанавливают два или три пароохладителя.
Использование таких схем обеспечивает защиту металла пароперегревателя от пережога и уменьшает инерционность системы регулирования.
Однако следует отметить, что использование в этих схемах поверхностных пароохладителей влечет за собой ряд эксплуатационных ограничений и трудностей, к примеру:
необходим регулярный контроль расхода и температуры охлаждающей воды до и после пароохладителя, т. к. снижение или даже кратковременное прекращение расхода может привести к испарению воды, оставшейся в трубках, и последующее возобновление расхода охлаждающей среды через поверхностный пароохладитель будет сопровождаться гидроударами, способными нарушить гидравлическую плотность пароохладителей;
нарушение плотности пароохладителя приводит к попаданию питательной воды в перегретый пар, что вызывает увеличение его солесодержания;
сравнительно большая инертность усложняет настройку автоматики ре-
гулирования температуры пара и др.
В связи с этим в современных мощных котлоагрегатах высокого и сверхкритического давлений, в схемах регулирования температуры перегретого пара, широко используются впрыскивающие пароохладители вследствие своей простоты и незначительной инерционности регулирования. При этом расход воды для регулирования при впрыскивающих пароохладителях примерно в три раза меньше, чем при поверхностных. Впрыскивающие пароохладители обеспечивают широкий диапазон регулирования температуры пара примерно до 100-130 С.
Надежная работа впрыскивающих пароохладителей определяется двумя основными условиями: во-первых, испарением впрыснутой воды до распределения пара по змеевикам пароперегревателя, во-вторых, высоким качеством впрыскиваемой воды. Первое условие обеспечивается тем, что впрыск охлаждающей среды осуществляют в паропровод или коллектор, имеющий достаточную длину. В этом случае впрыск осуществляется через специальное сопло, а паропровод (или коллектор) снабжается внутри защитной рубашкой для предохранения его стенок от резких колебаний температур при попадании на них капель воды, что может вызвать появление трещин. Второе условие обеспечивается тем, что для впрыскивания используют так называемый собственный конденсат, полученный в результате конденсации части насыщенного пара барабана котла. Конденсация насыщенного пара происходит
114
вконденсаторе (конденсационной установке), представляющем собой поверхностный пароводяной теплообменник, установленный выше барабана котла (примерно на 1,5 м), что создает свободный слив избыточного конденсата из сборного бачка (конденсатосборника) в барабан. Вследствие этого в конденсаторе отсутствует уровень воды во всех режимах и обеспечивается постоянный температурный режим конденсаторных трубок. В качестве охлажденной среды используется питательная вода. По питательной воде конденсатор подключается до экономайзера или в рассечку между ступенями экономайзера.
На рис. 2.19 представлена принципиальная схема регулирования температуры перегретого пара с впрыскивающими пароохладителями. Схема типична для барабанных котлов, работающих на сверхвысоких параметрах. Полученный в конденсационной установке, в результате конденсации части насыщенного пара, конденсат поступает в общий коллектор, откуда распределяется на соответствующие пароохладители. Располагаемый напор для впрыска определяется сопротивлением первой ступени пароперегревателя, а количество подаваемого на впрыски конденсата регулируется индивидуальными регуляторами впрыска (РВ-1,2,3).
При регулировании температуры острого пара необходимо максимально использовать первый по ходу пара впрыск и минимально – второй и третий. В схеме предусмотрен также аварийный впрыск питательной воды в первую ступень регулирования температуры перегретого пара.
Поскольку жесткость питательной воды барабанного котла значительно превышает жесткость перегретого пара, то случаи использования аварийного впрыска должны быть четко регламентированы местными инструкциями, так как даже незначительная добавка питательной воды в перегретый пар через впрыскивающий пароохладитель резко ухудшает его качество. Как правило, аварийным впрыском пользуются в режимах пуска котла, когда возникает необходимость защиты металла пароперегревателя от пережога, а собственного конденсата недостаточно по причине малого расхода питательной воды через конденсационную установку. В режимах нормальной эксплуатации котла аварийный впрыск может быть использован в порядке исключения настолько и до тех пор, пока качество перегретого пара будет удовлетворять требованиям ПТЭ. Причем все случаи использования аварийного впрыска должны быть согласованы с персоналом химического цеха и зафиксированы
воперативной документации. Для обеспечения плавного регулирования температуры перегретого пара на линии аварийного впрыска монтируется так называемый узел разгрузки. Он обеспечивает необходимое давление питательной воды перед регулятором температуры за счет сброса части этой воды по линии рециркуляции в деаэратор.
