
2344 - Пустов Ю.А., Ракоч А.Г. - Коррозионностойкие и жаростойкие материалы - 2013
.pdf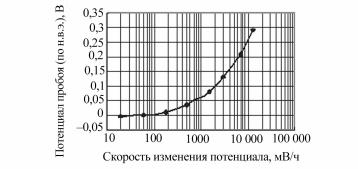
Рис. 4.4. Зависимость потенциала питтингообразования стали Х18Н10 от скорости изменения потенциала в растворе 0,1 моль/л NaCI (н.в.э. – нормальный водородный электрод)
В гальваностатическом методе (ступенчатое изменение плотности тока поляризации) анодная поляризация сплавов, склонных к пит- тинговой коррозии (ПК), наблюдается лишь до определенных значе- ний потенциалов, по достижении которых наступает активирование отдельных участков поверхности (рис. 4.2, б). Чем положительнее потенциал активирования, тем более устойчиво пассивное состояние по отношению к воздействию ионов Cl−.
При определении склонности сплава к питтинговой коррозии снятием кривых заряжения на электрод накладывается определенная плотность тока (для коррозионностойких сталей 2…5 мкА/см2), а потенциал запи- сывается автоматически. По виду кривой судят о склонности к питтинго- вой коррозии. Если на кривой заряжения обнаруживаются колебания по- тенциала, на таком сплаве будут образовываться питтинги (рис. 4.3, кри- вая 1). При этом, чем меньше число колебаний в единицу времени и меньше предел изменения этих колебаний, тем выше устойчивость в питтингу. На кривых заряжения сплавов, не склонных к питтинговой коррозии, флуктуации потенциала отсутствуют (рис. 4.3, кривая 2).
Для ускоренного электрохимического определения сравнительной стойкости сталей и сплавов против ПК используется основной прак- тический электрохимический критерий – противопиттинговый базис или базис питтингостойкости:
Епк = Епо – Екор, |
(4.2) |
где Епо – минимальный гальваностатический потенциал питтинго- образования; Екор – потенциал коррозии.
101
При необходимости определяют дополнительные критерии:
|
|
|
Eпдк = Епдк − Е |
кор |
; |
Е |
реп |
= Е |
реп |
– Е , |
(4.3) |
|
|
|
|
по |
по |
|
|
|
кор |
|
|||
где Епдк |
и Е |
реп |
– потенциалы питтингообразрования и репассивации |
|||||||||
по |
|
|
|
|
|
|
|
|
|
|
|
|
(защиты), здесь индекс «пдк» – потенциодинамическая кривая. |
||||||||||||
Устойчивость стали против питтинга тем выше, чем больше |
Епк, |
|||||||||||
Епдк и |
Е . |
|
|
|
|
|
|
|
|
|
|
|
по |
реп |
|
|
|
|
|
|
|
|
|
|
|
В зависимости от цели испытаний используют в электрохимиче- ских методах следующие растворы:
1)0,5 моль/л NaCl, температура 25 °С (модель морской воды);
2)0,3 г/л Na2SO4 + 0,4 г/л NaCl, температура 50 °С (модель обо- ротной воды, загрязненной хлорид-ионами).
4.2. Испытания на контактную коррозию
Контактная коррозия исследуется с двумя целями: для изучения защитного действия протекторов или для оценки дополнительных коррозионных потерь, связанных с контактом разнородных металлов. Этот вид коррозии связан главным образом с различием электрохими- ческих характеристик контактирующих металлов или различных уча- стков на одном и том же металле. Скорость контактной коррозии за- висит от плотности гальванического тока, определяемого относитель- но поверхности контактирующих металлов. Поэтому на результаты испытаний будут оказывать влияние геометрические факторы из-за изменения сопротивления электролита и распределения тока.
Наиболее простым методом изучения контактной коррозии являет- ся измерение разности потенциалов в разомкнутой цепи между метал- лами, находящимися в контакте, в исследуемых условиях. Это позво- ляет определить возможное направление контактного тока, но не дает сведений о скорости процесса. Измерение потенциалов разомкнутой цепи, но с применением электродов сравнения, дает также возмож- ность наблюдать изменение потенциала каждого металла, поскольку общая разность потенциалов будет меняться в процессе испытаний.
Для измерений потенциалов обычно применяют потенциометры или электрометры, позволяющие делать измерения без утечки токов на поляризацию электродов. Применяют также мультивольтметры с высоким внутренним сопротивлением, необходимым для исключе- ния возможной утечки тока. Для измерения гальванического тока необходимо использовать амперметры с «нулевым» сопротивлением.
