
Shilina SOSUN_kr / ptpip_kr
.pdfмодель. Застосування сталевих моделей забезпечує отримання робочої поверхні до – 11 класу чистоти, керамічних – на 3…4 класи нижче. Високий клас чистоти робочої поверхні досягається шляхом нанесення покриття на поліровану поверхню сталевої основи.
Напилення на гладку поверхню моделі обумовлює цілий комплекс вимог до технологічних параметрів і режимів напилення. Наприклад, взаємодія матеріалів покриття і моделі повинна забезпечити міцне утримання покриття на моделі в процесі формування всієї товщини покриття і дозволити видаляти модель без руйнування матеріалу покриття.
На робочій поверхні формоутворюючої деталі не повинно бути відкритих пор, викрашивання та інших дефектів. Напилений матеріал на межі з поверхнею моделі повинен бути максимально щільним.
Матеріали для отримання формоутворюючих деталей умовно можна поділити на дві групи:
•матеріали для нанесення робочого шару;
•матеріали для нанесення конструкційного шару.
До кожній із груп матеріалів висуваються свої вимоги. Так, наприклад, матеріали робочого шару повинні бути більш твердими, зносо-, жаро-, корозієстійкими, добре розплавлятися у високотемпературному струмені і формувати щільні покриття. У свою чергу, матеріали конструкційного шару повинні бути більш пластичними і легко піддаватися механічній обробці. З точки зору вартості бажано, щоб матеріали конструкційного шару були більш дешеві, бо їх витрата значно більша порівняно з матеріалами робочого шару.
Враховуючи згадані умови, для створення робочого шару можна використовувати порошкові самофлюсуючі хромонікелеві сплави типу СНГН, ПГХН80-СР2 (СР3, СР4). Крім високої зносостійкості і твердості, ці сплави мають значну корозійну стійкість і жаростійкість. Завдяки додаванню бору і кремнію сплав набуває здатності до самофлюсовання, добре змочується з поверхнею основи і має порівняно низьку температуру плавлення (980.1080 оС).
Для нанесення робочого і конструкційного шарів використовуються також порошки нікелю, заліза, міді та їх композиції. Залежно від складу композиції в процесі напилення можна отримувати матеріали робочого і конструкційного шарів із заданими фізико-механічними властивостями.
6.3 Вибір методу нанесення покриття і робочого середовища процесу
Вибір методу і способу нанесення покриття доцільно проводити:
•виходячи із вимог, що висуваються до якості покриття.
21
Високу якість покриття достатньо легко досягти вакуумнокондесаційними методами напилення. Особливо це стосується способів, де потік частинок (пари) стимульований плазмою.
Серед газотермічних методів нанесення покриття найбільш високу якість забезпечують високошвидкісні методи: детонаційний, надзвукові плазмові та газополуменеві.
Високі результати досягаються газотермічними методами напилення із захистом робочої зони, наприклад, плазмовими у динамічному вакуумі;
•враховуючи властивості матеріалу покриття.
Вакуумні конденсаційні методи дозволяють отримувати покриття практично любого складу.
Номенклатура покриттів, нанесених реакційними вакуумними методами, визначається речовинами, які є складовими синтезованого матеріалу покриття. Доцільним є отримання карбідних, нітридних або оксидних сполук. При цьому процес проходить у відповідних середовищах: атмосфері азоту, кисню тощо.
При використанні газотермічних методів можливі ускладнення, пов’язані з нанесенням термічно нестабільних сполук. У процесі нагрівання спостерігається часткова дисоціація цих сполук або їх сублімація. Так ведуть себе багато нітридів (TiN, ZrN, AlN та ін), деякі оксиди (міді, заліза та ін) та ряд інших сполук.
Склад матеріалу покриття може суттєво змінюватися внаслідок вибіркового випаровування окремих елементів з високою пружністю пари.
Газотермічне напилення на повітрі практично завжди пов’язане з окисленням компонентів матеріалу, який напилюється. При цьому склад покриття може суттєво відрізнятися від вихідного. Збереження вихідного складу матеріалу можливе при загальному або місцевому захисті ділянки нагрівання та прискорення матеріалу, що утворює покриття, і самої зони формування покриття. Такий захист частково здійснюється при використанні нейтральних або інертних робочих газів (плазмові методи напилення) і додатковому захисті зони формування покриття застосуванням захисних насадок, камер тощо. Або використанням складним газових сумішей, які дозволяють змінювати окислювально-відновний потенціал середовища через зміну співвідношення компонентів суміші, наприклад, сумішей горючих вуглеводневих газів із окислювачем.
