
2013_Book_Industrial_engineering_technologies_Valetov_Pompeev
.pdf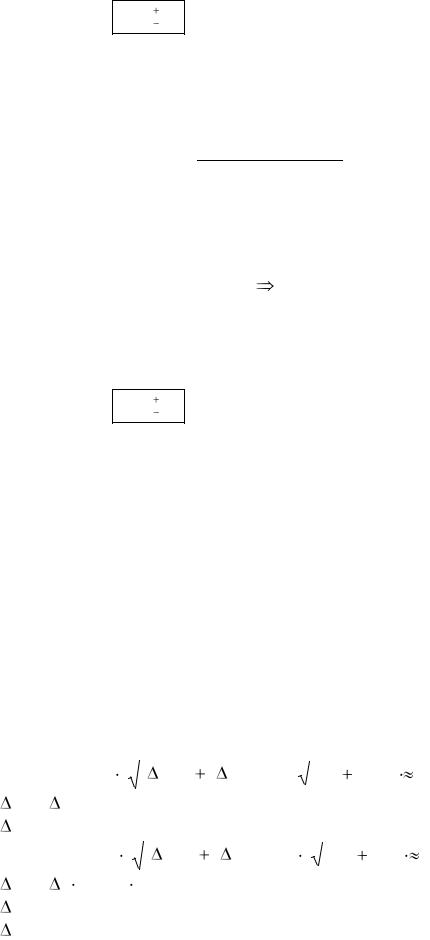
191
Т н2 = Т2min + | ei | = 11,68 + | -0.4 | = 12,08 мм.
1,0
Примем Т2 = 12,1 0,4 мм.
Z ф |
= Т |
– Т = 11,7 – 11,2 = 0,5 мм. |
2min |
2min |
5max |
Z ф2 max |
= Т2max – Т5min = 13,1 – 10,93 = 2,17 мм. |
|
|
|
Z2 = 0,5+1,67 мм. |
Z1 = Т1 – Т5 – Т4 .
Z 1расчmin = (RZ + h)i-1 +ei max = 0,16 + 0,2 + 0,12 = 0,48 мм.
RZ i-1 = 160 мкм = 0,16 мм [9, т.1, с.186, табл.12]. hi-1 = 200 мкм = 0,2 мм [9, т.1, с.186, табл.12].
ei max = e осу |
= 120 мкм = 0,12 мм [9, т.1, с.42, табл.13]. |
|
Z1min = Т1min – Т5max – Т4max |
Т1min = Z1min + Т5max + Т4max = |
|
|
= 0,48 + 11,2 + 19,53 = 31,21 мм. |
|
Размер |
Т1 выполняется |
в заготовке с отклонениями |
es = +1,0 мм и ei = -0,4 мм. Тогда
Т 1н = Т1min + | ei | = 31,25 + | -0.4 | = 31,65 мм.
1,0
Примем Т1 = 31,7 0,4 мм.
Z 1фmin = Т1min – Т5max – Т4max = 31,3 – 11,2 – 19,53 = 0,57 мм.
Z1фmax = Т1max – Т5min – Т4min = 32,7 – 10,93 + 19,2 = 2,57 мм.
Z1 = 0,57+2,0 мм.
Результаты расчета линейных технологических размеров заносим в операционные эскизы, представленные на рис. 7.10.
Используя размерную схему биений (рис. 7.9), проведем расчеты биений элементов в исходной заготовке относительно ее идеальной оси, биений базовых, обрабатываемых и обработанных поверхностей относительно баз системы «Обработка» и между собой, а также определим неравномерности припусков элементов вращения.
Операция 005. Биения элементов 41, 11, 21 и 32 (см. рис. 7.9) в исходной заготовке относительно ее идеальной оси определим по формуле (7.26).
Б 0541 = 2 |
|
|
|
|
|
|
|
|
|
|
|
( кор )2 |
( см )2 = 2 |
0,52 |
0,632 |
|
|
1,608 мм. |
|||||
кор = |
экс = 0,5 мм [9, т.1, с.186, табл.17]. |
|
|
|
|
||||||
см = 0,63 мм [9, т.1, с.186, табл.17]. |
|
|
|
|
|
|
|||||
|
Б 1105 = 2 |
|
|
|
|
|
|
|
|
|
|
|
|
( кор )2 |
( см )2 = 2 |
0,42 |
0,52 |
|
1,28 мм. |
||||
кор = |
к l = 20 |
20 = 400 мкм = 0,4 мм. |
|
|
|
|
|||||
к = 20 |
мкм/мм [9, т.1, с.187, табл.19]; |
|
l = 20 мм. |
|
см = 0,5 мм [9, т.1, с.187, табл.20].