102
Возможно подключение в цепь шунта с достаточно низким сопро- тивлением, по отношению к которому измерения падения напряже- ния I·R могут быть сделаны для расчета величины тока. Этот метод позволяет проводить измерения без размыкания цепи даже в том слу- чае, когда в цепь подключается прибор для измерения тока.
При изучении контактной коррозии разнородных металлов жела- тельно иметь информацию о распределении гальванического тока. Оно зависит от размера, формы и относительного положения контак- тирующих образцов: параллельное расположение в электролите, непо- средственный контакт по определенной линии и т.д. Коррозионное разрушение по линии контакта может быть обнаружено визуально при достаточно длительной экспозиции. Распределение гальваниче- ского тока (в единицах плотности тока) на анодной и катодной состав- ляющих работающей коррозионной системы получают из анализа данных о распределении потенциала в электролите в области контакта образцов. Последнее изучают путем измерения эквипотенциальных линий при перемещении в нескольких фиксированных направлениях электрода сравнения. При изучении контактной коррозии с примене- нием электрических измерений могут быть использованы методы оп- ределения скорости коррозии по потерям массы, описанные ранее.
4.3. Испытания на коррозионное растрескивание
Коррозионное растрескивание (КР) происходит в результате од- новременного воздействия на металл коррозионной среды и прило- женных напряжений. При проведении испытаний на КР стараются воспроизвести условия, встречающиеся на практике: структуру, со- став материала, величину приложенных напряжений и особенности коррозионной среды.
Существует большое количество способов создания напряженно- го состояния испытуемых образцов, однако нет ни одного способа, имеющего преимущества перед остальными. С одной стороны, метод испытаний не должен быть слишком жестким, чтобы вызывать за- браковку годного к эксплуатации материала, с другой, не должен быть слишком мягким, допускающим использование материала, под- вергающегося быстрому коррозионному разрушению.
Методы создания напряженного состояния в испытываемых об- разцах можно подразделить на три группы:
1)постоянная деформация на изгиб;
2)постоянная нагрузка;
3)постоянная скорость деформации.
103
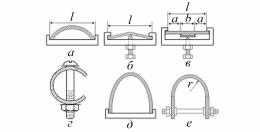
Испытания при постоянной деформации на изгиб. Нагружающие устройства, применяемые при испытаниях на изгиб, просты, дешевы
ихорошо моделируют напряженное состояние, возникающее в реаль- ных конструкциях и приводящее к КР. Изгиб призматической балки является наиболее распространенным способом испытания листовых
ипластинчатых материалов. Способы создания напряженного состоя- ния в образцах различной формы представлены на рис. 4.5.
Рис. 4.5. Способы создания напряжений в образцах при испытаниях на коррозионное растрескивание:
а– двухточечный изгиб; б – трехточечный изгиб;
в– четырехточечный изгиб; г – изгиб кольца (С-образный изгиб);
д, е – изгиб U-образного образца
Пластически деформированные U-образные образцы (рис. 4.5, д, е) предназначены для моделирования сравнительно мягких условий экс- плуатации. Цилиндрические материалы могут быть испытаны на С- образных (рис. 4.5, г) и кольцевых образцах. Первые нагружают путем уменьшения зазора (с помощью болта), вторые – путем увеличения диаметра калиброванной пробки большего диаметра, чем диаметр коль- ца. Максимальные напряжения создаются на внешней поверхности С-образного образца; у кольцевого образца напряжения постоянны по всей периферии.
Расчет максимального напряжения σ (Н/мм2) в зависимости от способа создания напряженного состояния проводится по сле- дующим формулам:
1) двухточечный изгиб (рис. 4.5, а): |
|
|
||
σ = |
4Ehf |
, |
(4.4) |
|
l2 + 4h 2 |
||||
|
|
|
где Е – модуль упругости (модуль Юнга), Н/мм2; h – толщина образца, мм;
104
f – стрела прогиба, мм;
l – расстояние между опорами, мм;
2) трехточечный изгиб (рис. 4.5, б): |
|
|||||||
σ = |
6Еhf |
|
; |
|
(4.5) |
|||
l2 |
||||||||
|
|
|
|
|
|
|||
3) четырехточечный изгиб (рис. 4.5, в): |
|
|||||||
σ = |
|
3Еhf |
|
, |
(4.6) |
|||
|
|
|
||||||
|
(l + 2b)a |
|
||||||
где l, a, b – расстояния между опорами, мм; |
|
|||||||
4) С-образный изгиб (рис. 4.5, г): |
|
|
|
|||||
σ = |
4Ehzδ |
, |
(4.7) |
|||||
|
||||||||
|
|
|
πd 2 |
|
|
|
где z – коэффициент корреляции (0,8 < z < 1), связанный с отношени-
ем d/h (5…100);
δ = dн – d0,
dн, d0 – внешний диаметр нагруженного и ненагруженного образ- ца соответственно, мм;
d – средний диаметр, мм.
