
detlab8
.pdfФЕДЕРАЛЬНОЕ АГЕНСТВО ПО ОБРАЗОВАНИЮ РФ ВОЛГОГРАДСКИЙ ГОСУДАРСТВЕННЫЙ ТЕХНИЧЕСКИЙ УНИВЕРСИТЕТ
Кафедра «Детали машин и ПТУ»
ДЕТАЛИ МАШИН ИССЛЕДОВАНИЕ ТРЕНИЯ В ПОДШИПНИКАХ СКОЛЬЖЕНИЯ
Методические указания Лабораторная работа №8
Волгоград 2006
Составители: М.М. Матлин, С.Л. Лебский, И.М. Шандыбина УДК 375 621.8
Исследование трения в подшипниках скольжения: Метод. указ. к учебноисследовательской лабораторной работе №8 по курсу «Детали машин» / Сост. М.М. Матлин, С.Л. Лебский, И.М. Шандыбина – Волгоград: ВолгПИ, 2006, 22 с.
Приводится методика определения коэффициентов трения и потерь мощности на трение в подшипниках скольжения. Описаны конструкция лабораторной установки, методика обработки экспериментальных данных. Включены элементы научного исследования.
Рис. 5, табл. 3, библ. наим. 5.
Печатается по решению ред. – издательского совета Волгоградского государственного технического университета.
Рецензент – к.т.н., доцент ВолгПИ ___.
Волгоградский
государственный
технический университет, 2006

Цель работы Исследовать влияние различных факторов на коэффициент трения,
потери мощности в подшипнике скольжения и определить допустимые давления и скорость скольжения в подшипнике.
1.ТЕОРИЯ ИЗУЧАЕМОГО ВОПРОСА
Подшипники скольжения служат опорами для валов и вращающихся осей. В них присутствует трение скольжения: опорный участок вала скользит по поверхности подшипника.
По характеру воспринимаемой нагрузки подшипники подразделяют на радиальные (рис. 1.2 а) и упорные (подпятники, рис. 1.2 б).
В зависимости от режима работы подшипника в нём может быть полужидкостное или жидкостное трение. Схематическое представление об этом даёт рис. 1.1.
Рис. 1.1
При жидкостном трении рабочие поверхности вала и вкладышей разделены слоем масла, толщины h , который должен быть больше суммы высот RZ шероховатостей вала RZ1 и вкладыша RZ2 .
h > RZ1 + RZ2 |
|
|
(1.1) |
При этом условии масло воспринимает внешнюю нагрузку, |
|||
предотвращающую |
непосредственное |
соприкосновение |
рабочих |
поверхностей, то есть износ. |
|
|
|
Значение коэффициента жидкостного |
трения находится |
в пределах |
fж = 0,001...0,005. При полужидкостном трении условие (1.1) не соблюдается.
В подшипнике наблюдается смешанное трение – одновременно жидкостное и
граничное, т.е. трение, при котором трущиеся поверхности покрыты тончайшей пленкой смазки, образовавшейся в результате действия молекулярных сил и химических реакций активных молекул смазки и материала вкладыша.
Граничные пленки устойчивы и выдерживают большое давление. Однако в местах сосредоточения давления они разрушаются, происходит соприкосновение чистых поверхностей металла, их схватывание и отрыв частиц материала при относительном движении. Поэтому полужидкостное трение сопровождается износом трущихся поверхностей даже без попадания внешних абразивных частиц.
Значение коэффициента трения лежит в пределах fпж = 0,008...0,1. Момент трения (Н·мм) в подшипнике и потери мощности (Вт) на трение
определяют по формулам: |
|
|||||
1) в радиальном подшипнике |
|
|||||
Mr |
= 0,5 Fr d fr , |
(1.2) |
||||
Nr |
= |
Mr n |
; |
(1.3) |
||
|
|
|||||
|
9550 |
|
|
|
||
2) в упорном подшипнике |
|
|||||
Ma |
= Fa Rпр fa , |
(1.4) |
||||
Na |
= |
Ma n |
, |
(1.5) |
||
|
||||||
|
9550 |
|
|
|
где Fr , Fa - соответственно радиальная и осевая нагрузки, Н;
fr , fa - коэффициенты трения в радиальном и упорном подшипниках;
d - диаметр цапфы, мм;
n - частота вращения вала, мин-1;
Rпр - приведенный радиус кольцевой пяты, мм.