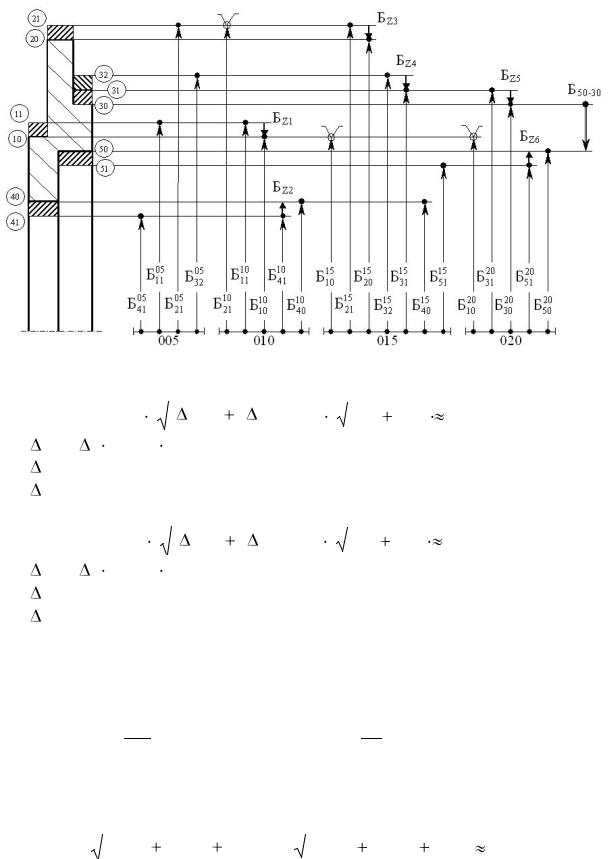
192
|
|
|
|
|
|
Рис.7.9. Схема биений |
|
|
|
|
|||
Б 0521 |
|
|
|
|
|
|
|
|
|
|
|
||
= 2 |
( кор )2 |
( см )2 = 2 |
0,22 |
0,52 |
|
|
1,078 мм. |
||||||
кор = |
к |
|
l = 20 |
10 = 200 мкм = 0,2 мм. |
|
|
|
|
|||||
к = 20 |
мкм/мм [9, т.1, с.187, табл.19]; |
l = 10 мм. |
|
||||||||||
см = 0,5 мм [9, т.1, с.187, табл.20]. |
|
|
|
|
|
||||||||
Б 30 |
25 |
|
|
|
|
|
|
|
|
|
|
||
= 2 |
|
( кор )2 |
( см)2 = 2 |
0,82 |
0,52 |
|
|
1,887 мм. |
|||||
кор = |
к |
|
l = 20 |
40 = 800 мкм = 0,8 мм. |
|
|
|
|
|||||
к = 20 |
мкм/мм [9, т.1, с.187, табл.19]; |
l = 40 мм. |
см = 0,5 мм [9, т.1, с.187, табл.20].
Операция 010. Биение базового элемента 21 (рис. 7.9) относительно базы системы «Обработка» (оси шпинделя) определим по формуле (7.27) с учетом установки в трехкулачковый патрон нормальной точности
Б 1021 = 2 а1
ITб
(1 + 0,02
l) = 2
0,17
1,6
(1 + 0,02
5) = 0,473 мм.
