
Техническое обслуживание грузовых вагонов / МИАЛЕВИЧ РЕМОНТ БУКСОВОГО УЗЛА
.PDFМинистерство транспорта Российской Федерации
Федеральное агентство железнодорожного транспорта
ГОУ ВПО «Дальневосточный государственный университет путей сообщения»
Кафедра «Вагоны»
М.П. Михалевич
ИЗГОТОВЛЕНИЕ И РЕМОНТ РОЛИКОВЫХ БУКС
Конспект лекций
для студентов 5–го курса ИИФО направления 190300 «Подвижной состав и тяга поездов» специальности 190302 и для студентов 4 курса очной формы обучения специальности 190302 «Вагоны»
Хабаровск Издательство ДВГУПС
2008
2.2.ТЕХНИЧЕСКОЕ СОДЕРЖАНИЕ И РЕМОНТ БУКСОВЫХ УЗЛОВ
Втиповых узлах букс вагонов устанавливаются два цилиндрических роликовых подшипника полузакрытого типа габаритом 130х250х80 мм. Подшипники при работе испытывают многократные переменные контактные напряжения сжатия, поэтому металл подшипников должен обладать высоким пределом сопротивления пластической деформации, высокой контактной прочностью и износостойкостью. В наибольшей мере этим требованиям удовлетворяют, стали химической состав которых приведён
втабл. 2.1.
Таблица 2.1
Марка сталей для подшипников и их химический состав
Марка стали |
|
|
Содержание элементов, % |
|
|
||
|
C |
Mn |
Si |
Cr |
SnP |
Ni |
Cu |
ШХ 15 |
0,95- |
0,2-0,4 |
0,17- |
1,30- |
0,02- |
0,30 |
0,25 |
|
1,0 |
|
0,27 |
1,65 |
0,027 |
|
|
ШХ 15 СГ |
0,95- |
0,9-1,2 |
0,4-0,65 |
1,3-165 |
0,02- |
0,30 |
0,25 |
|
1,0 |
|
|
|
0,027 |
|
|
ШХ 15 СГШ |
1,01 |
1,10 |
0,52 |
1,5 |
0008- |
0,21 |
0,20 |
|
|
|
|
|
0,0007 |
|
|
ШХ 4 |
0,95- |
0,15- |
0,15- |
0,35- |
0,02- |
0,30 |
0,25 |
|
1,05 |
0,30 |
0,30 |
0,50 |
0,027 |
|
|
Стали ШХ-15 и ШХ15СГ являются высокоуглеродистыми хромистыми сталями. Детали подшипников, изготовленные из этих сталей, подвергались закалке и отпуску. В результате сквозной прокаливаемости достигалась одинаковая твёрдость по всему сечению деталей. Она составляет: для колец HRC 58-60; для роликов HRC 60-64. Эксплуатация выявила склонность этих сталей к хрупкому разрушению из-за высокой чувствительности к концентраторам напряжений. Так, имели место изломы внутренних колец в местах концентрации напряжений на дорожке качения и в переходной выточке от дорожки к бурту из-за значительных растягивающих напряжений, возникающих при посадке колец на шейку оси.
Сталь ШХ15СГШ имеет улучшенные механические свойства, которые получены посредством электрошлакового или электровакуумного переплава. Однако проблема хрупкости осталась из-за сквозной прокаливаемости при термообработке.
Детали, изготовленные из стали ШХ4, получены путём применения при термообработке метода регламентированной прокаливаемости. В результате чего образуется, по всему периметру поперечного сечения детали на глубину 2,5-3 мм, слой твёрдостью HRC 58-62, в котором возникают остаточные напряжения сжатия, а сердцевина, твёрдостью HRC 3540, остаётся вязкой.