Альтернативним шляхом є зменшення часу перебування частинок у агресивному середовищі. Цей шлях реалізується при використанні високошвидкісних методів газотермічного нанесення покриття (звукових або надзвукових);
22
•залежно від товщини покриття.
Суттєвий вплив на вибір методу нанесення покриття має необхідна товщина покриття. Вакуумні методи дозволяють отримувати покриття товщиною від 10-8 нм до кількох мікрометрів. Газотермічні методи нанесення покриття забезпечують мінімальну товщину покриття близьку до діаметра частинок, що утворюють покриття. Вона дорівнює 10–100 мкм.
Максимальна товщина газотермічного покриття принципово не обмежена, але потрібно враховувати накопичення напружень у товстих покриттях, що погіршує показники якості отриманих покриттів, зокрема, міцність зчеплення покриття з основою;
•з урахуванням досягнення максимальної продуктивності.
За цим показником газотермічні методи нанесення покриття значно (у десятки разів) продуктивніші за вакуумно-конденсаційні методи. Продуктивність сучасних плазмових та електродугових установок досягає 50 кг/год за металевим та 25–30 кг/год за керамічним матеріалом.
Продуктивність такого ж порядку мають електродугові методи розпилення.
•з урахуванням геометричних розмірів виробу;
Вакуумні методи нанесення покриття мають практичні обмеження на розміри виробу, які накладаються розмірами вакуумної камери, у якій проводиться процес нанесення покриття. Сучасні вітчизняні серійні установки вакуумно-конденсаційного нанесення покриття універсального призначення мають розміри вакуумних камер в межах 500x500x500 мм.
Газотермічні методи напилення у відкритій атмосфері таких обмежень не мають. Все визначається типом та можливостями застосованого допоміжного обладнання: маніпуляторів.
•з урахуванням економічних показників процесу.
Важливими факторами є енергоємність процесу (коефіцієнт використання енергії КВЕ) та коефіцієнт використання матеріалу (КВМ).
Плазмові методи забезпечується високі значення КВМ: 0,7–0,25 для дротяних матеріалів та 0,3–0,8 для порошкових. При цьому коефіцієнт використання енергії не перевищує 0,02–0,18 при дротяном напиленні і 0,001–0,2 при порошковому.
Газополуменеві методи, маючи обмеження за температурою матеріалу, з якого формується покриття, забезпечують для своєї номенклатури матеріалів КВМ на рівні плазмового методу, однак ефективний коефіцієнт нагрівання матеріалу не перевищує 0,02–0,1.
Детонаційний метод забезпечує КВМ на рівні 0,3–0,6 і коефіцієнт
23
ефективності використання енергії на рівні 0,1–0,15, з урахуванням збільшення ентальпії частинок в момент зустрічі з основою. Ефективний ККД нагрівання порошкових частинок при їх перенесенні оцінюється сотими долями.
Електродуговий метод має найвищий енергетичний ККД, який складає 0,7– 0,9 та достаньо високий КВМ.
Економічне співставлення методів газотермічного нанесення покриття можна виконати шляхом розрахунку витрат на нанесення 1 кг покриття. У цьому випадку за питомими витратами “на обладнання” методи можна розмістити у такому порядку: газополуменевий-електродуговий-детонаційний-плазмовий.
За питомими витратами на робочі гази вибудовується такий ряд: електродуговий-газополуменевий-плазмовий-детонаційний.
За витратами на заробітну плату з нарахуваннями: електродуговий- газополуменевий-плазмовий-детонаційний.
За витратами на електроенергію: газополуменевий-детонаційний- електродуговий-плазмовий.
Сумарні питомі витрати на технологічну операцію напилення 1 кг покриття: електродуговий-газополуменевий-плазмовий-детонаційний.
Електродуговим способом наносять покриття із алюмінію, нержавіючої сталі, ніхрому, цинку, латуні та інших металів і сплавів у вигляді дроту, вартість 1 кг яких відносно мала.
Для нанесення покриття газополуменевим способом поряд із дротяними використовуються порошкові матеріали, головним чином самофлюсуючі на нікелевій основі. Вартість таких матеріалів у 3.10 разів вища за згадані дротяні. Окрім того, покриття потребують додаткової обробки у вигляді оплавлення. До витрат на напилення додаються витрати на оплавлення.
Перспективним матеріалом для створення покриттів вважаються керамічні порошкові матеріали, зокрема оксиди. Їх вартість нижча за вартість дротяних матеріалів. Основним методом нанесення оксидів, внаслідок їх високої температури плавлення, є плазмовий.