Биение обрабатываемого элемента 11 (рис. 7.9) относительно базы системы «Обработка» (оси шпинделя) на операции 010 определим, составив уравнение размерной цепи с использованием формулы (7.31)
Б 10 |
|
|
|
|
|
|
|
|
= |
(Б10 )2 |
(Б05 )2 |
(Б05 )2 |
= 0,4732 |
1,0782 1,282 |
1,739 мм. |
||
11 |
|
21 |
21 |
11 |
|
|
|
|
Биение обработанного элемента 10 (рис. 7.9) относительно базы системы «Обработка» (оси шпинделя) на операции 010 определим по формуле (7.32), учитывая, что, согласно [9], коэффициент уточнения после получистового точения равен 0,05
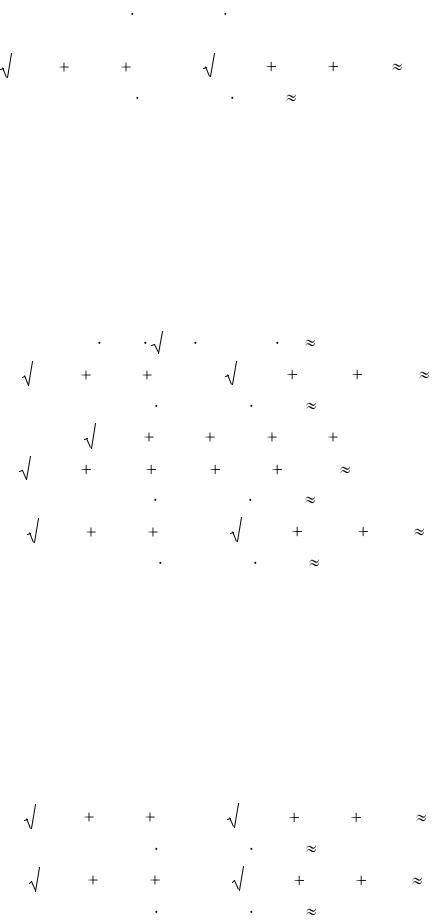
193
|
Б 10 |
= К |
Б 10 |
= 0,05 |
1,739 = 0,087 мм. |
||||
10 |
у |
11 |
|
|
|
|
|
|
|
Аналогично |
|
|
|
|
|
|
|
|
|
|
|
|
|
|
|
|
|||
Б 1041 = (Б2110 )2 (Б2105 )2 |
(Б4105 )2 |
|
= 0,4732 1,0782 1,6082 1,993 мм. |
||||||
|
Б 10 |
= К |
Б 10 |
|
= 0,06 |
1,993 0,12 мм. |
|||
40 |
у |
41 |
|
|
|
|
|
|
Операция 015. Аналогично определяем биения базового, обрабатываемых и обработанных элементов относительно базы системы «Обработка» (рис. 7.9). При этом биение элемента 10 определяем с учетом установки в трехкулачковый патрон повышенной точности. Биения обрабатываемых элементов 21, 32 и элемента 40, который является заготовкой для элемента 51, определяем, составляя уравнения размерных цепей. Биения обработанных элементов 20, 31 и 51 определяем с учетом, что, согласно [9], коэффициент уточнения
после получистового точения равен 0,05. |
|
|
|
|
|
|
|
|||||||||||||
|
|
Б 1015 = 2 |
|
|
|
|
|
|
|
|
|
|
|
|
|
|
|
|||
|
|
0,11 |
|
0,3 |
|
(1 + 0,02 |
0) |
0,121 мм. |
|
|
||||||||||
Б 1521 = |
|
|
|
|
|
|
|
|
|
|
|
|
|
|
||||||
|
(Б1015 )2 |
(Б1010 )2 |
|
(Б2110 )2 = |
0,1212 |
0,0872 |
0,4732 0,496 мм. |
|||||||||||||
|
|
Б 15 = К |
у |
|
Б |
15 |
= 0,05 0,496 0,025 мм. |
|
|
|||||||||||
|
|
|
20 |
|
|
21 |
|
|
|
|
|
|
|
|
|
|
|
|||
|
Б 1352 = |
|
|
|
|
|
|
|
|
|
|
|||||||||
|
|
(Б1015 )2 |
|
(Б1010 )2 |
(Б2110 )2 |
(Б2105 )2 (Б3205 )2 = |
|
|
||||||||||||
|
|
|
|
|
|
|
|
|
|
|||||||||||
= |
0,1212 |
0,0872 |
|
0,4732 |
1,0782 |
1,8872 |
|
2,229 |
мм. |
|
Б 1531 = Ку |
Б 1352 |
= 0,05 |
2,229 |
0,112 мм. |
|||
|
|
|
|
|
|
|
||
Б 1450 = (Б1015 )2 (Б1010 )2 |
(Б4010 )2 = 0,1212 |
0,0872 0,122 0,191 мм. |
||||||
|
Б 1551 = Ку |
Б 1450 |
= 0,05 |
0,191 |
0,01 мм. |
Операция 020. Аналогично определяем биения базового, обрабатываемых и обработанных элементов относительно базы системы «Обработка» (рис. 7.9). Биение элемента 10 определяем с учетом установки в трехкулачковый патрон повышенной точности. Биения обрабатываемых элементов 31 и 51, определяем, составляя уравнения размерных цепей. Биения обработанных элементов 30 и 50 определяем с учетом, что, согласно [9], коэффициент уточнения после чистового точения равен 0,04.