Применяемые в буксах вагонов цилиндрические роликовые подшипники имеют следующие конструктивные особенности:
2
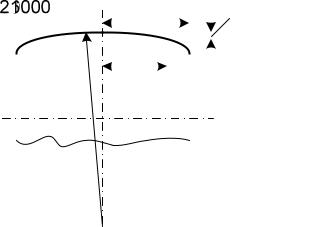
–наружное кольцо двухбортовое;
–внутреннее кольцо заднего подшипника однобортовое;
−внутреннее кольцо переднего подшипника имеет приставное (упорное) кольцо;
– ролики короткие. Отношение длины ролика к его диаметру менее 2-х;
– ролики бочкообразные (рис. 2.1). |
|
|
|
|
|
|
|
|
|
|
||||
Бочкообразная |
форма ро- |
|
|
|
|
|
|
|
|
|
|
|||
ликов способствует изменению |
|
|
|
|
|
|
|
|
|
|
||||
|
|
|
|
|
|
|
|
|
|
|||||
|
|
|
|
|
|
|
|
|
|
|||||
|
|
|
|
|
|
|
|
|
|
|||||
их перекрутки по концам. |
|
|
|
|
|
|
|
|
|
|
||||
|
|
|
|
|
|
|
|
|
|
|||||
|
|
|
|
|
|
|
|
|
|
|||||
Ранее применявшиеся ци- |
|
|
|
|
|
|
|
|
|
|
|
|
||
|
|
|
|
|
|
|
|
|
|
|
||||
|
|
|
|
|
|
|
|
|
|
|
|
|||
|
|
|
|
|
|
|
|
|
|
|
|
|||
линдрические ролики без ско- |
|
|
|
|
|
|
|
|
|
|
|
|
||
|
|
|
|
|
|
|
|
|
|
|
|
|||
са и со скосом кромок с экс- |
|
|
|
|
|
|
|
|
|
|
|
|
||
плуатации |
сняты. |
Расчётная |
|
|
|
|
|
|
|
|
|
|
|
|
долговечность роликовых под- |
|
|
|
|
|
|
|
|
|
|
|
|
||
|
|
|
|
|
|
|
|
|
|
|
||||
шипников |
для пассажирских |
|
|
|
|
|
|
|
|
|
|
|||
вагонов – 3 млн.км пробега, а |
|
|
|
|
|
|
|
|
|
|
||||
для грузовых вагонов – 1.5 |
|
|
|
|
|
|
|
|
|
|
||||
млн.км. При этом пробеге вы- |
Рис. 2.1. Конструкция ролика |
|||||||||||||
ход подшипников из эксплуата- |
ции по повреждениям усталостного характера не должен превышать 10%. Фактически выход
больше, для повышения надёжности создана система технического обслуживания и диагностики буксовых узлов.
В настоящее время выполняются теоретические исследования и эксплуатационные испытания конических подшипников кассетного типа габаритов: 130х230х150 мм – для работы с адаптером; 130х250х160 мм – для установки в серийный буксовый узел; 130х250х175(160) мм для вагонов с нагрузкой на ось 25 тс.
Прорабатывается конструкция цилиндрических подшипников кассетного типа габарита 130х250х160 мм для установки в серийный буксовый узел.
Ремонт подшипников кассетного типа после гарантийного пробега 500 тыс. км предполагается выполнять в сервисных центрах.
Для своевременного изъятия из эксплуатации подшипников, имеющих повреждения, функционирует система технического обслуживания и ремонта буксовых узлов.
2.2.1. Техническое обслуживание роликовых букс
Техническое обслуживание роликовых букс определяется «Инструктивными указаниями по эксплуатации и ремонту вагонных букс с роликовыми подшипниками» [1] которые определяют: наблюдение и уход за роликовыми буксами в эксплуатации; виды, сроки и правила ревизии букс; порядок производства работ при демонтаже, подготовке к монтажу и монтажу; нормы допусков и износов; возможные неисправности деталей букс
3
и осей, и условия дальнейшего их использования; виды ремонта подшипников.
2.2.1.1.Наблюдение и уход за роликовыми буксами в эксплуатации
Контроль за состоянием буксовых узлов осуществляется:
–в пути следования;
–при постановке вагонов в поезд;
–на пунктах подготовки вагонов под погрузку;
–на станциях формирования и расформирования поездов;
–на пунктах технического обслуживания участковых станций.
В пути следования контроль за состоянием буксовых узлов грузовых вагонов осуществляется системами бесконтактного обнаружения нагрева букс КТСМ, а пассажирских вагонов – термодатчиками. Эти устройства сигнализируют о недопустимом нагреве букс, что, в большинстве случаев, заканчивается отцепкой вагонов и сменой колёсных пар.
Для подтверждения правильности настройки аппаратуры КТСМ осмотрщики парков прибытия имеют бесконтактные измерители температуры «Кельвин 200 ЛЦ–М».