На рис. 2.20 изображена принципиальная схема регулирования температуры перегретого пара с поверхностным пароохладителем. Подобные схемы используются в основном на энергетических котлах с рабочим давлением до 9 МПа включительно. Регулирование перегрева пара в данных схемах производится изменением расхода питательной воды через поверхностный пароохладитель. Данная схема отличается от подобных ей тем, что в ней используется специальный регулирующий клапан РТП, который, при постоянном расходе питательной воды в барабан котла, обеспечивает изменение расхо-
115
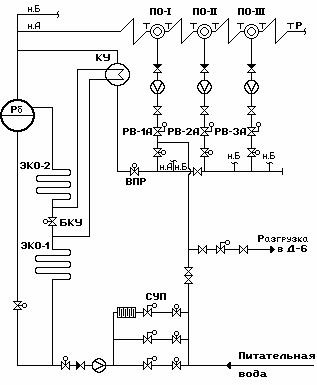
Рис. 2.19. Принципиальная схема регулирования температуры перегретого пара с впрыскивающими пароохладителями барабанного котла сверхвысокого давления:
н.А, н.Б – трубопроводы по “нитке” А и Б; ПО-I,II,III – пароохладители впрыскивающие I,II,III ступени;
РВ-1А,2А,3А – регуляторы впрысков I,II,III ступеней по нитке А; ВПР, БКУ – запорная арматура на коллекторе впрысков и байпасе конденсационной установки; СУП – сниженный узел питания котла; КУ – конденсационная установка
116
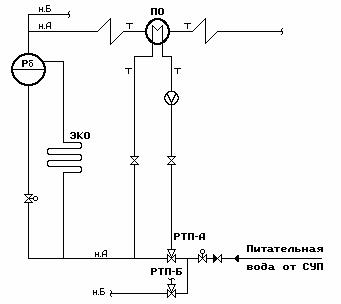
Рис. 2.20. Принципиальная схема регулирования температуры перегретого пара с поверхностным пароохладителем:
ПО – пароохладитель поверхностного типа; н.А, н.Б – трубопроводы по “нитке” А и Б; РТП-А – регулятор температуры пара на нитке А
да охлаждающей среды через поверхностный пароохладитель. То есть конструкция клапана позволяет осуществлять независимое друг от друга регулирование температуры перегретого пара и уровня воды в барабане котла.
Газовое регулирование применяется для поддержания требуемой температуры пара промежуточного перегрева, но оно связано с изменением топочного режима и температур газов по тракту, поэтому влияет на температуру пара высокого давления. Газовое регулирование вызывает дополнительные расходы энергии на тягу и увеличение потерь теплоты с уходящими газами и усложняет эксплуатацию.
Газовое регулирование может осуществляться за счет рециркуляции дымовых газов, байпасирования части потока продуктов сгорания помимо поверхности нагрева пароперегревателя и реже изменением положения факела в топочной камере.
Наибольшее распространение имеет способ регулирования температуры пара с использованием рециркуляции дымовых газов. Данный способ используется преимущественно на газомазутных котлах для регулирования как температуры острого пара, так и температуры пара промежуточного перегрева. В таких случаях обеспечивают небольшую (5-10 %) рециркуляцию газов даже
117
при полной нагрузке, в целях ослабления прямой отдачи в топочной камере и защиты экранных поверхностей нагрева от чрезмерно высоких тепловых нагрузок.
Отбор дымовых газов на рециркуляцию может осуществляться после экономайзера, в этом случае система регулирования получается компактной и малозатратной.
Введение инертных газов может осуществляться вниз или в верх топки, или непосредственно в конвективный пароперегреватель. Рециркуляция дымовых газов может использоваться как метод борьбы со шлакованием фестона, а также для подавления окислов азота. Поэтому во всех случаях место отбора и ввода дымовых газов выбирается на основе технико-экономических расчетов с учетом всех поставленных задач.
Поскольку абсолютное давление в топке выше, чем в месте отбора газов на рециркуляцию, их подача в топку возможна только специальными дымососами рециркуляции газов. В связи с этим возрастают общие затраты энергии на перекачку газов. Кроме того, возврат части газов в топку увеличивает общий объем газов в тракте от топки до места отбора газов и сопротивление этого тракта, отчего дополнительно увеличиваются затраты энергии на тягу в основных дымососах.