R |
|
= |
1 |
|
d13 |
− d |
03 |
(1.6) |
|
пр |
3 |
|
|
2 |
|||||
|
|
|
d |
2 |
− d |
|
|||
|
|
|
|
|
|
1 |
|
0 |
|
Примечание. Если ось подшипника расположена под углом 0 < β < 90O , то подшипник воспринимает как радиальную Qr , так и осевую нагрузку Qa . В
этом случае в лабораторной установке регистрируется суммарный момент трения
Mc = Mr + Ma ,
Апотери мощности на трение вычисляются по формуле
Nc |
= |
Mc |
n |
(1.7) |
|
9550 |
|||||
|
|
|
В инженерной практике применяют условные расчеты подшипников скольжения.
Виды разрушения и критерии работоспособности: 1) среднее давление
p = |
F |
(1.8) |
|
A0
где, F - нагрузка,
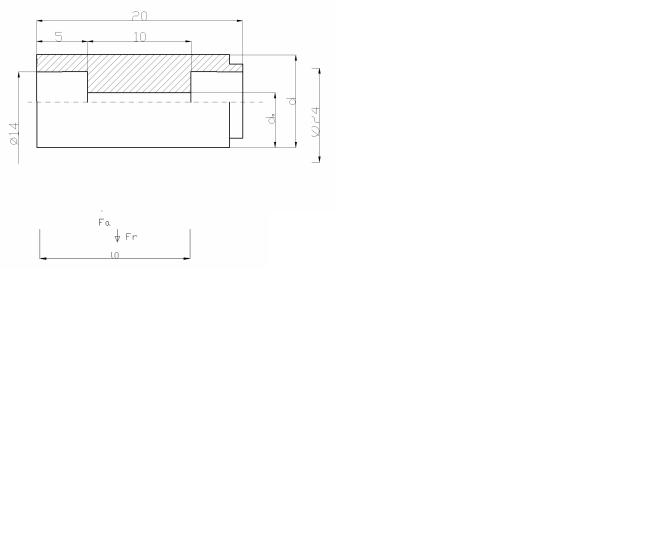
A0 - проекция опорной поверхности на плоскость, перпендикулярную
вектору нагрузки;
2) произведение среднего давления p на скорость скольжения υ . Давление p характеризует несущую способность и износ подшипника, а
произведение p υ - износ и тепловыделение в подшипнике.
Таким образом, для обеспечения нормальной работы подшипника
должны быть удовлетворены два условия |
|
p ≤ [ p], |
(1.9) |
p υ ≤ [p υ]. |
(1.10) |
Для радиального подшипника (рис. 1.2, а) выражение (1.8) примет вид
Схемы подшипников скольжения
|
|
|
|
|
|
|
|
|
|
|
|
а) Радиальный подшипник (β = 90O ) |
б) Упорный подшипник (β = 0O ) |
|
|||
|
|
|
|
|
|
|
|
|
|
|
|
|
|
|
|
|
|
d = 10мм ; lp = 8мм ; |
d = 5мм ; lp = 10мм; |
d0 = 15мм ; d1 =18,5мм ; |
d0 = 14мм ; d1 = 20мм . |
в) |
г) |
|
Рис. 1.2 |

|
|
|
F |
|
|
||
P = |
r |
≤ [ p], |
(1.11) |
||||
|
|||||||
|
r |
|
d lp |
|
|
||
а скорость скольжения, м/с |
|
||||||
υ |
|
= |
π d n |
, |
(1.12) |
||
r |
60 1000 |
||||||
|
|
|
|
где d,lp - диаметр и рабочая длина вкладыша в мм;
n - частота вращения цапфы в мин-1.
Для упорного подшипника (рис. 1.2, б) формулы (1.11), (1.12) примут
вид
Pa |
= |
4 Qd |
≤ [p], |
(1.13) |
||
π (d12 |
− d02 ) |
|||||
|
|
|
|
π n R
υa = 30 1000пр , (1.14)
Кматериалу вкладыша подшипника скольжения предъявляются
следующие требования:
1)Малый коэффициент трения и высокая сопротивляемость заеданию в процессе отсутствия жидкостного трения.