При постановке вагонов в поезд осмотрщики должны оценить общее состояние буксовых узлов. Для этого необходимо:
–проверить состояние колёсных пар;
–осмотреть корпусы букс и лабиринтные кольца;
–обстучать смотровые крышки.
На пунктах подготовки вагонов под погрузку, на ПТО сортировоч- ных, участковых и пассажирских технических станций контроль техни-
ческого состояния буксовых узлов осуществляется:
–при встрече поезда с ходу;
–во время стоянки поезда.
Если при осмотре букс при приёмке (встрече) поезда на станцию будет выявлены:
–движение колёсной пары юзом при отпущенном тормозе;
–выброс смазки хлопьями на диск и обод колеса;
–сильные потёки смазки на смотровую и крепительную крышки;
–частые вертикальные колебания одного из концов тележки;
–выброс искр со стороны лабиринта, то это признаки разрушения подшипников.
Или будут выявлены: скрежет, пощёлкивание, искрение между колёсной парой и буксой, а также между рамой тележки и колёсной парой; наклон корпуса буксы по отношению к раме тележки, то это признаки излома шейки.
Если при осмотре вагонов, при стоянке поезда, будут выявлены:
смещение корпуса буксы относительно лабиринтного кольца; окалина на смотровой крышке, выпуклость крышки или потертость; ослабление бол-
4
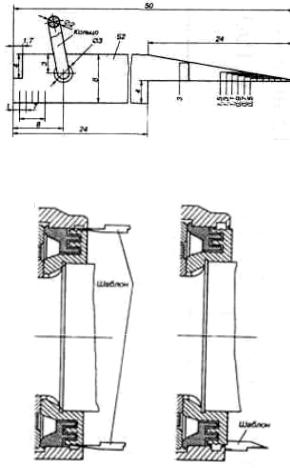
тов крепительной крышки; отбои при обстукивании смотровой крышки, то это признаки разрушения торцового крепления.
Или будут выявлены: нагрев передней части буксы больше задней; нагрев задней части буксы больше передней; выброс смазки на диск, обод колеса и обшивку пола вагона; разработана втулка в кронштейне для валика подвески башмака, выпадание валика из отверстия подвески башмака, излом пружин буксового подвешивания, то это признаки разрушения подшипников.
Разрушение подшипников и повреждение торцевого крепления может быть выявлено с помощью шаблона (рис.2.2). Клиновая часть шаблона вводится в зазор между корпусом буксы и лабиринтным кольцом
(рис.2.3,а). Если шаблон входит в за- |
а) |
|
зор вверху и внизу на одинаковое рас- |
б) |
|
стояние, то подшипники в буксе ис- |
|
|
правны. Если шаблон в верхней части |
|
|
входит меньше, чем в нижней, то неис- |
|
|
правен задний подшипник, а если он в |
|
|
верхней части входит больше, чем в |
|
|
нижней, то неисправен передний под- |
|
|
шипник. Допустимая разность в разме- |
|
|
рах сверху и снизу не более 1 мм. Вы- |
|
|
резом в основании шаблона глубиной |
|
|
1,7 мм проверяют смещение корпуса |
|
|
буксы относительно лабиринтного |
|
|
кольца (рис. 2.3,б), которое допуска- |
|
Рис. 2.3. Контроль положения |
ется не более 1,4 мм. Недопустимое |
|
буксы |
смещение является признаком повре- |
|
|
ждения торцового крепления.
На колёсные пары, забракованные приборами автоматического контроля нагрева букс и выкаченные из под вагона для замены наносится, на внутренней поверхности диска колеса, надпись «Аварийная –ДИСК», а на забракованные визуально – «По внешним признакам». Такие колёсные пары направляются в депо для ремонта.