|
|
|
|
|
Б 1200 |
= Б 1015 |
|
= 0,121 мм. |
|
|
|
||||||
Б 3210 |
|
|
|
|
|
|
|
|
|
|
|
|
|
|
|||
= |
(Б1020 )2 |
(Б1015 )2 |
(Б3115 )2 |
= |
0,1212 |
0,1212 |
0,1122 |
0,205 мм. |
|||||||||
|
|
|
Б 3200 |
= Ку |
Б 3210 |
= 0,04 |
0,205 |
0,008 мм. |
|
||||||||
Б 5210 |
|
|
|
|
|
|
|
|
|
|
|
|
|
||||
= |
|
(Б1020 )2 |
(Б1015 )2 |
(Б5115 )2 |
= |
0,1212 |
0,1212 |
0,012 |
|
0,171 мм. |
|||||||
|
|
|
Б 5200 |
= Ку |
Б 5210 |
= 0,04 |
0,171 |
0,007 мм. |
|
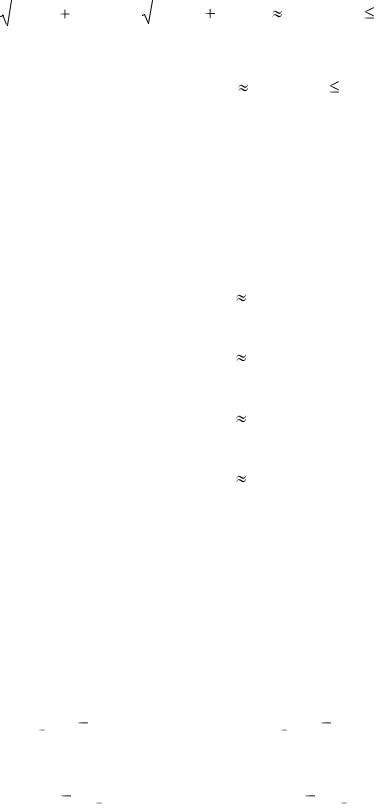
194
Проверим технические требования, заданные конструктором, составив уравнение размерной цепи
|
|
|
|
|
|
Б50-30 = (Б5020 )2 |
(Б3020 )2 = 0,0072 0,0082 0,011 мм 0,05 мм. |
||||
При наихудшем варианте, когда вектора направлены в разные |
|||||
стороны, |
|
|
|
|
|
Б50-30 = Б 5200 |
+ Б 3200 = 0,007 + 0,008 0,015 мм 0,05 мм. |
Таким образом, требования чертежа выполнены.
Рассчитаем неравномерности припусков элементов вращения, используя формулу (7.33).
Б |
= 2е |
= Б10 |
– Б 10 |
= 1,739 – 0,087 = 1,652 мм; |
|
Z1 |
Z1 |
11 |
10 |
|
|
|
еZ1 = БZ1 / 2 = 1,652 / 2 = 0,826 мм. |
||||
Б |
= 2е |
= Б 10 |
– Б 10 |
= 1,993 – 0,12 = 1,873 мм; |
|
Z2 |
Z2 |
41 |
40 |
|
|
|
еZ2 = БZ2 / 2 = 1,873 / 2 |
0,937 мм. |
|||
Б |
= 2е |
= Б15 |
– Б 15 |
= 0,496 – 0,025 = 0,471 мм; |
|
Z3 |
Z3 |
21 |
20 |
|
|
|
еZ3 = БZ3 / 2 = 0,471 / 2 |
0,236 мм. |
|||
БZ4 = 2еZ4 = Б 1352 |
– Б 1531 |
= 2,229 – 0,112 = 2,117 мм; |
|||
|
еZ4 = БZ4 / 2 = 2,117 / 2 |
1,059 мм. |
|||
БZ5 = 2еZ5 = Б 3210 |
– Б 3200 |
= 0,205 – 0,008 = 0,197 мм; |
|||
|
еZ5 = БZ5 / 2 = 0,197 / 2 |
0,099 мм. |
|||
БZ6 = 2еZ6 = Б 5210 |
– Б 5200 |
= 0,171 – 0,007 = 0,164 мм; |
|||
|
еZ6 = БZ6 / 2 = 0,164 / 2 = 0,082 мм. |
Расчет промежуточных диаметральных размеров проводим таблично [7], используя формулы (7.10), (7.34) и (7.35). Результаты расчета сводим в табл. 7.8.