Наличие рециркуляции газов приводит также к некоторому повышению температуры уходящих газов и, следовательно, потерь теплоты с ними, при этом несколько возрастает расход топлива по сравнению с режимом без рециркуляции.
Другие способы газового регулирования имеют ограниченное применение и поэтому подробно не рассматриваются.
Из приведенного ниже анализа различных методов регулирования температур перегретого пара следует, что каждый из них в той или иной мере отрицательно влияет на экономичность котлоаграгата.
Комбинированный способ регулирования позволяет наиболее успеш-
но обеспечить требуемые характеристики системы регулирования температуры перегретого пара: диапазон регулирования, безынерционность, гибкость, простоту управления и т. п. В качестве примера комбинированного регулирования может служить схема с установкой поверхностного пароохладителя на стороне насыщенного пара и впрыскивающего пароохладителя, расположенного в рассечку пароперегревателя. Первый предупреждает чрезмерный перегрев пара до впрыска и обеспечивает защиту металла пароперегревателя от пережога, второй, установленный ближе к выходу пара, обеспечивает малую инерцию регулирования (25-30 с против 2-3 мин) и стабильность поддержания температуры перегретого пара на заданном уровне. Суммарный диапазон регулирования становится при этом шире, и достигается гибкое регулирование.
Другим примером может служить комбинированное регулирование поворотными горелками и пароохладителем.
В некоторых случаях рециркуляцию газов также сочетают с впрысками. Применяются и другие способы комбинированного регулирования температуры перегретого пара.
Для обеспечения надежной и экономичной работы котельных агрегатов системы регулирования температуры перегретого пара оборудуются средст-
118
вами контроля параметров, дистанционного управления, автоматического регулирования и защит.
Эксплуатация современных котельных установок не допускается без автоматизации систем регулирования температуры пара. При этом должны автоматически обеспечиваться избирательность работы регуляторов температуры, требуемая нечувствительность и регулировочный диапазон.
Основную запорную арматуру и оборудование (ДРГ) систем регулирования температуры перегретого пара задействуют в системе автоматической защиты котла, которая автоматически обеспечивает отключение системы регулирования температуры пара при аварийных отключениях котла.
2.3.8. Сведения о технологических схемах обеспечивающих водно-химический режим барабанных котлов
При эксплуатации современных котельных агрегатов, в особенности высокого и сверхвысокого давлений, большое значение в повышении надежности и экономичности работы котлов оказывает состояние технологических схем, обеспечивающих водный режим котлов, и правильная организация воднохимического режима работы котла.
Нарушение водного режима может вызвать серьезную аварию котельного агрегата, а повышенное содержание примесей в паре привести к снижению экономичности и надежности работы турбины.
Организацию и контроль водно-химического режима (ВХР) работы котла осуществляет непосредственно оперативный персонал химического цеха путем систематического отбора и анализа проб котловой, продувочной, питательной и добавочной воды, а также насыщенного пара.
Показатели водно-химического режима котла регламентируются ПТЭ и поддерживаются на заданном уровне за счет ввода химических реагентов (гидразина, аммиака, фосфатов) в соответствующие тракты паротурбинной установки, а также за счет организации периодических и непрерывных продувок котловой воды.
Таким образом, для организации водно-химического режима котельная установка оборудуется следующими технологическими схемами:
1) схемой отбора проб воды, пара и конденсата для ручного и автоматического контроля параметров. Согласно ПТЭ рабочая среда из пробоотборных точек должна быть охлаждена до температуры 20…40 С и иметь соответствующий расход. Для этих целей от мест отборов проб монтируются специальные трубопроводы из нержавеющей стали диаметром 12 – 14 мм, которые выводятся на так называемые пробоотборные корыта, оборудованные специальными водяными холодильниками для охлаждения проб и устанавливаемые на основных площадках обслуживания котлов или в специальных экспресс-лабораториях;
2) узлами приготовления и дозирования реагентов (гидразина, аммиака, фосфатов), которые включают: расходные мерники, оборудованные указательными стеклами и трубопроводами подачи обессоленной (очищенной) воды для приготовления рабочих концентраций реагентов; насосы-дозаторы, обеспечивающие подачу реагента в распределительный коллектор, в необходимом количестве и с соответствующим напором; распределительный кол-
119