2.2.1.2. Причины повреждений буксовых узлов
Многолетний опыт эксплуатации буксовых узлов, результаты наблюдений за их техническим состоянием и анализ накопленных данных позволили установить:
– сезонность их повреждаемости. Число отказов в осенне-зимний период возрастает в 1,5–2 раза, что объясняется изменением состояния верхнего строения пути и увеличением действующих сил;
5
–рост количества отказов в начальный период после полной реви-
зии. В первые 2-3 месяца эксплуатации буксовых узлов, после полной ревизии, число отказов выше, чем в последующий период. Это свидетельствует о недостаточном качестве ремонта и подбора подшипников, монтажа буксовых узлов и взаимной приработке деталей;
–ослабление и разрушение торцового крепления. Отмечается рост этих повреждений с увеличением скорости движения и повышением гру-
зоподъёмности вагонов. Происходит жёсткая передача горизонтальных (осевых) сил на упорное кольцо, торцовую гайку и резьбу шейки. Поло-
жительно влияли применение упругих торцовых гаек, имеющих про- точку; тарельчатых шайб и болтов М20; накатка резьбы и применение герметика. Отрицательно сказывается некачественное выполнение резьбы и монтажа букс, а также несвойственная для подшипников качения работа в режиме трения скольжения торцов роликов о борта колец и недостаточная роль смазки, как разделителя трущихся поверхностей (хе-
мосорбированного слоя смазки). Положительно влияет применение препарата-модификатора ЭМПи –1;
–возникновение усталостных раковин на дорожках качения наруж-
ных и внутренних колец и роликов, что объясняется достижением предела контактно-усталостной прочности материала колец и роликов. Этому способствует перекос буксовых узлов в вертикальной и горизонтальной плоскостях, что вызывает дополнительную нагрузку. Положи-
тельно влияет применение подшипников с «бонбированными» роли- ками, что обеспечивает их самоустановку при перекосах букс;
–возникновение трещин и разрывов внутренних колец имеет свои- ми причинами плохое качество металла, нарушение процессов термо- обработки и технологии монтажа буксовых узлов. Положительно ска-
зывается применение стали регламентированной прокаливаемости ШХ4;
–ослабление натяга (проворот) внутренних колец является след- ствием неправильного подбора внутренних колец по натягу и несоблю-
дение температурного режима. Установлено, что уже при разности тем-
ператур кольца и шейки 18 °С натяг в 30 мкм полностью исчезает. Поэтому важно соблюдать температурный режим и не допускать измерение шеек менее, через 12 ч после обмывки колёсных пар в моечных машинах и 2–х часов после обточки колёсной пары, а подшипников – через 8 ча-
сов после обмывки.
Применение прессовой посадки позволит контролировать величину усилия запрессовки;
– возникновение износов торцов роликов и бортов колец («ёлочка») происходит в результате действия больших осевых сил; разрыва мас-
ляного слоя между торцами ролика и бортами колец; нарушение геомет-
рии роликов, то есть перпендикулярности торцов роликов к их оси, возникающее при шлифовке торцов; нарушение исходной геометрии бортов колец, как результат их износа и ремонта. Применение препарата
- модификатора ЭМПи–1 для смазывания подшипников, вместо индуст-
6
риального, веретенного и авиационного масел перед их установкой в буксу способствует сохранению хемосорбированного слоя;
–возникновение коррозионных повреждений является результатом гигроскопичности смазки ЛЗ–ЦНИИ. Предлагаемая смазка «Буксол» должна уменьшить возникновение коррозии;
–возникновение электроожогов колец и роликов является резуль- татом нарушения технологии выполнения сварочных работ на вагоне,
когда рельсы используются в качестве обратного провода. Обратный провод должен присоединяться непосредственно у места сварки.
2.2.2. Виды и сроки ревизий букс
Для роликовых букс установлены два вида ревизий: промежуточная и полная ревизии.
Промежуточная ревизия выполняется с целью:
–проверки состояния торцового крепления подшипников;
–проверки состояния смазки;
–проверки общего состояния буксы и видимой части переднего подшипника.
Выполняется промежуточная ревизия в следующих случаях: а) при обточке колёсных пар без демонтажа букс; б) при обыкновенном освидетельствовании колёсных пар;
в) при единой технической ревизии пассажирских вагонов (ТО-3), то есть через шесть месяцев после планового ремонта (пробег 150 тыс. км);
г) в качестве профилактической ревизии по указанию ОАО «РЖД». Если промежуточная ревизия выполняется в случаях а и б, то она на-
чинается с осмотра буксы и оценки технического состояния подшипников посредством проворачивания букс. При вращении с толчками и ненормальным шумом буксы передаются на полную ревизию.
При наличии в депо установок для диагностирования роликовых подшипников УДП-85 или УДП-85М, АЛ2-3 и др. все колёсные пары, подлежащие обыкновенному освидетельствованию должны диагностироваться на этих установках. Установки состоят из стенда, обеспечивающего вращение колёсной пары и диагностического блока(микропроцессорного пульта) с пъезоакселерометрическими датчиками. Метод основан на анализе сигналов виброускорений регистрируемых датчиками, установленными на буксу.