Расчет фактических припусков на обработку проводим также таблично (см. табл. 7.8), используя формулы
– для вала
Z iфmin |
= |
D(i 1) min Di max |
; |
Z iфmax |
= |
D(i 1) max Di min |
; |
|
2 |
2 |
|||||||
|
|
|
|
|
|
– для отверстия
Z iфmin |
= |
Di min D(i 1) max |
; |
Z iфmax |
= |
Di max D(i 1) min |
. |
|
2 |
2 |
|||||||
|
|
|
|
|
|

195
|
|
|
|
|
|
|
|
|
|
Таблица 7.8 |
|
|
|
Расчет промежуточных диаметральных размеров |
|
|
|||||||
|
|
|
|
|
|
|
|
|
|
|
|
Маршрут |
№ |
|
Диаметр, мм |
От- |
Составляющие |
расч |
Фактический |
||||
|
припуска, мм |
припуск, мм |
|||||||||
обработки |
опе- |
|
|
|
кло- |
Zi min , |
|||||
элемента |
рац. |
|
Расч. |
Окр. |
нен. |
RZ(i-1) |
h(i-1) |
emax i |
мм |
Zi min |
Zi max |
|
|
||||||||||
|
|
|
|
|
|
|
|
|
|
|
|
Ø80h8(-0,046) |
|
|
|
|
|
|
|
0,099*3 |
|
|
|
Чист. точ. (h8) |
020 |
|
80 |
80 |
-0,046 |
0,025 |
0,025 |
0,149 |
0,19 |
0,323 |
|
|
|
|
|
|
|
|
|
|
|
|
|
П/чист. точ.(h11) |
015 |
|
80,518 |
80,6 |
-0,22 |
0,1 |
0,1 |
0,053*2 |
0,253 |
0,265 |
0,81 |
|
|
|
|
|
|
|
|
|
|
|
|
Черн. точ. (h14) |
015 |
|
81,976 |
82,0 |
-0,87 |
0,16 |
0,2 |
1,059*1 |
1,419 |
1,45 |
2,635 |
|
|
|
|
|
|
|
|
|
|
|
|
Штамповка ГКМ |
005 |
|
85,338 |
85,4 |
+1,0 |
- |
- |
- |
- |
- |
- |
|
-0,5 |
||||||||||
|
|
|
|
|
|
|
|
|
|
|
|
|
|
|
|
|
|
|
|
|
|
|
|
Ø80h12(-0,3) |
|
|
|
|
|
|
|
0,042*5 |
|
|
|
П/чист. точ.(h12) |
010 |
|
80 |
80 |
-0,3 |
0,1 |
0,1 |
0,242 |
0,265 |
0,85 |
|
|
|
|
|
|
|
|
|
|
|
|
|
Черн. точ. (h14) |
010 |
|
81,354 |
81,4 |
-0,87 |
0,16 |
0,2 |
0,826*4 |
1,186 |
1,2 |
2,385 |
|
|
|
|
|
|
|
|
|
|
|
|
Штамповка ГКМ |
005 |
|
84,272 |
84,3 |
+1,0 |
- |
- |
- |
- |
- |
- |
|
-0,5 |
||||||||||
|
|
|
|
|
|
|
|
|
|
|
|
|
|
|
|
|
|
|
|
|
|
|
|
Ø120h12(-0,35) |
|
|
|
|
|
|
|
0,012*7 |
|
|
|
П/чист. точ.(h12) |
015 |
|
120 |
120 |
-0,35 |
0,1 |
0,1 |
0,212 |
0,25 |
0,925 |
|
|
|
|
|
|
|
|
|
|
|
|
|
Черн. точ. (h14) |
015 |
|
121,424 |
121,5 |
-1,0 |
0,16 |
0,2 |
0,236*6 |
0,596 |
0,6 |
1,9 |
|
|
|
|
|
|
|
|
|
|
|
|
Штамповка ГКМ |
005 |
|
123,292 |
123,3 |
+1,0 |
- |
- |
- |