2)Достаточная износоустойчивость наряду со способностью к приработки.
3)Достаточно высокие механические характеристики.
Исходя из этого, для вкладышей подшипников скольжения с учетом условия их эксплуатации могут быть выбраны в качестве материала: олово, алюминий, бронза, чугун, баббит, пластмасса, металлокерамика и т.д.
2. ОПИСАНИЕ ЭКСПЕРИМЕНТАЛЬНОЙ УСТАНОВКИ
Прибор ДП-16АПС смонтирован на основании 1 и содержит следующие основные узлы (рис. 2.1): электродвигатель 2, ременную передачу 3, шпиндель 4, тахогенератор 5, узел испытуемого подшипника 6, осветитель 7 с фотодиодом 8, поворачивающуюся вертикальную плиту 9, закрепленную на горизонтальной оси 10 и рукоятки с фиксатором 11 для ее поворота. Плита 9 установлена на литой стойке 12 (рис. 2.1).
Электродвигатель 2 смонтирован в специальном корпусе, снабженном амортизатором для уменьшения вибрации. Вращение на рабочий валик шпинделя 4 передается при помощи ременной передачи 3. Рабочий валик шпинделя смонтирован на двух шарикоподшипниках, установленных в корпусе. Верхняя часть валика имеет резьбовое отверстие, в которое ввинчивается узел испытываемого подшипника 6. На узел подшипника устанавливают и закрепляют груз 11. На грузе имеется поводок, который вставляется в плоскую измерительную пружину 12. На конце пружины 12 имеется шторка, перекрывающая при деформации пружины световой поток, между осветителем 7 и фотодиодом 8. Величина тока фотодиода

пропорциональная прогибу пружины 12 (то есть, пропорциональна моменту в исследуемом подшипнике) регистрируется микроамперметром 13. Частота
Рис. 2.1 Общий вид прибора ДП-16АСП
вращения рабочего валика измеряется с помощью тахогенератора 5 и регистрируется микроамперметром 14. График тарировки микроамперметра по моменту трения и частоте вращения приведен на рис. 2.2.
Конструкция прибора обеспечивает поворот на 90° в вертикальной плоскости плиты 9 с установленными на ней механизмами; это позволяет изменять соотношение радиальной и осевой нагрузок на подшипник. Поворот плиты осуществляется при помощи рукоятки с пружинным фиксатором 11. С противоположной стороны стойки 12 смонтирован сектор с пазами, позволяющими фиксировать положение плиты 9 через каждые 15°.
Панель управления установкой содержит: микроамперметры 13, 14; тумблер 15 и сигнальную лампочку включения в сеть установки; тумблер 16, предназначенный для изменения чувствительности микроамперметра 13; ручку 17 потенциометра, предназначенного для бесступенчатого регулирования частоты вращения двигателя.
3.ПОРЯДОК ВЫПОЛНЕНИЯ РАБОТЫ
1)Изучить правила по технике безопасности (см. раздел 7).
2)Провести экспериментальное исследование момента трения в подшипнике скольжения от частоты вращения вала, угла наклона оси подшипника, от нагрузки на подшипник.
Для этого необходимо:
по указанию преподавателя выбрать из таблицы 3.1 исходные данные (в каждом варианте выполняется три эксперимента «а», «б», «в»);
по данным таблицы 3.2 и формулам (1.9) – (1.14) проверить допустимость эксплуатации подшипника на максимальных режимах (при nmax ,Qmax ), содержащихся в исходных данных;
в рабочий валик ввинтить сменную ось, на которую установить соответствующий подшипник и закрепить его сверху винтом; затем на подшипник установить необходимый груз и зафиксировать его стопорным винтом; при этом необходимо поводок груза ввести в седловину измерительной пружины 12;
установить тумблеры на панели управления в следующие положения: тумблер 15 в положение «2», тумблер 16 в положение «Скорость», тумблер 17 в положение «Двигатель»;
включить установку тумблером 14 и ручкой 18 потенциометра установить (пользуясь показаниями микроамперметра 13 и тарировочным графиком на рис. 2.2) выбранную частоту вращения вала;
поставить тумблер 16 в положение «Момент» и показаниями микроамперметра 13 (пользуясь тарировочным графиком рис. 2.2) определить момент трения в подшипнике; при недостаточной чувствительности микроамперметра тумблер 15 привести в положение «1». Результаты измерений внести в таблицу 3.3. Аналогично выполнить пункты б и в таблицы 3.1. Результаты измерений внести в табл. 3.3.