Технологический процесс промежуточной ревизии включает в себя выполнение следующих работ:
–очистка места прилегания смотровой крышки, протирка, снятие крышки и укладка её внутренней стороной вверх на место хранения, где невозможно её загрязнение;
–удаление из передней части буксы смазки с укладкой на снятую крышку с целью дальнейшего использования;
7
– проверка состояния смазки. Для этого проба смазки в количестве 4-5 г отбирается в прозрачный стакан, растворяется 100 мл бензина температурой 70-90 °С, и помещается в зеркальный прибор. Наличие продуктов износа стальных деталей выявляется магнитом, неметаллических загрязнений – по россыпи на дне стакана, обводнение – по изменению цвета смазки на белый и её неприлипаемости к стенкам стакана. Буксы с загрязнённой смазкой передаются на полную ревизию;
–проверка состояния видимой части переднего подшипника. При обнаружении повреждений сепаратора и приставного кольца букса передаётся на полную ревизию;
–снятие стопорной планки и её магнитная дефектоскопия;
–проверка плотности затяжки торцовой гайки. Для этого используют инерционный ключ или слесарный молоток массой 3-5 кг и оправку. Поворот гайки, хотя бы в одном направлении, расценивается как ослабление;
–снятие ослабевшей гайки и проверка состояния резьб шейки и гайки. Колёсные пары с повреждённой резьбой (износ, срыв ниток, смятие, забоины) подлежат ремонту. Гайки с повреждённой резьбой – бракуют. Гайки, при исправной резьбе, затягиваются двумя–четырьмя ударами молотка (или качаниями инерционного ключа) массой 3-5 кг, прилагаемыми на плече ключа 0,5 м до получения чистого металлического звука.
При торцовом креплении подшипников тарельчатой шайбой болты М20 освобождают от стопорения и динамометрическим ключом проверяют их затяжку. При наличии хотя бы одного болта затянутого крутящим моментом менее 5 кгс∙м все болты вывертывают и проверяют визуально
состояние резьбы в отверстиях и болтах. Болты М20х60 × 4.8 должны иметь на опорной поверхности головок ложную шайбу. Болты с затяжкой более 5 кгс∙м подтягивают моментом 23-25 кг×см;
–если поверхности катания колёс нуждаются в обточке, то взамен снятых смотровых крышек ставят временные с отверстием для прохода центров станка;
–после обточки или затяжки торцового крепления в буксу возвращается удалённая смазка (может быть добавлена и свежая). Она укладывается валиком на видимую часть подшипника с последующим вдавливанием в зазор между сепаратором и бортом наружного кольца;
–постановка смотровой крышки с резиновой прокладкой;
–постановка бирки и клейм на ней.
При ревизии в случаях в случаях в) и г) колёсные пары из под вагонов не выкатываются, а ревизия производится без снятия стопорных планок. Надёжность торцового крепления проверяется отстукивания.
2.2.2.1. Полная ревизия
Она производится при полном освидетельствовании колёсных пар с выполнением нижеследующих работ: демонтаж букс; промывка подшипников и деталей букс; осмотр и контроль подшипников; осмотр и контроль
8
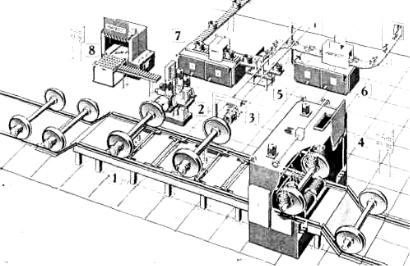
деталей букс; обмер и подбор подшипников для монтажа; монтаж; постановка клейм.