Використання поряд з оксидами карбідів, нітридів, боридів, які мають значну вартість але забезпечують унікальні властивості покриттів, значно підвищують вартість 1 кг покриття. Згадані матеріали характерні для детонаційного та плазмового методів нанесення покриття - дорогі матеріали у сполученні із дорогими методами.
Якщо врахувати значну відміну методів у номенклатурі матеріалів, що використовуються для утворення покриття, та різну вартість одиниці маси матеріалу, що найбільш широко застосовуються в конкретному методі напилення,
24
тоді зростання вартості 1 кг покриття на деталі буде відповідати такому ряду: електродуговий-плазмовий-газополуменевий-детонаційний.
Вартість 1 кг покриття, отриманого вакуумно-конденсаційними методами нанесення значно перевищуює вартість 1 кг покриття, отриманого газотермічними методами. Тому використання ВКНП потрібно ретельно обгрунтовувати, спираючись на факт отримання характеристик покриттів, недосяжних при використанні альтернативних методів.
• з урахуванням екологічної безпеки процесу.
Загальновідомі шкідливі фактори, що супроводжують процеси газотермічного нанесення покриття: значний шум, випромінювання у ультрафіолетовому та інфрачервоному діапазонах, наявність у зоні технологічного процесу значних виділень озону, оксидів азоту та вуглецю, аерозолів матеріалів, що застосовуються для нанесення покриття. Захист від них здорожчує процес, потребує значних технічних та організаційних зусиль.
Вакуумно-конденсаційні методи значно безпечніші у цьому відношенні: відсутній шум, а проведення процесу у герметичній камері спрощує захист персоналу і навколишнього середовища від наявних шкідливих факторів.
Таким чином, вибір методу нанесення покриття у конкретному випадку носить неоднозначний характер. Він лежить у площині вибору серед кількох альтернативних методів, які забезпечують приблизно однакові якісні характеристики покриття та мають близькі економічні показники.
Тому часто виникають додаткові суб’єктивні параметри, за якими обирається метод: особисті уподобання, наявність необхідного обладнання, доступність матеріалів, що використовуються у процесі, та ін.
6.4. Вибір вихідного виду матеріалу, що застосовується для створення покриття
Для вакуумного конденсаційного напилення покриттів використовується широкий клас матеріалів, в тому числі і композиційних. Вихідний матеріал може бути у вигляді дроту, стрижня, таблеток, дисків та інших форм, які визначаються типом застосованого обладнання. Загальною вимогою є сувора відповідність потрібному хімічному складу за основними легуючими елементами; високий ступінь чистоти за домішками та сторонніми включеннями; мінімальна загазованість.
При газополуменевому та плазмовому нанесенні покриття найчастіше, а при детонаційному виключно, використовується порошкові матеріали. Вони дозволяють досягати максимальної продуктивності, не мають обмежень за
25
хімічним складом, забезпечують достатньо прогнозовану морфологію отриманого покриття. Серійно випускаються однокомпонентні та композиційні (багатокомпонентні) порошкові матеріали. Можливо використання механічних сумішей порошкових матеріалів.
Рівномірне подавання порошкових матеріалів (особливо складної форми і дрібнодисперсних) у зону їх обробки досить складна технічна задача. До того ж, вартість порошкових матеріалів порівняно із дротяними матеріалами того ж хімічного складу - вища. Якщо вибраний для покриття матеріал дозволяє виготовлення дроту, використання дроту може бути найкращим варантом вирішення проблеми. До того ж, як вже згадувалось, коефіцієнт використання енергії, як правило, вищий при напиленні дротяних матеріалів порівняно з напиленням порошкових матеріалів. Сучасною тенденцією розвитку методів ГТНП є використання для напилення композиційних покриттів порошкових дротів із металевою і органічною оболонкою.
Електродуговий метод використовує виключно суцільний дротяний матеріал або порошковий дріт із металевою оболонкою.
Використання стрижнів на сьогоднішній час обмежено, що пов’язано з багатьма причинами і, не в останню чергу, із складністю їх безперервного рівномірного подавання у зону розпилення.
6.5. Розробка конструкції покриття
Процес конструювання покриття містить у собі вибір складу матеріалу покриття, визначення структури системи “покриття-основа” та товщини шару (шарів) матеріалу, який створює робочу поверхню.
Досить поширеним є одношарове покриття (рис.6.3, а).
Його використання доцільне у випадку створення конструкції “покриттяоснова” із матеріалів з близькими значеннями коефіцієнтів термічного розширення. Необхідною умовою є також забезпечення міцності зчеплення покриття з основою. Як правило, такі умови витримуються при нанесенні металевих покриттів на металеву основу.