- |
- |
- |
|
-0,6 |
||||||||||
|
|
|
|
|
|
|
|
|
|
|
|
|
|
|
|
|
|
|
|
|
|
|
|
Ø50Н14(+0,62) |
|
|
|
|
|
|
|
|
|
|
|
Черн. раст.(Н14) |
010 |
|
50 |
50 |
+0,62 |
0,16 |
0,2 |
0,937*8 |
1,297 |
1,3 |
2,31 |
|
|
|
|
|
|
|
|
|
|
|
|
Штамповка ГКМ |
005 |
|
47,006 |
47 |
+0,4 |
- |
- |
- |
- |
- |
- |
|
-1,0 |
||||||||||
|
|
|
|
|
|
|
|
|
|
|
|
|
|
|
|
|
|
|
|
|
|
|
|
Ø60Н9(+0,074) |
|
|
|
|
|
|
|
|
|
|
|
Чист. раст.(Н9) |
020 |
|
60 |
60 |
+0,074 |
0,03 |
0,035 |
0,082*10 |
0,147 |
0,15 |
0,337 |
|
|
|
|
|
|
|
|
|
|
|
|
П/чист.раст.(h12) |
015 |
|
59,406 |
59,4 |
+0,3 |
0,1 |
0,1 |
0,004*9 |
0,204 |
0,23 |
0,75 |
|
|
|
|
|
|
|
|
|
|
|
|
Черн. раст.(h14) |
015 |
|
58,252 |
58,2 |
+0,74 |
- |
- |
- |
- |
- |
- |
|
|
|
|
|
|
|
|
|
|
|
|
Примечание к табл. 7.8
е *max1 |
i = eZ4 = 1,059 мм. |
|
е *max2 |
i = е *max1 |
i Ку = 1,059 0,05 0,053 мм. |
е *max3 |
i = eZ5 = 0,099 мм. |
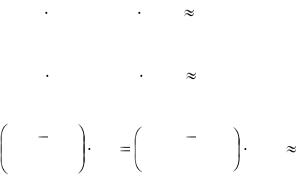
|
|
|
|
|
|
|
|
196 |
|
|
е *max4 |
i |
= eZ1 = 0,826 мм. |
|
|
|
|
||||
е *max5 |
i |
= е *max4 |
i |
Ку = 0,826 |
0,05 |
0,042 мм. |
||||
е *max6 |
i = eZ3 = 0,236 мм. |
|
|
|
|
|||||
е *max7 |
i |
= е *max6 |
i |
Ку = 0,236 |
0,05 |
0,012 мм. |
||||
е *max8 |
i |
= eZ2 = 0,937 мм. |
|
|
|
|
||||
е *max9 |
|
= |
Б1540 |
Б1551 |
Ку |
0,191 |
0,01 |
0,04 0,004 мм. |
||
i |
|
|
2 |
2 |
|
|
||||
|
|
|
|
|
|
|
|
|
||
е *max10 |
i |
= eZ6 = 0,082 мм. |
|
|
|
|
||||
По результатам размерного анализа ТП окончательно |
||||||||||
оформляются |
|
операционные эскизы, |
которые представлены на |
|||||||
рис. 7.10. |
|
|
|
|
|
|
|
|
|
|
Таким образом, на примере детали типа тело вращения рассмотрено проектирование ТСЗ и проведение размерного анализа ТП ее изготовления.

197
005 Штамповка ГКМ |
RZ320 |
+1,0
12,1–0,4
|
|
|
|
|
|
|
+1,0 –0,6 |
+1,0 –0,5 |
+0,4 –1,0 |
|
|
|
+1,0 –0,5 |
||
|
|||||||
84,3 |
47 |
|
|
|
|
85,4 |
123,3 |
|
|
|
|
|
|
|
|
|
|
|
|
|
|
|
|
|
|
|
|
|
|
|
|
31,7 |
+1,0 |
|
–0,4 |
|
|
|
41,7 |
+0,4 |
|
–1,0 |
1.Штамповка повышенной точности.
2.Неуказанные штамповочные уклоны – 2°,
радиусы – 2 мм.