Величину деформации С-образных образцов вычисляют по формуле
ε = |
σ d 2 |
π |
|
|
|
|
, |
(4.8) |
|
|
|
4Eh
где σ – приложенное напряжение; d – внешний диаметр образца; h – толщина образца;
Е – модуль упругости.
При выборе способа испытаний на КР необходимо учитывать, что жесткость приспособлений для испытаний при постоянном изгибе может влиять на результаты испытаний вследствие релак- сации напряжений в образце как на начальной стадии нагружения, так и при распространении трещины. Так, при испытании пла- стичных материалов начальная упругая деформация частично пе- реходит в пластическую даже при сохранении постоянной стрелы прогиба на протяжении всего процесса КР. Это связано с тем, что
105
как только трещина начинает расти, напряжения на неразрушен- ной части образца вблизи трещины увеличиваются и достигают значений, соответствующих пределу текучести. Материал в этом месте начинает течь, что сопровождается раскрытием трещины и, как результат, резким падением нагрузки, которое ошибочно можно принять за внезапное механическое разрушение.
Если жесткость устройства, используемого при испытаниях, меньше упругой деформации, то коррозионное растрескивание
внекоторых случаях может затормозиться, особенно тогда, когда заданные начальные напряжения близки к пороговым. Метод ис- пытаний при постоянной деформации является наиболее распро- страненным, однако следует иметь в виду, что его результаты могут быть ошибочными.
Испытания при постоянной нагрузке. Испытания при посто-
янной растягивающей нагрузке имеют преимущества перед дру- гими методами, так как позволяют точно оценивать напряжения
вслучае одноосного нагружения образца. Эти испытания в отли-
чие от испытаний при постоянной изгибающей деформации не сопровождаются релаксацией напряжений. Более того, по- скольку в процессе испытаний за счет образования трещины уменьшается эффективное сечение образца, напряжения посто- янно возрастают. Очевидно, что в этом случае зародившаяся од- нажды трещина не прекратит свой рост, как это часто происхо- дит в испытаниях при постоянной изгибающей деформации при начальных напряжениях, близких к пороговым. Оценкой чувст- вительности материала к КР в этом случае является время до разрушения.
Испытания при постоянной скорости деформации. Сущность мето-
да состоит в том, что образцы деформируют с малой скоростью (растя- жение на изгиб со скоростью около 106 мм/с) в соответствующих сре- дах. Основная задача метода – создание трещин, которые металлогра- фически не отличаются от трещин, возникающих при испытаниях с за- данными нагрузкой и деформацией. Испытания на КР при постоянной скорости деформации относятся к ускоренным, поэтому для получения информации о материале за относительно короткое время ужесточают условия испытаний. С этой целью увеличивают агрессивность среды, температуру и давление, стимулируют коррозионные реакции (потен- циостатическая и гальваностатическая поляризация), изменяют струк- туру сплава (термообработка), усиливают нагружение путем нанесения надреза или предварительного выращивания трещины.
106
В лабораторных испытаниях скорости распространения тре- щин при КР составляют от 10–3 до 10–6 мм/c, поэтому разрушение обычных образцов (толщиной 3…5 мм) следует ожидать через несколько суток. Применение метода деформации с малой скоро- стью, как и предварительное выращивание трещины, способству- ет зарождению трещины КР. Но первый метод является более предпочтительным. Поскольку образец разрушается всегда, не приходится прерывать испытания через некоторый произ- вольно выбранный промежуток времени с целью увеличения же- сткости условий испытаний.
Испытания при постоянной скорости деформации – относительно жесткий вид лабораторных испытаний. Следует учитывать, что эти испытания часто облегчают КР, и оно может проявляться в тех сре- дах, в которых другие способы испытаний не обнаруживают склон- ности материала к коррозионному растрескиванию.
Анализ большого числа экспериментальных данных дает основа- ние полагать, что в зарождении и распространении трещины при КР определяющую роль играют не сами напряжения, а поддержание оп- ределенной скорости деформации.