4.ОБРАБОТКА ЭКСПЕРИМЕНТАЛЬНЫХ ДАННЫХ
1)По экспериментальным значениям момента трения (см. табл. 3.3), пользуясь формулами (1.2), (1.4) определить коэффициент трения в подшипнике. Результат внести в табл. 3.3.
2)Определить потери мощности на трение по формулам (1.3), (1.5), (1.7). Результаты внести в табл. 3.3.
3)По данным таблицы 3.3 построить следующие графики:
зависимости трения, коэффициента трения, потерь мощности в подшипнике, от частоты вращения вала;
зависимости момента трения потерь мощности на трение от угла наклона оси подшипника.
|
|
|
|
|
|
Таблица 3.1 |
|
|
ИСХОДНЫЕ ДАННЫЕ |
|
|
|
|
||
|
(задаются преподавателем) |
|
|
|
|||
Вариант |
Диаметр |
Вес груза |
Угол наклона |
Частота |
|
||
|
|
|
цапфы d , |
Q, Н |
оси |
вращения n , |
|
|
|
|
мм |
|
подшипника β , |
об/мин |
|
|
|
|
|
|
град. |
|
|
1 |
|
а |
10 |
9,8 (1кг) |
радиальный 900 |
600÷1000 |
|
|
|
б |
10 |
19,6 (2кг) |
радиальный 900 |
600÷1000 |
|
|
|
в |
10 |
9,8 |
радиально- |
800 |
|
|
|
|
|
|
упорный 0÷90° |
|
|
2 |
|
а |
10 |
9,8 |
упорный 0° |
600÷1000 |
|
|
|
б |
10 |
19,6 |
упорный 0° |
600÷1000 |
|
|
|
в |
10 |
9,8 |
радиально- |
900 |
|
|
|
|
|
|
упорный 0÷90° |
|
|
3 |
|
а |
5 |
9,8 |
упорный 0° |
600÷1000 |
|
|
|
б |
5 |
19,6 |
упорный 0° |
600÷1000 |
|
|
|
в |
5 |
9,8 |
радиально- |
1000 |
|
|
|
|
|
|
упорный 0÷90° |
|
|
4 |
|
а |
5 |
9,8 |
радиальный 900 |
600÷1000 |
|
|
|
б |
5 |
19,6 |
радиальный 900 |
600÷1000 |
|
|
|
в |
5 |
9,8 |
радиально- |
800 |
|
|
|
|
|
|
упорный 0÷90° |
|
|
5 |
|
а |
5 |
9,8 |
радиальный 900 |
600÷1000 |
|
|
|
б |
10 |
9,8 |
радиальный 900 |
600÷1000 |
|
|
|
в |
5 |
9,8 |
радиально- |
900 |
|
|
|
|
|
|
упорный 0÷90° |
|
|
6 |
|
а |
5 |
19,6 |
упорный 0° |
600÷1000 |
|
|
|
б |
10 |
19,6 |
упорный 0° |
600÷1000 |
|
|
|
в |
5 |
19,6 |
радиально- |
800 |
|
|
|
|
|
|
упорный 0÷90° |
|
|
Примечание: а, б, в – порядок выполнения опытов
|
|
|
|
Таблица 3.2 |
|
ДОПУСТИМЫЕ РЕЖИМЫ РАБОТЫ ПОДШИПНИКОВ |
|||||
Вариант |
Материал |
[p] , |
[p υ], |
υmax , м/с |
|
|
вкладыша |
Н/мм2 |
Н·м/мм2·с |
|
|
1 |
Бронза Бр. ОФ10-1 |
15 |
15 |
8 |
|
2 |
Бронза Бр. ОЦС 6- |
6 |
8 |
6 |
|
|
6-3 |
|
|
|
|
3, 4 |
Бронза Бр. ФЖ9-4 |
13 |
10 |
5 |
|
5, 6 |
Латунь ЛКС 80-3-3 |
12 |
10 |
2 |
|