Більш поширеним є покриття з підшарком (рис.6.3, б). Підшарок газотермічного покриття - частина газотермічного покриття, яка безпосередньо прилягає до основи і виконує функції зв’язку між основною частиною покриття і основою.
Основна частина газотермічного покриття - частина газотермічного покриття, яка розміщена над підшарком і виконує робочу функцію покриття.
Основа - поверхня основного матеріалу, на яку наноситься покриття.
26
Підшарок має меншу, ніж основна частина покриття, товщину, яка лежить у межах 0,025–0,1 мм. Призначення прошарку - забезпечення міцного зв’язку покриття з основою, а також узгодження коефіцієнтів термічного розширення матеріалів основної частини покриття і основи. Найчастіше, як прошарок, використовуються нікель-алюмінієві матеріали у вигляді композиційних порошків або сплавів. При нанесенні оксидних покриттів добрі результати, як матеріал прошарку, показують нікель-титанові сплави.
При конструюванні теплозахисних покриттів та покриттів, стійких до спрацьовування, перспективними можуть бути багатокомпонентні покриття (рис.5.2, в). Покриття такого типу можуть бути отримані при нанесенні механічних сумішей або композиційних порошків.
Композиційний порошок - порошок, кожна частинка якого складається із макрооб’ємів декількох компонентів, які відрізняються за хімічним складом, та ідентична за якісним складом всім іншим частинкам. Композиційні порошки поділяються на плаковані та конгломеровані порошки.
Плакований композиційний порошок - композиційний порошок, кожна частинка якого складається із відмінних за хімічним складом центральної частини і оболонки, що її охоплює.
Конгломерований композиційний порошок - композиційний порошок, кожна частинка якого є конгломератом макрооб’ємів декількох компонентів, скріплених між собою в’яжучою речовиною або спіканням.
Обов’язковими складовими багатокомпонентних покриттів є тверда та пластичні компоненти. Пластична компонента покращує експлуатаційні властивості покриття, підвищує міцність зчеплення покриття з основою і міцність покриття, знижує його пористість. Як пластична фаза використовуються чисті метали (нікель, алюміній, кобальт, мідь, хром та ін.) або термореагуючі порошки алюмінідів, ніхром.
Тверда фаза (оксиди, карбіди, нітриди, бориди, силіциди тощо) підвищує зносостійкість або покращує захисні властивості матеріалу покриття.
У випадку експлутації покриття в умовах механічних ударних навантажень і теплозмін, а також при необхідності сполучення багатьох різних функціональних властивостей (наприклад, високої зносостійкості і корозієстійкості), використовуються багатошарові покриття (рис.6.3, в).
Багатошарове газотермічне покриття - газотермічне покриття, що складається із двох або більше шарів, які відрізняються за складом (рис.6.3, а, в).
Зовнішній шар газотермічного покриття - шар багатошарового покриття,
поверхня якого стикається із зовнішнім середовищем.
27

Проміжний шар газотермічного покриття - любий шар багатошарового покриття, що розміщується між основою або підшарком і зовнішнім шаром.
Товщина шарів покриття залежить від методу нанесення покриття та його функціонального призначення і визначається розрахунковоеспериментально із урахуванням технічно мінімально можливої товщини шару покриття.
Покриття із плавним переходом від одного матеріалу до іншого в межах товщини покриття називають градієнтним покриттям.
Градієнтне покриття - багатошарове газотермічне покриття, в якому кожний проміжний шар містить кілька компонентів із градієнтом концентрації, що напрямлений від основи до зовнішнього шару (рис.6.3, г).
Градієнтне покриття, незважаючи на деяку технічну складність його нанесення, може бути дуже перспективним при необхідності ретельного узгодження КТР матеріалів основи і покриття та при нанесенні покриттів, матеріал яких не сумісний ізх матеріалом основи. Важливим етапом процесу конструювання покриття є визначення його товщини.
Товщина напиленого газотермічного покриття на деталях, у яких зміцнюється поверхня або відновлюються втрачені розміри, повинна передбачати припуск на наступну обробку (токарну, фрезерну, шліфувальну).
Методика розрахунку товщини покриття з урахуванням припусків на обробку ілюструється рис.6.4.