020 Токарная с ЧПУ 16К20Ф3 |
|
|
10 |
|||
10–0,15 |
5+0,12 |
|
|
|
|
|
1 |
|
|
2 |
|
|
|
|
1 |
45° |
3 |
|
|
|
|
5 |
|
|
|
А |
|
|
|
|
|
|
||
|
2,5 |
|
4 |
5 |
|
6 |
2 |
5 |
|
|
|
|
|
|
|
|
|
|
||
|
|
|
|
|
|
|
0,05 А |
5 |
+0,074 |
0,3– |
|
|
0,046– |
|
|
|
|
|
|
|
|
2,5 |
60 |
76 |
|
80 |
|
|
|
|
|
|
|
|
3 |
|
2 |
45° |
|
|
|
|
|
45 |
0,125 |
7 |
||
|
50,4–0,3 |
|
|
|
|
8 |
9 |
|
|
|
|
|
|
|
|
|
|
|
|
010 Токарная с ЧПУ 16К20Ф3 |
10 |
025 Сверлильная с ЧПУ 2Р135РФ2 10 |
|
3 |
1 |
2 |
|
|
|
|
|
|
|
|
4 отв. |
|
12+0,43 |
|
|
|
|
1 |
2 |
|
|
|
|
|
|
|
|
|
|
|
+0,62 |
–0,3 |
|
–0,12 |
|
|
|
|
50 |
80 |
|
3,85 |
|
|
|
|
|
|
|
|
3 |
|
|
|
|
|
|
|
2 |
|
|
11,2–0,27 |
19,2+0,33 |
|
|
4 отв. |
8 |
+0,36 |
|
4 |
|
|
3 |
|
3 |
||
|
|
|
|
|
|||
|
|
|
|
|
|
|
015 Токарная с ЧПУ 16К20Ф3
10 |
1 |
2 |
|
|
|
|
5 |
|
2 |
|
|
|
+0,3 |
–0,22 |
5 |
59,4 |
80,6 |
|
|
|
20 |
100 0,175 |
|
3 |
|
4 |
120–0,35
|
|
3 |
6 |
6–0,18 |
10,5–0,18 |
|
||
|
|
4 |
51,2–0,46
5
Рис. 4.13. Операционные эскизы
Рис.7.10. Операционные эскизы
технологического процесса
технологического процесса
изготовления детали "Фланец"
изготовления детали «Фланец»
Пример для корпусной детали рассмотрен в Приложении Б.
198
Глава 8. Проектирование сборочных техпроцессов
Сборка – образование разъѐмных и неразъѐмных соединений составных частей деталей или изделий. Она осуществляется: соединением; запрессовкой; свинчиванием; сваркой; пайкой; клѐпкой; склеиванием.
Сборку классифицируют по следующим признакам.
–По объему работ различают общую (объект сборки – изделие в целом) и узловую (объект сборки – составная часть изделия) сборку. В единичном и мелкосерийном производстве бόльшая часть работ выполняется по общей сборке. В массовом и крупносерийном производстве объемы узловой и общей сборки приблизительно равны, а иногда объем узловой сборки больше общей.
–По стадиям процесса различают предварительную (сборка изделия, которое в последующем подлежит разборке) и промежуточную (выполняется для сборки изделий с целью их дальнейшей обработки) сборку, сборку под сварку и окончательную сборку (не предусматривается последующая разборка при изготовлении).
–По методу образования соединений различают слесарную сборку, монтаж, электромонтаж, сварку, пайку, клепку и склеивание.
Вид организационной формы сборки зависит от типа и условий производства.
1. Непоточная сборка 1.1. Непоточная стационарная сборка – характеризуется тем, что
весь процесс выполняется на одной сборочной позиции (стенде). Она проходит в двух формах:
1.1.1. Непоточная стационарная сборка без расчленения сборочных работ. Вся сборка проводится одной бригадой рабочих с начала и до конца.
Достоинства:
–положение базовой детали неизменно, поэтому достигается высокая точность;
–применяются универсальные приспособления и инструмент, что сокращает время и стоимость подготовки производства.
Недостатки:
–большой цикл сборки, т.к. все операции выполняются последовательно;
–высокая квалификация рабочих;
–требуется для сборки длительное время занимать производственную площадь.
Применяется: в единичном и мелкосерийном производстве; экспериментальных и ремонтных цехах.