Для испытаний с постоянной скоростью деформации используют устройства, обеспечивающие различные скорости деформации и об- ладающие необходимой мощностью (например, обычные испыта- тельные машины).
Результаты испытаний оценивают по параметрам пластично- сти или вязкости, таким как относительное сужение поперечного сечения, максимально допустимая нагрузка, скорость роста тре- щины или время до разрушения образца. Однако измерение пла- стичности по изменению площади поперечного сечения и макси- мально допустимой нагрузки не всегда можно провести с доста- точной степенью точности. Легче всего точно измерить время до разрушения, которое находится в простой зависимости от ха- рактеристик пластичности: чем меньше интенсивность КР, тем больше удлинение образца до момента разрушения и, следова- тельно, тем больше время до разрушения.
Растворы для испытаний сплавов на коррозионное растрески-
вание. Количество сред, стимулирующих КР, постоянно растет, однако некоторые растворы вследствие их широкого использова- ния в течение многих лет можно считать наиболее предпочтитель- ными. В табл. 4.1 приведены составы электролитов для испытаний некоторых сплавов на склонность к КР.
107
Таблица 4.1
Составы электролитов для испытаний сплавов на склонность к коррозионному растрескиванию
Материал |
Электролит |
Режим |
ГОСТ на |
|
испытания |
||||
|
|
|
||
|
3%-ный раствор NaCl |
Периодическое |
|
|
|
погружение при 18…25оС |
|
||
Алюминиевые |
3%-ный раствор NaCl + |
Погружение в электролит |
9.019–74; |
|
сплавы |
+ 0,1% H2O2 |
|
ИСО 9591–89 |
|
3%-ный раствор NaCl |
Погружение в электролит |
|||
|
|
|||
|
|
|
|
|
|
3%-ный раствор NaCl |
Распыление в камере |
|
|
|
|
|
|
|
|
|
Периодическое погружение |
|
|
|
|
при 18…25 оС, распыление |
|
|
|
0,001%-ный раствор NaCl; |
в камере (влажность 95…98 %), |
|
|
|
дистиллированная вода |
выдержка при 50 оС в течение |
|
|
Магниевые |
|
6 ч + выдержка при 18…25 оС |
9.019–74 |
|
|
в течение 8 ч |
|||
сплавы |
|
ИСО 9591–89 |
||
|
|
|||
|
3%-ный раствор NaCl |
Распыление в камере |
|
|
|
|
|
|
|
|
3%-ный раствор NaCl |
Периодическое погружение; |
|
|
Коррозионно- |
распыление в камере |
|
||
|
9.903–96 |
|||
стойкие стали |
42%-ный раствор MgCl2 |
Полное погружение |
||
|
||||
|
|
при кипячении |
|
|
|
3%-ный раствор NH4NO3 + |
Полное погружение |
|
|
Низколегиро- |
+ 50…57 % Ca(NO3)2; |
|
||
при кипячении |
|
|||
ванные |
42 %-ный MgCl2 |
9.903–96 |
||
|
||||
|
Периодическое погружение; |
|||
стали |
3%-ный раствор NaCl |
|
||
|
распыление в камере |
|
||
|
|
|
||
|
|
|
|
|
|
3%-ный раствор NaCl; |
|
|
|
Титановые |
CH3OH + 1,5 % HCl + |
|
|
|
+ 1,0 % H2O; |
Погружение в электролит |
9.903–96 |
||
сплавы |
||||
CH3OH + 0,01н. NaCl + |
|
|
||
|
|
|
||
|
+ 0,2 % H2O |
|
|
|
|
20%-ный раствор NH3 + |
|
|
|
|
+ 1 % Cu(OH)2; |
|
|
|
Медные |
5%-ный раствор NaNO2 + |
Погружение в электролит |
9.903–96 |
|
сплавы |
+ 4 % CuSO4·5H2O; |
|||
|
|
|||
|
1%-ный раствор |
|
|
|
|
HgNO3 + 1%HNO3 |
|
|
Примечание. Периодическое погружение проводят по режиму: 10 мин в электролите, 50 мин на воздухе.
108
При проведении испытаний важная роль принадлежит способу приготовления и контролю за состоянием раствора в процессе испы- таний. В частности, использование 42%-ного раствора MgCl2 требует учета гигроскопичности гидрата хлористого магния. Приготовление раствора весовым методом может привести к значительному измене- нию точки его кипения и, следовательно, повлиять на результаты ис- пытаний. Поэтому более надежным с точки зрения получения опреде- ленной точки кипения является добавление воды к гидрату MgCl2.