а |
б |
в |
г |
д |
Рис.6.3. Конструкції покриття: а - одношарове покриття; б - покриття з прошарком; в - багатокомпонентне покриття; г - багатошарове покриття; д - градієнтне покриття (з поступовим переходом від матеріалу основи до матеріалу верхнього шару покриття); 1 - основа; 2 - прошарок; 3 - шар покриття; 4 - верхній шар покриття
28
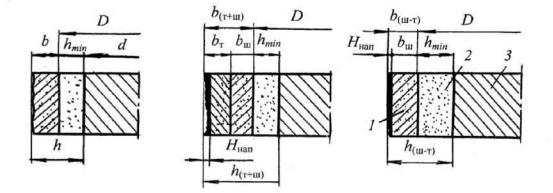
а |
б |
в |
Рис.6.4. Схеми до розрахунку товщини покриття з урахуванням припусків на обробку: а - припуск на обробку (загальний випадок); б - токарна (фрезерна) і шліфувальна обробка; в - шліфування без попередньої токарної (фрезерної) обробки; 1 - припуск на обробку; 2 - напилений шар покриття, який залишився після обробки; 3 - основний метал деталі
Товщина покриття, що нарощується на зовнішні поверхні, може
визначатися за формулою: |
|
|
|
|
h |
D d |
b , |
(6.1) |
|
2 |
||||
|
|
|
де D- номінальний діаметр деталі; d - діаметр деталі після підготовки до напилення; b - припуск на обробку після напилення.
Для забезпечення нормального функціювання виробу і необхідної міцності покриття, а також виключення деформації основи з покриттям, що перевищує допустиму, товщина, покриття після кінцевої обробки на повинна бути менше деякої визначеної величини.
Мінімальна товщина покриття, що працює в умовах спрацьовування, збільшується на деяку величину hпс, пропорційну потрібному ресурсу роботи виробу.
В більшості випадків залежність між шляхом тертя Ь і величиною
спрацьовування є лінійною, тому в умовах спрацьовування: |
|
hпс = iпс L, |
(6.2) |
де ісп - интенсивність спрацьовування; L - шлях тертя.
В умовах корозійного впливу зовнішнього середовища мінімальну товщину покриття збільшують на величину, пропорційну питомому зменшенню товщини покриття внаслідок корозійного руйнування протягом його експлуатації.
У згаданому випадку потрібно також враховувати висоту нерівностей, яка буде отримана при кінцевій обробці покриття, бо процес руйнування залежить від топографії поверхні.
29
Аналогічно враховуються інші фізичні величини, що залежать від товщини покриття, наприклад, діелектрична міцність.
У загальному випадку мінімальна робоча товщина покриття визначається за виразом:
hmin = hпн +hпс + Rzп + Wп, |
(6.3) |
де hпн - товщина покриття, що забезпечує необхідну |
міцність покриття і |
нормальне функціювання виробу; Rzп - висота нерівностей, отриманих при кінцевому переході обробки покриття; Wп - хвилястість поверхні виробу.
Розрахунок значення hmin за формулою (6.3) ускладнений, внаслідок деякої попередньої невизначеності складових правої частини формули.
Тому, враховуючи загальні міркування, попередні розрахунки та накопичений промисловістю досвід, в літературі для випадку відновлення деталей рекомендується емпірична мінімальна товщина покриття, яка залежить від діаметра деталі і, зазвичай знаходиться в межах від 0,6 до 1, 0 мм (табл.6.1.). В спеціальних випадках, можливе застосування газотермічних покриттів меншої (30–50 мкм) або більшої товщини (до 5–.6 мм).
Для токарної обробки напилених деталей покриття наноситься з припуском Ьт, який залежить від діаметра деталі і, крім того, обумовлений ступенем рівномірності покриття за товщиною. Припуск Ьт заходиться у прямій залежності від висоти нерівностей напиленого покриття. Нерівності покриття визначаються методом, який був застосований, і кваліфікацією оператора-металізаторщика. Величина припуску bT буде також залежати від кваліфікації токара, що обробляє деталь після нанесення покриття. Величина припуску bT практично може знаходитися в межах 0,5–1,0 мм.
Припуск на шліфування у розмір після обточування bT залежить від якості абризивних кругів і точності станка. Ця величина приймається в межах 0,15–0,20 мм.
Таким чином, загальний припуск на токарну (фрезерну) і шліфувальну обробку b(T+Ш) може бути розрахований як сума припусків bT та bШ (рис.6.4, б):
b(T+Ш) = bT+bШ |
(6.4) |
Звідси мінімальна товщина покриття для наступної токарної (фрезерної) і шліфувальної обробки b(T+Ш) можна підрахувати за формулою:
h(T+Ш) =hmin+b(T+Ш) |
(6.5) |
30