1.1.2. Непоточная стационарная сборка с расчленением сборочных работ. Предполагает дифференциацию на узловую и общую сборку,
199
которые делаются в одно время. Достоинства:
–сокращается цикл процесса;
–сокращается трудоѐмкость операций за счет: а) специализации рабочих мест; б) специализации рабочих – сборщиков; в) лучшей организации труда;
–снижается потребность в дефицитной рабочей силе сборщиков высокой квалификации;
–рационально используются помещения цехов;
–сокращается себестоимость работ.
1.2. Непоточная подвижная сборка – характеризуется последовательным перемещением собираемого изделия от одной позиции к другой. Перемещение может быть свободным и принудительным.
Свободное – рабочий, закончив свою операцию, с помощью механизирующих средств или вручную перемещает собираемую сборочную единицу на следующую рабочую позицию.
Принудительное – объект сборки передвигается при помощи конвейера или тележек, замкнутых ведомой цепью. Сборка может выполняться как на конвейере, так и возле него. Организация подвижной сборки возможна только на основе расчленения сборочных работ. Продолжительность выполнения операций в этом случае зависит от квалификации рабочего и от интенсивности его труда. Такая форма применяется в серийном производстве.
2. Поточная сборка.
Поточная сборка характеризуется тем, что при построении ТП отдельные операции выполняются за одинаковый промежуток времени (такт) или за промежуток времени кратный такту. Синхронизация операций обеспечивается путем уменьшения числа переходов или механизацией их, или включением дополнительных работ, когда трудоемкость меньше такта.
Поточная сборка может быть организована со свободным и принудительным ритмом. В первом случае изделие передается на операцию по мере выполнения предыдущей операции. Во втором случае момент передачи определяется сигналом или скоростью конвейера (сигнал звуковой или световой).
Межоперационные перемещения изделия осуществляются: вручную, тележками; наклонным лотком или рольгангом; распределительным конвейером; конвейером с периодическим перемещением; непрерывно движущимся конвейером.
Достоинства:
–Сокращается цикл производственного процесса;
–Уменьшаются межоперационные заделы;
–Повышается специализация рабочих;
200
–Повышается степень автоматизации операций;
–Снижается трудоемкость на 30…35%.
Условие обеспечения организации поточной сборки – обеспечение высокой взаимозаменяемости собираемых узлов и отдельных деталей, входящих в поточную сборку. В случае необходимости использования пригоночных работ они должны осуществляться за пределами потока на операциях предварительной сборки, а пригнанные детали узлы должны подаваться на поточную сборку в окончательно скомплектованном и проконтролированном виде. Эта операционная форма сборки используется в массовом и крупносерийном производстве, рентабельна при большом объеме выпуска изделий.
2.1.Поточная стационарная сборка – характеризуется тем, что собираемое изделие находится на месте, а передвигается рабочий или бригада (например, по сигналу). Такая форма применяется при сборке крупных и громоздких изделий.
Преимущества:
– наименьшие затраты на организацию сборочного процесса;
– равномерный выпуск продукции;
– высокая производительность. Используется в серийном производстве.
2.2.Поточная подвижная сборка – характеризуется применением непрерывно или периодически перемещающегося конвейера.
Преимущества:
– работа с тактом;
– возможность почти полного совмещения времени, затрачиваемого на транспортировку изделия со временем сборки.
Одним из основных направлений совершенствования технологии сборки является проведение широкой механизации сборочных работ путем применения разнообразных сборочных приспособлений и стендов, а также механизированных универсальных, унифицированных и специальных сборочных инструментов.
Ручной механизированный инструмент, используемый при сборке узлов и изделий, классифицируют по следующим признакам.
–По роду используемой энергии различают гидравлический, пневматический и электрический инструмент. Пневматический инструмент может быть с вращательным движением рабочего органа (сверлильные машины, гайковерты, механические отвертки), ударного (молотки) и давящего (поддержки) действия. Электрический инструмент может быть с вращательным (электродрели, резьбонарезатели, шлифовальные машинки, одно- и многошпиндельные электрогайко- и шпильковерты, полировальные машинки) или поступательным движением рабочего органа (электронапильники и электромолотки).
–По назначению различают инструмент для резки материалов и
подготовки кромок под сварку, сверлильный, резьбонарезной,