Заметное влияние на результаты испытаний оказывает рН раствора. Так, при испытании низкоуглеродистых сталей в нитратах было обна- ружено повышение рН в зависимости от объема раствора, площади по- верхности экспонируемого образца и продолжительности испытаний, что приводило при определенных рН к прекращению КР. Обнаружен- ные эффекты могут проявляться в еще большей степени при использо- вании для ускорения КР анодной поляризации, особенно в тех случаях, когда вспомогательный электрод (катод) находится непосредственно в испытательной ячейке. Поэтому для зарождения и поддержания раз- вития трещины требуется локальное изменение рН и границы трещины.
На результаты испытаний на КР может оказывать значительное влияние концентрация кислорода в растворе, которая определяется способом проведения испытаний (полное погружение, переменное погружение, разбрызгивание электролита и т.д.). В этой связи при моделировании режимов испытаний следует по возможности учиты- вать реальные условия эксплуатации материалов.
4.4. Испытания на межкристаллитную коррозию
Межкристаллитная коррозия (МКК) – наиболее опасный вид элек- трохимического разрушения сплавов, поскольку она приводит к ощу- тимой потере прочностных свойств без заметного изменения внешнего вида. МКК наблюдается у хромистых, хромоникелевых сталей, никеле- вых, алюминиевых и других сплавов. Причиной склонности к МКК яв- ляются структурные превращения в области границ зерен, приводящие
кобеднению приграничной области легирующим (пассвирующим) эле- ментом и ее усиленному растворению (анодные участки по отношению
ктелу зерна). Например, при нагреве хромоникелевых сталей при 600…800 оС происходит выделение из твердого раствора сложных кар- бидов Cr23C6 или (Cr,Fe)23C6 и обеднение приграничных участков хро- мом. В связи с этим возникла необходимость в разработке методов ис- пытаний, позволяющих обнаружить склонность сплавов к МКК в зави- симости от их состава и структурного состояния.
109
Сплавы алюминия с медью при неправильной термической обра- ботке также становятся склонными к МКК. Иногда МКК подверга- ются и алюминиймагниевые и алюминийкремниевые сплавы, но скорость их разрушения значительно ниже.
Валюминиевых сплавах при искусственном старении или нагреве
впроцессе технологической обработки в интервале 90…270 °С в ре- зультате распада твердого раствора образуется фаза, близкая по со- ставу к интерметаллическому соединению (типа AlmCun). Поскольку эта фаза выделяется преимущественно по границам зерен, вблизи границ образуется зона, значительно обедненная атомами меди, на- ходящимися в состоянии твердого раствора. Концентрация меди снижается в этой области с 4 до 0,3…0,5 %. Внутри зерна выпадение фазы происходит в меньшей степени, поэтому в зонах, удаленных от границ, твердый раствор меньше обедняется медью.
После термического воздействия (искусственного старения) по- верхность алюминиевого сплава Al + 4 % Cu является электрохими- чески неоднородной трехэлектродной системой, в которой наиболее отрицательно заряжена зона вблизи границы (–0,48 В). Находясь под воздействием двух катодов (границы и тела зерна) с более положи- тельным потенциалом [–0,37 В и (0,41…0,44) В соответственно], эта зона будет усиленно разрушаться.
4.4.1.Химические методы испытаний на устойчивость
кмежкристаллитной коррозии
Воснову методов испытаний положен принцип, согласно которо- му применяемые электролиты растворяют обедненные хромом гра- ницы зерен, оставляя пассивным само зерно. В табл. 4.2 представле- ны методы испытаний на склонность к МКК коррозионностойких
сталей, рекомендуемые межгосударственным стандартом ГОСТ 6032–2003, модифицированным по отношению к международ- ным стандартам: ИСО 3651–1:1998 «Определение стойкости к меж- кристаллитной коррозии нержавеющих сталей. Часть 1. Аустенитные
иферритно-аустенитные (двухфазные) нержавеющие стали. Корро- зионные испытания в азотной кислоте путем определения потери массы (испытания по Хью)» – в части сущности метода и подготовки образцов; ИСО 3651-2:1998 «Определение стойкости к межкристал- литной коррозии нержавеющих сталей. Часть 2. Ферритные, аусте- нитные и ферритно-аустенитные (двухфазные) нержавеющие стали. Коррозионные испытания в средах, содержащих серную кислоту» – в части компонентов растворов для испытаний, подготовки образцов
иоценки стойкости к межкристаллитной коррозии.
110