2.2.2.2. Демонтаж букс
Процесс демонтажа заключается в снятии смотровой и крепительной крышек, разборке торцового крепления, снятии буксы совместно с блоками подшипников с шейки оси, удалении блоков подшипников из корпуса
буксы. |
|
|
Для |
демонтажа |
|
букс и обмывки их де- |
|
|
талей ООО «ИР- |
|
|
ТРАНС» |
разработан |
|
механизированный |
|
|
комплекс рис. 2.4. Он |
|
|
включает в себя: эста- |
|
|
каду 1 высотой 600 мм |
|
|
с подъёмником колёс- |
|
|
ных пар; устройствами |
|
|
перемещения колёс- |
|
|
ных пар по эстакаде и |
|
|
их позиционирования; |
|
|
стенд для |
демонтажа |
Рис. 2.4. Механизированный комплекс |
роликовых букс 2, оснащённый одно-, двух- и четырёхшпиндельными гайковёртами; стенд с
буксосъёмником 3, позволяющий снять буксы и передать их на выпрессовку подшипников; машину 4 для обмывки колёсных пар; устройство 5 для выпрессовки подшипников из букс; машину 6 для мойки и сушки подшипников; машину 7 для мойки корпусов букс и машину 8 для мойки деталей букс.
При необходимости снятия с шейки внутренних и лабиринтных колец (в случае их неисправности или расформирования колёсной пары) применяется индукционный нагреватель. Время нагрева колец 35-40 с, температура нагрева 100-120 °С.Возможно применение стендов для распрессовки.
2.2.2.3. Промывка подшипников и деталей букс
Демонтированные блоки подшипников (наружные кольца с роликами и сепараторами) подлежат очистке от смазки. Очистка (промывка) должна выполняться только в автоматических машинах для мойки и сушки подшипников – МСП. Для предупреждения выпадания роликов из гнёзд сепаратора в блок устанавливается фиксирующая втулка. Моющая жидкость – 8-10 % отработанной смазки ЛЗ – ЦНИИ в воде температурой 90-95 °С. Просушка после обмывки выполняется обдувкой горячим воздухом.
Корпуса букс обмываются в моечных машинах – МКБ, а детали букс (смотровые и крепительные крышки, лабиринтные кольца, гайки, стопор-
9
ные планки и болты) промываются в автоматических моечных машинах – МД, двумя моющими жидкостями температурой не ниже 90 °С. Первая жидкость – 2-5 % раствор каустической соды в воде, вторая – 8-10 % раствор отработанной смазки ЛЗ – ЦНИИ в воде. Если внутренние кольца не снимались с шейки оси, то после обмывки колёсных пар с установленными внутренними кольцами выполняется их протирка обтирочным хлопчатобумажным материалом.
2.2.2.4. Осмотр и контроль деталей подшипников
Обмытые блоки подшипников транспортируются в ремонтно-комплек- товочное отделение, где они разбираются. Разборка заключается в смещении всех роликов к центру наружного кольца, снятии наружного кольца и извлечении роликов из сепаратора.
Наружные кольца, ролики, сепараторы, упорные кольца и неснятые с шейки оси внутренние кольца осматриваются с помощью лупы при рассеянном свете с целью установления их пригодности для дальнейшего использования.
При наличии на наружных и внутренних кольцах трещин, отколов, раковин, шелушения дорожек качения, коррозионных раковин на дорожках качения, повреждении электрическим током они бракуются.
Кольца подшипников и упорные кольца повторно используются после зачистки наждачным полотном № 6 с маслом коррозии на посадочных поверхностях и износа бортов типа «ёлочка».
Дефектоскопия снятых с шейки внутренних, наружных и упорных колец производится способом СОН на установке УМДП – 01, с использованием суспензии на основе концентрата «Диагма» с последующим размагничиванием.
Ролики бракуются при наличии трещин, отколов, ползунов, коррозионных раковин, электроожогов и др. Ролики с повреждением торцов типа «ёлочка» зачищают наждачным полотном № 6 с маслом.
Для контроля роликов подшипников качения (тип 2726), используемых в буксовых узлах грузовых и пассажирских вагонов, применяется вихретоковый дефектоскоп ВД-211,5, состоящий из электромеханического и электронного блоков. Электромеханический блок дефектоскопа позволяет разбраковать, заложенную в падающую кассету, партию роликов в количестве 15 штук на годные не имеющие поверхностных трещин и не годные для дальнейшей эксплуатации. Электронный блок служит для накопления информации о контролируемых роликах и передачи ее в компьютер.
Сепараторы – латунные заменяются на полиамидные. Повреждённая «чеканка» по перемычкам, послужившая причиной выпадания роликов, восстанавливается. При трещинах, износах перемычек и др. сепараторы заменяются. Сепараторы подвергаются испытанию на растяжение на приборах контроля полиамидных сепараторов КС–22. Растяжение осуществляют до увеличения наружного диаметра каждого основания сепаратора на 0,5 мм.
10